プラズマ切断vsレーザー切断:どちらがより良い切断手順です
機械工は、レーザー切断とプラズマ切断を同じ意味で使用します。ただし、これらは同様の切断機能を実行しますが、アプリケーションと原理が異なります。これらの2つの切断技術は、20世紀から存在していますが、機械工はより効果的な使用のためにそれらを近代化しました。
ここでは、プラズマ切断とレーザー切断の違いを学びます。また、2つの切断方法の利点に加えて、どちらを使用するかを決定する方法についても学びます。
レーザー切断とは何ですか?
レーザー切断は、増幅されたレーザー光を使用して材料をスライスする切断技術です。この手法は1960年代半ばに導入されました。レーザー切断は精度が高く、手作業ではないためです。代わりに、コンピューター数値制御(CNC)などのコンピューターがそれを制御します。
切断にレーザー光を使用することはロケット科学ではありません。代わりに、それは単純なプロセスです。これには、光学系を使用してレーザー光を小さな点に集束させることが含まれます。レーザー光は、光学系に入るにつれて小さくなり、熱くなります。この温度上昇が溶けてワークピースを切り裂き、コンピューターがプロセス全体を指示します。ただし、一部のオブジェクトは、溶けるのではなく、燃えるか、ガスの噴流によって吹き飛ばされるか、気化してしまいます。これにより、エッジが滑らかになり、高品質の表面仕上げが得られます。
レーザー切断で使用されるレーザーには、3つの重要なタイプがあります。それらは、二酸化炭素(CO2)、ネオジム(Nd)、およびイットリウム-アルミニウム-ガーネット(Nd:YAG)です。これらのレーザーはそれぞれ、さまざまな目的に適しています。 CO2は、切断、穴あけ、彫刻に最適です。
ただし、高エネルギーと低繰り返しが必要なボーリング用のレーザーが必要な場合は、Ndが最適です。一方、Nd:YAGは、高出力が必要なボーリングや彫刻に適しています。したがって、NdとNd:YAGはどちらもスタイルは同じですが、目的が異なります。これらの3つの主要なタイプのレーザーに共通していることの1つは、すべてが増幅されたレーザーを使用してワークピースを切断することです。
プラズマ切断とは何ですか?
機械工は何十年にもわたってプラズマ切断を使用してきましたが、今日でも優れた使用法を誇っています。それは1950年代に始まり、それ以来最高の切断方法の1つです。このプロセスでは、高温プラズマの加速ジェットを使用して導電性材料を切断します。この高温プラズマは、どんなにタフであっても、どのような材料でも溶ける可能性があります。
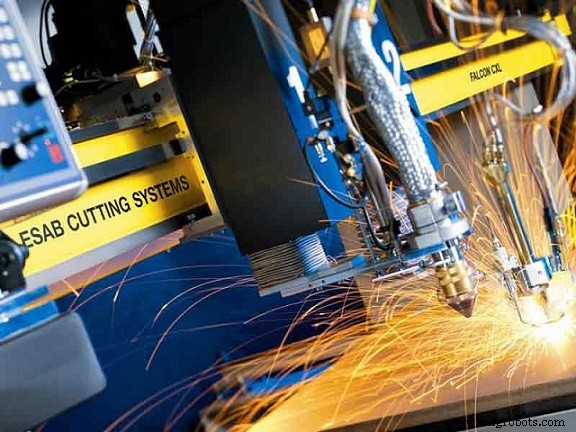
プラズマ切断は、アルミニウム、ステンレス鋼、鋼、真ちゅう、銅などの導電性材料に対してのみ機能します。裸火は使用しません。代わりに、導電性イオン化ガスであるプラズマを使用します。プラズマは通常、切断プロセス中は非常に高温になります。ただし、使用されるプラズマトーチのタイプによって一般的に温度が決まります。トーチはさまざまな温度を生成しますが、温度は通常非常に高温です。
プラズマは華氏40,000度までの非常に高い温度に達する可能性があります。プラズマトーチは、精密なCNC制御と組み合わせることで、仕上げをほとんどまたはまったく必要としない部品を製造できます。これらの松明は放射線を放出しますが、これは人間に害を及ぼす可能性があります。したがって、作業者は保護メガネまたはゴーグルを着用して目の弧から身を守る必要があります。
レーザー切断とプラズマ切断の違い
プラズマ切断とレーザー切断を比較する場合、2つの切断方法が異なる2つの主要な領域を検討する必要があります。それらは:
原則の違い
プラズマ切断では、使用する材料の種類に応じて、酸素、空気、不活性ガスなどの圧縮ガスを使用します。この切断プロセスには、ワークピースを通るプラズマの人工チャネルの作成が含まれます。プラズマは非常に高温になり、そのような温度では、どんなに厚くても、あらゆる物体を溶かしたり、蒸発させたり、燃やしたりする可能性があります。
一方、レーザー切断では、レーザーデバイスによって生成されたレーザービームを使用します。一連の反射板がレーザービームを透過します。その後、ビームはフォーカスレンズによってワークピースに集束されます。レーザービームは焦点を加熱して溶かし、高品質の表面仕上げで滑らかなエッジを作成します。
要約すると、プラズマ切断とレーザー切断は原理的に異なります。プラズマ切断はプラズマを使用し、レーザー切断は増幅されたレーザー光を使用します。
アプリケーション
機械工はプラズマ切断を使用してあらゆる種類の金属を切断します。ただし、中厚のプレートをカットするのに最適です。
中薄板の切断にはレーザー切断が最適です。金属、非金属、ガラス、セラミック、ゴム、木材、プラスチック、PVC、皮革、有機ガラス、繊維など、切断材料も幅広くなっています。
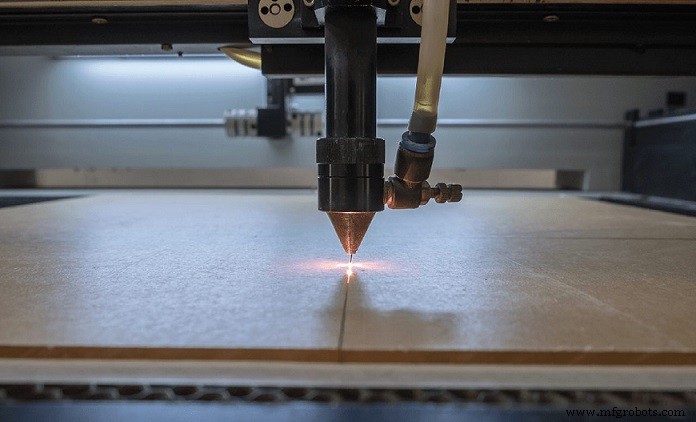
したがって、プラズマ切断された材料は、より広い範囲のレーザー切断と比較して、選択の範囲が狭くなります。薄いシート切断の場合、レーザー切断はプラズマ切断よりも優れています。
機械工は、次のことが必要な場合にプラズマ切断を使用します:小さな変形、小さな熱影響領域、狭い切断スロット、および速い切断速度。
一方、レーザーは、非常に高精度、高方向、高強度、高速で、その後の処理が不要な場合に使用されます。
また、プラズマ切断とレーザー切断のコストを比較すると、プラズマ切断の方が安価です。
レーザーおよびプラズマ切断の利点
レーザー切断とプラズマ切断にはそれぞれの利点があり、使用するのに適したものを見つけるときに考慮する必要があります。それぞれの利点は次のとおりです。
レーザー切断の利点
- 余分な仕上げを必要としない滑らかなエッジを提供します
- 薄いシートで10m/minに達する可能性のある高速切断速度
- 0.05mmに達する可能性のある高い測位精度と、0.02mmに達する可能性のある再配置精度を備えた高精度
- 金属、ゴム、木材、プラスチック、PVC、皮革、有機ガラス、繊維など、さまざまな素材を切断できます。
プラズマ切断の利点
- 中厚板を非常に高速で切断できます
- プラズマ切断の維持費は安いです
プラズマ切断とレーザー切断のどちらかを選択する際に考慮すべき要素
ほとんどの人は、主に2つの方法が類似しているため、適切な切断方法を選択するのが難しいと感じています。ただし、レーザー切断とプラズマ金属切断のどちらを選択するかという不必要な混乱を避けるために、3つの重要な要素を考慮する必要があります。それらは:
素材
プラズマ切断は、レーザー切断に比べて用途が限られています。したがって、金属、ゴム、木材、プラスチック、PVC、皮革、有機ガラス、繊維などの材料を切断する場合は、レーザー切断を選択する必要があります。一方、あらゆる種類の金属、主に中程度の厚さのプレートを切断する必要がある場合、適切な切断方法はプラズマ切断です。
精度
仕事に必要な精度のレベルも考慮する必要があります。非常に高精度の切断が必要な場合は、レーザー切断が最適です。
コスト
予算に合わない場合、特定の切断プロセスを選択するのは無意味です。プラズマ切断は安価です。したがって、予算にやさしい切断方法をお探しの場合は、プラズマ切断が最適です。
RapidDirect板金サービス
かつて板金会社をひいきにしましたが、受けたサービスに不満がありますか?肯定的に答えれば、信頼できるより良い会社を見つけたので、今すぐリラックスできます。
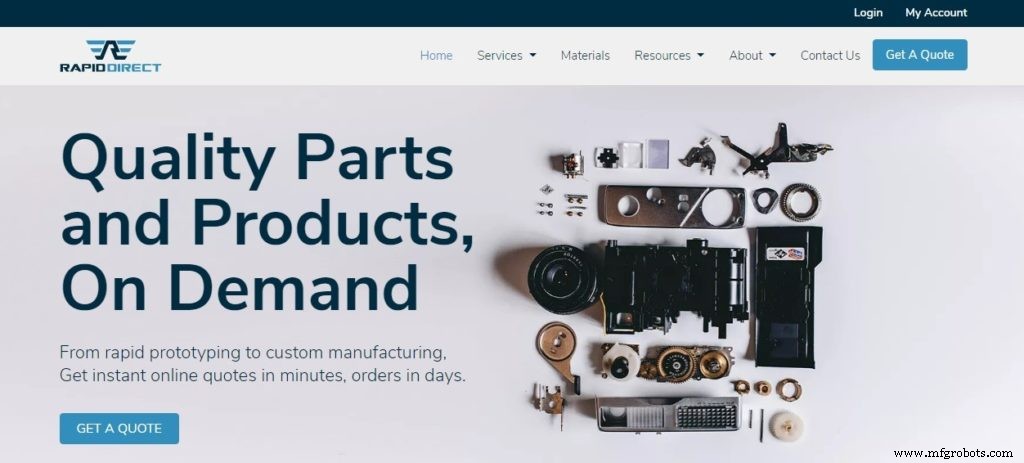
RapidDirectは、品質を損なうことなく費用効果の高いサービスを提供します。少量の試作品と大量生産のためのオンデマンドの金属加工を提供します。 12時間以内に見積もりを取得することもできます。
RapidDirectでは、クライアントと私たちの間の優れた通信システムが、部品を適切に処理するための秘訣であることを認識しています。したがって、保護中に必要なすべての技術サポートを利用できます。私たちの板金エンジニアリングチームは、20年以上の経験を持ち、何十年にもわたって業界に携わってきました。したがって、ご希望の高品質のサービスを提供するだけでなく、プロジェクトの技術的な提案も提供します。
おそらく、ラピッドプロトタイピングからカスタム生産までプロジェクトを処理できる1つの会社を探しています。私たちはあなたにぴったりの会社なので、もう探す必要はありません。大規模なプロジェクトで優れたサービスを提供できると確信しています。
結論
プラズマ切断とレーザー切断はどちらも非常に効果的な切断方法です。どちらも「切断機能」を果たしますが、用途や原理が異なります。機械工はこれら2つを同じ意味で使用しますが、最初に使用目的を考慮せずにランダムに選択することは専門家ではありません。ニーズを検討し、それを各切断方法の原則と適用と比較すると、選択する適切な方法について明確な決定を下すことができます。ただし、それでも決心がつかない場合は、サポートさせていただきます。
よくある質問
Q :どのプラズマ切断ガスが最適ですか?
A :切断するワークピースの種類に応じて、さまざまな種類のガスまたは特別な組み合わせが必要になります。ただし、最も推奨されるガスは、窒素、圧縮空気、および酸素です。
Q :使用するプラズマ切断ガスを知るにはどうすればよいですか?
A :ステンレス鋼またはアルミニウムの切断には、圧縮空気で十分です。軟鋼を切断する場合は、酸素を選択する必要があります。軟鋼やステンレス鋼、アルミニウムなど、最大3インチの厚さの金属を切断する場合は、窒素を選択します。
産業技術