新規購入または再構築?困難な保守決定のための体系的なアプローチ
製造業の世界では信頼性について誤解があり、工場、管理者、技術者、信頼性の専門家と世界中の製造工場での最終的な結果。誤解は、信頼性に対するリスクベースのアプローチに根ざしており、生産性の向上を適切に特定できず、コストの増加につながる可能性があります。
一部の信頼性の専門家が犯している間違いは次のとおりです。生産機械またはプロセスが工場フロアで故障したときに答えを探すとき、彼らは故障の根本原因を分析するのではなく、製造プロセスのみに焦点を当てるリスクベースのアプローチを取ります。
統計によると、保守および修理の注文の50%に部品が必要です。プラントの運用費用の最大20%が保守関連であり、保守MRO在庫の73%が非アクティブであるため、信頼性と保守の資本支出および費用予算の管理により、信頼性アプローチの改善が困難になります。
幸いなことに、別のアプローチがあります。プロセスレベルの分析は間違いなく重要であるため、信頼性の専門家は、生産性の向上と稼働時間の増加を試みる際に製造プロセスを評価することは間違いありません。一部の信頼性部門が誤りを犯しているのは、根本的な原因を掘り下げていないことです。必要なのは、プロセスをさらに数ステップ進め、データの傾向を分析して、システムレベルのコンポーネントが失敗する方法と理由を理解するためのアプローチです。
このホワイトペーパーでは、プロセスレベルの分析のみに焦点を当てたリスクベースのアプローチに固有の問題について検討します。ソリューションの概要を説明します。これは、要因の調査、障害の排除と継続的な改善に役立つ是正措置の開発と実装を含む、コンポーネントレベルの分析を含む戦略の拡張です。次に、このペーパーでは、信頼性アプローチを最新化するときにメーカーが期待できる結果を確認します。
信頼性へのリスクベースのアプローチ
製造施設では、信頼性エンジニアは通常、バリューストリームマッピング戦略を使用して、原材料を完成品に変換するプロセスの各フェーズを特定し、ワークフローのすべてのステップを詳細に分析します。生産設備はバリューストリームの重要な部分であり、信頼性エンジニアは、最高のパフォーマンスを確保するために、すべてのコンポーネントが可能な限り信頼できることを確認する必要があります。
信頼性戦略の一環として、信頼性エンジニアは各コンポーネント(電気システム、油圧など)を特定し、各システムを系統的に処理し、コンポーネントの障害が生産にどのように影響するかを評価します。
たとえば、信頼性エンジニアは、油圧ラインを障害点として特定し、リスクベースの戦略を使用して、ラインの交換部品の供給を維持したり、冗長性を構築して運用を継続または取得したりすることを含む緩和計画を作成する場合があります。システム障害が発生した場合、すぐに軌道に戻ります。
これらは必要な手順かもしれませんが、信頼性の専門家がシステムコンポーネントレベルではなくプロセスレベルから信頼性を攻撃する場合、コストと不要な支出につながる決定を下す可能性があります。
複雑なプロセスシステムの交換に関連する多額のコストであろうと、展開されない可能性のあるMROコンポーネントの在庫に資本を閉じ込めることであろうと、信頼性に対するリスクベースのアプローチは、生産ラインの故障を防ぐための非効率的で費用のかかるアプローチです。
リスクベースのアプローチの問題は、コンポーネントである可能性が高い障害の根本原因に対処していないため、十分に進んでいないことです。特定のコンポーネントにはいくつかの障害点があります。
老朽化したコンポーネントや廃止された製品、設計上の欠陥、誤認された部品は、コンポーネントレベルで機器の故障を引き起こす可能性のある要因のほんの一例です。
信頼性アプローチを真に近代化するには、信頼性の専門家は、システムレベルのコンポーネントが失敗する方法と理由を理解する必要があります。信頼性へのコンポーネントレベルのアプローチは、障害の根本原因をより適切に定義し、在庫への投資と将来のCAPEX投資を削減します。
失敗するすべてのコンポーネントの背後にはストーリーがあることを覚えておくことが重要です。信頼性の専門家は、ストーリーがスクラップやゴミ箱で失われないようにするための措置を講じる必要があります。図1に示すように、信頼性、メンテナンス、スペアパーツが重要な役割を果たします。
<中央>
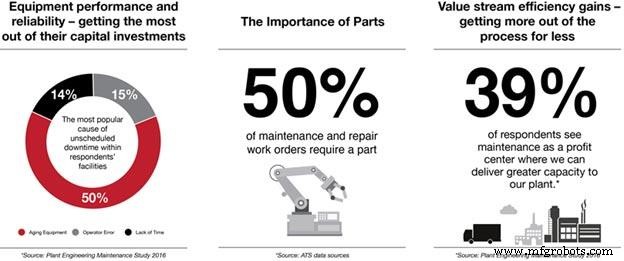
図1.信頼性、メンテナンス、スペアパーツの重要性
老朽化したサーボモータードライブの実際の例を考えてみましょう。これは、複数の生産ラインの障害を引き起こす廃止された製品でもあります。リスクベースのアプローチを使用して、信頼性エンジニアは、ランダムなボード障害が耐用年数を超えたドライブを示していると判断し、生産の遅延を最小限に抑えるためにインストールベースを置き換えるCAPEX計画を実装する場合があります。
ただし、信頼性エンジニアがコンポーネントレベルの戦略を追求する場合、障害点の調査には、ランダムな回路基板の障害が経年によるものであると判断する根本原因分析が含まれます。
信頼性エンジニアは、回路基板の再構築手順を開発し、古いコンポーネントを新しいプレミアムコンポーネントに置き換えることができます。実際のシナリオでは、このアプローチにより、障害が54%減少しました。
信頼性エンジニアは、プロセスレベルの解決策だけに焦点を当てるのではなく、このように問題の根本原因に対処することで、コンポーネントの耐用年数を延ばすだけでなく、時間の経過とともに故障率を下げることができました。以下の図2に示されている傾向チャートは、進化する再構築手順標準に関連する障害の減少を示しています。
<中央>

図2.進化する最小基準に相関する故障率の低下
設計上の問題も、生産設備の故障の一因となる可能性があります。たとえば、信頼性エンジニアは、モータードライブで繰り返し発生する制御盤の故障を分析し、制御盤が過熱したために故障したと判断します。
信頼性エンジニアがプロセスレベルの要因のみを考慮している場合、是正措置は、在庫の最小/最大を設定して、生産の遅延を最小限に抑えるためにモータードライブの交換部品の在庫をすぐに利用できるようにすることです。
ただし、信頼性エンジニアがコンポーネントレベルの戦略を追求する場合、障害点の調査には、設計上の欠陥を発見する根本原因分析が含まれます。実際の例では、モータードライブにヒートシンクに近すぎる制御ボードがあり、コンデンサが故障することがわかりました。
根本原因を特定した後、製造業者は、他の設備の事前リコールと、ヒートシンクから制御ボードを移動する結果となった設計ソリューションを含む修正計画を実装しました。これにより、障害が96%減少しました。下の図3に示されています。
<中央>
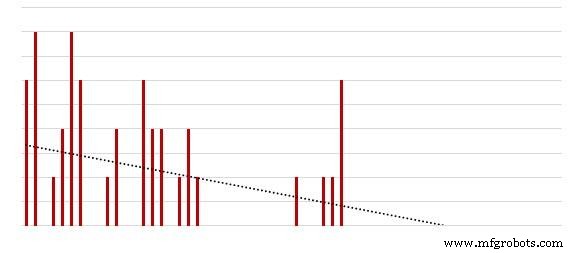
図3.スクラップ率の削減
プロセスレベルのアプローチが不必要な支出と故障の増加につながる可能性のある3番目の実際の例には、部品の誤認が原因で圧力トランスデューサの取り付けが正しくないという問題があった工場が含まれます。
製造業者は、単一の部品番号でさまざまな用途向けのトランスデューサーの複数のモデルを在庫していました。リスクベースのアプローチでは、是正措置は、圧力トランスデューサーが故障したときに在庫が確実に利用できるように、在庫の最小/最大を設定することでした。
信頼性エンジニアがコンポーネントレベルの評価を実施し、圧力トランスデューサが正しく取り付けられていない問題を特定しました。信頼性エンジニアは、設定された圧力パラメーターごとにトランスデューサーをストックし、パラメーターごとに新しいSKUを確立するための修正計画を実装しました。その結果、下の図4のグラフに示すように、計画の実施に伴い、障害は37%減少しました。
<中央>
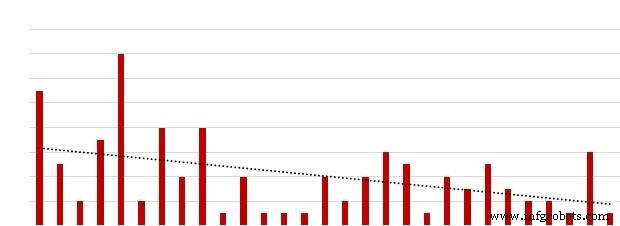
図4.トランスデューサーの故障の減少
これらの3つの例が示すように、これらのシステムレベルのコンポーネントが失敗する方法と理由を理解することは、真の信頼性パフォーマンスを確立するための鍵です。プロセスレベルを超えてドリルダウンすることにより、信頼性エンジニアは根本原因を分析し、稼働時間を改善し、運用コストを削減し、効率を向上させるソリューションを開発することができました。新しいテクノロジーも、効率を達成する上で重要な役割を果たすことができます。
たとえば、積層造形(3D印刷)は、コンポーネントレベルの信頼性を向上させるためにも使用できる新しいテクノロジーです。アディティブマニュファクチャリングテクノロジーは急速に変化していますが、早期の摩耗や故障を防ぐためのソリューションを設計するための効果的な方法です。
プロトタイプは非常に費用対効果の高い方法で製造でき、設計が元の設計アプリケーションの適合、形状、および機能の要件を確実に満たすようにします。チタンなどのさまざまな材料を積層造形プロセスで使用して、コンポーネントを動作環境ではるかに耐久性のあるものにすることができます。
コンポーネントレベルのアプローチの有効性を示す多くの例があります。コンポーネントの障害に関する情報を収集することで、信頼性エンジニアは単純な「迅速な」改善を特定し、大幅な節約につながる標準的な作業手順と技術者トレーニングプログラムを作成できます。
信頼性へのコンポーネントベースのアプローチ
プロセスレベルの分析を超えてサブシステム内のコンポーネントレベルの問題に焦点を当てる信頼性部門は、結果を大幅に改善できますが、そのためには、障害点と軽減戦略について別の考え方が必要です。
コンポーネントレベルの戦略への移行に従事している信頼性の専門家は、相手先ブランド供給(OEM)で使用されている方法やサードパーティの専門知識など、外部の視点から利益を得ることができます。
基本的な改善は、信頼性に基づく改善の追加の機会となる可能性があり、5-S、部品の識別と保管のベストプラクティス、トラブルシューティングに使用されるコンポーネントの認証手順のテスト、ストーリーがないことを確認するためのコアトラッキングなど、保管室プロセスの実装が含まれる場合があります。ごみ箱に捨てられます。
保守標準の開発も、RCAプロセスに技術リソースを関与させることや、コンポーネントレベルの部族の知識を文書化するシングルポイントのレッスンなど、重要なコンポーネントになる可能性があります。
新しい信頼性パラダイムを完全に受け入れるには、抽象的な理論を超えて、実践的な経験を活用して新しいソリューションを開発する必要があります。チームの専門知識に幅広くアクセスすることで、より良い結果と価値を提供するための強いコミットメントにつながる可能性があります。
真の信頼性パフォーマンス
信頼性に対するリスクベースのアプローチは、残念ながらメーカーのコストの増加につながる可能性があります。ただし、それでも価値のある分析であり、信頼性の専門家の中核機能であり続ける必要があります。
しかし、信頼性に関する現代の理解には、障害の本当の根本原因は、製造プロセス自体ではなく、コンポーネントである可能性が高いという認識が含まれています。さらに、より信頼性が高く、より収益性の高い成果を達成するために、新しいテクノロジー、最先端の分析、およびベストプラクティスを採用する必要があります。
実際の真の信頼性パフォーマンスの一例は、修理可能な部品の在庫を管理するための新しいアプローチを実装した乗用車および商用車の交換用タイヤのリーダーとして認められている経験にあります。
サードパーティの信頼性専門家が会社の固有の状況を評価し、オンサイトの修理可能な部品管理プログラムを通じて部品プログラムを管理する計画を作成しました。より積極的な部品管理プログラムにより、製造業者は部品の故障が53%減少したことを確認しました。修理可能な部品管理プログラムでは、部品の在庫を15%削減することもでき、その結果、大幅な節約になりました。
稼働時間とマシンの可用性が向上したことで、メーカーは製品に対する需要の高まりに効率的に対応することができました。会社の企業保守部門の上級管理者は、サードパーティの専門知識を利用し、会社の修理可能な資産の信頼性の向上に注力することで、製造業者は製造効率を向上させながら全体的なコストを削減できると述べました。
真の信頼性性能の価値を示す別の例では、一流の自動車サプライヤーが信頼性の専門家と協力してコンポーネントレベルの問題を改善し、ボールねじの耐用年数の問題を特定しました。ボールねじは複数の機械に配置され、ドイツからカスタムオーダーする必要があったため、信頼性が問題でした。つまり、自動車サプライヤーは、長いリードタイムや散発的なリードタイムに対処する必要がありました。
信頼性へのよりスマートなアプローチ
世界中の製造会社は、プロセスレベルの改善に専念することで、絶好の機会を逃しています。これは、全体的な信頼性戦略の重要な部分ですが、利用可能なすべての生産性の向上とコスト削減を実現するのに十分な深さではありません。
コンポーネントおよびサブシステムレベルで障害の根本原因を分析することを怠ることにより、リスクベースのアプローチに固執する信頼性部門は、会社に時間とお金を費やしています。
このホワイトペーパーで取り上げた例が示すように、より良い方法があります。多くの場合、障害点はコンポーネントレベルで発生します。プロセスレベルのレビューを超えて根本原因分析を含めるようにアプローチを拡張する信頼性の専門家は、設計上の欠陥、コンポーネントの古さ、不適切なインストールなどの要因によって引き起こされる問題を特定して軽減できます。
システムレベルのコンポーネントが失敗する方法と理由をよりよく理解し、新しい視点を含めるように考え方を変えることで、信頼性の専門家はあらゆるレベルで結果を改善できます。 IoT対応部品などの新技術の支援を受け、データ分析を使用して行動をより効果的に推定し、予知保全プログラムなどの戦略を実装することで、最新の信頼性専門家は、信頼性の高い部品、信頼性の高いプロセス、信頼性の高い節約を実現するために機械を機能させることができます。
機器のメンテナンスと修理