カスタム金属鋳物の指定と注文:ガイド
カスタム金属鋳造プロジェクトを確実に成功させるための9つの重要な考慮事項
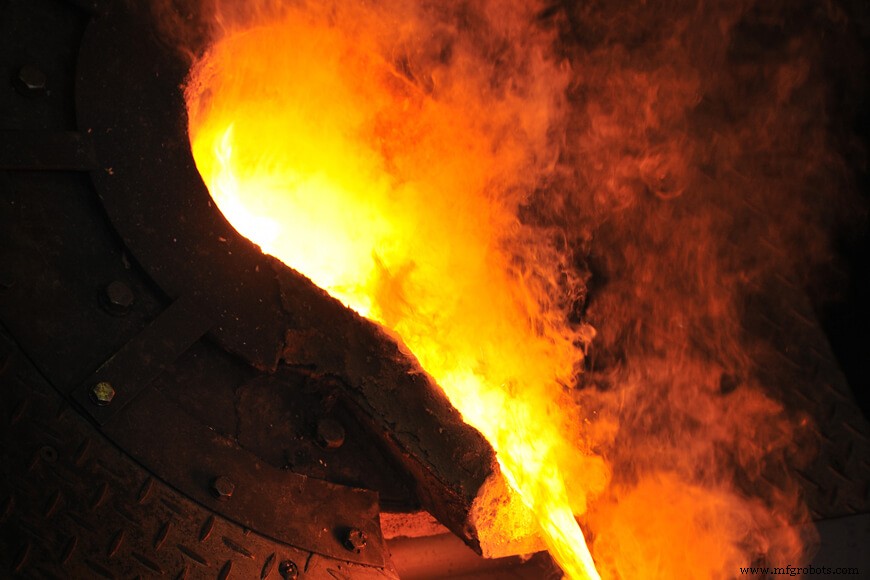
金属鋳造は、金型の空隙を液体金属で埋めることによって形状(鋳造)を生成するプロセスです。鋳造金属製品は、並外れた強度と耐久性を備えており、農業、自動車、鉄道、家電製品、建築建築、造船、石油およびガス抽出、水処理、林業、鉱業などの産業での重機用途に役立ちます。少数。
サプライヤーの鋳造所の資格を取得し、金属鋳物を注文することは、時間のかかる試練になる可能性がありますが、そうである必要はありません。見積もりとキャストのプロセスを理解することで、コストのかかる失敗を避けることができます。サプライヤーのファウンドリとの明確で徹底的なコミュニケーションにより、適切に設計された経済的な最終製品が得られます。
見積もりのリクエスト
鋳造品の見積もりを依頼する目的は、購入した鋳造品のコスト、品質、納期の最適なバランスを確立することです。見積もりの最低価格を自動的に選択したくなるかもしれませんが、そうすると、納期が遅れたり、鋳造の品質が低下したりする可能性があります。どちらも長期的には高額になる可能性があります。
精通した顧客は、工具要件、公差、仕上げ許容値、および図面、仕様、処理要件の例外を含む、受け取った見積もりのすべての規定を比較検討する必要があります。機械加工の削減、納期の改善、サプライヤーの鋳造経験と信頼性などの他の要因は、鋳造の実際のコストと価値を決定するために特に重要です。
サプライヤーの鋳造所に金属鋳造の価格を要求する場合、対処すべき重要な考慮事項が少なくとも9つあります。
- 予備鋳造設計
- 数量
- 仕様
- 健全性
- テストと検査
- 重量
- パターン
- 機械加工
- 生産と配達のスケジュール
1。予備鋳造設計
鋳造金属部品は、鋳造プロセスを最大限に活用するように設計する必要があります。効率的でコストに敏感な生産のために、鋳造設計は、望ましい物理的特性、正味の形状要求、および外観をもたらす最も単純な生産方法を選択する必要があります。
必要な部品の正確な寸法の詳細を示す図面は、見積もりのリクエストに含める必要があります。
ファウンドリのプロセスやサプライヤーのファウンドリとのコミュニケーションを理解することが、ファウンドリの観点から最も費用効果の高い設計を決定するのに役立つ、設計のいくつかの重要な要素があります。
最小断面厚
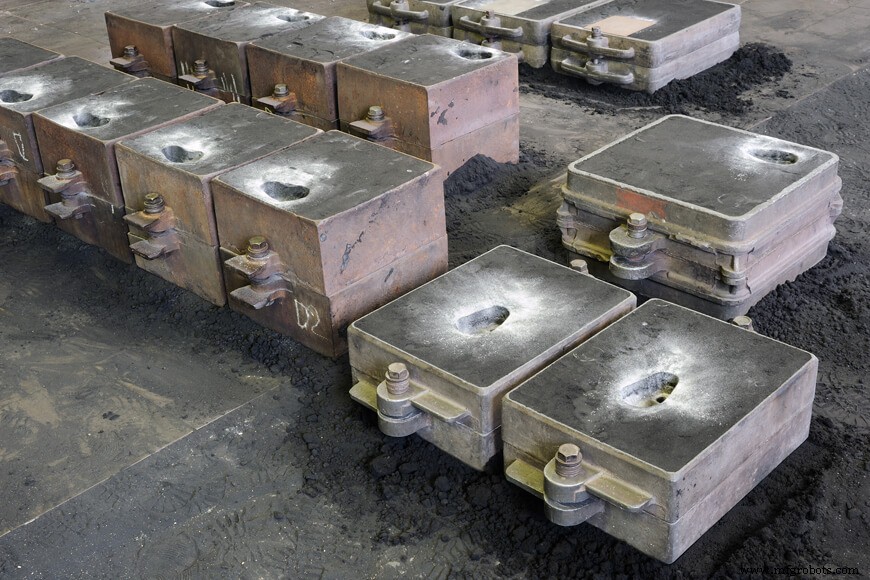
すべての鋳造物には、その強度と剛性によって決定される最小の厚さがあります。仕様よりも薄いデザインでは、プロジェクトがキャストできなくなる可能性があります。鋳造を成功させるには、液化金属がより薄い部分の金型に充填できるようにする必要があります。
液化(溶融)金属は非常に速い速度で冷却します。金型のゲートから遠く離れた薄いセクションに入るには、冷却が速すぎる可能性があります。原則として、従来のプロセスを使用する場合、設計には0.25インチ(6 mm)よりも薄い領域を含めないでください。インベストメント鋳造はより高いレベルの自由を可能にし、壁の厚さは0.030インチ(0.76 mm)まで下げることができます。
ドラフトとコア
「ドラフト」という用語は、パターンの垂直面のテーパーを指します。型壁を乱さずに型からパターンを抽出するには、ドラフトが必要です。これらの角度の制限を無視すると、型が鋳造物から取り外されたときに型が裂ける原因になります。
いくつかの要因が、各鋳造に必要なドラフトの量に影響します。製造プロセス、鋳造サイズ、および成形が手作業で行われるか機械で行われるかによって、必要なドラフトの程度がすべて変わります。機械成形された鋳物に必要なドラフトは少なくなります。ただし、生砂型で製造された鋳物は、通常よりも多くのドラフトが必要になります。一般的な経験則では、1フィートあたり3/16インチのドラフト(約1.5度)を許可します。
コアは、鋳物砂によって鋳物内に作成された中空の空間です。パターンだけではスペースやキャビティを作成できない場合は、コアが必要です。コアを使用するとドラフトが不要になる場合がありますが、鋳造のコストが増えるため、コアの使用は制限する必要があります。
鋳物に配置できるコアの最小直径には、次の3つの要素が影響します。
- コアが配置される領域の厚さまたは深さ
- コアの長さ、および
- サプライヤーの鋳造所が採用する鋳造方法。
パーティングライン
1つの平面で分離すると、型の作成だけでなくパターンの作成も容易になります。直線のパーティングライン(1つの平面にパーティングラインがある)のパターンは、不規則なパーティングラインのパターンよりも簡単かつ低コストで作成できます。対称的な鋳造形状は、パーティングラインを容易に示唆します。このような鋳造設計は、成形とコアリングを簡素化するため、可能な限り使用する必要があります。それらは常に「分割パターン」(別々のコープとドラッグ)として作成する必要があります。これにより、金型での手作業が最小限に抑えられ、鋳造仕上げが改善され、コストが削減されます。
コア
コアは、型の内側に配置された別個の部品(多くの場合、鋳物砂から作られます)であり、パターンだけでは作成できない開口部と空洞を作成します。鋳造の最終的なコストを削減するには、必要なコアの数を削減または削減するために、設計によってあらゆる試みを行う必要があります。
鋳鋼で正常に使用できるコアの最小直径は、次の3つの要因に依存します。
コアを囲む金属部分の厚さ、
コアの長さ、および
サプライヤーファウンドリが使用する特別な注意事項と手順。
コアを取り巻く金属の厚さが増加し、コアの直径が減少するにつれて、コアがさらされる悪熱条件は深刻さを増します。重いセクションからのこれらの増加する量の熱は、コアを通して放散されなければならない。熱条件の厳しさが増すにつれて、鋳物の洗浄とコアの除去ははるかに困難で費用がかかるようになります。
コアを囲む金属部分の厚さ、およびコアの長さは両方とも、浮力によってコアに誘発される曲げ応力に影響を与え、したがって、必要な公差を取得するためのサプライヤーファウンドリの能力に影響を与えます。コアのサイズが十分に大きい場合は、ロッドを使用してコアを強化することができます。当然、金属の厚さとコアの長さが増加すると、曲げ応力に耐えるために必要な補強の量も増加します。したがって、追加の補強に対応するために、最小直径のコアも大きくする必要があります。
洗浄する領域にアクセスできない場合、鋳造キャビティからコアを取り外すコストは法外に高くなる可能性があります。鋳造設計では、コアを取り外せるように十分な大きさの開口部を用意する必要があります。
鋳造物のアクセスしにくい領域は、コアの除去をより困難にし、プロジェクトの経済的実現可能性に影響を与えます。鋳物は常に、コアを取り外せるように十分な大きさの開口部を備えて設計する必要があります。
鋳物は通常、特に指定がない限り、機械加工されていない、鋳造されたままの表面で出荷されます。鋳造プロセスを利用するには、サプライヤファウンドリは、最終的に機械加工されるサーフェス(詳細については、以下の「8.機械加工」を参照)と基準点の位置を知る必要があります。図面を提供する際には、許容可能な寸法公差を示す必要があります。公差は通常、サプライヤーのファウンドリと顧客の間で合意されています。
鋳造設計を最適化するには、顧客の設計エンジニアとサプライヤーの鋳造所との緊密な協力が不可欠です。すべての鋳造設計は、鋳造プロジェクトの実現可能性を判断するために、製造前に鋳造専門家によってチェックされる必要があります。
2。数量
製造する鋳物の数、またはランの長さを明確に記載する必要があります。注文数量は価格に大きな影響を与え、実行時間が長くなると鋳造あたりのコストが低くなります。
必要な部品の数量は、ささいな考慮事項ではありません。部品のプロジェクト消費は、必要な工具の種類を決定するだけでなく、生産量のニーズを満たすための特定のファウンドリの能力も定義します。
多くのファウンドリは短期、短期の「ジョブ」作業の生産を専門としていますが、他のファウンドリは大量生産に焦点を合わせています。早い段階でニーズを定義することで、正しい生産施設と確実にコミュニケーションをとることができます。
3。仕様
業界標準の仕様は、ほとんどすべての鋳造アプリケーションの基準を確立するために必要なツールを鋳造の顧客に提供します。これらの仕様は、お客様の技術スタッフが必要とする可能性のある特別な要件を排除するものではありません。標準仕様からの変更は、誤解、より高いコスト、および潜在的なサプライヤーファウンドリの失格につながる可能性があります。仕様要件の本体の規定に例外が生じた場合(仕様の補足要件に例外が生じた場合とは対照的に)、結果として得られる鋳造は、それらの仕様に準拠するように保持することはできません。
鋳造される正確な金属合金は、ASTMなどの国際的に認められた規格を使用して指定する必要があります。鋳物は、鉄(鉄ベース)と非鉄(鉄ベースではない)の2つのカテゴリーの金属から製造されます。
鋳鋼は最も一般的な鉄鋳物金属ですが、ステンレス鋼、可鍛性鉄、延性鉄など、必要な物理的特性に応じて他の金属を使用することもできます。アルミニウムと銅は、鋳造に使用される最も一般的な非鉄金属です。

機械的特性は、個別に鋳造するか、鋳造物に取り付けたテストバーを使用して確認できます。得られた機械的特性は金属の品質を表しますが、必ずしも鋳造物自体の特性を表すわけではありません。これらの特性は、凝固条件と熱処理中の冷却速度に影響され、鋳造物の厚さ、サイズ、形状に影響されます。 。一部のグレードの硬化能力により、必要な機械的特性が得られる最大サイズが制限される場合があります。
熱処理
熱処理は、特定の合金の特性を標準化し、均質化し、強化するために使用されます。多くの合金では、熱処理は、指定された最小の物理的特性が最終鋳造製品で達成されることを保証するために採用される日常的なプロセスです。温度制御装置や高度な温度記録装置でさえ、熱処理ステップの一貫性と品質を確保するために、最新の熱処理炉に日常的に見られます。
場合によっては、特殊な熱処理(火炎硬化、肌焼きなど)を、サプライヤーの鋳造所が実施する追加のプロセスとして指定することができます。
4。健全性
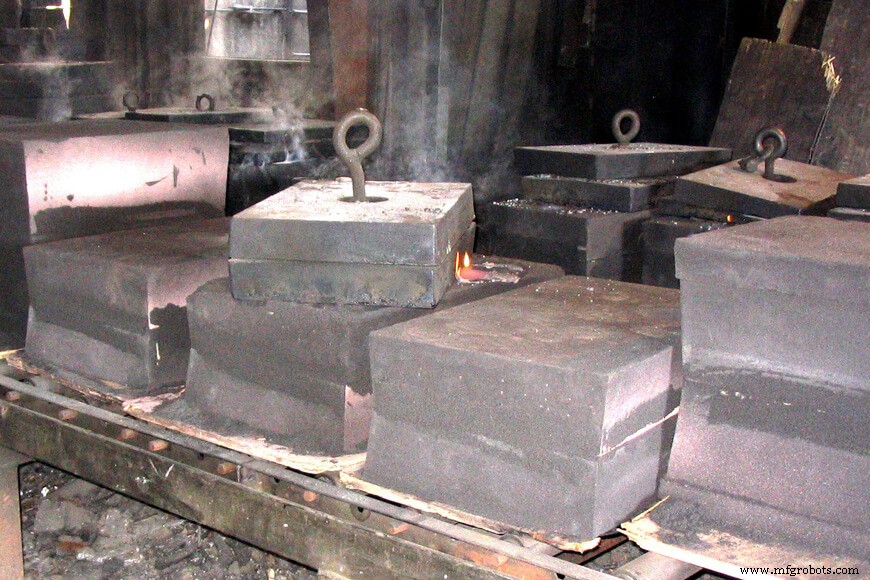
金属部品の健全性とは、砂の含有物、スラグの含有物、マクロ多孔性、収縮などの不純物や不連続性がないレベルを指します。欠陥のない鋳造物を製造することは不可能であり、さまざまな程度の欠陥がある鋳造物のみを製造します。鋳造品の受け入れまたは拒否は、顧客の正式なエンジニアリング要件に基づいて(ASTMなどの国際的に認められた規格に従って)部品を検査することによって決定されます。受け入れ基準と拒否基準は、製造前のサプライヤーファウンドリとクライアント間の合意によって定義されます。これらの基準は、鋳造コストと使用される製造プロセスの両方に影響します。
5。テストと検査
製造後、すべての鋳造品をテストして、仕様の要件を満たしていることを確認する必要があります。鋳造品は、寸法精度、表面仕上げ状態、物理的特性、内部の健全性、および亀裂についても検査されます。多くのアプリケーションでは、テストは必須です。材料仕様またはその他の一般的な要件が満たされていることを確認するために、追加のテストが必要になる場合があります。
テストと受け入れの基準は、製造前に明確に伝達され、合意されている必要があります。より厳格なテスト条件は、全体的なコストを増加させます。費用対効果を維持するには、テストと承認の条件は、各アプリケーションの正確な要件に基づいている必要があります。
鋳造品の検査に使用されるテストには、破壊テストと非破壊テストの2種類があります。
破壊的テスト
破壊試験では、必要な部品に加えて、別の試験鋳造を行う必要があります。次に、テストキャスティングは破壊され、内部の健全性(介在物の量、収縮、または存在するガス)が視覚的に判断されます。破壊テストは、テストされたピースの状態のみを示し、テストされていない他のピースが健全であることを保証するものではありませんが、実際には広く使用されています。テスト鋳造が許容できる場合、同じ方法で製造された鋳造が同じレベルの健全性を示すという仮定の下で製造を進めることができます。
非破壊検査
製品に損傷を与えることなく内部および外部の健全性を検証するために、鋳造自体に非破壊検査法が採用されています。方法には、目視検査、寸法検査、液体浸透探傷検査(LPI)、磁粉探傷検査(MPI)、超音波探傷試験(UT)、およびX線検査(X線)が含まれます。
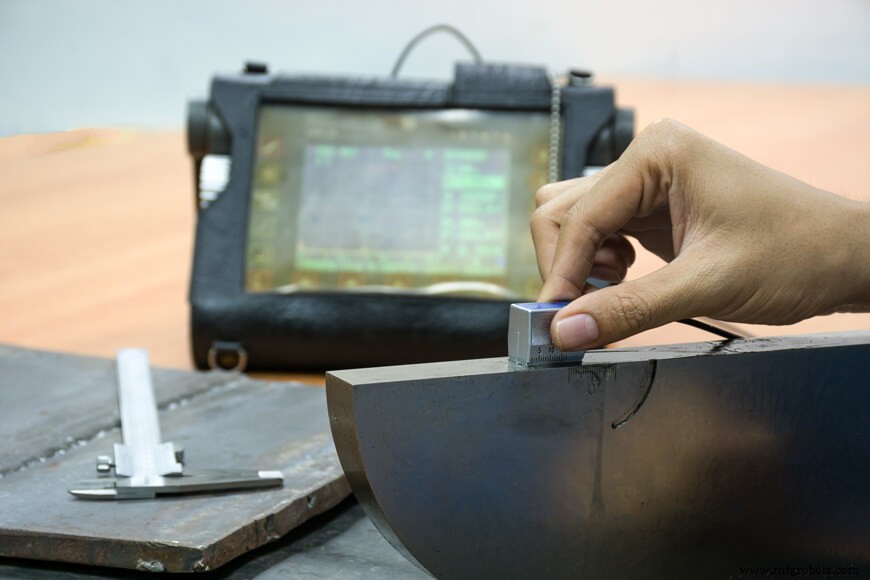
検査が完了した後、検査され受け入れられた鋳造品がそのまま使用されて顧客に出荷されることもありますが、多くの場合、さらに処理されることがあります。これには、特殊な熱処理、塗装、防錆油、その他の表面処理(溶融亜鉛めっきなど)、および機械加工が含まれる場合があります。
6。重量
鋳造の重要なコスト要素は材料です。鋳物の重量が大きいほど、その鋳物の材料費は高くなります。問題の部品について鋳造所に提供できるより詳細な重量データほど、より正確で信頼性の高い価格計算を行うことができます。
鋳造所は、鋳造品の正味(結果として生じる)重量だけを懸念しているわけではありません。彼らは主に鋳物の総重量を心配しています。総重量は、得られた鋳造物で構成される金型を充填するために必要な溶融金属の重量、および鋳造プロセスから健全な鋳造物が得られるようにするために必要なすべての供給材料(ゲート、ライザーなど)によって測定されます。鋳造所の鋳造価格は、鋳造の歩留まり(鋳造プロセスの効率と、得られた鋳造物の重量を金型に注入された供給金属の重量で割ったもの)によって大きく影響されます。
7。パターン
型を作るには型紙が必要であり、型紙作りは型紙を作るためのプロセスとトレードです。パターンは鋳造物の形であるため、鋳造物はそれが作られるパターンよりも優れていることはできません。厳しい公差または滑らかな鋳造仕上げが望まれる場合、パターンを注意深く設計、構築、および仕上げることが特に重要です。
パターン機器の設計とそれに伴うコストは、顧客とサプライヤのファウンドリの間の誤解の主な原因となる可能性があります。既存/古い設備が利用可能であるにもかかわらず、鋳造所の生産機械に適合する新しいパターン設備を構築する必要性、ハーフコアボックスの代わりにフルスプリットコアボックスの要件、木製パターンの代わりに金属パターンを生産する必要性、および/または緩いパターンの使用ではなくマウントされたパターンのニーズは、機器のコストに影響を与える多くの議論の領域のほんの一部です。常に、最低の鋳造コストと最高の鋳造品質は、最高のパターンコストを生み出すより洗練されたパターン機器から進化します。
8。機械加工
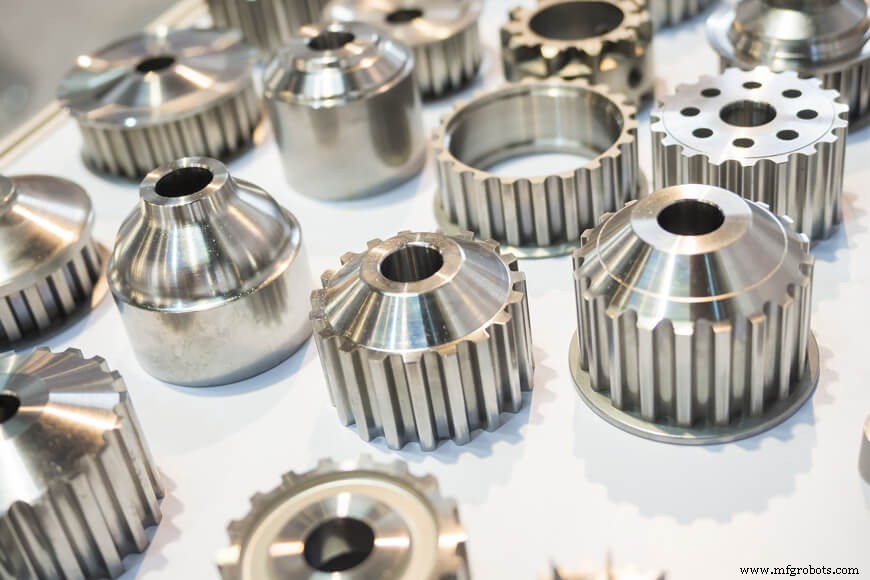
余分な不要な材料を機械的に除去するプロセスは機械加工と呼ばれ、高レベルの寸法精度が必要な場合に不可欠なプロセスです。そのため、特に鋳造された部品または製品の公差が厳しい場合は、必要に応じて、ある程度の追加材料を機械加工許容量に割り当てる必要があります。
公差とは、特定の製造方法で達成可能な寸法精度を指します。金型の膨張、凝固収縮、および熱収縮はすべて、生砂型鋳造プロセスでの完成部品の公差に影響を与えます。したがって、鋳造部品の公差には制限があります。より厳しい公差が必要な場合は、その後の機械加工が一般的に使用されます。
すべてのサプライヤーファウンドリが社内で機械加工を提供しているわけではありませんが、部品の特定の要件を満たすために機械加工によって変形できる鋳造製品を製造する責任があります。この目標を達成するには、顧客のエンジニアリングおよび購買スタッフと鋳造生産者の間で緊密な関係を維持する必要があります。協調的なアプローチでは、次の点を考慮する必要があります。
- 鋳造プロセスとその利点と制限
- すべての機械加工面のクリーンアップを保証するための機械加工許容量(荒削り後に仕上げに残された材料の量)
- 機械加工中に部品を固定するクランプおよび固定装置の適用に関連する製品設計
- 材料仕様と熱処理の選択、および
- 生産される部品の数量。
すべての機械加工要件が達成可能かどうかを判断するために、最初に製造されたすべての鋳造設計をチェックする必要があります。これを実現する1つの方法は、サンプル鋳造の完全なレイアウトを作成し、機械加工手順を必要とするすべての表面に適切な機械加工ストック許容値が存在するかどうかを確認することです。
より単純な設計の場合、鋳造の完全なレイアウトは必要ない場合があります。ただし、加工寸法がより複雑な場合は、鋳造を徹底的にチェックすることをお勧めします。これは、ターゲットポイントを考案し、すべての機械加工された表面を示すために線をマークアウトすることで実行でき、生産のすべての段階で一貫性を確保します。
9。生産と納品のスケジュール
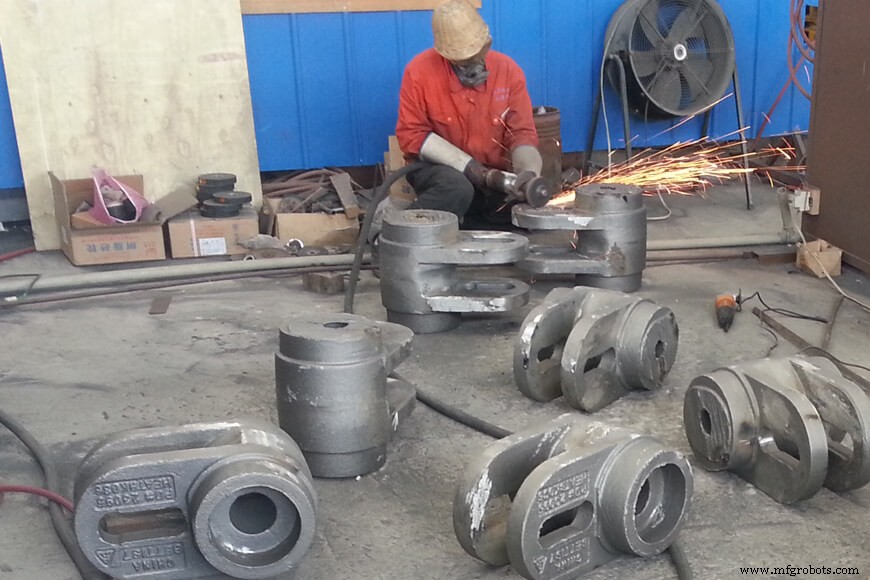
短期的および長期的なニーズの両方を満たす適切なショップを見つけるには、配達と需要の要件の伝達が不可欠です。
上記の他のすべての考慮事項に加えて、顧客とサプライヤの両方が生産スケジュールのニーズを認識することが不可欠です。たとえば、顧客が6週間以内に生産部品を納品する必要がある場合、そのような作業を見積もることができる、または見積もることができるファウンドリの数が大幅に制限されます。ましてや、このような厳しいスケジュール内で確実に生産を実行することもできます。逆に、クライアントが関心のあるファウンドリを探して、詳細で長期的なニーズを確認する場合(たとえば、パーツ「x」の年間600個、注文ごとに150個のロットで生産され、最初の生産実行は早ければ必要です)今から6か月後)、彼らはさらに多くの関係者が関心を持ち、彼らのニーズに対応できるようになるでしょう。
見積もりのリクエストは、必要な納期のかなり前に行う必要があります。金属鋳造プロセスは複雑であるため、プロジェクトのリードタイムは最大24週間で簡単に実行でき、鋳造品を注文すると完全な生産と納品が可能になります。この時間には、商業上の考慮事項(財務管理)、パターンとツールの構築、サンプリング、検査、パターンの変更、(完全な)生産セットアップ、生産、ポストプロダクションプロセスなどが含まれます。
鋳造品の注文
金属鋳造プロジェクトのアウトソーシングを成功させるには、協力的な取り組みが不可欠です。サプライヤーのファウンドリは、設計の初期段階から製造、製品の納品に至るまで関与する必要があります。
サプライヤーファウンドリが見積もり要求を確認すると、クライアントと協力してすべてのコストを評価し、製品の目標を決定します。ファウンドリの専門家が生産前にプロジェクトを評価し、最も経済的なソリューションを実現するための最良の材料と方法を推奨するため、適切な計画はファウンドリとクライアントの両方に利益をもたらします。
鋳造のニーズについて可能な限り正確で詳細な情報をファウンドリに提供することにより、顧客は多くのフィードバック、質問、および(詳細が確認されたら)利害関係者からの価格設定を受け取ることを期待できます。適切な準備により、注文プロセスが合理化され、時間が節約され、製品エラーの可能性が減少します。
製造プロセス