本番環境のサービススペシャリスト向けのインダストリー4.0ソフトウェア
マシンの可用性を効率的に改善する必要性を満たす
先週、インダストリー4.0についてプロダクションマネージャーと詳細に話し合いました。彼は約500人の従業員と約150台の機械を備えた工場を担当しています。いつものように、機械は多くの異なるメーカーによって異なる年に製造されました。彼は、インダストリー4.0ソリューションが、生産目標を確実に達成するためにマシンの可用性を高めるのに役立つかどうかを私に尋ねました。彼は、サービス技術者が簡単に使用できるソリューション、つまりプログラミングスキルを必要とする複雑なソフトウェアツールがないソリューションを見つけることに興味を持っていました。
幸いなことに、レックスロスの制御システムを搭載した彼のマシンでは、その場で解決策を示すことができました。 Open Core Engineering(OCE)のおかげで、ソフトウェア機能はIndraMotionコントロールユニットに直接アクセスできます。何よりも、PLCコードを1行追加する必要はありません。これらの機能は、PLCと並行して任意のデバイスで機能します。
最初のステップは、制御システムがコンポーネントの動作状態に関する利用可能なデータを送信することです。制御システムのOCEテクノロジーインターフェースは、ルールベースの分析のためにこの情報をソフトウェアに送信します。ユーザーは、PLCコードを1行入力したり、マシンに触れたりする必要はありません。
リードするメンテナンス技術者–予知保全への移行
しかし、このデータだけではまだ何も解決されていません。まず、情報とルールに変換する必要があります。これは、Production RulesConfiguratorによって実行されます。たとえば、サービス技術者は、エンジントルクの変化が機械的な摩耗を示していることを知っています。これまで、彼らは定期的に各マシンを検査し、データを個別に呼び出していました。これは非常に時間のかかるプロセスです。これで、サービス技術者は知識をソフトウェアが実行するルールに変換します。エンジンのトルクが所定の量だけ変化すると、システムはそれに応じてメンテナンスグループに通知します。サービス技術者は、ルールから逸脱した場合はいつでもソフトウェアに通知してすぐに通知できることを知っているため、各マシンの値を手動で呼び出す必要がなくなりました。
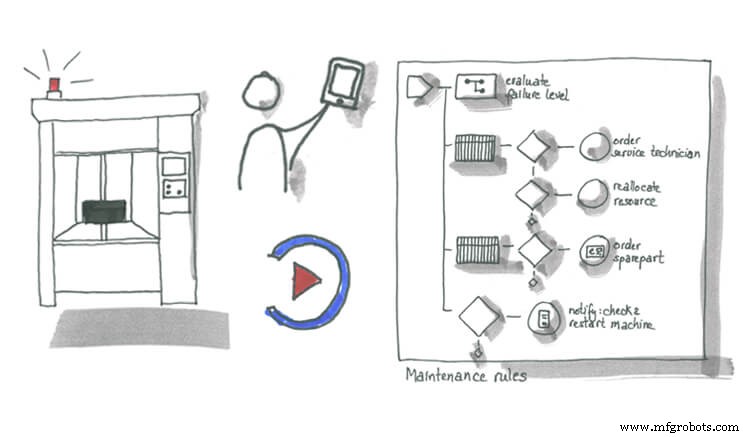
サービス技術者によってモデル化されたルールは、定義された許容値と傾向を使用して、そのような偏差をすばやく検出し、適切なサービス技術者に報告します。運用データの継続的なルールベースの監視は、実際の摩耗に対応するためにサービス間隔を動的に調整できることを意味します。ほとんどの場合、これにより不要な作業がなくなるため、サービスコストが大幅に削減されます。もう1つの特に重要な考慮事項は、ルールが製造元に関係なく、既存のITシステムに便利に統合されていることです。費用のかかるトレーニングを必要とせずに、サービス技術者自身が既存のルールを変更したり、新しいルールをモデル化したり、マシンの稼働中にこれらを制御システムに送信したりすることもできます。
デジタルアシスタントは柔軟性と速度を向上させます
ルールは基本的に、熟練した従業員が適切なタイミングで適切な決定を下すのに役立つデジタル支援システムです。私たちが始めたところに戻る:私たちの議論では、プロダクションマネージャーは最初は懐疑的でした。彼はメンテナンスグループのサービス技術者の1人を連れてきました。彼は、プログラミングの知識がなく、PLCやマシンに触れることなく、PCでルールを定義する方法を教えてくれたときに非常に興味を持っていました。彼はそれをデジタルアシスタントと呼び、柔軟性を高め、メンテナンスの応答時間を短縮しました。
メンテナンスは、一方ではマシンの運用データと本番データ、もう一方ではビジネスプロセスとアクションの間のリンクを必要とする可能性のあるアプリケーションケースの1つにすぎません。そして忘れてはならないのは、マシンプログラムを変更することなくです。
本番環境でのルールベースの分析とサポートのために、どのようなアプリケーションを考えることができますか?
産業技術