切削液のさまざまな切削プロセス要件
金属切削液は切削液と略されます。切削プロセスにおける潤滑効果により、すくい面と切りくずの間の摩擦、および逃げ面と機械加工面との間の摩擦が減少し、潤滑膜の一部が形成されるため、切削力、摩擦、消費電力が減少し、表面温度と工具が低下します。工具と被削材の摩擦部分の摩耗を防ぎ、被削材の切削性能を向上させます。
切削プロセスが異なれば、切削液の要件も異なります。適切な切削液を正しく選択することは、ワークピースの品質にとって非常に重要です。
R まあ T うねる
荒削りでは、取り代が大きいため、切り込みや送りが大きく、切削抵抗が大きく、切削熱が多く、工具の摩耗も深刻です。主に冷却に使用し、特定の洗浄、潤滑、防錆に使用する必要があります。効果的な水性切削液は、切削熱を時間内に除去し、切削温度を下げ、工具の耐久性を向上させます。一般的には、極圧エマルジョンを使用する方が良いです。優れた冷却性能に加えて、極圧エマルジョンには優れた極圧潤滑性もあります。水性切削油剤を使用する場合は、工作機械のガイドレール面のメンテナンスに注意してください。作業台で切削液を乾かし、潤滑剤を塗布してから作業を終了してください。
F 仕上げ T うねる
旋削仕上げ時の切削代は少なく、切削深さは通常0.05~0.8mm程度で、送り速度も小さい。ワークの精度と表面粗さを確保する必要があります。切削抵抗が低く、仕上げ旋削中の温度が低いため、摩擦係数が低く、潤滑性能に優れた切削油剤を使用する必要があります。一般に、高濃度 (質量分率 10% 以上) のエマルションと、油性添加剤を含む切削油剤を使用する必要があります。細目ねじ切りなどの高精度が要求される旋削では、菜種油、大豆油、またはその他の製品を潤滑油として使用して、精度要件を満たす必要があります。前述のように、植物油は安定性が悪く酸化しやすいため、精密切削油として(質量分率)JQ-1精密切削油剤15%、L-AN32全損系油85%を使用している工場もあり、好成績を収めています。
退屈
ボーリングのメカニズムは旋削と同じですが、内部穴加工であり、切削量と切削速度は大きくありませんが、放熱条件が悪く、切削液としてエマルジョンを使用でき、流動性があります。該当する場合は、切削液の圧力を適切に高める必要があります。
ミリング
フライス加工は間欠切削です。各刃の切り込み深さは刻々と変化し、振動や一定の衝撃を受けやすいため、フライス加工の条件は旋削よりも悪くなります。高速フラットフライス加工または高速エンドミル加工に高速度鋼工具を使用する場合、極圧エマルジョンなどの良好な冷却特性と特定の潤滑特性を備えた切削液が必要です。低速フライス加工では、精密切削油や不活性極圧切削油など、潤滑性の良い切削油が求められます。ステンレス鋼や耐熱合金鋼には、硫黄や塩素の極圧添加剤を含む切削油が使用できます。
リーミング
リーマ加工は穴の仕上げ加工であり、高い精度が要求されます。リーマ加工は低速で小送りの切削です。これは主に、工具と穴の壁が絞られて切削され、切りくずの破片が溝に留まりやすく、刃の端に付着しやすく、絞り効果に影響を与えるためです。土地の。加工精度と表面粗さを破壊し、切削トルクを増加させるだけでなく、構成刃先を生成し、工具の摩耗を増加させます。リーマ加工は基本的に境界潤滑の状態に属します。一般的には、高濃度の極圧エマルジョンや極圧切削油など、潤滑性と流動性に優れたものを使用すると良好な結果が得られます。ステンレス鋼や耐熱鋼には、極圧の高い複合切削油剤が使用できます。深穴リーマ加工では、潤滑性能に優れた深穴加工用切削油が技術的要求を満たすことができます。
ブローチング
ブローチは、ブレードの歯に合わせて軸方向に多数の歯が配列された加工工具です。ブローチ加工の特徴は、複雑な形状のワークを高精度に加工できることです。ブローチは貴重な工具であるため、工具の耐久性が生産コストに大きく影響します。また、ブローチ加工は仕上げ加工であり、ワークの表面粗さに厳しい要件があります。ブローチ加工の場合、切削抵抗が大きく、切りくず排出が難しく、冷却状態が悪く、被削材の表面に傷が付きやすいため、切削油の潤滑性と切りくず排出性が求められます。中国には硫黄極圧添加剤を含む特別なブローチングオイルがあります.
ステンレス鋼、耐熱合金のブローチ加工の場合、次の式(質量分率)が使用できます:JQ-2極圧潤滑剤20%、塩素化パラフィン15%、ベンゼン80使用1%、L-ANN22全損システム油64 %.
D リリング
一般的なツイストドリルでの穴あけは荒加工です。穴あけ加工時の切りくずの排出が難しく、切削熱が逃げにくいため、ブレード焼鈍が発生しやすく、ドリルの寿命や加工能率に影響を与えます。性能の良い切削液を選べば、ドリルの寿命を数倍以上延ばすことができ、生産効率も大幅に向上させることができます。一般に、極圧エマルジョンまたは極圧合成切削油剤を使用できます。極圧合成切削油剤は表面張力が低く、浸透性に優れています。ドリルを時間内に冷却することができ、工具の寿命を延ばし、加工効率を向上させるのに非常に効果的です。ステンレス鋼や耐熱合金などの難削材には、低粘度の極圧切削油を使用できます。
スレッド 機械加工
ねじ切りの際、工具は被削材にくさび状に接触し、刃先は三方を被削材に囲まれます。切削トルクが大きく、切りくずの排出が難しい。熱はチップによって時間内に奪われることはできません。工具が摩耗しやすく、切削屑が詰まりやすく振動が発生しやすい。特にねじ切りやタッピングでは切削条件が厳しくなり、チッピングやタップ折れが発生することもあります。
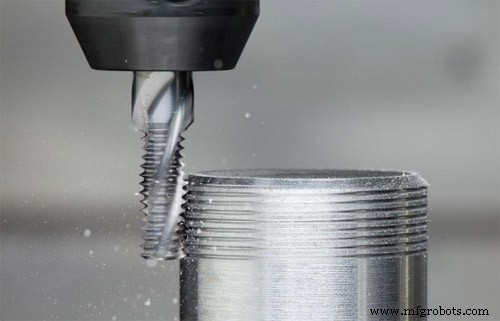
切削液には、工具の摩擦抵抗を減らし、工具寿命を延ばすために、より低い摩擦係数とより高い極圧が同時に要求されます。一般的には、油性剤と極圧剤の両方を含む複合切削油剤を選択する必要があります。さらに、ねじをタッピングするときは、切削液の透過性が非常に重要です。切削液が刃先に間に合うように浸透できるかどうかは、タップの耐久性に大きく影響します。切削液の透過性は粘度に関係しています。粘度の低いオイルは浸透性が良いです。必要に応じて、透過性を向上させるために少量の軽油または灯油を追加できます。止まり穴をタッピングする場合、切削油が穴に入りにくい場合があります。この場合、粘度が高く付着力の強い切削油剤がより効果的です。
以下は、タッピング用の切削液の式 (質量分率) です。
- 硫酸化脂肪油 10%、塩素化パラフィン 10%、脂肪油 8%、L-AN15 総損失油 72%、鋼および合金鋼タッピング スレッドに適しています。
- JQ-2 極圧潤滑剤 20%、JQ-1 精密切削潤滑剤 10%、L-AN15 総損失システム オイル 70%、鋼および合金鋼のタッピングに適しています。
- JQ-2 極圧潤滑油 15%、ディーゼル エンジン オイル 20%、L-AN15 トータル ロス システム オイル 65%、アルミニウムおよびアルミニウム合金のタッピングに適しています。
- JQ-2 極圧潤滑剤 30%、塩素化パラフィン 10%、脂肪油 10%、L-AN32 トータルロス システム オイル 50%、ステンレス鋼および止まり穴のタッピングに適しています。
- 油20%+水80%の極圧乳化で、鋼製標準部品のねじ加工に適しています。
研磨
研削加工により、高い寸法精度と低い面粗さが得られます。研削時の研削速度が速く、発熱が大きく、研削温度が800~1000℃以上になることもあります。熱応力によるワークの表面ヤケや表面クラック、部品変形を起こしやすい。砥石は不動態を摩耗し、研削粒子が脱落し、砥粒や砥石の粉が部品の表面に飛び散りやすくなり、加工精度や表面粗さに影響を与えます。硬くて塑性の材料を加工する場合、砥石の作用面の隙間に砥石が詰まりやすい、または砥石の表面で砥石と加工金属が融着し、砥石がはがれやすくなります。粉砕能力を失います。したがって、研削温度を下げ、研削屑や砥石粉を洗い流し、研削比やワークの表面品質を向上させるためには、冷却性や洗浄性の良い切削液を使用する必要があり、ある程度の潤滑性と防錆性。
1. 通常の研磨:
防錆エマルジョンまたはソーダ水と合成切削液(質量分率)を使用できます。たとえば、防錆エマルジョン2%、亜硝酸ナトリウム0.5%、炭酸ナトリウム0.2%、水97.3%です。 0.8% 亜硝酸ナトリウム、0.3% 炭酸ナトリウム、0.5% グリセリン、98.6% 水; 3%-4% の防錆エマルジョンまたは化学合成液を直接使用してください。
高い精度が要求される精密研削では、H-1 ファイン研削液を使用すると、工作物の加工精度と研削効率が大幅に向上し、使用濃度は 4 ~ 5% です。
2. 高速研削:
通常、砥石速度が50m/sを超える研削を高速研削と呼びます。砥石の線速度が上がると、研削温度が大幅に上昇します。テストによると、砥石線速度が 60m/s の場合の研削温度 (ワークの平均温度) は、30m/s の場合よりも約 50 ~ 70% 高くなります。砥石線速度が 80m/s の場合、研削温度は 60m/s の場合よりも高くなります。 15 ~ 20% 高くなります。砥石車の線速度を上げた後、単位時間に研削に関与する砥粒の数が増加し、摩擦が強まり、エネルギー消費も増加し、ワークピースの表面温度が上昇し、増加します表面に火傷やひび割れの可能性があります。効率的な冷却性能を持つクーラントを使用して解決します。したがって、高速研削では通常の研削液は使用できず、浸透性と冷却性の良い高速研削液を使用する必要があります。たとえば、GMY 高速研削液は、線速 60m/s の高速研削プロセスに対応できます。
3. パワーグラインディング:
高度な高能率研削加工です。例えば、プランジカットの高速強力研削では、線速60m/sの砥石を3.5~6mm/minの送り速度で放射状に切削します。速度は 20 ~ 40mm3/mm.s にもなります。このとき、砥石の砥粒と工作物との摩擦は非常に激しくなります。高圧大流量の冷却条件でも、摩擦部のワーク表層温度範囲は700~1000℃です。いいえ、研削加工はできません。押し込み研削では、エマルジョンと比較して、総研削量が 35% 増加し、研削比が 30 ~ 50% 増加し、通常の研削時間が約 40% 長くなります。電力損失は約 40% です。そのため、クーラントの性能が強研削時の研削効果に大きく影響します。現在、国産の強力研削液には、QM高速強力研削液とHMスローフィード強力研削液があります。
4. ダイヤモンド砥石の研削:
硬質合金、セラミック、ガラスなど硬度の高い材料の研削に使用されます。粗く、細かく粉砕することができます。研削された表面は一般的にクラックやギャップを生成せず、より良い低表面粗さを実現できます。研削中の過剰な発熱と研削砥石の早期摩耗を防ぎ、表面粗さを小さくするために、継続的かつ十分な冷却が必要です。ワークピースの硬度が高いため、研削液は主に冷却およびクリーニング性能を備えており、研削砥石を鋭く保つ必要があります。研削液の摩擦係数が低すぎると、研削効率が低下し、表面が焼ける原因になります。研削液には無機塩系の化学合成液を使用しています。ポリエチレングリコールを微量研削時に潤滑剤として添加することで、ワークの表面加工品質を向上させることができます。加工精度の高い部品には、潤滑性に優れた低粘度の油性研削液を使用できます。
5. ねじ、歯車、ねじの研削:
このタイプの研削では、研削後の加工面の品質と寸法精度に特に注意が払われます。一般的には、極圧添加剤を含む研削油を使用することをお勧めします。このタイプの油性研削液は、潤滑性能が優れているため、研削熱を低減でき、極圧添加剤が被削材と反応して、せん断強度の低い硫化鉄皮膜と塩化鉄皮膜を生成できます。砥粒の切れ刃の摩耗を減らし、研削をスムーズにします。冷却性と洗浄性を高め、火災の安全性を確保するために、低粘度で引火点の高い研削油を選択する必要があります。
製造プロセス