成形プロセスの種類–完全な概要[写真付き]
この記事では、成形プロセス、乾式砂型鋳造、グリーンサンド成形、ベンチ成形などのさまざまな用語に基づいて分類された成形プロセスのタイプについて説明します。
成形プロセス 一般的に使用される場合、さまざまな形式に従って分類できます。それらは大まかに次のように分類されます:
- 手成形 、および
- 機械成形 。
ピースと、小ロット生産の鋳物工場の練習用砂型は手作業で作られています。成形機は大量生産や大量生産に採用されています。
成形プロセスの種類
成形プロセスは、多くの場合、次のように分類されます:
(A)型が作られている材料の種類または
(1)緑砂型、
(2)乾いた砂型、
(3)皮膚乾燥型、
(4)ローム型。
(B)型の作成に使用される方法。
(1)ベンチ成形、
(2)床成形、
(3)ピット成形、
(4)スイープ成形、および
(5)プレート成形。
使用した砂に基づく成形プロセス
1。緑の砂型鋳造
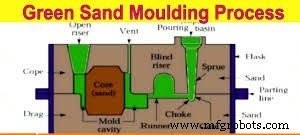
緑の砂型鋳造 は、高品質の鉄および非鉄鋳物用の金型を作成するための、用途が広く、迅速で、低コストの方法です。緑砂は、珪砂、水、ベントナイト、および鉄用途の炭塵などの他の添加剤で構成されています。
生砂型は、天然の鋳物砂またはケイ砂、結合粘土、および水の混合物を使用して作成されます。これらの材料は、行われている作業のクラスに望ましい特性を与える比率で完全に混合されます。
2。乾いた砂型
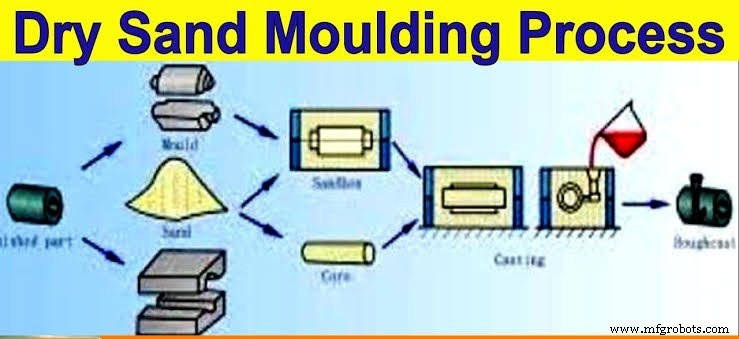
乾いた砂型の製造に関連する成形プロセス 異なる砂の混合物が使用され、鋳造のために再組み立てされる前に型のすべての部分がオーブンで乾燥されることを除いて、生砂成形で使用されるものと同様です。
緑砂型は、その形状を維持するために、水分と砂中の天然粘土バインダーに依存しています。しかし、乾いた砂型に使用される砂は、小麦粉、樹脂、糖蜜、または粘土などの追加の結合材料に依存します。材料は完全に混合され、薄い粘土水で焼き戻されます。 バインダーの量 鋳造のサイズによって決定されます 作られています。
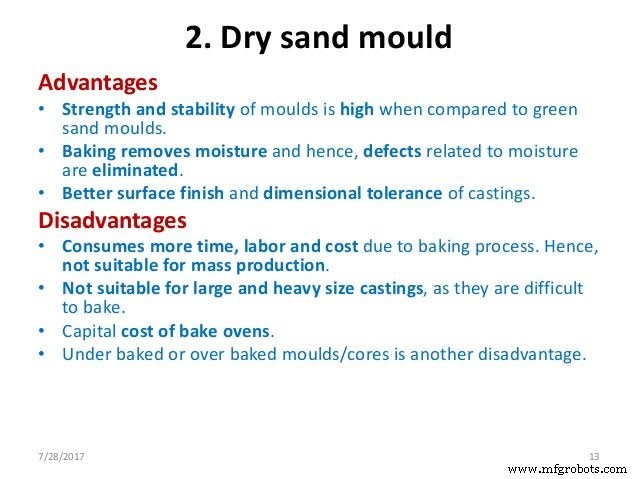
3。スキンドライ成形
スキンドライ成形プロセスは、ガストーチまたはヒーターを使用して、突っ込んだ砂の表層から約25mm以上の深さまで水分を乾燥させるプロセスです。ある程度、生砂型鋳造と乾式砂型鋳造の両方の利点があります。乾燥砂に比べて乾燥にかかる時間が短いため、安価です。皮膚乾燥は、特に非常に大きな型、または正確な詳細を必要とする作業に適しています。
4。ローム型
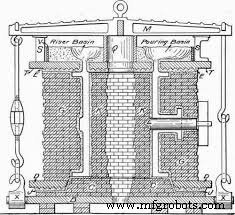
ローム 粘土と砂を水と混合して薄いプラスチック混合物を形成し、そこから型を作ります。ローム砂には、耐火粘土やガニスターも含まれています。ロームは、垂直面に付着できるように十分に接着性がなければなりません。ローム型は、適切な換気を確保するために常に特別な準備が必要です。目的は、人工的な手段によって、そうでなければコンパクトで緊密に編まれた塊の細孔を開くことです。したがって、刻んだわらなどのさまざまな種類の有機物、特に馬の糞 、砂と混ざっています。典型的なローム砂の混合物を以下に示します。
これは、通常レンガで作られた型の大まかな構造に石膏として適用され、正確な形状は、図に示すように中央紡錘体の周りを回転するスイープによって与えられます。鋳鉄板と棒は、成形材料を保持するレンガを補強するために使用されます。ローム型は、木で作られた骨格パターンを使用して作成することもできます。ロームの表面は黒くなり、組み立てる前に乾燥させます。
ローム型は主に、フルパターンや通常のフラスコ装置を使用するには費用がかかりすぎる大型の鋳物の製造に使用されます。大きなシリンダー、丸底のやかん、化学鍋、大きな歯車、その他の機械部品などの物体は、ローム型で製造されます。
使用する方法に基づく成形プロセスの種類
1。ベンチと床のモールディング
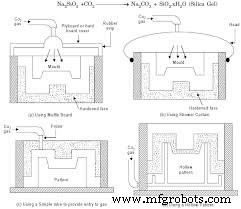
ベンチモールディング 主に、成形業者にとって便利な高さの作業台で作成できるほど小さい金型に適用されます。
非常に重い鋳物またはかなりの深さまたは面積の鋳物は、生砂または乾砂成形とほぼ同じ方法で鋳造床の砂に成形することができます。このような場合、床自体が引きずりとして機能し、これをコープで覆うか、型をキャストして開くことができます。
2。ピットモールディング
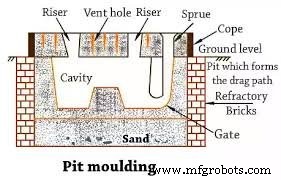
ピットモールディング プロセス :大規模な仕事の型は、通常、ピット掘りで準備されます パターンを持ち上げて型を簡単に鋳造するのを容易にする鋳造所の床で。引きずりとして機能するピットは転がすことができないため、パターンの下の砂がベッドインによって押し込まれる可能性があります。砂がその下に押し込まれているため、パターンは正しい位置に吊り下げられている可能性があります。他の場合では、パターンの底面が平らである場合、パターンはそれのために突っ込んだ平らなレベルの表面に置くことができます。
コークスのベッドがピットの底に置かれ、わらで覆われ、次に砂の層が押し込まれ、平らにされます。コークス床は、ピットの隅にある垂直ベントパイプによって大気と接続され、生成されたガスの出口を提供します。床が少し湿っている場合、ピットの内面はタール紙、レンガ、または木の板で裏打ちされています。通常、成形プロセスを完了するには1つのボックスが必要です。ランナー、流域、フィーダーがカットされています。
3。スイープモールディング
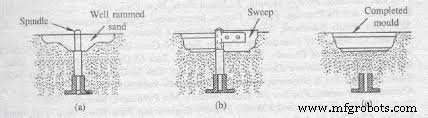
スイープモールディング 回転面形状の成形品に採用されています。準備プロセスでは、ベース1とスピンドル2が鋳造フロアに適切に配置されます。掘削が必要な鋳物とほぼ同じ形状とサイズになるまで、砂を埋めて押し込みます。これを図aに示します。
次に、スイープホルダー5がスピンドルランドに配置され、スイープ6はボルトおよびナットによって取り付けられる。金型の表面は、図(b)に示すように、スピンドルを中心に回転するスイープのプロファイルによって生成されます。スイープ後、スピンドルが取り外され、金型が中央にパッチされます。その後、ゲートが切断され、型を注ぐ準備が整います。これを図(c)に示します。
4。プレート成形
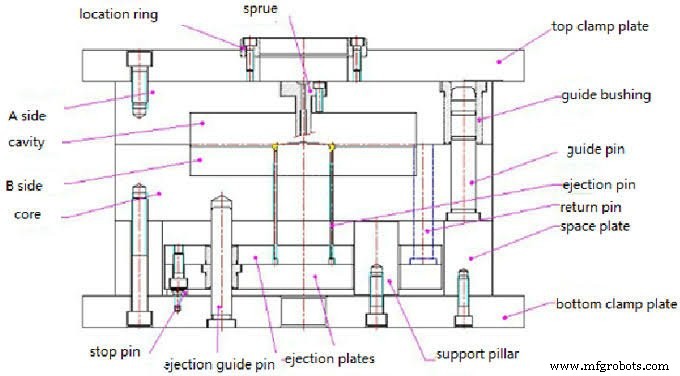
プレート成形 プロセス :この取り付けられたパーティングプロセスでは、パターンはパーティング全体で半分に分割され、図と同じ形状の平行な側面を持つプレートに半分に分割されます。プレートを使用すると、次の利点が得られます :
- パターンは簡単に処理できます そして急速に。
- フラスコが突っ込んだときにプレートが独自のジョイントを提供するため、金型の2つの部分の間のジョイントを作成する作業が軽減されます。
- パターンはすばやく描画できます 、プレートがボックスの側面に重なるため、プレートを所定の位置に保持するピンが描画操作中のガイドとして機能します。
いくつかの特別な成形プロセス
近年、特殊成形工程 時間と費用を節約し、より高品質の金型とコアを製造し、少ない労力とスキルで生産性を向上させるために開発されました。一般に、これらのプロセスは、すべての場合に金型またはコアの乾燥またはベーキングを必要とせず、それらの化学反応により急速な硬化作用が起こります。近年、以下の特殊成形工程の使用が大幅に増加しています。
1。二酸化炭素成形
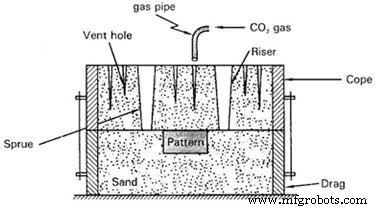
二酸化炭素成形 プロセス: このプロセスは、基本的に金型とコアの硬化プロセスです。 作業の原則 CO2プロセスの概要は、CO2ガス パススルー サンドミックス ケイ酸ナトリウムを含む (水ガラス)、ケイ酸ナトリウムが固いゲルになると、砂はすぐに非常に強く結合します。このゲルは、型に必要な強度を与える役割を果たします。
2。フェロシリコン成形
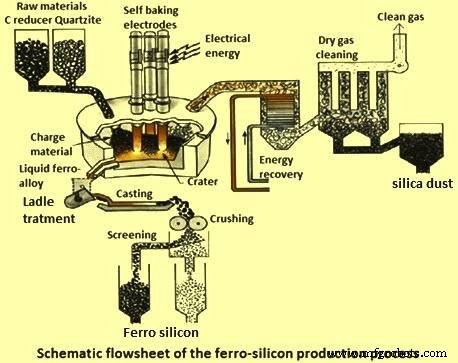
フェロシリコン成形 :この成形プロセスは、原則に基づいています ケイ酸ナトリウムの場合 および粉末状のフェロシリコン 混合 2.25:1の比率で 重量で、発泡作用が起こり、それらの間の発熱反応によって温度が上昇します。室温では、この反応はゆっくりと起こりますが、温度が上がると反応が加速します。最後に、ケイ砂は硬い海綿状の塊を形成します。 CO2プロセスのように金型やコアを焼く必要はありません。
通常、鉄鋳造の場合 きれいな65メッシュの乾いた砂 、非鉄鋳造の場合 、100メッシュの砂 適しています。金型は、閉じる前に適切な洗浄液でコーティングする必要があります。
3。ケイ酸二カルシウム成形
ケイ酸二カルシウム成形 :この成形プロセスは、原則に基づいています 約2〜3パーセントのケイ酸二カルシウム 、非常に効果的な硬化剤であることが知られており、5パーセントのケイ酸ナトリウム 混合 砂 適切な発泡化学物質とともに、砂塊の流動性が向上します。その結果、砂の混合物が金型内を容易に流れることができ、従来の成形プロセスで必要とされるような突っ込みの必要がありません。最後に、砂は十分な崩壊性を持った固い塊を形成します
主な利点 この成形プロセスの利点は、労働力の大幅な節約です。 および成形装置 乾燥や裏打ちが必要ないので。一方、高品質の欠陥のない鋳造品が製造されます。これは、ねずみ鋳鉄と鋼の両方の鋳物で、中型および重型の鋳物に幅広い用途があります。
4。セメント-砂型鋳造
セメント-砂型鋳造 :ポルトランドセメントは、砂粒を結合するための結合材料として使用できます。ケイ酸ナトリウムと一緒にセメントを使用することにより、強度、透過性、および流動性の良好な組み合わせが達成されることがわかります。流動性セメントスラリーは、砂混合物に発泡化学物質を使用して製造することもできます。したがって、砂の衝突は大幅に減少します。ただし、約2%の2セメント、4〜5%のケイ酸ナトリウム、および1%のピッチまたは糖蜜を追加することで、砂に良好な結合を形成できます。
これらの型は滑らかで正確な表面を生成しますが、セメント結合砂型の主な欠点は、フラスコからノックアウトするのが難しいことです。
5。シェルモールド
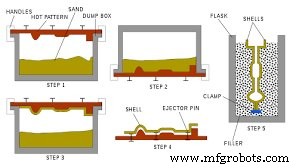
シェルモールド :発明者の名前にちなんで、シェルモールドはクロニングプロセスとしても知られています。 またはCプロセス 。これは、レジンボンドサンドテクニックの変形です。 鋼、鉄または非鉄合金の鋳造用。
型は、細かい砂(100〜150メッシュ)と、加熱された金属パターン(できればねずみ鋳鉄製)に対して配置された熱硬化性樹脂バインダーの混合物から形成されます。このように混合物を加熱すると、樹脂が硬化し、砂粒が互いに付着して、パターンの寸法と形状に正確に一致し、型の半分を構成する頑丈なシェルを形成します。
シェルが硬化してパターンから剥がされた後、必要なコアが設定され、金型の2つの半分が一緒に固定され、フラスコに入れられ、バックアップ材料が追加されます。これで、型を注ぐ準備が整いました。
6。ホットおよびコールドボックス成形
ホットボックスプロセス 特にコアメイキングに採用されているのは、シェルモールドで使用されているものと基本的に同じ材料を使用していますが、ここでは砂粒のコーティングに樹脂が使用されています。次に、樹脂と砂の混合物を、約200°から300°Cに加熱された金属パターンまたはコアボックスに吹き付けます。 シェルを形成する代わりに、固い塊を形成することができます。
砂の混合物が加熱されたパターンに吹き付けられ、吹き付けられた砂が硬化され、次に型またはコアがパターンまたはコアボックスから剥がされる特別なホットボックスマシンが利用可能になりました。
シェルモールドの場合よりも高い寸法精度と高い生産率が達成されます。これは、本質的に大量に必要とされる小さな鋳造品の機械的生産のための成形およびコア製造プロセスです。
コールドボックスプロセス 細かい乾いた砂を混ぜることで構成されます ポリイソシアネート樹脂 バインダー およびアルキドフェノール樹脂 、混合物を密閉されたコアボックスに吹き込み、空気中の触媒であるトリエチルアミン蒸気をコアボックスから注入します。液体フェノール樹脂のヒドロキシル基は、イソシアネート基と結合して、硬いウレタン樹脂を形成します。 2つのバインダー成分は通常1:1の比率で使用され、砂に1〜2重量パーセントの樹脂混合物が添加されます。 a
このプロセスには、パターンの加熱が不要であり、硬化が20〜30秒以内に行われるという利点があります。そのため、シンプルで高生産性のコア製造プロセスであり、大量に必要とされる小型の鋳造に非常に適しています。
7。投資成形
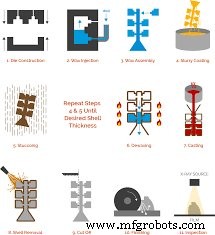
インベストモールディング :この鋳造プロセスは、「ロストワックスプロセス」と呼ばれることがよくあります。 」および「精密鋳造プロセス 」。このプロセスでは、鋳造を非常に近い公差で行うことができ、その後の機械加工は必要ありません。
主に2つのステージで構成されています 図に示されています。まず、マスターパターンは木または金属でできており、その周りに型が形成されます。それは型砂ではなく、マスターパターンの上に注がれるゼラチンまたは低融点の合金で構成されています。このマスターモールドは通常の2つのセクションで構成されており、開くことができます。 「失われたパターン」を作成するために使用されます 「。
8。しっくい成形
石膏成形 :この方法では、型は準備されます 石膏 またはパリの石膏。実際には、パリの石膏は、タルク、アスベスト、繊維、シリカ粉、および制御された量の水と混合されて、スラリーを形成します。この石膏スラリーは、フラスコに閉じ込められた金属パターンの上に注がれます。
型を振動させ、スラリーを固化させます。硬化が完了し、約30分後にパターンが除去され、コンベヤーオーブンで約200°Cにゆっくりと加熱することにより、型が乾燥され、裏打ちされます。インサートとコアが配置され、ガイドピンによって対応およびドラッグマッチされます。次に、溶融金属が型に注がれます。最後に、鋳物は型の中で冷却され、振り出され、型が破壊されます。次に、鋳物からゲート、スプルー、フラッシュがトリミングされます。
9。セラミック成形
セラミック成形 このプロセスでは、特別に開発されたセラミック骨材と液体化学バインダー(アルコールベースのシリコンエステル)で構成される濃厚なスラリーが、通常はマッチプレートに取り付けられている再利用可能なスプリットゲートメタルパターン上にピュアされます。スラリーはそれ自体ですべてのキャビティとくぼみを満たし、金型の突っ込みや振動は必要ありません。パターンは、約3〜5分で固まった後に撤回されます。次に、セラミック塊をフラスコから取り出し、硬化剤で処理して化学的安定化を促進し、炉内で約980℃に加熱して液体結合剤を除去します。これで、金型は溶融金属を注ぐ準備が整いました。
10。サクションモールディング
サクションモールディング プロセス: この方法では、金型空間から空気を抜いて真空を作ります。続いて鋳物砂を吸い込み、キャビティを充填します。その後、砂をパターンに押し込むことができます。このプロセスは、鉄、鋼、アルミニウムの鋳造に使用されます。
成形プロセスとそのタイプおよび分類に関連するすべての重要なポイントをカバーしようとしました。この記事を楽しんでいただけたでしょうか。以下のコメントでフィードバックをお寄せください。
産業技術