専門家インタビュー:金属3D印刷による連続生産の達成に関するSintavia社長Doug Hedges
Sintaviaは、航空宇宙、防衛、石油およびガスなどの重要な産業に金属積層造形サービスを提供する独立したメーカーです。 。
アディティブマニュファクチャリングを使用した金属部品の連続生産に重点を置いて、同社は製造と後処理だけでなく、テストも含む独自のエンドツーエンドのサービスを提供しています、社内研究所での冶金および粉末の特性評価。
最近、Sintaviaは拡張計画を発表し、生産に明確に重点を置いた新しい55,000平方フィートの施設に移転しました。
今週は、Sintaviaの社長であるDoug Hedgesと、同社が高品質の認定金属部品を製造する方法、AMが航空宇宙産業に最適である理由などについて話し合うことができてうれしく思います。 AM業界は、テクノロジーの採用を加速するためにできることです。
シンタビアについて少し教えてください。
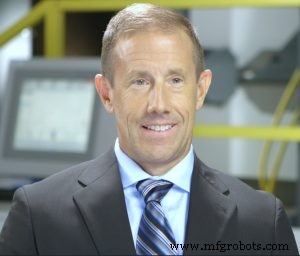
Sintaviaは、同社のCEO兼会長であるBrianNeffによって2012年に設立されました。同社は、フロリダ州フォートローダーデールに拠点を置く独立したジェットエンジンMROであるCTSEnginesと呼ばれる会社との社内の積層造形の取り組みとして設立されました。
Sintaviaは2015年に別会社になり、現在もフロリダ州デイビーに移転しました。
会社として、私たちは航空業界で幅広いバックグラウンドを持っています。この背景を利用して、さまざまな製品と垂直統合された会社を作成する機会があったことがわかりました。アディティブが得意であるためには、計測、冶金、機械加工、熱処理、テストなども得意である必要があります。
したがって、私たちのコアスキルはアディティブマニュファクチャリングですが、 MROおよびOEM製造分野は、航空宇宙および防衛、ならびに石油およびガスに焦点を当てた新しい独立した会社を作成します。
Sintaviaのユニークな点は、垂直統合が、後処理、品質、冶金、スキャンなど、私たちが行うすべてのことを支えていることです。これらの要素はすべて、フロリダ州デイビーにある当社の生産施設内の1つの屋根の下にあります。
航空宇宙はSintaviaの中心的な焦点です。航空宇宙産業向けの積層造形の利点について教えてください。
アディティブマニュファクチャリングは、さまざまな理由で航空宇宙に適しています。
まず、このテクノロジーは、航空宇宙および防衛産業内のOEMが設計とテストを迅速に繰り返すための、プロトタイプ開発ツールとして始まったことに注意することが重要です。エンジン。今では、企業が添加剤部品を使用してエンジンを構築しているところまで進化しています。
それでも、それは大きな推進力です。しかし、AMを優れたテクノロジーにする他のすべての典型的な利点があります。ここでは、溶接部の統合、複雑な鋳造、軽量化、工具不要の設計について言及しています。もちろん、複雑さは自由ではありませんが、添加剤を使用すると大幅に拡張されます。
例として、部品の選択に関する私たちの主な焦点は、ジェットエンジンとダクトの外側にある外部バルブ本体です。また、航空宇宙産業におけるシャーシおよび熱交換器の新興市場も見られます。
使用する金属3D印刷技術の1つは、Powder BedFusionです。航空宇宙アプリケーションにおけるこのテクノロジーの利点は何ですか?
ええと、一般的に金属3D印刷は、ユニークなデザインに非常に役立ちます。
私たちが行っていることの初期段階では、レーザーと電子ビームを使用した粉末床融合を使用して、高圧ダクトとコンポーネントを層ごとに構築しています。業界ですでに使用されている溶接物や鋳造品の代替ツールとしてこのテクノロジーを使用することには、明らかに利点があります。
しかし、添加剤の力はそれをはるかに超えています。より良く、より軽く、より強力な部品を作ることができ、本質的にパフォーマンスの向上を促進します。最終的に、AMのパワーを真に活用するには、コンポーネントを積層造形用に設計する必要があります。
熱交換器やシャーシなどのコンポーネントに、以前は製造できなかった形状を作成するために、主にここでレーザーについて話している積層造形を使用できます。
また、たとえば、AMを使用してより高速に作成および統合できるフローボディまたはバルブアセンブリもあります。これにより、お客様は既存のサプライチェーンを最適化するだけでなく、より優れた製品を製造し、OEMの航空宇宙および防衛市場の強みを活かすことができます。
例として、熱交換器を取り上げます。コンポーネント内に非常に細かい壁と小さくて複雑な形状を作成します。したがって、200ミクロン以下の壁を持つことができます。さらに、アディティブマニュファクチャリングを使用すると、コンポーネントから熱を逃がすためのより良い方法が得られます。熱交換器の最終的な目的は、コンポーネントから熱を奪い、より多くの電子機器をコンポーネントに詰め込むことであるため、これは素晴らしいことです。
私たちは、製品を改善するために金属積層造形を使用しています。バルブ本体、外部ジェットエンジンのコンポーネント、ダクト、熱交換器から、シャーシ、およびそれらを溶接するための多くの複雑なジグと固定具を備えた溶接によって作成されたさまざまなタイプのチューブ構造まで、あらゆるものがあります。
、それ以上のこともします。たとえば、コンプレッサーの内部にある可能性のある小さなインペラーから、ロケットの内部にある可能性のある大きなインペラーまで、ターボ機械装置の内部にあるものに取り組んでいます。
私たちは、商用航空宇宙(本質的にはジェットエンジン)に焦点を当てており、ロケット部品である推進力にも焦点を当てています。
次に、航空宇宙および防衛産業内の「中間」があります。これは、かつて10〜100個で製造されていたあいまいなコンポーネントを指しますが、現在はアディティブマニュファクチャリングを使用した1つの特異なピース。
これらのアプリケーションに関連する設計上の課題について詳しく教えてください。
AMは、製造における比較的新しいプロセスです。レーザーまたは電子ビームを使用して、粉末を層状に溶かしています。基本的に、私たちが実際に行っているのは、中小規模の溶接、つまり「マイクロ溶接」を行うことです。
このマイクロ溶接プロセスでは、レーザーが金属粉末を露出させる急速冷却が行われます。 2つの極端なケースがあります。それは、非常に高温の印刷プロセスであり、同時に急速な冷却が行われます。
これらの極端な温度差のため、部品は歪みの影響を受けます。したがって、これらの部品は、鋳造部品で作られた従来の溶接物とは異なります。それらはそれ自体がユニークなアイテムです。
重要な課題の1つは、これらの部品が積層造形プロセス内でどのように動くかを予測できることです。この課題の重要な部分は、この非常に最新のテクノロジーとハイテクツールを使用して最初に予測を行い、プロセスの全体的な調整を支援することです。
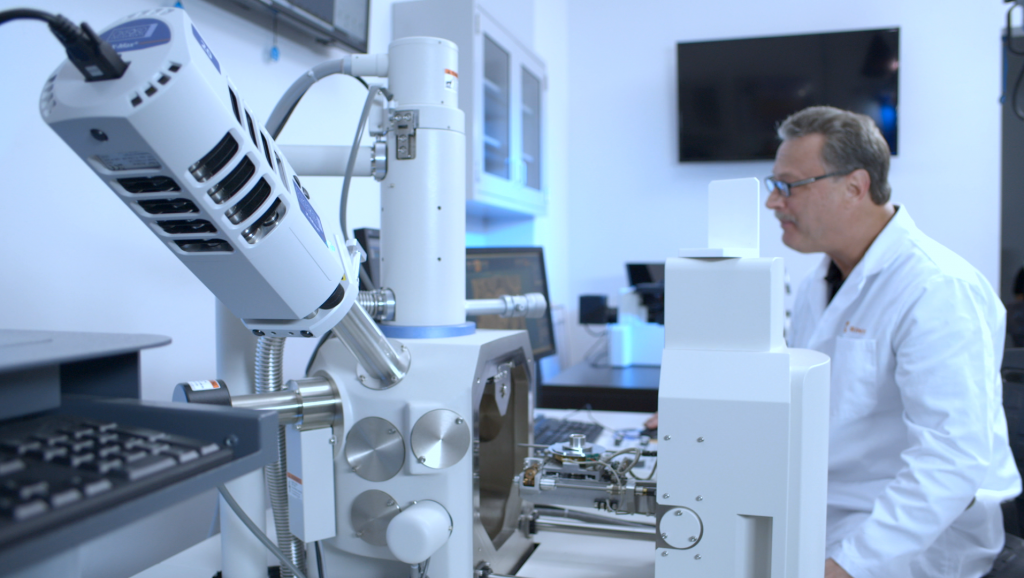
Sintaviaでは、設計サイクルの開始時に有限要素解析(FEA)を使用しています。 Sintaviaのエンジニアは、CADモデル、図面、仕様の形式でお客様から初期データを取得します。当社のエンジニアは、お客様と協力して、ビルドプレート上でパーツを方向付ける方法、パーツが作成される角度、パーツを押し下げるか熱を取り除くためのサポートの使用方法などの重要なパラメーターを検討します。パーツ。
数学を使用して、パーツがどのように歪むかを予測し、その歪みを最小限に抑えて、非常に忠実なパーツを作成します。その部分がどのように移動して移動するかを知る必要があります。これにより、フランジ、ボア、穴などにストックを追加して、プロセスの最後にクリーンアップするのに十分なストックがあることを確認できます。このアプローチを使用すると、後でそのパーツの後処理を考慮することもできます。
覚えておくべきことの1つは、積層造形は複雑な部品を作成するための非常に強力なプロセスですが、従来のプロセスと連携して使用する必要があるということです。アディティブプロセスとサブトラクティブプロセスの調整は重要です。
金属部品の後処理に伴う課題について多くのことを耳にしますが、それはSintaviaが提供するサービスの1つです。後処理とアプローチに関する最大の課題について教えてください。
後処理は、印刷プロセス自体と、製造後にその部分に伴う後処理との間の調整された作業である必要があります。
ほとんどの人に見られない一般的な課題は、プロセス後の粉末の除去です。印刷プロセスの後、すべての粉末を部品から取り除く必要があります。これらの部品のいくつかは非常に複雑な形状をしているため、粉末を除去するために、超音波または従来の振動システムのいずれかのカスタムマシンを作成します。
通常、次のステップの前に部品から粉末を取り除きます。これはほとんどの場合、応力緩和です。真空炉またはボックス炉のいずれかを使用して社内で応力を緩和し、添加剤の構築プロセスから残留応力を取り除きます。
そこから、ワイヤーEDMまたはバンドソーに移動して、プレートから部品を取り外します。次に、もちろん、サポートを削除する必要があります。これらの支持体は、単純な格子支持体から、部品を保持し、非常に大きなニッケル超合金部品を製造するために使用される非常に堅固なものまで、何でもかまいません。これらは多くの熱応力にさらされます。
このため、これらの部品からサポートを取り外すには、非常に堅牢な機械プロセスが必要になる場合があります。これにはかなりの作業が伴う可能性があります。そして、私が「機械プロセス」と言うとき、これは多くの異なることを意味する可能性があります。それは、部品からそれらのサポートを取り外すために、非常に剛性の高い5軸工作機械にペンチでそれらを切り離すのと同じくらい簡単なことを意味する可能性があります。
この時点から、いくつかの選択肢があります。たとえば、現場で紹介しているHIPにアクセスしたり、機械加工を使用したりできます。この場合、機械加工とは、印刷するための機械加工を意味します。したがって、これは実際には機械工場で見られるものと何ら変わりはありません。
ほとんどの場合、多くのコントロールを備えた2D図面があり、その部分を機械加工して仕様に合わせています。
金属粉自体に移りますが、シンタビアで金属粉を開発するプロセスは何ですか?
明確にするために、私たちは実際には粉末自体を開発していません。しかし、私たちは企業がこれまで市販されていなかった合金を開発するのを支援することに携わってきました。
私たちが協力している会社には、たとえば工具鋼の変種やステンレス鋼の変種があります。これらは通常、将来何らかのパフォーマンス上の利点を得るために使用するために開発された特殊合金です。
私たちが持っているのは、航空宇宙産業向けの飛行承認済みの粉末ソリューションです。粉末を調達し、それをラボに持ち込み、ビルドを開始する前に多数のテストを実行します。
Sintaviaの強みの1つは、ラボ内で粉末の完全なオンサイト特性評価を行っていることです。これにより、粉末に何が起こっているのかをサンプリングして理解することができます。通常、他の企業がこのプロセスを外部委託しています。そのため、粉末サプライヤーから材料を調達する場合もありますが、フローテスト、形態、粒子サイズ分布、ガス分析、化学用ICPなどを行います。
粉末がお客様の製造要件を満たしていることを確認するために、約8〜9回のテストを実行します。次に、パウダーが使用されるときに、これらのパウダーサンプルをサンプリングしてアーカイブし、ビルドが続行されるときにパウダーに何が起こるかを理解します。これは、粉末が徐々に使用されるにつれて、粉末に何が起こるかを正確に理解できることを意味します。
Sintaviaは、今月、機械を増やして新しい施設を開設する計画を発表しました。この新しい施設の背後にあるビジョンを共有できますか?
今月、新しい施設を開設できることを大変うれしく思います。
新しい施設は55,000平方フィートになり、過去の成功に基づいて施設を建設します。
重要な点は、本番環境に大きく依存することです。 3,000万ドルを超える新しい機械、より大型の最新のAM機器、粉末処理システム、バックアップジェネレーター、電源、不活性ガスを収容する予定です。シンタビアと南フロリダで最大135以上の新しい仕事を追加することを想定しています。
新しい施設は、実際には、私たちが行ったことを小規模に取り入れ、現在の施設で12台のマシンを実行し、それを最大65の55,000平方フィートの施設にスケールアップするというビジョンです。マシン。
積層造形、熱処理には多大な労力が必要です。後処理、仕上げ、洗浄など。
基本的に、私たちは1つの施設内で添加剤プロセスを制御することを目指しています。これがまさにビジネスモデルです。私たちは、これまでに行ったことをスケールアップし、OEMのお客様に品質と再現性を保証する製造プロセスに取り入れたいと考えています。
将来的には、自動車や医療など、3Dプリントされた金属部品の需要も大きい他の業界に拡大することを検討しますか?
はい、もちろんです。私たちは自動車と医療の両方でいくつかのことが起こっています。そして、添加剤も理にかなっている他の産業があります。
たとえば、私たちは産業用ガスタービンに携わっています。私たちのバックグラウンドはエアロガスタービンですが、エネルギー用の地上ベースのガスタービンは基本的にスケールアップされており、エアロタービンエンジンはわずかに異なります。
このテクノロジーは、生物医学分野にも非常によく適用されます。
SintaviaはAS9100の認定を受けており、AS9100は航空宇宙産業向けの品質管理システムです。私たちのラボは、機械的測定についてISO 17025の認定を受けています。これは、粉末の特性評価や化学から引張試験や疲労試験まで、あらゆることを意味します。
生物医学業界には、異なる認定機関があります。そのほとんどはISO13485にまで及びます。AS9100を入手したら、ISO13485に移行できます。これらの異なる業界間を行き来することはそれほど大きな飛躍ではありません。結局のところ、品質は品質であり、プロセスはプロセスです。航空宇宙を行うことができれば、他の市場に移行することができます。
また、私が言及したすべてを超えて、品質管理は最も重要な側面です。
初日から、AS9100を使用した品質システムの開発に注力してきました。 ISOおよびNadcap認証。これはすべてOEMのお客様にとって非常に有益であり、他の業界にとっても間違いなくリソースになる可能性があります。
あなたの意見では、金属3D印刷の採用を加速するために必要なものは何ですか?
私たちのテクノロジーと分析における優れた能力のすべてについて、私たちは本当にビジネスを推進するものに焦点を当てる必要があります。ビジネスはお金とスピードによって推進されます。これは、テクノロジーがより速く、より安く、より確立される必要があることを意味します。
そうは言っても、私たちは物事がどのように変化しているかを見ています。ここシンタビアにいる間、メタルAMがどのように進化したかを見てきました。たとえば、ある時点では、アルミニウムは積層造形で印刷するのに比較的扱いにくい素材でしたが、今ではほとんど一般的です。追加のレーザーが見られるように、添加剤の専門知識と部品の設計が見られるように、それはお客様により速いスピードとコスト削減を提供するでしょう。
これはすべて、歴史的にプロトタイピング業界から生まれたものであり、私たちはそれを連続生産に移したいと考えています。それをより速くそしてより安くし、品質を提供し、そして金属添加剤が提供できることを誰もが知っている利点を提供するために私たちがしなければならない特定のことがあります。
今後5年間で金属積層造形がどのように進化していくと思いますか?また、Sintaviaはそのビジョンにどのように適合しますか?
私たちが本当にしなければならないのは、生産的な方法で部品を作り始めることです。重要な業界では、完全に機能する実際の金属部品を製造していることを確認する必要があります。
これらの部品は、機械的特性に関して鋳造品と非常によく競合することを私たちは知っています。適切なプロセスと管理があれば、生の製品、場合によっては鍛造製品とも競合する可能性があります。
品質管理、つまり品質要件を理解し、自分の部品を検証できることは、将来的に大きな違いを生むでしょう。
しかし、テクノロジーがまだ比較的新しいという事実を見失うことはできません。業界として、私たちは初めて多くのことを行っています。
これは、プロセスのフロントエンドを最初に学習する必要があることを意味します。
たとえば、プロセスの開始時に、エンジニアはサポート戦略を理解する必要があります。パーツの形状とサポートの形状を最適化するための最善の方法を学ぶことに時間を費やします。これにより、より良い部品を製造し、サポートが比較的簡単に外れるようになります。
この作業のおかげで、まず、サポートを削除するための費用と時間のかかる手順を実行し、大幅に安価にしました。部品を製造するためのエンジニアリングの取り組みは、製品を次々と製造するための成熟した段階に到達するために非常に重要です。
シンタビアの将来はどうなるでしょうか?
とてもエキサイティングに見えます!もちろん、私たちが新しい施設に移動するとき、それはまた非常に挑戦的に見えます。リーン生産方式を実施します。 OEMとサプライチェーンの連携のために意図的に開発された、最初の大規模で無駄のない積層造形施設があります。
2019年も、お客様向けの部品の認定と開発に関して、過去2年間に行ってきた多くの作業を継続します。
名前は付けませんが、世界の主要な航空宇宙企業を見ると、私たちが彼らのためにビジネスを行っている可能性が非常に高いです。
一部の企業ではハネウェルとの関係のように、ハネウェル航空宇宙向けの飛行可能な部品の製造を承認された最初のAMサプライヤーです。私たちはHoneywellと提携して、現在の施設と次の施設を使用してそれを引き出し、Honeywellの生産部品を製造しています。
Honeywellはこのテクノロジーを比較的急速に採用しており、多くのアプリケーションがあります。しかし、ハネウェルの外に出れば、それがエアフレーマーであろうとエンジン発電所であろうと、航空宇宙および防衛プロバイダーであろうと、私たちが現在彼らのために仕事をしている可能性があります。
金属添加剤の採用に関する限り、2019年と2020年は私たちにとって比較的大きな年であると考えています。ハネウェルが今日ここにいることは本当にエキサイティングですが、今後数年間でより多くの顧客が連続生産を行うようになるでしょう。
私たちは、世界中のOEMにそのリソースを提供するために会社を調整しているので、OEMは、積層造形でこれらの部品を製造するためのワンストップショップ、垂直統合パートナーを持つことができます。
最終的な考えはありますか?
品質が私たちの焦点であることを繰り返し述べたいと思います。
私たちの顧客は、間違いなく、世界で最もリスクを嫌う顧客です。アディティブマニュファクチャリングによって製造されたこれらの重要なコンポーネントを快適に飛行できるようにするためには、品質が最も重要です。
結局のところ、製品を設計図や仕様に適合させて、実際のアプリケーションで使用したいと考えています。そのためには、適合性に重点が置かれます。
また、今日のAMは、すべてのメディアの注目を集め、多くの時間とお金が費やされている場所です。しかし、最終的には、積層造形によって作成した部品を使用し、それを顧客のエンジニアリング要件に適合させる必要があります。
そうです、私たちは積層造形について話したいと思います。しかし、私はそれを高度なと考えることも好きです。 製造。私たちは、積層造形の流行語から離れて、精密航空宇宙部品の先進的なメーカーであると言いたいと思います。お客様が現在の設計を大幅に改善できるように、高度な部品を製造したいと考えています。
Sintaviaの詳細については、次のURLをご覧ください。 https://sintavia.com/
ダグヘッジについて
Doug Hedgesは、OEMの実験的なコンポーネント設計から、業界標準の仕様と制御に基づくFAA承認の修理、変更、コンポーネント開発まで、航空宇宙業界で20年以上の経験があります。
Sintaviaの前は、 CTS Enginesのシニアエンジニアとして、General Electricジェットエンジンのオーバーホールの修理とプロセスの開発、HEICO Aerospaceのリードプロジェクトエンジニア、Kapco GlobalのシニアPMAエンジニア、Rolls-Royceの設計エンジニアとして。ダグはミネソタ大学で機械工学の学士号を取得しています。
専門家のインタビュー
AMFGのExpertInterviewsシリーズは、積層造形の未来を形作るのに役立つ革新的な企業や個人を紹介しています。シリーズへの参加の詳細については、marketing @ amfg.aiにお問い合わせください。
3Dプリント
- アディティブMESを使用してシリアルアディティブプロダクションにどのように拡張できますか?
- 専門家へのインタビュー:Xaarの3Dプリンティングディレクター、ニールホプキンソン教授
- 専門家へのインタビュー:3Dfilemarket.comの創設者であるPhilip Cotton
- 専門家へのインタビュー:FabRxのDr Alvaro Goyanes
- 専門家インタビュー:3Dプリントの未来についてのUltimaker社長John Kawola
- 専門家インタビュー:金属3D印刷による連続生産の達成に関するSintavia社長Doug Hedges
- 専門家のインタビュー:3D印刷用の高性能ポリマーの開発に関するソルベイのブライアンアレクサンダー
- 専門家のインタビュー:Carbonの共同創設者Philip DeSimoneが、3Dプリントによる大量生産に向けた動きについて
- ソフトウェアで解決できる4つの積層造形の課題
- 専門家インタビュー:アディティブマニュファクチャリングの未来に関するJabil’s Rush LaSelle
- 専門家のインタビュー:シミュレーションによる金属3D印刷の成功の達成に関するANSYSの最高技術責任者