ハイブリッド、大判添加剤工具:大きな部品用のより軽く、より速く、より安価な金型
30年以上の間、商用航空はますます複合材料を採用してきました。実際、今日の主要な民間航空機のいくつかのモデルの重要な構造コンポーネントの半分以上は複合材料です。これらの材料の使用が部品の量とサイズの両方の点で成長するにつれて、これらの部品をより迅速にプロトタイプ化して製造するためのツール、特に手頃なツールを構築することがますます困難になっています。たとえば、エアバスSE(オランダ、ライデン)のA350 XWBの翼は、それぞれ長さ32メートル、幅6メートルで、これまでに製造された中で最大の複合航空構造のいくつかを表しています。
「現在、市場には画期的な製造技術があり、ツールの進化に大きな一歩を踏み出すことができ、複合航空機コンポーネントの開発で直面している課題に対処するのに役立ちます」と、複合製造エンジニアのM.PilarMuñozLopezは述べています。エアバスのスペイン、イジェスカスの工場。「将来に備えるために、これらの技術、機能、制限を調査することが重要です。」
ツーリングが航空構造部品の総プログラムコストのかなりの割合を占め、それらの部品のサイズが大きくなっていることを考えると、コストとリードタイムがより低い新しいツーリングオプションが必要です。プロトタイプおよび少量生産の航空構造部品用のハイブリッド、大判、付加製造(LFAM)ツールに関する興味深い研究が、Airbus、Northrop Grumman Aeronautics Systems – Aerospace Structures Business Unit(Clearfield、Utah、US)および大学によって最近完了しました。デイトン研究所(UDRI、デイトン、オハイオ、米国)の有望な結果をもたらしました。
熱膨張の問題を抑える
炭素繊維強化プラスチック(CFRP)の航空構造の大部分は、エポキシマトリックスプリプレグから製造されています。このような部品を成形するには、180°C / 356°Fまでのオーブンまたはオートクレーブ硬化温度に耐える必要があります。また、CFRPの(線形)熱膨張係数(CLTEまたはCTE)が非常に低いため、室温および高温で工具と成形材料のCLTEを可能な限り一致させることが重要です。これにより、金型が寸法を維持し、結果として得られる部品も寸法要件を満たすことができます。最終的な構造の歪みや応力を回避するために、成形品の材料よりも速く冷却する工具材料の使用を回避することも重要です。結果として、大きなCFRP空気構造を成形するために使用される最も一般的なツールは、CFRP自体、またはCLTEが低いことで知られるニッケルと鉄の鉄合金であるインバーのいずれかから作られています。どちらもコストがかかり、かなりのリードタイムがかかる可能性があります。さらに、インバーは機械加工が難しく、時間もかかり、出荷も大変です。鋼またはアルミニウムの工具はコストを削減できますが、CLTE値が比較的高いため、多くのアプリケーションでの使用が制限されます。特に、大きな部品や長い部品を成形する場合はそうです。
多くの公的および民間部門の研究は、熱可塑性材料で印刷された付加的に製造されたツールを評価し、熱硬化性ラミネート複合材料を製造するための低コストやリードタイムの短縮などの利点を提供する可能性があると結論付けました。残念ながら、ポリマーベースのLFAM工具には、工具の多孔性などの問題があり、硬化温度/圧力で大幅な真空損失を引き起こす可能性があります。これを解決するには、追加のツール充填のやり直しと表面コーティングが必要です。さらに大きな課題は、押出/印刷中の面内原料フィラーの位置合わせにより、異方性の高いCLTE値です。これにより、X軸およびY印刷軸よりもZ軸の膨張/収縮の差が5〜10倍大きくなる可能性があります。そのため、寸法的に正確な部品を繰り返し再現性のある方法で入手することが困難になります。特に、部品が大きい場合、アスペクト比が高い場合、および/または複雑な表面を特徴とする場合は困難です。
「添加剤工具に関心のある人は誰でも、多孔性と制御されていない熱膨張の同じ問題に直面しており、これらの問題に対処する効果的な方法はほとんどありません」と、構造材料部門の高度な製造プロセス開発のUDRIチームリーダーであるScottHuelskampは説明します。 「AMツールを使いたいと思っている人はたくさんいますが、彼らは誰かがこれらの問題を解決するのを待っています。」
工具費とリードタイムを削減するAMの可能性を考えると、業界は、新しい印刷可能な材料、プリンターハードウェアの変更、革新的なモデリングアプローチを模索することにより、拡張の問題に対処することにかなりの努力を注いできました。たとえば、一部のグループは、CLTEの差異に対処するためのAMツールを設計するための「補償値」を開発しました。ただし、Huelskampは、どのを決定することに注意しています。 使用する補償値は難しく、エラーが発生しやすくなります。また、このようなアプローチは、メスキャビティツールや、ツールの熱サイクル中に部品に損傷を与える可能性のあるダイロック状態を作り出すトラップ機能を備えたツールには効果がありませんでした。
「その種の問題を解決する補償要素はありません」と彼は付け加えます。 「これまで、高温での低い等方性CTE値の必要性に完全に対処したAMツールの研究はありません。この特性がないと、工具のサイズと形状は常に制限され、大きな工具は硬化温度での寸法誤差が大きくなります。」
LFAMツーリングの課題を解決するための新しいアプローチを試すために、18か月のプロジェクトが、Institute for Advanced Composites Manufacturing Innovation(IACMI、米国テネシー州ノックスビル)の支援の下、米国の支援を受けて、いくつかのメンバー企業によって実施されました。エネルギー省およびジョブズオハイオ州(オハイオ州コロンバス)。チームはUDRIによって率いられ、エアバスとノースロップグラマンが含まれていました。これらの組織は以前、IACMIの内外で他の研究に協力していたため、お互いの能力に精通していました。
「ブルートフォース」アプローチ
UDRIは、すでにAMツールの研究に取り組んだ経験が豊富で、米国AMコンソーシアムであるAmerica Makes(Youngstown、Ohio、U.S。)の積極的なメンバーです。さらに、この研究所は、金属製の裏打ちを備えたAM構造を含む米空軍の研究を行い、Big Area Additive Manufacturing(BAAM)プリンターのプロデューサーであるCincinnati Inc.(Harrison、Ohio、US)と協力して純粋なAMツールを開発しました。
「3Dプリンター用の新しい原料についてもカスタムコンパウンダーと協力していましたが、何も進んでいないようで、他の誰かが私たちよりも成功していることに気づいていませんでした」とHuelskamp氏は振り返ります。 「そのとき、私たちは問題に別の方法でアプローチするというアイデアを思いつきました。 AMマテリアルの動作を変更できない場合、またはその動作を直接予測できない場合 、そしておそらく私たちは彼らに私たちが望むように間接的に振る舞うように強制することができます 。」 Huelskampが「ブルートフォース」アプローチと呼ぶものを採用して、UDRIは、従来のを適用することによって航空構造ツールを生成するハイブリッドLFAM研究を提案しました。 CFRPフェイススキンを熱可塑性複合材に AMコア。
プロジェクトの目標は単純でした。航空構造用の大型ツールを作成するための、より安価で高速な方法を見つけることです。チームは、コストを50%削減し、その後のテストのために少なくとも10個の許容可能なプロトタイプまたは少量生産部品を生産するオプションを探しました。
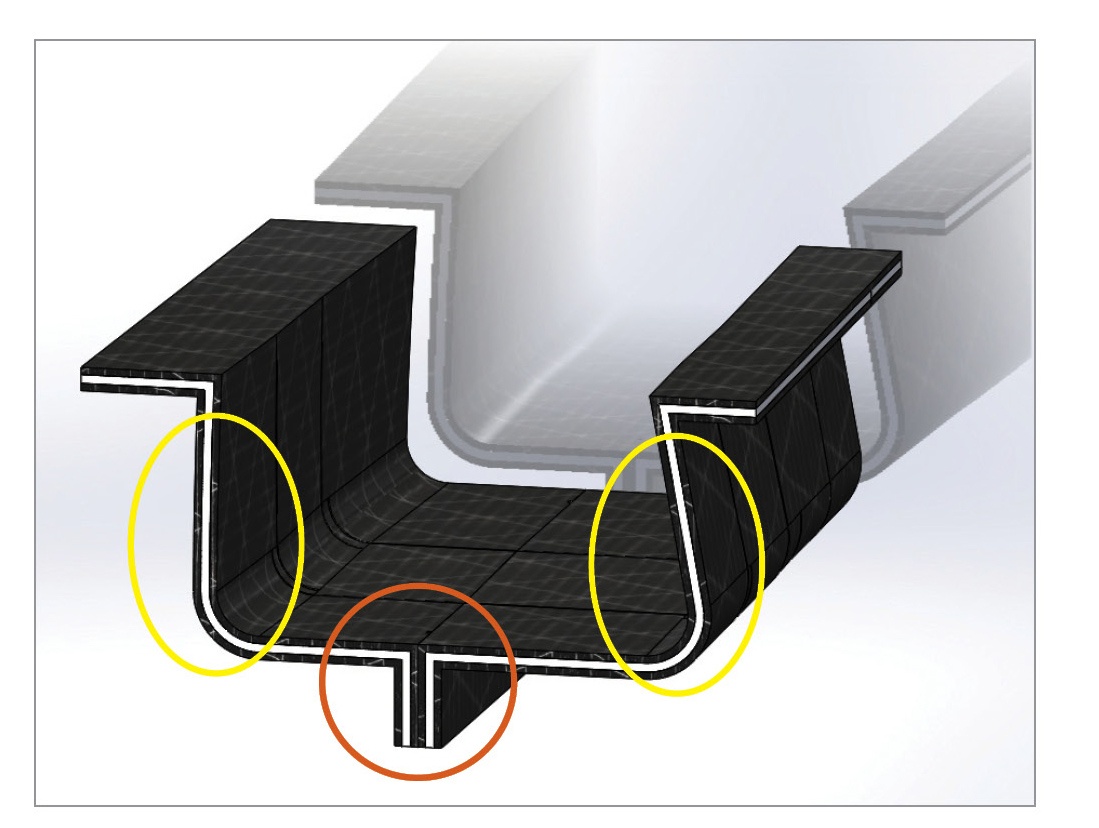
チームは、サンドイッチ構造を使用して、エアバスのツールデータを使用して一般的な翼桁のセクションの片面ツールを作成することを決定しました。 UDRI施設のスペース制限のため、実物大のCスパーの一部のみを成形するための工具を製造する以外は、大きな設計変更は行われませんでした。
メス工具は、ハードツールの表面を使用して重要な部品の形状が形成されるように設計されています。このスパーキャップツールはわずかに内向きの角度を持っていたため、負のドラフトとダイロック状態が発生し、一体型のツールでした。これにより、研究者は、ガスケット/コードストックを使用して密封された分割ツールに設計を変更することになりました。リスクを軽減するために、チームはコンセプトを証明するために0.6メートル/2.0フィートのサブスケールツールから始めました。ツール開発プロセスとそのツールで作成されたプロトタイプパーツがテストされ、機能することが判明すると、チームはプロトタイプテスト用にスパーのより大きなセクションを成形するために、より大きな3.3メートル/ 11フィートの長さのツールを構築しました。
>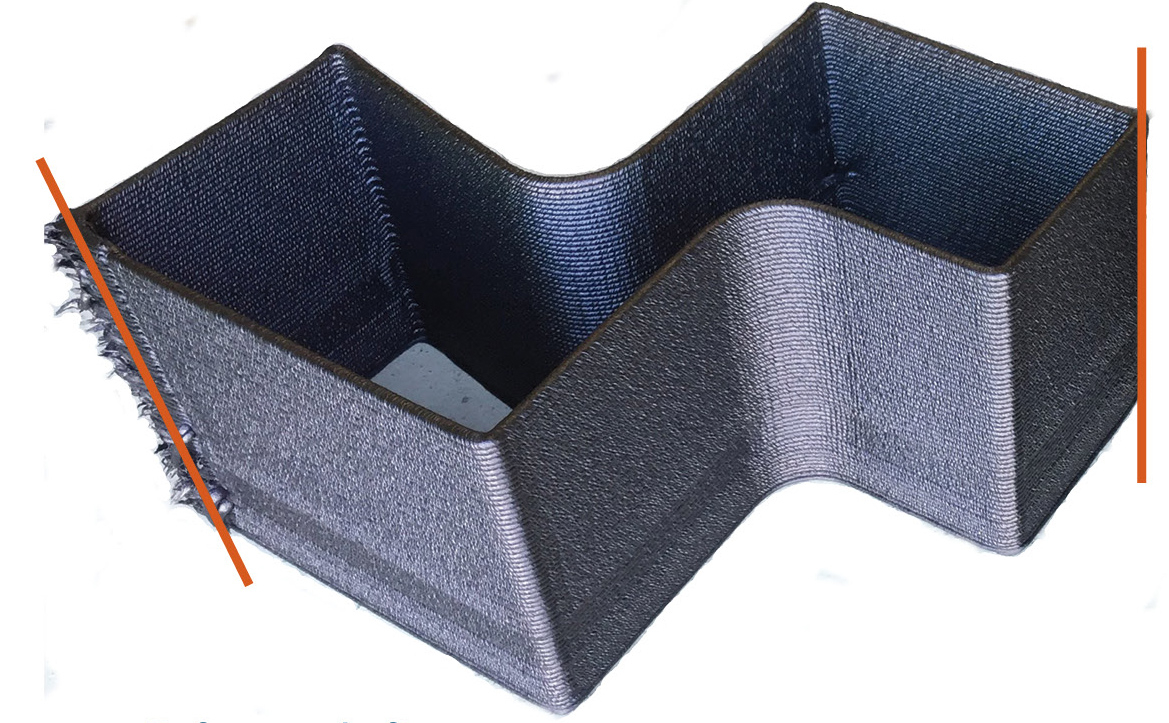
CFRPツールのCLTE値は非常に低く、Invarよりも軽量であり、ツールはプロトタイプ/少量生産部品用であったため、チームはCFRPフェーススキンを使用してAMコアを拘束することにしました。スキンは、Hexcel(Corp.、Stamford、Conn。、U.S。)のHextoolM81エポキシツーリングプリプレグで作成されました。
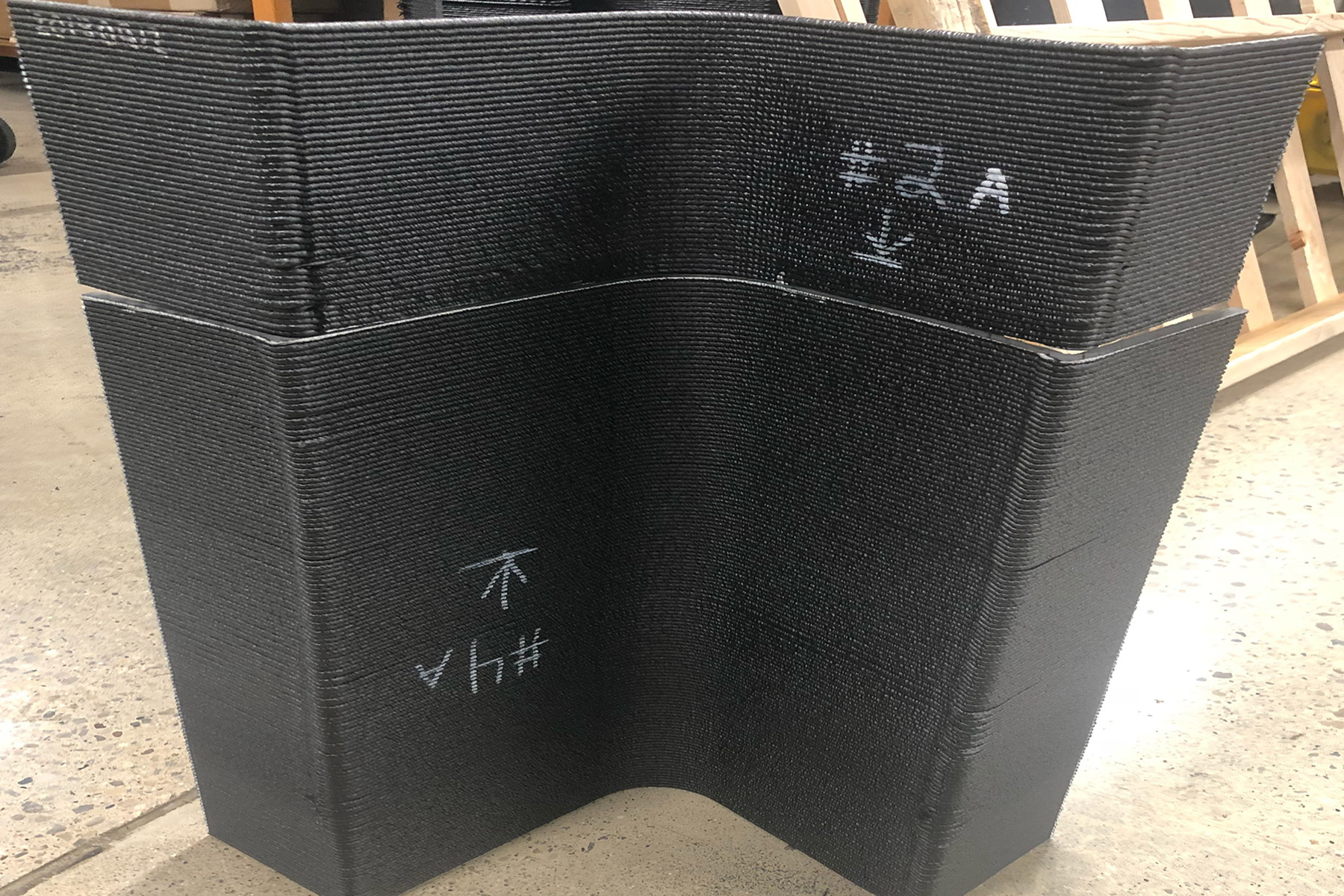
上の画像は、サブスケールの右半分のBAAM印刷ツールの一部を示しており、赤い線は印刷後のカットラインを示しています。下の画像は、セクションが結合された後の右半分のツールを示しています。写真提供者:デイトン大学研究所。
材料のフォーマットは、ヘクセルの8552強化エポキシを含浸させたチョップドカーボンファイバーの2,000グラム/平方メートル/ 59オンス/平方ヤードのマットでした。この材料は、ほぼ等方性であるため、複合工具によく使用されます。これにより、残留応力緩和によって引き起こされる可能性のある工具の動きなしに、金型後の加工が可能になります。
コアがAdditiveEngineering Solutions(Akron、Ohio、US)のCincinnati Inc. BAAM 1000プリンターで印刷され、UDRIとCincinnatiが高温熱可塑性ポリエーテルイミド(PEI)での作業に豊富な経験を持っていることを考えると、彼らはSABIC(Riyadh、Saudi Arabia)の20%短炭素繊維強化PEI(Thermocomp EX004EXAR1 Ultem)を使用して、ニアネットシェイプのコアを印刷します。 (カーボンファイバーの存在により、印刷中にポリマーが安定し、スランプが防止されます。完成した構造では、ファイバーが印刷方向のCLTEを低減します。)コストを低く抑えるために、コアはツーリングマスターとして機能し、フェーススキンは直接ラミネートされました。接着剤なしでコアに、しかしプロジェクト中に開発された知的財産(IP)で覆われているコア表面にいくつかの変更を加えました。このアプローチは効果的であり、複数の熱サイクルの後でも層間剥離はありませんでした。
凝縮製造
従来の航空構造CFRP工具の製造では、最初に低コストのマスターが作成されます。これには通常、オーブンまたはオートクレーブでツーリングボードのブロックを結合し、モノリシック構造を目的の部品形状に機械加工することが含まれます。次に、工具材料をオートクレーブ内のマスター上に置き、袋に入れ、硬化させます。型から外してクリーンアップした後、バッキング構造を工具に接着し、工具の表面をもう一度機械加工して、良好な幾何公差と表面仕上げを確保します。
チームはハイブリッドAMツールを使用して、リードタイムとコストを削減するための凝縮された製造プロセスを開発しました。最初に、ニアネットシェイプコア(ツールマスター)が3Dプリントされました(短炭素ファイバー/ PEI)。次に、CFRPツーリングプリプレグをコアの両側に直接ラミネートしました(サプライヤの推奨に従って、プライ1、4、および7の間にホットデバルクを使用)。次に、構造全体を真空バッグに入れ、オートクレーブで硬化させました。
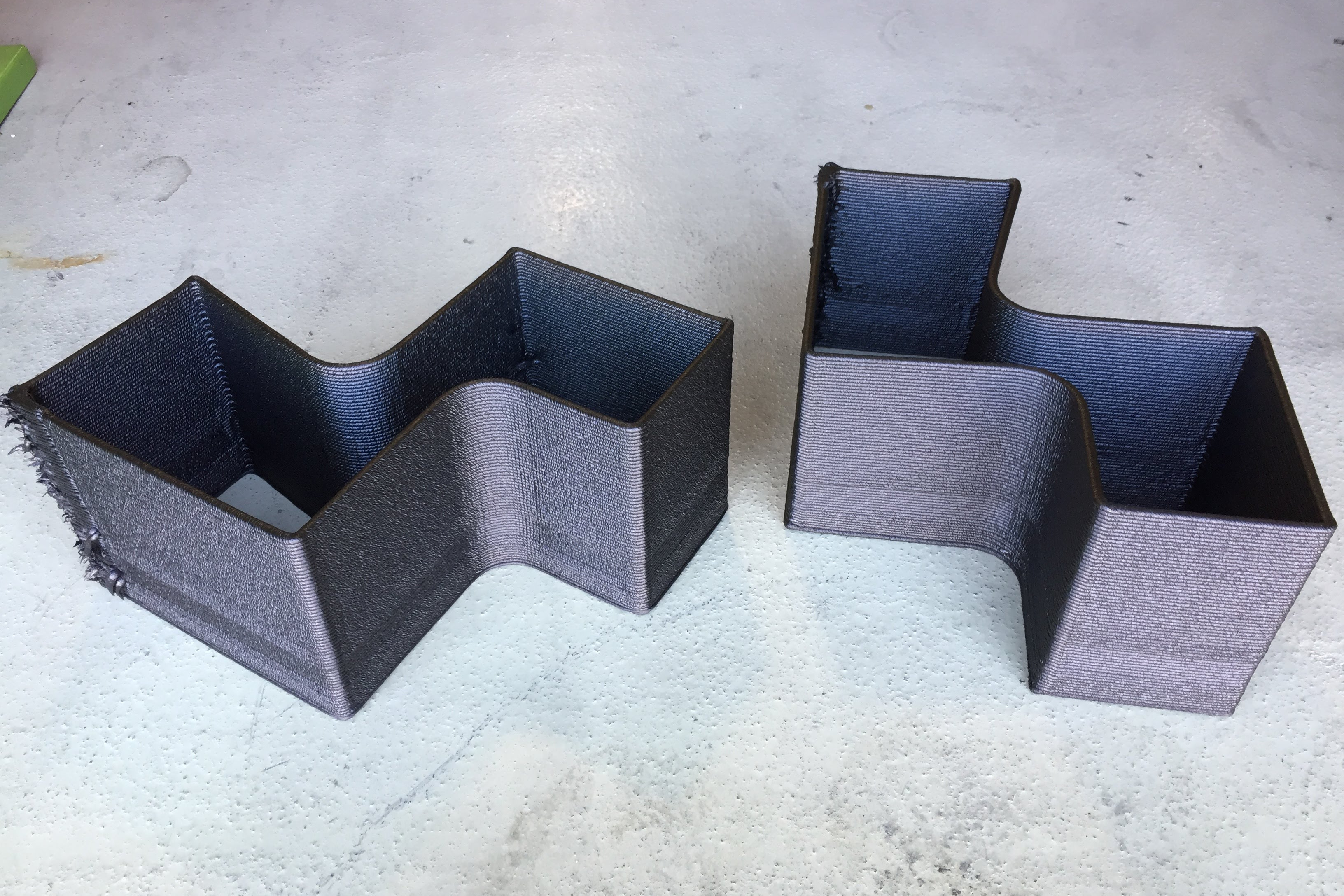
ステップ2:BAAMプリントを中央から左右半分にカットします。
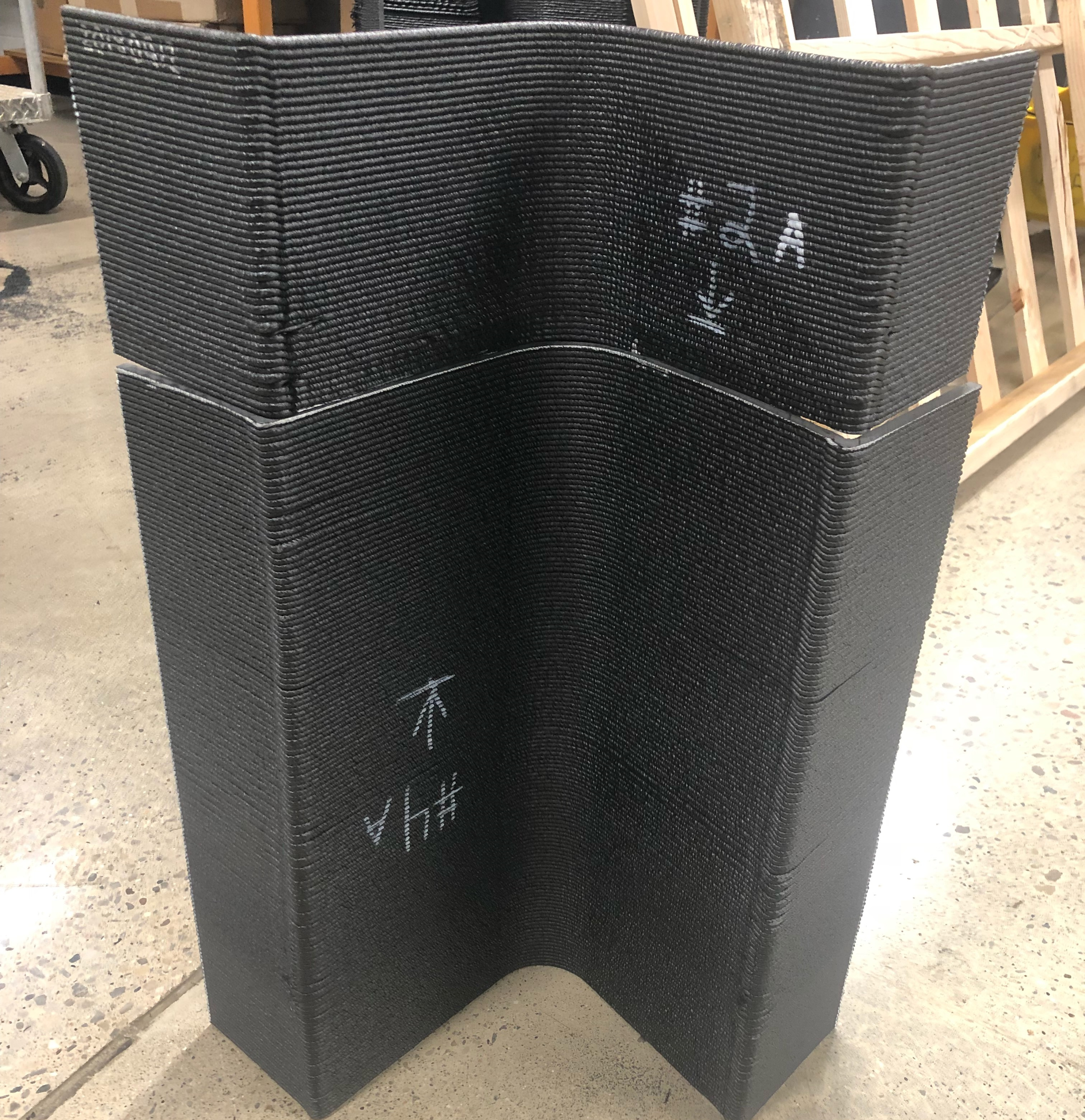
ステップ3:BAAMプリントを接着して必要な長さにし、硬化させます。
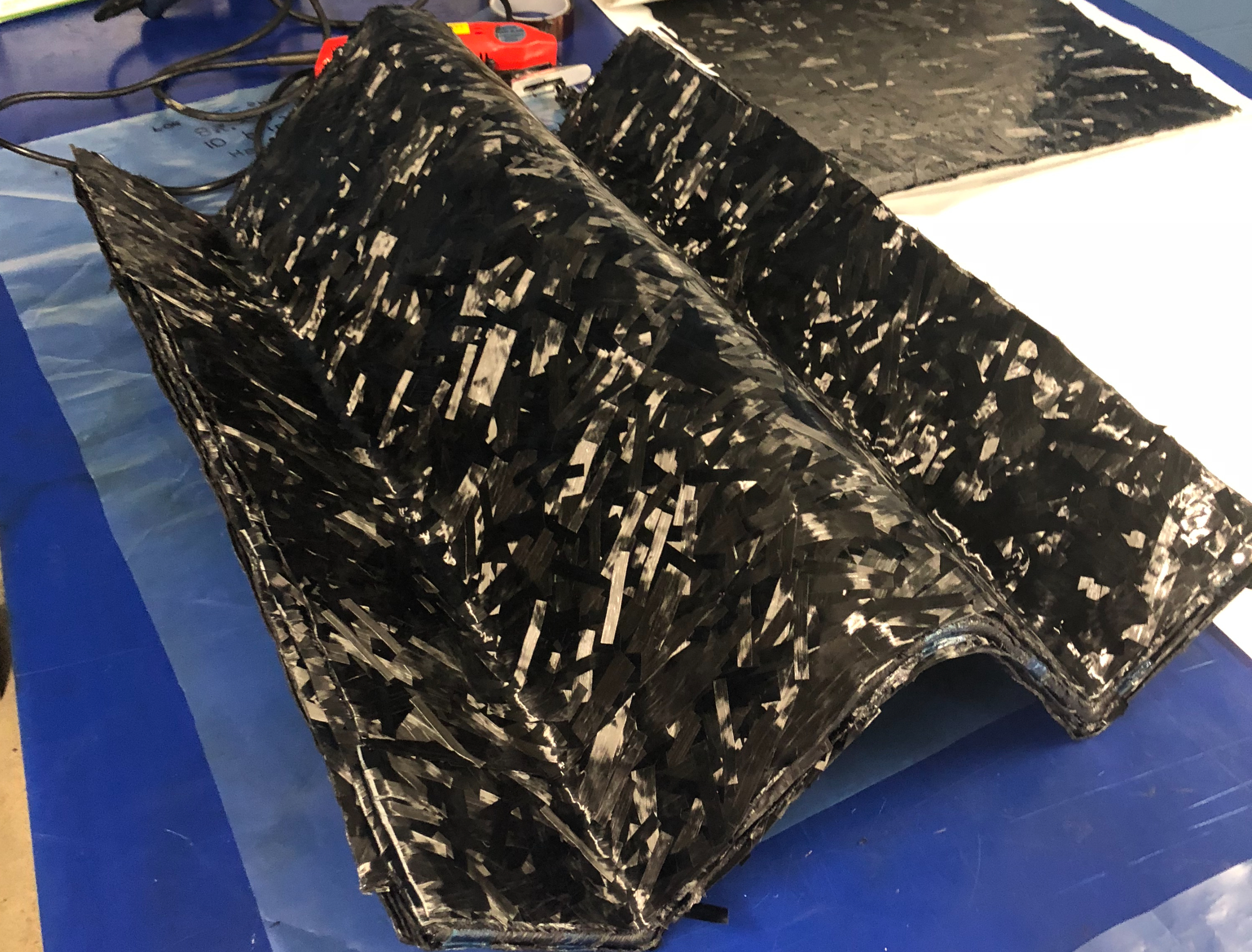
ステップ4:メーカーの指示に従って、ホットデバルクを使用してコアの両側にツーリングプリプレグをラミネートします。
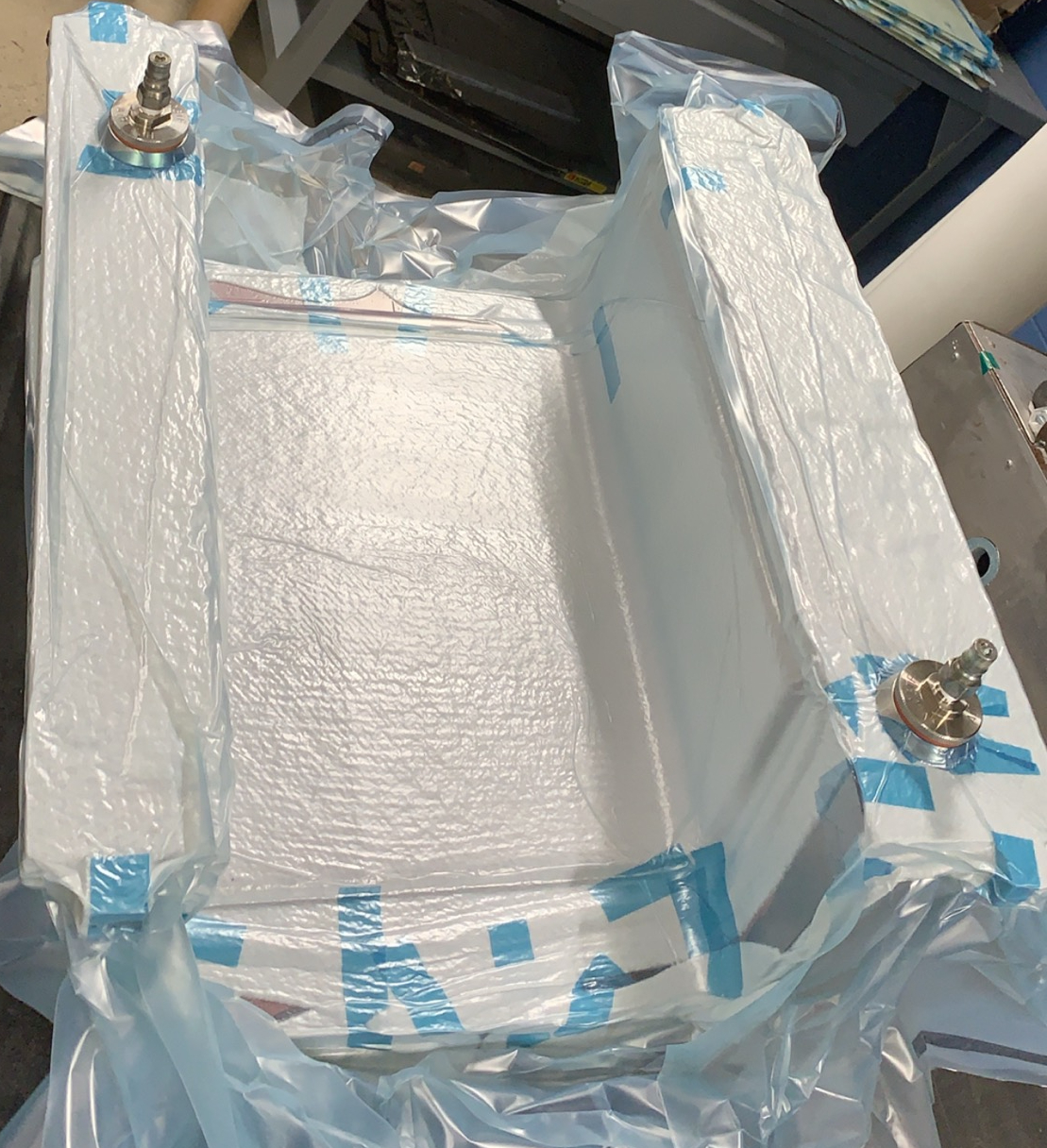
ステップ5:バッグを掃除機で吸い取り、オートクレーブで硬化させます。
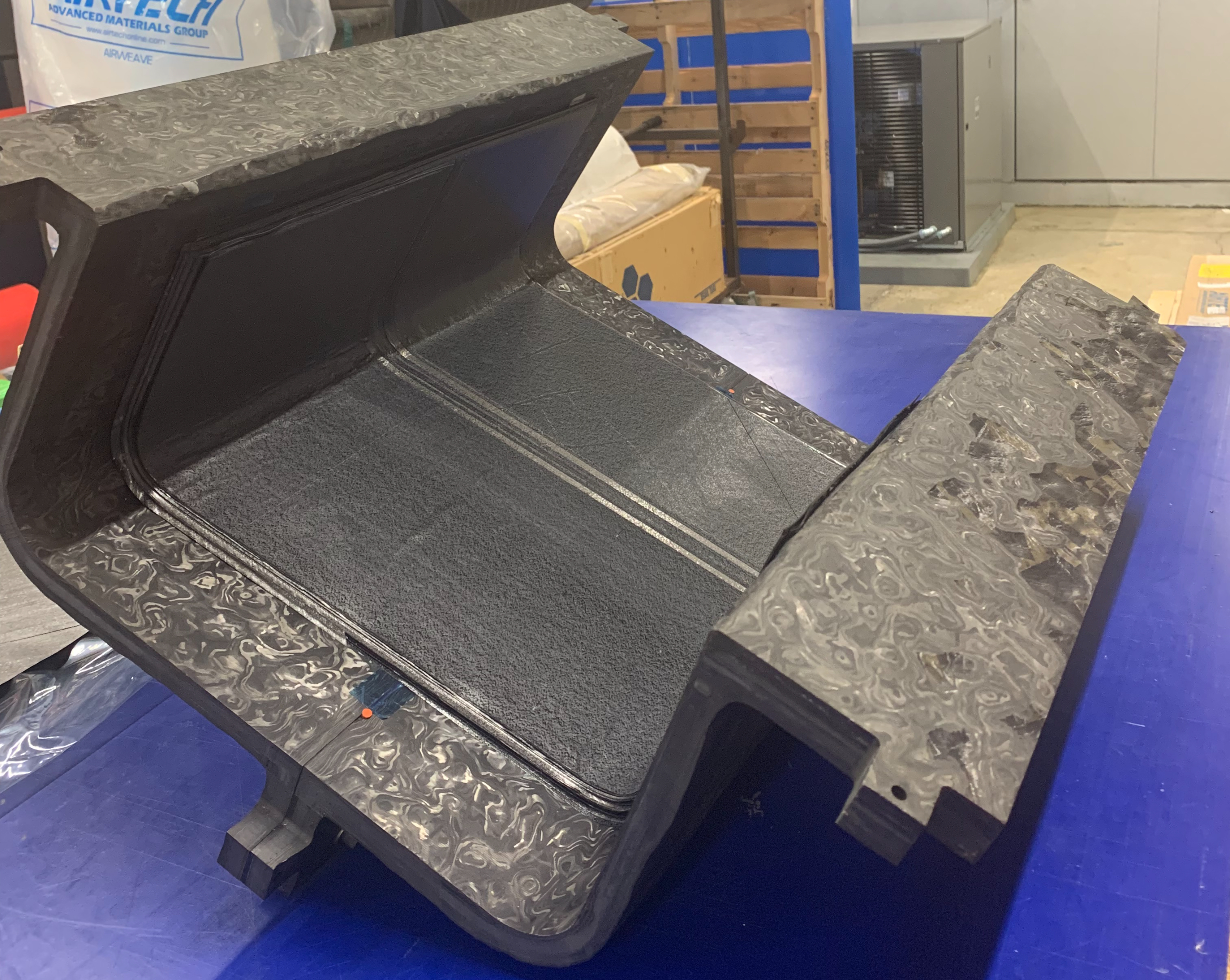
ステップ6:最終的な寸法と表面仕上げを実現するための機械硬化ツール。
前へ次へラミネート硬化中にPEIコアとエポキシスキンの間で良好な接着が達成されたため、接着剤は必要ありませんでした。 CFRPスキンは、AMコアよりも非多孔性で耐久性があるだけでなく、CLTE値がはるかに低いため、温度変化中のコアの動きを物理的に制限します。単一の硬化と単一の機械加工操作のみ—従来の の両方の主要な費用 ツールの製造—最終的な寸法と表面仕上げを実現するために必要でした。また、サンドイッチ構造とツール形状により、横方向の剛性のために金型の上部にリターンフランジがあり、垂直方向の剛性のために金型の中央にボルト継手があり、ボンディング操作が不要であるため、裏打ちは必要ありませんでした。
最初の課題
研究者は、新しいプロセスでいくつかの管理可能な課題に直面しました。
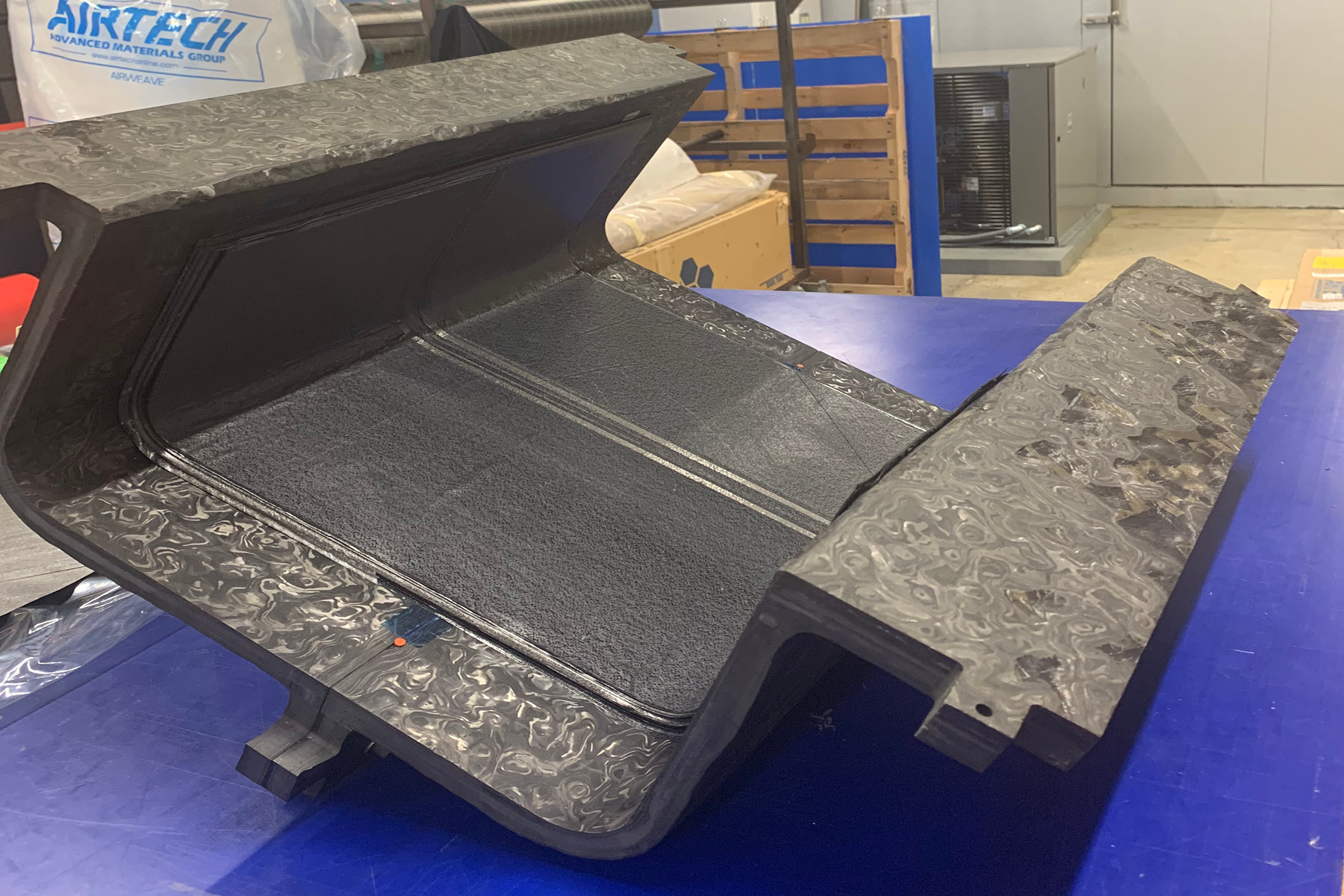
BAAMでの製造を容易にするために、コアの好ましい製造方向は、断面を垂直ビルドとして印刷することでした。 0.6メートルのツールではそれは問題ではありませんでした。ただし、大型のツールの場合、3.3メートルはBAAM1000が垂直方向に印刷できるよりも高かった。プリンタのZ軸の印刷スペースの制限により、研究者は両方のサブスケールツールの長さを半分にしてから、再び左右のセクションに分割することを選択しました(スパーキャップのアンダーカットの問題に対処し、離型を容易にするため)。
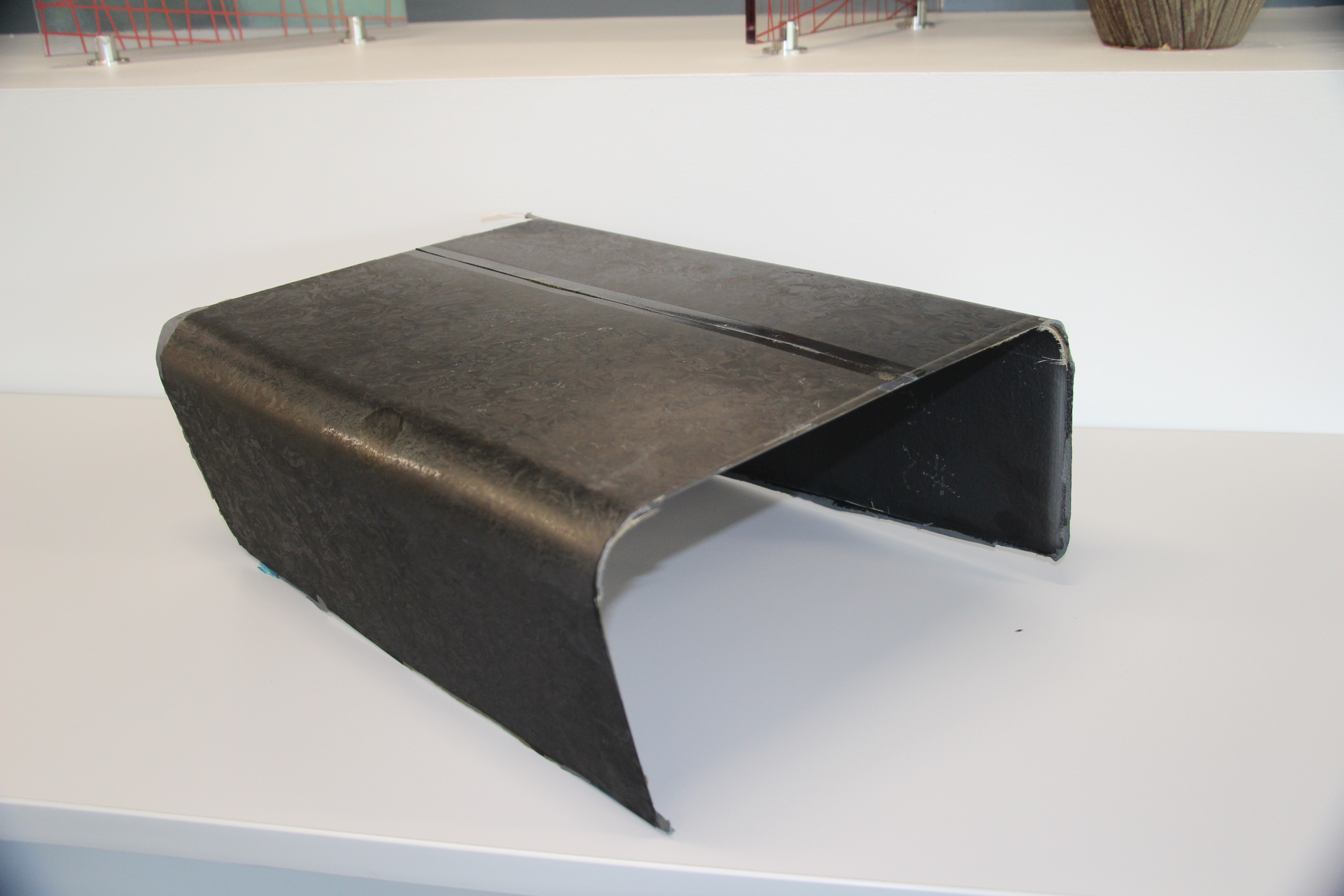
印刷効率を上げるために、ツールのセクションを連続して印刷してから、右側と左側にカットしました。 3.3メートルの長さを実現するために、ヘンケル社(米国コネチカット州ロッキーヒル)のロックタイトEA9394エポキシ接着剤を使用して、右側の2つのセクションを接着し、続いて左側の2つのセクションを接着しました。チームはAMコアを機械加工せずに残しました。これは、低い工具コストと短いリードタイムを達成し、AMコアと両側のCFRPスキンの間に機械的なインターロックを作成するために重要であると感じました。各ツールの半分の裏側は5層のプリプレグでラミネートされ、表側は9層でラミネートされて、硬化後の機械加工中に除去できる余分な材料を提供しました。
暫定結果
AMコアのCLTEを制御することに加えて、プリプレグは、シーラント/コーティングを必要とせずに真空の完全性を維持するピットのない表面を提供しました。このアプローチは非常に成功したため、ガスケットで密封されたマルチピースツール設計の使用が可能になりました。これは、高温で使用されるAMツールではこれまで実証されていなかったと研究者は考えています。さらに、工具の質量が大幅に削減されました。サブスケールツールは、同等のインバー設計で計算された重量の3分の1でした。軽量のCFRPツールは、取り扱いとラックへの保管が簡単であるだけでなく、オートクレーブの加熱/冷却サイクルを短くする必要があります。実物大のCスパーを成形するためのツールでは、その重量の利点により、一部の製造スペースでガントリー/クレーンの重量制限を下回るか上回るかが異なる可能性があります。
重要なことに、0.6メートルのハイブリッドツールのコストは、製造中に業界標準の人件費を使用して計算され、24,136米ドルで、機械加工コストと印刷/ラミネートコストが約50/50に分割されています。対照的に、同一のInvarツールの見積もりは46,775米ドルで、ほぼ50%の節約になります。 3.3メートルのツールのコストは完全ではありませんが、材料/印刷コストは直線的に増加するため、コスト/ユニット長ベースで約30%の節約が見込まれますが、機械加工コストはその影響を軽減する規模の経済を享受します。ハイブリッドアプローチは、エアバスとノースロップグラマンの運用パフォーマンス要件を満たし、ラピッドプロトタイピングまたは低使用ツールのインバーの実行可能な代替手段と見なされるツールを作成しました。工具寿命の調査はこの研究の一部ではありませんでしたが、実証された12サイクルを大幅に超える可能性があります。
プログラムは18か月から30か月に延長されましたが、最終的な印刷時のコアジオメトリが、CAEモデルで予測されたものとどのように異なるかを理解するなど、さらに調査が必要な領域がまだあります。チームはまた、機械加工中にパンチスルーが発生しないように、重要な領域に十分なプライが追加されるように、予測精度を向上させたいと考えています。それでも、チームはこれを成功したプロジェクトであり、将来のLFAMツールにかなりの機会があると考えました。
「ノースロップグラマンは、UDRIによって構築された長さ3.3メートルのハイブリッドツールと、ツールの耐久性と寸法安定性を評価するための独自の自動補強材成形(ASF)プロセスを使用して、3メートルのスパーデモンストレーションパーツを構築することを楽しみにしています」と付け加えます。ノースロップグラマンのテクニカルフェロー、ヴァーンベンソン。
樹脂
- エボニック、STEPプロセス用の3D印刷材料を開発するための添加剤ソリューションの進化
- ヘンケルは積層造形用の材料プラットフォームを提供しています
- EssentiumとLehvossが提携して積層造形用の材料を開発
- ハイブリッドおよび電気駆動列用の新しい熱安定化ナイロン6
- Trelleborgは、工具材料の新しい販売代理店を発表しました
- UAMMI、不可能図形は、米国空軍用の複合部品を構築します
- 3DプリントPAEKパーツのVictrexとBondのパートナー
- AeroLasは、熱可塑性ハイブリッドヤーンの新しい紡績技術を探求しています
- 3Dプリント金型のヒント
- 大きな部品の所要時間を最小限に抑える
- 燃料噴射システム用金属部品の製造とツーリング