チップベースのナノマシニングに関する分子動力学研究:レビュー
要約
チップベースのナノマシニング(TBN)アプローチは、微細構造の製造のための強力で実行可能な技術であることが証明されています。分子動力学(MD)シミュレーションは、実験では完全には明らかにできなかったメカニズムを調査するために、TBNアプローチに広く適用されています。この論文は、TBNアプローチのMDシミュレーションにおける最近の科学的進歩をレビューします。最初に、さまざまな材料のシミュレーションモデルの確立方法を示します。次に、切削抵抗分析、材料除去の分析、地下の欠陥分析など、TBNアプローチの機械加工メカニズムの分析について説明します。最後に、MDシミュレーションにおけるTBN法の現在の欠点と将来の展望を示します。このレビューが追跡調査のための特定の参考資料を提供できることを願っています。
はじめに
マイクロ/ナノ製造技術は、環境、エネルギー、生物学、医学、国防などのさまざまな分野で広く使用されており、国の発展と社会の進歩を促進する上でますます重要な役割を果たしています[1,2,3,4] 。高精度のマイクロ/ナノファブリケーションを実現するために、TBNと呼ばれる原子間力顕微鏡(AFM)プローブベースの機械加工アプローチは、簡単な装置と操作、環境要件の低いナノスケールの機械加工精度を備えており、強力で実行可能であることが示されています微細構造を製造するためのアプローチ[5、6]。これまで、ナノドット、ライン/グルーブ、2次元(2D)/ 3次元(3D)構造、さらにはナノデバイスの主要コンポーネントとして知られる曲面上のナノ構造でさえ、TBN法によってすでに成功裏に製造されています[7]。
より高精度にナノ構造を作製するには、TBN法の機械加工プロセスを深く理解する必要があります。多くの学者が、金属[8]、半導体[9、10]、ポリマー[11]などのさまざまな材料で実験を行い、TBNアプローチのメカニズムを調査してきました。ただし、実験によってTBNアプローチの内部メカニズムをさらに調査することは困難です。分子動力学(MD)シミュレーションは、実験では完全には明らかにできなかったナノマシニングプロセスを探索するための強力なツールであることが実証されています[12、13]。実験的方法と比較して、MD法は、切削力、応力状態、エネルギー散逸、および表面トポグラフィーの分析を通じて、材料除去と表面生成のマイクロスケールメカニズムをよりよく説明できます[12]。
過去に、一部の学者はすでにMDシミュレーション技術を使用してTBNプロセスを調査しました。 Fang etal。ナノリソグラフィープロセスに対するスクライビングフィードとコーン角度の影響を調査しました[14、15]。磯野と田中は、ニッケル金属の温度、被削性、原子間力の影響を分析しました[16、17]。ヤンら。 AFMベースのリソグラフィプロセスにおけるチップ形状の影響を研究しました[18]。現在、いくつかの新しいTBNプロセスがMDシミュレーションで調査されています。 Xiao etal。静的耕起法と動的耕起法の違いを比較し、動的耕起法でより小さなナノ構造を製造できることを発見しました[19]。 Geng etal。プローブに一定の法線荷重を直接加えることにより、荷重制御されたナノスクラッチのMDシミュレーションを実行しました[20]。より高密度のナノグルーブを製造するには、最小フィード(MF)を検討する必要があります。レンら。 MDシミュレーションを使用してMFを決定するための粗い基準から細かい基準を含む新しいアプローチを提示しました[21]。結果は、高精度のMFが得られることを示しています。ただし、以前のレビューペーパー[12、13、22、23、24]には、TBNプロセスに使用されるMDシミュレーション技術のこれらの新しい進歩は含まれていません。したがって、このレビューでは、TBNメソッドのMDシミュレーションの最近の最先端に焦点を当てます。最初に、さまざまな材料のモデリング技術と新しい機械加工方法について説明します。次に、切削抵抗分析、材料除去の分析、地下の欠陥分析など、TBN法のメカニズムをレビューします。最後に、TBNのMDシミュレーションにおける残りの課題と将来の展望もこのレビューで示されています。
シミュレーション方法
正確な予測結果を得るには、シミュレーションモデルと関連する処理構成を最適化する必要があります。シミュレーションモデルには、主に原子配置とポテンシャル関数が含まれています。原子配置は、結晶構造とアモルファス構造に分類できます。銅、鉄、シリコンなどの結晶性材料の原子は規則正しく整然と配置されており、ポリマーなどのアモルファス材料は不規則な分子鎖で構成されています。ナノスケールでの材料の挙動は、ポテンシャル関数によってMDシミュレーションで表され、さまざまなポテンシャル関数が提案され、原子シミュレーションで材料の挙動をシミュレートするために利用されています。また、さまざまな加工条件や加工方法などの加工構成も考慮する必要があります。次のセクションでは、モデルの確立と処理の構成の方法論について説明します。
MDモデルの確立
結晶性物質の内部原子配置は、銅(面心立方)、鉄(体心立方)、チタン(最密六方晶)、シリコン(ダイヤモンド構造)などさまざまです[27、28]。ほとんどの結晶性材料は、単結晶および多結晶構造の形をしています。単結晶固体は、欠陥がなく、その体積全体にわたって周期的に繰り返される原子構造を持っています。ユニットセルを3つの空間方向すべてに複製すると、単結晶モデルを簡単に確立できます[13]。アトミックMDモデルを確立する際には、ワークピースの加工特性に影響を与える可能性のあるさまざまな表面配向を考慮する必要があります[29、30、31]。多結晶構造は、ボロノイ分割法[32]に従って構築された、さまざまな粒子サイズの構造を持っています。ナノツイン(NT)材料は、多結晶の特殊構造の一種であり、超高強度、優れた延性、高い破壊靭性などの優れた機械的特性により、より重要な研究対象となっています[33,34,35,36]。 。このレビューでは、NT多結晶Cuを構築する方法を例として示します[25]。最初に、同じ厚さの複数の単結晶Cu層からなる多層を構築し、隣接する層の間にTBを形成します。次に、各粒子の角度が計算されます。最後に、周期境界条件を持つNT多結晶は、多層構造と得られた粒子角度に対応するボロノイ構造を使用して生成されます。図1aは、単結晶Cu、多結晶Cu、NT多結晶Cuを含む銅の原子配置を示しています。これらの原子は、共通の隣接銅によって着色されています。
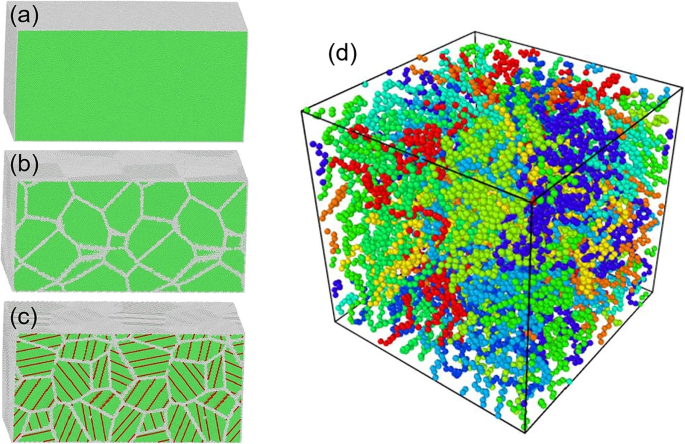
a 単結晶Cuの微細構造。 b ナノ多結晶の微細構造。 c NT多結晶の微細構造。緑と白はFCCと欠陥原子を表すため、原子はCNA値に従って色分けされます[25]。 d アモルファスPEの平衡化された結合原子モデルであるモデルは、さまざまな分子鎖によって着色されています[26]
以前の研究では、ポリマーは一般的な粗視化モデルでモデル化されていました[37、38]。たとえば、ポリエチレン(PE)のモデルを確立するための詳細は次のとおりです[39]。(i)モンテカルロ自己回避ランダムウォークアルゴリズムを使用して、10個の分子鎖を持つ初期PEシステムが取得されました[39]。; (ii)各鎖の最初の原子が最初に格子の利用可能なサイトに挿入され、次に分子鎖が結合長とセル内の占有されていないサイトに応じて確率的に段階的に特定の方向に沿って成長し始めました。; (iii)初期密度が与えられると、シミュレーションボックスのサイズが決定されます。私たちのシミュレーションでは、最初のシミュレーションボックスの寸法は約80.06×80.06×80.06Å 3 でした。 10個のPEチェーンで構成されるシステムの場合。 PEのMDモデルを図1dに示します。
先端の形状は一般に複雑で変化しやすく、円錐形[40]、三角錐[18]、半球(鈍い形)[21]など、TBNプロセスで重要な役割を果たします。特に、MDモデルのピラミッドツールの形状はAFM機械加工プロセスの形状と一致しており、球面ツールは研削プロセスの砥粒と一致しています。このように、シミュレーション結果と実験結果を比較することで、加工メカニズムをよりよく説明することができます。ほとんどの場合、先端は無限に剛性があると見なされます。これは、原子の相対位置を一定に保ち、一定の速度で移動することによって実現されます[41]。
シミュレーション結果の信頼性を決定する適切な位置エネルギー関数を選択することも重要です[21]。 EAMは、金属システムに適したマルチボディポテンシャルです[24]。これは、金属凝集のより現実的な記述を提供し、銅[42]や鉄[43]などの金属原子間の相互作用を記述するために使用される体積依存性によって継承されるあいまいさを回避します。 Tersoff [44]およびStillinger-Weber(SW)[45]のポテンシャルは、ダイアモンドの立方体構造を持つ材料のモデリングに特に適していることが証明されています。 TBNプロセスにおけるSiのメカニズムを調査するには、MDシミュレーションで転位すべりと相変態を観察する必要があります。 Tersoffポテンシャルと比較して、SWポテンシャルは、多くの異なるシリコン構成を記述するのに十分な柔軟性を備えているだけでなく、欠陥のないシリコンをもたらすab initio転位核形成に最も近い一致を提供します[46、47]。したがって、SWポテンシャル関数は、シリコン原子間の相互作用を説明する可能性が高くなります。分析的結合次数ポテンシャル(ABOP)、反応性経験的結合次数(REBO)、および適応分子間反応性経験的結合次数(AIREBO)ポテンシャルは、タイトバインディング近似に従ってTersoffのポテンシャル関数を拡張し、基本量に依存するポテンシャルのクラスです。 48]。 ABOPポテンシャルは、シリコン原子と炭素原子間の相互作用に理想的です。これは、SiCプロセスでの材料の変形と除去挙動を調査するために使用されます。 REBOポテンシャルは、カーボンおよびカーボンナノチューブのシミュレーションで特に人気があります。 AIREBOモデルは、REBOポテンシャル関数の欠陥を克服するために開発され、REBO項よりも正確な近似を提供し、より複雑な相互作用をモデル化する機能も追加しました[41]。ポリスチレン試料の分子間および分子内相互作用は、確立されたAIREBOポテンシャルによって説明されます[49]。
MDシミュレーションの大部分は、大規模原子/分子大規模並列シミュレーター(LAMMPS)を使用して実行されました[50]。多結晶およびナノツイン多結晶材料のようないくつかの複雑なワークピースモデルは、Atomskを使用して実行できます[51]。原子、結合角、不適切、およびそれらのさまざまなタイプを含むポリマーの構造は、Material Studio(MS)から生成されたデータファイルから取得されます[52]。 Open Visualization Tool(OVITO)[53]とVisual Molecular Dynamics(VMD)[54]はどちらも、モデルまたは機械加工のプロセスを視覚化するための便利なツールです。
MDシミュレーションを使用することで、さまざまな材料モデルを効果的に確立できます。ただし、ほとんどのワークピースモデルはサイズが50nm×50nm×50nmより小さいため、実際の結果から逸脱する可能性があります[40、55、56]。その上、GaAsやLu 2 のようないくつかの材料を効果的に記述することができる潜在的な機能がまだ不足しています。 O 3 。したがって、シミュレーションプロセスをより正確に記述するために、MDモデルと関連する潜在的な関数を最適化する必要があります。
構成の処理
TBN実験では、負荷制御モードは通常、チップに一定の通常の負荷をかけることによって実行されます。このモードは、特に傾斜面または曲面でナノマシニングを実行する場合に、より高精度であることが実証されています。ただし、TBNプロセスの多くのMDシミュレーションは、変位コントローラーモードで実行されるため、シミュレーションと実験の間に違いが生じる可能性があります[18、57]。したがって、一部の学者は、プローブに一定の通常の負荷を直接適用することにより、負荷制御されたナノスクラッチプロセスのMDシミュレーションを実行しました[20、58]。機械加工工程では、緩和段階、浸透段階、引っかき段階の3つの部分に分けることができます。さらに、原子間力顕微鏡(AFM)のビーム曲げ、傾斜角のある基板、およびサンプル表面の粗さのために、チップはワークピースに対して完全に垂直ではありません。したがって、チップの傾きの影響を無視してはなりません。 Liu etal。傾斜角度の異なるチップを選択して、加工結果に対するチップの傾斜の影響を調査しました[59]。また、先端の摩耗は加工工程の重要な要素であり、加工品質に大きな影響を与えます。水層潤滑によるナノスクラッチは、チップの摩耗を減らして工具寿命を延ばし、加工品質を保証する場合があります。しかし、水層潤滑の影響を受ける加工メカニズムはまだよくわかっていません。この点を解決するために、Ren等。 MDシミュレーション法を使用して、単結晶銅の加工結果に対する水層潤滑の影響を調査しました[60]。
シングルスクラッチプロセスは、ナノグルーブを製造する簡単な方法であることが証明されていますが、グルーブの寸法に制限があります。ナノグルーブのサイズを拡大するために、マルチパススクラッチ法が提示されました[62]。 Geng etal。シングルパスアプローチとマルチパスアプローチの違いをMDシミュレーションと実験結果で研究しました[20]。シングルパスとマルチパスの両方のアプローチは、AFMシステムの接触モードで実行される静的耕起リソグラフィーと見なすことができます。ただし、静的プラウリソグラフィーは、長距離スクラッチプロセスを実行するときに無視できないチップ摩耗を引き起こす可能性があります。タッピングモードベースの機械加工技術は、ダイナミクスプラウリソグラフィーと呼ばれ、チップの摩耗を減らす可能性があります。図2に、単結晶銅の静的および動的耕起リソグラフィーの概略図をそれぞれ示します。静的耕起の場合、ダイヤモンドチップは最初に下向きに供給され、次に x の負の方向に沿って耕起を開始しました。 軸。耕起が終了した後、先端を元の垂直位置まで上方に引き抜いた。動的耕起プロセスでは、ダイヤモンドの先端が尖ったピークバレーの振幅と周期を持つ正弦曲線に沿って移動しました[19]。タッピングモードベースの機械加工技術の原理に基づいて、Sundaram等。は、AFMを使用した新しいナノ加工方法を開発しました。これは、緩い研磨剤による振動支援ナノ衝撃加工(VANILA)と呼ばれます。この方法では、AFMをプラットフォームとして使用し、シリコンワークピースとAFMチップの振動の間のスラリーにナノアブレイシブを注入します。研磨剤の運動エネルギーは、AFMチップの振動によって生成され、その結果、サンプルのナノスケールの材料除去が行われます[61]。 VANILAプロセスの概略図を図2b、cに示します。
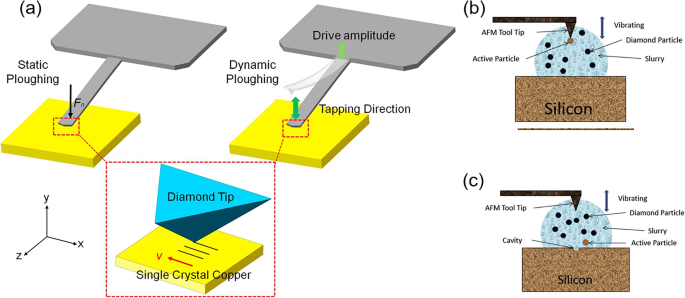
a 単結晶銅の静的および動的耕起リソグラフィーの概略図[19]。 b ダイヤモンド粒子を打つAFMツールチップ。 c ワークピースに衝突するダイヤモンド粒子[61]
シミュレーション結果の分析
切削抵抗分析
切削抵抗は、材料の除去プロセスと進化の欠陥を明確に反映している可能性があります。これは、切削現象を理解するための重要な物理的パラメータです[19、63、64]。さらに、切削抵抗は切削抵抗と工具寿命に密接に関連しており、TBN加工プロセスのガイダンスを提供する可能性があります[65]。 TBNプロセスでは、切削抵抗は主に力校正法で評価されますが、横力はこの方法では取得できませんでした[66、67]。分子動力学技術を使用することにより、横力と接線力を含む切削抵抗の変化をプロセス全体でリアルタイムに観察できます[68]。さらに、平均力と合力もMDシミュレーション法で取得できます。
切削抵抗の変動を分析しますが、さまざまな材料構造の違いや、加工パラメータがTBNプロセスに与える影響を反映できます。 Li etal。単結晶Cuと比較して、多結晶Cuに引っかき傷を付ける力が高いのは、チップが結晶方位の異なる別のグレインに移動するときに、表面グレインの異方性がワークピースとチップの間でほとんど影響を与えないためです。安定した塑性流動は、単結晶Cuの単一配向システムによる材料除去で示されます[25]。また、ナノスクラッチ速度が速いほどチップが多くなるため、異なる結晶構造の切削力は切削速度の増加とともに増加することがわかります[69]。逆に、切削抵抗の変化は、SiCのスクラッチプロセスに悪影響を及ぼします。これは、速度が速いほどアモルファス結晶構造原子が生成され、SiC材料の延性が高まり、除去が容易になるためです[70]。ヤンら。 MDシミュレーション法を使用してCu / Ni二重層の加工性を調査し、転位の移動が機能する二重層の界面によって妨げられたため、Ni-Cu二重層の力がCu、Ni、および二重層Cu-Niと比較して高いことを発見しました伝播の障壁として[71]。アモルファスポリマーに関しては、加工特性は次の3つの異なる側面で引っかき速度の影響を受けました[72]。まず、高速で生成された先端の前のパイルアップ高さが大きいほど、先端への抵抗。次に、速度が速いほど変形速度が速くなり、材料のひずみ硬化が発生する可能性があります。これはまた、切削抵抗の増加につながります。最後に、速度の増加に伴い、熱軟らかさ効果により、ワークピースをより簡単に加工できるようになり、接線力と法線力が減少します。ポリマーの機械加工プロセスでは、切削力は速度の増加とともに増加します。これは、パイルアップとひずみ速度の硬化効果が引っかき力を決定する上でより重要な役割を果たすことを示しています。ワークピースの材料の影響に加えて、チップの形状も機械加工プロセスで重要な役割を果たします[18、73、74]。レンら。円錐形の先端での切削抵抗に対する先端角度の影響を調査しました。先端と被削材の接触面積が大きくなるため、半頂角が大きくなると力が大きくなることがわかります[21]。また、摩擦係数は半頂点で大幅に減少し、硬度は増加します[75]。
一部の学者は、特定の加工条件での切削抵抗の変化についても調査しました。レンら。水層の厚さと引っかき力の相関関係を分析しました。水層の厚さの変化に伴う引っかき力の変化を図3に示します。水層が主に潤滑と切削抵抗の低減の役割を果たすマクロ引っかきプロセスとは異なり、水層の抵抗は潤滑効果と比較して支配的です。水層が厚くなると、総切削抵抗が大きくなります[60]。さらに、先端の傾きの影響は、硬度(原子あたりの垂直抗力)と摩擦係数の分析によっても議論されます[59]。結果は、通常の硬度が前方または後方方向に比べてより敏感であり、横方向の先端傾斜の影響を無視できることを示しています。さらに、摩擦係数が変化する主な理由は法線力に対する傾斜効果であり、引っかき力に対する傾斜効果は法線力に対する効果よりもはるかに小さいです。
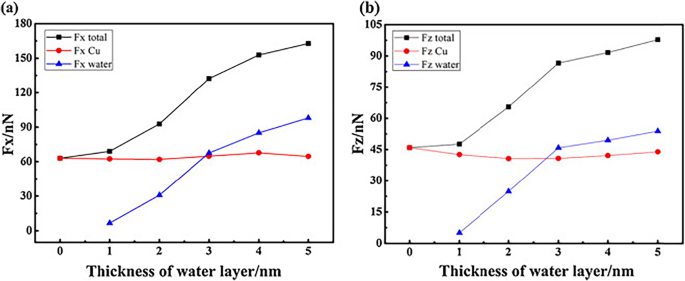
a 水層の厚さの変化に伴う平均引っかき力の変化: a 接線力と b 法線力[60]
静的耕起と動的耕起の切削抵抗を比較することにより、メカニズムの違いを明らかにすることができます。動的プラウリソグラフィーの切削力は、ダイヤモンドチップの周期的なタッピングによって大幅に振動しますが、静的プラウではわずかな変動が見られます。さらに、動的耕起の平均加工力は静的耕起の平均加工力の半分よりも小さく、動的耕起リソグラフィーの先端摩耗が少ないことを示しています[19]。動的耕起工程では、先端の向きが切削抵抗に大きく影響します。ヤンら。溝深さとすき力を組み合わせて加工効率を比較しました。結果は、チップのサイドフェイスフォワードが、チップのフェースフォワードの配向と同様の耕起力を持っていたが、同時に溝の深さの2倍以上であったため、最高の効率を持っていることを示しています[63]。切削抵抗の分析を通じて、さまざまな材料と加工条件でのTBN加工プロセスのメカニズムをさらに説明することができました。さらに、さまざまな処理モードでの切削抵抗の比較は、TBNアプローチのプロセス最適化のガイダンスを提供する可能性があります。
材料除去状態の分析
材料除去状態分析も、TBNアプローチのメカニズムを明らかにするために不可欠な方法です。機械加工プロセスでの材料とトポグラフィーの除去は、通常、走査型電子顕微鏡(SEM)とAFMで観察されます。しかし、溝の形態と除去状態は処理後にしか検出できず、材料除去プロセスを動的に理解することはできませんでした。最近、張等。 SEMに直接接続された線形切削工具を使用して、材料切削の切りくず生成プロセスを確認しましたが、この方法は複雑であり、SEMを変更する必要があります[76]。したがって、この方法を一般化することは困難です。実験法と比較して、MDシミュレーション法はナノスケールでの材料除去メカニズムと表面生成を容易に調査することができ、MD法により加工プロセスをリアルタイムで観察することができます。
TBNプロセスのMDシミュレーション結果から、変形状態は耕起状態と切削状態に分類されることがわかっています。先端の動きに伴い、先端前方の被削材原子が圧搾されて蓄積し、切削状態で連続切りくずを形成します。同時に、チップを通過した後、製造された溝の左側と右側にいくつかのワークピース材料原子が堆積します[57]。切削状態と非切削状態の比率を比較することにより、さまざまな先端半径を使用してさまざまな引っかき深さで引っかいたときに、切削状態と耕起状態のどちらが支配的な部分を占めるかを知ることができます[77]。過去数年間、多くの学者が材料除去状態の材料特性をさらに調査してきました。たとえば、単結晶材料はTBNプロセスで異方性を示し、材料の除去に大きな影響を及ぼします[20]。単結晶材料と比較して、粒界は多結晶材料の機械的特性に重要な影響を及ぼします。 Gao etal。パイルアップのプロファイルを決定する際には、粒子サイズではなく粒子配向も支配的であることがわかりました[78]。さらに、先端の形状も材料の除去に強い影響を及ぼします。 3種類のチップ(円錐形、三角錐、半球形のチップ)を選択して、材料の除去状態に対するチップの形状の影響を明らかにしました。円錐形の先端の場合、頂角の半分に明確に依存します。先端の頂角の半分を大きくすると、切りくずの体積が増え、引っかき面の滑らかさが向上しますが、より高い引っかき力が必要になり、ワークピースの摩擦係数と温度が高くなり、表面下の損傷が増加します[40]。 Alhafezは、パイルアップの形成に対する半頂角の影響も調査しました[75]。先端の半頂角が小さい場合は、主に前方にパイルアップが蓄積し、先端の半頂角が大きい加工条件では横方向のパイルアップが支配的であることがわかります。いくつかの研究は、AFMベースの機械加工プロセスにおけるチップの実際の形状と一致する三角錐チップに焦点を合わせました[19、20、63、79]。主に、エッジフォワード、フェイスフォワード、サイドフェイスフォワードの3つの加工方向を比較しました。 SiCの加工工程では、工具の引っかき方向を調整するだけで、材料の除去状態を簡単に制御できます。エッジフォワードスクラッチ方向は、より安定したプロセスを提供でき、その結果、得られた溝のサイズ精度と一貫性が向上します[79]。ただし、ポリマーの材料除去状態は、金属または半導体材料と比較して温度に敏感です。スクラッチプロセス中、スクラッチゾーンの局所温度はガラス転移温度よりも高く、これはスクラッチゾーンのワークピースを延性のある方法で除去できることを示しています[72]。 Zhan etal。非晶性ポリスチレンの微視的摩擦メカニズムを調査しました。彼らは、分子鎖の柔軟性が温度の上昇とともに上昇することを発見しました。これにより、分子鎖がより簡単にカールして元の状態に戻ることができます[56]。 Du etal。加工速度がポリスチレンの加工結果に大きな影響を与えることを発見しました。加工速度が小さい場合は鎖内変化がポリスチレン試験片の永久変形を支配し、加工速度が大きい場合は鎖間滑りがより顕著になります[80]。
上記の議論からわかるように、ほとんどの研究は、流体ではなく、主に乾燥状態に焦点を合わせていました。ただし、水層の厚さが厚いと、ツールの前に蓄積された原子が減少し、溝に沿ったバリが目立たなくなり、表面粗さが目に見えて減少し、比較的滑らかな表面になります。水層が潤滑剤として作用し、工具と新たに形成された切りくず表面との間の付着領域を減らし、切りくずと工具の面の境界で示される抗力を減らすと説明することができます。直接的な結果は、表面品質が大幅に向上することです。水層の厚さが増すにつれて、表面品質を徐々に改善することができます[60]。いくつかの新しい機械加工アプローチでは、Shockly etal。振動支援ナノ衝撃加工におけるパラメータ(衝撃速度、衝撃角度、および動作温度)がナノキャビティの形成に及ぼす影響を調査し、動作パラメータが、図に示すように、生成されたナノキャビティの深さと幅に実質的な影響を与えることを発見しました。 。4[61]。 Xiao etal。動的耕起プロセスの溝の深さと幅は静的耕起プロセスのそれよりも小さいことがわかりました。これは、動的耕起リソグラフィーによって小さな特徴を持つナノ構造を製造できることを意味します。さらに、溝の寸法は、動的耕起プロセスの駆動振幅比によって制御できます。これは、溝の製造も制御可能であることを示しています[19]。
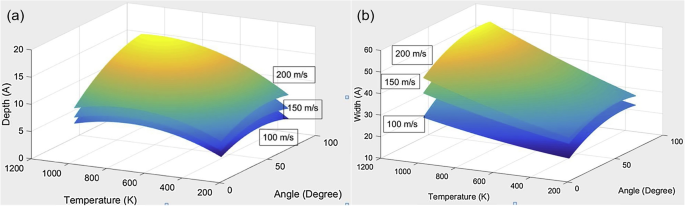
a の重回帰プロット ナノキャビティの深さ(衝撃速度、衝撃角度、および動作温度)および b ナノキャビティの幅(衝撃速度、衝撃角度、および動作温度)[61]
材料除去プロセス中、摩耗挙動が先端に存在します。これまでのほとんどの研究では、先端は剛体として定義されていました。つまり、工具の摩耗現象を直接観察することはできませんでした[13]。多くの学者は、材料の除去状態、応力、および温度分布を研究することによって工具の摩耗を調査しました[70、77]。機械加工プロセス中のチップの実際の摩耗現象を反映するために、Meng etal。チップを変形可能なボディとして設定し、機械加工プロセス中のチップの摩耗挙動を確認しました[81]。結果は、ダイヤモンドアブレシブ摩耗の形態が主に初期段階での接着摩耗と加工安定段階での原子ごとの摩耗であり、アブレシブの原子ごとの帰属摩耗の量が切削速度の影響を受けにくいことを示しています。 81]。チップの摩耗挙動に関する報告が比較的少ないことが注目に値します。うまくいけば、チップの変形可能なボディを使用することで、ナノマシニングプロセス中のチップの摩耗挙動の調査がさらに促進されることが期待されます。
材料除去状態分析は、機械加工プロセスのリアルタイム監視を効果的にサポートします。しかしながら、上記のような長さスケールの制限のために、機械加工された表面の形態および材料除去プロセスは、定性的な比較によってのみ分析することができた。正確な処理結果を予測することは困難です。
欠陥進化プロセス分析
スクラッチプロセス中に発生する欠陥に関する情報を取得するために、通常、TEMはFIBサンプル準備技術の後に使用されます。これには、操作が比較的複雑で、コストが高く、材料に強く依存するなど、いくつかの欠点があります。
MDシミュレーション法では、サンプル表面の下に発生する欠陥を簡単に取得できます。さらに、スクラッチ中の欠陥進展プロセスは、実験的方法では得られなかったMDシミュレーションアプローチを使用して観察することもできました。一般的などちらの分析(CNA)[82]、中心対称性パラメーター(CSP)[83]、すべりベクトル分析[84]、Ackland-Jones分析[85]など、欠陥タイプを抽出するために利用できる多くのアルゴリズムが提示されました。 、これらの方法は、転位の伝播を追跡するのには適していません。特に、特定の方向に沿った先端の引っかき傷によって多数の転位が生成される場合、これらの方法を使用して試料内で何が起こっているかを調べることはできなくなります[86]。 Chen etal。材料変形の原子滑りプロセスを視覚化するための滑り分析を提示しました。これにより、多数の原子が存在する条件で、指定された期間中に隣接する原子に対して滑り落ちた原子を除外できます[86]。この方法を使用することによって、Xiao等。動的および静的耕起リソグラフィー中のすべりプロセスを調査しました[19]。切削抵抗とすべり過程の関係を図5に示します。動的耕起の場合、サンプル材料は主に下向きと横向きに流れますが、静的耕起過程では明らかな下向きの物質の流れは観察されません。さらに、転位の伝播は先端の向きに依存し、溝のさまざまな形態につながります。転位抽出アルゴリズム(DXA)は、格子転位を識別し、それらのバーガーベクトルを決定するための有用な転位分析ツールでもあります[87]。この方法を使用することによって、Gao等。鉄のナノスクラッチの挙動を調査しました。彼らは、転位ネットワークの明確な再編成を発見しました。最初は、プラスチックゾーンはパスに沿った引っかき傷の長さとともに直線的に成長します。その後、ある程度の長さの転位反応の後、転位密度は急速に減少します。その場合、塑性活動はスクラッチフロントにのみ集中します。スクラッチの真ん中に残っている転位はごくわずかです。このゾーンの空孔は、転位反応によって生成されます。また、転位反応と変形双晶によって生成された点欠陥空孔が見出されます[88]。
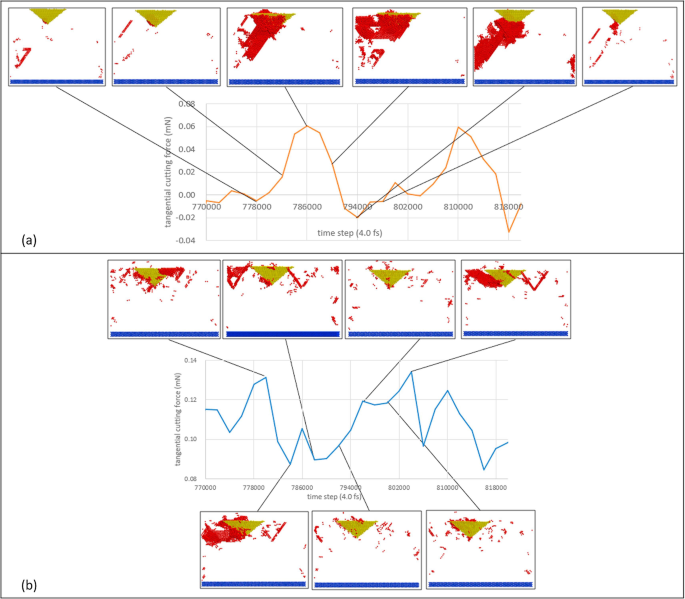
a でのスリッププロセス 動的耕起と b 静的耕起[19]
多結晶材料の場合、変形メカニズムは、結晶粒内部の転位核形成と多結晶材料の粒界転位によって媒介されていました[43]。転位の伝播は、粒子サイズが大きい場合はナノボイドと格子間クラスターの形成に関連しており、結晶粒界での双晶の形成は、クラスターが小さい場合に支配的でした。この挙動は、引っかきプロセス中に転位の動きが滑らかな(大きな粒子)から粗い(小さな粒子)に移行したことに起因していました。 Liはさらに、単結晶Cu、多結晶Cu、およびNT多結晶Cuに関する材料変形メカニズムの違いを結論付けました。結果は、塑性変形が主に単結晶Cuのスクラッチプロセス中の転位間の相互作用によって影響を受けることを示しています。一方、多結晶Cuの場合、転位とGBの両方が塑性変形を支配します。塑性変形は、転位、粒界(GB)、および双晶/双晶を伴う双晶境界(TB)の相互作用によって制御されます[25]。
さらに、多くの研究は、シリコン、炭化ケイ素、ガリウムヒ素、窒化アルミニウムなどの半導体材料でのTBNプロセスのMDシミュレーションに焦点を当てていました。これらの脆性材料を調査するために、相変態は転位すべりに加えて重要な変形モードでもあります[89]。転位と相変態の相互作用は、結晶方位によって異なります。結果は、「ポップイン」イベントの前に、Si(010)は、Si(110)では発生しないSi-IからSi-III / Si-XIIへの相変態を伴う非弾性変形を受けることを示しています。およびSi(111)。一方、Si-Iからbct-5への相変態は、各結晶方位の初期塑性の主要なメカニズムであり、転位核形成は、Si(010)の弾塑性転移における動作変形モードでもあります。ダイらTBNプロセス中の単結晶シリコンの表面下損傷メカニズムを調査しました。結晶相の進展は、静水圧応力と温度の分布と一致していることがわかります[40]。 SiCも重要な半導体材料の一種であり、シリコンと同様の性質を持っています。 SiC材料の除去プロセスは、亜鉛ブレンドから、六角形のダイヤモンド構造がほとんどないアモルファス構造への相間移動によって実現されます。より高いスクラッチ速度は、より大きな衝突とより短い再配列時間のために、より多くのアモルファス構造原子、より少ない六角形のダイヤモンド原子、およびより少ない転位原子を生成します[90]。 Meng etal。相転移が主要な変形メカニズムではない場合、シュミット係数法はTBNプロセス中の3C-SiCの滑り運動(弾性滑り運動と転位滑り運動)を効果的に予測できます[79]。さらに、Meng etal。 SiCの除去メカニズムに対するひずみ速度と熱の影響についてさらに研究しました。彼らは、ひずみ速度効果と熱軟化効果が、材料除去量と表面下損傷(SSD)の形態に直接影響することを発見しました。高ひずみ速度条件下での加工領域の応力に対する熱軟化効果の影響は、転位発生速度の成長速度の低下の影響を上回っている。多結晶SiC除去プロセスは、アモルファス相転移によって支配されます。さらに、いくつかの六角形のダイヤモンド構造の原子と転位が、引っかきの間にGBに見られます。より高い引っかき速度とより深い切り込みは、より大きな衝撃により、より多くの原子がアモルファス構造に移動するのを促進します[81]。単結晶SiCと比較して、多結晶の微細構造は、通常の引っかき力とアモルファス構造の相転移を生成し、塑性変形によって引き起こされるSSDを薄くすることにより、SiCをより柔らかくします[91]。転位の伝播と相転移の分析は、機械加工プロセスのメカニズムを説明することができます。ただし、単結晶材料や複雑な構造の材料に焦点を当てたほとんどの研究はほとんど報告されていないため、さらに調査する必要があります。
将来の研究の方向性と課題
現在、MDシミュレーションによるTBNプロセスの研究が広く報告されています。ただし、考慮すべきいくつかの制限があります。したがって、今後の方向性については、このレビューで説明します。
- (1)
TBN法の開発に伴い、この分野でいくつかの新しい技術が提案されています。たとえば、AFMチップベースのナノミリングプロセスは、その優れた機械加工性能とサイズ制御特性により、幅広い展望があります[92、93]。しかし、検出装置の制限により、ナノミリングのメカニズムは完全には理解されていません。 MDシミュレーションを使用することで、切削抵抗の変化、欠陥のダイナミクスの変化、およびチップの回転プロセス中の被削材の除去状態が期待されます。さらに、サンプルの振動支援ナノスクラッチ法はまだ報告されていません。 MDシミュレーションアプローチは、早い段階で意味のあるガイダンスを提供する可能性があります。
- (2)
長さと時間スケールの制限のため、MD法はまだ実験プロセスを定量的に完全に説明することができませんでした。実験とMDシミュレーションを組み合わせたいくつかの研究では、MDシミュレーションアプローチは実験現象を定性的にしか説明できませんでした[19、20、94]。特に、アモルファスポリマーなどの一部の時間依存材料の場合、プローブの速度はポリマーの除去状態に大きな影響を与えます。したがって、実験プロセスを正確に予測し、実験結果を定量的に分析するには、アルゴリズムと計算能力の向上が不可欠です。
- (3)
TBN法[95,96,97]を使用して、ポリマー材料上で多くのナノ構造が実現されています。特に、TBN法に基づくポリマー材料の機械加工プロセスは、機械加工されたナノ構造の精度を保証するために、通常の負荷を一定に保ちます[98]。ただし、TBNプロセスにおけるポリマーのMDシミュレーションの報告はこれまで限られています。さらに、熱走査プローブリソグラフィーはポリマーで開発されており、TBNプロセスの加工精度を向上させる可能性があります。機械的熱的効果を伴うナノスケールの引っかきプロセスを行う場合、ポリマー材料の材料除去メカニズムを明らかにする必要があります。
結論
MDシミュレーション技術がナノマシニングプロセスにおいてますます重要な役割を果たし、これまで知られていなかった現象を明らかにすることは否定できません[99]。このレビューは、TBN法のMDシミュレーションにおける最近の進歩を結論付け、上記の内容は以下のように要約されます。
- (1)
さまざまな材料のMDモデルの確立と関連する潜在的な機能が要約されました。特に、NT多結晶材料とアモルファスポリマーのモデリングプロセスについては、このセクションで説明しました。 MDモデルの精度は、その後のシミュレーション結果にとって非常に重要です。
- (2)
マルチスクラッチ、ダイナミックプラウ、VANILAなどのTBNメソッドの新技術が紹介されました。 MDシミュレーションの助けを借りて、これらの方法のメカニズムをよりよく理解することができます。特に、静的耕起と動的耕起の本質的な違いは、内部欠陥、形態、および切断力の観点からMD法によって明らかにされました。
- (3)
切削抵抗、材料除去の状態、欠陥分析など、TBNプロセスでのMDシミュレーションの分析も要約されています。その上、滑り分析のようないくつかの新しい分析方法も与えられます。これらの方法では、TBNアプローチに基づく処理メカニズムが見直され、TBN加工プロセスへの材料の依存性が示されます。
略語
- TBN:
-
チップベースのナノマシニング
- AFM:
-
原子間力顕微鏡
- MD:
-
分子動力学
- NT:
-
ナノツイン
- PE:
-
ポリエチレン
- EAM:
-
埋め込み原子法
- SW:
-
Stillinger-Weber
- ABOP:
-
分析的結合次数ポテンシャル
- REBO:
-
反応性の経験的結合次数
- AIREBO:
-
適応分子間反応性の経験的結合次数
- LAMMPS:
-
大規模な原子/分子の大規模並列シミュレータ
- MS:
-
マテリアルスタジオ
- OVITO:
-
視覚化ツールを開く
- VMD:
-
視覚的分子動力学
- VANILA:
-
緩い研磨剤による振動支援ナノインパクト加工
- SEM:
-
走査型電子顕微鏡
- CNA:
-
一般的なネイバー分析
- CSP:
-
中心対称性パラメーター
- DXA:
-
転位抽出アルゴリズム
- GB:
-
粒界
- TB:
-
ツインバウンダリー
- SSD:
-
地下の損傷
ナノマテリアル
- Nano and Battery Anode:A Review
- 農業生態系におけるバイオセンサーとナノセンサーの応用に関するレビュー
- ナノチャネルにおける油輸送に対する表面効果:分子動力学研究
- セリウムのダイヤモンドカッティングの分子動力学モデリングとシミュレーション
- 新規ナノ粒子増強ワーム状ミセルシステムの研究
- コンドロイチン硫酸-メトトレキサートナノゲルの抗腫瘍研究
- 分子動力学法によるアブレシブナノメートル切削プロセスに及ぼす衝撃方向の影響の研究
- 分子動力学法を用いた金基板上のグラフェンのナノスケール摩擦挙動の研究
- ヨウ素末端アルカン単一分子接合の低トンネリング崩壊
- <100>引張荷重下のタンタル単結晶の弾性特性の温度および圧力依存性:分子動力学研究
- 新しい調査では、米国の製造業における生産性のダイナミクスと推進要因を調査しています