金属3D印刷技術はどの程度成熟していますか?
[画像クレジット:CCDC陸軍研究所]
金属3D印刷には、それぞれ独自の利点と用途、および独自の成熟度を備えた幅広いテクノロジーが含まれます。
生産に特定の金属3D印刷技術を採用することを検討する場合、その機能と制限が現在どこにあるかを理解することが重要です。ただし、金属3D印刷に関しては、企業は現実を誇大広告から切り離すという課題に直面しています。
企業が主要な金属3D印刷技術の成熟度をより簡単に評価できるように、今日はNASAによって最初に開発されたTechnologyReadiness Level(TRL)システムに基づいて、最終部品の生産にどれだけ準備ができているかを調べます。
技術成熟度(TRL)とは正確には何ですか?
1970年代初頭にNASAによって最初に開発された「技術準備レベル」は、新しい技術が宇宙探査に適しているかどうかを評価するために使用されるアプローチです。 1990年代までに、TRLは多くの米国政府機関に適用され、現在では多くの業界で一般的に使用されています。
TRLシステムは、テクノロジーの成熟度をレベル1(概念評価)からレベル9(導入の成功)まで測定します 。 9つのレベルのそれぞれは、テクノロジー開発のマイルストーンを示しています。
TRLを使用して金属3D印刷技術の成熟度を評価するにはどうすればよいですか?
このアプローチを適用して、さまざまな3D印刷テクノロジーの成熟度を評価しました。各金属3D印刷技術のTRLを特定するために、その進化、それを採用している業界、現在の使用方法、およびその将来を形作る開発を分析しました。
特に、場合によっては、TRLがアプリケーション固有である可能性があります。たとえば、Direct EnergyDepositionテクノロジーは実稼働アプリケーションではTRL8に位置し、修理アプリケーションはレベル9に達しました。
私たちの調査によると、金属3Dの大部分は印刷技術はTRL7を超えました。これは、パフォーマンスの問題に対処するための運用環境でのテスト、および機能的なプロトタイピングとツーリングでのアプリケーションを指します。
一部は、通常の運用条件下で成功することも証明されています(TRL 8)そしてより広い製造エコシステム(TRL 9)への統合に向かっています。
レーザー粉末ベッドフュージョン

技術準備レベル:8
レーザーパウダーベッドフュージョン(PBF)は、最も確立された金属3D印刷技術の1つです。金属PBFプロセスでは、強力で微調整されたレーザーを金属粉末の層に選択的に適用します。このようにして、金属粒子が層ごとに融合して部品を作成します。
金属PBFの起源は、ドイツのアーヘンにあるフラウンホーファー研究所が金属のレーザー溶融に関する最初の特許を出願した1995年にさかのぼることができます。それ以来、EOS、Concept Laser(GEが買収)、SLM Solutionsなどの定評のある企業を含む多くの企業が、この技術を取り入れてPBF市場に参入しました。
過去10年間、金属PBF 3Dプリンターのメーカーは、生産のためのテクノロジーの最適化に懸命に取り組んできました。この目的のために、主要な市場プレーヤーが自動化され統合された生産のためのソリューションを立ち上げているのを見てきました。
これらのソリューションの大部分は、同様の特性を共有しています。モジュール式で構成可能であり、効率を最大化し、必要な手作業の量を減らすために、高レベルの自動化を提供します。
同時に、PBFの材料の選択肢は継続的に拡大しています。たとえば、EOSは先月、金属3Dプリンター用に4つの新しい金属粉末を発表しました。その中には、ステンレス鋼CX、アルミニウムAlF357、チタンTi64グレード5、チタンTi64グレード23があります。
これらの開発のおかげで、レーザーPBFは多くの産業やアプリケーションに採用されています。金属PBFの採用に特に熱心な業界の1つは、航空宇宙産業です。
今日、金属製のPBF 3D印刷部品は、エンジンなどの重要な航空機や宇宙船システムに電力を供給しています。ここで、テクノロジーの主要な機能である、組み立てが簡素化され、材料の無駄が少ない複雑な部品の製造が真に輝いています。
現在、レーザーPBF技術は機能部品を繰り返し提供することができます。ただし、メーカーが本格的な生産を開始する前に、微調整とテストが必要です。そのため、現在は技術準備レベル8にあることをお勧めします。
今後、ソフトウェアの進歩と全体的な進歩により、金属PBFシステムの使いやすさと信頼性が向上します。ワークフロー。
この傾向を裏付ける一例は、カリフォルニアを拠点とする金属3DプリンターメーカーであるVELO3Dです。
Intelligent Fusionと呼ばれるレーザーPBFテクノロジーの開発において、同社はソフトウェアとハードウェアの統合に重点を置いてきました。その結果、緊密に統合されたシステムにより、サポートが少なく、表面仕上げが向上し、成功率が高くなると報告されています。これにより、信頼性が向上し、生産が速くなり、後処理が少なくなります。
レーザーPBFは、金属3D印刷業界の原動力であり続けています。金属PBF3Dプリンターは、他の金属3D印刷技術の中で最大の設置ベースを持っています。また、PBF 3Dプリンターのメーカーは、他のタイプの金属3Dプリンターを製造している企業と比較して、金属3D印刷市場で最大のシェアを持っています。
そのため、最初に金属PBF技術用に多くの材料が開発されています。これは、高性能で複雑な金属3D印刷部品の需要に牽引されて、この技術の進化が続くことを意味します。
電子ビーム溶解
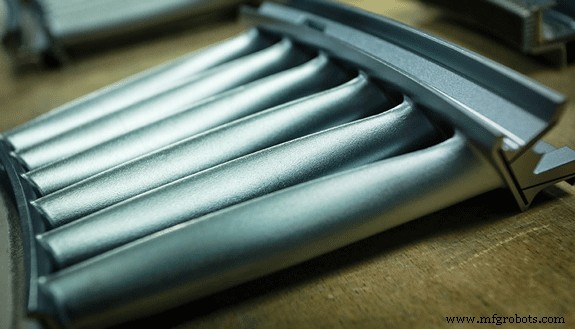
技術準備レベル:8
電子ビーム溶融は、レーザーPBFと同様に、3D印刷技術の粉末床融合ファミリーに属しています。 EBMは、金属粉末も溶融して完全に緻密な金属部品を作成するという点で、レーザーPBFと同様に機能します。
2つのテクノロジーの主な違いはエネルギー源です。EBMシステムは、レーザーの代わりに、金属粉末の層を溶かすための熱源として高出力の電子ビームを使用します。
2000年にこの技術の特許を取得して以来、スウェーデンの企業であるArcamは、EBM3Dプリンターの主要メーカーであり続けています。
2016年にGEが買収した後、EBMテクノロジーは進化を続けました。 2018年、Arcamは次世代のEBMマシンであるSpectraHをリリースしました。
「H」は「溶銑」の略で、高熱を処理し、チタンアルミミドなどの亀裂が発生しやすい材料を処理できることを意味します。 (TiAl)1000°Cに達する温度で。
Arcam EBM Spectra Hには、生産性の向上と全体的なコストの削減を目的とした多くの新機能があります。
たとえば、EBM SpectraHには6kWのHV電源が搭載されています。ユニットは、現在市販されている他のEBMマシンと比較して、予熱および後加熱のステップを50%削減するのに役立ちます。
さらに、高温を低減するためにレイヤリングプロセスがアップグレードされました。これにより、メーカーはフルハイトビルドで最大5時間節約でき、他のEBMマシンと比較して印刷速度を最大50%向上させることができます。
GEAviationビジネスのAvioAeroは、35Arcamを使用していると報告されています。マシン:31台のArcamA2Xマシンと4台のArcamEBM SpectraHマシン。 Avio Aeroでは、3Dプリンターを使用して、新しい大型GE9Xエンジンの低圧タービン用のTiAlブレードを製造しています。
航空宇宙に加えて、医療業界はこの技術を使用して医療用インプラントを製造しています。 。このアプリケーションでのEBMの最初の使用は、2007年にさかのぼります。
GEの金属AMに関するリソースと専門知識に支えられて、EBMテクノロジーは工業化に向けて順調に進んでいます。この技術は、航空宇宙や医療などの規制の厳しい業界の生産環境に適用されています。これらのアプリケーションを考慮すると、EBMはTRL8に達しました。
直接エネルギー沈着
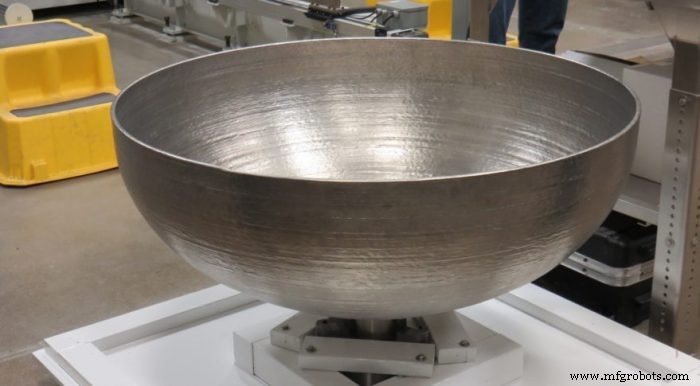
技術準備レベル:8
溶接プロセスに由来する直接エネルギー蒸着(DED)は、材料がノズルからビルドプラットフォームに押し出されるときに、レーザーまたは電子ビームで金属を溶かすことを伴います。
DEDシステムは、原料としてワイヤーまたは粉末のいずれかを使用します。ほとんどのシステムは、溶接または粉末冶金用に開発された市販の材料を使用しています。既製の材料を使用することには、材料の選択範囲が広く、品質が高く、価格が安いなど、多くの利点があります。
DEDの最初で最も成功したアプリケーションの1つは、損傷したコンポーネントの修理です。この技術は、タービンブレードや射出成形金型インサートなどの損傷した部品に材料を追加するために使用されます。 DEDは、摩耗した部品を修理することにより、部品の寿命を延ばしながら、部品の交換に関連するダウンタイムとコストを削減するのに役立ちます。
修理アプリケーションを超えてDEDを使用できるようにするために、DEDシステムのメーカーは、機能性金属部品の製造のためのソリューションを開発および最適化しています。
たとえば、DEDテクノロジーのパイオニアの1つであるSciakyは、電子ビーム積層造形システムに閉ループ制御を導入しました。 Sciakyのプロセス監視システムは、リアルタイムの光学イメージングとマシンビジョンを組み合わせて、溶融池のサイズ、形状、温度を測定します。
画像から得られたデータに基づいて、閉ループ制御システムビームパワー、ワイヤ送り速度、およびマシンの動きを制御するソフトウェアに調整コマンドを提供します。これにより、プロセスの再現性を大幅に向上させることができます。
DEDテクノロジーは、すでに複数の航空宇宙および防衛アプリケーションに適用されています。例としては、衛星用のチタン燃料タンクドーム、ボーイング787ドリームライナー用の構造用チタン部品、軍用車両用の交換部品などがあります。
このテクノロジーは、すぐに利用できるメンテナンスソリューションとしての地位を確立しています。このアプリケーションでは、DEDはTRL9になります。
本番アプリケーションに関しては、DEDは製造ツールとしても使用できます。ただし、工程内制御の進歩と印刷解像度の向上に関しては、さらなる開発が必要です。
現在のところ、この技術はニアネット形状を生成しますが、部品の仕様と良好な表面仕上げを実現するには、かなりの機械加工が必要です。印刷解像度を向上させることで、メーカーは二次加工に必要な時間とコストを削減できます。
金属バインダー噴射
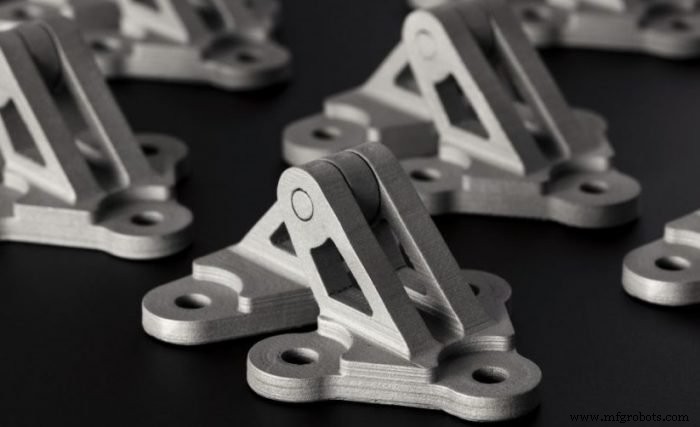
技術準備レベル:さまざま
Metal Binder Jettingは、非常に有望な製造技術へと急速に進化しています。ただし、技術の準備レベルは、現在市場に出回っている金属バインダー噴射技術によって大きく異なります。
金属バインダー噴射は、1993年にMITで最初に開発されました。印刷プロセスは、粉末の薄層を広げることから始まり、プリントヘッドがバインダーの液滴を粉末床に戦略的に堆積させます。このプロセスは、部品が完成するまで層ごとに繰り返され、未使用の粉末(約95%)がリサイクルされます。
1996年からMITから技術のライセンスを取得しているExOneは、金属を提供する唯一の企業であり続けました。 2010年代初頭までのバインダー噴射サービスとシステム。 ExOneの金属バインダー噴射システムは、主に金属のプロトタイプと工具を作成するために使用されました。
しかし、金属バインダー噴射の特許が失効し始めたため、競争が激化し、同社は生産レベルのソリューションの開発を開始するようになりました。最新のX125PRO 3Dプリンターは、数か月前に商業的に発売されました。
金属バインダー噴射市場のもう一つの大きなプレーヤーは、デジタルメタルです。 2017年に最初に導入された同社のDMP2500 3Dプリンターは、航空宇宙、高級品、歯科用工具、産業機器など、さまざまな業界で30万を超えるコンポーネントを製造していると報告されています。
また、HPやDesktop Metalなど、金属バインダー噴射分野への新規参入者も数名います。
2016年にポリマー部品向けのマルチジェットフュージョンテクノロジーを発表した後、HPは2018年に添加剤製品の次の拡張であるメタルジェット3D印刷システムを発表しました。新しいシステムにより、HPはこのテクノロジーを大量生産環境に導入することを目指しています。
これを実現するために、同社はシステムにさらに多くのノズルを装備し、革新的な結合剤を導入しました。これらの進歩を組み合わせることで、印刷プロセスがより速く、より簡単になることが報告されています。
Desktop Metalの3Dプリンターの背後にあるテクノロジーは、同社がシングルパスジェッティング(SPJ)と呼んでいるもので、一般的なバインダージェッティングプロセスの高速バージョンです。同社によれば、システムは最大12,000 cm3 / hrで印刷でき、これは1時間あたり60kgを超える金属部品に相当します。
興味深いことに、HPのMetalJetとDesktopMetalの生産システムはやや類似した価値を共有しています。命題。両方のバインダー噴射ベースのマシンは、より高い速度と拡張性を可能にすることにより、従来の製造を混乱させるように見えます。
DesktopMetalのProductionSystemは今年初めにリリースされましたが、HPのテクノロジーは2020年のリリースが予定されており、現在HP Metal Jet ProductionServiceを通じてのみ利用できます。
確かに、金属バインダーの噴射技術の多くは最近登場したばかりです。これは、社内または顧客サイトでのさらなるテストを通じて、シリアルプロダクションアプリケーションの準備ができていることを証明するために時間がかかることを意味します。
生産アプリケーションでの実績により、Digital MetalやExOneのような古い技術は、技術準備レベル7と8の間にあります。最近の金属バインダー噴射技術はTRLに達し、それを超えると予想されます。今後数年間で8。
金属バインダー噴射システムは、大量の自動車や工業製品の生産など、他の金属3D印刷技術の浸透が困難な市場に対応するために、進化を続けます。これにより、今後このテクノロジーに多くの刺激的な成長の機会が生まれます。
結合金属の堆積
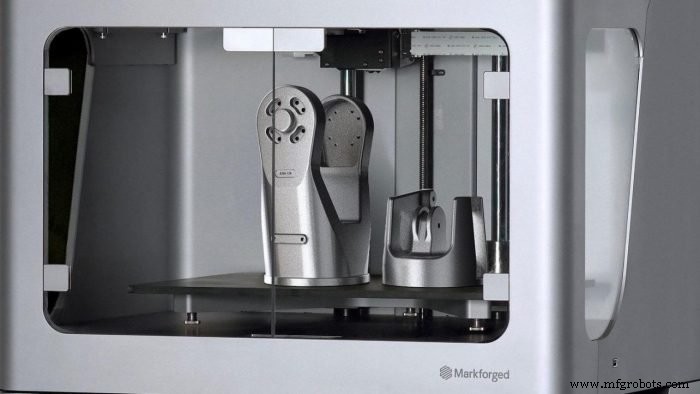
技術準備レベル:7
バウンドメタルデポジションは、金属積層造形の分野でエキサイティングな新参者です。この技術は、フィラメントが加熱されてノズルから押し出され、層ごとに部品が作成される溶融フィラメント製造(FFF)と同様に機能します。ただし、FDMで使用されるプラスチックフィラメントとは異なり、金属押出成形では、プラスチックバインダーに包まれた金属粉末またはペレットで作られたフィラメントが使用されます。
この分野で活動している2つの最も著名な企業は、MarkforgedとDesktopMetalです。両社は、2017年に最初に金属3D印刷システム(MarkforgedのMetalXとDesktopMetalのStudioSystem)を発表しました。
現在、このテクノロジーは主に、金属のプロトタイプと工具をより速く、より安価に作成するために使用されています。
1つの例は、流体移送業界向けのアクセサリのメーカーおよびサプライヤであるDixon Valve&CouplingCompanyです。同社は、MarkforgedのMetalXから3Dプリントのグリッパージョーを使用しています。これらのツールは基本的にクランプであり、スチールカップリングにシールリングを追加するロボットアームに取り付けられています。
このようなツールの製造には14日かかり、費用は355ドルです。比較すると、金属グリッパーの3D印刷は、7ドルかかり、完了するまでに1。25日かかります。これは、コストとリードタイムの両方で90%以上の削減です。
バウンドデポジション技術は、コストを大幅に向上させています-効果的なプロトタイピングと市場投入までの時間の短縮により、生産側での使用は制限されたままです。 1つは、このようなシステムはコンパクトな金属製の3Dプリンターとして位置付けられているため、拡張が難しい場合があります。
ただし、特に石油プラットフォームなどの遠隔地でこのテクノロジーを採用する企業が増えるにつれ、より多くの例が見られる可能性があります。今後数年間で結合金属堆積を使用して作成されたスペアおよび最終用途の部品の。
金属3D印刷による革新
金属3D印刷技術の大部分は、非常に高い技術準備レベルに達しており、生産アプリケーションに適していることを意味します。
明らかに、特に金属3D印刷技術の経済性と速度の向上に関しては、まだ多くの作業が必要です。現在、粉末床プロセス、DED、および金属バインダー噴射は、従来の製造システムよりもかなり高価です。
低コストのバウンドパウダーデポジションシステムは、金属3D印刷へのアクセスを可能にし、中小企業にとって優れたエントリーポイントを提供する可能性があります。
結局のところ、テクノロジー自体を進歩させることは、パズルのほんの一部にすぎません。金属3D印刷を取り巻くエコシステムが進化し続けることも、同様に重要です。これには、より統合された使いやすいソフトウェアソリューションの開発、後処理操作の自動化、および合理化されたワークフローの作成が含まれる場合があります。
すべての部品を組み合わせるだけで、金属3D印刷で大幅なプロセスと製品の革新を実現する方法があります。
3Dプリント
- 3Dプリント用にオブジェクトモデルを設計する方法
- 3Dプリントでのブリッジの使用方法
- 3Dプリントはどのように金属鋳造に利益をもたらすことができますか?ここに3つの方法があります
- 金属3D印刷:私たちは今日どこにいますか?
- あなたの業界は3Dプリントの採用においてどの程度成熟していますか? [インフォグラフィック]
- 過去12か月で出現した10のエキサイティングな3D印刷技術
- デスクトップ3Dプリンターが3D印刷をどのように変革しているか
- AM Around the World:アジア太平洋地域の3D印刷はどの程度成熟していますか?
- 2020年に3D印刷ハードウェア市場がどのように進化しているか
- 産業用3D印刷はどの程度持続可能ですか?
- 3D印刷技術を理解する