7倉庫プロセスとそれらを最適化する方法
倉庫、配送センター、またはフルフィルメントセンターは、施設に出入りする在庫の一定の流れを管理する必要があります。テクノロジーにより、倉庫管理システム(WMS)などの集中型プラットフォームにより、このプロセスがはるかに簡単になりました。これらのソフトウェアプログラムをセンサー、スキャナー、バーコードに接続して、デジタルで自動化された作業環境を作成できます。
在庫の流れを最適化するには、倉庫管理者は作業の分散を特定のステップに分割する必要があります。この投稿では、倉庫内の7つの主要なプロセスを確認し、それぞれを最適化する方法について説明します。システム全体を見ると、倉庫をより効率的にするために合理化できる重要なステップを特定することができます。改善計画の最終的な目標は、在庫の正確性、需要予測の正確性、およびその他の重要なサイト指標を改善することです。
1。受信
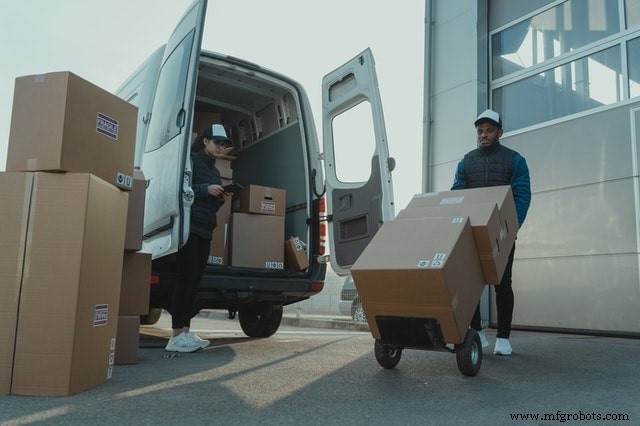
受信プロセスは、施設内の他のすべてのアクティビティのペースを設定するため、倉庫環境では重要です。効率的な運用には、不必要な配達の蓄積を避けるために適切に編成された受け取りエリアのレイアウトが必要です。受け取り活動を最適化するには、コンベヤーやその他の形式の自動処理装置を設置することが有益な場合があります。
受け取りエリアとステージングおよび在庫保管のための他の場所との間に大きなスペースがある場合、機器の取り扱いは特に役立ちます。また、いつでもすばやくスキャンできるバーコードを使用して、受信手順を自動化することをお勧めします。もう1つのベストプラクティスは、サプライヤと事前出荷通知(ASN)を追求することです。これは、受領時にスキャンして、アイテムを在庫にすばやく追加できます。
2。収納庫
典型的な倉庫ワークフローの次のプロセスは、商品が入庫エリアから保管エリアに移動されるときに保管されます。在庫を管理する際の最も重要な考慮事項の1つは、保管に適切な場所を選択することです。保管プロセスを迅速かつ効率的にするために、事前に保管場所を定義し、倉庫内の人とフォークリフトのための明確な移動経路を作成することが重要です。
これらの場所には、倉庫の床ラベル、再帰反射倉庫の標識とラベル、吊り下げられた倉庫の標識、およびフォークリフトなどの長距離からはっきりと見えるおよび/またはスキャン可能な倉庫の通路の標識をラベル付けして、作業者がすばやく位置を特定できるようにすることができます。在庫受入タスクの正しい保管場所。パレットのバーコードラベルとタグ、およびリターナブルトート、トレイ、コンテナのバーコードラベルは、倉庫作業員が適切な保管場所に在庫を整理するのにも役立ちます。 WMSプラットフォームは、在庫の場所を割り当てたり、ストレージの内外でアイテムをスキャンしたりするときに非常に役立ちます。
3。ストレージ
工場での保管場所を適切に計画するには、使用可能なスペースの量を最大化するようにレイアウトを慎重に検討する必要があります。各倉庫の具体的な組織計画は、ビジネスニーズ、施設構造、および使用されるオンサイトシステムに基づいて一意になります。
ストレージを最適化する最良の方法の1つは、さまざまな種類の商品の使用率と効率を追跡できる明確な指標を定義することです。これは、動きの遅い在庫を混雑した移動レーンから離れた場所に移動するなどの改善点を特定するのに役立ちます。
4。ピッキング
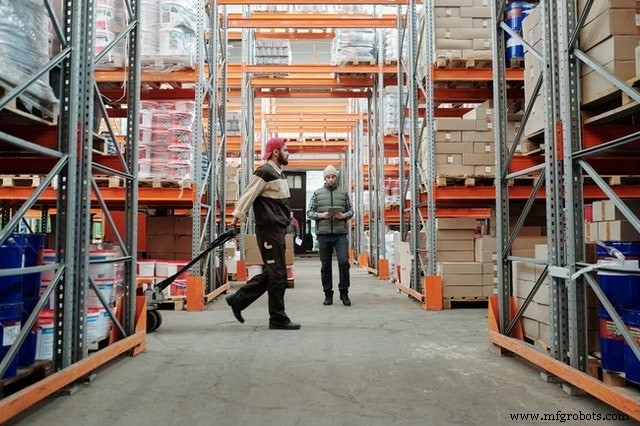
ピッキングは、注文を満たすために出荷する必要のある商品を選択するために、どの倉庫でも必要なプロセスです。かなりのコストと時間がタスクの選択に費やされており、それは最適化するための最も重要なステップの1つです。今日の効率的なピッキングプロセスは、テクノロジーによって実現する必要があります。
採用できるピッキング方法は多数ありますが、ソフトウェアシステムと統合された倉庫ラックラベルを使用すると、いくつかの個別のステップで効率を追跡し、さらなる改善を推進する方法を見つけることができます。冷蔵ラックラベルと冷蔵ラックプラカードにより、温度管理された倉庫エリアでも倉庫ラックにラベルを付けることができます。倉庫でのピッキングの正確さを理解することは、ピッキング戦略の調整や個々の注文のニーズに関する決定を下すときにも役立ちます。
5。パッキング
倉庫が販売注文を受け取り、アイテムがピッキングされたら、梱包して出荷の準備をする必要があります。このプロセスの最適化には、多くの場合、梱包材の合理化と検査の速度の向上が含まれます。また、問題が特定された場合に移動を追跡できるように、各アイテムが倉庫内に完全な管理過程を持っていることも重要です。
6。配送
出荷または発送のプロセスは、アイテムが倉庫を離れる前の最後のステップです。積み込みドックでの遅延を最小限に抑えるために、注文は流通センターの管理者と慎重に調整して、準備ができたらすぐに商品が受け取られるようにする必要があります。配送を最適化するための最良の方法の1つは、ピッキングアクティビティを「ウェーブ」で整理して、1回のピックアップで多数の関連パッケージを準備できるようにすることです。
7。返品
注意が必要なもう1つのステップは、返品プロセスです。倉庫管理の望ましい部分ではありませんが、返品は非常にビジネス上の現実です。すべての企業は、返品管理承認(RMA)手順を利用して、返品ごとに一意の番号を割り当て、顧客に指示を与える必要があります。また、倉庫内に返品と在庫補充のための在庫を処理するための専用スペースを用意することも重要です。
ご覧のとおり、これらの7つの主要なプロセスは倉庫内で相互に接続されており、真空状態で管理することはできません。システム全体を見て、主要なステップごとに有用なメトリックを特定することにより、最も高度な倉庫設計でさえも改善することができます。この投稿で提示されたヒントが、自社の倉庫業務における改善のいくつかの領域を特定するのに役立つことを願っています。
産業技術
- 7つの一般的なピックアンドパックエラー—およびそれらを修正する方法
- 6つの一般的なロジスティクスの間違いとそれらを回避する方法
- ラストマイルデリバリーの7つの課題とその解決方法
- テクノロジー、人、プロセスを通じてサイバーセキュリティにアプローチする方法
- 4種類のサイバー攻撃とその防止方法
- ラストマイルデリバリーの3つの落とし穴—そしてそれらを回避する方法
- 7つの一般的な輸送の失敗とそれらを回避する方法
- 開閉装置の故障の4つの主な原因とそれらを回避する方法
- 機械の故障の主な原因とその防止方法
- 3つの主要な倉庫プロセス(およびそれらを改善する方法)
- アディティブ マニュファクチャリングと従来の製造が補完的なプロセスである理由