インダストリー4.0プロジェクトの成功に向けた5ステップのアプローチ
前回のブログ投稿「アジア太平洋地域で勢いを増しているインダストリー4.0」では、アジア太平洋地域におけるインダストリー4.0の現状についての洞察を共有しました。今日は、インダストリー4.0プロジェクトの概念実証(POC)を成功させるために必要な手順を詳しく見ていきたいと思います。 POCプロジェクトは、管理可能な設備投資とともに低リスクを負担しながら、インダストリー4.0テクノロジーの可能性を示しています。これは、現在の製造プロセスで対処する特定の問題点を特定した後の実装の最初のステップである必要があります。
ステップ1:ビジネス目標を設定する
インダストリー4.0プロジェクトの大部分は、運用管理者が問題を解決したり、製造現場での日常業務を改善しようとした結果として開始されます。したがって、アプローチの最初のステップは、彼らが常に直面している運用上の問題を特定して理解することです。インダストリー4.0はどのような運用上の問題に対処していますか?厳格な測定を必要とする独自のビジネス目標またはクライアントの要求はありますか?次に、比較のベースラインとして機能するように、明確なメトリックを決定する必要があります。
ステップ2:プロトタイプの作成
次のステップでは、限られた予算でトライアルPOCプロジェクトを実行するための計画を立てます。トライアル中の目標は、分析結果に基づいて手動でプロセスを改善することで最適化を実現することです。これらの利益の定量化は、試験をより広く拡大すべきかどうかの(検証段階での)重要な指標です。
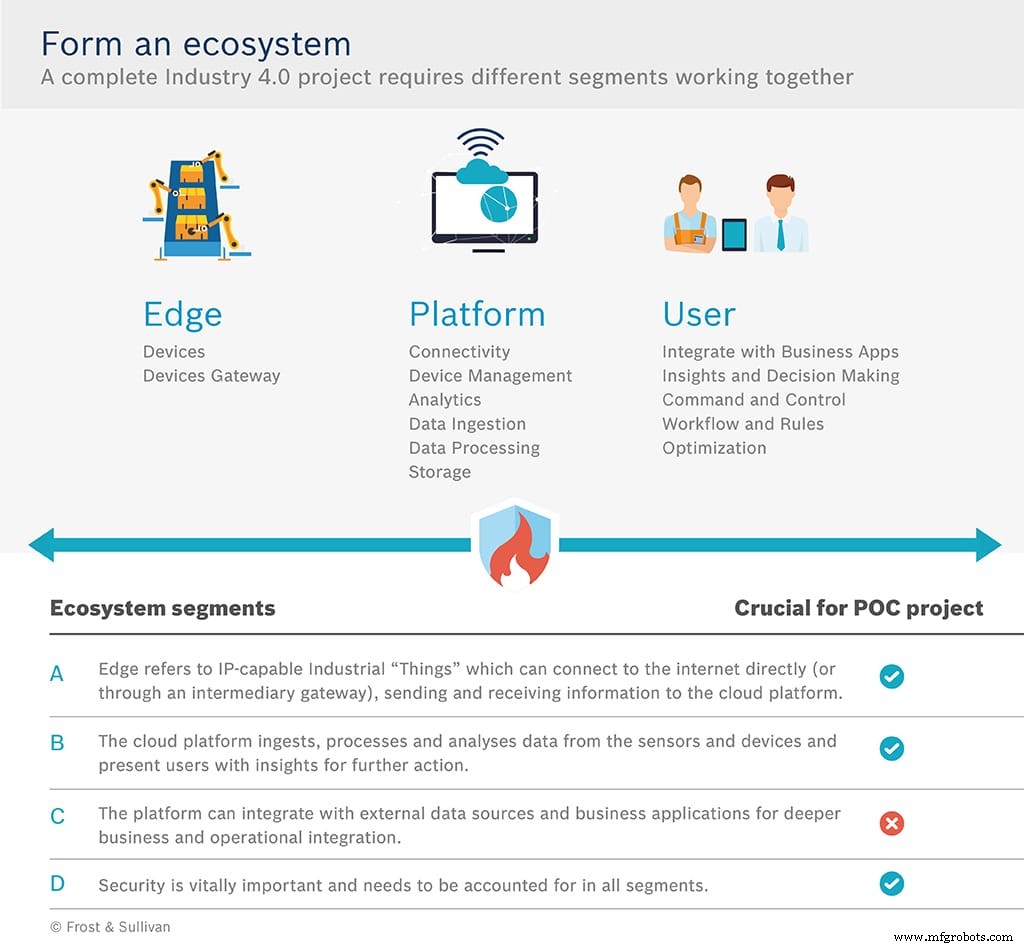
POCプロジェクトの目的では、センサーからデータを収集し、そのデータを処理および分析するためにクラウドプラットフォームを活用することが重要です。クラウドコンピューティングは、センサーからプラットフォームへの便利で手頃な接続を可能にします。パブリッククラウドでインダストリー4.0クラウドプラットフォームを試用することで、最小限のコストで小規模な導入を短期間で作成できるため、サーバーや機器に投資する必要がなくなります。
ステップ3:調査結果の検証
POCプロジェクトが稼働した後、試験の結果を定量化し、管理者の承認を得るために検証することができます。パイロット機械からセンサーによって収集されたデータを使用して、より深刻なエラーにつながる可能性のある非効率な領域や問題を特定できます。管理者はこの情報を適用して、プロセスの改善を定義し、無駄を減らすことができます。これらの改善は、データ収集と検証の次のラウンドのために製造現場で実装する必要があります。次に、ビジネス目標フェーズで定義されたベースラインを使用して、チームはベンチマークと比較した新しいステータスと状況の徹底的な分析を実行できます。製造業務によって特定された主な問題を参照すると、いくつかの潜在的な指標は次のとおりです。
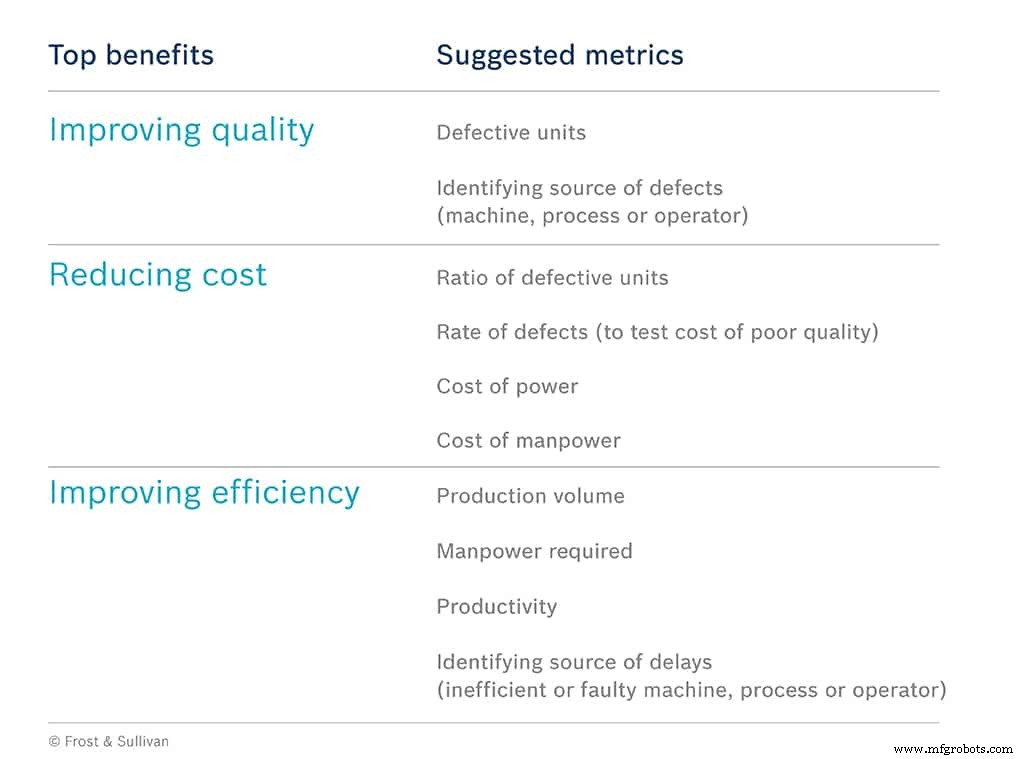
ステップ4:成功したユースケースを複製する
チームがデータを検証し、ユースケースを確認した後、プロジェクトの目標を達成した場合、POCは成功と見なすことができます。システムがセンサーとデバイスのパイロットセットで機能するようになったので、次のステップは、セットアップをより多くのマシンとラインに拡張することです。
このステップでは、システムの複雑さの規模が劇的に増大する可能性があるため、メーカーが信頼できるインダストリー4.0パートナーとチームを組むことが重要です。このパートナーは、製造元と協力して、拡張された目標と指標を満たすように設計され、運用が中断されないように段階的なアプローチで展開される、包括的なインダストリー4.0実装ビジョンを作成できます。最初のPOCプロジェクトは、いくつかの接続されたシステムで正常に機能した可能性がありますが、新しい拡張された実装によってこれが数百または数千に増加した場合はどうなりますか?単純な温度やトルクの設定から、場所、湿度、光などのデータまで、より多くの種類のデータが収集される場合もあります。
データポイント、センサー、接続されたマシンの数を増やすと、データの量が大幅に増加します。これを相殺する簡単な方法は、クラウド展開を使用してコンピューティングとストレージの容量を拡張することです。ただし、中央に配置されたサーバーに保存されるデータの増加には、企業にとって重要な資産であるデータを保護および保護するためのより厳しいセキュリティ対策も必要です。同時に、これらの対策では、許可された担当者がすべてのデータを簡単に利用できるようにする必要があります。
ステップ5:グローバルロールアウトの実施
概念実証を考案してテストしたら、最後のステップに進みます。ここでの目的は、接続されたインダストリー4.0システムをプラントの外部でより広いエコシステムに拡張することにより、さらなる効率と可視性を獲得することです。
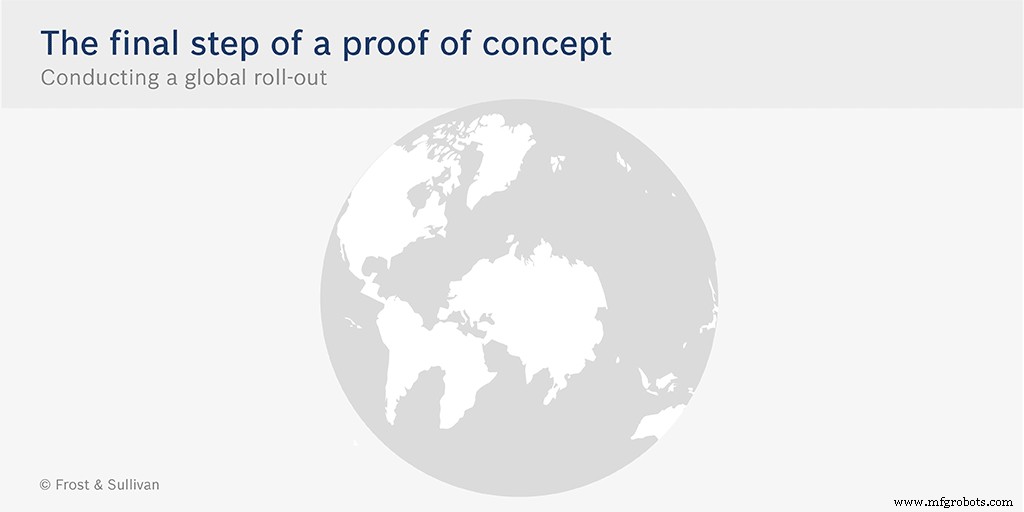
接続されたエコシステムで在庫を少なくする
通信とデータの可用性を関連するサプライチェーンパートナーに拡張することで、インダストリー4.0システムは情報のサイロをリンクして相互接続されたサプライチェーンを形成できます。その結果、より効率的でありながら、ビジネスに必要なだけの俊敏性を備えた統合ワークフローが実現します。接続されたエコシステムは、原材料とスペアパーツのジャストインタイム(JIT)配信を保証し、ロジスティクスチャネルを介して完成品を効率的にマーシャリングできます。これにより、過剰在庫が削減され、ロジスティクスコストが削減されると同時に、顧客への配送がスピードアップします。また、オペレーターは、注文量の急激な減少や急増など、市場の変化に迅速に対応できます。
価値の高い生鮮食品の追跡
より広範なエコシステムに参加することのもう1つの利点は、機密性の高い商品が指定されたパラメーターとタイムライン内で適切に配信されるようにする機能です。畑から消費者までの生鮮食品の追跡に関連する複雑さとコストが長い間大きな関心事であった食品および飲料業界を取り上げてください。サプライチェーン取引に関するリアルタイムの洞察と情報が急務となっています。現在、インテリジェントデバイスが生産バッチの間に配置され、主要なバリューチェーン参加者間で重要な情報を送信し、新鮮な生産物が最良の状態で適切な目的地に確実に届くようにしています。
インダストリー4.0を接続された工場に拡張する
最終的な目標は、複数の工場を接続して、インダストリー4.0システムから最大の利益を得ることになります。より多くのマシンがシステムに接続されると、より多くのデータが本番環境から収集され、より包括的なデータセットが作成されます。これにより、経営陣はグローバルオペレーションの統合されたビューと生産の全体像を把握し、より良い意思決定をサポートできます。これらの決定は、効率を改善するための最適化された手動プロセス、またはダウンタイムを防ぐための予測障害検出につながる可能性があります。もう1つの利点は、この大規模なデータセットの分析により、同様のマシンの障害を特定できるため、より正確な予知保全スケジュールが作成され、最終的に予定外のダウンタイムが削減されることです。
1つのチームから学ぶことによるプロセスの改善
すべてのシステムが単一の統合プラットフォームに統合されたため、チームは、成功したメトリックとベストプラクティスの改善を示すプロセスを簡単に分析し、それらを共有して世界中の他の工場に実装できます。同様に、問題を克服するために取られた問題解決の手順も共有して実装できます。
産業技術