リスクベースのメンテナンス(RbM)の実装|レイマンの用語で分解
すでに限られたリソースを必要のない資産に費やさないことで、時間とリソースを節約できるかどうかを自問したことはありますか?
資産管理のメンテナンス戦略を作成することで時間とお金を節約できるかどうか疑問に思いますか?
リスクベースのメンテナンス(RbM)ガイド 信頼性を向上させ、コストを削減し、機器のライフサイクルと整合性を経済的な方法で向上させながら、メンテナンスリソースを使用する最も効率的な方法をすばやく分析する方法を、素人の言葉で段階的に説明します。
デンマークのオールボー大学によるオフショア鉄骨構造に関する調査では、ある企業が総修理費を80%以上節約できた方法が概説されています。
リスクベースのメンテナンスとは何ですか?なぜそれが重要なのですか?
リスクベースのメンテナンスは非常に堅牢で複雑になる可能性がありますが、一言で言えば、メンテナンスリソースの最も経済的な使用法を判断するのに役立ちます。リスクベースのメンテナンスと信頼性中心のメンテナンスの違いは何ですか?
これは複雑に聞こえるかもしれませんが、プロセスは比較的単純です。以下の要点を詳しく説明しますが、リスクベースの修正メンテナンスの要点は、重要/問題のある資産を見つけて、重要でない資産からリソースを転用しながら、それらにメンテナンスリソースを割り当てることです。
正しく行われた場合、報酬は素晴らしいです。ヨーロッパの石油ガス会社は、リスクベースのメンテナンスを利用して、年間1,500万ドル以上を節約することができました。
リスクベースのメンテナンスをどのように実装しますか?
リスクベースのメンテナンスでは、予防(障害の可能性)と回復(障害の結果)という2つの主要な測定値を分析する使命を負っています。
開始するには、まず、これら2つのフレーズの意味を理解する必要があります。
失敗の確率 単に「この機器が故障する可能性はどのくらいですか?」という意味です。
多くの場合、故障の確率(PoF)は、機器の使用年数(実行時間)と相関関係があります。
ただし、時間だけを考慮する必要はありません。意思決定と失敗の可能性に関しては、労働条件が重要です。
濡れた場所やほこりの多い場所にある資産は、より多くの維持管理が必要になる可能性があり、失敗する可能性が高くなります。ご想像のとおり、地理、気候、その他の環境条件などがPoFを決定する上で重要な役割を果たします。
失敗の結果 つまり、「このマシンの故障費用はいくらですか?」
失敗の結果(CoF)を決定する際には、できるだけ多くの要因を考慮する必要があります。次のような質問を自問することをお勧めします:
- 平均修理費はいくらですか?
- このマシンが適切に機能していないために、ダウンタイム(生産損失)で毎年どのくらいの損失がありますか?
- この機器の故障に関連する事故はありますか?このマシンのメンテナンスプロセスにより、他の生産領域の速度が低下していませんか?
- このマシンのメンテナンスアプローチまたはメンテナンスの欠如に関連する安全上の問題はありますか?
ご覧のとおり、修理費用だけでなく、考慮すべきことがたくさんあります。
用語を理解したので、プロセスを開始しましょう。
1。メンテナンスデータを収集する
他のことをする前に、現在のメンテナンスデータを収集して分析する必要があります。ここでの目標は、手元のデータを利用して問題のある領域を特定することです。
あなたはあなたの資産とそれらがあなたに費やしているもののまともな目録を手に入れる必要があるでしょう。これを行うには、CMMSおよびその他のメンテナンス記録を参照してください。 CMMSとは何かについて詳しくは、CMMSシステムとは何かとその仕組みガイドをご覧ください。
これらの記録から、施設内の各機器について次のことを知りたいと思うでしょう。
- この機器は何歳ですか?
- 機器が故障する頻度はどれくらいですか? (MTBF)
- 機器を正常な状態に戻すにはどのくらい時間がかかりますか? (MTTR)
- この機器が故障した場合の費用はいくらですか? (生産の中断、部品コスト、人件費など)
- この機器のメンテナンスはどのくらいの頻度で行いますか?
すべての機器のデータを取得したら、注意が必要な資産を特定する必要があります。
これを行うにはいくつかの優れた方法がありますが、この投稿では、例として重要度マトリックスを使用します。
あなたが素晴らしいCMMSを持っている幸運な数少ない人の一人であるなら、それはあなたにあなたの問題の資産を自動的に教えてくれます。たとえば、Limble CMMSでは、問題のあるアセットがリストの一番上に表示される強力なレポートセクションを作成しました。これにより、どのアセットが最もコストがかかり、その理由が一目でわかります。
2。重要度マトリックスで視覚化
重要度マトリックス(これは非常にオタクで複雑に聞こえますが、そうではありません)は、失敗の確率がX軸(水平方向)にプロットされ、失敗の結果がY軸にプロットされた単純なグラフです(垂直方向)。このように:
グラフの作成方法を示すために、例を使用してグラフを少し分解します。
次の機器のインベントリを作成したとします:ジェネレーター11、12、および13 。
各機器のメンテナンス記録を確認し、それぞれのPoFとCoFを決定するために必要なデータを入手しました。
これをグラフ化するには、各ジェネレーターが故障する可能性を表すスコアを割り当てることにより、ジェネレーター11、12、および13の故障確率(PoF)をスコアリングする必要があります。
スコア範囲は次のようになります:
1 =3年以内に障害が発生する可能性は非常に低い
2 =3年以内に障害が発生する可能性は低い
3 =障害は発生しないまたは発生しない
4 =障害が発生する可能性がある
5 =失敗する可能性が高い
ヒント#1:任意のタイプのスコアリングシステムを使用できます。パーセンテージを考えるのが簡単な場合(つまり、失敗の可能性が10%、失敗の可能性が20%など)、ぜひともそれを選択してください!
スコアリングフレームワークが設定されたので、スコアリングを行いましょう。
私たちのデータによると、過去3年間で、発電機11は5回故障し、発電機12は2回故障し、発電機13は3回故障しました。これらの数値に基づいて、次のスコアを付けましょう。
障害スケールの確率
ジェネレーター11–スコア5
ジェネレーター12–スコア2
ジェネレーター13–スコア3
次に、各ジェネレーターに失敗の結果スコアを割り当てます。ここでも、各資産の結果のレベルを表すスコアリングシステムを作成する必要があります。 (CoFは任意の方法でスコアリングすることもできます)。
障害の影響を測定しましょう:
ジェネレーター11 –この発電機は、移動式の夜間乗務員が照明用の電気を供給するために使用します。それが壊れた場合、乗組員は仕事を続けることができず、無駄な時間、労働プロジェクトの遅延などで5,000ドルかかります。修理費用は通常、故障ごとに300ドルです。
ジェネレーター12 –これはめったに使用されない古いジェネレーターです。この発電機の故障は大きな影響はありません。修理作業、無駄な時間、労力などはたったの500ドルです。修理費用は通常、故障ごとに300ドルです。
ジェネレーター13 –このマシンは、庭でのランダムなワークアウトに使用されます。庭でのランダムな作業は緊急ではありませんが、完了できない場合は費用がかかります。無駄な時間や労力などの推定損失は2,500ドルです。修理費用は通常、故障ごとに200ドルです。
障害スケールの結果
1 =年間コストが2,500ドル未満
2 =年間コストが2,500ドルから5,000ドルの間
3 =年間コストが5,000ドルを超える
次に、各マシンの特定の結果(コスト)に基づいて、各ジェネレーターにスコアを割り当てます。そのように:
ジェネレーター11 =3
ジェネレーター12 =1
ジェネレーター13 =2
ヒント#2:失敗の結果を理解するための最良の方法は、チームと話し合うことです。特定の機器が機能しない場合に何が起こるか、そしてそれが彼らに何をもたらすかを彼らに尋ねてください。 CMMSまたはメンテナンスの記録を見て、修理費用を確認してください。これらのアクションにより、機器の故障の真のコストに関する優れた洞察が得られます。
失敗の確率と失敗の結果のスコアがわかったので、データをプロットします。このグラフは次のようになります:
赤い領域(番号11と13)に隣接しているか、内側にある発電機は、グラフの左下(番号12)にある機器よりもはるかに高いリスクレベルを持っています。この場合、発電機11および13の新しい保守戦略を検討する可能性があります。
これは、クリティカルマトリックスの非常に単純なバージョンです。これは、少数のアセットのみをプロットし、PoFとCoFのスコアリングを非常に基本的なものにしたためです。ただし、どの資産が保守計画から最も恩恵を受けるかについては、依然として優れた見解を持っています。アセットが多いほど、このグラフはメンテナンスプログラムのアセットをすばやく選択するのに役立ちます。
リアクティブメンテナンスを73.2%削減
ケーススタディ
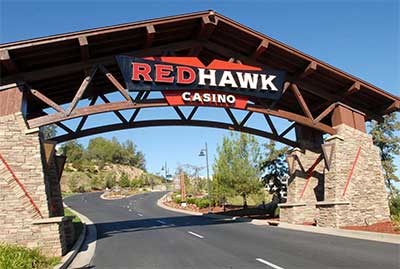
どのタイプのメンテナンスを実装するかをどのように知っていますか?
どの資産にメンテナンス計画が必要かがわかったので、各マシンに適切な計画をどのように選択しますか?
私たちはあなたにそれを破ることを嫌いますが、あなたの会社に自動的に最適になる事前に決定された標準的な戦略はありません。施設はそれぞれ異なり、さまざまな機器で満たされ、さまざまな製品を製造し、さまざまな人間が機器を操作しています。
ここで述べられていることは、実装する保守戦略を決定するときに役立ついくつかの質問です。
メンテナンスリソースはいくらですか?
残念ながら、メンテナンスの世界では、リソースプールが縮小し続けることで、毎年より多くのことを行うことが期待されています。完璧な世界では、メンテナンススタッフは仕事を正しく遂行するのに十分な人数ですが、そうなることはめったにありません。メンテナンス戦略を検討するときは、リソースを検討する必要があります。
たとえば、予防保守計画は、PMがスケジュールされたときにPMを実行するための人的資源がない場合、ほとんど効果がありません。
メーカーは何を推奨していますか?
製造元は、頼りになる情報源である必要があります。多くの場合、機器のマニュアルには、適切に保守するために実行する必要のある作業の詳細な概要が記載されています。とはいえ、これらは一般的なガイドラインであり、状況に応じて、頻度を増減することをお勧めします。
各資産の交換にかかる費用と、予想される残存期間はどれくらいですか?
残りの寿命が短い非常に古い資産がある状況では、資産を失敗させてから、交換品を購入するのが最善であると思うかもしれません。アセットのCoFが非常に高い場合、これは当てはまらない可能性がありますが、幸いなことに、この答えを見つける方法を知っています🙂
クリティカルマトリックスのどこに到達しましたか?
アセットがマトリックスの右上隅(非常に危険な領域)に着地した場合は、何らかの戦略を実施する必要があります。定期検査を割り当てたり、予知保全計画を実施して、絶対に修理が必要な場合にのみ機器を修理できるようにすることができます。
大きな決断をする前に、すべての選択肢を知っていることを確認してください。各アプローチの長所と短所を学ぶために、メンテナンス戦略の詳細な比較を確認してください。
小規模から始めてから規模を拡大することでリスクを軽減します
アセットに適したメンテナンス方法を特定したら、小規模から始めて成功する可能性を高めることができます。つまり、数個の機器を使用して計画を実行に移します。進捗状況を監視し、成功した場合はそこから戦略を拡大します。
メンテナンスプランを実装することにした場合は、CMMSソリューションへの投資を検討する必要があります(CMMSソリューションがない場合、または古くて古いパッケージを使用している場合)。
Limble CMMSを使用すると、ワークフローを合理化し、品質データを収集し、重要な決定をすばやく下して、手のひらから会社の生産を最適化できます。
機器のメンテナンスと修理