メンテナンスの種類:比較
メンテナンスの種類
予定外のダウンタイムと資産の質の低さにより、毎年数十億ドルが失われていることはよく知られています。この統計と戦うための終わりのない戦いで、組織はさまざまなタイプのメンテナンスの1つを実装し、多くの場合2つ以上を組み合わせます。メンテナンスの種類の定義は業界によって異なるため、予防メンテナンスや予知メンテナンスなどを区別するのはかなり混乱する可能性があります。
ほとんどの種類のメンテナンスは、予防と修正の2つの主要なカテゴリに分類されます。 予防保守 障害の発生を防ぐために、タスクと保守計画を積極的に開始するときです。予防保守は、障害の防止に加えて、障害の影響を最小限に抑えること、または障害が発生するリスクを判断することを目的とする場合があります。
適切なメンテナンス 障害が発生した後に発生します。あなたのチームは基本的に、この時点でアセットを正常な状態に戻しています。明確にするために、修正保守は、失敗までの保守戦略の形で意図的に行うことができます。これについては、以下で説明します。
製造業とプロセス産業で使用される最も一般的なタイプのメンテナンスを調べてみましょう。
- 予防保守。 予防保守とは、機器を定期的に検査し、小さな問題に気づき、大きな問題になる前に修正するという確立されたルーチンです。予防保守の主な目標は、ダウンタイムをゼロにすることです。この目標は、機器の生産寿命を延ばし、重大な機器の故障を減らし、機器の故障による生産損失を最小限に抑えるという3つの目的を使用した後に求められます。
予防保守のカテゴリに分類される保守には、いくつかの種類があります。これらには以下が含まれます:
- 使用量ベースのメンテナンス これは、各アセットの実際の使用量に基づいてトリガーを使用します。機器モニターで資産の使用状況を追跡することで、保守管理者は事前設定されたパラメーターに従って予防保守スケジュールを設定できます。
- 処方メンテナンス 予防保守によく似ていますが、人工知能(AI)やモノのインターネット(IoT)などの機械学習ソフトウェアを活用して、予防保守タスクのスケジュールを設定します。
予防保守の種類、予防保守プログラムの設計方法、予防保守ツールなどの詳細については、このセクションの冒頭にあるリンクを確認してください。
- 予知保全。 予知保全とは、通常の運用状態で機器の性能や状態を監視し、故障の可能性を低減する保全です。予防保守に似ており(一部の人々はそれを予防保守の一種として分類することさえあります)、条件ベースの保守(CBM)と密接に関連しています。 、予知保全の目標はその名前にあります。最初に障害が発生する可能性がある時期を予測し、次にスケジュールされた修正保守によって障害を防止することです。
多くの組織が予測保守と予防保守の両方を採用していますが(最近の信頼できるプラントの調査によると、76%が予防保守を使用し、65%が予測保守を使用しています)、いくつかの重要な違いがあります。最も注目すべきは、予防保守は、予知保全のように状態監視の側面を必要としないことです。これは、予知保全が赤外線サーモグラフィー、音響モニタリング、振動分析、オイル分析などの条件ベースのテクノロジーを利用することを意味します。もう1つの重要な違いは、予防保守には、機器の保守が必要かどうかに関係なく、資産の検査と保守の実行が含まれることです(保守スケジュールはトリガーに基づいています)。予知保全はしません。
以下は、条件ベースのメンテナンスが予測的および予防的なメンテナンスとどのように関連しているかを示すグラフです。ここで、予知保全は、CBMに由来する2つの側面の1つです。障害の根本原因を見つけることに焦点を当てる予防的な側面と、障害の症状と障害に集中する予測的な側面です。
予知保全、予知保全技術などの詳細については、このセクションの冒頭にあるリンクをクリックしてください。
- 信頼性中心のメンテナンス(RCM)。 信頼性中心のメンテナンスは、機器の潜在的な問題を特定し、それらの資産が最大容量で生産され続けるようにするために何をすべきかを決定するプロセスです。つまり、内訳を分析して、個々の資産ごとに適切なメンテナンス方法とカスタマイズされたメンテナンススケジュールを把握します。
信頼性中心の保守は予防保守と混同されることがありますが、重要な違いが1つあります。予防保守はRCMのように選択的ではなく、効率が低下します。 RCMは各資産を個別に確認するため、各機器に合わせたメンテナンスタスクを割り当てることで、非効率性を軽減します。
信頼性中心の保守では、一般的な4つのステップのワークフローを使用します。資産を選択し、資産を評価し、保守のタイプを決定して、プロセスを繰り返します。 RCMプログラムを実装するための評価基準では、次の7つの質問があります。
- この機器のパフォーマンスはどの程度ですか?
- この機器はどのように故障する可能性がありますか?
- それぞれの失敗の原因は何ですか?
- 障害が発生するとどうなりますか?
- それぞれの失敗が重要なのはなぜですか?
- これらの障害の発生を防ぐために、どのようなタスク(プロアクティブ)を実行する必要がありますか?
- 適切な予防タスクが見つからない場合はどうすればよいですか?
このセクションの冒頭にあるリンクをクリックして、RCMの実装方法、RCMプログラムを実装した組織の実際のケーススタディなど、信頼性中心のメンテナンスの詳細をご覧ください。
- 総合的設備管理(TPM)。 総合的生産的メンテナンスとは、機械、設備、従業員、およびサポートプロセスを使用して、生産とシステム品質の整合性を維持および改善するプロセスです。 TPMプログラムの目標は、予防および自律保守、機械オペレーターのトレーニング、作業プロセスの標準化などのコア領域に対処するための小規模な学際的なチームを形成することにより、設備総合効率(OEE)を向上させることです。総合的生産管理は、組織内のすべての部門に焦点を当て、生産手段の効率的かつ効果的な使用を保証します。
総合的生産的メンテナンスは、プログラムというよりもプロセスであると見なされ、本格的なメンテナンスプログラムではなく、運用改善プロセスと見なされます。また、高品質のTPMプロセスから最大の利益を得るには何年もかかるため、これは迅速な解決策ではありません。ただし、結果はすぐに確認できます。
総合的生産管理には、リーン生産方式と、自律保守、集中的改善、計画保守、品質保守、早期設備管理、トレーニングと教育、安全、健康、環境の8つの柱で構成される国際的に認められたベンチマークの5-Sシステム技術が組み込まれています。および管理におけるTPM。
TPMの実装には、次の5つのフェーズが含まれます。
- パイロットエリアを特定する
- 機器を最高の動作状態に復元します
- OEEを測定する
- 大きな損失に対処/削減する
- 計画的なメンテナンスを実施する
このセクションの冒頭にあるリンクをクリックして、TPMの8つの柱、その実装方法、TPMプロセスの維持方法など、TPMの詳細をご覧ください。
- 自律メンテナンス。 自律保守は、オペレーターをトレーニングして機器を継続的に監視し、調整を行い、マイナーな保守タスクを実行して効率を高めることで構成される保守戦略です。これは、定期的にスケジュールされた維持管理を実行するために保守技術者を専念させる代わりに行われ、より重要で差し迫った保守作業のために彼らを解放します。
自律保守には2つの基本原則があります。適切な操作によって機器の劣化を防ぐことと、復元と適切な管理によって機器を「新品同様」の状態に保つことです。これには、オペレーターが機械のコンポーネントを理解し、改善を行い、品質の問題を特定し、品質の問題の原因を突き止めることによって異常を検出するなどのスキルを習得する必要があります。
自律保守の実装には、オペレーターの知識の向上、初期の機械の清掃と検査、汚染の原因の除去とアクセスの改善、潤滑と検査の基準の開発、検査と監視、視覚的な保守の標準化、継続的な改善の7つのステップが含まれます。
自律型メンテナンス、その実装方法、およびそれを維持する方法の詳細については、このセクションの冒頭にあるリンクをクリックしてください。
- Run-to-Failure Maintenance(RTF)。 実行から障害までのメンテナンスは、計画外の事後対応型のメンテナンスであり、通常、コストを最小限に抑えるように設計された意図的な戦略です。組織は、使い捨て資産(修理ではなく交換することを目的とした使い捨て部品を備えた機械)、工具などの重要ではない資産、耐久性のある資産、摩耗の影響を受けない、または摩耗する可能性が低い資産などにRTFプランを採用することを選択できます。通常の動作条件下で障害が発生するか、予測できないランダムな障害パターンを示す資産。
RTFメンテナンスの注意点は、適切な判断が必要なことです。何かを修復するのではなく、いつ大規模な障害にラベル付けするかを知ることは、RTFメンテナンスに付属するスキルセットの一部です。資産が監視されていないため、リスクが発生する可能性があり、何かが壊れたときに組織が計画外のダウンタイムのバレルを凝視する原因になります。
ただし、避けられない障害に対処するためのスマートな計画を使用して適切な資産に実装すると、RTFは、壊れていない機器を交換しないことで時間と費用を節約できます。
機械のメンテナンスと人体の並列化
メンテナンスの種類、技術、コストに関しては、主要な種類のメンテナンスを人体と比較して、同等の「ボディメンテナンス」タスクのスナップショットを取得できます。次の表は、発電資産の例を使用して、それを人間の心臓と比較しています。
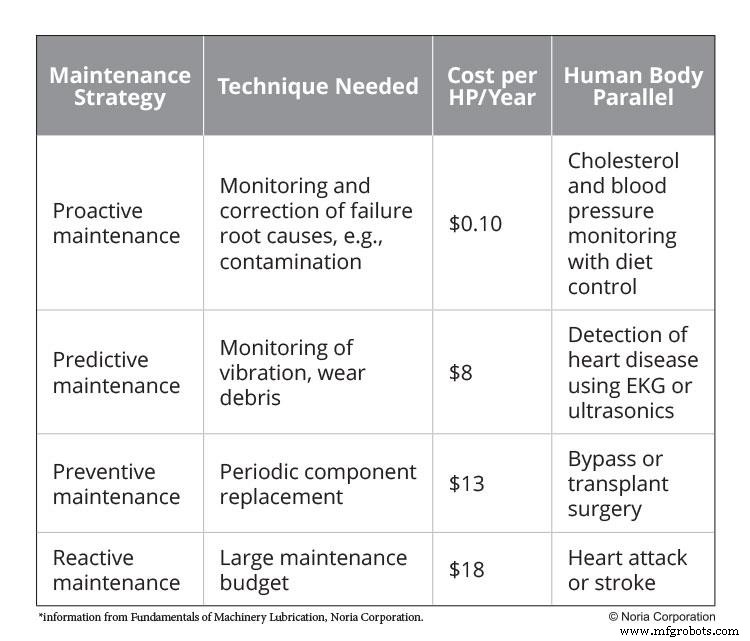
メンテナンストリガーの種類
メンテナンストリガーを設定して、複数のタイプのメンテナンスで使用できます。故障トリガーは、故障までの実行または事後対応型の保守計画で使用されます。予知保全は、アラートの形で時間ベースのトリガーなどを使用して、障害の発生を防止しようとします。説明するその他のトリガーには、イベントベース、使用状況ベース、および条件ベースのトリガーが含まれます。
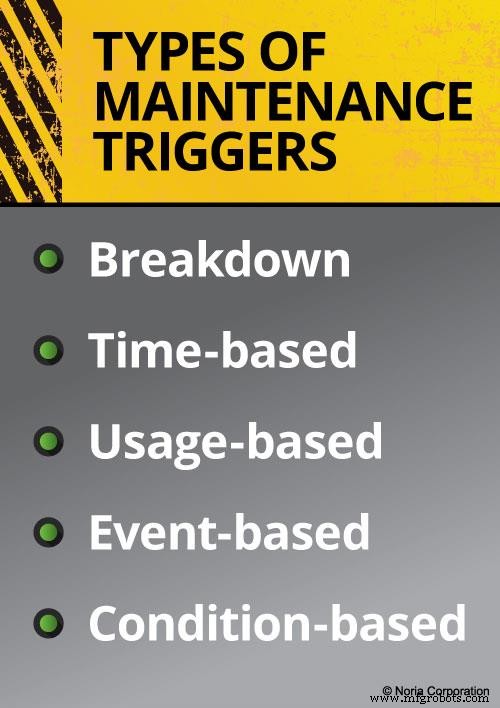
- ブレークダウントリガー。 前述のように、故障トリガーは、故障までの実行または事後対応型の保守プログラムで使用されます。アセットが機能しなくなると、アラートがトリガーされ、アセットを修復して通常の動作状態に復元するためのメンテナンス作業指示がスケジュールされます。
故障トリガーは通常、組織が低コストで交換が容易な機器のグループを実行していて、交換部品とユニットが在庫にあり、簡単かつ簡単に交換できるため、ダウンタイムを可能な限り最小限に抑える場合にのみ役立ちます。ブレークダウントリガーの使用は、いたちごっこゲームに似ています。メンテナンスの計画を立てる必要がないため、メンテナンス予算を節約できますが、問題を解決するための人員だけでなく、スペアパーツと機器を常に利用できるようにする必要があります。このような株式の保有は、保有株式を削減するように設計されたジャストインタイム(JIT)のようなリーン原則に反します。
- 時間ベースのトリガー。 おそらく、最も一般的に使用されるメンテナンストリガーは時間ベースです。これらは、コンピュータ化された保守管理システム(CMMS)などの保守計画ソフトウェアにリンクされており、事前設定された時間間隔に基づいてアラートを出します。時間ベースのトリガーは、ギアの潤滑や検査のスケジュール設定などの単純なタスクの予測および予防保守プログラムで使用されます。たとえば、アセットが14日間の実行時間に達すると、アラートがトリガーされてサービスが提供されます。製造環境以外では、時間ベースのトリガーにより、暖房、換気、および空調(HVAC)ユニットのエアフィルターが3か月ごとに交換されます。
- 使用量ベースのトリガー。 時間ベースのトリガーと同様に、使用量ベースのトリガーは、期間に関係なく、問題の資産の使用量に基づいて事前に決定されたメトリックに依存します。マシンの状態に関係なく定期的に実行される時間ベースのトリガーとは異なり、使用量ベースのトリガーは、資産が特定の量のサービスを完了した後にのみメンテナンスを受けることを意味します。
車が5,000マイルごとにオイル交換を行うのと同じように、時間制限または数量制限のある操作を実行するマシンは、使用量ベースのトリガーを使用してセットアップできます。メーターの読み取り値をCMMSに追加し、目的の数量または値に達したときにアラートを設定するために使用できます。使用量ベースのトリガーは、不規則なタイムテーブルの影響を受ける機器を保守するための優れた方法であり、ほとんどの場合、予測または予防保守プログラムで使用されます。
- イベントベースのトリガー。 イベントトリガーは、火災や洪水などのイベントが発生した後、機器や施設に対応して評価するために使用できます。たとえば、洪水後の電気システムとインフラストラクチャのチェックをスケジュールして実行する必要性は、CMMSによって推進され、システムはそのようなタスクについて保守チームに警告します。イベントベースのトリガーはイベントが発生した後に発生しますが、すべてがイベント自体に直接接続されているとは限りません。ほとんどのイベントベースのトリガーは、イベントのフォローアップチェックとして機能します。
- 条件ベースのトリガー。 条件ベースのトリガーは、個々の資産の評価に従って使用されます。この評価は、資産の実行を継続できるかどうか、またはメンテナンスが必要かどうかを判断するために使用されます。これは、保守担当者が資産の状態について十分な情報に基づいた決定を行うために資産の実用的な知識を持っている必要があるため、より詳細なオプションです。
機器の状態もリモートで評価できます。温度、振動、ノイズなどのパラメーターを監視するために資産に配置されたセンサーは、状態によってトリガーされるアラートとして使用できます。たとえば、センサーが所定の範囲を超える温度の急上昇に気付いた場合、検査をスケジュールするためにアラートが送信されます。
最新のメンテナンステクノロジー
メーカーが運用保守で優れている最大の鍵の1つは、最新のテクノロジーによって提供されるデータを使用することです。これを行うには、資産、従業員、およびプロセスを整理してシームレスに機能させるために、新しいメンテナンスソリューションがほとんど必要です。
技術の進歩は、予防的および予知保全の形での状態ベースの監視で最も普及しています。これらのタイプのメンテナンスでは、オイル分析、振動分析、サーモグラフィー、モーター電流分析などのテクノロジーが、根本原因と障害の症状を特定し、機械の寿命を延ばしたり、障害を早期に検出したり、障害の数と影響を減らしたりするのに役立ちます。
製造業における今日の技術革命は、エラーや欠陥の減少、生産の最適化、人件費の削減につながりました。機械を継続的に監視できる自動センサーは、最大の改善点の1つです。複数の種類のメンテナンスで使用できるだけでなく、分析してプロセスを改善するために使用できる大量のデータを生成することもできます。
CMMSソリューションは、これらすべてのデータを活用し、予知保全の使用、データとIoTの重視、在庫の管理、継続的な成功のためのサイクルの改善という、最新の保守技術戦略の4つの主要な側面と統合するのに役立ちます。
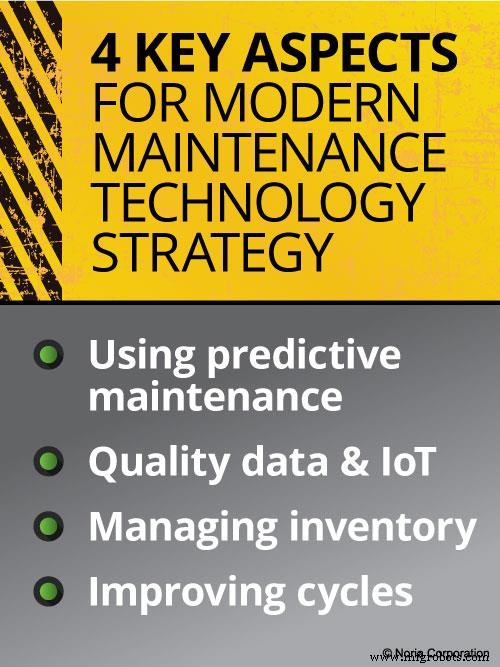
- 予知保全の使用: 予防保守は、障害が発生してダウンタイムが発生するのを防ぐための優れた方法ですが、次のステップは、予知保全を実装して、マシンが生成しているデータを効率的に収集および分析することです。
- 品質データとIoT: プラント全体で生成される大量のデータを処理できるCMMSを用意することが重要です。基本的な自己インストール型センサーから組み込みセンサーまで、およびその間のすべてのデータを統合する必要があります。これは通常、単一のタイプのハードウェアと結婚しないように、IoT戦略を備えたCMMSを探す必要があることを意味します。
IoTは、プラントフロアの資産から収集されたデータを組織全体で利用されるCMMSにワイヤレスで統合するために採用されています。これには、人の介入なしに作業指示書を自動的に作成するために、前述のトリガーとアラートを設定する必要があります。
- 在庫の管理: 最近のプラントサービスの調査によると、回答者の29%近くが3〜4週間のメンテナンスタスクのバックログを抱えていました。メンテナンスに対して常に事後対応的なアプローチを取ると、バックログが増えるだけです。つまり、資産は必要な適切なメンテナンスを受けていません。 CMMSでバックログされたタスクを追跡することは、問題、原因、および解決策を特定するのに役立ち、バックログを減らすためのより積極的な文化を受け入れることにつながります。
- サイクルの改善: 最新のプラントフロア設定からのデータを活用し、CMMSを介して統合することで、メンテナンスサイクルを改善し、節約を維持し、効率を高めることができます。
最新のメンテナンステクノロジーのトレンド
- 産業用モノのインターネット: 前に説明したように、モノのインターネット、より具体的には産業用モノのインターネット(IIoT)は、ワイヤレスセンサーのネットワークを使用した最新の自動データ収集形式です。今日、低コストの多目的センサーがこれまでになく簡単に利用できるようになりました。これらは、複数の産業資産上の異なるセンサーネットワークに構成でき、メンテナンスデータを自動的に収集するために使用できます。これにより、人的エラーが発生しやすい、高価で時間のかかる手動データが不要になります。
- 拡張現実(AR): リモート命令を提供する機能のおかげで、リモートメンテナンスとトレーニングはARの恩恵を受け始めています。このカスタマイズされたアプローチにより、メンテナンスタスクを従業員の理解とスキルレベルに合わせてカスタマイズできます。拡張現実は、タスクの実行方法を示すサイバープレゼンテーションを介して、機器ベンダーまたは上級レベルの保守担当者が提供するトレーニングを容易にすることができます。
まだ新しい傾向ですが、産業機器の複雑さが増しているため、トレーニングにARを使用することが人気を集めています。拡張現実は、各資産に付随する技術的に高度な機能を含む、新しい機器のバリエーションに対応しようとする保守担当者の負担を軽減することができます。メンテナンスタスク用の大規模なARソリューションを提供するベンダーや、バンドルパッケージの一部としてARを提供するIIoTプロバイダーはすでにいくつかあります。
- サービスとしてのメンテナンス(MaaS): MaaSは、メンテナンスの世界にとってかなり新しいパラダイムです。基本的に、オンデマンドでメンテナンスサービスを提供する必要があります。 MaaSを使用すると、ベンダーは、定額のサービス料金の代わりに、実際に使用する保守サービスに応じてプラントオペレーターに請求できます。ベンダーは、大量のデータを収集して処理し、クラウドを介してそれらを保存し、このデータに基づいてタスクをスケジュールすることによってこれを行います。サービスが含まれます:
- 資産の存続期間を予測するか、最適なメンテナンス間隔に関する洞察を提供します。
- サービスマニュアル、ビデオ、バーチャルリアリティ(VR)およびARインタラクティブサポートを提供します。
- 分析結果に基づいてプラント内で情報技術(IT)およびその他のシステムを構成する。および
- 機械に関する詳細な統計とレポートを提供します。
MaaSプログラムの初期段階は、ベンダーによって利用可能になり始めています。ティッセンクルップエレベーターには、問題が発生する前に問題を予測し、適切な担当者に検査を実行するよう通知する予防保守プログラムが付属しています。 BMWはまた、近い将来、MaaSを消費者に提供することを計画しており、車の所有者に車のメンテナンスを行うのに最適な時期を知らせるプログラムを提供しています。
機器のメンテナンスと修理