アプリケーションスポットライト:3D印刷がどのように高性能の油圧コンポーネントを可能にするか
[画像クレジット:レニショー]
油圧部品の設計と製造における新しいアプローチの需要が高まっています。製造業者が油圧製造の新しい機会を探求できるようにする1つの技術は、3D印刷です。
LiebherrやFordからBoschRexrothまで、企業は3D印刷を利用して、よりエネルギー効率が高く、軽量で安価な油圧コンポーネントを作成しています。
今日のアプリケーションSpotlightは、油圧システムとコンポーネントの3D印刷の利点を掘り下げ、実際のテクノロジーの最もエキサイティングな例を探ります。
このシリーズで取り上げている他のアプリケーションを見てみましょう:
熱交換器用の3D印刷
ベアリングの3Dプリント
自転車製造用の3Dプリント
デジタル歯科およびクリアアライナー製造のための3D印刷
医療用インプラントの3Dプリント
3Dプリントロケットと宇宙船製造の未来
靴製造用の3Dプリント
電子部品の3Dプリント
鉄道業界における3Dプリント
3Dプリントアイウェア
最終部品生産のための3D印刷
ブラケットの3Dプリント
タービン部品の3Dプリント
3Dプリントが原子力産業のイノベーションをどのようにサポートするか
油圧コンポーネントに3D印刷を使用する理由は何ですか?
油圧は、重い負荷がかかる場合、または反復運動が必要な場合に、動きを作り出す最も効率的な方法の1つです。
油圧システムはポンプを使用して液体を加圧し、その動きを利用してクレーンから車まですべてに電力を供給します。
油圧は毎日私たちの周りにあります。車両、建設機械、建物、製造施設で使用されています。
油圧コンポーネントは、伝統的に機械加工または鋳造によって製造されます。ただし、多くの油圧機器メーカーは、3D印刷を使用して、マニホールド、サーボバルブ、油圧アダプターブロックなどの油圧コンポーネントを製造することに関心を持っています。しかし、そもそも何が彼らにテクノロジーを考えさせるのでしょうか?
Bosch RexrothAGの産業用油圧ビジネスユニットの責任者であるSteffenHaackによると、油圧業界を形作る多くのトレンドがあります。
- エネルギー効率(流動力の低減、圧力損失の低減、効率の向上)
- ノイズリダクション
- タンク容量の削減
- より高い圧力レベルと設置スペースの削減
- 改善された材料と油の特性
- より高い可用性と予知保全
- 使いやすさ
- 安全性
特に金属や砂を使用した3D印刷は、エネルギー効率の向上や設置スペースの縮小など、これらのトレンドのいくつかを推進する上で重要な役割を果たします。
どうやって?新しい機能を組み込むことを可能にする高度な設計を可能にすることにより、コンポーネントの重量とサイズを削減し、油圧システム全体のパフォーマンスを向上させます。
油圧用の3D印刷の利点について詳しく見ていきましょう。
油圧コンポーネントの重量とサイズを削減
3D印刷により、油圧部品メーカーは部品をより軽く、より小さくすることができます。
例として油圧マニホールドを取り上げます。油圧システムのコンポーネント間の流体の流れを調整するのに役立つこの部品は、通常、金属の固いブロックから機械加工されます。
必要以上に余分な金属を取り除くには費用がかかり、多くの場合、余分な金属は機械加工されないため、部品の重量が潜在的に可能になる可能性があります。
3D印刷は、マニホールドの製造に必要なほぼ同じ量の材料を必要とするため、この問題を克服するのに役立ちます。
選択的レーザー焼結のような金属3D印刷プロセスでは、レーザーが部品のミクロンの薄さの断面をトレースし、金属粉末を層ごとに選択的に溶融および溶融します。これにより、エンジニアは、CNC機械加工に必要な金属よりも少ない金属を使用して、部品に入る材料の量を制御できます。
3D印刷は、コンポーネントの軽量化に加えて、設計に制約のあるスペースにより適した、よりコンパクトなパーツを可能にします。この利点により、3D印刷された油圧コンポーネントは、高精度と軽量を必要とするアプリケーションで特に求められています。
スポットライト:Aidroの3Dプリントマニホールド
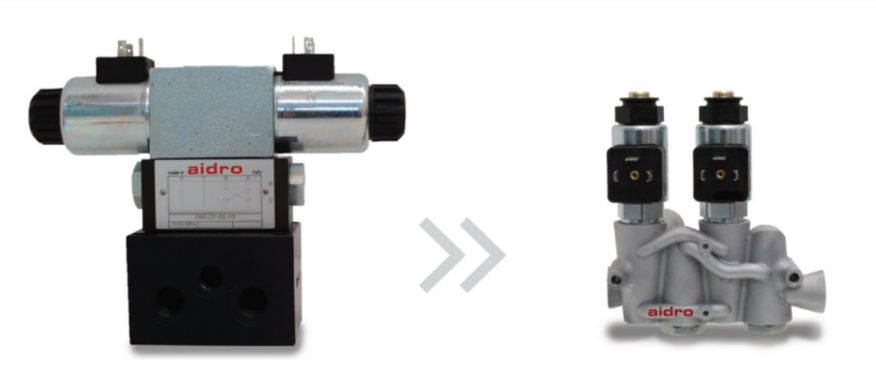
3Dプリントされた油圧コンポーネントの一例は、イタリアのメーカーであるAidroによるものです。
農業機械で使用されるAidroの油圧マニホールドは、使用するシステムの重量とスペースを節約するために再設計されました。3D印刷されたアルミニウムマニホールドは、交換するユニットと同じ機能を実行しますが、サイズが以前のマニホールドより75%軽量化されています。
部品の統合
3D印刷では、複数のパーツを1つに統合することで、コンポーネントを小さくすることもできます。これは、パーツ統合と呼ばれるアプローチです。
これにより、漏れの原因となる可能性のある弱い接合点が少なくなるため、製造業者はコンポーネントの複雑なアセンブリを排除し、部品の構造的完全性を高めることができます。
効率の最適化
3D印刷により、油圧コンポーネントの内部形状を再設計して、流体の流れを最適化し、圧力降下を減らすことができます。
マニホールドを例にとると、エンジニアは流体フローチャネルをマニホールド内の正確な位置に配置できます。必要とされ、さまざまな形やサイズで。これは、フローチャネルが湾曲した形状を持ち、従来のマニホールドよりも間隔を狭めることができることを意味します。これにより、完成品がよりコンパクトで軽量になります。
湾曲した流路は、流れの効率を30〜70%向上させると報告されています。
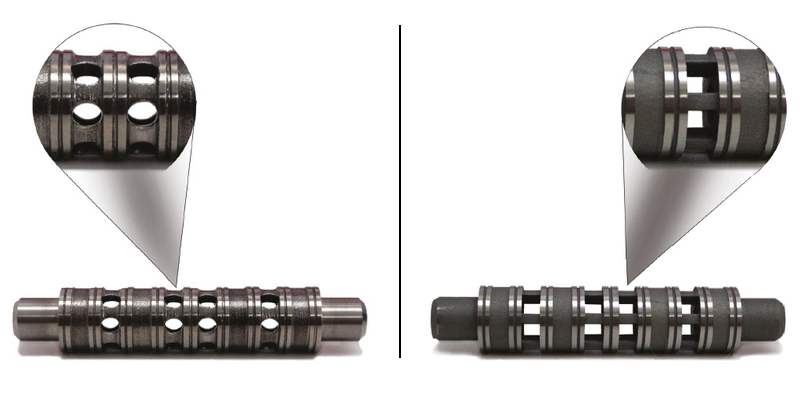
フローチャネルの断面の形状を再設計することも、違いを生む可能性があります。たとえば、バルブスプールの流路は、回転カッターで機械加工されているため、通常は丸い形状になっています。
3D印刷により、エンジニアは流路の断面を円形ではなく正方形に設計できます。これにより、流量が最大20%増加し、圧力損失が減少します。
さらに、マニホルドなどの従来の油圧コンポーネントでは、クロスドリル通路の機械加工が必要になることが多く、オイル漏れを防ぐために後でプラグを差し込む必要があります。ただし、これらのプラグされたチャネルは、システム障害を引き起こす可能性のある潜在的なリークパスを作成します。 3D印刷は、そもそもクロスドリルされたパッセージを作成する必要をなくすことで、この問題を解消します。
3Dプリントされた油圧コンポーネントのその他の例
油圧アダプターブロックの3Dプリント
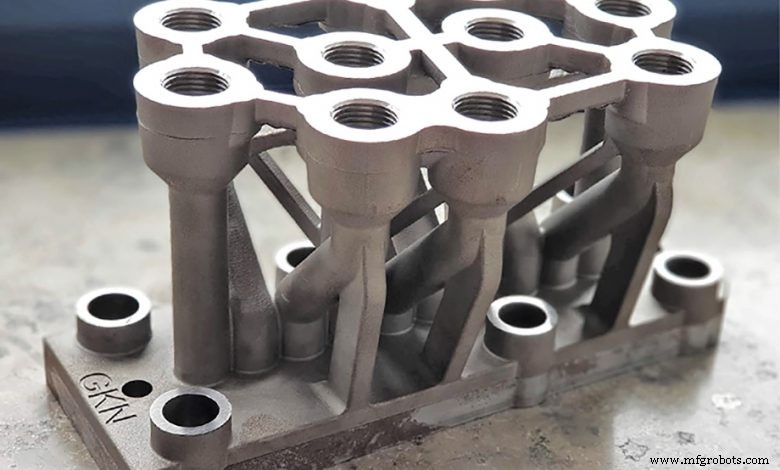
GKN Additiveは、油圧システム内の流体の流れを方向付け、バルブ、ポンプ、アクチュエーターをリンクするマニホールドである油圧アダプターブロックを3Dプリントしました。
従来使用されていた油圧ブロックは、一連の内部チャネルがドリルで開けられたブロック状の設計になっている傾向があります。油圧ブロックの製造プロセスは、上下から穴を開けることから始まります。
次に、垂直の穴を水平のチャネルで接続し、ねじを切り込みます。開いた水平チャネルからのオイル漏れを防ぐために、それらはグラブネジで塞がれ、密閉されています。
ただし、このプロセスはいくつかの理由で非常に非効率的です。第一に、ドリル加工およびフライス加工されたエッジは、後処理で到達するのが難しい鋭いバリを作成します。これらは、動作中に壊れてシステム障害を引き起こす場合があります。
次に、鋭いコーナー接続ポイントは乱流を生成し、エネルギーの非効率性をもたらします。第三に、未使用の水平チャネルは汚れを蓄積し、油圧システムの動作寿命を縮める可能性があります。
3D印刷は、GKN Additiveが上記の課題を克服し、より優れた性能の油圧ブロックを作成するのに役立ちました。
油圧ブロックの重量は、機能を犠牲にすることなく、30kgから5.5kgに減少しました。新しい設計により、余分な材料を取り除き、部品内にボアの重なりがないことを確認することができました。
さらに、新しい設計では未使用の水平チャネルが完全に省略されているため、汚れが蓄積する場所がありません。最後に、システム内の乱流を減らすために、エンジニアは鋭い内部コーナーを滑らかなパイプラインに置き換えました。
このアプリケーションの3D印刷の利点をまとめると、3D印刷により、製造業者はより少ない材料を使用しながら、コンポーネントの機能を向上させることができました。これは、部品の軽量化と製造コストの削減につながりました。
Liebherrの3Dプリントされた油圧バルブブロック
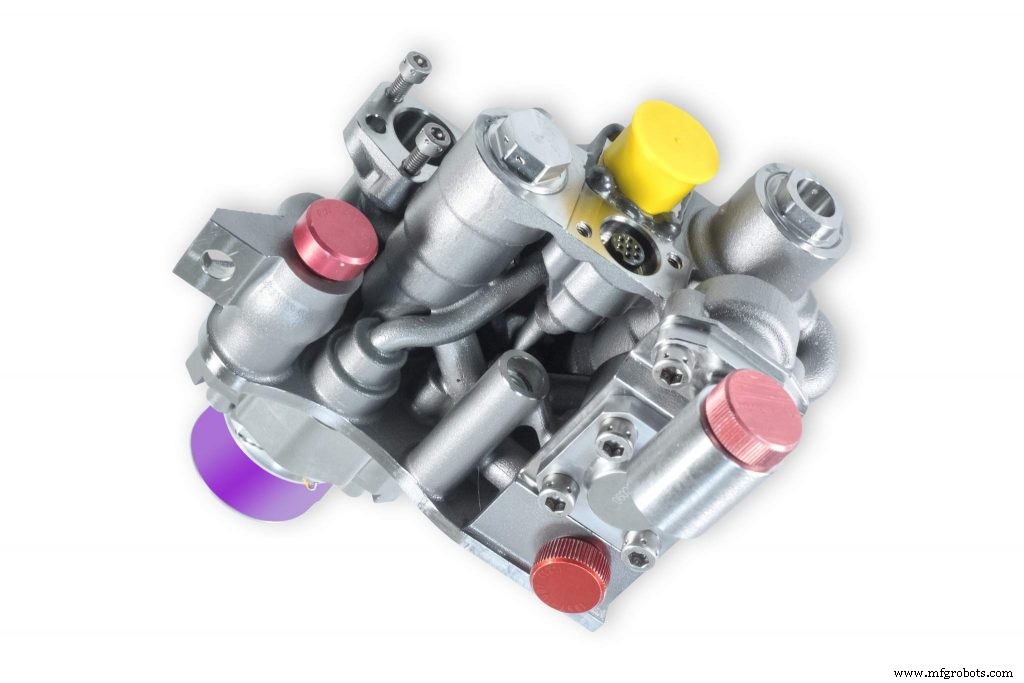
油圧用の3D印刷のもう一つの良い例は、LiebherrGroupからのものです。同社は3D印刷の助けを借りて、航空機で使用されている高圧油圧バルブブロックを再設計し、軽量化と効率化を実現しました。
Liebherrチームは、10個の機能要素を新しいバルブブロックに統合し、多数の横方向の穴がある複雑な配管システムを排除しました。その結果、より少ない部品で作られた35%軽量のバルブブロックが実現しました。
3D印刷された部品は、A380航空機のテスト飛行で正常にテストされました。
ドミン流体力 3Dプリントで流体動力システムを再考
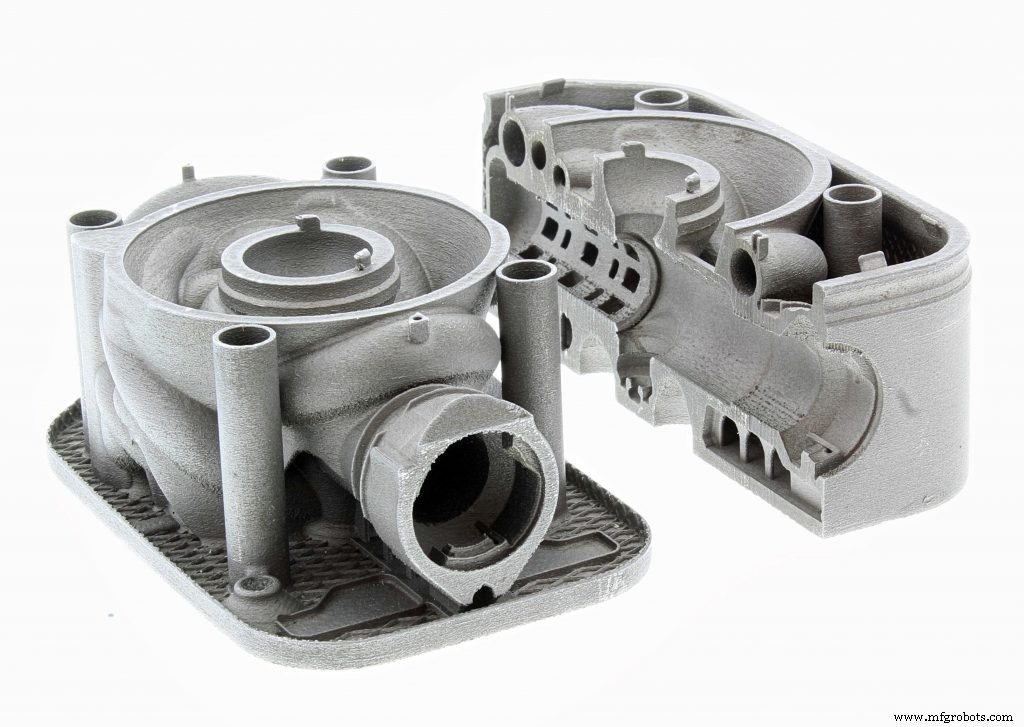
英国を拠点とする油圧システムメーカーのDominは、信号を圧力に変換するために使用される高性能ダイレクトドライブサーボバルブを再開発するために3D印刷に目を向けました。
Dominは、3D印刷により、複雑な部品をより速く、工具を使わずに構築できると述べています。たとえば、同社は、元のサイズの25%で、より強力なドライブの1つを設計しました。部品は3分の1のコストで製造され、製造時間は5.5時間からわずか1時間に短縮されました。
このような結果は、従来の方法では達成できないとドミン氏は言います。
Ford3Dはインテークマニホールドを印刷します
重機や航空機用に3D印刷された油圧コンポーネントの例を見てきましたが、フォードは自動車用油圧システム用の3D印刷の先駆者です。
昨年、自動車メーカーは、稼働中の車両に搭載された史上最大の3Dプリントされた金属製インテークマニホールドであると主張するものを展示しました。
その車両は、ケンブロックの「Hoonitruck」です。フォードピックアップ。
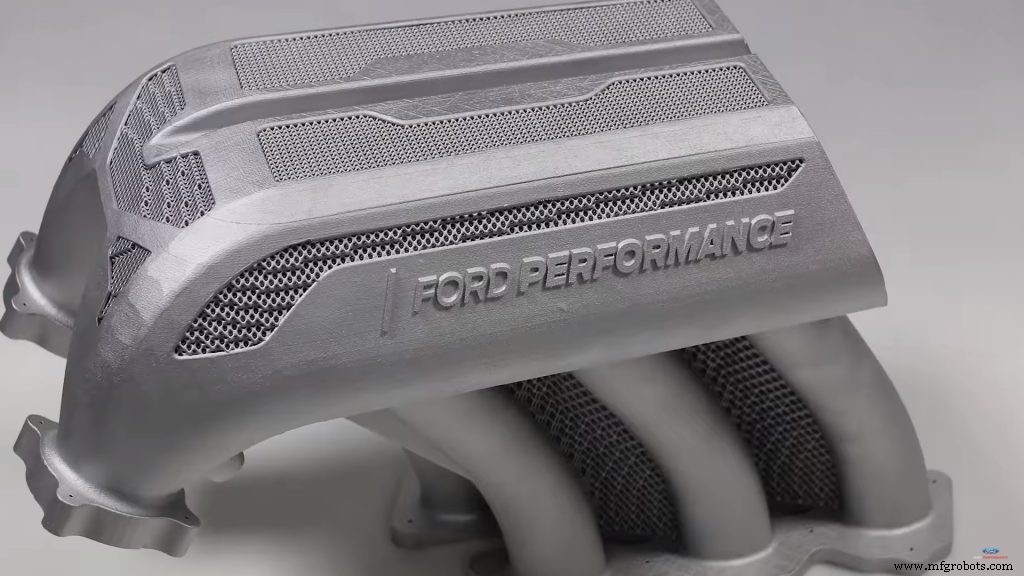
車両は、ターボチャージャーからの空気をエンジンのシリンダーに供給するために特別なインテークマニホールドを必要とし、フォードは金属3D印刷に目を向けることに決めました。
パーツは、コンセプトレーザーマシンを使用してアルミニウムから3D印刷され、構築に5日かかりました。最先端のCADソフトウェアを使用することで、従来の製造方法では作成できなかった複雑なウェブのような構造を作成することができました。設計は、パフォーマンスの向上と軽量化のために最適化されています。最終部品の重量はわずか6kgです。
Bosch Rexrothは、マニホールドに砂の3D印刷を使用しています
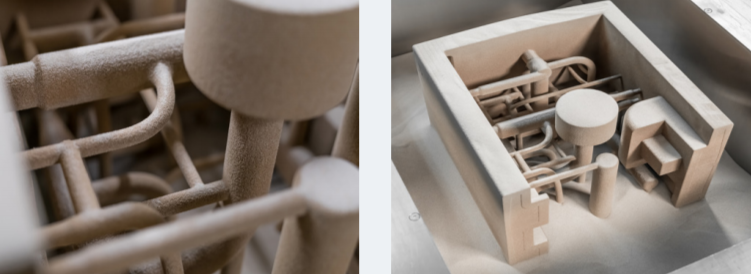
金属の3D印刷に加えて、後で油圧コンポーネントを鋳造するために使用できる砂のコアを3D印刷するオプションもあります。この用途に使用されるプロセスはバインダー噴射と呼ばれ、ケイ砂の層に結合剤を選択的に堆積させることによって機能します。
Bosch Rexrothは、ここ数年、コントロールブロックのキャストコアを製造するために砂の3D印刷を使用してきました。
これを行うことの主な利点の中で、Bosch Rexrothは、マニフォールド内のフィルターなどの機械コンポーネントを統合する機能と、最大30%の軽量化を挙げています。
追加の利点には、漏れを引き起こす可能性のある補助穴の必要性の排除、およびエネルギー効率を改善する内部フローチャネルの最適化が含まれます。
3Dプリントによる油圧コンポーネントの再考
油圧業界がよりエネルギー効率が高く、より小型の油圧コンポーネントに向けて努力しているため、3D印刷は、より優れた性能の設計を開発および製造するためのオプションを提供します。
リードタイム、軽量化、3D印刷によるコストとパフォーマンスの利点を見て、多くの油圧部品メーカーが自社製品にこのテクノロジーを模索し始めています。
今後、油圧部品の製造における3D印刷の役割が増大し、油圧業界の企業が現在および将来のトレンドに追いつくのに役立つと期待しています。
3Dプリント
- アプリケーションスポットライト:医療用インプラントの3D印刷
- アプリケーションスポットライト:デジタル歯科およびクリアアライナー製造のための3D印刷
- アプリケーションスポットライト:自転車製造のための3D印刷
- アプリケーションスポットライト:ベアリングの3D印刷
- アプリケーションスポットライト:熱交換器用の3D印刷
- アプリケーションスポットライト:鉄道業界での3D印刷
- アプリケーションスポットライト:3Dプリントの恩恵を受けることができる5つの電子部品
- アプリケーションスポットライト:履物の3Dプリント
- アプリケーションスポットライト:3Dプリントロケットと宇宙船製造の未来
- アプリケーションスポットライト:3Dプリントアイウェア
- アプリケーションスポットライト:タービン部品の3D印刷