熱DCプラズマプロセスによって調製されたSi-SiC複合ナノ粒子を用いたスパークプラズマ焼結SiCの焼結挙動
要約
SiコーティングされたSiC(Si-SiC)複合ナノ粒子は、固体合成SiC粉末の非転写アーク熱プラズマ処理によって調製され、SiCセラミック形成用の焼結添加剤として使用されました。焼結SiCペレットはスパークプラズマ焼結(SPS)プロセスによって調製され、ミクロンサイズのSiC粉末の焼結挙動に及ぼすナノサイズのSi-SiC複合粒子の影響が調査されました。ミクロンサイズのSiCに対するSi-SiC複合ナノ粒子の混合比は10wt%に最適化されました。ビッカーの硬度と相対密度は、焼結温度と保持時間の増加とともに増加しました。相対密度とビッカース硬度は、ミクロンサイズのSiCとナノサイズのSi-SiCの混合物に追加の活性炭を使用した反応結合によってさらに増加しました。最大相対密度(97.1%)とビッカース硬度(31.4 GPa)は、1800°Cの焼結温度で1分間保持し、0.2 wt%の追加の活性炭をSiC / Si-SiCの混合物に添加したときに記録されました。
背景
炭化ケイ素(SiC)セラミックは、高温硬度、耐摩耗性、低熱膨張係数、高熱伝導率、強力な耐食性、過酷な環境での高い安定性などの驚異的な特性により大きな注目を集めています。タービンブレード、ディーゼルエンジン部品、航空宇宙および原子炉材料などのさまざまな分野に適用されます[1,2,3,4,5,6]。ただし、Si-C結合の共有結合性と低い自己拡散係数のため、添加剤なしでSiCを高密度化することは困難です[7、8]。バルクSiC材料は通常、固体焼結炭化ケイ素(SSS-SiC)または出発SiC結晶性粉末からの液相焼結炭化ケイ素(LPS-SiC)のいずれかによって調製されます[7、8]。 SSS-SiCの場合、ホウ素、アルミニウム、炭素、またはそれらの化合物などの液体形成添加剤は、粒子の表面エネルギーの減少と表面に存在するシリカとの反応によるSiCの緻密化に使用されていません。炭素。ただし、このプロセスでは、焼結に2000°Cを超える温度が必要です[7、9、10]。 LPS-SiCは、焼結温度での金属酸化物添加剤の液相形成によって支配され、この液相は、SiC焼結中に物質移動媒体として機能します[8、11、12]。マグネシアとアルミナを除いて、イットリアやその他の希土類酸化物が主に焼結添加剤として使用され、使用する焼結添加剤の組み合わせによっては、焼結温度を1850°Cまで下げることができます[11、12]。しかし、粒界と三重点にアモルファスケイ酸塩化合物が存在すると、SSS-SiCと比較して硬度と高温耐クリープ性が低下します[12]。しかし、処理を強化するために使用される添加剤は、最終的なセラミックでは常に「弱い」二次相になり、通常、高温での機械的特性が低下します[13]。この有害な影響は、添加剤のごく一部が望ましいことを示唆しています。さらに、添加剤の有効性は、それらの分布の均一性に大きく依存します[13]。反応結合炭化ケイ素(RB-SiC)と呼ばれるバルクSiCの製造のための別のアプローチもあります。 RB-SiCでは、溶融シリコンと炭素粉末の反応によりSiCが形成されます[13、14、15、16]。このアプローチはより低い焼結温度を必要とし、製品の形状とサイズの制限はありませんが、ボディの密度が低いことは欠点です[17、18]。ただし、エネルギーを節約するには、焼結温度を下げることが不可欠です。最近では、省エネが、低温でのバルクSiCセラミックの製造に適した他の方法を見つける原動力になっています。
最近、ナノサイズのSiCが広く研究され、バルク形態のものとは異なり、しばしば有用な機械的、物理的、および化学的特性が調べられています[19、20、21]。たとえば、主に高い比表面積と表面活性によるナノ粉末は、高密度に到達することを可能にすることにより、圧密処理におけるナノサイズのSiCの低温焼結性と機械的特性の改善を提供できます[22]。したがって、現在、我々は、固体合成SiC粉末の非転写熱DCプラズマ処理を使用することにより、焼結添加剤として適用するSiコーティングSiC(Si-SiC)ナノ粒子を調製する新しい方法を開発しました[23]。 / P>
本研究では、焼結添加剤としてのナノサイズのSi-SiC複合粒子を、スパークプラズマ焼結(SPS)プロセスによるバルクSiCセラミックの調製に適用し、ナノサイズのSi-SiC複合粒子の添加が焼結に及ぼす影響を調べました。焼結SiCセラミックの温度、相対密度、およびビッカース硬度を調査した。さらに、焼結SiCの相対密度と硬度をさらに高めるために、ナノサイズのSi-SiC粒子の遊離シリコンと追加添加された活性化炭素との反応結合がSiC焼結プロセスに新たに導入されました。ナノサイズ効果と反応結合効果に基づいて、SPSプロセスによりナノサイズのSi-SiC複合添加剤で製造されたSiCセラミックの焼結メカニズムについても議論した。この研究は、比較的低い焼結温度で高密度と硬度のSiCセラミックを調製できる新しい有望な戦略を提供します。
実験的
図1は、固固反応(焼成)によるミクロンサイズのSiC粉末、非転写アーク熱プラズマプロセスによるナノサイズのSiC粉末、およびSPSプロセスによる焼結SiCペレットの調製手順を示しています。この作業では、ミクロンサイズのSiC粉末(主な焼結材料として)とナノサイズのSi-SiC複合ナノ粉末(焼結添加剤として)の2つの異なるサイズのSiC粉末を、それぞれ焼成プロセスとプラズマプロセスで調製しました。
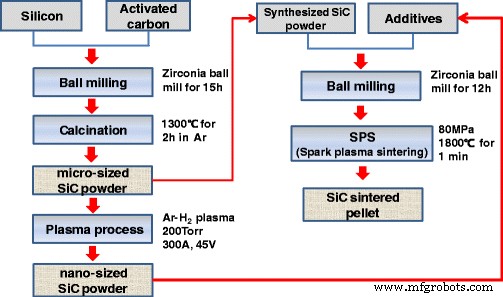
煆焼によるミクロンサイズのSiC粉末とプラズマによるナノサイズのSi-SiC複合粉末の調製、およびSPSによるSiCセラミックの焼結の実験手順
ミクロンサイズのSiC粉末の準備
ミクロンサイズのSiCは、平均粒子サイズが25μm(99.9%; Neoplant Co. LTD。)のSi粉末と、平均粒子サイズが32μmの活性炭(Sigma-Aldrich)を使用して合成されました。通常の手順では、ボールミルを15時間使用して、Siと炭素の比率を1:1.5molで混合しました。混合粉末を垂直管状炉に入れ、アルゴンガス(1 L / min)の存在下で10°C / minの加熱速度で1300°Cで2時間加熱しました。反応の完了後、得られた粉末を瑪瑙乳鉢で粉砕し、さらなる特性評価を行いました。
合成されたSiC粉末のプラズマ処理
プラズマ処理は、以前の研究[21、23]で報告されているように、非転写アーク熱プラズマ反応器によって実行されました。粉砕されたSiC粉末は、特別に設計された粉末フィーダーを使用して、プラズマトーチ内の内径2mmの内部供給パイプラインを介してプラズマアークに供給されました。粉末供給システムは、サンプルコンテナ、バイブレータ、およびキャリアガスラインで構成されていました。粉末は、1 g / minの供給速度で70Vの振動フィーダーによって供給されました。典型的な合成実験は、システム圧力200 Torr、Arプラズマガス流量30 L / min、H 2 ガス流量は約3L / min、DC電流は300 A(45 V)。プラズマ点火後、ミクロンサイズのSiC粉末がフィーダーから供給されました。合成されたナノ粉末は、反応器の壁およびプラズマ反応器システムの底部から収集された。収率は約80〜85%でした。
焼結SiCペレットの準備
焼結SiCペレットは、SPSプロセスによって調製されました(図1を参照)。両方のSiC材料、すなわち、焼成プロセスによって合成されたミクロンサイズのSiC粉末と、プラズマプロセスから得られたナノサイズのSi-SiC粉末の両方が、追加の添加剤なしで使用されました。ミクロンサイズのSiC粉末中のSi-SiCナノ粒子の混合含有量が5から15wt%に変更されました。
混合した粉末をグラファイトダイ(直径20 mm)に入れ、真空雰囲気(10 -2 )でSPSシステムを使用して焼結しました。 トル)。加熱速度は600°C / minに固定され、加えられた圧力は80MPaでした。焼結温度を1600℃から1800℃に変更しました。目標温度での保持時間は、1800°Cで0〜1分で変化しました。焼結後、サンプル表面を研削してグラファイト層を除去し、次にダイヤモンドペーストで研磨した。焼結試料の密度は、浸漬媒体としての脱イオン水中でアルキメデス法によって測定されました。
サンプルの特性評価
固体サンプルの結晶構造は、グラファイト単色化高強度Cu-Kα1放射線(λ)を備えたXRD(D / Max 2005 Rigaku)を使用して決定されました。 =1.5405Å)。 XRDパターンは20°から80°(2 θ)で記録されました。 )スキャン速度0.04°/ s。粒子サイズと形態は、走査型電子顕微鏡(SEM; JSM-5900、JEOL)と透過型電子顕微鏡(TEM; JEM-2010、JEOL)によって調査されました。
結果と考察
図2は、SiとCを1:1.5 molの比率で混合したソリッドステート法で合成されたSiCのXRDパターンとFESEM画像を示しています。 XRDパターンは、図2aに示すように、少量のα-SiCを含むβ-SiCの形成を確認します。遊離シリコンやSiO 2 など、他の不純物相はありませんでした。 。 FESEM画像は、ミクロンサイズのSiC粒子の形成を示し、図2bに示すように、粒子サイズは2〜5μmの範囲で変化しました。
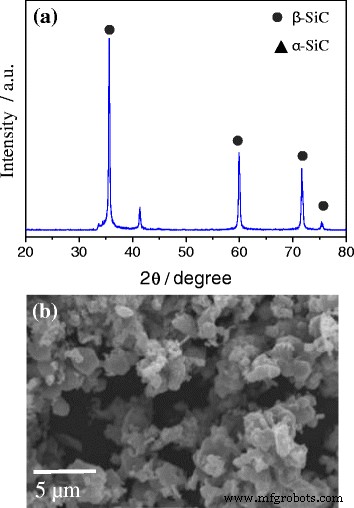
XRDプロファイル( a )およびFESEM画像( b )固体法で合成されたミクロンサイズのSiCの
ナノサイズのSiC粉末は、図3に示すように、熱プラズマ処理を使用してこのミクロンサイズのSiC粉末から調製されました。図3a、bは、それぞれFESEM画像とTEM画像です。これらの写真は、ナノサイズのSi-SiC粒子の形成を確認しており、粒子サイズは20〜70nmの範囲で変化しました。図3cは、SiナノサイズのSiC粒子のHRTEM画像であり、両方の材料(SiとSiC)の明確な格子縞が示されているため、ナノサイズのSi-SiC複合粒子の形成を確認しています。ナノサイズのSiC粉末の表面積は69m 2 でした。 / g。
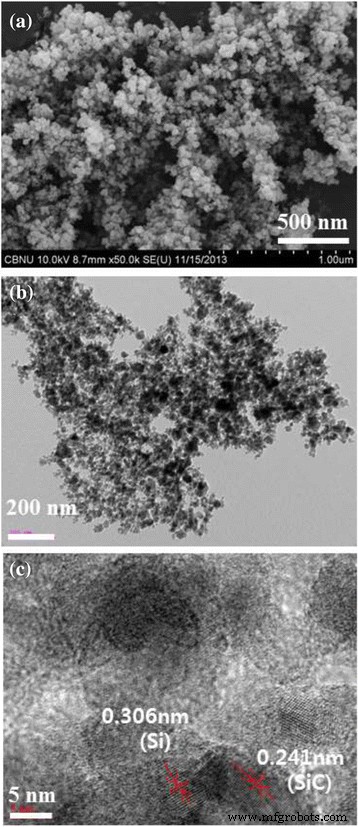
非転写アーク熱プラズマプロセスによって調製されたSi-SiC複合粒子のEM画像: a FESEM、 b TEM、および c HR-TEM
ナノサイズのSiC粒子の相と構造をXRDで分析し、図4に示します。ミクロンサイズのSiCと同様に、少量のα-SiCによるβ-SiCの形成も示しています。ただし、ナノサイズのSiCは遊離のSiとSiO 2 を示しました ピーク。シリコンピークの出現は、熱プラズマ処理中のSiCの部分分解に関連していた。 SiO 2 の起源 ピークは、プラズマ処理後の空気への暴露中のSiC表面の部分酸化に関連している可能性があります。焼結SiCセラミックペレットは、これら2種類のSiC、つまりミクロンサイズのSiCとナノサイズのSi-SiC複合材料から調製されました。混合物は、ミクロンサイズのSiCとナノサイズのSi-SiCのさまざまな組成を使用して、SPSプロセスによって焼結され、焼結温度、焼結温度での保持時間、および圧縮圧力は、表1に示すように変化しました。
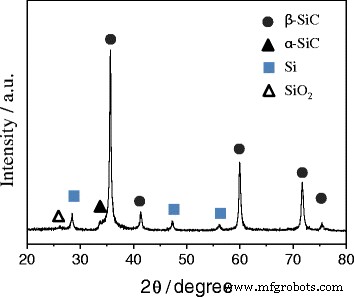
非転写アーク熱プラズマプロセスによって調製されたSi-SiC複合ナノ粒子のXRDプロファイル
焼結温度と目標焼結温度での保持時間に応じた焼結SiCの相対密度とビッカース硬度の変化も表1に示します。相対密度と硬度は焼結温度の上昇とともに増加し、最高相対密度(87.4%)と硬度は(18.6 GPa)は1800°Cで記録されました。相対密度と硬度は、1800°Cの焼結温度で保持時間が0分から1分に増加するにつれて、それぞれ88.2%と21.2GPaにさらに増加しました。これは、相対密度と硬度が保持時間の増加とともに増加することを示唆しています。残念ながら、SPSシステムの制限により、1800°Cでの保持時間をこれ以上延長することはできませんでした。
図5は、さまざまな焼結温度と保持時間での焼結SiC表面のFESEM画像を示しています。図5a–cに示すように、SiCの結晶粒径は、焼結温度の上昇とともに増加しました。ミクロンサイズのSiC粒子の形状とサイズは1600°Cまでほぼ維持され(図5a)、SiCの結晶粒成長は1700°Cから開始され、相対密度と硬度が最大86.1まで増加しました。 %と14.8 GPa、それぞれ(図5b)。 1800°Cの焼結温度では、SiCの粒径は2〜4 µmであり、結晶組織はより緻密化されていました(図4c)。 1800°Cでの相対密度と硬度は、それぞれ87.4%と18.6GPaでした。サンプルを1800°Cの焼結温度で1分間保持した場合、粒子の成長がさらに記録されました。これは、相対密度と硬度がそれぞれ88.2%と21.2 GPaに増加したことから明らかです(図5d)。
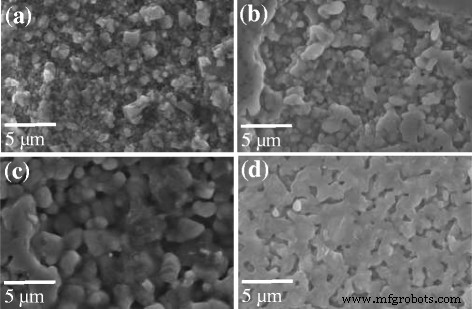
a でのSPSプロセスによるナノサイズのSi-SiC複合粒子を含む焼結SiCのFESEM画像 1600°C、 b 1700°C、 c 保持時間0分の1800°Cの焼結温度、および d 目標温度での保持時間1分の1800°Cの焼結温度
相対密度を上げるために、ミクロンサイズのSiC粉末にナノサイズのSi-SiCを添加する量を5から15 wt%に変更しました。さらに、この混合物に追加の活性炭を追加して、ナノサイズのSi-SiCの遊離シリコンとの反応結合(RB)によって相対密度を高めました。ミクロンサイズのSiC、ナノサイズのSi-SiC、および活性炭のさまざまな組成に応じた、焼結SiCの相対密度とビッカース硬度を表2にまとめています。
<図> 図>焼結温度(1800°C)、保持時間(1分)、および圧力(80 MPa)は、実験全体を通して一定に保たれました。炭素が追加されていない場合、相対密度と硬度は、ナノサイズのSiC含有量が10 wt%まで増加すると増加し、その後減少します。たとえば、ナノサイズのSi-SiCの含有量が5 wt%の場合、相対密度と硬度は85.9%と21.1GPaでした。相対密度と硬度は、ナノサイズのSi-SiCの10 wt%で、それぞれ88.2%と21.2GPaに増加しました。一方、含有量が15 wt%の場合、相対密度は85.6%のままでしたが、硬度は16.6GPaまで著しく低下しました。これは主に、ナノサイズのSi-SiC粒子を過剰に添加すると、焼結したSiCに大量の細孔が生じる可能性があるためです。相対密度と硬度をさらに高めるために、活性炭を追加しました。 0.1 wt%の活性炭を添加すると、相対密度(93.1%)と硬度(25.2 GPa)が著しく増加しました。相対密度と硬度はさらにそれぞれ97.1%と31.4 GPaに増加し、活性炭含有量は0.2 wt%まで増加しました。異なる組成のこれらの焼結SiCペレットのXRD分析を実行し、図6に示しました。29°で記録された弱いシリコンピークを除いて、焼結後も結晶構造に変化はありませんでした。ナノサイズのSi-SiC複合粒子。
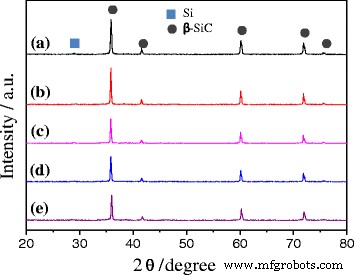
ナノサイズのSi-SiC複合粒子と活性炭をSPSプロセスで焼結したSiCペレットのXRDプロファイル(a、b、c、d、eの詳細を表2に示します)
図7は、ミクロンサイズのSiCとナノサイズのSi-SiCの組成が異なる焼結SiCペレットの表面のFESEM画像を示しています。ナノサイズのSi-SiC含有量が5wt%の場合、SiCの粒子サイズは2〜3 µmで、細孔が大きくなりました(図7a)。図7b、cに示すように、ナノサイズのSi-SiCの含有量が増えると、粒子サイズも大きくなります。 10および15wt%のSi-SiCを含むSiCペレットの粒径は、それぞれ約3〜5および4〜6μmでした。図7d、eは、活性炭を添加した後の焼結SiCペレットのFESEM画像を示しています。 0.1 wt%の活性炭を添加すると、巨大な粒子が現れ始めます。これは、シリコンと活性炭の反応結合によってSiCテクスチャの緻密化が進行したことを示しています。図7eに示すように、活性炭をさらに0.2 wt%まで増やすと、SiCテクスチャが完全に緻密化されました。
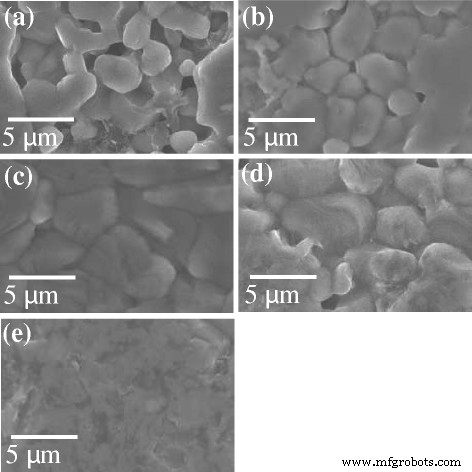
ナノサイズのSi-SiC複合ナノ粒子とSPSプロセスによる活性炭で焼結されたSiCペレットのFESEM画像( a の詳細 、 b 、 c 、 d 、および e 表2に示されています)
図8は、さまざまな焼結温度でのさまざまな組成の焼結SiCサンプルの収縮変位を示しています。 1500°Cまでのすべての試験片で膨張が記録されました。これは主に、SiC混合物に存在するガスの膨張によるものです(図8a–e)。また、初期の焼結ステップと比較して、焼結後のSiC混合粉末を含むグラファイトモールドの高さが1.0〜1.28mm増加することによっても観察できます。焼結温度をさらに上げると、ナノサイズのSi-SiCナノ粒子の焼結効果により、すべての試験片が収縮しました。焼結温度での試験片の保持時間が0分から1分に増加すると、試験片の収縮も増加しました。 SiCとSi-SiCの混合物に追加の活性炭を追加すると、活性炭を含まないSiC / Si-SiC混合物と比較して、1500°C後に高い収縮変位が示されました(図8d、e)。さらに、追加の活性炭の添加量が増えると、収縮変位が増加します。たとえば、図8dに示すように、活性炭の添加量をそれぞれ0.1から0.2 wt%に増やすと、収縮変位は1.11mmから1.61mmに増加しました。これは、Si-SiC複合ナノ粒子の遊離シリコンと活性炭の反応結合効果によるものです。この反応の発熱性により、焼結中にSiCペレット内の実際の温度が上昇します。したがって、これらの結果は、シリコンと活性炭の反応結合効果がSiCセラミックの相対密度と硬度を高めることができることを明確に確認しています。
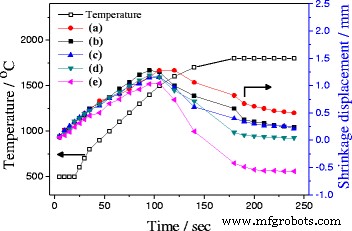
SPSプロセス中のナノサイズのSi-SiC複合ナノ粒子で焼結されたSiCペレットの収縮変位の変化(a、b、c、d、およびeの詳細は表2に示されています)
以上の実験結果から、ミクロンサイズのSiC粉末とナノサイズのSi-SiC複合粉末および活性炭との焼結メカニズムを以下のようにまとめることができます。表1から、ミクロンサイズのSiC粉末と10 wt%のナノサイズのSi-SiC複合粉末の焼結が1600°Cで開始され、焼結温度と保持時間の増加とともに焼結反応が加速されたことがわかりました。この結果から、ミクロンサイズのSiC粉末の焼結に対するSi-SiC複合ナノ粒子のナノサイズ効果を確認しました。ここで、ミクロンサイズのSiCとナノサイズのSi-SiC複合粉末の混合物に活性炭素を添加すると、Si-SiC複合ナノ粒子の遊離シリコン間の発熱反応に起因する反応結合を誘導することができます。図9に概略的に示すように、焼結プロセス。したがって、ナノサイズのSi-SiC複合粉末と焼結添加剤としての活性炭素を含むミクロンサイズのSiC粉末の焼結メカニズムは、両方の効果に依存していることがわかりました。ナノサイズのSi-SiC複合粉末から導入されたサイズ効果と反応結合効果。
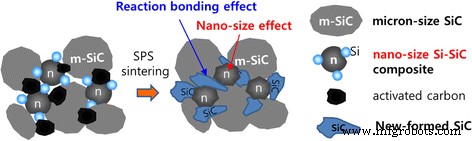
ナノサイズのSi-SiC複合粉末と焼結添加剤としての活性炭を使用したミクロンサイズのSiC粉末の焼結メカニズムの概略図
結論
ミクロンサイズのSiC(2〜5μm)粉末は、Si粉末と活性炭源を使用したソリッドステート法によって合成されました。粒子サイズが20〜70 nmのナノサイズのSi-SiC複合粉末は、非転写アーク熱プラズマプロセスによって調製されました。焼結SiCペレットは、焼結添加剤としてミクロンサイズのSiC粉末とナノサイズのSi-SiC複合粒子の比率が異なる混合物を使用したSPSプロセスによって調製されました。ミクロンサイズのSiCとナノサイズのSi-SiCの一定の比率(90:10)では、相対密度とビッカース硬度は、焼結温度と保持時間の増加とともに増加しました。最大相対密度(88.2%)とビッカース硬度(21.2)は、1800°Cの焼結温度で1分間の保持時間で記録されました。ミクロンサイズのSiCとナノサイズのSi-SiCの混合物に追加の活性炭を追加することにより、相対密度とビッカース硬度がさらに向上しました。 SiC / Si-SiC混合物に0.2wt%の追加活性炭を追加すると、相対密度とビッカース硬度がそれぞれ97.1%と31.4GPaに増加しました。 Si-SiC複合粒子のナノサイズ効果とシリコン-炭素反応結合の発熱性が相対密度と硬度の増加の原因であることがわかりました。したがって、ナノサイズのSi-SiC複合粒子は、SiCセラミックの焼結に有望な添加剤である可能性があることが示唆されました。
ナノマテリアル
- 耐火合金焼結プロセス
- 超長銅ナノワイヤーによるシリコーン複合材料の優れた熱伝導率の向上
- 化学センシング用の貴金属ナノ粒子で装飾されたエレクトロスピニングポリマーナノファイバー
- グリセロールの電気透析脱塩のための無機イオン交換体のナノ粒子を含む複合膜
- CuSナノ粒子でコーティングされた着色および導電性CuSCN複合材料の容易な合成
- 多機能GaN / Feナノ粒子による内皮細胞の標的化
- ナノカーボンフィラーの電界支援配向による複合材料の電気的性質
- 光触媒活性が強化されたAgナノ粒子/ BiV1-xMoxO4の相乗効果
- 分子動力学法によるアブレシブナノメートル切削プロセスに及ぼす衝撃方向の影響の研究
- クルクミンの処理効果を持つPEGコーティングされたCoFe2O4ナノ粒子の毒性
- 抗菌剤として銀ナノ粒子で装飾された酸化グラフェンベースのナノコンポジット