工業用複合材料製造用のDC誘電体センサー
メーカーが複合部品の製造コストの削減と速度の向上を同時に追求するにつれて、成形プロセスの内部をリアルタイムで確認し、樹脂の流れ、粘度、温度、圧力、Tg /硬化状態を監視する機能が差別化要因になります。 Synthesites(Uccle、ベルギー)はこの能力を開発しました。ドイツ航空宇宙センター(DLR、Stade)とNational Composites Center(NCC、ブリストル、英国)によって報告された結果に基づくと、このテクノロジーは、Tgと程度に基づいて治療法を決定し、サイクルタイムを最大50%短縮する可能性があります。一般的な材料の研究に基づいた、樹脂あたりの硬化と部品対保守的な期間の比較。実際、センサーからのデータを使用してプロセスと機器を制御し、シミュレーションと設計を改善することで、Composites4.0の生産に向けて進歩しています。
私は最初にOPTO-Lightプロジェクトを介してSynthesitesについて報告しました(「熱可塑性オーバーモールド熱硬化性樹脂」を参照)。 、2分サイクル、1セル」)。実際、OPTO-Lightで熱可塑性樹脂を熱硬化性樹脂に結合する機能 レーザーアブレーションされた表面は、圧力、温度、直流抵抗率(DCR)、および誘電分析(DEA)用のインモールドセンサーを使用することで可能になりました。 DCRセンサーはSynthesitesから提供され、DEA用センサーはNetzsch(Selb、ドイツ)から提供されました。どちらも樹脂の電気的特性を測定する誘電センサーです。これらのテクノロジーの歴史と違いについては、以下で説明します。
Synthesitesがさまざまな商業顧客と開発した技術は印象的です。これには、Cシリーズ(現在はエアバス220)の風力ブレードや樹脂注入翼の工業生産が含まれます。また、オートクレーブを含むさまざまな材料やプロセスでも実証されています。 -硬化プレプレグ、樹脂注入、高圧樹脂トランスファー成形(HP-RTM)。

- 抵抗率の最初の低下は、約120°Cへのランプ中の樹脂粘度の低下を反映しています。
- 120°Cでのこの滞留中、樹脂反応と揮発性物質の損失により樹脂の粘度が増加するにつれて、抵抗率が増加します。
- 樹脂を177°Cに加熱すると、抵抗率は再び低下し、最小になります。
- その後、硬化反応が急速に進行するにつれて、抵抗率が急速に増加します。
- 硬化反応が遅くなると抵抗率の増加が遅くなり、硬化反応が完了に近づくと300分後にゼロ勾配に近づきます。
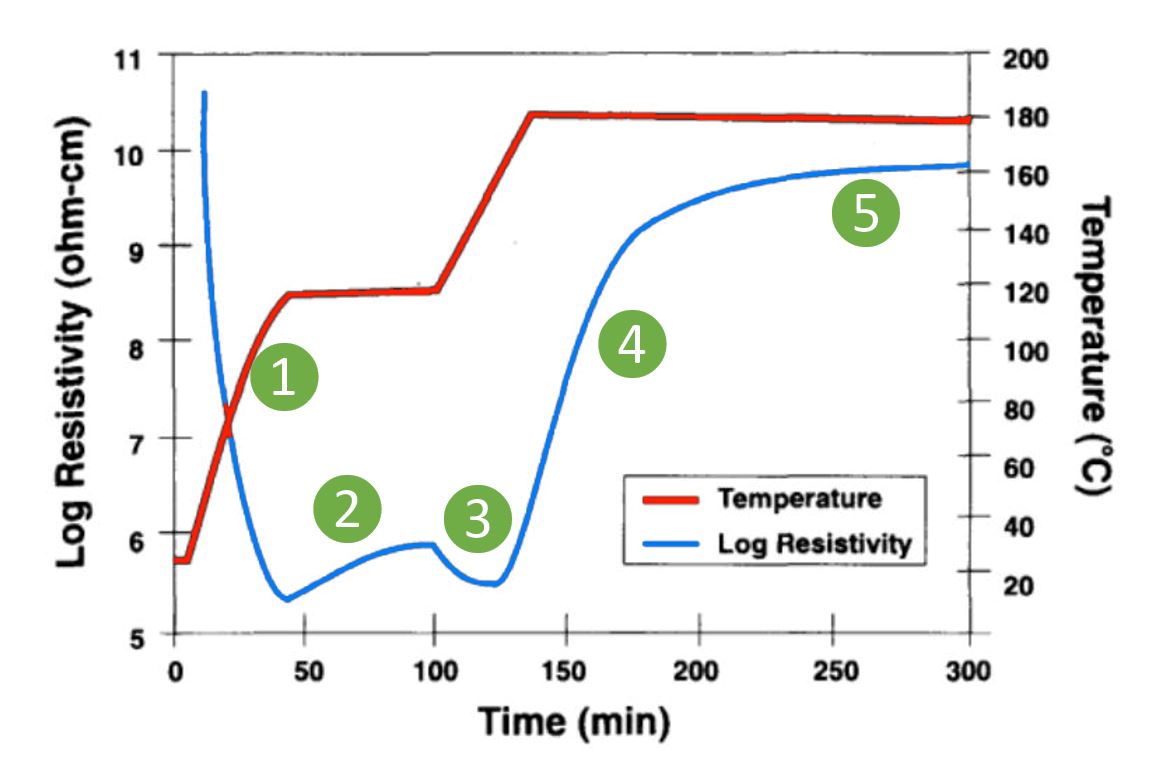
ソース|ロバートE.グリーンによって編集された材料VIIIの非破壊的特性化、p。 385。
イオン伝導度は、ゲル化前の樹脂粘度とゲル化後の剛性(高イオン移動度、低樹脂粘度、低剛性)に反比例します。したがって、イオン伝導率の逆数である抵抗率は、マトリックス樹脂の粘度/剛性の変化に直接関係します。
抵抗率の増加は、Tgの増加と相関することが示されています。これは、直流(DC)を使用したDEAである直流抵抗率(DCR)の基礎であり、Synthesitesが開発したプロセスに最初に与えられた説明です。
上で説明したように、DEAにDC電圧を使用するこの手法は、抵抗率と硬化状態の相関関係に基づいています。これらは、1962年にR.W. Warfieldによって、「電気抵抗率測定によって証明された架橋ポリマーの特性」、高分子化学、で報告されました。 巻58.(このセクションで使用される参照については、下部を参照してください。)
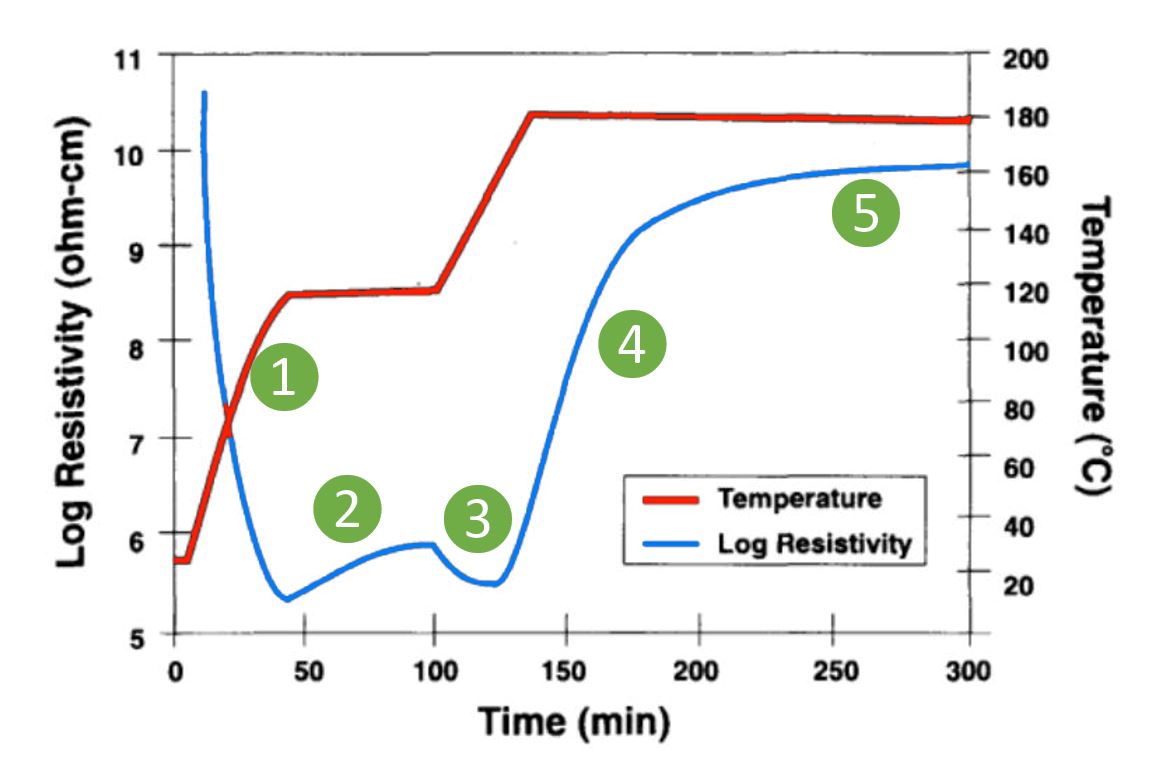
DEAおよびACセンサーとDCセンサーの履歴
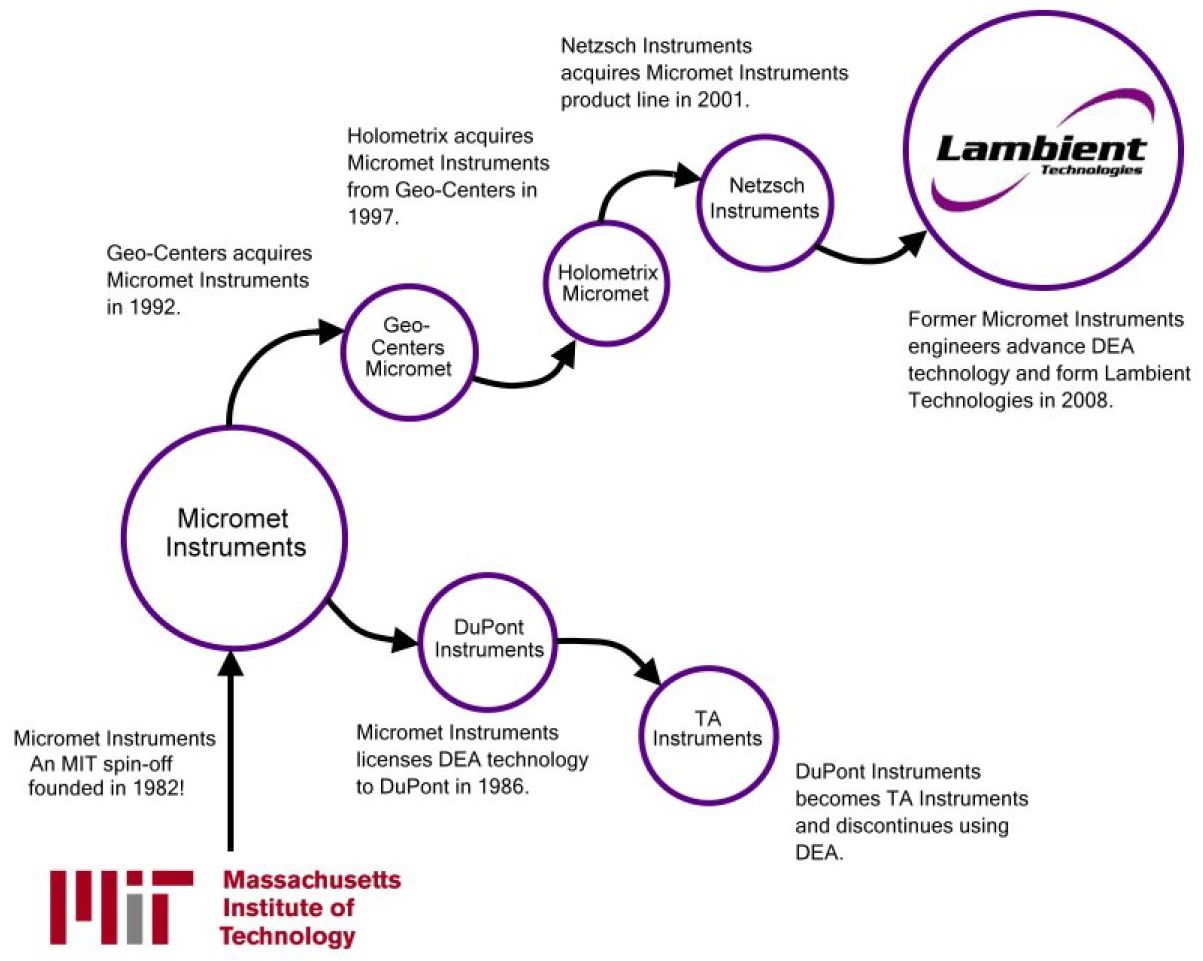
「治療モニタリングの考え方はかなり古いものです」と、SynthesitesのディレクターであるDr. NikosPantelelisは説明します。 「1980年代には、誘電体センシングの方法は、光ファイバーなどの他の方法よりも成熟していると考えられていました。 MIT(マサチューセッツ工科大学)はそれに取り組み、本番環境での実装を試みました。このテクノロジーは、Netzschが今日購入して使用しているものです。」
Synthesitesは2008年に設立されました。「交流ではなく直流の電気センサーを使用してゼロから技術を開発しました」とPantelelis氏は言います。 「私たちにとって、従来のAC誘電体センサーを使用する場合の欠点は、ある範囲の周波数で樹脂を励起してから、さまざまな信号のインピーダンス応答を測定する必要があることです。このすべてのデータを処理するのは難しいだけでなく、樹脂が液体から固体に変化するにつれて、正しい情報を取得するためにさまざまな信号周波数に焦点を合わせる必要があります。」
Pantelelisは、Synthesites DCセンサーは、「硬化中の樹脂の変態を測定するために必要な」非常に低い導電率と高い抵抗率を測定できると述べています。彼は、従来のDEAを1つの周波数でのみ使用して単純化しても、正確なデータが得られないと主張しています。 「複数の周波数はありませんが、定電圧を印加するだけです。欠点は、このアプローチが非常に狭いことです。つまり、樹脂硬化などの非常に特殊なアプリケーションではうまく機能しますが、すべてでは機能しません。ただし、当社の装置の性能を従来のDEAと比較すると、低温でも硬化の全範囲を測定できます。コンポジット以外の機器やサービスを提供している企業は、調整するパラメータが限られているため、私たちのアプローチを好みません。」
Synthesitesは特にコンポジットを対象としているため、これは問題ではありません。 「私たちのアプローチは、熱硬化性樹脂、RTM、プリプレグ、さらにはEliumのような反応性熱可塑性樹脂を含む幅広い複合樹脂とプロセスでうまく機能します。」 (Eliumは、Arkema(Colombes、France)の低粘度熱可塑性プラスチックで、樹脂注入を使用して処理できます。)
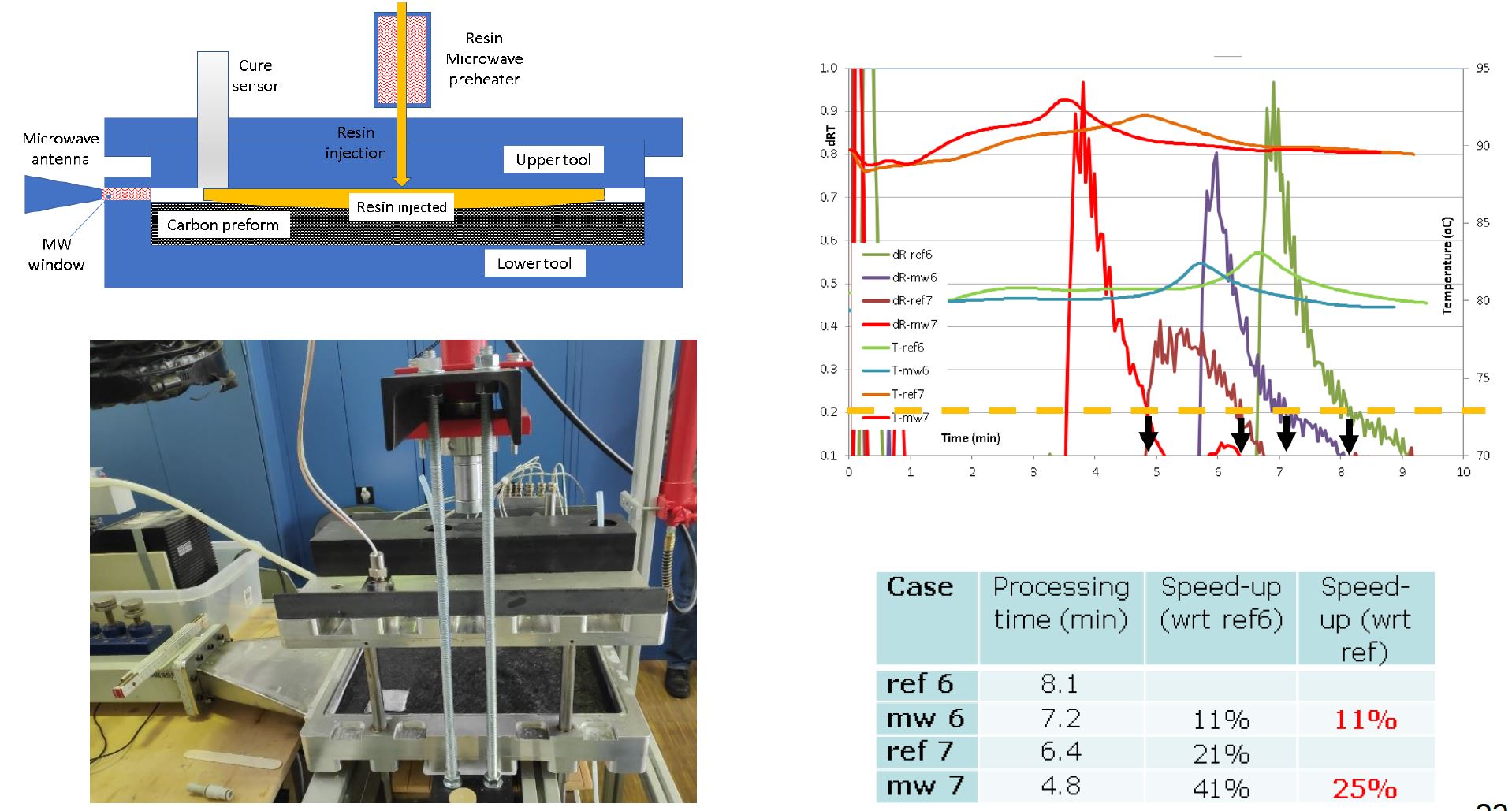
DCを使用するDEAが1960年代に知られていたら、なぜ1980年代にACセンサーが支持され、前進したのでしょうか。 「30年前、DCセンサーを使用するDEAの技術はそれほど開発されていませんでした」とPantelelis氏は指摘します。 「しかし、私たちは工業生産のための非常にスムーズで正確な測定を提供するために私たちのアプローチを進歩させました。 GE Aviation(Batesville and Ellisville、Miss。、U.S。)やBombardierなど、液体樹脂成形で大きな部品を処理しているお客様と一緒に、システムのデモンストレーションと開発を続けてきました。当社のシステムは、風力ブレードの製造にも毎日使用されており、オートクレーブで硬化したプリプレグラミネートの工業生産の能力を実証しています。」
プロセス制御
Pantelelisは、Synthesites DCセンサーが、複合材料の処理と硬化を監視する統合システムの一部にすぎないことを説明しています。 「私たちは抵抗と温度を直接測定し、これからオンライン粘度、ゲル化度、硬化度を計算します。耐久性のあるインモールドセンサーだけでなく、樹脂の入口、出口、フィードライン用のゲートセンサーとインラインセンサー、および部品の使い捨てセンサーも使用しています。センサーは必要な場所でのみ使用します。」
温度センサーは白金測温抵抗体(RTD)であり、熱電対よりもはるかに高い精度(0.1°C以内)を提供し、熱電対で可能な測定ドリフトに対して何年にもわたる安定性を提供します。 RTDは、多くの産業用アプリケーションの標準装備です。ゲートセンサー(以下のプロセス制御図を参照)はバイナリであり、樹脂の流れをオンまたはオフとして報告しますが、粘度を報告できる2番目のバージョンもあります。 Synthesitesは、ガルバニック腐食のリスクのない炭素繊維で使用するセンサー、真空バッグを介して使用できるセンサー、および金型の形状に合わせて成形された金型内センサーを開発しました。
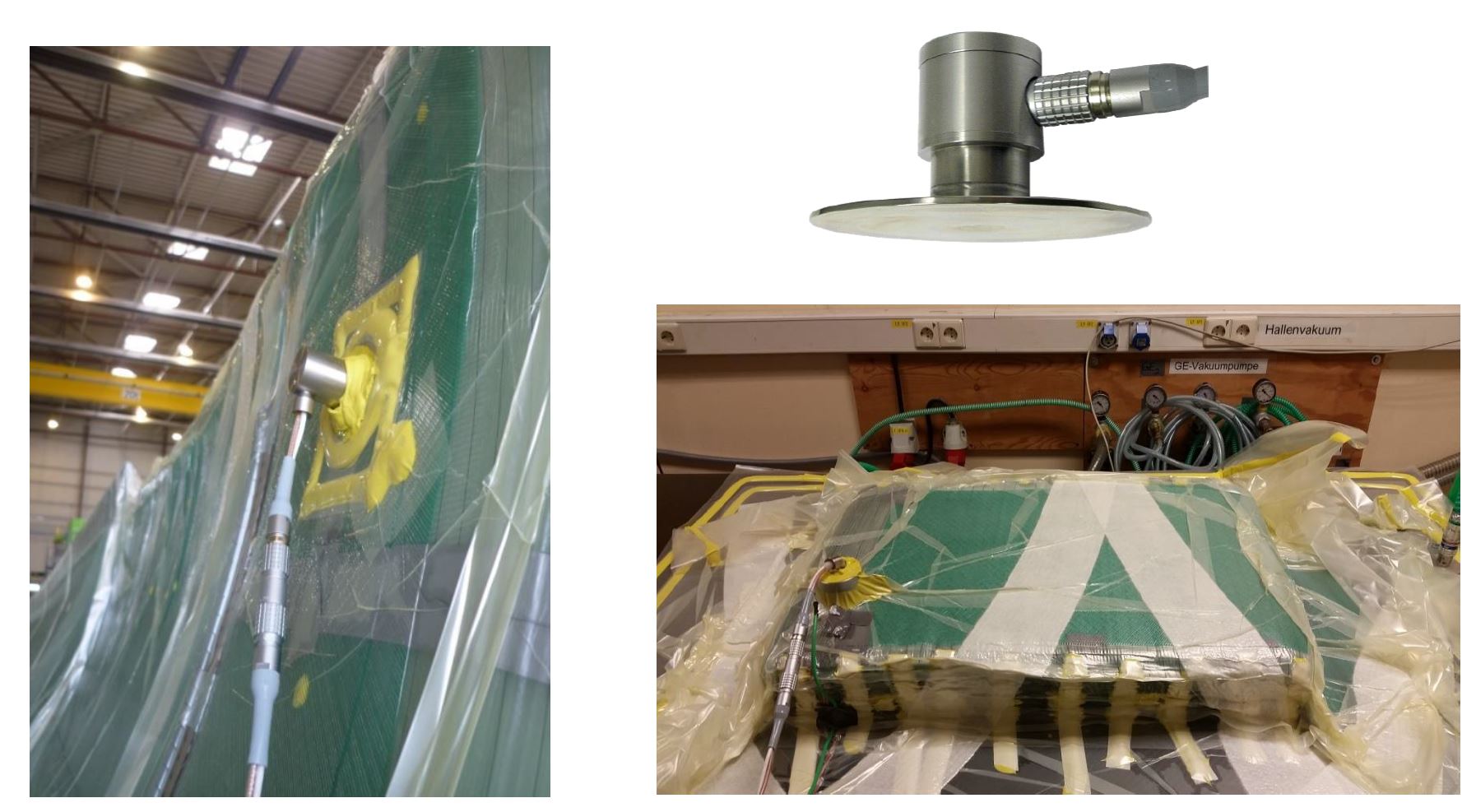
次のコンポーネントは、OPTIFLOWおよびOPTIMOLDデータ取得ユニットです。 OPTIFLOWは、液体複合材料成形用の樹脂の到着と温度をその場でリアルタイムに監視します。樹脂の流れを検証して記録し、樹脂の浸透中の生産偏差を特定できます。 OPTIMOLDは、温度と樹脂抵抗の測定値を使用して計算を行い、混合比、化学的老化、粘度、Tg、硬化度などの樹脂の状態を監視します。プリプレグおよび液体成形プロセスで使用できます。
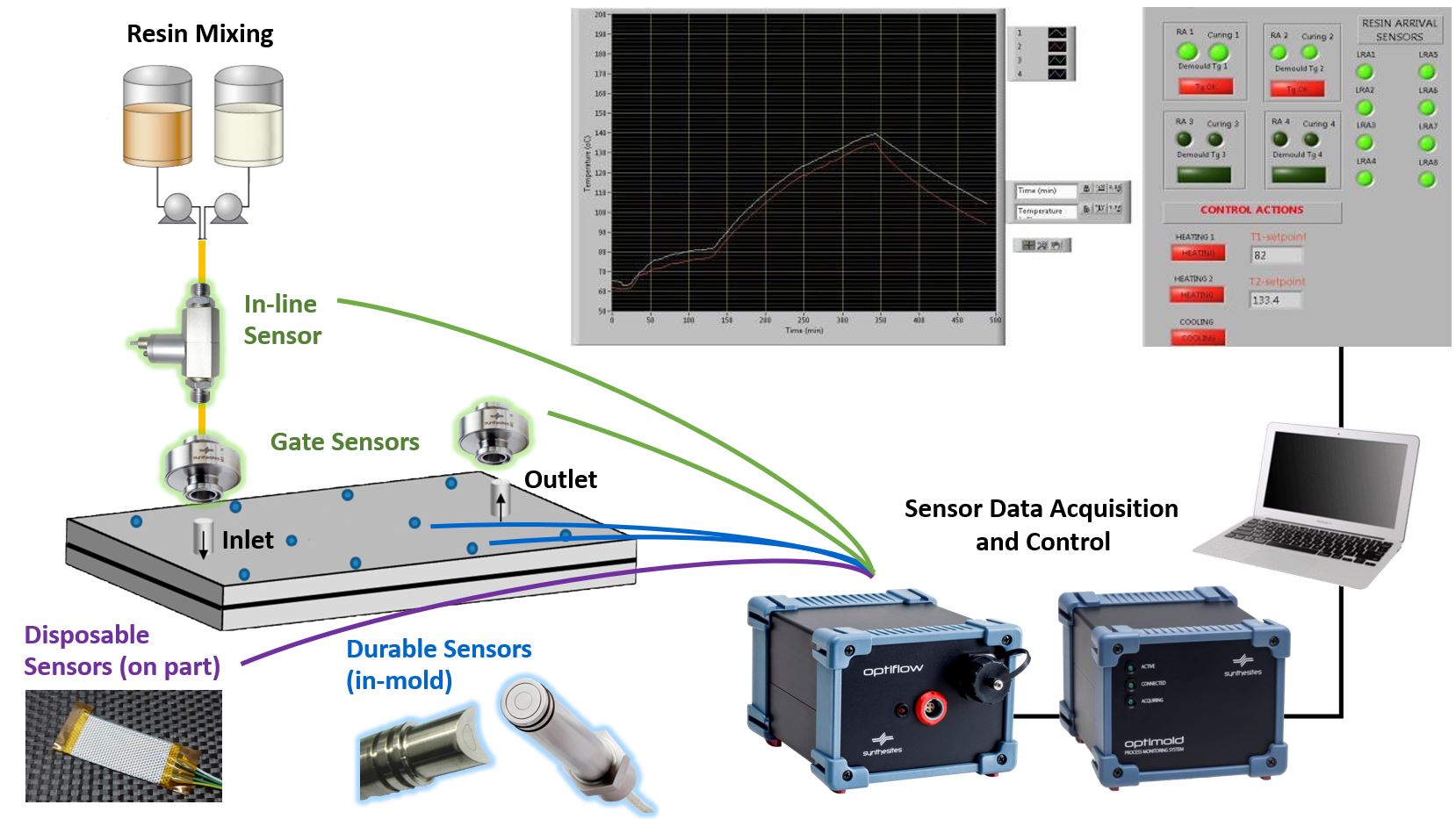
OPTIFLOWおよびOPTIMOLDユニットは、OPTIVIEWソフトウェアによって制御されます。 「このソフトウェアは、データの取得と保存を提供し、当社の機器に無料で提供されます」とPantelelis氏は説明します。 「オンラインレジンステート(ORS)ソフトウェアも提供しています。これは、顧客が追加購入できるより高度なオプションです。入力を収集し、オンライン計算を行い、インテリジェントなプロセス制御のために出力を送信します。」
OPTIFLOWシステムとOPTIMOLDシステムはどちらも、センサーが接続され、読み取り値が範囲内にあることを継続的にチェックします。 「プロセス制御にこれらのセンサーを使用している場合、センサーが機能していない場合、またはセンサーの読み取り値が規定の制限を超えている場合は、システムがアラームを発することが不可欠です」とPantelelis氏は言います。どちらのシステムにも、プロセス機器を制御するためのリレー出力があります。たとえば、樹脂到着データに基づいて供給ラインバルブを開閉したり、樹脂の粘度に基づいて加熱/冷却装置を管理したりできます。 「圧力センサーからの出力をOPTIMOLDに送ることができます。したがって、粘度データに基づいて金型内の圧力を制御できます。」
測定値と一般的なデータ曲線
以下のスクリーンショットは、NCC(ブリストル、英国)での高圧圧縮RTM(HP-CRTM)試験からのOPTIMOLD測定値を示しています。 115°Cでの簡単な試行からの最初のセットは、樹脂の電気抵抗と温度のリアルタイム測定が、ORSソフトウェアによって推定粘度とTgにどのように変換されるかを示しています。
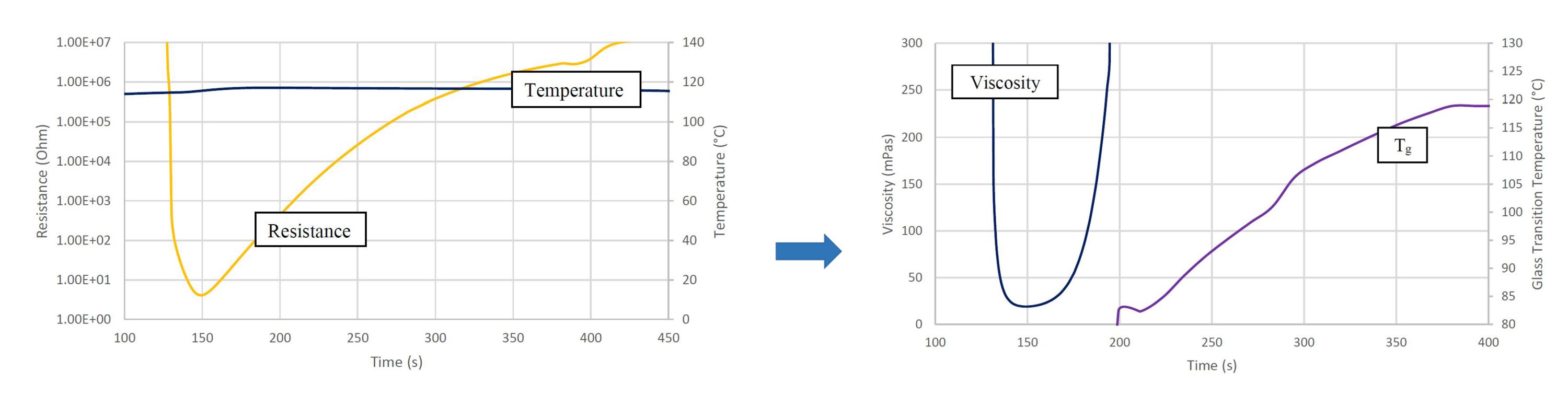
下のグラフでは、電気抵抗と温度(上のグラフ) 110°で記録されました(左) および120°C (右)。 抵抗(R)と温度(T)の読み取り値の下には、110°Cで計算された粘度とTgを示すグラフがあります(左) および120°C (右) 。これらの測定値は、金型の上半分にある2つのOPTIMOLDセンサー(Sn.1とSn.2、下の写真)からのものです。 )2つのキスラー6162A圧力センサー(Sn.3およびSn.4)を使用してキャビティ圧力を記録しました。
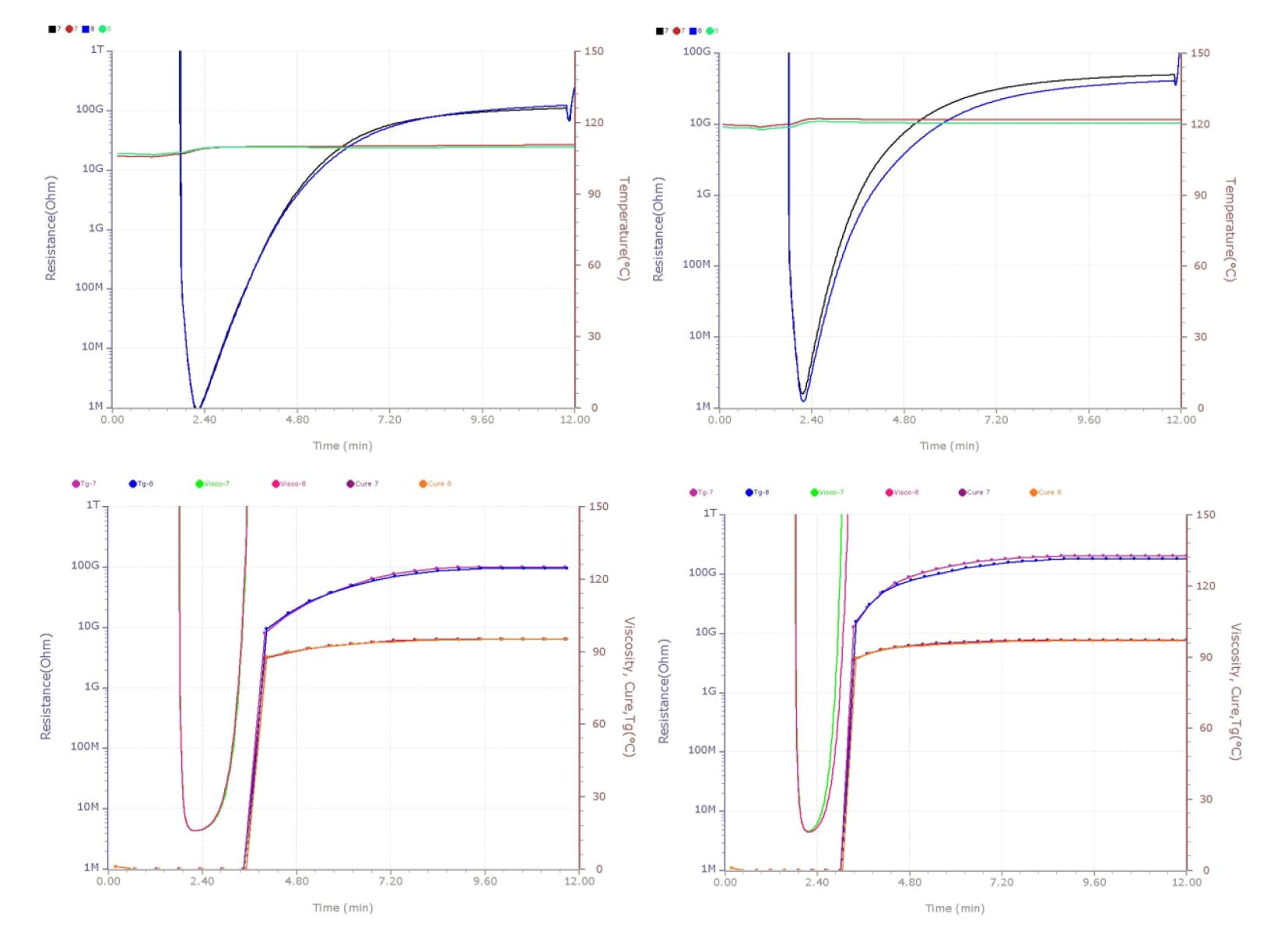
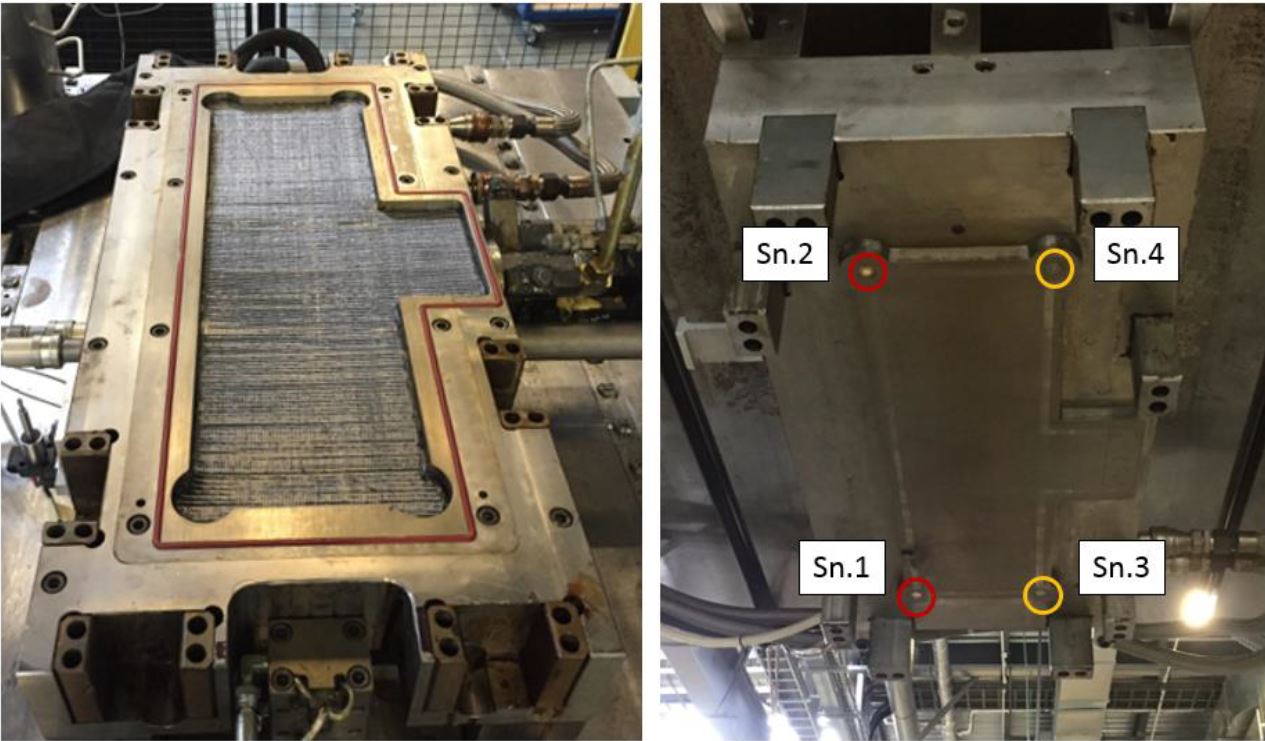
インモールドセンサー、プレスおよび射出装置によって記録されたすべてのデータを1つのログファイルにまとめることができるため、作成された各コンポーネントの製造プロセスの詳細な画像が得られます。
硬化時間の短縮
「メーカーはTgをリアルタイムで確認できるため、硬化時間を30%以上短縮できる可能性があります。そのため、硬化サイクルをいつ停止するかを決定できます」とPantelelis氏は説明します。 「必要以上のレガシーサイクルが完了するのを待つ必要はありません。たとえば、RTM6のレガシーサイクルは、完全に硬化するために180°Cで2時間です。特定のジオメトリでは、これが70分に短縮される可能性があることがわかりました。」
では、目標は、治療が完了したらプロセスを停止することですか? 「それは完全な硬化ではなく、各コンポーネントが必要とするレベルの硬化を達成することです」とパンテレリスは言います。 「完全な硬化には時間がかかりすぎます。重要なのは、十分な治癒がいつ達成されたかを確認できることです。風力ブレードメーカーには目標Tgがあります。それに達すると、冷却を開始できます。したがって、Tgを非常に正確にリアルタイムで測定できるセンサーが必要です。」
Synthesitesは、ハッチンソン(パリ、フランス)との実証プロジェクトを完了し、EUが資金提供するECOMISEプロジェクト(現場構造評価とプロセス調整による次世代複合材料製造の実現、2013年)のためにガラス繊維/エポキシとRTMで作られた自動車用サスペンションブレードを製造しました-2016)。このプロジェクトの目標は、リアルタイムのプロセス監視に基づいてRTMサイクルを最適化することでした。
- 最初の加熱ランプは、センサーに基づく樹脂の浸透が完了するとトリガーされます。
- 2番目の加熱ランプは、Tg計算に基づく硬化の完了によってトリガーされます。
- 冷却は、Tg計算に基づくポストキュアの完了によってトリガーされます。
Synthesitesシステムは、2つのインモールドで構成されていました。 硬化用センサー(CS1、CS2)、1つのインモールド 樹脂の流れと温度用のセンサー(フローセンサー1)と8つの使い捨て 樹脂の流れ/温度用のセンサー— 4つはテスト部品に埋め込まれ、4つはツールの表面に取り付けられています。
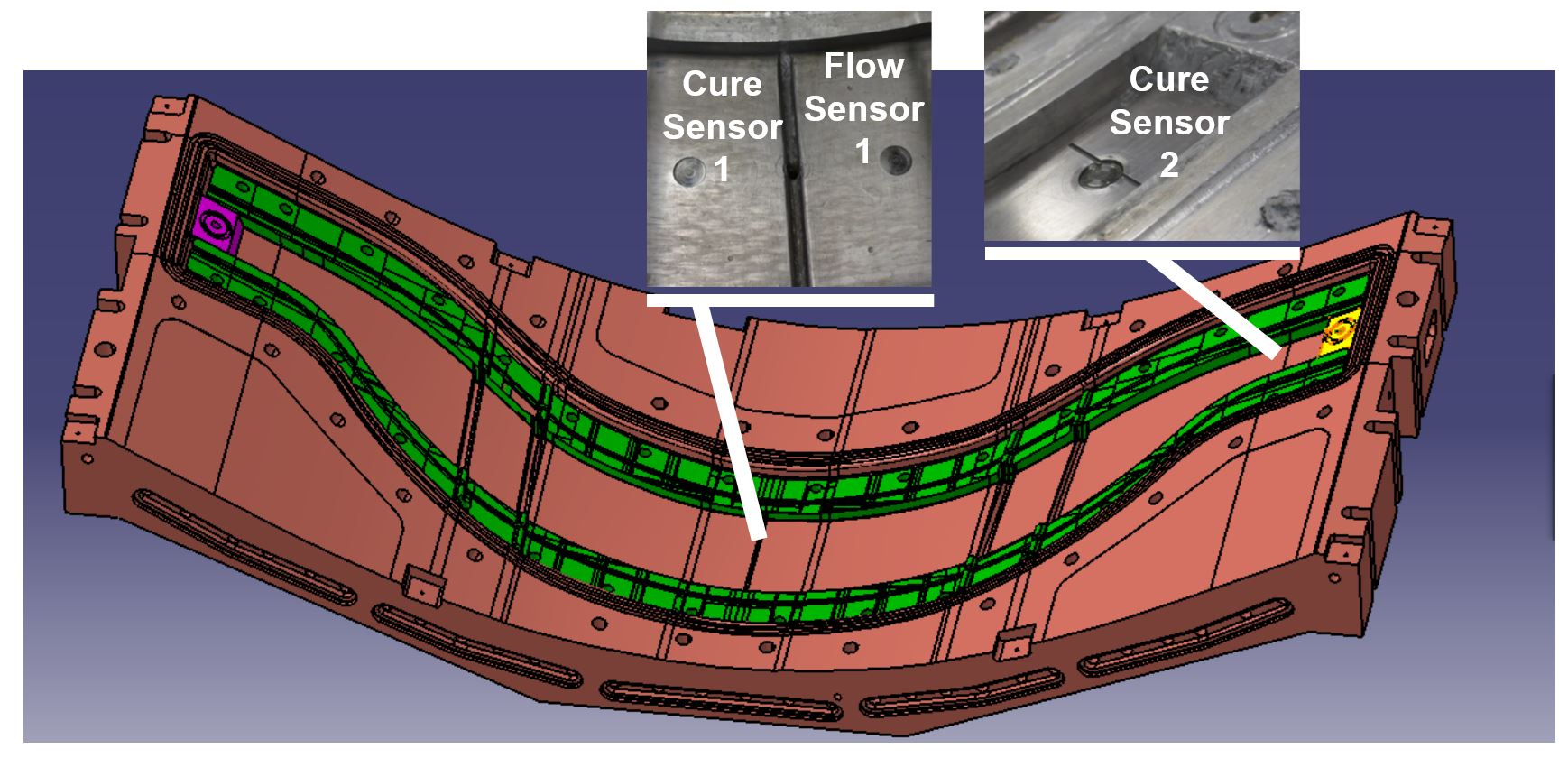
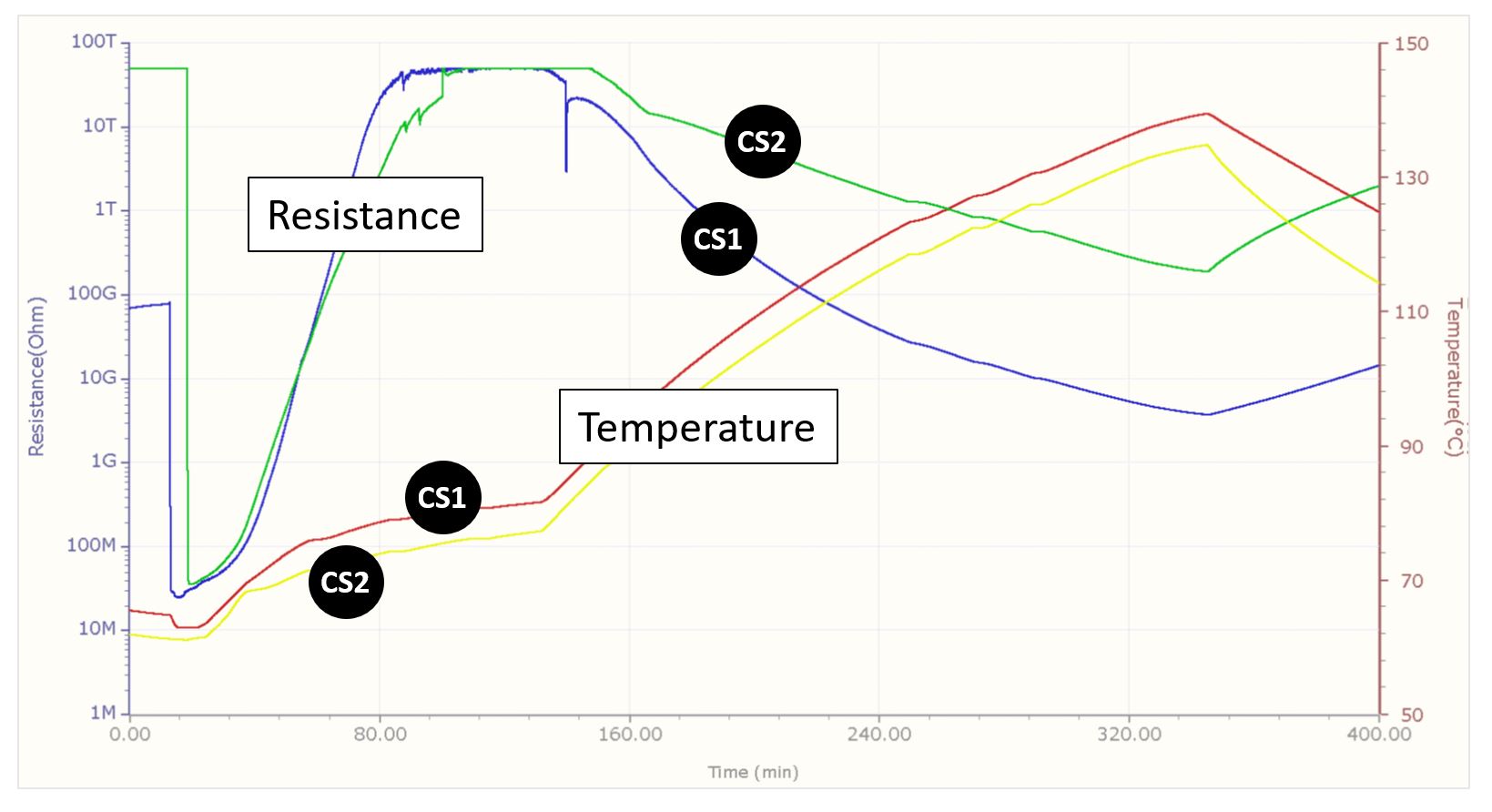
「OPTIMOLDユニットとOPTIFLOWユニットはイーサネットを介して相互に接続できるため、すべてのセンサーを1回のOptiviewセッションで記録できます」とPantelelis氏は説明します。 「したがって、CS1とCS2は2つのOPTIMOLDユニットに接続され、インモールドフローセンサー1と8つの使い捨てフローセンサーは3つのOPTIFLOWユニットに接続されました。」
次に、このセンサーシステム、OPTIMOLD / OPTIFLOWデータ取得ユニット、およびOPPTIVIEW / ORSソフトウェアを、RTM成形試験中に適用して、樹脂注入/浸透および2つのTgターゲットを含むさまざまなプロセス段階のターゲットを確立しました。 「これは、一方向繊維とハンツマンエポキシ樹脂を使用して作られた厚い部品でした」とPantelelis氏は言います。 「この場合、フローワイヤーセンサーを使用して、これらのUDプライ内のフローをチェックしました。これらは通常、密集しており、樹脂の浸透中に問題が発生する可能性があります。」
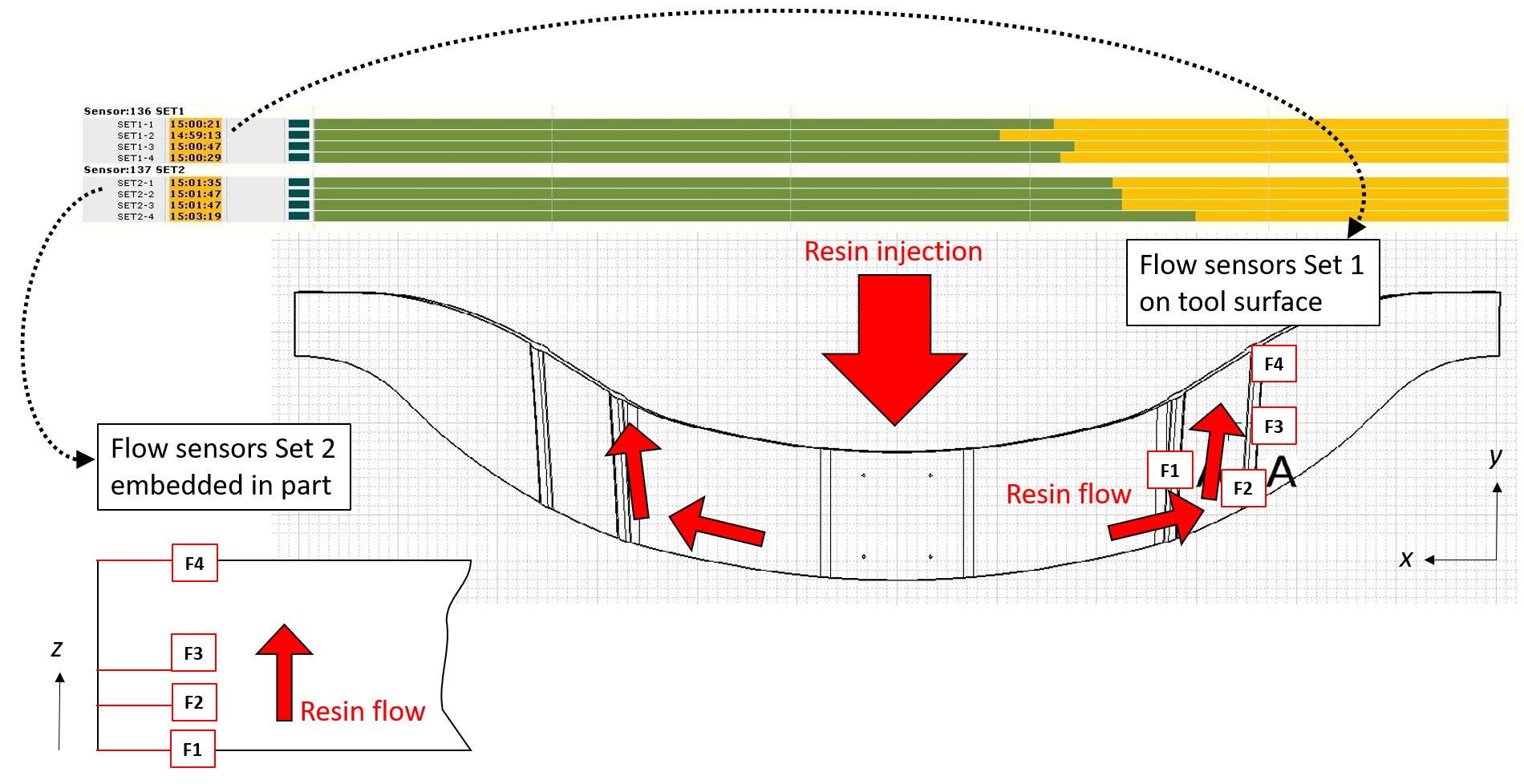
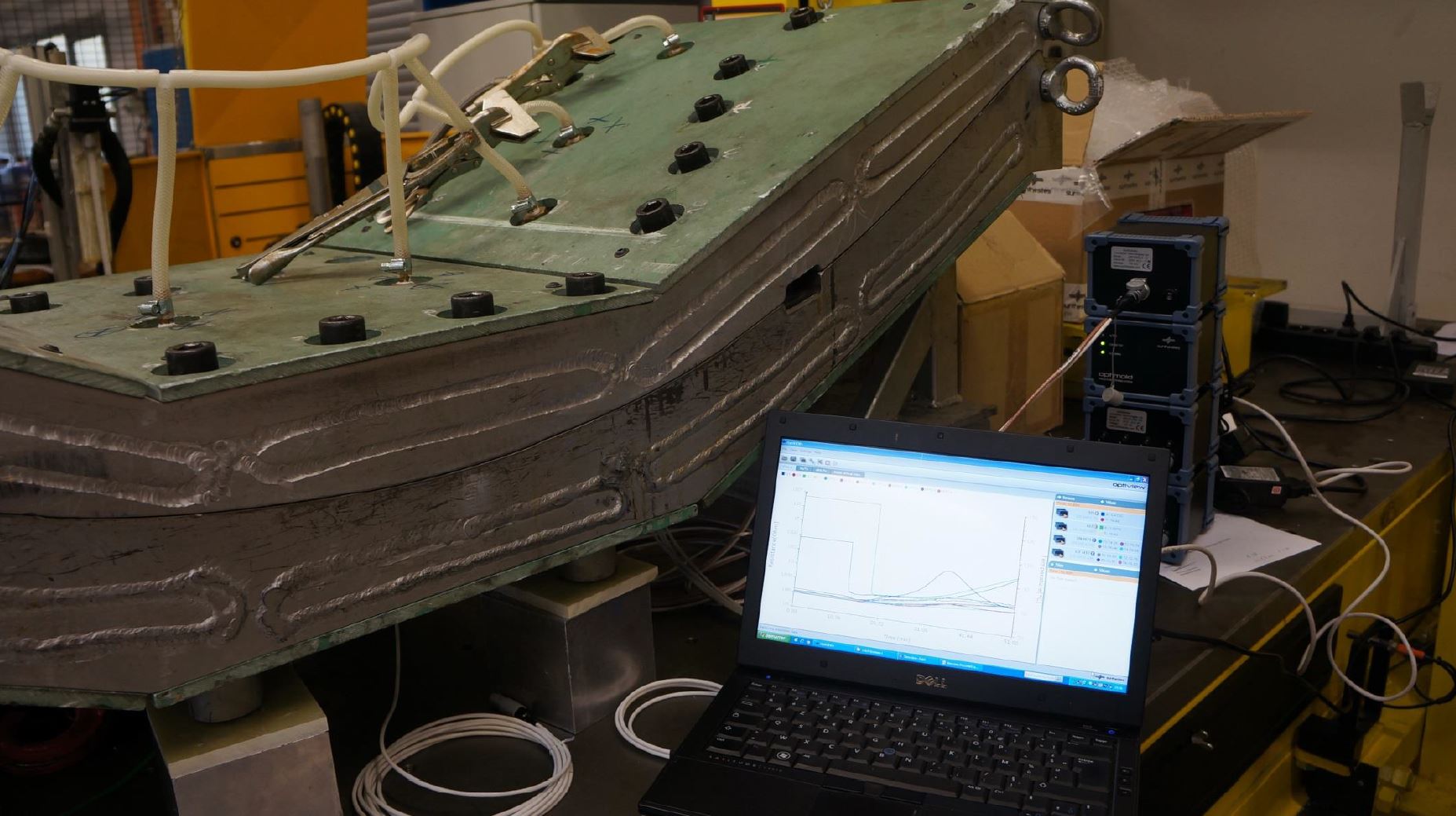
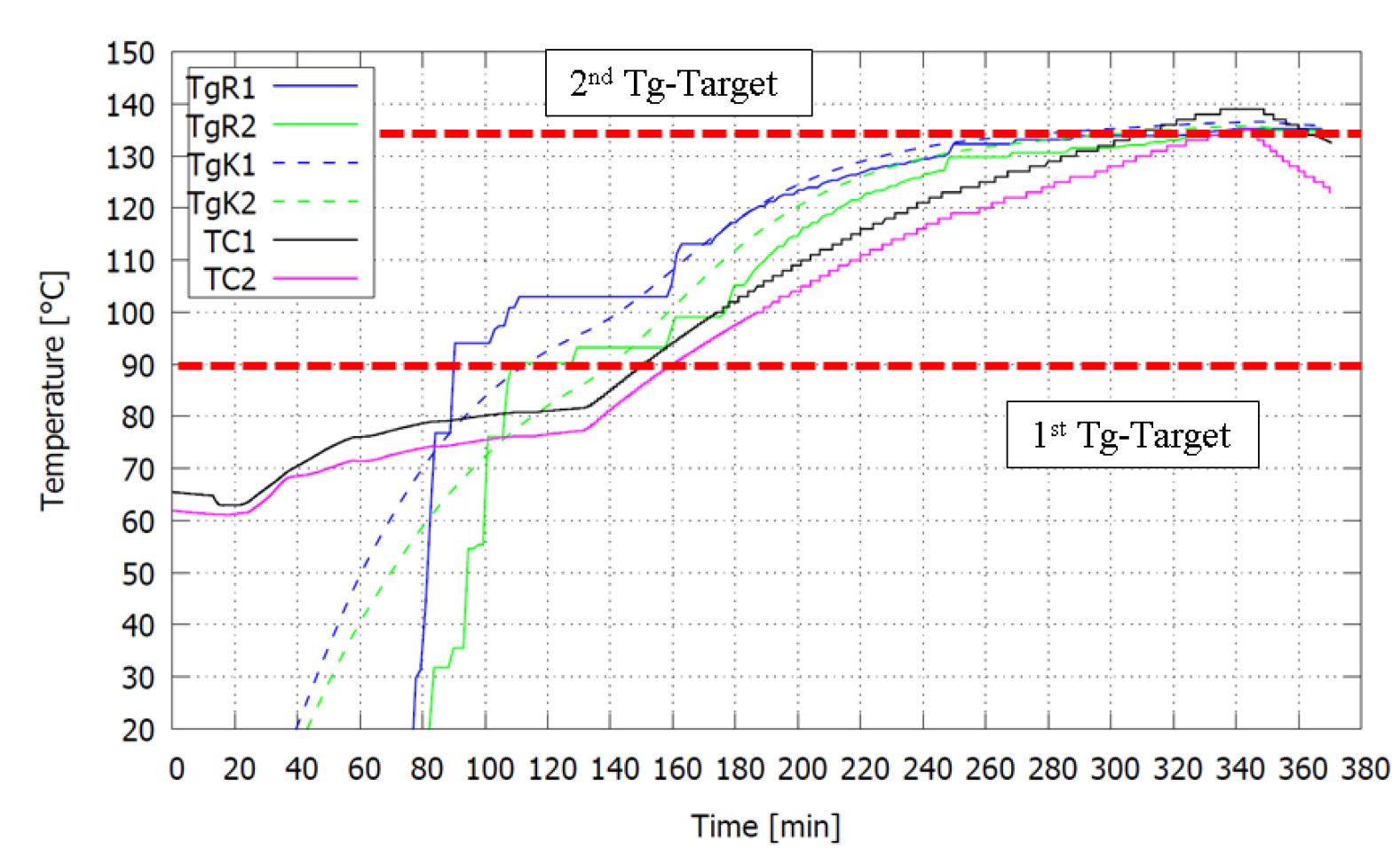
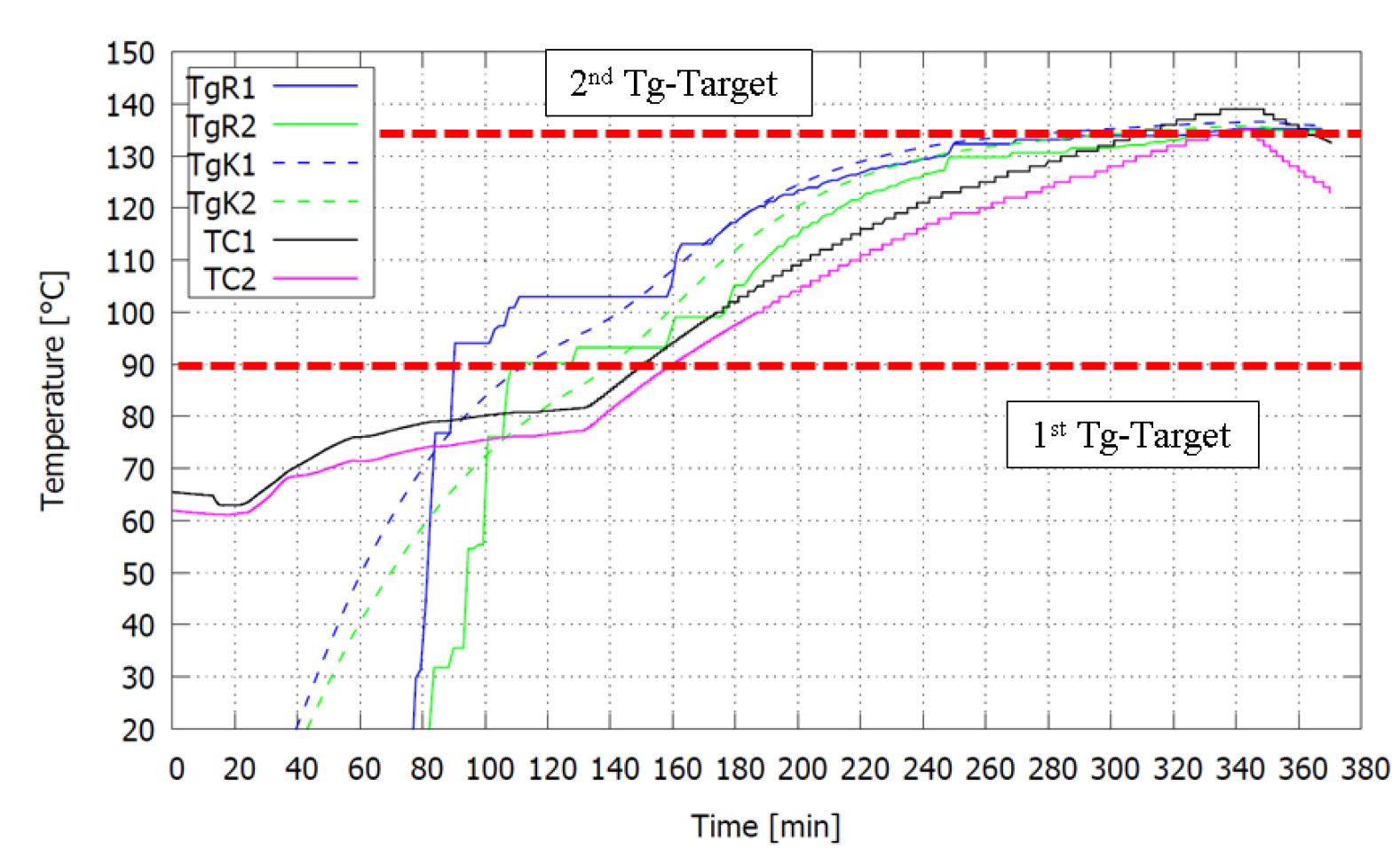
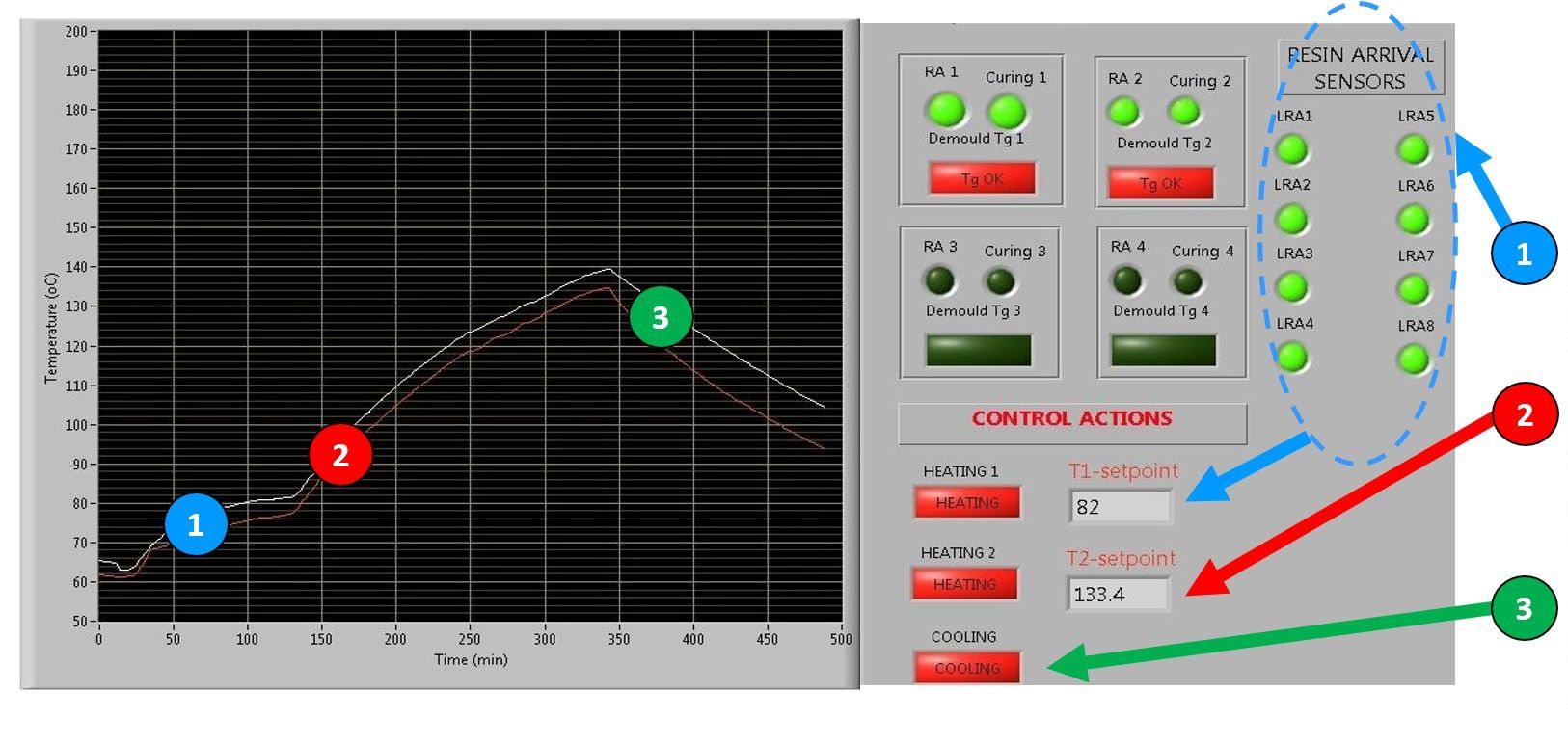
このプロセス制御システムを使用して、ハッチンソンのECOMISEプロジェクトは、硬化サイクルを30%以上短縮することができました。
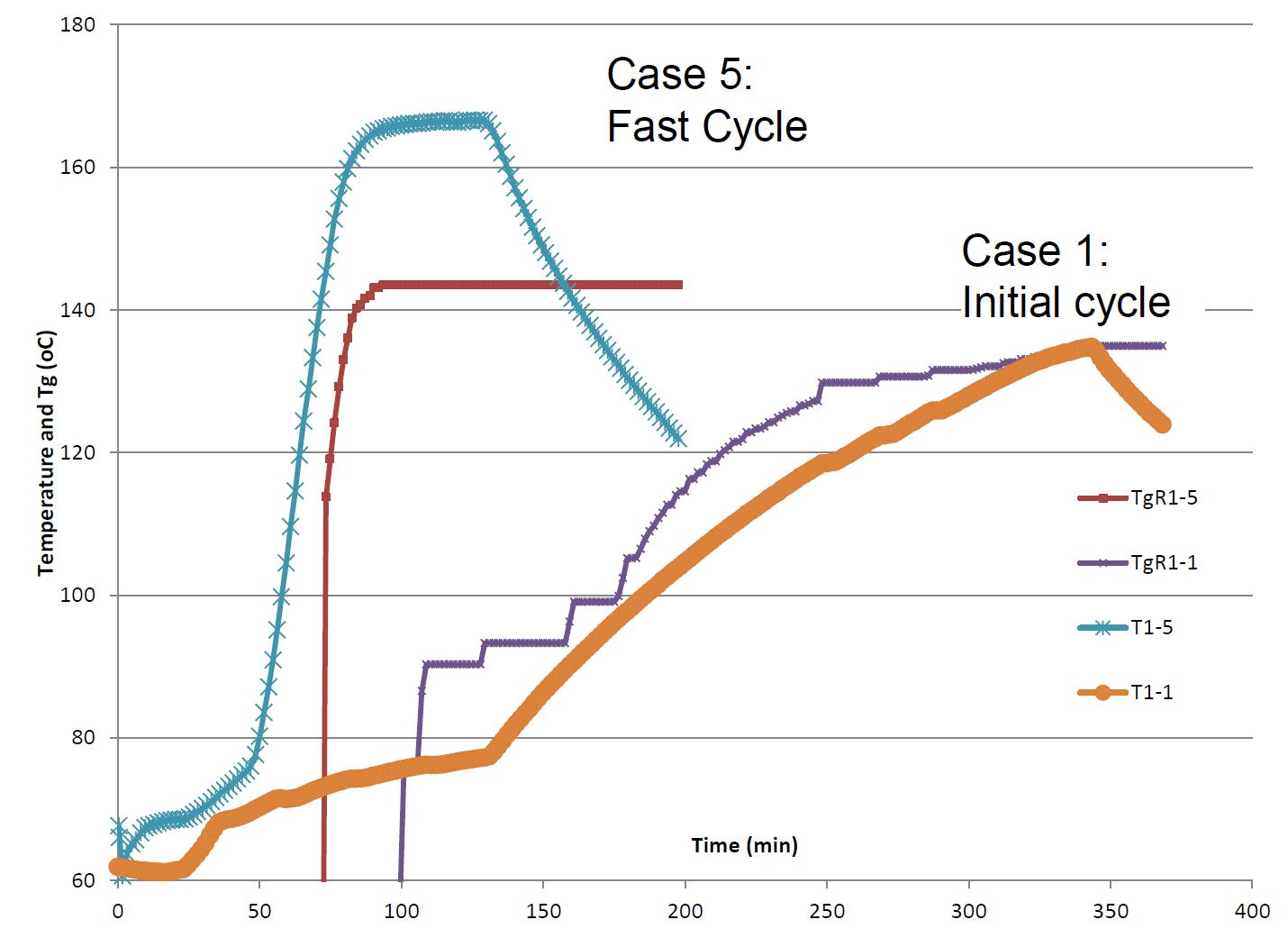
キャリブレーション
オンラインTgモニタリングにはキャリブレーションが必要です。測定値はOPTIMOLDユニットを介してセンサーから収集されるため、ORSソフトウェアは、特定の樹脂のキャリブレーションに基づいて、これらを粘度とTgに変換します。 「このキャリブレーションは、ORSソフトウェアが計算に使用する相関関係を提供するために、処理の前に行われる作業です」とPantelelis氏は説明します。 「樹脂をレオメーターに入れ、温度と粘度を測定することで校正します。適切な式を適用することにより、対応する抵抗とTgを計算します。お客様の基準に基づいて樹脂のキャリブレーションを開発し、樹脂のさまざまな硬化サイクルを研究します。このキャリブレーションデータは、その樹脂を処理するたびにORSソフトウェアによって使用されます。」

ORSソフトウェアのリアルタイムTg計算の精度は、風力ブレードの生産者であるCarbon Rotec Composite Technology(Lemwerder、ドイツ)による試験で示されました。 ORSソフトウェアによってオンラインで計算されたTgは、示差走査熱量計(DSC)を実行して離型直後に測定されたTgと比較されました。等温処理の場合、平均差は1.61°Cであり、非等温処理の場合、平均差は2.15°Cでした。
「この精度は、他の顧客とのプライベートプロジェクトで繰り返し示されています」とPantelelis氏は言います。
工業生産の進歩
このセンサーおよびデータ駆動型のプロセス制御は、完全に自動化されたインテリジェントなComposites4.0製造に向けた大きな一歩です。 ECOMISEやブリストルのNCCでも実証されていますが、まだ日常の生産には使用されていません。 「センサーを使用してTgを確認し、冷却を開始するというアイデアは、実際に風力ブレードの製造で開始されました」とPantelelis氏は報告します。「しかし、まだ完全に自動化されていません。目標Tgに達するとシステムはアラームを発し、オペレーターは硬化サイクルを停止します。自動化は簡単で、パイロット段階でメーカーがシステムの精度を検証すると完了します。」
「この目標に向けて、生産オペレーターが自動化されたプロセスを監視できるようにする新しいワークステーションを開発しました。これにより、彼の側からの入力は不要になります」と彼は続けます。 「風力タービンブレードの製造では、樹脂と接着剤の硬化中に単一のワークステーションを使用すると、品質を犠牲にすることなく、サイクルタイムを少なくとも2〜3時間短縮できることがわかりました。」
現在SpiritAeroSystemsであるBombardierBelfastは、Cシリーズ(現在はAirbus A220)用の樹脂注入複合翼の製造にSynthesites機器を使用していますが、プロセス制御は自動化されていません。ただし、SynthesitesはECOMISEのBombardierとも連携しており、その開発は進められています。重要な成果の1つは、オートクレーブの壁を通過するセンサーでした。 2013年のブログで説明されているように、「Cシリーズ複合翼」:
ボンバルディアは、レイアップが長さ21.3m、直径5.6mのオートクレーブに配置された後に注入し、粘度とウェットアウトの低減に必要なレベルに温度と圧力を維持できるようにします— Cytec890は80℃で注入可能。 。 。樹脂注入が完了した後、圧密中にオートクレーブに正圧が加えられ、工具要素が閉じ、ウェットラミネートが圧縮され、余分な樹脂が樹脂入口から特別に設計された樹脂ダンプに排出されます。
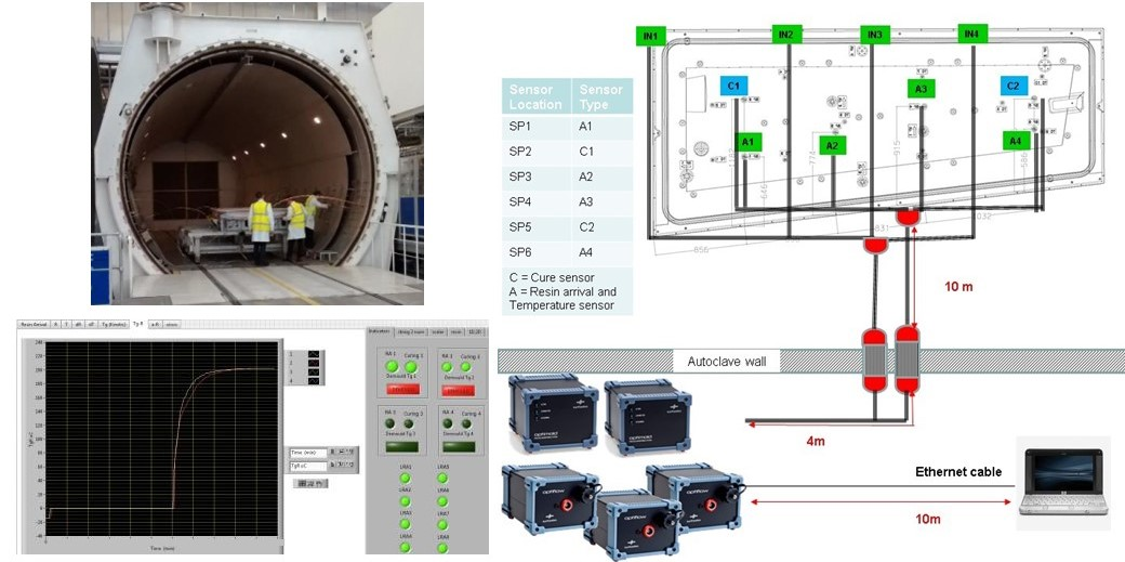
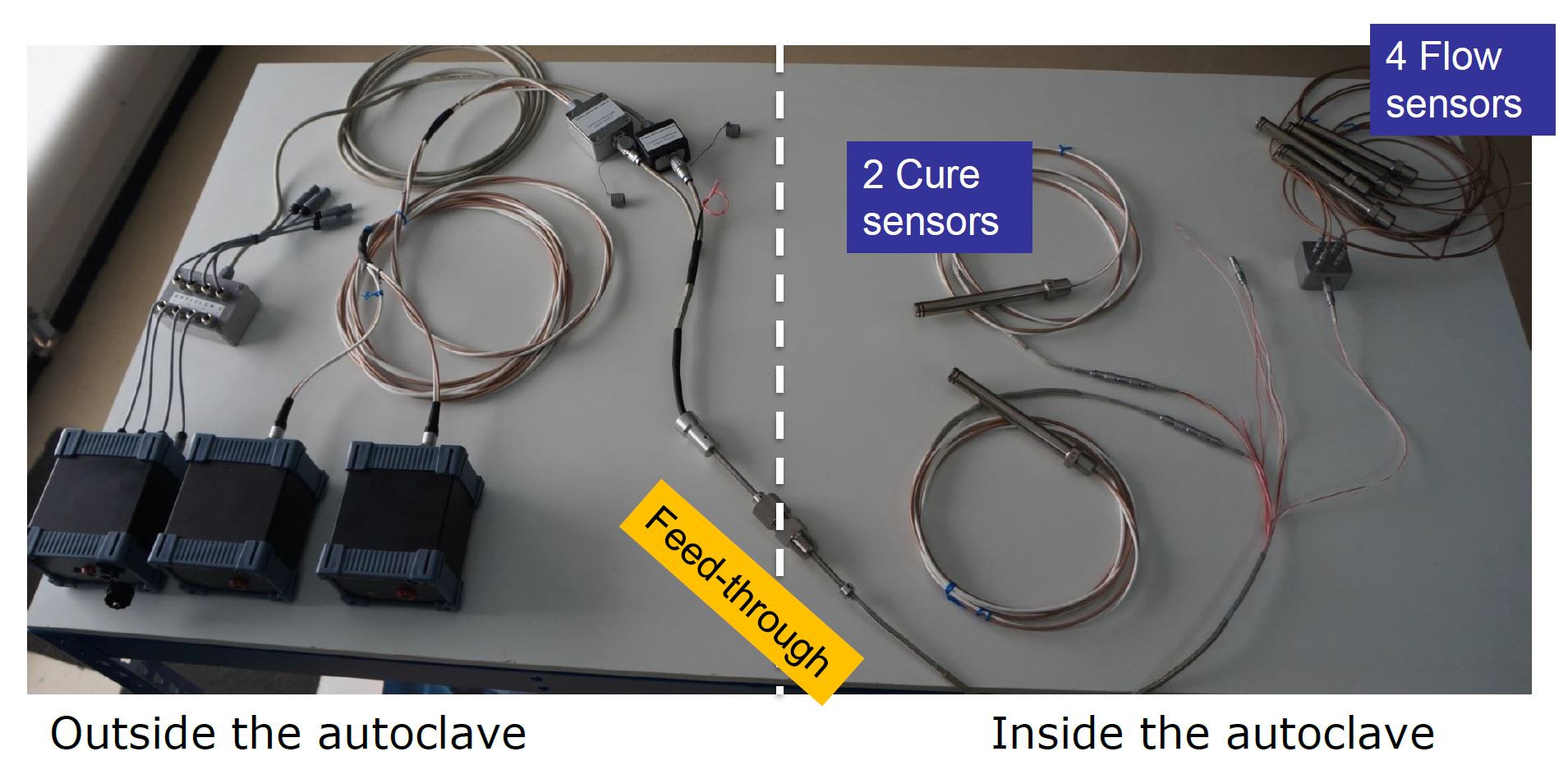
「商用航空宇宙のほとんどのメーカーと同様に、品質を確保し、速度を上げることに関心があります」とPantelelis氏は説明します。以下のレイアウトとECOMISEの結果は、デモンストレーター向けであり、商用パーツではありません。真空ラインに、2つのインモールド硬化センサーを備えた2つのOPTIMOLDユニットと、4つのインモールドフローセンサーと4つのインラインセンサーを備えた3つのOPTIFLOWユニットを使用しました。 「OPTIFLOWは、最大4つの樹脂到着と4つの温度/抵抗センサーを監視できます」とPantelelis氏は述べています。 「デモンストレーションの目標は完全に達成されました。センサー、配線、システムは、最も困難な航空宇宙仕様の下で問題なく機能することを証明しました。樹脂の到着測定値が、流れのシミュレーションと比較して大きな違いを示したことは興味深いことでした。また、オンラインのTgモニタリングでは、その特定のデモンストレーターの治療サイクルが大幅に短縮された可能性があることが示されました。」
「現在、ボンドラインの監視システムを開発しています」とPantelelis氏は言います。「主に風力タービンのブレード製造用ですが、最終的にはあらゆるボンディングプロセス用です。現在、コスト削減を目指す風力タービン業界で忙しい中、大量生産用の液体複合成形に向けて航空宇宙分野からの関心が高まっています。製造業者は、成形中に正確に何が起こっているのか、そしてどのようにプロセスを安定させ最適化できるのかについて、より多くの洞察を得ようとしています。」
EcomiseおよびRecotransプロジェクトは、助成金契約番号NMP2-SL-2013-608667および768737に基づいて、欧州連合のFP7およびHorizon2020研究およびイノベーションプログラムから資金提供を受けました。
「誘電分析(DEA)、AC対DC」セクションの参照 含める:
- VINCENTZによる「リアルタイムUV硬化モニタリング」、European Coatings Journal、2003年11月号、p。 7.
- Reinhold Meierによる「オンラインプロセス監視システム–ベンチマークとテストの調査」 1 、スウェンザレンバ 1 、Florian Springl 1 、クラウス・ドレクスラー 1 、Fabrice Gaille 2 とクリスチャンウェイマー 2 — 1 炭素複合材料研究所、ミュンヘン工科大学、ガルヒング、ドイツ。 2 Eurocopter Deutschland GmbH、ドナウヴェルト。複合材料のフロープロセス– FPCM 11、2012年7月9〜12日、ニュージーランド、オークランド。
- Robert E. Greenが編集したマテリアルVIIIの非破壊的特性評価、第8回 の議事録 国際材料の非破壊特性に関するシンポジウム、1997年6月16〜20日、米国コロラド州ボールダー、Springer Science&Business Media発行、384〜385ページ。
もう1つの役立つ参考資料は、LambientTechnologiesが発行したHuanL.Leeによる「TheHandbookof Dielectric Analysis andCureMonitoring」です。
樹脂
- センサーとプロセッサーは、産業用アプリケーション向けに統合されています
- ハイスループット産業用ビジョン用の新しいamsイメージセンサー
- BASFと東レが自動車および産業用CFRTテープの製造に関する供給契約を締結
- 履物用の超軽量TPEコンポジット
- 双胴船のレース用に選択されたソルベイコンポジット
- Hexionは、航空宇宙複合材料の製造に2成分エポキシソリューションを導入しました
- ランクセスは、連続繊維強化熱可塑性複合材料の生産能力を拡大します
- 熱可塑性複合材料コンソーシアムは、自動車および航空宇宙向けの大量生産を目指しています
- 産業用ロボットアーム用の超薄型、バッテリー不要のひずみセンサー
- スマートセンサー:産業機械の長所と短所
- 産業メンテナンスの革新は何ですか?