面内電流および加熱処理による濾過され剥離されたグラファイトシートの結晶性および電気的性質の改善
要約
ろ過され、剥離されたグラファイトフレークの熱と電流処理に基づいて高導電性グラファイトシートを製造するためのアプローチを報告します。この処理は、加熱(〜900°C)と面内電流の流れ(550 A・cm −2 )を組み合わせたものです。 )結晶欠陥の低減を通じて導電率を改善します。このプロセスは1分の処理時間しか必要としないことが示され、その結果、電気伝導率が2.1倍に増加しました(1088±72から2275±50 S・cm -1 )。ラマン分光法とX線回折による構造特性は、導電率の改善が結晶化度の30倍の改善(ラマンG / D比が2.8から85.3に増加)に起因し、他の観察可能な構造変化がないことを示しました。重要なことに、この処理は巨視的(10 mm)シート表面全体に均一に作用することがわかりました。これは、エネルギー生成および貯蔵用の電極や電磁シールドなどのアプリケーションの開発、および大型の開発の可能性を示しています。 -スケール処理技術。
はじめに
高度な炭素材料は、柔軟性、重量、および耐環境性により、シートに使用する多くの金属よりも優れています。カーボンナノチューブまたはグラファイトを使用したこれらのシート(フィルムとも呼ばれる)は、フレキシブルエレクトロニクス、センサー、および電磁シールドの多くのアプリケーションで有用であることが示されています[1,2,3,4,5,6,7,8,9、 10,11]。高い電気伝導率は、高周波、マイクロ波受動部品、膜などのアプリケーションでのパフォーマンスの向上を可能にするために調査されたもう1つの分野です[10、11、12]。いくつかのグループが以前に、100〜10,000 S・cm -1 の範囲の優れた導電率を備えたグラファイトベースのシートまたはフィルムの製造を報告しています。 グラファイトの剥離やポリマーの熱分解に至るまでの方法を使用します[12、13、14、15、16、17、18、19、20]。たとえば、大西ら。芳香族ポリマーを3000°Cで熱分解することにより、グラファイトフィルムを直接製造できることを実証しました。これは、10,000 S・cm -1 の電気伝導率を示しました。 [21]。さらに、Song etal。ポリマー前駆体の高温処理と11,000S・cm -1 の導電率を示す圧縮圧延を組み合わせることにより、フレキシブル無線周波数(RF)アンテナ用のグラファイトフィルムの製造を実証しました。 [12]。まったく対照的に、Behabtu等。は、剥離したグラファイト粉末から数層のグラフェンを吸引ろ過してグラファイトシートを製造したことを報告しました。これは、1100 S・cm -1 の電気伝導率を示しました。 [22]。さらに、Lotya etal。剥離したグラファイト薄膜(厚さ30 nm)の電気伝導率が0.35から15 S・cm -1 に改善したことが報告されています。 剥離したシートをアルゴン(Ar)/ N 2 で250°Cでアニーリングします。 2時間[23]。王ら。大面積で導電性があり柔軟な還元型酸化グラフェン(RGO)膜の導電率が、57.3から5510 S・cm -1 に向上することを実証しました。 [24]。これらの例は、溶液ベースの処理が芳香族ポリマーの高温熱分解よりも簡単な製造ルートを表している一方で、同じレベルの電気伝導率を達成できないことを示しています。興味深いことに、いくつか、特にSong etal。 [12]およびLotyaetal。 [23]、高導電性シートを生成するには、単一ステップのプロセスでは不十分です。これは、加熱、ひずみ、炭化などの複数のステップを使用して結晶欠陥の量を最小限に抑え、引張強度を約2から約10GPaに高める炭素繊維の製造に類似しています[25]。
これらのアプローチに動機付けられて、単純な剥離と熱電流処理によって高導電性グラファイトフィルムを製造するアプローチを報告します。真空ろ過で作られたグラファイトシートを使用して、処理には、面内電流の流れと組み合わせた中性ガス環境での同時加熱が含まれます。わずか1分の処理時間で、導電率が2275±50 S・cm -1 に2倍向上します。 達成することができます。処理されたグラフェンシートの構造分析は、結晶化度の30倍の改善を示し(ラマン分光法で測定)、これは観察された導電率の増加とよく相関していました。
メソッド/実験
グラファイトの剥離とシートの準備
グラファイトシートは、剥離したグラファイト粉末の分散液を濾過することによって調製した。市販の高純度黒鉛粉末(ACB-100)は、日本グラファイト工業株式会社から購入しました。これは、厚さ500〜1000nmの約80μmサイズの粒子で構成されていました。このグラファイト粉末2ミリグラムを、分散剤としてドデシルベンゼンスルホン酸50 mg(東京化成工業株式会社)と10 mlのハイドロフルオロエーテル(C 4 )に混合しました。 F 9 OC 2 H 5 、3.0 MのNovec7200、表面張力; 13.6mN・m -1 )。剥離は、ステンレス鋼のボールベアリングを使用して、10Hzで30分間のボールミル粉砕(Verder Scientific Co.、Ltd。)によって実行されました。ボールミル剥離後、原子間力顕微鏡(AFM)により、グラファイトフレークのサイズと厚さがそれぞれ約500nmと約45nmに減少しました(補足図1a)。したがって、平均して、分散したフレークには約130個のグラフェンが含まれていました。分散液を真空濾過して自立シートを形成した。濾過後、剥離したグラファイトシートは、厚さ計(Dektak XT、Bruker)によって特徴付けられるように、27〜48μm(平均35μm)の厚さを有していた。この剥離したグラファイトシートのSEM画像、ラマンスペクトル、およびXPSスペクトルを補足の図1b-dに示します。これらのシートを蒸留水ですすいで残留化学物質を除去した後、空気中100°Cで24時間乾燥させました[26]。最後に、シートに一軸圧力(〜0.5 MPa)をかけて、充填密度と導電率を高めました(図1b)。
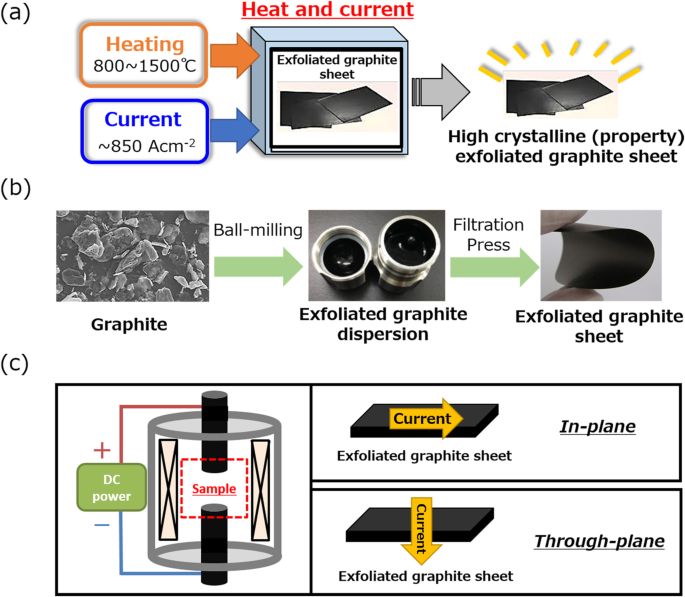
a ろ過され、剥離されたグラファイトシートの熱と電流の後処理を示す概念図。 b 購入したままのグラファイトフレークから剥離したグラファイト分散液およびシートへの剥離したグラファイトシートの調製プロセス。 c 治療装置の主要コンポーネント(チャンバー、ヒーター、電極)(左)と、面内または面内に電流を流すための2つの構成(右)
熱および電流技術の機器とプロセス
一般に、加熱と電流を同時に流すための処理装置は、(1)周囲を制御するための低真空から大気圧に適したチャンバー、(2)高周波誘導加熱システム(最大2000°)の3つの部分で構成されています。 C)、および(3)高電流(120Vで最大266A、または〜850 A・cm -2 )を印加するための等方性グラファイトで構成された対向する円形電極(直径10 mm) DC)。このシステムについては、以前のレポート[27、28]で詳しく説明されています。この一連の実験では、Arアンビエントを使用しました。
この電流検査にとって重要なのは、面内電流と面貫通電流の両方に対応するための、対向する同一平面上の電極接触面の設計でした(図1c)。面貫通電流構成では、図1cに示すように、シートを2つの対向する電極表面の間に挟みました。面内電流構成では、補足図2に示すように、電気絶縁性ジルコニアプレートを挿入できるように、長方形のくぼみを備えたカスタム形状の電極を用意しました。このように、シートは2つのカスタム接点の間に挟まれますが、電流はサンプルの平面を通過します。処理の安定性と再現性を確認するために、各実験を5回実行し、平均値と標準偏差を報告します。成長を開始するためにソース前駆体が導入されていないため、この処理はその場でのCVDプロセスではないことに注意してください。このプロセスは、熱と電流の組み合わせによってのみエネルギーを供給し、グラフェンシートの欠陥の治癒を誘導します。
処理の時間依存効果の結果から、30秒間はわずかな改善しか見られず、1.5分間以上はグラフェン構造の損傷が観察されたため、標準の処理時間は1分に選択されました。損傷は、補足図3aに示すように、G / D比の低下によって証明されました。 1分間の処理時間を使用して、800〜1000 ° の範囲の電気伝導率に対する温度依存性を調査することにより、標準処理温度を決定しました。 C(補足図3b)。
特性
剥離したグラファイトフィルムの表面抵抗は、4プローブ電気測定テスター(Loresta GP MCP-T610、Mitsubishi Chemical Analytech Co.、Ltd。)を使用して実行されました。
構造特性は、X線回折(XRD)CuKα(λ=0.15418 nm、MiniFlex II、Rigaku Corporation)を使用して調べました。層間距離は、ブラッグの回折定式化を使用して推定されました(1);
$$ \ lambda =2 \ kern0.5em d \ cdot \ sin \ kern0.5em \ uptheta $$(1)ここで d は層間距離です(グラファイトの理論上の層間距離は0.335 nmです)。
ラマン分光計(XploRA、HORIBA、Ltd。)を用いて、励起波長532 nm(サンプリング領域)で、熱処理前後の剥離黒鉛膜のラマン黒鉛対無秩序強度比(G / D比)を調べた。 100μm)。得られたラマンスペクトルのベースライン補正後、各ピーク強度は1300〜1400 cm -1 (Dバンド)および1580〜1620 cm -1 (Gバンド)を測定しました。さらに、2Dピークの位置と強度がGバンドに対して観察されました。シートの全体的かつ正確なサンプリングを提供するために、グラファイトフィルム全体に分布する10の位置でラマン測定を実行し、ラマンG / D比の各バンド強度を計算して平均しました。詳細な測定条件は次のとおりです。分光器:焦点距離200 mm、分解能(スリット幅100μm)のCzerny Turnerタイプの検出器:2–15 cm -1 、およびレーザー出力20–25mW。
結果と考察
真空ろ過されたグラファイトシートの電気伝導率を特徴づけることから、2段階のプロセスを開始します。 「方法/実験」のセクションで説明したように、厚さ約35μm(平均)のシートの電気伝導率は、4プローブの電気抵抗率測定デバイスを使用して実行されました。平均電気伝導率は1088±72S・cm -1 であることがわかりました。 これは、他のろ過されたグラファイトおよびグラフェンシートとよく比較されます。
次に、これらのシートに熱電流処理を施して、導電率を高めました。我々の結果は、グラファイトシートの特性を向上させる上で、加熱と面内電流を同時に流す必要性と利点を示しています。単層カーボンナノチューブ(SWCNT)について以前に報告されたように、電流の流れと加熱を組み合わせた処理を適用しました[27、28]。 900°Cの加熱温度を使用して、適用された面内電流密度の関数として処理されたシートの電気伝導率の依存性を調査しました。各ポイントで、温度を900°Cに上げ、面内電流(0〜850 A・cm -2 )1分間通過しました。各シートの電気伝導率を測定してプロットしました(図2b)。シートの電気伝導率対印加電流密度のプロットは、準備された値(1088±72 S・cm -1 )から急激な増加を示しました。 )2250±50 S・cm -1 まで 550 A・cm −2 、その後、電流密度が高くなると減少しました(850 A・cm -2 )(図2b)。ラマンG / D比の減少に基づく(550 A・cm -2 で85.3±5.7 850 A・cm −2 で10.7±1.0まで )、約550 A・cm -2 を超える電流密度で観察された電気伝導率の低下が疑われます。 エレクトロマイグレーションなどのメカニズムによる構造劣化の結果です。これらの結果に基づいて、Arガス環境の最適な処理条件は550 A・cm -2 であると決定されました。 900°Cで。これらの結果は、熱と電流の流れを同時に使用することの有効性と利点を示しています。
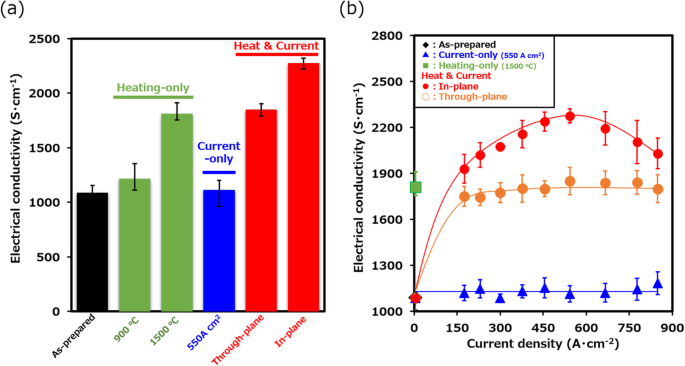
a 処理されたままの場合および異なる処理条件に従った場合のグラファイトシートの電気伝導率。 b さまざまな処理条件(電流のみ、熱と面内電流、および熱と面内電流)での印加電流密度への電気伝導率依存性の依存性。加熱のみと準備されたままの状態が参照として含まれています。
加熱と面内電流の組み合わせ処理の重要性を検証するために、(1)加熱のみの処理、(2)電流のみの処理、および(3)加熱とスルーの組み合わせを使用していくつかの制御実験を実施しました。 -平面電流の流れ。要するに、他のプロセス条件は、上記のような同等レベルの電気伝導率の改善を示しませんでした。まず、加熱のみの処理を、900℃と1500℃でAr雰囲気下で5時間実施しました。 CNTで観察された結果と同様に、加熱のみでは、1500°C以上の温度で観察可能な改善が見られました[29]。図2a(緑)に要約されているように、900°Cでの処理により、電気伝導率がわずかに向上しました(1215±70 S・cm -1 )、1500°Cでの処理により、約1812±79 S・cm -1 まで大幅に増加しました。 。さらに、どちらの場合も、わずかな重量(〜3%)の減少が観察されました。これは、剥離プロセスで残った残留化学物質の除去、おそらくデガッシングが原因である可能性があります。これらの結果は、加熱だけでもグラファイトシートの電気伝導率を改善するのに効果的である可能性があることを示していますが、1500°Cを超える温度と数時間の処理時間が必要です。
次に、電流のみの治療の効果を調べました。このテストでは、175〜850 A・cm -2 の範囲のいくつかのサンプルについて、面内に電流を流しました。 1分間の治療時間。処理後、シートは電気伝導率の顕著な改善を示さなかった(図2aの青いバー、図2bの三角形)。この結果は、この電流のみの治療の効果がないことを示しています。電流によって引き起こされるオーム加熱は、シートの結晶化度と電気伝導率に大きな変化を引き起こすには不十分であると思われます。
第三に、熱と電流を組み合わせたプロセスにおける電流の流れの方向(面内と面内)の重要性を示すために、電流は、絶縁アルミナプレートのない電極を使用して、一連のグラファイトシート上で面を通過しました。 「方法/実験」のセクションで説明されているように。グラファイトシートは、175〜850 A・cm -2 の範囲の電流密度にさらされました。 、および電気伝導率を測定し、印加電流の関数としてプロットしました(図2b)。このプロットから、いくつかの観察を行います。 1つは、電気伝導率への影響は、比較的低い印加電流ですぐに発生することです。印加電流密度が最も低い(150 A・cm −2 )、グラファイトシートの電気伝導率は約70%増加しました。第二に、印加電流をさらに増やしても、それ以上の改善は見られませんでした。第三に、電気伝導率のレベルが増加します(〜1812±79 S・cm -1 )は、加熱のみの検査の結果と同等でしたが、対照的に、1分の治療時間しか必要としませんでした。
まとめると、これらの結果は、加熱と電流処理を組み合わせた相乗効果を示しています。面貫通電流と組み合わせた900°Cの加熱で1分間の処理を適用すると、加熱のみの処理(1500°C、5 h)と同様の電気伝導率のレベルが向上しました。しかしながら、印加電流の増加による追加の改善は観察されなかった。これは、加熱および面貫通電流の条件下で、提供されるエネルギーがグラファイト構造にさらなる変化を誘発するには不十分であることを示唆している。面を通過する電流の流れがオーム加熱を引き起こし、これが熱のみの処理と同等のこの配置を本質的に減少させると考えられます。さらに、電気伝導率の印加電流への依存性が弱いことは、改善を推進するメカニズムが熱プロセスだけではないことを示しています(図2b)。温度が上昇しても処理時間が短すぎる可能性があります。この仮説は、印加電流に対する観察された弱い依存性を説明するでしょう。したがって、これらの結果は、加熱と面内電流の流れを組み合わせて、ろ過されたグラファイトシートの電気伝導率を改善するための効果的かつ効率的な処理プロセスを実現することの重要性を示しています。
私たちの処理は、10mm×10mmのシートにろ過されたグラファイトフレークの巨視的なアセンブリに作用するため、改善の均一性は非常に重要です。 DC / AC電流およびプラズマ処理を使用した以前の報告では、表面全体を均一に処理することが困難であることが示されています[30]。治療のばらつきが大きいことは、将来のスケールアップ開発やアプリケーション開発の障害となります。この点に対処するために、導電率の均一性は、処理されたグラファイトシート(φ10mm)の中心から0、±1.0、±3.0、および±5.0mmで評価されました。図3cに見られるように、平均電気伝導率は〜2275±50 S・cm -1 でした。 分散はわずか1.5%(x、〜0.7%; y、〜1.5%)です。この結果は、熱と電流の処理がグラファイトシート全体に非常に均一に作用したことを示しており、将来のスケールアップの可能性を示唆しています。
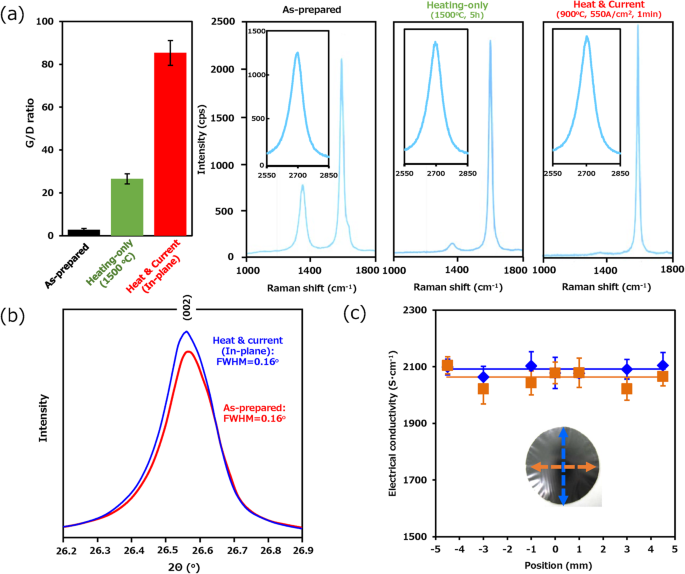
a 熱および電流プロセスの前後および加熱のみのプロセス後の、濾過され、剥離されたグラファイトシートのラマンスペクトル。 b XRDのFWHM(002)は、準備および処理されたままの剥離グラファイトシートの反射です。 c 処理された剥離グラファイトシート表面全体の電気伝導率の均一性
改善された電気伝導率の起源を明らかにすることを試みるために、処理の前後のシートの構造的特徴づけが行われた。結晶化度の特性評価は、「方法/実験」のセクションで説明したように、グラファイトシート表面全体でサンプリングされたマクロラマン分光法を使用して実行されました。まとめると、処理前後のグラファイトフィルムのスペクトルは、鋭いグラファイトバンド、無秩序バンド、および2Dバンドというグラファイトの特徴を示しました。熱処理および電流処理されたシートのラマンG / D比は、調製されたままのシートのラマンG / D比から約85.3±5.74に30倍以上増加しました(G / D比〜2.8±0.55)。ジンらによる以前の報告。 SWCNTの欠陥は、ナノチューブに沿った電流の通過を通じて移動することが報告されています[31]。このように、我々は、処理がグラファイトドメインのエッジに向かって欠陥の移動を誘発すると仮定します。これは、面内電流の必要性を説明している可能性があります。比較のために、1500°Cの温度でのみ加熱処理されたシートは、G / D比の9.5倍の増加(約26.5±2.38)を示しました(図3a)。電流のみの処理で処理されたシートのG / D比は、175〜850 A・cm -2 の範囲で2.7±1.96であることがわかりました。 、これは、図2bの電気伝導率と同様に、印加電流密度(これらのスペクトルは表示されていません)からの増強がないことを示しています。この結果は、結晶化度の改善が電気伝導率の改善とよく相関していることを示しています。 2Dピークは、すべてのサンプルで約2700 cm -1 で観察されました。 熱および電流プロセスの前後。ピーク位置の類似性は、層数が熱および電流プロセスによって明らかに変化しなかったことを示しています[32]。
X線回折(XRD)による構造特性評価は、未処理および熱処理および電流処理されたシート(CuKα:λ)で実行されました。 =0.15418 nm、MiniFlex II、リガク株式会社)。 2θ=26.5°での(002)反射の観察では、処理の結果として反射位置とプロファイル形状に明らかな変化は見られませんでした(図3b)。これは、処理済みシートと未処理シートの層間距離(約0.335 nmと推定)が処理の影響を受けなかったことを意味します。さらに、層の間隔に関連する(002)反射の半値全幅(FWHM)も、約0.16°で影響を受けませんでした。これらの結果は、電気伝導率の観察された改善が、個々のフレークの層間間隔の改善から生じたものではないことを示唆している。まとめると、ラマンとXRDの結果は、結晶化度の改善、および粒子間接合や隣接ドメインの結合などの関連する構造的特徴が、観察された電気伝導率の増加の主な原因であるように見えることを示唆しています。この現象を顕微鏡で観察する試みは失敗しました。
このプロセスの制限とスケールアップの可能性についてコメントしたいと思います。この処理は、グラファイトシートの効果的かつ効率的な特性改善の可能性を示していますが、時間効率を維持するには、高出力の電源と比較的高い処理温度(〜900°C)の必要性を認識しています。単層カーボンナノチューブの処理に関する以前の研究に基づいて、処理温度は、関連する処理電流の増加とともに低下する可能性があります[29]。したがって、温度を約800°Cに下げるための1つの可能なアプローチは、印加電流を約20%増やすことです。さらに、以前の研究では、このプロセスは、複数のシートを同時に処理して同様の結果を取得することにより、基本的にスケーラブルであることが示されています。このプロセスが電気伝導率を効率的に改善できることを考えると(1088±72から2275±50 S・cm -1 )わずか1分で剥離したグラファイトの場合、この技術は、グラファイトシートの連続的かつ大規模な処理を可能にするロールツーロールプロセスに適しているはずです。したがって、この作業は、導電性、電磁シールド、およびフォトニックデバイスを備えたナノコンポジットの電極材料用の巨視的で高導電性のグラファイトフィルムの改善に大きな影響を与える可能性があります。
結論
結論として、剥離したグラファイトシートからなる高導電性グラファイトシートを製造するアプローチと、加熱と面内電流を組み合わせた処理からなる処理を示しました。この処理は、剥離したグラファイトシートの電気伝導率を1088±72から2275±50 S・cm -1 に2.1倍改善するのに重要であることがわかりました。 。私たちの電気伝導率のレベルは、Songらによって報告されたレベルの約20%のままであることに注意してください。 (11,000 S・cm -1 、5–8 h)[14]、しかし対照的に、このアプローチは1分の治療時間しか必要としません。さらに、私たちのアプローチでは、10 mmシート全体を1.5%の分散内で均一に処理しました。これは、この材料の適用とスケールアップの可能性の両方に大きな影響を及ぼします。
データと資料の可用性
すべてのデータは制限なしで完全に利用可能です。
略語
- CVD:
-
化学蒸着
- N 2 :
-
窒素
- Ar:
-
アルゴン
- XRD:
-
X線回折
- DC:
-
直流
- AC:
-
交流
- FWHM:
-
半値全幅
- AFM:
-
原子間力顕微鏡
ナノマテリアル