ウレタン鋳造 vs. 射出成形 — DFM ガイド
製造のための設計 (DFM) には、部品設計の最適化が含まれます。これにより、製造業者は高品質の部品を可能な限り低い単位あたりのコストで製造できます。製造方法とその制約を考慮に入れることで、設計者は生産時間を短縮し、コストを削減し、大幅な再設計を防ぐことができます。
DFM のベスト プラクティスは、作成する製品と選択した製造方法によって異なります。射出成形とウレタン鋳造はどちらもプラスチック成形部品を作成できる成形技術ですが、DFM ガイドラインは異なります。知っておくべきことはすべてここにあります。
ウレタン鋳造 vs. 射出成形
部品の射出成形を開始する前に、適切な工具を設計し、CNC 機械加工によって製造する必要があります。部品の形状はツーリングに直接影響するため、複雑なコンポーネントがある場合は、複雑なツーリングが必要になります。複雑な部品では、金型の設計にスライド アクション、リフター、または取り外し可能なコアを組み込む必要がある場合があります。射出成形プロセス中に、コアとキャビティが一緒になります。次に、溶融プラスチックが金型に射出され、冷却され、硬化され、排出されて、使用可能な部品が作成されます。
ウレタン鋳造は、CNC 機械加工または 3D プリントによって作成されるマスター パターンから始まります。オペレーターは、マスター パターンをモールド ボックスに入れ、ボックスに液体シリコンを充填して硬化させます。硬化プロセスが完了したら、型を半分に切断してマスター パターンを取り外します。後に残るのは、成形される部品の形状の空洞です。次に、キャビティにウレタン キャスティング レジンを充填し、硬化のために加熱された真空チャンバーに入れます。
- どちらのプロセスも金型のキャビティにプラスチック材料を充填する必要がありますが、ウレタン鋳造と射出成形にはいくつかの重要な違いがあります。
- 射出成形用の金型は多くの場合、スチールまたはアルミニウムで作られているため、ウレタン鋳造で使用されるシリコンの金型よりもはるかに耐久性があります。
- ウレタン鋳造金型の作成は、射出成形用の金型の作成よりも安価です。複雑な射出成形金型は簡単に数万ドルの費用がかかりますが、ウレタン鋳造金型の製造には通常、数百ドルまたは数千ドルの費用がかかります。
- 射出成形金型が生産段階に入るまでに数か月かかる場合がありますが、ウレタン鋳造金型は 2 週間以内に成形できます。
- ウレタン鋳造は、射出成形よりも肉厚とアンダーカットの点で寛容です。
大量生産を計画している場合や公差が厳しい場合は、射出成形を検討してください。金型はシリコン金型よりも耐久性と剛性が高く、金属は一貫した部品品質を継続的に提供します。さらに、射出成形は、ウレタン鋳造に比べてはるかに制御しやすくなります。メーカーは、材料の流れと冷却速度だけでなく、射出成形時の射出温度と位置も制御できます。射出成形用の金型を作成するコストは最初は高く見えるかもしれませんが、数千の部品に分割すると費用対効果が高くなります。
一方、ソフト ツーリングは速度、柔軟性、手頃な価格を提供するため、プロトタイプの開発や少量生産の実行にはウレタン キャスティングが最適です。製品に対する需要が高いものの、恒久的な金型がまだ準備できていない場合は、ウレタン キャスティングで生産を開始できます。
ウレタン鋳造と射出成形に関する DFM の主な懸念事項
ウレタン鋳造または射出成形の DFM に関しては、公差、肉厚、およびアンダーカットを念頭に置いておく必要があります。
公差
完璧な製造プロセスはないため、設計者やエンジニアは、許容できる公差を確立することで、これらの変動を許容します。部品は、基本測定値からのこれらの許容可能な測定値の変動と比較されるため、寸法がこれらの制約に準拠しているものは許容可能と見なされます。公差で定義された量を超える寸法の変動があるものは、意図したとおりに機能しません。これらの公差は設計プロセス中に確立され、どの製造プロセスを使用できるかを決定します。
鋳造ウレタンで厳しい公差を達成することは、不可能ではないにしても非常に困難です。金型は、真空負荷によって動くことができる柔軟なシリコンでできているためです。非常に正確な部品が必要な場合は、鋳造ウレタンを使用して部品を製造しないでください。
一方、金属射出成形金型は、あまり動かないため、最終測定寸法の変動が少なくなります。ただし、溶融プラスチックは冷却するにつれて収縮するため、部品の最終測定寸法にわずかな変動が生じます。これを反映する射出成形公差を確立する必要があります。
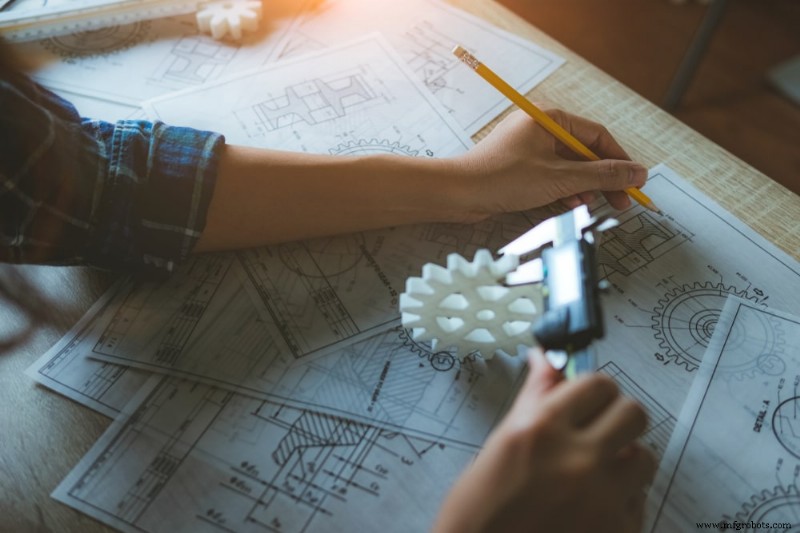
公差が小さすぎると手頃な価格になる可能性がありますが、使いやすさに影響する可能性があり、公差が大きすぎると費用と時間がかかります。時間をかけて 2 つの間の完璧なバランスを見つけることで、部品の信頼性、機能性、および意図した他の部品との適合性を確認できます。部品の機能、公差スタック、および製造と組み立てのプロセスを考慮してください。選択した製造方法が公差要件を満たすことができない場合は、別の製造技術を使用する必要がある場合があります。また、公差を緩めても機能するようにパーツを再設計することもできます。
肉厚
均一な肉厚を維持することは、部品間の一貫性を高め、応力分布を改善し、コストを削減するために重要です。肉厚が不均一または不均一であると、射出成形部品に反り、ヒケ、収縮、ショート ショット、またはボイドが発生する可能性があります。
部品の理想的な肉厚は、そのサイズ、形状、構造的および美的要件によって異なります。最良の結果を得るには、射出成形部品の肉厚を 1 ~ 4 mm にすることをお勧めします。ウレタン鋳造でパーツを作成する場合、さまざまな厚さの壁を持つことができますが、硬化中に収縮や変形が発生する可能性があります。どちらのプロセスでも、壁の厚さを 5mm 未満に保つことが最善です。
一体型金型から部品を損傷せずに突き出すのを妨げる突起やくぼみは、アンダーカットと見なされます。場合によっては、くぼんだ表面、溝、およびオーバーハング フィーチャにより、離型プロセスが困難になり、パーツが損傷する可能性があります。それ以外の場合は、これらの機能が害を及ぼすことはありません。これらの機能とコンポーネントをどのように設計し、方向付けたかによって異なります。
アンダーカット
アンダーカットの影響は、製造方法にも依存します。ウレタン キャスティング シリコンが提供する柔軟性のおかげで、アンダーカットが発生した場合でも、工具を曲げたり伸ばしたりするだけで、部品を解放することができます。はるかに柔軟性の低い射出成形で使用される金属工具については、同じことは言えません。製造業者は、アクションを追加したり、金型に穴やスロットを作成したり、金型が分離する軸に平行な機能を備えた金型を再設計して、部品を確実に排出できるようにする必要がある場合があります。これにより、より複雑で高価なツールが必要になります。

Fast Radius を使用した製造用の設計
ウレタン鋳造と射出成形のどちらを選択しても、DFM を設計プロセスに統合することで部品あたりのコストを削減し、時間を節約できます。設計時に製造方法、公差、肉厚、およびアンダーカットを考慮に入れることで、パーツのミスアライメントを最小限に抑え、生産プロセスを最適化できます。
どの製造プロセスを選択しても、Fast Radius は、最終製品の品質とコストに満足できるように製造可能性を考慮して設計するのに役立ちます。当社の専門家チームは、適切な公差と壁の厚さについてアドバイスしたり、設計に最適なアンダーカットの回避策を決定するのに役立ちます。今すぐお問い合わせください。
産業技術