PtFSを使用したRAPM開発
このブログは、2020年5月の特集「複合材料のコストパラダイムの革命、パート2:成形」のオンラインサイドバーであり、ボーイング社が主導するRApid高性能製造(RAPM、「ラップエム」と発音)プログラムについて説明しています。 (シカゴ、イリノイ州、米国)、DARPAのTailorable Feedstock and Forming(TFF)プログラムの「フォーミング」部分であり、小型で複雑な形状の複合部品の迅速、低コスト、俊敏な製造を可能にします。
RAPMプログラムの3つの材料およびプロセストラック(樹脂注入、熱硬化性プリプレグ、熱可塑性成形)にはすべて、Surface Generationが提供し、ボーイングR&TにあるProduction to Functional Specification(PtFS)ピクセル化加熱制御およびツーリングシステムを使用した試験が含まれていました。セントルイス(下の表を参照)。
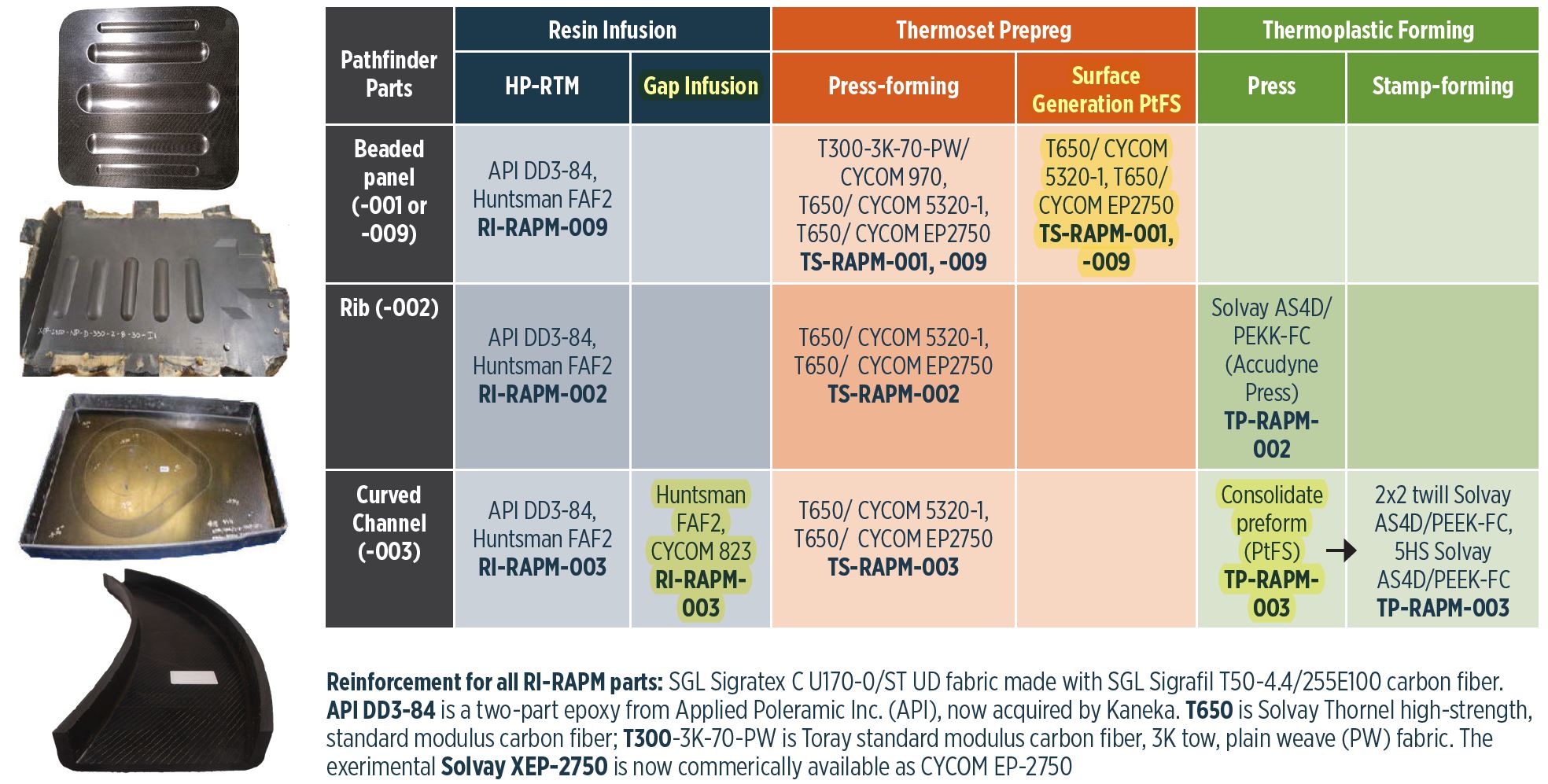
PtFSは何年もの間商品化されていることに注意してください。このブログは、PtFSシステムを使用したRAPMのプロセス開発に関するものです。このブログの参照は次のとおりです。
- 2019 SAMPE(5月20〜23日、ノースカロライナ州シャーロット)テクニカルペーパーおよびスライドプレゼンテーション、Steven M. Shewchuk 1 による「フレキシブル複合材料製造ワークセル用のスケーラブルな動的制御アーキテクチャの開発」 、ベンハルフォード 2 、Michael P. Matlack 1 、Andrew Sharpe 2 とピートマッセイ 2 。 1 ボーイング社、ミズーリ州セントルイス、米国 2 Surface Generation Ltd.(英国、ラトランド)。
- 2020 SAMPEテクニカルペーパー、「複雑な熱硬化性ラミネートの圧縮成形」、Travis R. Adams、Timothy J. Luchini、Jared B. Hughes、Steven M. Shewchuk、Adam Martinez、Gail Hahn、ボーイング社。 >
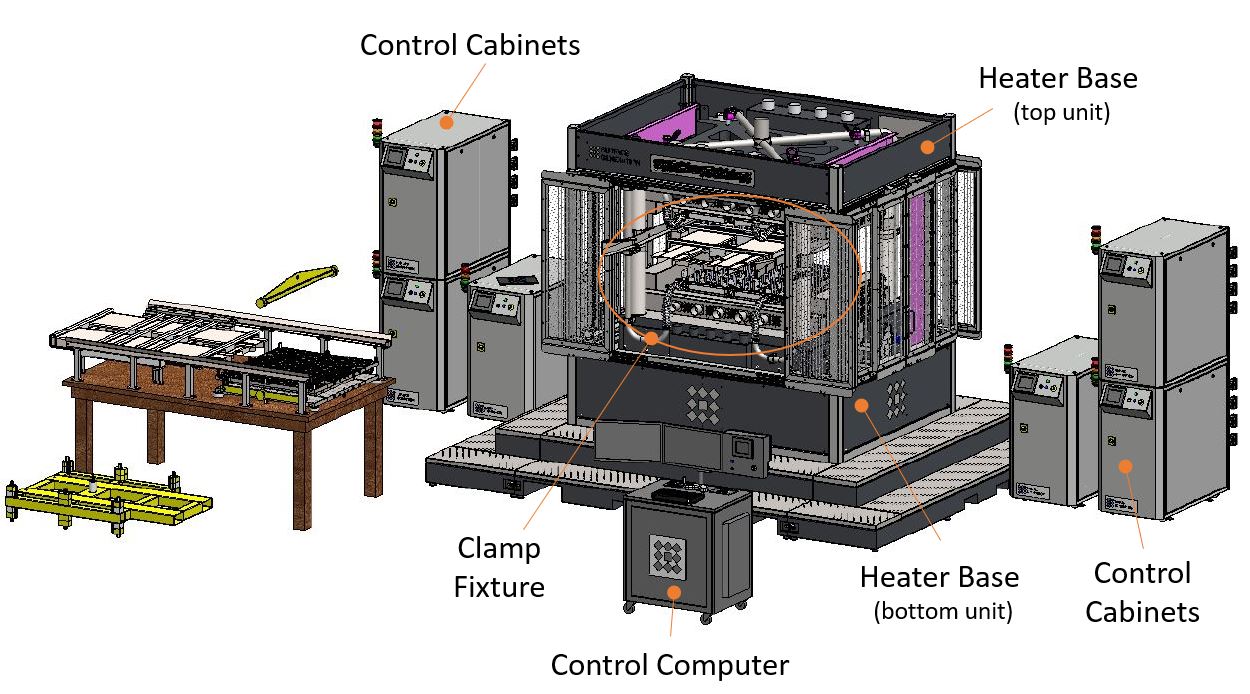
PtFSシステムコンポーネント
PtFSシステムはモジュール式であり、完全にスタンドアロンにすることも、既存のインフラストラクチャの一部を使用することもできます。圧密/圧密圧力の場合、システムは既存の油圧プレスまたは油圧作動式ツールクランプフィクスチャを使用できます。ボーイングセントルイスのPtFSセルには、後者の150メートルトンのクランプ固定具が装備されています。 表面生成によって設計されました。この成形セルは、750 x 750 x100ミリメートルの部品体積に対応します。
ボーイングセントルイスPtFSセルには、位置と圧力の制御が含まれています。 「SurfaceGenerationのOrchestratorソフトウェアは、CF-OaO-RAPM PtFSワークセルを制御するために使用されます」と、ボーイングのテクニカルフェローでRAPMプログラムマネージャーのGailHahn氏は述べています。 「各ツールは、変位と圧力の調整を通じてシステム内で校正されます。圧力校正は、ツールが処理中に受けると予想される圧力に油圧を調整するために実行されます。ツールの分離と変位のキャリブレーションは、ツールの開閉位置と低速/高速のクローズ領域を設定するために実行されます。これにより、手動および自動制御中にツール面が保護されます。」位置測定は4つのストリングポテンショメータで完了します、とボーイング複合材料エンジニアおよびRAPM研究者のスティーブンシューチュクは説明します。 「それぞれがクランプ固定具のガイドポストに配置され、プラテンの位置を測定し、操作中にプラテンラックを識別するための安全な方法を提供します。圧力制御は、クランプ固定具の油圧ポンプにフィードバック制御を提供する単一のインライン圧力トランスデューサーで完了します。」
クランプフィクスチャの上下には、上部と下部のヒーターベースユニットがあります。 。これらにはすべての加熱/冷却コンポーネントが含まれており、制御キャビネットからの出力に応じて動作します (ボーイングのセットアップでは、ヒーターベースごとに3つのキャビネット)。ツール面はヒーターベースごとに設計されており、レールとローディングシステムを使用して取り付けられています。
各ツール面は、各ツール面の下側に向けられ、ディフューザーを介して分散される圧縮空気を使用して加熱および冷却されます。 一致する金属工具面の各セット 180個の個別に制御可能なヒーターチャンネルに分割されています —上部のツール面の場合は90、下部の場合は90。ヒーターチャネルは、各ツール面を横切るグリッドで10.0センチメートルの間隔で配置されています。各チャネルには、ヒーター、2ステージの圧縮空気源、および2つのフィードバック熱電対があります。 ツール面の裏側との密接な接触を確実にするためにバネ仕掛けになっています。 RAPMツール面の加熱には、ヒーターチャネルごとに1立方フィート/分の圧縮空気が使用され、冷却には3立方フィート/分が使用されました。
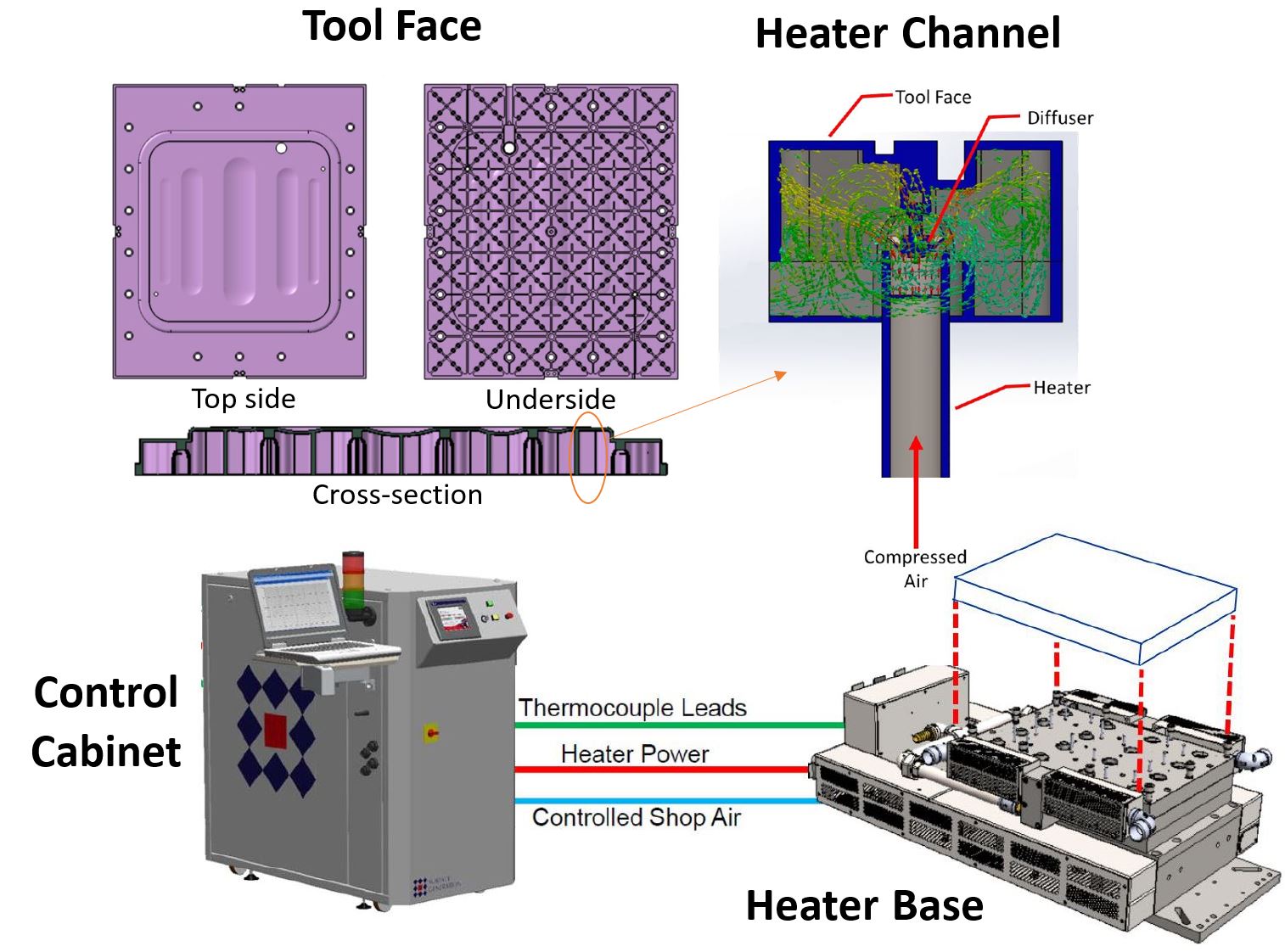
ツール面
RAPMの工具面は、工具鋼から約3ミリメートルの厚さに機械加工されました。 TS-RAPM-001-201の下部ツール面は、上の図の左上に示されています。ツール面の上部は標準のスタンプ形成ツールのように見えますが、下部には加熱チャネルがあります。
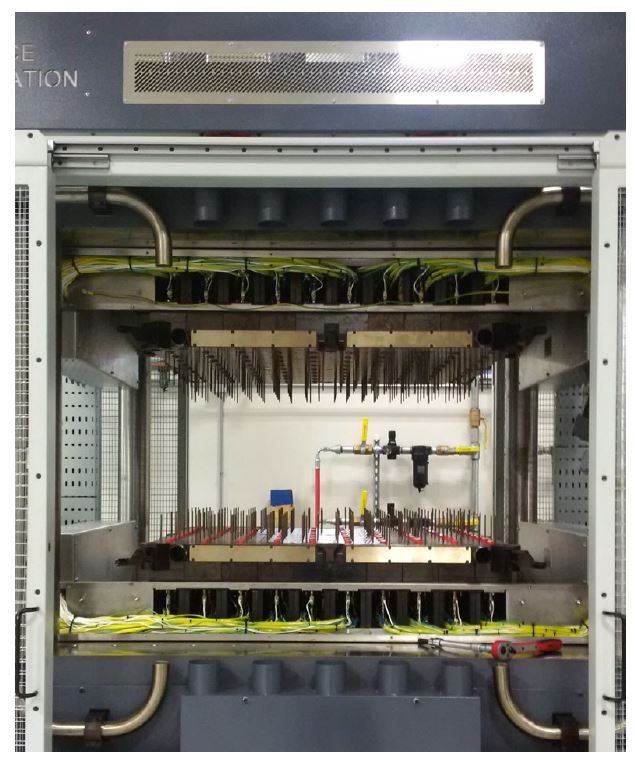
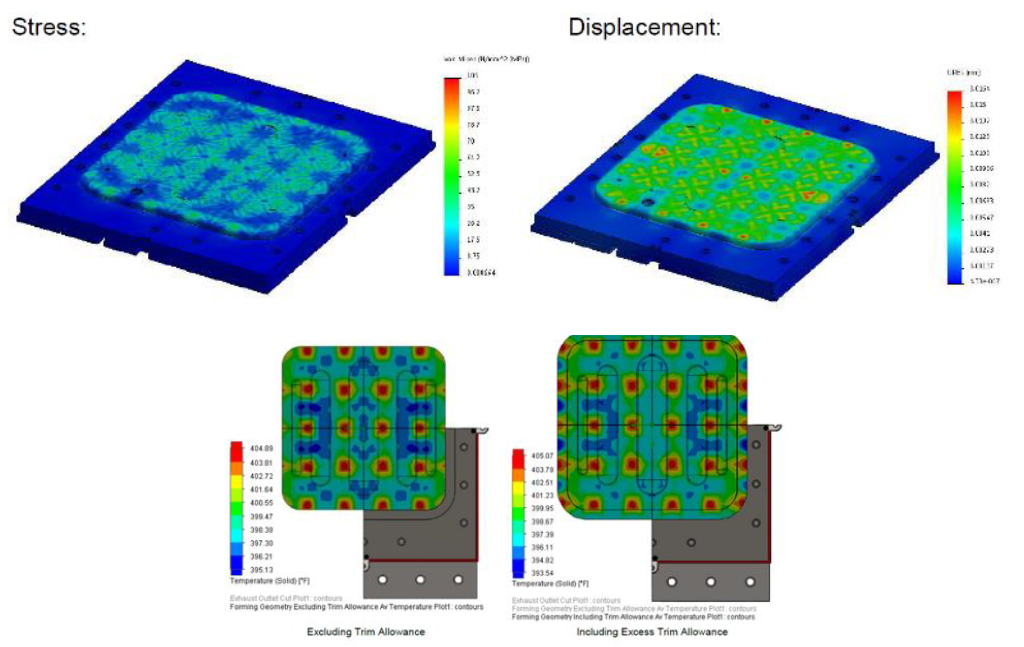
許容可能な形状の工具面は、同じヒーターベース用に設計された他の工具面と交換できます。ツールには、同じヒーターチャネルの寸法、おおよその熱電対の配置、およびバネ仕掛けの熱電対の移動範囲内に収まる深さが必要です。
ツール面を変更するために使用されるレールローディングシステムは、180個のスプリング式フィードバック熱電対すべてをツール面の裏側のスリーブに位置合わせします。ピンは工具面を整列させ、正確なフォークリフト制御なしで工具のロードを実行できるようにします。ツールの交換は、ツールの面を額縁に分解および再組み立てするなど、2人のオペレーターが2〜4時間で完了できます。
熱質量を減らし、加熱および冷却速度を向上させるために、可能な限り多くの材料が機械加工されます。このため、RAPMで使用される各ツール面では、ツール面が処理温度と圧力に耐えられるかどうかを判断するために、構造有限要素解析(FEA)が必要でした。ツール面は、線形および非線形FEAと、定常状態および過渡的な計算流体力学(CFD)熱解析を使用して最適化されました。後者は、均一な工具加熱を保証するのに役立ちました。温度の均一性を改善するために、各ヒーターチャネル内のツールの厚さとエアディフューザーの両方が変更されました。 FEAとCFDの間の反復ループにより、形状を調整して、工具面のサポートに必要な安全率を満たしながら、目的の工具面の温度を維持することができました。
暖房ゾーンと温度制御
ヒーターチャネルは通常、ゾーンにグループ化され、ゾーンごとのヒーターチャネルの数がパーツごとに指定されます。各ゾーンには加熱プロファイルが関連付けられており、必要に応じてゾーン内およびゾーン間に許容誤差を設定できます。これにより、各ゾーンのすべてのヒーターは、ヒーターの電力レベルと圧縮空気の流量を動的に変化させることにより、規定の加熱プロファイルに従って温度を加熱、冷却、または維持できます。
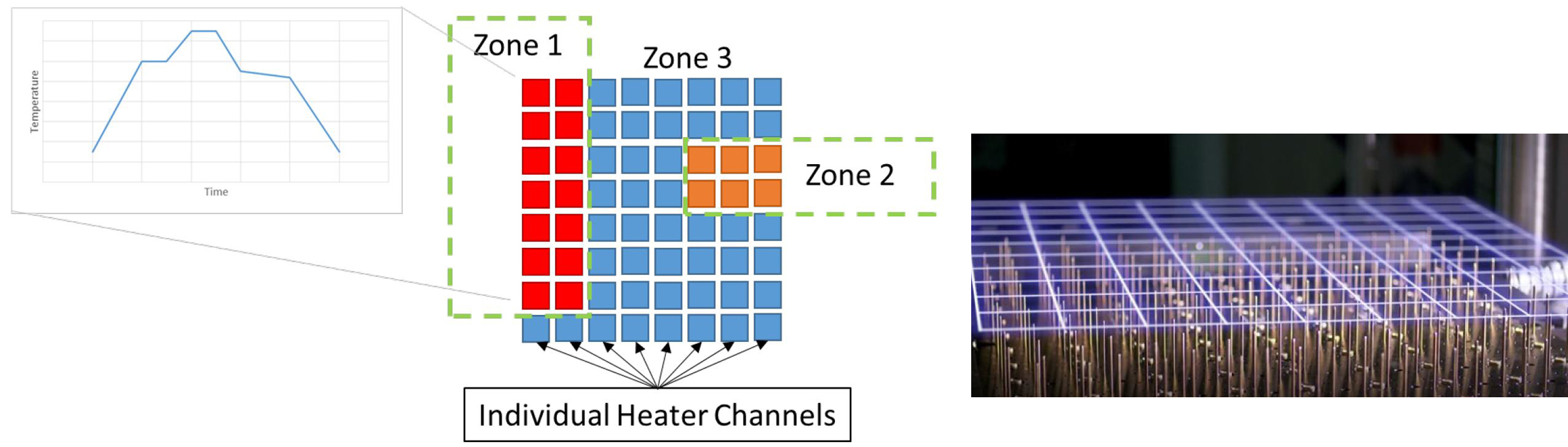
PtFS機器制御ソフトウェアには、さまざまな加熱シナリオに合わせて調整できるアナログとデジタルの両方の加熱戦略がありますが、RAPMセルはアナログ制御を使用します。これには、目標温度でのヒーター電力レベルを決定するためにシステムを自動調整する必要があります。各ヒーターの電力レベルは、加熱/冷却ランプ中のオーバーシュートまたはアンダーシュートを防ぎ、温度設定値を維持するように設定されています。オートチューンは、指定された各温度でのすべてのヒーターチャネルの修正された比例積分微分制御法の定数値を自動的に決定します。自動調整が完了すると、ゾーンごとに加熱プロファイルを書き込むことができます。すべての熱プロファイルは、複合部品が目的の設定値の±5.5°C(±10°F)以内の温度にさらされていることを確認するために検証されました。
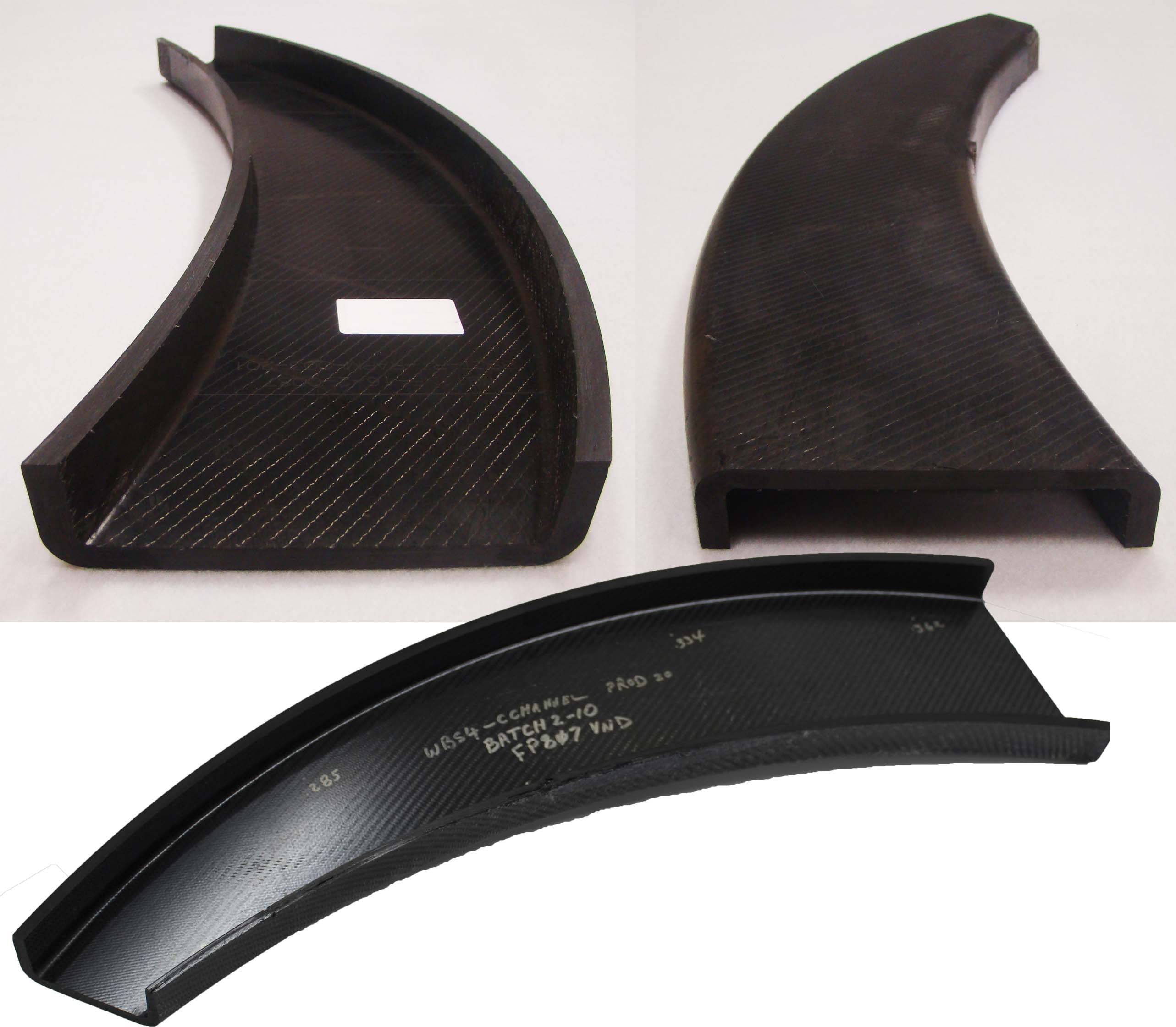
ボーイングPtFSセルの最高温度は440°Cです。当初、ボーイングが1日に複数の高温サイクルを処理していたとき、処理サイクル間の冷却不足のために特定のコンポーネントが損傷する可能性があるという懸念がありました。ただし、冷却システムは2019年9月から10月にアップグレードされ、熱抽出用の追加ファン容量が含まれています。この改善された冷却により、セルは440°Cで継続的に処理できます。
冷却方法として大量の周囲温度の圧縮空気を使用した場合、ツール面の冷却は温度範囲の上限近くでは高速でしたが、60°C(140°F)に達すると大幅に遅くなりました。熱可塑性温度(> 350°C)に加熱している間、工具面の温度は平均41°C /分(74°F /分)で上昇しました。同じ実行の冷却中、ピーク平均冷却速度は36°C /分(65°F /分)でした。冷却に圧縮空気を使用すると、より継続的な冷却ランプが提供され、アクティブな熱管理(つまり、必要に応じて加熱)と組み合わせて、冷却中の温度はかなり直線的に保たれました。
等温TSプリプレグスタンピング
PtFSワークセルを使用した最初の部分の試験は、熱硬化性プリプレグ圧縮成形(スタンピング)で作られたTS-RAPM-001ビーズアクセスカバーパネルを対象としたものでした。このパーツのツールは、RAPMPtFSワークセルの180チャネルのうち112チャネルを占有します。これには、上部ツール面の56チャネルと下部ツール面の56チャネルが含まれます。ただし、実際の部分はそのツール全体をカバーしているわけではなく、ツール面の上下にある56個のチャネルのうち30個しかカバーしていません。次の図は、RAPM-001部品に使用される78個の熱電対(TC)の配置を示しています。両方で同じ配置で、上面が39、下面が39です。 TCの数は、セルごとに1つ(ヒーターチャネル)と、CFD熱分析で特定された高温領域と低温領域の追加のTCで構成されます。
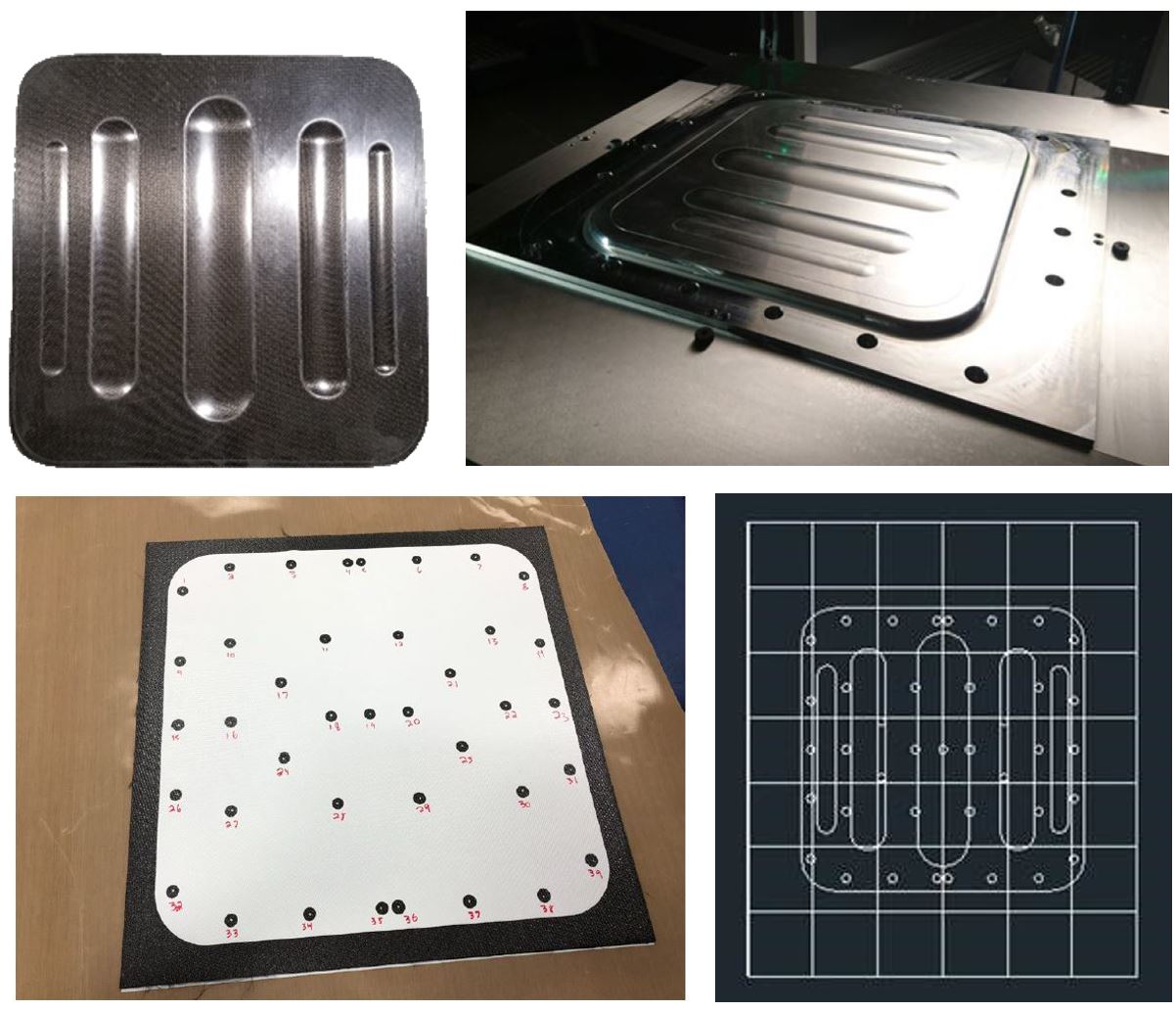
空のツール面の温度均一性をテストし、16層の炭素繊維織物/エポキシラミネートの中間点に熱電対を埋め込んだ後、テストを繰り返しました。複合材料が追加されると、複合材料が熱伝達経路として機能するため、ツール面の温度分布がより狭くなります。また、複合ラミネート内の温度均一性は、ツール面の読み取り値よりも厳しかった。実行1の単一のTC (下の図、右側のグラフの上部を参照) 目的の温度範囲を超えて振動したのは部品の端の近くであり、部品のトリムラインの外側にある隣接するセルの温度変動が原因であると考えられます。
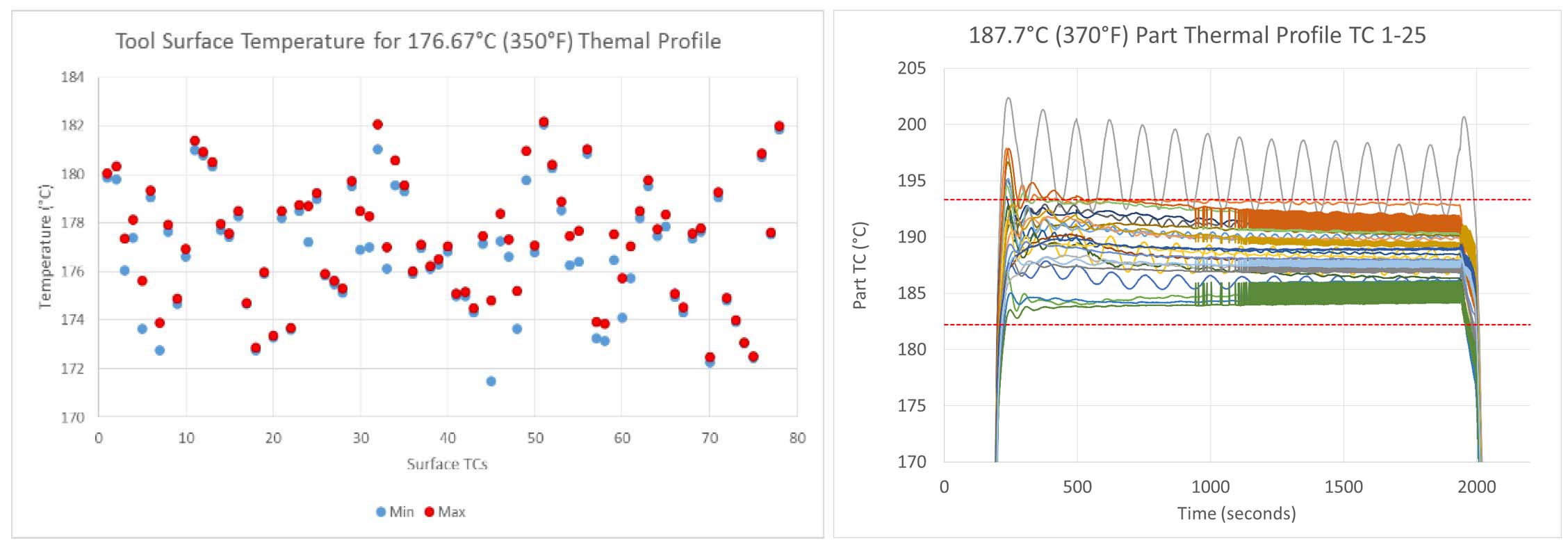
処理の等温圧縮成形により、ツールは±5.5°C(±10°F)の許容範囲内で176.7°C(350°F)に保たれました。 TS-RAPM-001の場合、次のシーケンスに従いました。
- アプリではシステムが187.7°Cに加熱されます。 8分
- ホットツールにロードされた複合ブランク
- ツールは12:09に閉じられました(例)
- ツールからゲルコンポジットまで30分
- 最初の圧力段階:樹脂の絞り出しを最小限に抑えながら、ブランクを最初に急速に加熱します
- 第2圧力段階:良好な圧密を確保し、ボイドの成長を防ぐために、300psiまで上昇させます
- 後硬化のためにホットツールから「グリーン」コンポジットを除去します
このプロセスは、現在の複合プロセスよりも高品質の部品を実現し、サイクルタイムの短い部品を実証しました。より高いプロセス温度は、複合材料をさらに速くゲル化する可能性がありますが、材料の劣化や発熱のリスクを引き起こす可能性もあります。 PtFSツールは、従来の大きな熱質量を使用して発熱を吸収するのではなく、低熱質量ツールの裏側を積極的に冷却して発熱を放散するため、これは懸念事項でした。
PtFSセルは、TS-RAPM-012の「ウェーブ」チャレンジパーツの作成にも使用されました。以前の開発試験を使用して、177°Cで30分の等温サイクルを使用してこれらの部品を硬化し、続いて同じ温度で2時間のポスト硬化を行うことが決定されました。ただし、以前の試験との違いには、より積極的な形状と、オートクレーブ外の航空宇宙部品の標準であるCYCOM 5320-1エポキシを使用した準等方性レイアップと、8ハーネスのサテンおよび一方向の炭素繊維層と外側の層が含まれていました。片面にスタイル108のガラス織物。 RAPM PtFSコントローラーは、適切な粘度が得られるまで、ラミネートに最小限の圧力を加えるようにプログラムされています。この最初のステップの後、硬化を完了するために最終圧力が加えられました。 1つの試行はオーブンで後硬化され、残りは試行間の時間を短縮するためにPtFSクランプ固定具で後硬化されました。複数の高品質部品が製造されました。
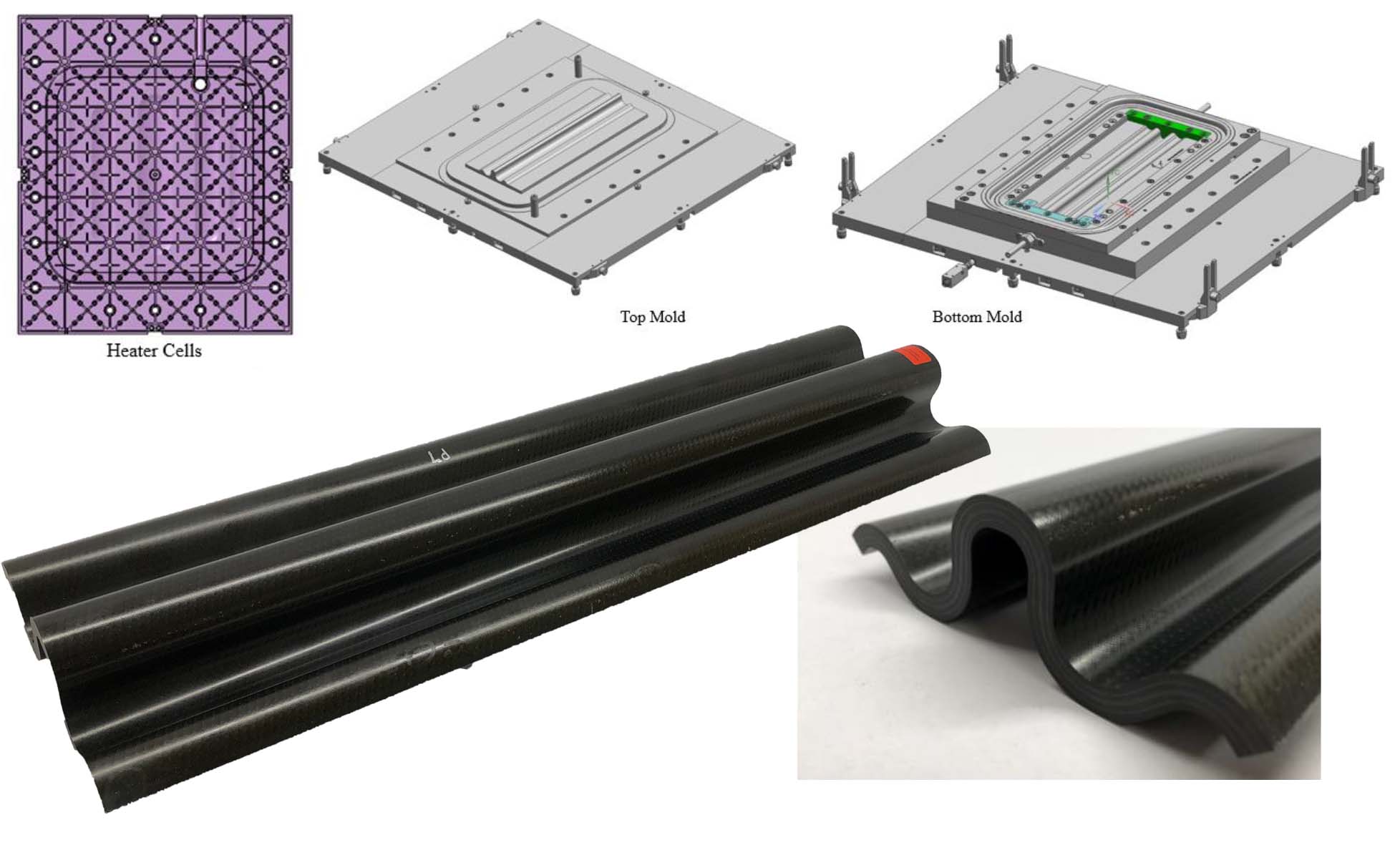
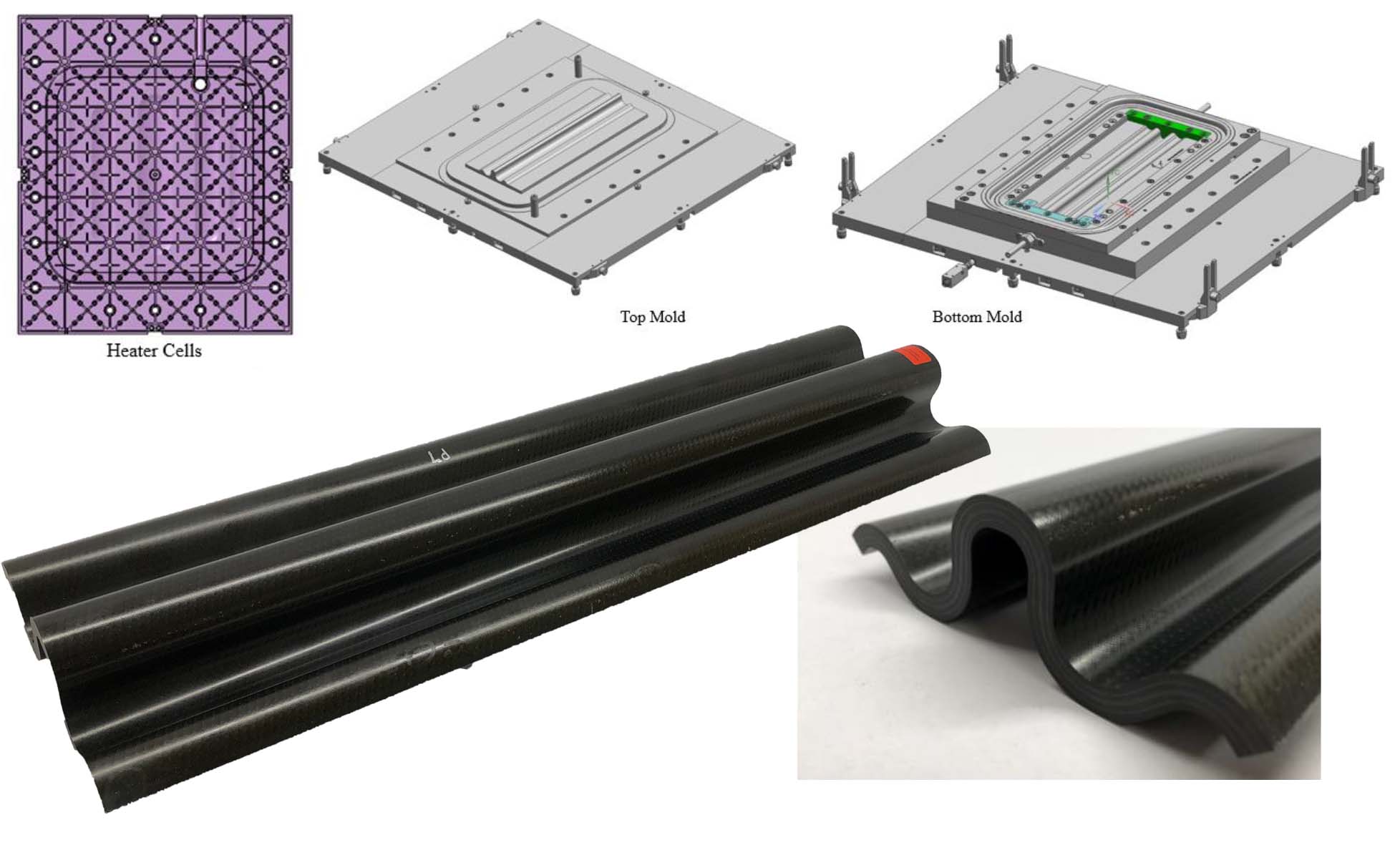
樹脂注入の動的温度サイクル
PtFSワークセルを使用したレジン注入部品の試験は、RI-RAPM-003湾曲Cチャネル部品から始まりました。 3つの異なるエポキシ樹脂システムが最初に試されました:
- Solvay CYCOM 823、80°で注入された後、125°Cで滞留するように傾斜します
- ハンツマンFAF2(クイックキュアシステム)を100°Cで注入し、150°Cで滞留させます
- Applied Poleramic(現在はKanekaが取得)API DD3-84(クイックキュアシステムでもあります)を60°C、滞留温度160°Cで注入。
非圧着布プリフォームを注入し、2°C /分で指定された滞留温度まで上昇させた後、60分間保持してから冷却しました。速硬化性樹脂の場合、発熱反応が進行すると、PtFSは特定の工具領域にアクティブ冷却を自動的に適用して、特定の部品温度を維持しました。
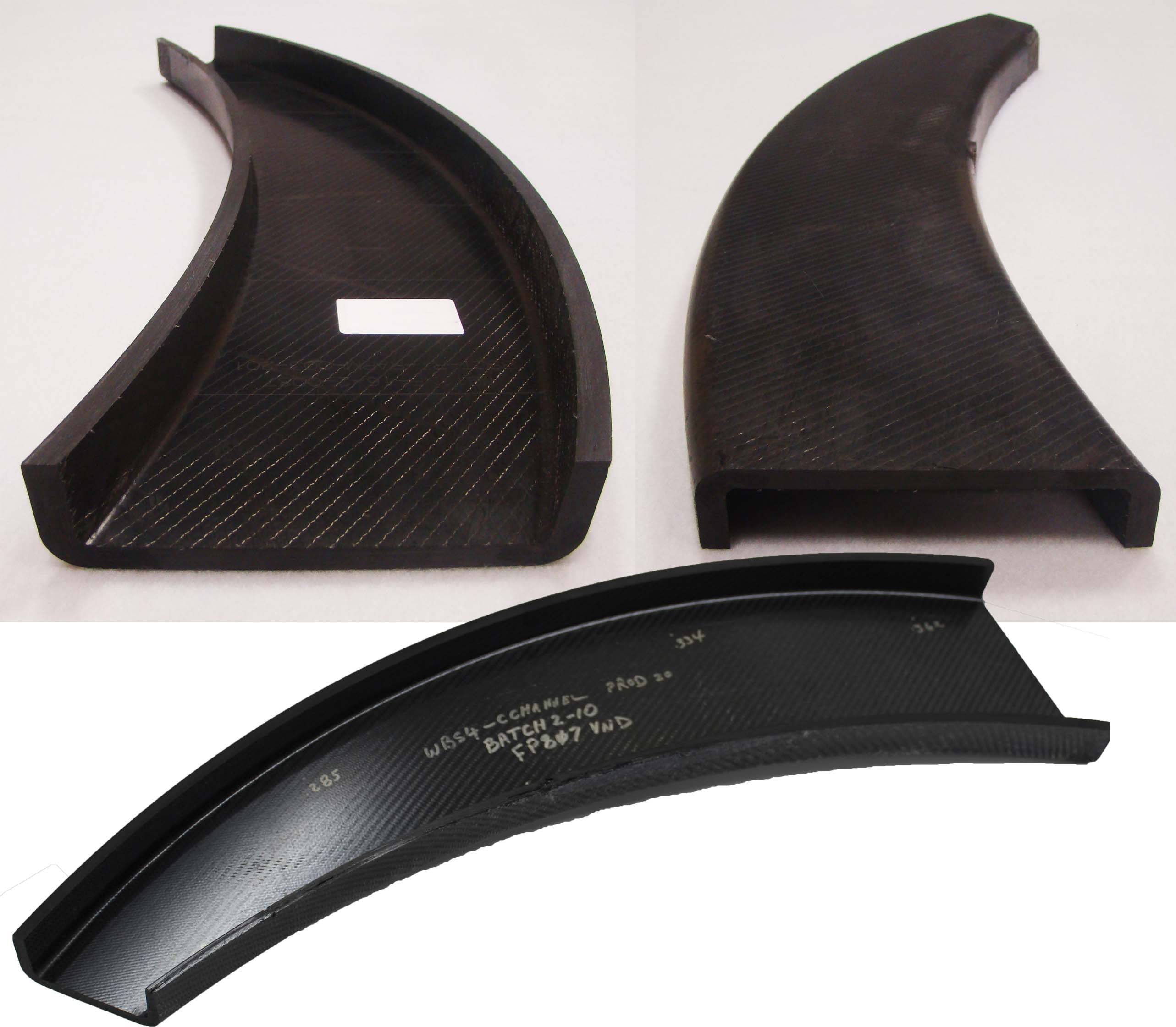
PtFS装置は、RI-RAPM-003部品のギャップ注入法をサポートするための位置制御も提供できました。この方法では、ツールを真空ガスケットの初期の高さまで閉じ、注入中にツールを1.3ミリメートル開いたままにしておくことができました。注入が完了した後、ツールを残りの距離で閉じて、樹脂をz方向にプリフォームに押し込みました。このプロセスを使用して部品が正常に作成されました。
熱可塑性スタンピングの動的温度制御
PtFS装置は、熱可塑性複合材料でRAPM-003湾曲Cチャネルを作成するためにも使用されました。具体的には、部品の長さに沿って32から24プライに落下した複雑なプリフォームを、断面が先細りの平らなブランクに統合するために使用されました。次に、統合されたブランクはATC Manufacturing(Post Falls、Idaho、U.S。)に送られ、最終部品に垂直フランジがスタンプされました。
TP-RAPM-003湾曲Cチャネル用に統合された材料は、ポリエーテルエーテルケトン(PEEK)で粉体塗装された炭素繊維2x2ツイル生地でした。 PtFSワークセルを使用して、熱可塑性樹脂のチャージ上でAZ31マグネシウムブラダーを超塑性成形し、ブラダーを加熱して、アプリで400°CのPEEKプロセス温度にチャージしました。 55分。
この成形温度で、アルゴンガスがブラダーに適用され、熱可塑性複合材料に圧密圧力が適用されました。次に、セルはブラダーを冷却し、30分でPEEK結晶化温度未満に充電し、合計サイクル時間は3時間になります。
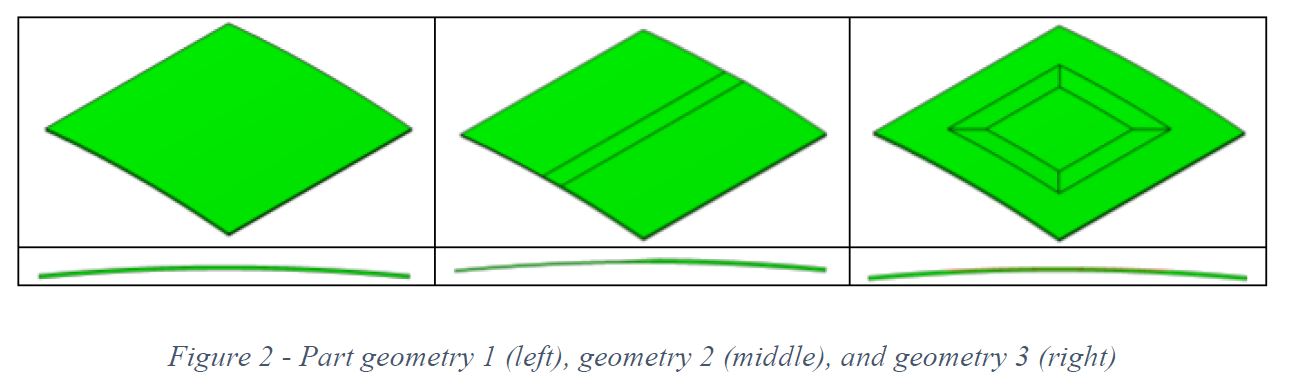
上のスライド11は、ブラダーの超塑性成形および熱可塑性プラスチックの固化中に加えられた圧力の進行を示しています。ブラダーが超塑性成形温度に達した後、冷却によって維持された20psiから140psiに増加します。プリフォームは正常に統合され、ATC Manufacturingに送信され、そこでパーツがこの非常に困難な形状にスタンプされました。
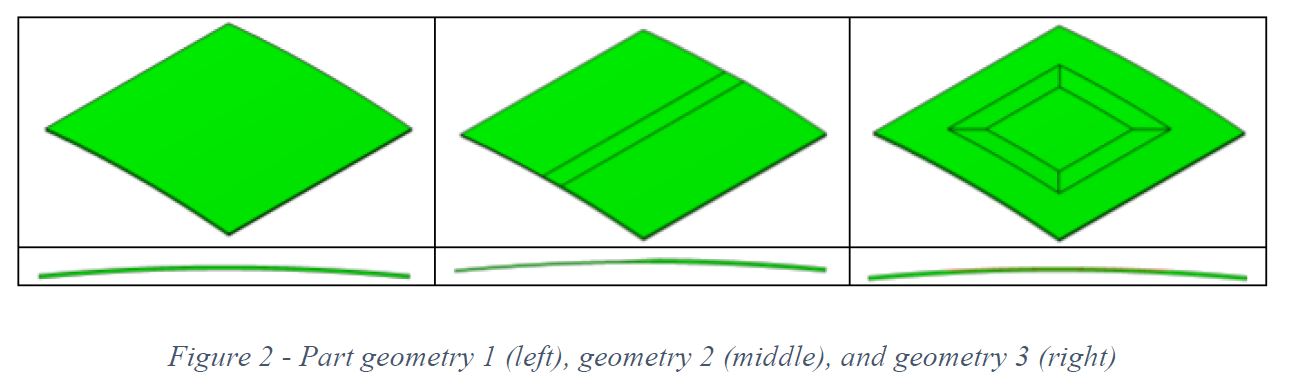
PtFSセルは、さまざまなオプションの研究において、一方向(UD)炭素繊維/ポリエーテルケトンケトン(PEKK)テープのバランスのとれた対称的なレイアップから作られたTP-RAPM-017パネルのワンステップブランクからパーツへのスタンピングにも使用されました部品の特徴は膀胱形成に影響を与えます。 TP-RAPM-017パネルのサイズは40.6x 40.6センチメートルで、高さ1.3センチメートルに達する緩やかな輪郭があります。 3つの異なる部品形状(フラット(プライドロップなし)、一方向プライドロップ、額縁)を評価しました。厚い領域に32プライ、薄い領域に16プライ、その間に20:1のプライドロップ比があります。パーツサイクル時間は、すべてのジオメトリで1.5時間でした。
ツール面は、UD熱可塑性複合テープの熱膨張に最もよく一致するようにインバー42から機械加工されました。 UDテーププライキットをカットして照合し、超音波溶接して硬化ツールに入れ、385±15°Cに加熱しました。さまざまな圧力サイクルをテストし、パーツを220°C未満に冷却した後、圧力を解放してパーツを離型しました。
ジオメトリ1の圧力サイクルの一例は、室温で20 psiであり、遅れている熱電対が溶融温度310°Cに達した後、140 psiに上昇し、部品の熱電対が220°C未満で測定されるまで圧力下で10°C /分で冷却されました。 。 20 psi、30 psi、50 psi、および70psiの初期圧力を試しました。圧力ランプも、最大圧力140 psiまで、毎分10psiから15秒あたり10psiまで変化しました。
注目すべき結果の1つは、プライが超音波で仮付け溶接された場合、すべてのパネルでCスキャンの結果が不十分であったことです。したがって、最良の結果を得るには、このような仮付け溶接をパーツネットトリムラインの外側に配置する必要があります。許容できる部品が製造されましたが、一部の部品はプライの端で不十分な固結を示しました。これは、加熱する前に初期圧縮圧力を30psiに上げることで改善されました。ただし、この圧力の上昇により、成形品のブラダー側に表面粗さ/マット仕上げが発生しました。また、50および70 psiの初期圧縮圧力を使用して作成された一部のジオメトリ2パネルでは、パーツの中央にシワが見られました。これらのより高い圧力により、処理中にプライが互いにすべり合うのを防ぎ、部品のしわを閉じ込めた可能性があると考えられていました。
試みられた別のバリエーションは、ブラダーを加圧するためにアルゴンガスをより安価な窒素ガスに置き換えることでしたが、これは、クロススキャンで多孔性が検出されなかったにもかかわらず、表面粗さ/マット仕上げを含む部品品質を低下させ、Cスキャン結果でより高いレベルの減衰を引き起こしました。セクション。
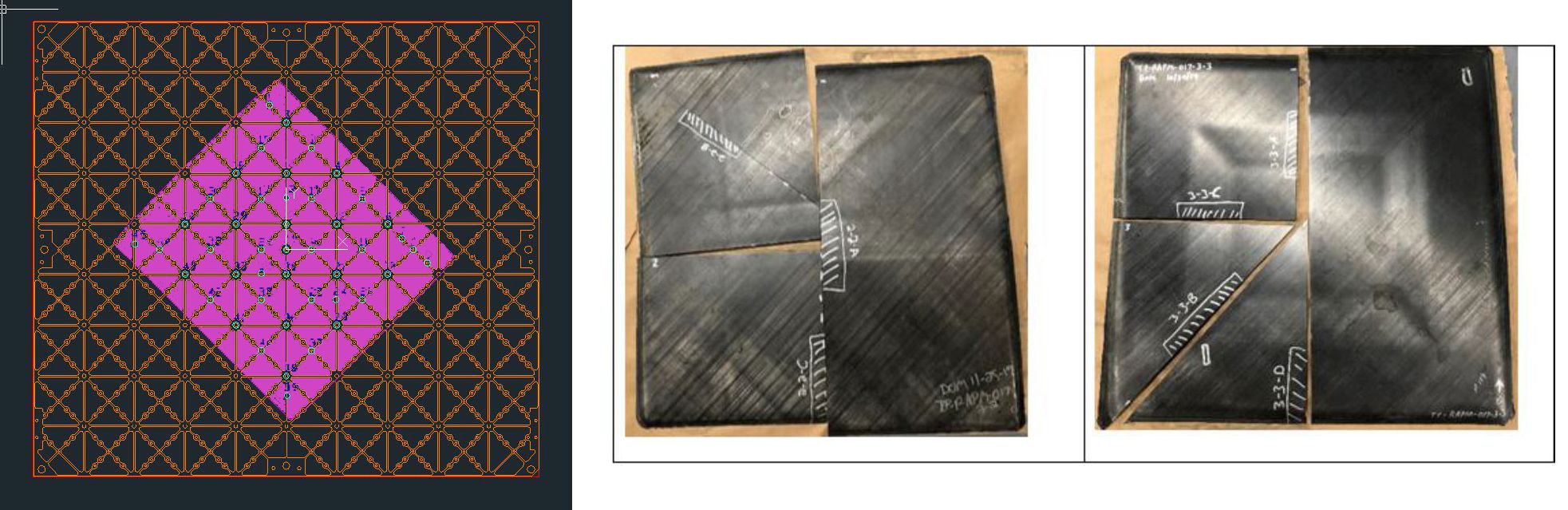
RAPMでのPtFSの長所と短所
PtFSワークセルは急速な加熱を示しました(約180°Cでのエポキシ硬化の場合は10分未満)。自動化された工具交換と組み合わせると、これにより部品の迅速な切り替えが可能になり、短い製造工程での複合部品のコストを削減できます。 PtFSは、(等温部分サイクルとは対照的に)高温動的実行にも適しています。
ボーイングセントルイスPtFSセルの機能は、RAPMプログラム中に大幅に向上しました。これは、熱均一性とクランプ固定具制御を改善するためのソフトウェアアップグレードの改善、冷却能力と熱電対制御の改善、および自動プレスクレーブ圧力制御システムのおかげです。各ヒーターチャネル設定値、ヒーターパワーレバー、圧縮空気レベルなど、システムによって毎秒生成および記録される膨大な量のデータを使用することで、さらに機能を向上させることができます。このデータに機械学習を適用すると、部品の品質とプロセスの改善。さらにソフトウェアを強化することで、このデータで、必要な過剰なエネルギーや特定のツール位置の応答性の低さなどの処理の異常を特定できるようになる可能性があります。
「PtFSは、その名前が示すように、多くのカスタマイズを提供します。生産から機能仕様へ」とハーンは言います。「しかし、そのカスタマイズには、新しいツール/部品構成のためにシステムを確立して「調整」するための時間の投資が必要になる場合があります。」 RAPMの機械加工された金属工具面の設計のほとんどは、英国のSurface Generationによって作成されました。ただし、BoeingとSurface Generationは、米国の工具設計者と米国の工具メーカーを「トレーニング」して、金型面の設計が米国で実施できることを実証しました。サーフェス生成以外のソースによる。そのツールのモールドフェースであるCMD-TP-RAPM-008-503は、TP-RAPM-008-203ショートファイバーアクセスパネルの作成に使用されています。
「ツールや部品の何らかの形の温度制御はすべての複合材料部品の成形に役立ちますが、実際に必要なのは重要な領域と時間での温度制御であり、これは部品やプロセスごとに異なります。したがって、特定の部品を形成するために実際に必要な温度制御を理解することが重要です。 PtFSの180ゾーンは便利ですが、それぞれがツールに機械加工されたチャネルを必要とするため、コストもかかります。パーツに必要なのが外側と内側のゾーン、またはトリガーポイントジオメトリに沿った特定のゾーンのみである場合は、別のソリューションの方が手頃な価格である可能性があります。ただし、これにより、複数のタイプのプロセスや部品に柔軟に対応できる複合部品製造セルを開発するための最善のアプローチについての議論が始まります。」
ボーイングとDARPAは、2020年にRAPMプログラムを終了し、さらなる結果を発表する際に、この討論に情報を追加し続けます。
樹脂