ウレタン キャスティングの設計に関する 5 つのヒント
ウレタン キャスティングは、3D プリントされたマスター パターンとシリコン型を使用して最終用途のプラスチック パーツを作成する、用途の広い伝統的な製造プロセスです。ウレタンキャストの工程では、マスターパターンを密閉した箱の中に入れ、液状シリコーンで覆い、硬化させます。シリコーンが硬化した後、メーカーはそれを半分にカットしてマスター パターンをリリースします。この時点で、キャスト ウレタン型を使用する準備が整います。
カスタム キャスト ウレタン パーツを作成するには、エンジニアはウレタン キャスト樹脂 (通常、射出成形で使用されるプラスチックの物理的特性を模倣できるポリウレタン材料) を金型に流し込み、オーブンで硬化させます。通常、最終部分では、後処理はほとんど必要ありません。
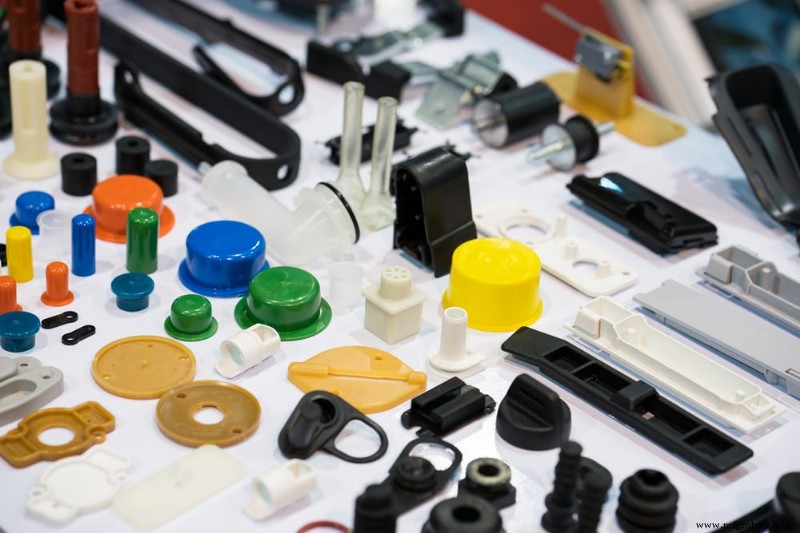
ハード ツーリングよりも安価で時間もかからないウレタン キャスティングは、ラピッド プロトタイピングや複雑なビルドの少量から中量生産に最適です。この製造プロセスを最大限に活用するには、製品チームは製造可能性を考慮して設計し、早い段階で金型設計を最適化して、製造プロセスを合理化し、コストを低く抑える必要があります。クリーンで機能的なカスタム キャスト ウレタン パーツを作成するための 5 つの重要な設計のヒントを次に示します。
ウレタン鋳造の設計に関する 5 つのヒント
1.壁の厚さを均一にする
多くのエンジニアは、射出成形よりもウレタン キャスティングを好みます。前者のプロセスでは肉厚のばらつきが大きくなるからです。ただし、特定のウレタン金型設計が均一な壁を備えていることを確認することは依然として重要です。均一な壁は、硬化中の変形のリスクを減らし、金型が完全かつ正確に充填されるようにし、その他の設計上の問題を軽減します。
最小肉厚は 0.040 インチ (1 mm) が推奨されますが、小さい部品では肉厚が 0.020 インチ (0.5 mm) になる場合もあります。より大きなパーツの場合、壁が適切なサポートを提供できるように、パーツのサイズに比例して壁の厚さを常に増加させる必要があります。
2.収縮の説明
ウレタンモールドの設計では、厚さの異なる 2 つの壁が交差すると、収縮が発生する可能性があります。厚い壁は薄い壁よりも固化が遅いため、公称壁で壁が取り付けられている領域は、突起 (リブまたはボス) が収縮するにつれて収縮します。これにより、公称壁にくぼんだ領域が生じます。収縮を最小限に抑え、沈み込みを防ぐために、エンジニアは、リブの厚さが、リブが取り付けられている壁の 50% から 60% の間にあることを確認する必要があります。
それでも、ウレタンモールドの設計上の欠陥以外の理由で、ウレタン鋳造部品が収縮することがあります。ウレタン キャスト パーツの最終的な寸法は、マスター パターンと金型の精度、パーツの形状、およびウレタン キャスト マテリアルに依存します。 0.15% の収縮率は許容範囲と見なされますが、収縮率がこのしきい値を超える場合、エンジニアはウレタン金型の設計を再検討する必要があります。
3.肋骨を使う
ウレタンモールドのデザインにリブを追加することで、厚みを増やさずに端部の強度と剛性を高めることができます。リブを適切に使用するには、エンジニアは次のガイドラインに従う必要があります:
身長
リブが長いほど補強は強化されますが、リブが長いと成形が困難になる可能性があります。このため、リブはその厚さの 3 倍の高さを超えてはなりません。高さの問題を完全に回避するために、エンジニアは 1 つの長いリブの代わりに複数の短いリブを使用して、パーツの剛性を高めることができます。
幅
パーツの交点におけるリブの幅は、パーツの肉厚の 40% ~ 60% である必要があります。フィレット半径が設計に含まれる場合、成形品の肉厚の 25% 以上にする必要があります。これらのパラメータは、肋骨を可能な限り強くするのに役立ちます.
ドラフト角度
エンジニアは、沈み込みの可能性を減らすように設計されたリブを作成する必要があります。各サイドのドラフト角度は 0.25 ~ 0.5 度で、各サイドのドラフト角度は等しくなければなりません。テクスチャ サーフェスの場合、テクスチャの深さ 0.025 (0.001 インチ) ごとに 1.0 度のドラフトを追加します。
間隔
エンジニアは、パーツの重量をすべてのリブに均等に分散させるために、連続したリブを互いに少なくとも 2 倍の厚さで離して設定する必要があります。
オリエンテーション
リブの向きは、パーツが応力を受ける方法と場所を決定するため、エンジニアは、パーツの曲げ剛性を最大化する方法でリブを配置するように注意する必要があります。リブが間違った位置に配置されていると、パーツの強度にプラスの影響がありません。
製品チームは、リブを扱う際に交差と沈みにも注意する必要があります。リブがパーツと交差するポイントでは、リブが重いとパーツがくぼむ可能性があります。エンジニアは、リブの交差部分での沈み込みを回避するために、フィレットを使用して部品の表面の応力を緩和し、部品の反対側の沈みを減らすことができます。フィレットの半径は、パーツの肉厚の少なくとも 4 分の 1 にする必要があります。さらに、パーツのコアリングまたは軽量化により、使用する材料の量が減り、パーツ全体で均一な肉厚を維持するのに役立ちます。
リブはエンド パーツのパフォーマンスを劇的に向上させることができますが、エンジニアと製品チームは夢中になってはいけません。リブは、パーツに追加の補強が必要な場合にのみ役立ちます。そうでない場合、リブは不適切に配置されることが多く、パーツの強度や剛性をほとんど向上させません。また、不要なリブは部品の重量と価格を増加させ、成形上の問題を引き起こし、材料の無駄につながります。エンジニアと製品チームは、ウレタン金型の設計にリブが必要かどうかを判断する際に、これらの考慮事項を念頭に置く必要があります。
4.下書きとアンダーカットを考慮する
液状シリコーンはどんな型でも成形できるため、ウレタン鋳造では抜き勾配やアンダーカットは問題になりません。ただし、エンジニアがウレタン鋳造を使用してプロトタイプを作成し、最終的に射出成形などの別のプロセスを使用して製造する場合は、最終用途の生産を意図した設計を作成する必要があります。これには、ドラフトとアンダーカットの組み込みが含まれる場合があります。ゼロ ドラフト フィーチャが長いと、金型からパーツを取り出すときにパーツが破損するリスクがわずかに伴うため、特に大規模な生産工程では、わずかな角度が役立つ場合があります。
5.文字とロゴの間に十分なスペースを含める
ウレタン キャスティングを使用すると、デザイナーは、高品質の凸状または凹状の文字やロゴをカスタム キャスト ウレタン パーツに簡単に成形できます。文字をできるだけ美しく読みやすくするために、デザイナーは、高さまたはフィーチャの深さ、フィーチャの幅、フィーチャの半径、およびフィーチャ間のスペースを念頭に置く必要があります。
製品チームは機能間を少なくとも 0.050 インチ離す必要がありますが、これは設計の詳細によって異なります。すべての半径は少なくともフィーチャの高さの半分に等しい必要がありますが、半径が大きいほどさらに優れています。最後に、すべてのロゴまたは文字の幅は高さの 2 倍にする必要があります。
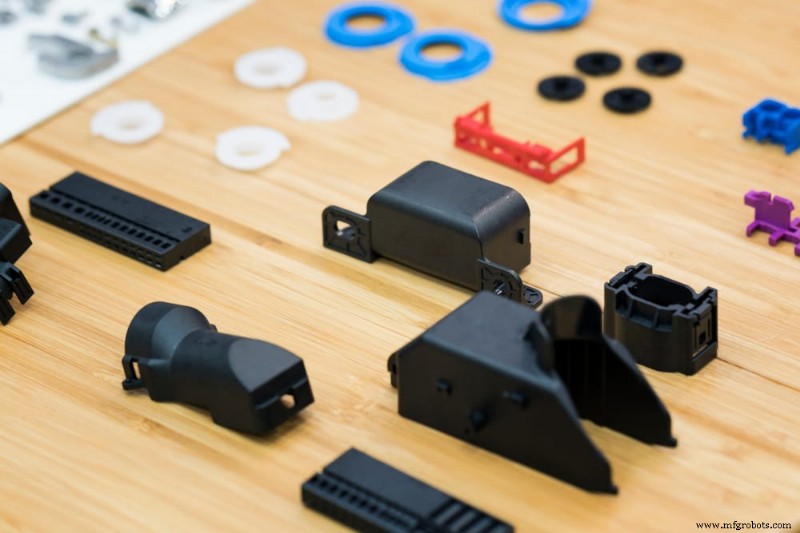
ウレタン キャスト パーツの最適化
ウレタン鋳造と製造可能性の設計により、いくつかの小さな設計変更が大いに役立ちます。エンジニアと設計者は、均一な肉厚を維持し、収縮を考慮し、リブを効果的に使用していることを確認する必要があります。製品チームは、最終用途の生産を目的としたデザインを作成し、文字とロゴの間に十分なスペースを確保して美学を向上させることで、製造可能性をさらに最適化できます。
Fast Radius のような経験豊富な製造パートナーは、製品チームが製造可能性の設計を簡素化するのに役立ちます。私たちは、かつては不可能と考えられていた製品の開発に情熱を傾けており、最新のデジタル設計技術についていくことを常に心がけています。
画期的なアプリケーションの開発や既存のウレタン金型設計の最適化を目指す製品チームは、製造プロセス全体にわたる設計チームの長年の経験から恩恵を受けることができます。カスタム キャスト ウレタン パーツの作成を開始するには、今すぐお問い合わせください。
ウレタン キャスティングに関する設計のヒントと情報については、Fast Radius ラーニング センターの関連記事を参照してください。
Fast Radius でパーツを作成する準備はできましたか?
見積もりを開始する産業技術