レオナルドとCETMA:低コストと環境への影響のためにコンポジットを破壊する
このブログは、Leonardo Aerostructures Division(Grottaglie、Pomigliano、Foggia、Nola生産施設、南イタリア)の材料エンジニア、研究開発責任者、IPマネージャーであるStefano Corvagliaと、研究エンジニア兼責任者であるDr.SilvioPappadàへのインタビューに基づいています。 CETMA(イタリア、ブリンディジ)でのレオナルドとのプログラムの一覧。
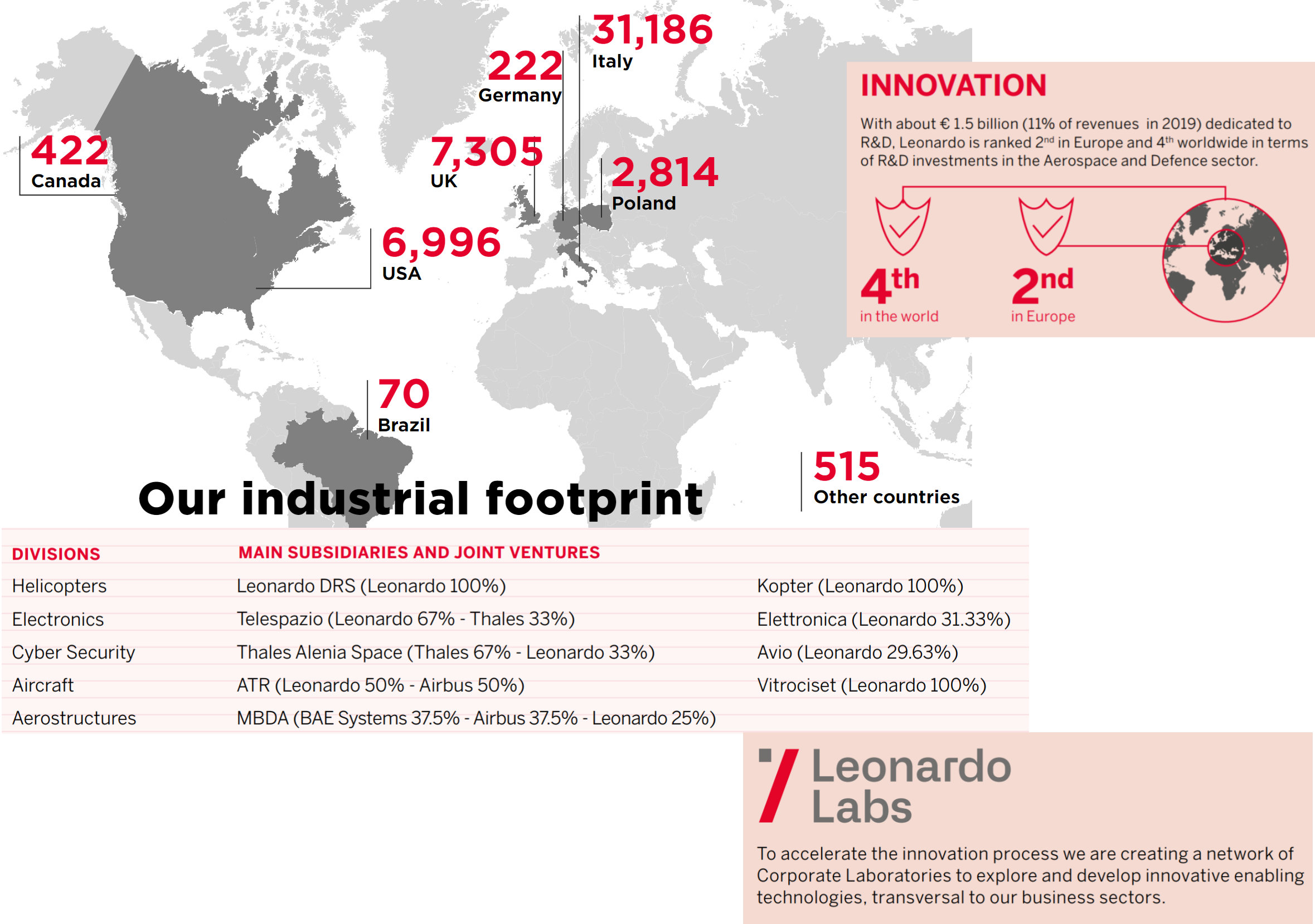
レオナルド(イタリア、ローマ)は、航空宇宙、防衛、セキュリティにおける世界の主要プレーヤーの1つであり、収益は138億ユーロ、従業員数は世界中で40,000人を超えています。同社は、空、陸、海、宇宙、サイバー、セキュリティ、および無人システム向けに、世界規模で包括的なソリューションを提供しています。レオナルドは、研究開発に約15億ユーロ(2019年の収益の11%)を費やしており、航空宇宙および防衛セクターへの研究投資の点で、ヨーロッパで2位、世界で4位にランクされています。
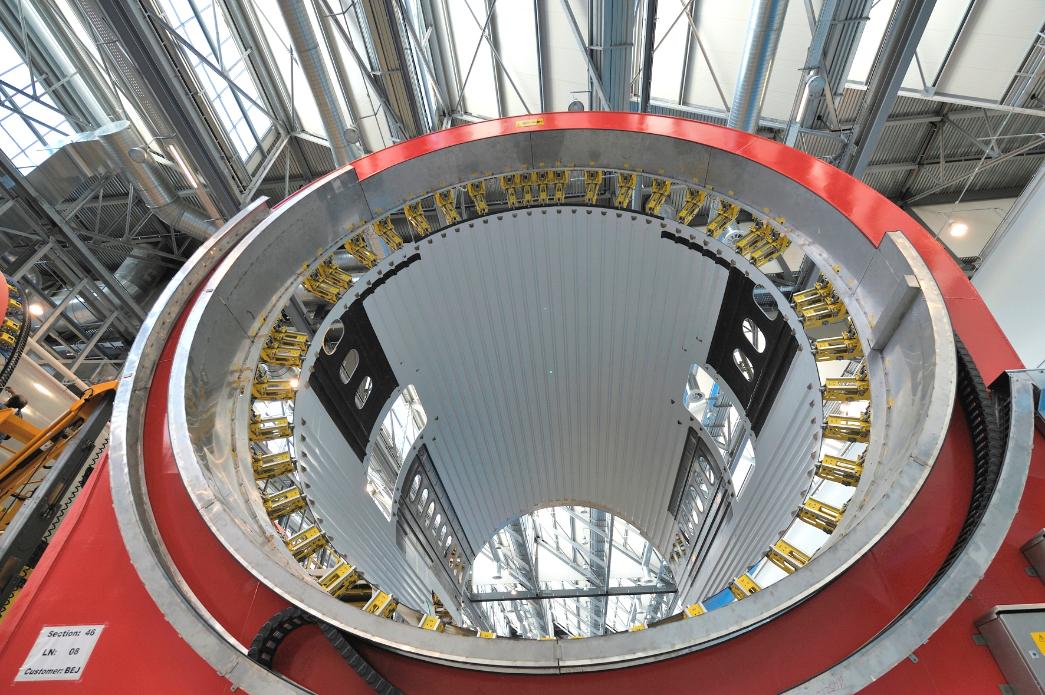
レオナルドは、航空構造部門を通じて、胴体や尾翼などの大型構造コンポーネントの製造と組み立てを、世界の主要な民間航空機プログラム用の複合材料や従来の材料で提供しています。
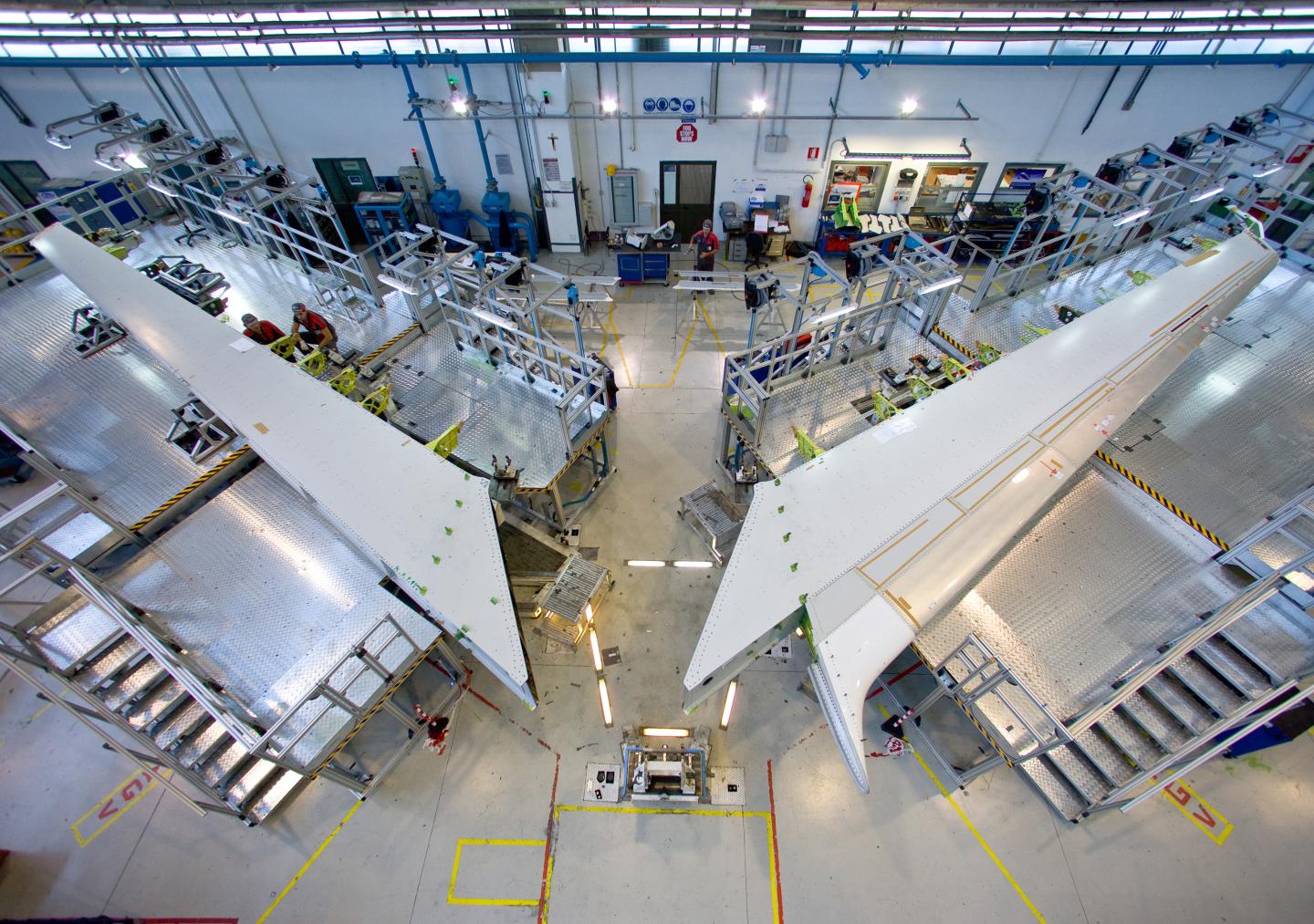
複合材料では、レオナルド航空構造部門は、グロッターリエ工場でボーイング787中央胴体セクション44および46用の「ワンピースバレル」を製造し、フォッジャ工場で水平尾翼を製造しています。これは、787機体の約14%です。その他の複合構造物の生産には、フォッジャ工場でのATRおよびエアバスA220民間航空機用の尾翼の製造と組み立てが含まれます。 Foggiaは、ボーイング767や、ジョイントストライクファイターF-35、ユーロファイタータイフーン戦闘機、C-27J軍用輸送機、レオナルドが製造したFalcoファミリーの無人航空機の最新メンバーであるFalcoXplorerなどの軍事プログラム用の複合部品も製造しています。
CETMAの操作
「CETMAでは、熱可塑性複合材料や樹脂トランスファー成形(RTM)など、多くの継続的な活動を行っています」とCorvaglia氏は言います。 「私たちの目標は、研究開発活動を可能な限り短い期間で生産できるようにすることです。私たちの部門(R&DおよびIP管理)では、TRLが低い破壊的技術も検討しています[技術準備レベル-つまり、TRLが低いほど、生産からの初期段階にあります]が、競争力を高め、世界中のお客様を支援することを目指しています。 。」
「私たちは一緒に仕事を始めてから、コストと環境への影響を低く抑えることを常に目指してきました」とパパダは付け加えます。熱可塑性複合材料(TPC)は、熱硬化性樹脂と比較して両方の樹脂を削減できることがわかりました。」
Corvaglia氏は、「Silvioのチームと協力して、これらの技術を開発し、生産でこれらを評価するためにいくつかの自動セルプロトタイプを構築しました。」と述べています。
連続圧縮成形(CCM)
「CCMは私たちの共同作業の良い例です」とPappadàは言います。 「レオナルドは、熱硬化性複合材料で作られたいくつかのコンポーネントを特定し、スプライス構造や単純な形状の支柱など、航空機内に多数の部品がある場所を調べて、TPCでこれらを提供する技術を一緒に調査しました。」
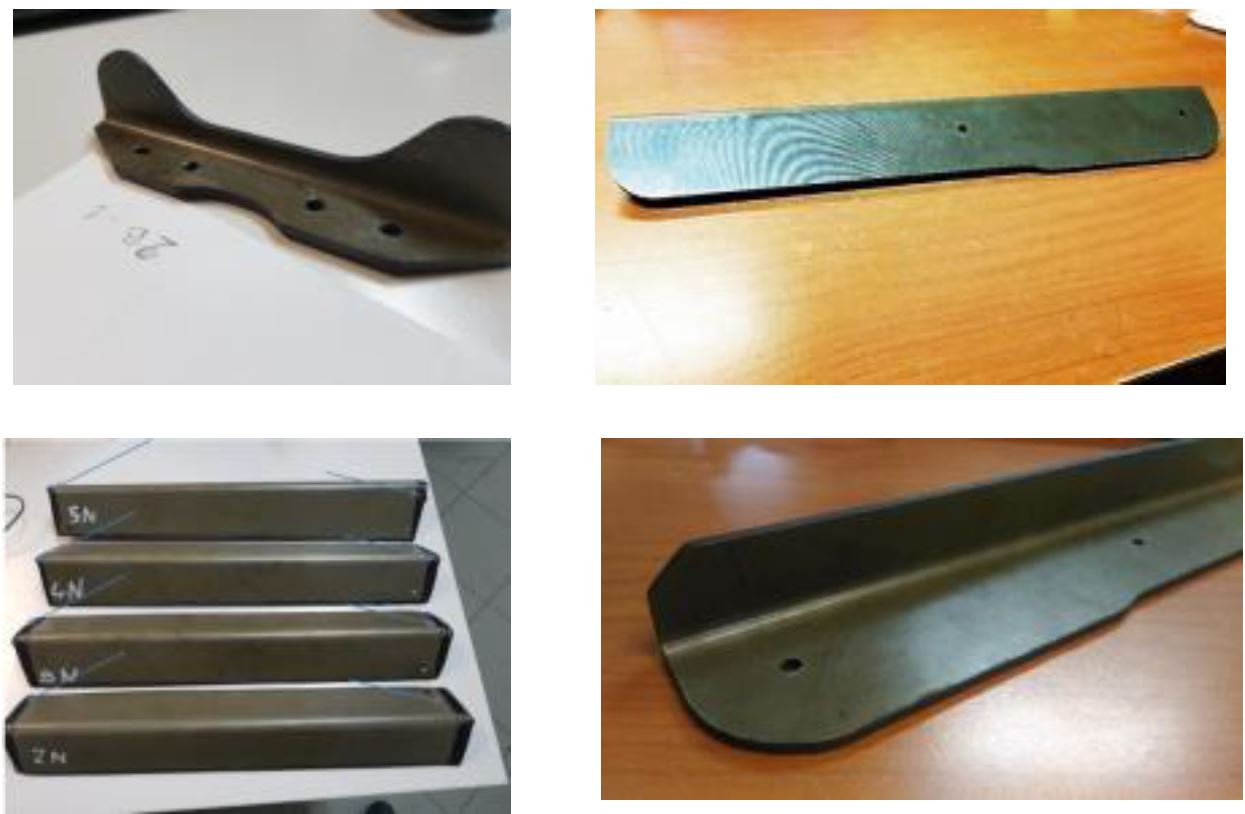
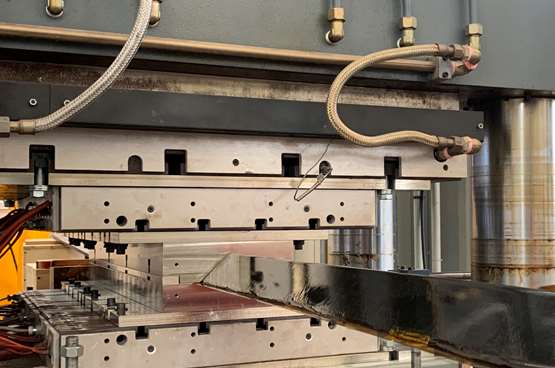
「低コストと高レートを特徴とする新しい生産技術が必要でした」と彼は続けます。彼は、過去には、単一のTPCコンポーネントが大量の廃棄物で製造されていたと指摘しています。 「そのため、非等温圧縮成形に基づいてネット形状を作成しますが、スクラップを減らすためのいくつかの革新(特許取得中)があります。このために完全に自動化されたセルを設計し、イタリアの会社がそれを構築してくれました。」
このセルは、レオナルドが設計したコンポーネントを生産することができます、とパパダは言います。「5分ごとに1つのコンポーネントの速度で、24時間/日動作します。」しかし、彼のチームはその後、プリフォームの製造を理解する必要がありました。 「当初、フラットラミネーションプロセスが必要でした。これがその時点でのボトルネックでした」と彼は説明します。 「したがって、私たちのプロセスはブランク(フラットラミネート)から始まり、これを赤外線(IR)オーブンで加熱してから、成形用のプレスに入れます。フラットラミネートは通常、大きなプレスを使用して製造され、4〜5時間のサイクルタイムを必要とします。フラットラミネートをより早く製造できる新しい方法を検討することにしました。そこで、レオナルドのエンジニアのサポートを得て、CETMAで生産性の高いCCMラインを開発しました。 1メートル×1メートルの部品のサイクルタイムを15分に短縮しました。重要なのは、これは継続的なプロセスであるため、無制限の長さを作成できることです。」
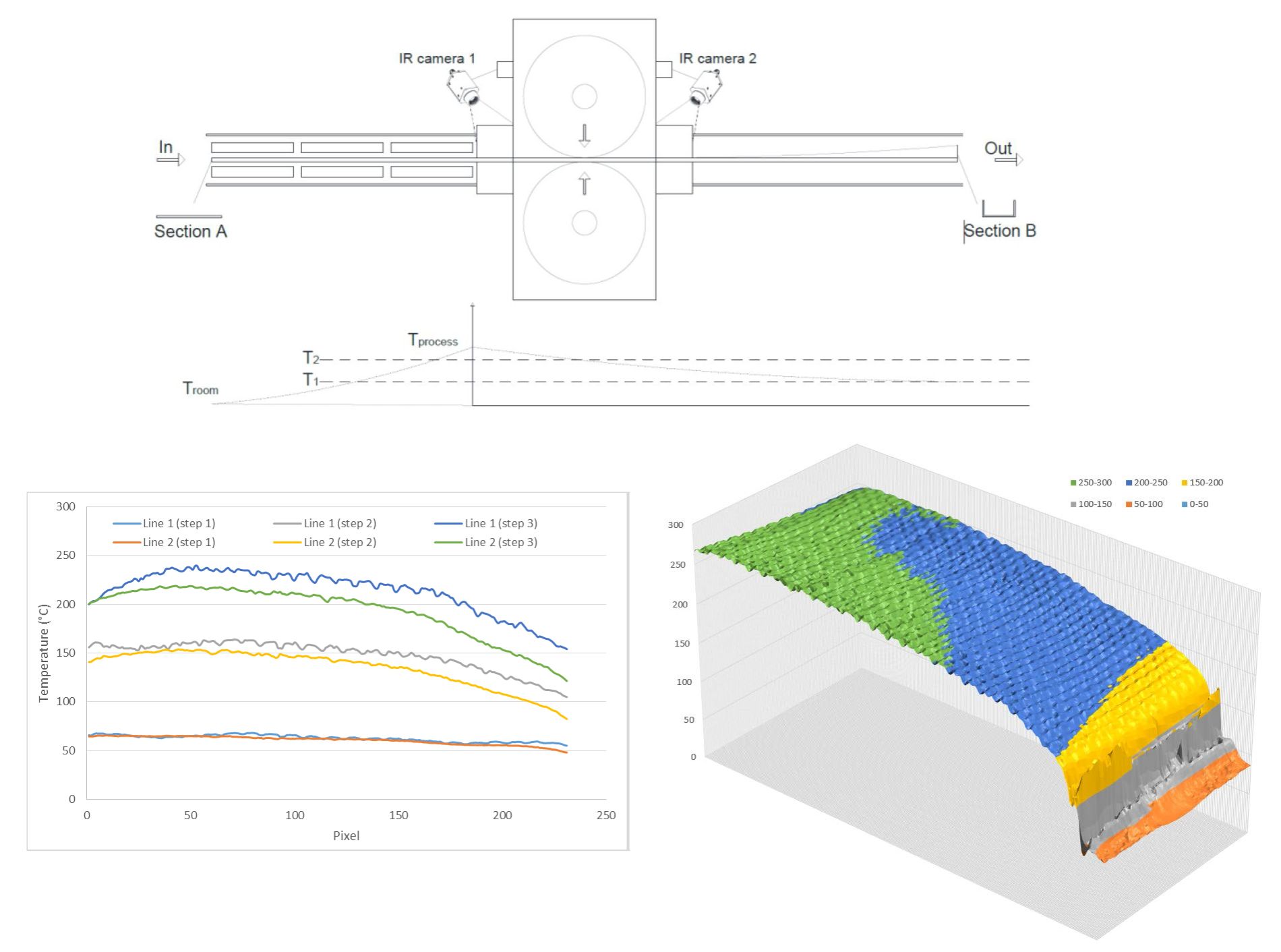
しかし、これは、Xperion、現在はXELIS(Markdorf、ドイツ)によって10年以上使用されているCCMと比較してどのように新しいのでしょうか。 「ボイドなどの欠陥を予測できる解析モデルと数値モデルを開発しました」とPappadà氏は言います。 「これは、レオナルドとサレント大学(イタリア、レッチェ)と協力して、パラメーターとその品質への影響を理解するために行いました。これらのモデルを使用して、非常に厚いだけでなく高品質も実現できるこの新しいCCMを開発しました。これらのモデルのおかげで、温度と圧力だけでなく、これらの適用方法も最適化できます。温度と圧力を均一に分布させるために開発できる技術的側面はたくさんあります。ただし、これらが複合構造の機械的性能と欠陥の成長に与える影響を理解する必要がありました。」
Pappadàは続けます。「私たちのテクノロジーはより柔軟です。また、CCMは20年前に開発されたものですが、使用した企業が知識やノウハウを共有していないため、情報がありません。そのため、複合材料と処理に関する知識だけで、何もないところから始めなければなりませんでした。」
「現在、社内プログラムとお客様と協力して、これらの新しいテクノロジーの部品を探しています」とCorvaglia氏は言います。 「これらの部品は、生産を開始するために再設計および再認定される可能性があります。」どうして? 「目標は、飛行機を可能な限り軽量にすると同時に、価格競争力を高めることです。したがって、厚さで最適化する必要もあります。しかし、部品がさらに軽量化されたり、類似した形状の複数の部品を識別したりできることがわかる場合があります。これにより、大幅なコスト削減が可能になります。」
今まで、彼は繰り返します、この技術は少数の人の手にありました。 「しかし、より高度なプレス成形を追加することで、これらのプロセスをさらに自動化するための代替技術を開発しました。平らなラミネートを入れて、部品が出てきて、すぐに使用できます。現在、部品の再設計とフラットCCMとシェイプCCMの開発の段階にあります。」
「現在、CETMAには非常に柔軟なCCMラインがあります」と、Pappadà氏は言います。「複雑な形状を実現するために、必要に応じてさまざまな圧力を加えることができます。レオナルドと一緒に開発するラインは、特定のニーズに合うコンポーネントにさらに焦点を当てます。フラットパネルとLストリンガーでは、より複雑な形状とは異なるCCMラインを使用できると考えています。このようにして、複雑な形状のTPC部品を製造するために現在使用されている大型プレスと比較して、機器のコストを低く抑えることができます。」
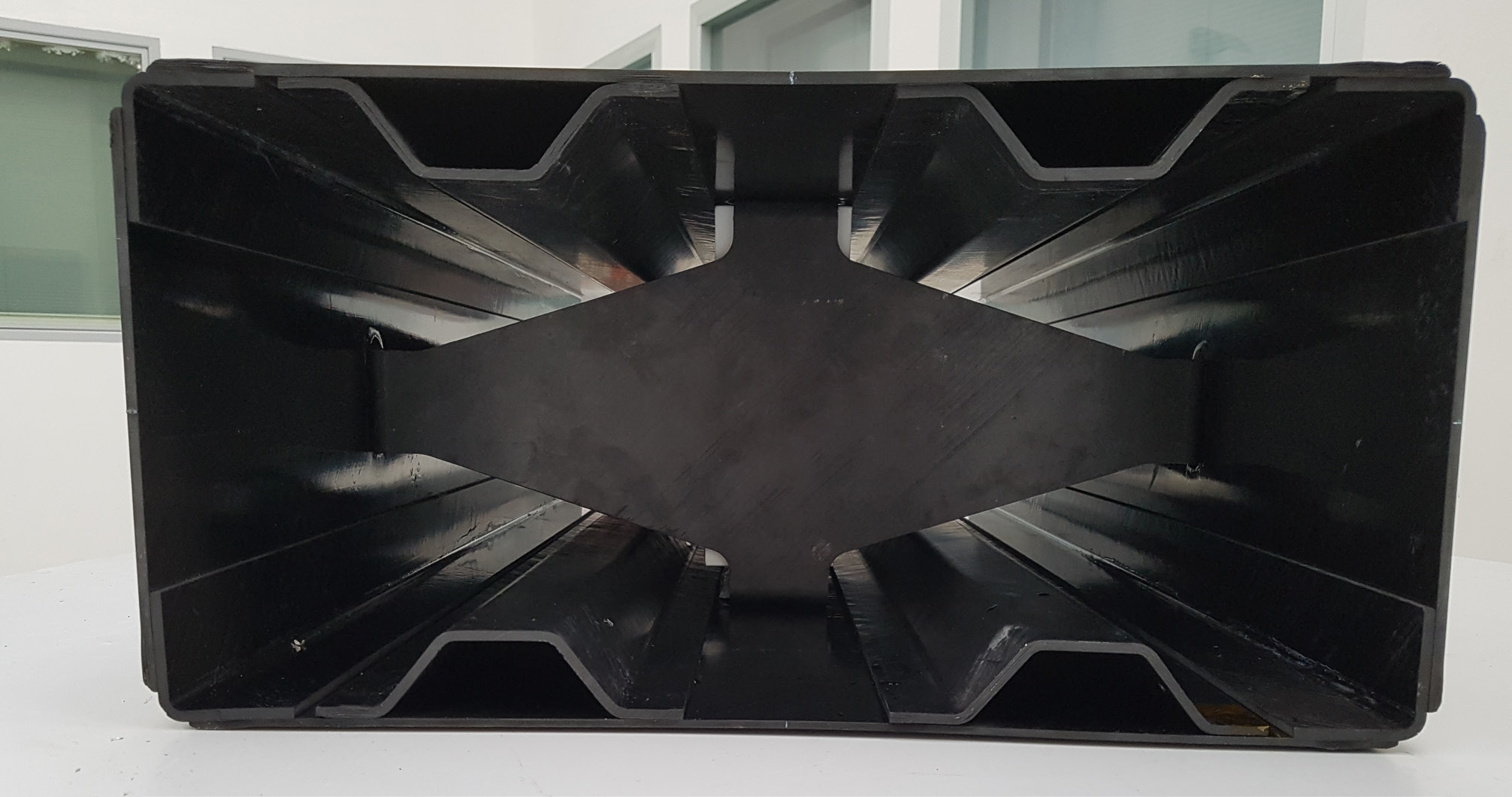
現場圧密のための誘導溶接
「誘導溶接は、温度を非常にうまく調整および制御し、非常に迅速に加熱し、非常に正確に制御することができるため、複合材料にとって非常に興味深いものです」とPappadà氏は述べています。 「レオナルドと共同で、TPCコンポーネントを接合するための誘導溶接を開発しました。しかし現在、TPCテープの現場圧密(ISC)に誘導溶接を使用することを考えています。そのために、専用機を使用した誘導溶接で非常に素早く加熱できる新しい炭素繊維テープを開発しました。このテープは、市販のテープと同じマトリックス材料を使用していますが、電磁加熱を改善するアーキテクチャが異なります。機械的性能を最適化するだけでなく、プロセスについても考え、さまざまなニーズに対応しようとしています。たとえば、自動化で費用対効果の高い方法で処理する方法などです。」
彼は、ISCをTPCテープで良好な生産率で達成するのは非常に難しいと指摘しています。 「これを工業生産に使用するには、加熱と冷却を速くし、非常に制御された方法で圧力をかける必要があります。そこで、誘導溶接を使用して、材料を固めている小さな領域のみを加熱し、残りのラミネートは冷たくすることにしました。」組み立てに使用される誘導溶接は、TRLが高いとPappadàは言います。 「
その場での統合に誘導加熱を使用することは非常に破壊的であるように思われます—他のOEMやティアサプライヤーが現時点で公然と行っていることはありません。 「はい、これは破壊的技術である可能性があります」とCorvaglia氏は言います。 「私たちは機械と材料の特許を取得しました。熱硬化性複合材料に匹敵するものを目指しています。多くの人がTPCでAFP(自動ファイバー配置)を試しましたが、統合のために2番目のステップを実行する必要があります。これは、形状、コスト、サイクルタイム、および部品のサイズの点で大きな制限です。確かに、航空部品の製造方法を変更する可能性があります。」
SQRTM
熱可塑性プラスチックに加えて、レオナルドは引き続きRTMテクノロジーを検討しています。 「これは、CETMAと協力して、古いテクノロジー(この場合はSQRTM)に基づいた新しい開発の特許を取得したもう1つの分野です。同じ認定樹脂トランスファー成形(SQRTM)は、当初、Radius Engineering(米国ユタ州ソルトレイクシティ)によって開発されました。 「すでに認定されている材料を使用できる脱オートクレーブ(OOA)法を採用することは重要です」と、Corvaglia氏は述べています。 「また、よく知られた特性と品質を持つプリプレグを使用することもできます。このテクノロジーを使用して、航空機の窓枠を設計、実証、特許取得しました。」
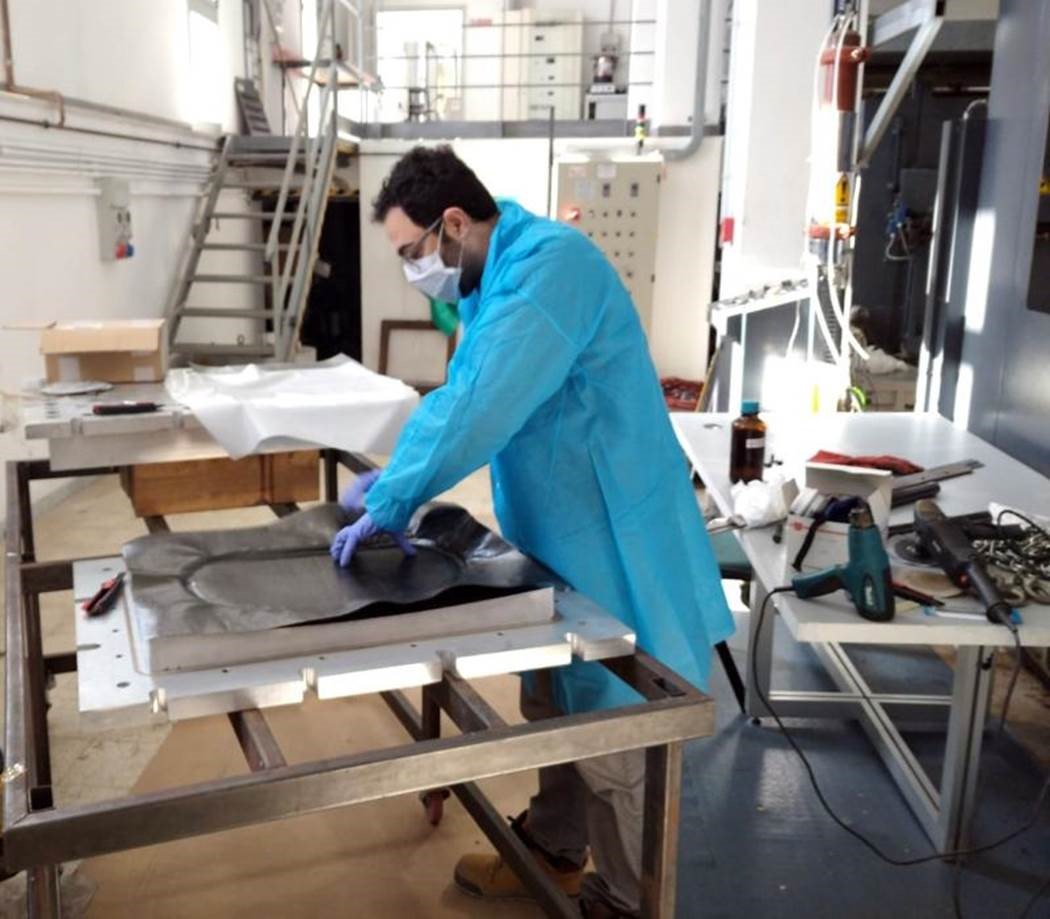
「これも古い技術ですが、Webにアクセスすると、この技術に関する情報を見つけることができません」とPappadà氏は述べています。 「重要なのは、ここでも、分析モデルを使用してプロセスパラメータを予測および最適化することです。この技術により、乾燥領域や樹脂のプールがなく、樹脂の分布が良好になり、ボイド含有量がほぼゼロになります。繊維含有量を制御できるため、高い構造性能を生み出すことができ、この技術を利用して複雑な形状を作り出すことができます。オートクレーブ硬化に適した同じ材料を使用していますが、代わりにOOA法を使用していますが、サイクル時間を数分に短縮するために速硬化樹脂を使用することもできます。」
「現在のプリプレグでも、硬化時間を短縮しました」とCorvaglia氏は述べています。 「たとえば、8〜10時間の通常のオートクレーブサイクルと比較して、窓枠のような部品ではSQRTMを使用して3〜4時間を達成できます。熱と圧力が部品に直接加えられ、加熱するための質量が少なくなります。また、オートクレーブ内の空気に対して液体樹脂を加熱する方が速く、部品の品質が優れているため、特に複雑な形状の場合に有利です。真空バッグではなくツールがそれを制御しているため、手直しがなく、ボイドがほぼゼロで、優れた表面品質が得られます。」
先見の明のあるテクノロジーベースの未来
レオナルドは、多種多様なテクノロジーのセットでイノベーションを生み出しています。技術の急速な進化により、リスクの高い研究開発(低TRL)への投資は、現在の製品ですでに維持されている段階的(短期)開発を超えて、将来の製品に必要な新しい技術を開発するために不可欠であると考えています。このような短期戦略と長期戦略の組み合わせは、持続可能で競争力のある企業のための統一されたビジョンであるレオナルドの2030 R&Dマスタープランで組み合わされています。
この計画の一環として、高度な研究と技術革新を専門とする企業の研究開発研究所の国際ネットワークであるLeonardoLabsを立ち上げています。 2020年に向けて、同社はミラノ、トリノ、ジェノア、ローマ、ナポリ、タラントの各地域に最初の6つのレオナルド研究所の開設を目指し、次の分野のスキルを持つ68人の研究者(レオナルドリサーチフェロー)を募集しています。自律型インテリジェントシステム、ビッグデータ分析で15、高性能コンピューティングで6、航空プラットフォームの電化で4、材料と構造で5、量子技術で2。 Leonardo Labsは、Leonardoの将来のテクノロジーの革新的な前哨基地およびジェネレーターの役割を果たします。
特に、レオナルドが航空機で商品化する技術は、その陸と海の部門にも応用できる可能性があります。レオナルドとその複合材料への潜在的な影響に関する最新情報にご期待ください。
樹脂
- 履物用の超軽量TPEコンポジット
- 持続可能性とコストを改善するためのフォームPP
- スーパーキャパシター用途向けのグラフェンおよびポリマー複合材料:レビュー
- 複合材料プロセスの最適化と制御のための超音波センサーのカスタマイズ
- OTOMcompositeは、レーザー支援テープの配置と巻き取りを使用して、Composites4.0を作成するためのソフトウェアを開発しています
- 複合材料用の再処理可能、修理可能、リサイクル可能なエポキシ樹脂
- 複合材料の硬化監視のためのACおよびDC誘電測定の組み合わせ
- 双胴船のレース用に選択されたソルベイコンポジット
- 熱可塑性複合材料コンソーシアムは、自動車および航空宇宙向けの大量生産を目指しています
- 半導体および電子機器製造の環境への影響
- 健康と環境の監視のためのウェアラブルガスセンサー