グリップトルク:間違った質問への答え
グリップトルク:間違った質問への答え。
2部構成のシリーズの第2部
(グリップトルク:これはツール/ツールホルダーの有効性を測定する正しい方法ですか?)を参照してください。
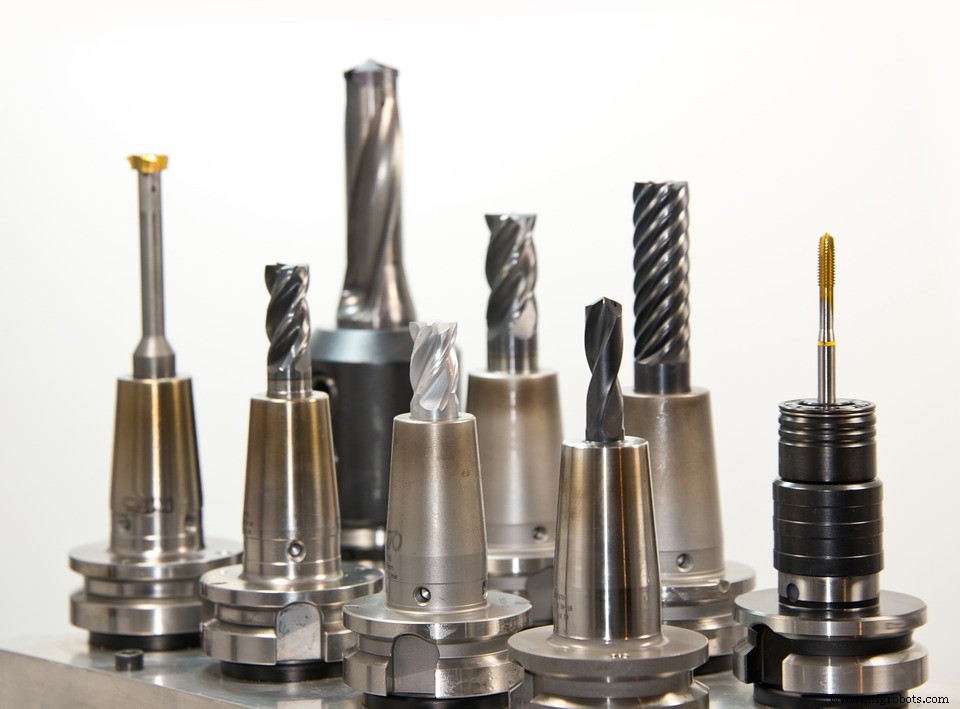
金属加工用の機械が進化し、ますます速くなるにつれて、私たちが「ツールセキュリティ」と呼ぶものの探求も続いています。新しい形式のツールホルダーが使用されるようになると、グリップトルクは、最高の生産性を得るためにツールを所定の位置に維持するためのさまざまな方法を判断および比較するための好ましい方法であり続けました。
サイドロックエンドミルチャック
サイドロックチャックは、ツールのセキュリティを確保するための初期の(ほぼ100年前の)ソリューションでした。このインターフェースには、ツールの側面の平らな地面と組み合わせて、ホルダーの側面のネジを締めることが含まれます。ツールのセキュリティは保証されていますが、フォームフィットソリューションは他の多くの問題を引き起こし、最新の機械加工方法には理想的とは言えません。
まず、止めねじによる片側クランプの性質により、明らかな同心性の問題が発生します。シャンクの底部近くに力が加えられると、工具の刃先が反対方向に移動します。したがって、工具寿命と寸法精度を低下させる振れの問題が発生します。第二に、ホルダーの片側のネジと、片側から材料の塊が欠けている切削工具を組み合わせると、明らかな不均衡の問題が発生します。その結果、振動が増加し、工具寿命、仕上げ、スピンドルベアリング寿命に影響を与えます。これらの欠点の両方を克服するための一般的な解決策は、寿命、仕上げ、または機械加工の音を改善するために、速度と送りを遅くすることです。多くの機械加工プロセスが継承されているため、多くの場合実現されない最終的な最終的な不利益は、生産性の低下です。
前回の記事で述べたように、サイドロックチャックは、ツールのセキュリティ対策を提供することもあり、現在でも使用されています。しかし、振れの精度とバランスが本質的に欠如しているため、同様に人気のあるコレットチャックシステムが進化しました。しかし、このシステムの精度が向上したことで、ツールのセキュリティが低下しました。
コレットチャック
コレットチャックは、従来のサイドロックホルダーよりも高い精度の必要性から発展しました。この点で、精度のマークが大幅に改善されました。さらに、設計の多様性は別の大きな属性であり、異なる工具直径が必要な場合に、新しいホルダー全体の追加コストを削減しました。改良された汎用性と精度により、このチャックは間違いなく業界で最も人気のある工具保持方法の1つになりました。しかし、コレットチャックの精度は向上しましたが、グリップトルクは低下しました。このソリューションの機械的な性質により、ツールの引き出しは、あらゆるタイプの重いフライス盤操作を試みた人にとって大きな問題になりました。多くのオペレーターはナットを締めすぎて補おうとしますが、残念ながら、これは振れの精度とツールのセキュリティを失うだけであり、それでも不十分でした。したがって、さらなる進歩が続いた。
ミルチャック
ツールホールディングの次の進化は、ミルチャックの形でもたらされました。これらは50年前に開発された機械的ソリューションであり、コレットチャックよりも優れたグリップトルク(より高いセキュリティ)を同様の精度で提供し、メーカーが荒削りが可能なコレットのようなシステムを実現できるようにします。ミルチャックは、適切にクランプされている場合、セキュリティを向上させるためにグリップトルクが向上し、精度が向上するという点でサイドロックよりも優れていると見なされていました。精度の向上は、ベアリングレースが締め付け時のトルク伝達を向上させている間、カッターのシャンクの周りを360°均等にグリップするコレットインターフェースからもたらされました。さらに、スリーブを付けることができるため、ツールの直径ごとに必要なさまざまなホルダーの数を制限できます。
ただし、ミルチャックには多くの個別のコンポーネントがあります。前述のように、ツールはローラーベアリングケージを使用してグリップされ、ローラーベアリングケージは大きな外側のナットで締められ、ツールの周りのチャックを圧縮します。グリップトルクはコレットよりも大幅に増加しますが、ローラーベアリングケージのサイズが大きいため、それらを収容するために大きなナットが必要になるため、ホルダープロファイルは非常にかさばり、到達能力が低くなります。
また、前に触れたように、ミルチャックの有効性はオペレーターに大きく依存しています。適切にクランプするには、ナットを最後まで締めてから、1/4回転後退させる必要があります。これは、ベアリングを締めるとベアリングが少し転がり、振れが発生するためです。バックオフすることで、ベアリングへの圧力を解放します。しかし、多くのオペレーターは、意識の欠如、時間の制約、またはその他の理由により、後退せずにナットを締めすぎる傾向があります。
このシステムのもう1つの欠点は、ニードルベアリングが締め付け後に毎回同じ場所に配置されることはなく、多くの場合、互いに転がされることです。その結果、再現性のあるバランスを実現できなくなります。低速では、不均衡の悪影響がすぐにわかるとは限りませんが、速度が上がると、振れの精度と工具寿命が急速に低下します。
最後に、ミルチャックは高価な保持ソリューションです。ほとんどの場合、6か月ごとに分解してグリースを塗る必要があるため、初期費用とは別に、考慮すべきメンテナンス費用があります。これには時間とお金がかかるため、オペレーターはこの重要なステップをスキップすることがよくあります。その結果、グリップトルクが低下し、振れ精度が低下します。
その他のオプション
ツールのセキュリティを実現するために、エンドミルチャックまたはミルチャックオペレータが使用した他の代替手段は何ですか?
焼きばめは、摩擦ばめの方法を別のレベルに引き上げます。熱膨張の特性を利用して、高いグリップトルクに対応し、精度とバランスの再現性を高めています。 Safe-Lock™システムでも使用できます。このシステムは、高いクランプトルク、精度、バランスを備えているだけではありません。また、オペレーターが習得するのに最も簡単なシステムの1つです。
圧入システムは、機械プレスを使用してコレット/スリーブを一時的に変形させ、丸いシャンクツールを挿入します。ホルダーの角度はコレットスリーブの角度とわずかに一致しています。真ん中の真っ直ぐな穴を通って動く油圧プレスは、コレットとツールを一緒に押し込みます。グリップトルクが高く、振れ精度は良好ですが、ホルダー本体は物理的な質量が不足しているため、重い横荷重には適さないため、重い荒削りには適していません。ツールには特定のサイズのシャンクが必要であるため、柔軟性も不足しています。そうしないと、コレットにひびが入る可能性があります。また、このシステムは独自仕様であるため、価格、在庫状況、さまざまな製品の選択肢について、1つのメーカーのみに依存するようになります。
油圧チャックは、真っ直ぐな垂直作業(穴あけ/リーマ加工)には適していますが、フライス盤には適していません。それらは、圧力下の流体を使用して内部ブラダーを拡張し、最終的にツールに係合します。切削深さや切削抵抗が小さい高速加工には適していますが、荒削りやラジアル力や熱が大きくなるシナリオには適していません。なんで?チャック内の液体は柔軟性が高すぎて、十分なグリップトルク伝達を提供できません。さらに、場合によっては高性能フライス盤が温度を発生させ、実際に内部オイルが蒸発して故障の原因となることがあります。ミルチャックと同様に、内部ブラダーが過度に摩耗して漏れ始めないように、メンテナンスも時々必要になります。
この記事が示すように、最大グリップトルクの検索は、ニーズが適切に定義されていなかったため、実際の満足感なしに何十年も続けられました。グリップトルクは間違った質問への答えでした。
以前はHaimer-USA.comで紹介されていました。
産業技術