単純な圧延層を介したリチウムイオン電池用のエレクトロスピニング繊維に基づくバインダーフリー電極
要約
より高いエネルギー密度とより小さなサイズのリチウムイオン電池(LIB)の需要に伴い、高比容量の活物質の開発と不活性物質の使用量の削減が主な方向性です。ここでは、エレクトロスピニングされた膜を市販の集電体に直接転がすことにより、優れた安定したLIBのためのバインダーフリー電極のための普遍的な方法が開発されています。圧延プロセスは、繊維構造を変えることなく繊維ウェブをより高密度にするだけであり、繊維ウェブは依然として多孔質構造を維持する。この戦略は、直接炭化エレクトロスピニング膜と比較して、膜の構造安定性を大幅に改善します。さらに、この方法はさまざまな重合性接着剤ポリマーに適しており、各ポリマーは異なるポリマー、無機塩などと合成できます。この方法で調製した電極は、電流密度2500で2000サイクル以上安定してサイクルできます。 mA g -1 。この研究は、実験的研究と実用化のために、高エネルギー密度と安定性を備えたLIB電極を設計するための費用効果が高く用途の広い戦略を提供します。
背景
リチウムイオン電池(LIB)は、ポータブルデバイス、電気自動車、および定置型エネルギー貯蔵システムに広く適用されています[1、2]。エネルギー密度は、LIBの最も重要なパラメータの1つです。アノードおよび/またはカソード材料の比容量を改善するために多くの努力がなされてきたが、電極材料中の電気化学的に不活性な成分を減らす研究は限られている。バインダーおよび導電性添加剤としてそれぞれ約10wt。%のポリフッ化ビニリデン(PVDF)および炭素材料を使用する最先端のバッテリー調製プロセスは、LIBの比容量およびエネルギー密度を制限します[3]。電極中の不活性物質の量を減らすことは、エネルギー密度を改善するための効果的な方法です。したがって、活物質と導電性基板のみで構成されるバインダーフリー電極は、電極のエネルギー密度を高める新しい機会を提供します[4]。
今日、バインダーフリー電極を調製する方法は、主に水熱合成、蒸着などであり[5,6,7,8]、これらは一般に限られた規模で過酷な条件下で動作します。バインダーフリーの電極は、エレクトロスピニング技術によって簡単で用途が広く、費用効果の高い方法で簡単に製造できますが[8]、準備されたままの膜は炭化後にもろくなることがよくあります[9]。したがって、電極は、有機溶液中で炭化材料をPVDFと混合および粉砕することによって準備する必要があり、これは時間がかかるだけでなく非効率的でもあります。粉砕プロセスは、粒子サイズの減少、表面積の増加、および電解質への活物質の曝露につながる可能性があり、これらはすべて、電気化学的性能の低下をもたらします[10]。したがって、高度なバインダーフリー電極用の安定したエレクトロスピニング膜を設計することは非常に重要です。
ここでは、エレクトロスピニングされたメンブレンを市販の集電体に直接転がすことにより、安定したLIB用のバインダーフリー電極用のユニバーサルメソッドが開発されています。繊維ネットワークの多孔質構造は、圧延プロセス後も維持できます。この方法は、直接炭化膜と比較して、膜の構造安定性を大幅に改善します。活物質の出力とエネルギー密度は、独自のバインダーフリープロセスによって大幅に向上させることができます。さらに、さまざまな重合性接着剤ポリマーをこの研究のエレクトロスピニング膜源として使用することができ、無機塩または粒子をポリマーに添加して高性能電極を製造することができます。この方法で作成された電極は、2500 mA g -1 の電流密度で2000サイクル以上安定してサイクルすることができます。 。
仮説の提示
バインダーフリー電極は、高エネルギー密度のリチウムイオン電池に有望です。エレクトロスピニングされた膜を市販の集電体に直接圧延することにより、安定したLIB用のバインダーフリー電極用にユニバーサルローリングプレス法が開発されました。繊維ネットワークの多孔質構造は、圧延プロセス後も維持できます。この方法は、直接炭化膜と比較して膜の構造安定性を向上させます(図1)。
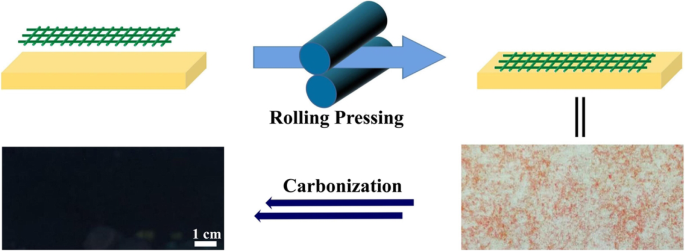
バインダーフリー電極の製造の概略図。エレクトロスピニングされた膜は、最初に集電体に押し付けられ、次に電極を実現するために熱処理されます
仮説の検定
繊維膜の製造
同軸エレクトロスピニング針はChangshaNanoapparatusChinaから購入しました。コアシェル繊維膜は、ジメチルホルムアミド(DMF)中の10 wt。%ポリアクリロニトリル(PAN)と8 wt。%ポリメチルメタクリレート(PMMA)をそれぞれ外側と内側のキャピラリーから押し出すことによって得られました。 PANおよびPMMA溶液の流量は0.54および0.27mL h -1 でした。 、 それぞれ。銅箔で覆われた円筒形のローラーを針の下に約11cmの距離で垂直に置き、繊維を集めました。電圧は14kVに制御されました。得られた材料は、Cu箔なしおよびCu箔ありで熱処理した後、それぞれPMMA @PANおよびPMMA @ PAN @Cuとラベル付けされました。得られた膜を最初にローリングプレスでプレスし、次に空気中で280℃で2時間、5℃min -1 の加熱速度で酸化した。 。その後、管状炉に移し、N 2 を流しながら650°Cで2時間炭化しました。 。酸化物@PMMA @PANと酸化物@PMMA @ PAN @ Cuは同じ方法で製造され、DMF中の無機塩とPMMAの内部溶液とPANの外部溶液が同時に押し出されました。
膜の特性評価
バインダーフリー電極の形態は、走査型電子顕微鏡(SEM、日立、SU-8010)によって特徴づけられました。膜の結晶構造は、X線回折(XRD、SmartLab、Rigaku)およびラマン分光法(Horiba、HR-800)によって調べられました。 XRDは、5 o の間の2θでテストされました。 および80 o CuKα源の下(波長=1.5406Å)。ラマン分光法は、1000〜2000 cm -1 の100mWの入射レーザー出力でテストされました。 。
電気化学的特性評価
電気化学的性能は、作用電極としてファイバーメンブレンディスクを、対電極としてリチウム箔を備えたコイン電池を使用して評価されました。電解質には1mol L -1 が含まれていました LiPF 6 エチレンカーボネート(EC)とジメチルカーボネート(DMC)の混合物(v / v =1:1)。静電流放電-充電サイクルは、0.01〜3 Vの電圧範囲でLandシステム(CT2001A、BTRBTS)で調べられ、電流密度は250 mA g -1 に設定されています。 活性化のための最初の5サイクルで、2500 mA g -1 に徐々に増加しました 次のサイクルで。
仮説の意味
プレス加工は、エレクトロスピニングされた膜とCu箔の物理的な組み合わせです。プレスするとき、溶剤を含むエレクトロスピニングされた繊維はバインダーに似ており、集電体に強く付着します。プレス工程では、材料の多孔質構造に損傷を与えることはありませんでした(図2)。炭化後、Cu箔はポリマーとの強い結合を形成します。この方法はさまざまなエレクトロスピニング繊維に適していることは注目に値します。ここでは、純粋なポリマー(図2a)、高分子複合材料(図2b)、無機および高分子複合材料(図2b)の3つの代表的な材料を示します。 。2c)。
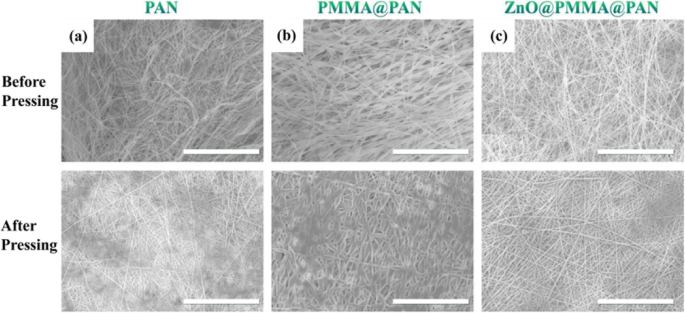
プレス前後のエレクトロスピニング膜の形態。 a PAN。 b PMMA @PAN。 c ZnO @ PMMA @PAN。スケールバー、100μm
炭素化膜の安定性研究の例としてPMMA @ PAN膜を選択します。これは、PAN膜の膜形成が比較的良好であるのに対し、PMMA @PANおよび酸化物@PMMA @PAN膜は安定性が低く類似した構造であるためです。図3aに見られるように、PMMA @ PAN膜は炭化後にもろくなり、亀裂がはっきりと観察されます。対照的に、PMMA @ PAN @ Cuは非常に滑らかで、亀裂はありません(図3b)。この方法により、実験室での大規模生産(約5cm×10cm)で高品質のバインダーフリー電極が可能になります。材料の構造安定性をさらに実証するために、PMMA @PANおよびPMMA @ PAN @ Cuをエタノール溶液に入れて30分間超音波処理し、膜の強度をテストします。これは、PMMA @ PANが処理の開始時に壊れ始め、約5分後に完全に破壊されてエタノールに分散するのに対し、PMMA @ PAN @ Cuは30分後も無傷のままであり、目に見える亀裂がないことを示しています(図3c 、b)。さらに、PMMA @ PAN粉末をボールミル粉砕し、バインダーとしてPVDFを使用してCu箔にコーティングし、図3eに示すように接着性をテストします。 PMMA @ PANは、粉砕プロセス中に簡単に凝集します。また、作製した電極の表面は非常に粗く、活物質を完全に剥がすことができます。ただし、同じテストプロセスの後、大量のPMMA @ PAN @ Cu材料がCu箔上にスムーズに残ります(図3e、f)。超音波処理と接着試験は、PMMA @ PAN @Cuの炭素材料がCu箔に強い接着性を持っていることを明確に示しています[11]。
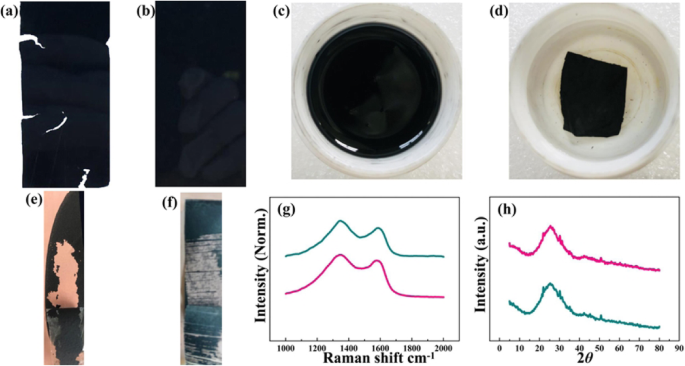
バインダーフリー電極の特性評価。 a の画像 PMMA @PANおよび b PMMA @ PAN @Cu。 c の安定性 PMMA @PANおよび d 30分間の超音波処理後のPMMA @ PAN @Cu。 e の剥離試験 PMMA @PANおよび f PMMA @ PAN @Cu。 g ラマンと h それぞれPMMA @ PANとPMMA @ PAN @CuのXRD曲線
PMMA @PANとPMMA @ PAN @ Cuの結晶構造は、ラマン分光法とXRDによって特徴付けられ、ポリマー繊維をCu箔に押し付けた後の違いを観察します(図3 g、h)。約1350cm -1 でのラマンスペクトルの最初のピーク 2番目は1590cm -1 欠陥誘起モードのDバンドとE 2g のGバンドに対応します。 それぞれグラファイトモード[12]。炭素材料の無秩序度を示すDバンドとGバンドの強度比。これは1.2の同じ値を示しており、ポリマー繊維をCu箔に押し付けた後の影響は無視できることを示しています。さらに、無秩序の特徴はPMMAによって引き起こされる可能性があり、これはPANの不均一な炭化と材料の脆性につながります。 PMMA @PANとPMMA @ PAN @ Cuは同様のXRDパターンを持ち、どちらも25.0 ° で2θ値の強い回折ピークを示します。 。この特徴的なピークは、グラファイト構造の層に対応しています[13]。つまり、エレクトロスピニングされた膜の炭化プロセスは、Cu箔と合成された後も変化していません。
電気化学的性能
CR2032コイン型ハーフセルを使用して、さまざまなバインダーフリー電極の電気化学的性能を調べます。 250〜2500 mA g -1 の範囲の電流密度でのレート性能 図4aに表示されます。 ZnO @ PMMA @ PAN @ Cu、ZnO @ PMMA @ PAN、PMMA @ PAN @ Cu、PMMA @ PAN、PAN @ Cu、およびPANの放電容量は、260、248、202、163、174、および162mAhのままにすることができます。 g -1 2500 mA g -1 の電流密度で 、 それぞれ。ただし、電流密度の増加に伴う静電容量の保持は、一般に、ポリマー繊維をCu箔に押し付けた後は低くなります。これは主に、プレスされた電極の多孔性が低く、一部の繊維が一緒に押しつぶされて、電解質から炭素材料へのLiイオンの移動が制限されるためです。 300サイクル後、放電容量は219、178、165、137、130、および124 mAh g -1 のままです。 それぞれ、ZnO @ PMMA @ PAN @ Cu、ZnO @ PMMA @ PAN、PMMA @ PAN @ Cu、PMMA @ PAN、PAN @ Cu、およびPANの場合。ポリマー繊維をCu箔に押し付けて炭化することによって調製された電極の容量保持は、50サイクル目からほぼ100%を維持しますが、Cu箔をサポートしていない膜は保持力が低く、約71%、89%、81%です。それぞれ、ZnO @ PMMA @ PAN、PMMA @ PAN、およびPAN。 ZnO @ PMMA @ PAN @CuおよびZnO @ PMMA @ PANのサイクル寿命は、2500 mA g -1 の電流密度で評価されます。 (図4b)。 ZnO @ PMMA @ PAN @CuおよびZnO @ PMMA @ PANは、180および96 mA h g -1 の可逆容量を示します。 2000サイクル後の容量保持率はそれぞれ82%と55%です。ポリマー繊維をCu箔に押し付けた後の優れたサイクリング性能を示しています。
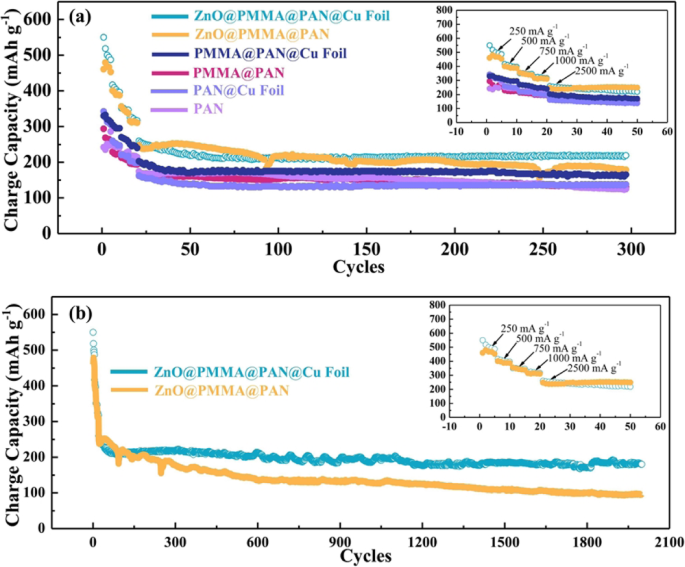
a 、 b さまざまなバインダーフリー電極のサイクリング性能、および対応するレート性能が挿入画像に示されています
結論
安定した電気化学的性能を備えたLIB用のバインダーフリー電極用にユニバーサルメソッドが開発されています。この方法は、バインダーフリー電極の作成に適しているだけでなく、集電体保護戦略になる可能性もあります。不活性材料の含有量を増やすことなく、集電体と電解質の接触を回避するために、活性炭材料の薄層を集電体の表面にコーティングすることができます。 Cu箔だけでなくAl箔も同様の機能を発揮できると考えられています。さらに、カーボンを集電体にコーティングすることにより、バインダーと集電体との間の接着を強化することができる。したがって、この戦略を利用して高エネルギー密度電極を開発する方が便利です。
データと資料の可用性
すべてのデータは制限なしで完全に利用可能です。
ナノマテリアル
- 将来のバッテリーのためのスズナノ結晶
- エネルギー貯蔵への応用のための酸化鉄ベースのナノ構造の進歩
- グリセロールの電気透析脱塩のための無機イオン交換体のナノ粒子を含む複合膜
- リチウムイオン電池用の高性能フレキシブルカソードとしてシード支援水熱プロセスを介して炭化繊維上に成長した3D相互接続V6O13ナノシート
- スーパーキャパシタ用の優れた電極材料としてのCoMoO4ミクロスフェアの水熱合成
- リチウムイオン電池の高性能アノードの前駆体としての酸素内方拡散によるスラッジSiのナノSi / SiOx構造への変換
- 高性能リチウムイオン電池用の共沈/焼成経路を介したMoS2 / Cナノコンポジットのフミン酸支援合成
- フィルム摩擦電気ナノ発電機に基づく周波数選択性のためのバイオニック蝸牛基底膜音響センサーの設計
- シンプルなプラスチックパッケージによるエレクトロスピニングカーボンナノファイバーに基づく新しい柔軟なフルセルリチウムイオン電池
- 安定したFOLEDのための二次移動グラフェン電極
- 完璧な電極浸透のレシピ