アプリケーションスポットライト:3Dプリントロケットと宇宙船製造の未来
3D印刷は、宇宙船製造、特にロケットのエキサイティングな技術に急速になりつつあります。新興企業と定評のあるメーカーの両方が3D印刷を採用して、設計と性能を強化し、低コストで、所要時間を短縮したロケットコンポーネントを作成しています。
今週は、ロケット部品、さらにはロケット全体の3D印刷の利点を見て、ApplicationSpotlightシリーズを続けます。
このシリーズで取り上げている他のアプリケーションを見てみましょう:
熱交換器用の3D印刷
ベアリングの3Dプリント
自転車製造用の3Dプリント
デジタル歯科およびクリアアライナー製造のための3D印刷
医療用インプラントの3Dプリント
靴製造のための3Dプリント
電子部品の3Dプリント
鉄道業界における3Dプリント
3Dプリントアイウェア
最終部品生産のための3D印刷
ブラケットの3Dプリント
タービン部品の3Dプリント
3Dプリントで高性能の油圧コンポーネントを実現する方法
3Dプリントが原子力産業のイノベーションをどのようにサポートするか
ロケット部品の製造に3D印刷が使用されているのはなぜですか?
衛星を宇宙に運ぶ競争はますます激しくなっています。
このため、宇宙船メーカーは、コストを削減し、効率を高めると同時に、ロケットの開発と生産を加速するという課題に直面しています。
ただし、従来のロケット製造では、複数のプロトタイピングサイクルと製造ステップにより、プロセスが長くなり、非常にコストがかかります。
たとえば、従来の燃焼室(燃料と圧縮空気の混合物が点火される構造ロケット部品)の製造には10〜14か月かかる場合があります。
これらの燃焼室を製造するには、メーカーは別々の部品を鋳造して鍛造する必要があります。次に、冷却チャネルを周囲で機械加工する必要があります。 チャンバー—非常に時間と労力とコストのかかるプロセス。
これらの課題を考慮して、主要なロケットメーカーはすでに積層造形による燃焼室の製造を開始しています。設計が完了すると、3D印刷された燃焼室を数週間以内に製造できるため、製造業者は製造時間とコストを大幅に削減できます。
宇宙で打ち上げられるハードウェアの製造には、並外れた性能と精度が必要です。起動を成功させるには、すべてのパーツがシームレスに連携する必要があります。
従来の製造では、エンジニアは非常に複雑なロケット部品を設計する際に制限に直面します。金属3D印刷により、エンジニアは従来のプロセスの制限のいくつかを克服し、より複雑なロケットコンポーネントをより迅速に開発できます。
ロケット部品の製造に使用されている3D印刷技術
今日の時点で、宇宙船会社は概して、選択的レーザー溶融(SLM)などのレーザーベースの金属3D印刷技術を採用して、燃焼室、インジェクター、ノズル、ポンプ、バルブなどのロケットエンジン部品を製造しています。 SLMは、強力で微調整されたレーザーを金属粉末の層に適用し、金属粒子を融合させます。このプロセスは、部品が作成されるまで数百層にわたって繰り返されます。
SLMは、高精度(20ミクロンの薄さの層を印刷可能)を提供し、さまざまな高性能金属で機能するように最適化されています。 、チタンからニッケル合金まで。この技術は通常、小さな部品に使用されます。
SLMに加えて、一部の宇宙船会社はDirect Energy Deposition(DED)テクノロジーを使用して大きなコンポーネントを作成しています。 DED 3Dプリンターは、金属材料がノズルからビルドプラットフォームに堆積するときに、レーザーまたは電子ビームで金属材料を溶かすことによって機能します。
通常、DEDマシンは材料の堆積速度が高く、粉末またはワイヤーの形の金属材料を処理できるため、ニアネット形状の高密度部品を作成できます。
ロケットの3Dプリントのメリット
反復する機能 迅速に
ロケット部品の3D印刷の最大の利点の1つは、設計を非常に迅速に繰り返すことができることです。
「アディティブを使用すると、従来の方法で最初のデザインを取得する前に、デザインを5回繰り返すことができ、5つすべてを合わせるとおそらく1つ未満のコストになります。従来の反復 」と、EOS NorthAmericaの航空宇宙事業開発マネージャーであるScottKillianは、engineering.comとのインタビューで述べています。
3Dプリンターは、工具を必要とせずに、設計ファイルから直接ロケット部品を作成できます。部品に変更が必要な場合、エンジニアは元のCADファイルに変更を加えるだけで、従来のプロセスよりもはるかに迅速に新しい変更された設計を作成できます。
設計の柔軟性
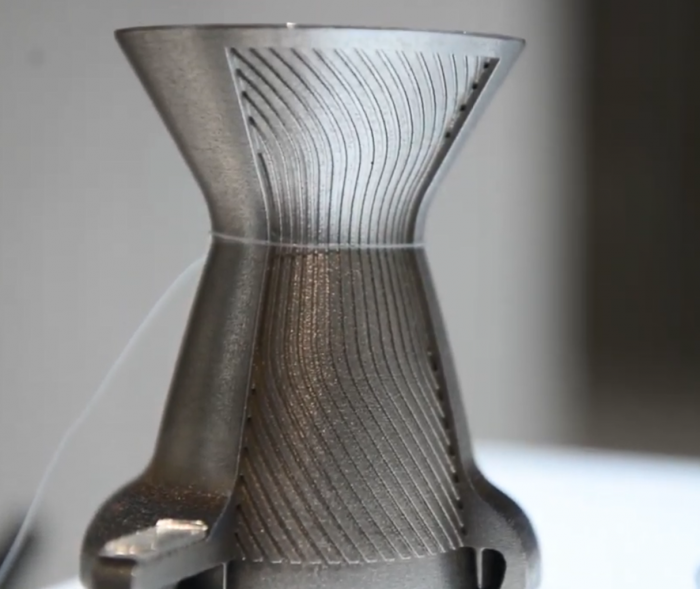
3D印刷は、工具に依存することなく、宇宙船のエンジニアに、従来のプロセスでは達成できない複雑な形状や形状を作成する柔軟性を提供します。
燃焼室を検討してください。すべてのロケットエンジンの重要なコンポーネントである燃焼室は、推進剤が混合して内部で発火するため、高圧環境と最大5,000°F(2760°C)の温度に耐える必要があります。
効率的に実行するには、このコンポーネントには、絶対零度より100°F(38°C)未満に冷却されたガスで満たされた複雑な内部冷却チャネルが必要です。
従来、これらの冷却チャネルは非常に複雑で、開発にコストがかかります。それらは、CNC機械冷却チャネルとチャンバーの外壁をろう付けするための特別な工具を必要とします。次に、これらの個別のセグメントを1つの部品に溶接する必要があります。
一方、3D印刷は、チャンバー全体を直接製造できるようにすることで、プロセスを合理化します。さらに、上の画像に示すように、機械加工が不可能な複雑な冷却チャネル設計が可能になります。
安価なロケット部品
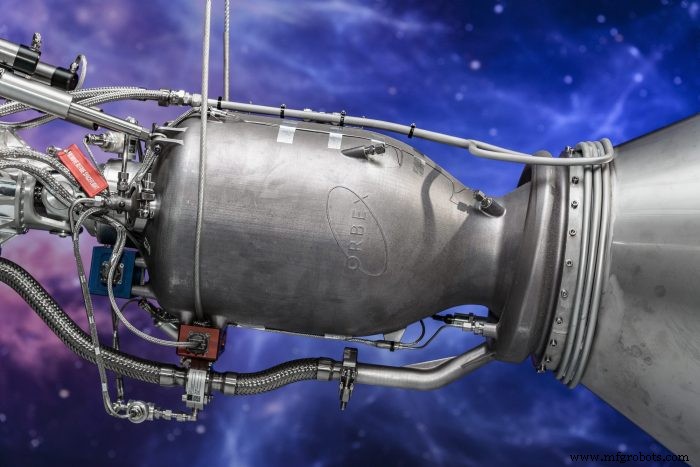
エンジンは、打ち上げロケット(衛星やその他の宇宙船を宇宙に打ち上げるために使用されるロケット推進機)の中で最も高価な部分です。エンジンのコストは、ロケット全体のコストの40%にもなる可能性があります。 3D印刷を使用して重要なエンジン部品を作成することにより、ロケットメーカーは宇宙船の全体的なコストを劇的に削減できます。
3D印刷により、エンジニアはロケットエンジンコンポーネントの生産を合理化でき、多くの生産ステップをバイパスできます。ステップが少なければ少ないほど、必要な設備と微調整が少なくなり、最終的には製造コストが削減されます。
さらに、3D印刷で製造プロセスを自動化すると、ほとんどの人件費が方程式から排除されます。 。
たとえば、英国の航空宇宙会社Orbexは、SLMテクノロジーとニッケル合金を使用してPrimeランチャーのエンジンを3Dプリントしました。金属3D印刷により、Orbexは、CNC機械加工などの従来の製造プロセスと比較して、所要時間を90%短縮し、コストを50%削減できました。
Elon Muskの個人所有の商業宇宙ベンチャーであるSpaceXは、また、3D印刷を採用して、コストを削減し、DracoおよびSuperDracoスラスターの製造プロセスの柔軟性を高めました。同社はSLMベースの金属3Dプリンターを使用して、インコネル燃焼チャンバーを作成しています。
Muskによると、「 3D印刷により、堅牢で高性能なエンジン部品をわずかな割合で作成できます。従来の製造方法のコストと時間 。」
簡略化されたアセンブリ
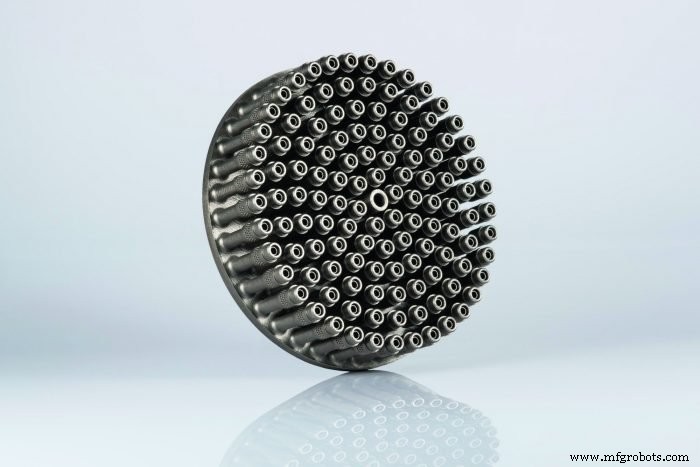
さらに、エンジニアは組み立てプロセスのステップ数を大幅に減らすこともできます。これは、複数のコンポーネントから1つのピースとして作成されたロケットパーツを3Dプリントすることで実現できます。
例としてインジェクターヘッドを取り上げます。インジェクターヘッドは、燃料混合物を燃焼室に押し込む推進モジュールのコア要素の1つです。
従来、インジェクターヘッドは数十、さらには数百の部品でできており、機械加工して溶接する必要があります。対照的に、3D印刷では、このようなコンポーネントを1つのピースとして作成できます。
ドイツ航空宇宙センター(DLR)の研究者は、3D印刷を使用して、小型衛星ランチャー用のインジェクターヘッドの新しい設計を作成しました。
その結果、10%軽量化されたモノリシックパーツになります。コンポーネントの数を30から1つに減らすことで、研究チームは固定サイトでの既知の障害点も排除しました。最後に、新しい最適化された設計は、部品のパフォーマンスを向上させ、部品の寿命を延ばすと言われています。
同様に、金属3D印刷のスペシャリストであるEOSは、Ariane6ランチャーのインジェクターヘッドの組み立てを簡素化しました。 、AirbusGroupとSafranの合弁会社であるArianeGroupによって開発されました。
SLMテクノロジーを使用することで、チームは、従来の設計に必要な248個のコンポーネントではなく、1つのコンポーネントとしてインジェクターヘッドを再設計することができました。その他の利点としては、50%のコスト削減と、3分の1のリードタイムがあります。
3Dプリントされたロケット部品の例
RocketLabの3Dプリントされたラザフォードエンジン
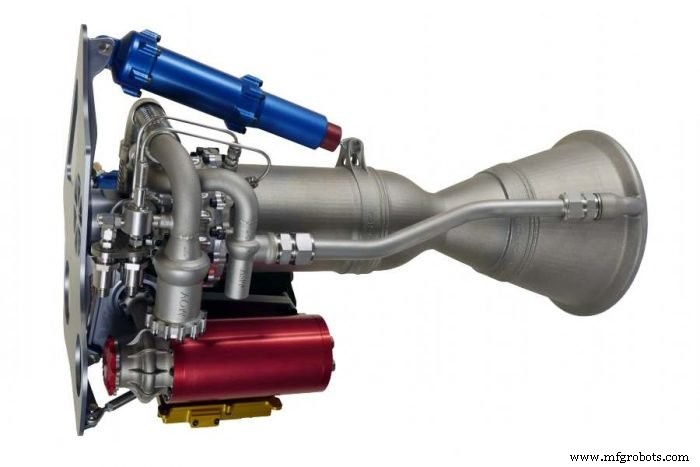
7月、カリフォルニアに本拠を置く航空宇宙会社であるRocket Labは、100番目の3Dプリントされたラザフォードロケットエンジンを完成させました。同社は2013年以来、すべての主要なエンジンコンポーネント(燃焼室、インジェクター、ポンプ、主要な推進剤バルブを含む)に3D印刷を使用しています。
9つのラザフォード液体推進剤エンジンがロケットラボのエレクトロンロケットに動力を供給します。これは複合材料でできており、最大225kgのペイロードを運ぶことができます。エンジン部品は、電子ビーム溶解(EBM)技術を使用して3D印刷されます。これは、従来のプロセスよりも安価にエンジン部品を製造すると言われています。
最近、Rocket Labは、3D印刷されたエンジンの信頼性を再び証明し、Electronランチャーを使用して軌道上に4つの衛星を打ち上げることに成功しました。
2020年までに、同社は月に2回の打ち上げを実施する予定です。 3D印刷により、Rocket Labは数か月ではなく数日でエンジンを製造できるため、チームはこの計画を実行に移すことができます。
ロケット全体を3Dプリントする
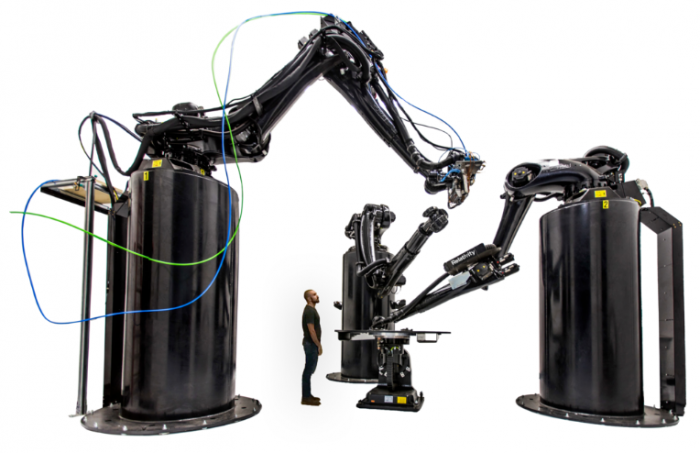
カリフォルニアを拠点とするスタートアップ、Relativity Spaceは、3Dプリントされたロケットエンジンを超えたいと考えています。同社はTerranロケットを開発しており、その約95%のコンポーネントが3Dプリントされます。
これを実現するために、同社は世界最大のDEDメタル3Dプリンターの1つであるStargateを開発しました。 Stargateは、直径2.7 m(9フィート)、高さ約4.5 m(15フィート)のコンポーネントを作成できるため、すべての燃料タンクとその他の大型ロケットコンポーネントを印刷します。
3D印刷を使用してロケット全体を実質的に製造することにより、Relativity Spaceはロケットの重量を大幅に削減し、ペイロードを増やしながら打ち上げのコストを削減できる可能性があります。
3D印刷はまた、組み立てる必要のある部品の数を減らし、それによってロケットの強度と安定性を高めます。
小さな部品の場合、同社はSLM技術を使用しています。
Relativity Spaceによると、3D印刷を使用すると、ロケットの開発に通常必要とされるよりも少ない工具と労力で、設計をすばやく変更できます。最終的に、これによりRelativitySpaceは2か月以内に原材料から飛行可能なロケットに移行できる可能性があります。
Relativity Spaceは現在、ロケット全体に3D印刷技術を適用している唯一の企業です。 3Dプリントされたロケットのコンセプトは成功するでしょうか?答えは、最終的にはテストと起動にあります。 3Dプリントされたテランロケットのテスト打ち上げは2020年後半に予定されています。
航空宇宙における3Dプリントの未来
3D印刷は、ロケットやロケットエンジン部品の設計と製造の方法に革命をもたらしました。ロケット設計の基本は変わっていないかもしれませんが、金属3D印刷はロケットの性能を向上させる新しい方法を解き放ち、設計の自由度を高めています。
この技術は、最も高価なロケット部品の1つであるエンジンの製造コストを削減するのに役立ちます。これは、製造ステップの数を減らし、より頻繁な設計の反復を可能にすることによって達成されます。
エンジン部品以外の3D印刷の機能はまだテストされていませんが、完全に3D印刷されるテクノロジーの可能性将来のロケットは本当にエキサイティングです。
3D印刷は、宇宙船製造の主要な製造技術になり、エンジニアがより迅速に革新し、次世代の宇宙旅行を実現できるようになりました。
次の記事では、靴業界の3Dプリントについて見ていきます。しばらくお待ちください!
3Dプリント