AFMチップベースの動的耕起リソグラフィーを使用したポリマー薄膜上での高スループットのナノスケールピットの製造
要約
原子間力顕微鏡(AFM)チップベースの動的耕起リソグラフィー(DPL)アプローチを使用して、高スループットでナノスケールピットを製造できることを示します。この方法は、隣接するピットの分離距離の原因となるタッピングモードでサンプル表面を比較的高速で引っ掻くことに依存しています。引っかき試験は、ダイヤモンドライクカーボンコーティングチップを使用して、ポリ(メチルメタクリレート)(PMMA)薄膜で実行されます。結果は、100μm/ sが引っかき速度の臨界値であることを示しています。引っかき速度が100μm/ sを超えると、ピット構造が生成される可能性があります。対照的に、ナノグルーブは臨界値よりも遅い速度で形成することができます。チップとサンプルの1つの相互作用で高周波負荷と低エネルギー散逸が適用されたガラス状態ポリマーの分子鎖を切断することは困難であるため、1つのピットで65〜80回の貫通を達成する必要があります。続いて、ピットの成形プロセスが詳細に分析されます。これには、弾性変形、塑性変形、およびパイルアップを乗り越えるという3つのフェーズが含まれます。特に、この提案された方法を使用すると、1秒で4800〜5800のピットを取得できます。ピットを効率的に製造するためのこの提案された方法の可能性を完全に決定する実験と理論的分析の両方が提示されます。
背景
ナノテクノロジーの最近の急速な発展は、ナノ電気機械システム、ナノセンサー、ナノフォトニクスなどのさまざまな分野でのナノ構造の応用にますます注目を集めています。特に、一次元ナノ構造として定義されるナノドットは、高密度貯蔵および量子ドットの調製の分野で広く利用されています[1]。ただし、ナノドットの効率的な製造は依然として大きな課題に直面しています。多くの学者は、多種多様な材料上にナノドットを製造するためのさまざまな方法を提案しています。その中で、化学合成法は、ほとんどの特性検出およびナノスケールデバイス用のナノドットを取得するために広く使用されています[2]。ただし、この方法を使用してナノドットの寸法と空間分布を決定することは困難です。これらの結果、後続のプロセスでの位置特定と操作に必要な労力が増えます。したがって、多くの学者は、集束イオンビームリソグラフィー[3]、電子ビームリソグラフィー[4]、ナノインプリントリソグラフィー[5]など、数ナノメートルの寸法のナノドット構造を取得するためのより制御可能な方法を探求することにリソースを費やしてきました。ただし、複雑さ、厳格な環境要件、および/または高コストは、これらの手法の適用を大幅に妨げます。
原子間力顕微鏡(AFM)は1986年に発明されて以来、高精度の表面プロファイラーとして一般的に利用されてきました[6]。 AFMチップとサンプル間の相互作用力が数百ナノニュートンまたは数百マイクロニュートンなどの比較的大きな値に拡大されると、小さな切削工具と同様に、サンプル材料を鋭利なチップで塑性的に除去できます[7 ]。化学的および熱的エネルギーも、サンプル材料の除去を支援するために、局所酸化[8]またはサンプルの加熱[9]を通じてAFMシステムに導入されています。したがって、既存のAFMチップベースのナノリソグラフィー(TBN)法の範囲を拡張するために、いくつかの新しい製造方法が生まれます。すべてのTBN手法の中で、機械的除去アプローチが最も簡単で柔軟性があります[10]。この方法は、最初にさまざまな材料の押し込みとその後の引っかき動作で構成され、先端と材料の相互作用は、金属[11]、半導体[12、13]、ポリマー[14]などの材料の種類に強く依存します。ナノスケールでチップと材料の相互作用を正確に制御することにより、ナノドット、ナノグルーブ、さらには3Dナノ構造などの複雑で高精度のナノ構造が正常に製造されています。特に、一部の学者は、ナノドット構造を得るために、半導体材料の表面にAFMチップベースのナノインデンテーションプロセスを実行しました[15、16]。彼らの研究では、ナノインデンテーションによって引き起こされる結晶欠陥は、InAsナノ構造の核形成サイトであると判断されています。ただし、半導体材料の硬度が比較的高いと、チップが著しく摩耗する可能性があります。したがって、一部の研究者は、最初にナノドット構造を製造するために、ポリマー薄膜レジストなどのより柔らかい材料でナノインデンテーションプロセスを実行することを提案しました。これらのナノドット構造は、反応性イオンエッチング(RIE)またはウェットエッチングプロセスによって半導体材料に転写することができます[17]。硬度が低く、厚みが非常に薄いため、比較的小さな通常の負荷でレジスト層を貫通することができます。一部の学者は、ポリカーボネート表面にナノドットアレイを取得するための2段階のスクラッチアプローチを提案しています[18]。この方法は、AFMチップベースのフォースコンスタントスクラッチプロセスによって形成された材料の波紋に依存しています。ただし、隣接するナノドット間の間隔距離はAFMチップの形状にのみ依存し、ナノドットの形成メカニズムは不明なままです。
一方、低スループットは、AFMチップベースのナノファブリケーション法の開発を妨げる重要な要因です。 AFMチップベースのナノインデンテーションプロセスは、大規模なナノドット構造を取得するのに時間がかかることが実証されています[19]。この問題を解決するために、Vettiger等。超高密度加工能力を実現するために並列に動作するマイクロカンチレバーの大規模なアレイを採用する「Millipede」の概念を提示しました[20]。大面積の引っかきプロセス後の深刻なチップ摩耗を考慮して、一部の学者は、チップとサンプルの相互作用力を減らし、チップ摩耗を減らすための新しい断続的接触モード操作を提案しました[21、22]。ただし、このアプローチで使用されるマイクロカンチレバーの大規模なアレイには、複雑な設計および製造プロセスが必要であり、サンプルとの接触を保証するために1つのプローブのすべてのチップの位置を調整するための面倒なプロセスが必要です。そのため、一部の研究者は、高速加工機能を促進するために、ハードウェアとソフトウェアを含む商用AFMシステムを変更しました[23、24、25]。これらの方法では、1つのカンチレバーを備えたチップが使用されました。ただし、これらのアプローチを効率的に使用して製造できるのはナノグルーブのみであり、高速で引っ掻くことも深刻なチップ摩耗につながる可能性があります。 AFMチップによる静的処理に加えて、AFMチップベースの動的耕起リソグラフィー(DPL)も最近ますます注目を集めています。このプロセスは、AFMシステムのタッピングモードで実行されます。カンチレバーの駆動振幅を大きくすると、AFMチップがサンプル表面を貫通して機械加工プロセスを実現できます[26、27、28]。 DPLアプローチではチップとサンプルが断続的に接触するため、参考文献で提案されている方法と同様に、チップの摩耗を減らすことができます。 [21、22]。 DPL法で得られる加工深さは、通常、数ナノメートルのオーダーであり、ポリマー薄膜レジストや二次元材料などの薄膜上にナノ構造を製造するのに適しています[29]。さらに、DPL法では、AFMチップのカンチレバーを駆動して数千ヘルツで振動させることができるため、チップがサンプル表面と短時間で何度も相互作用することになります。したがって、DPL法は、薄膜サンプル表面にナノスケールのピット構造を効率的に製造するための潜在的なアプローチとなる可能性があります。
この研究では、高速スキャンナノリソグラフィー(FSN)法が、DPL製造アプローチに基づいており、市販のAFMシステムを採用しています。図1aは、ダイヤモンドライクカーボンコーティングチップを使用したナノスクラッチプロセスの概略図を示しています。これは、シリコン基板上のポリ(メチルメタクリレート)(PMMA)薄膜と接触しているチップの図を示しています。カンチレバーはその共振周波数の近くで駆動され、チップとサンプル表面の間に断続的な接触を生成します。チップの駆動振幅は、制御システム(AM-AFM)によって一定値に維持されます。 AFMシステムに搭載されているNanomanモジュールは、すべての機械加工プロセスに使用され、引っかき方向はカンチレバーの長軸に平行になるように選択されます。機械加工されたナノ構造に対する引っかき速度の影響が研究されています。さらに、ピット構造の形成メカニズムも調べられます。
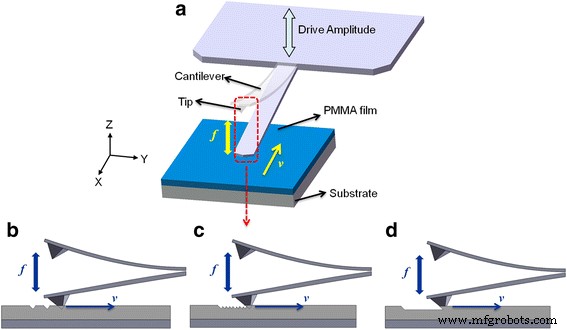
a FSN法によるPMMAフィルム表面のラインスクラッチプロセスの概略図。カンチレバーはその共振周波数 f で振動しています 垂直方向に。引っかき速度 v 高速スキャン方向に沿って変更されます。さまざまな引っかき速度範囲が示されています: b 高い引っかき速度、 c 中程度の引っかき速度、および d 引っかき速度が遅い
メソッド
PMMA溶液の濃度は1.25wt%で、分子量Mw =120,000のPMMA粉末をクロロベンゼンに溶解して調製します。 PMMAフィルムは、単結晶Si基板上で溶液を回転させることによって調製されます。この基板は、アセトンとアルコールの連続超音波浴で約10分間洗浄されます。数十ナノメートルの厚さのフィルムを生成するための実験では、回転速度は6000rpmになるように選択されています。コーティングプロセスに続いて、PMMAフィルムはPMMAのガラス転移温度に近い125°Cで30分間ポストベークされます。
実験は、市販のAFM(Dimension Icon; Bruker Corporation、USA)を使用して実行されます。シリコンチップは、メーカー(TESPD; Bruker Corporation、USA)から提供された、42 N / mの公称ばね定数と320kHzの共振周波数で選択されています。カンチレバーの先端側は、先端の寿命を延ばすためにダイヤモンドライクカーボン(DLC)コーティングで硬化されています。 PMMA表面のナノ構造の測定は、スキャンレートが1 Hz、スキャンラインが256のタッピングモードに設定されています。別のプローブを使用する場合は、カンチレバーシステムを調整する必要があります。この調査では、設定値は約300mVに調整されています。画像は、BrukerCompanyが提供するNanoscopeAnalysisソフトウェアを使用した一次平坦化によって処理されます。
AFMシステムに装備されたNanomanモジュールは、この研究の引っかきプロセスに利用されます。これは、サンプル表面に長方形や円などの望ましい構造を実現するための先端の軌道を設計するために広く採用されています。サーフェスを変更するには、チップの駆動振幅値を V に増やす必要があります。 w (書き込み)、チップとPMMAフィルム間の相互作用が促進され、チップがサンプル表面を貫通することが保証されます。スクラッチプロセスの後、チップの駆動振幅値はすぐに V に急落します。 r (読み取り)カンチレバーを交換せずに。静的耕起リソグラフィー法と比較して、DPLではチップの摩耗が非常に小さいことが証明されているため、無視することができます。プローブの変更やナノ構造の位置の検索を回避することにより、このinsituイメージング法はスクラッチプロセスの効率を向上させることができます。すべての実験は室温で行われます。
結果と考察
AFM PZTの速度制限を考慮して、実験テストでは0.1〜1000μm / sの範囲の引っかき速度が選択されています。図1は、3つの速度範囲を含むナノマシニングプロセスの概略図を示しています。図1bに示すように、比較的大きな速度(1秒あたり約数百マイクロメートル)で引っ掻くと、別々のピットが形成される可能性があります。スクラッチ速度が中程度の値(約100μm/ s)に低下すると、図1cに示すように、ピットが互いに重なり合う可能性があります。図1dに示すように、引っかき速度が比較的小さい値(1秒あたり数十マイクロメートル)に達すると、ピットはナノグルーブに変換されます。この結果は、2つの製造されたピット間の距離が、製造されたナノパターンに大きな影響を与える引っかき速度に依存していることを示しています。
この調査では、図2aに示すように、4つの典型的な引っかき方向が選択されています。 V 1 および V 3 カンチレバーの長軸に沿った引っかき傷を表します。 V 2 および V 4 カンチレバーの長軸に垂直な引っかき傷として定義されます。先端の軌道は、AFMPZTを制御することによって得られます。図3は、さまざまな引っかき速度で製造された正方形のナノ構造のAFM画像と、 V の方向で引っかかれたナノ構造の対応する断面を示しています。 1 、カンチレバーの共振周波数が380kHzの場合。図3aに示すように、200μm/ sの比較的大きな引っかき速度で、連続したピットを形成できます。事前に設定された4つの引っかき方向の場合、引っかき速度が2つの方向の転換点でスライドして離れても、1秒よりはるかに短い時間でピットが形成されます。中程度の引っかき速度(100μm/ s)では、図3bに示すように、加工経路に沿って明らかなピットは見られず、変動するナノ構造が形成されます。隣接する2つの引っかき経路の交差点には、はるかに深い深さの1つのピットしか観察できません。これは、次のように説明できます。隣接する2つのスクラッチパス間の変換期間中、スクラッチ速度は0まで遅くなり、スクラッチの場合よりもチップがサンプル表面に何度も押し込まれる可能性があります。これが、より大きな深さを生成する理由と考えられます。ピットの。 100μm/ sの引っかき速度は、PMMA薄膜上に連続ピットを製造するための重要な値と見なすことができます。図3cは、引っかき速度が50μm/ sの機械加工されたナノグルーブを示しています。機械加工されたナノグルーブの断面から、ナノグルーブの底は比較的平坦であり、ナノグルーブの明らかな深さを形成することができることが観察できる。また、図3に示すように、PMMAフィルムの先端がすき込むため、スクラッチ時に欠けが発生することはなく、溝の片側または両側にパイルアップのみが形成されます。さらに、得られたナノ構造の異なる側面のプロファイルは、異なる方向で引っ掻くときに一貫性がなく、これは、非対称の先端を有する静的リソグラフィーを使用した結果と同様である。 SU-8やポリスチレン(PS)などの他のレジスト材料の場合、応力緩和係数が異なるため、引っかき速度のしきい値はPMMAフィルムのしきい値とは異なります。ただし、これらのしきい値は、この調査と同じアプローチに従うことにより、引っかき実験を通じて取得できます。
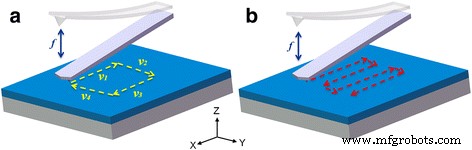
a 4つの典型的な引っかき方向( V 1 、 V 2 、 V 3 、および V 4 )この研究では、ナノマシニング製造に選択されています。 b 大面積パターンのフィードを使用した先端の軌道
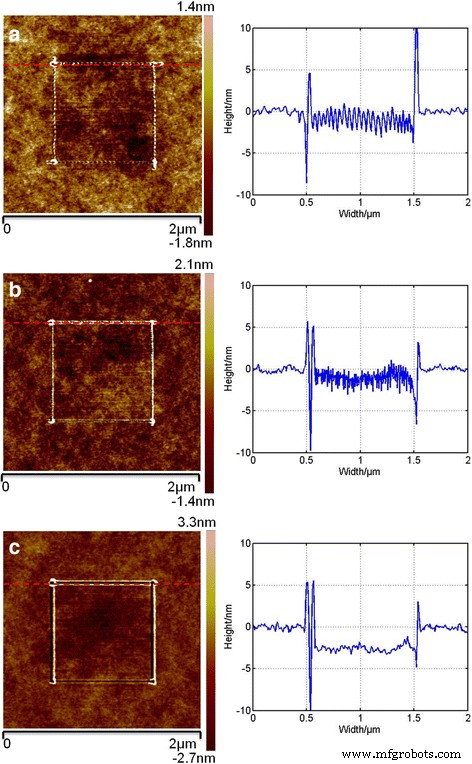
3種類のナノ構造のAFM画像と、スクラッチ速度が a の断面 200μm/ s、 b 100μm/ s、および c 50μm/秒
引っかき速度が100μm/ s未満の場合、高品質のナノグルーブを得ることができます。図4は、ナノグルーブの加工深さと、図2aに示すさまざまな引っかき方向での引っかき速度との関係を示しています。各ナノグルーブについて、実験的な深さは、5つの異なる場所での5つの深さの値の平均によって計算されます。すべての引っかき方向の引っかき距離は同じです。この調査では1μmです。すべての引っかき方向で引っかき速度を上げると、加工深さが減少することがわかります。考えられる理由の1つは、次のように説明できます。この調査で選択した1μmの引っかき距離の場合、100μm/ sと1μm/ sの引っかき速度でのプレス操作の数は、それぞれ3870と387,000になります。同じ引っかき距離の場合、AFMチップによる多数のプレス操作により、隣接するプレス操作間のオーバーラップの割合が比較的大きくなり、ナノグルーブの機械加工深さが大きくなる可能性があります。さらに、図4に示すように、引っかき速度が5μm/ s未満の場合、すべての方向に引っかかれたナノグルーブの深さは一定ですが、ナノグルーブの深さは V 方向に加工されています。 3 引っかき速度が5μm/ sを超える他の方向で得られる加工深さよりもはるかに小さくなります。さらに、方向 V で得られた加工深さのエラーバー 3 引っかき速度が5μm/ s未満の場合、他の場合よりもはるかに大きくなります。考えられる理由の1つは、次のように説明できます。この研究で使用された幾何学的AFMプローブは非対称であり、AFMチップのみがサンプル表面に接触することを保証するために使用される12°の典型的なカンチレバー傾斜によって引き起こされるプローブの傾きは、接触面積の違いをもたらす可能性があります先端とサンプル表面の間で、引っかき方向が異なります。引っかき速度が5μm/ s未満の場合、隣接するプレス操作の重なり合う領域は非常に大きくなります。したがって、チップとサンプル表面との接触面積も非常に大きくなります。したがって、加工深さに対する引っかき方向の影響は無視できます。ただし、先端表面に沿って形成されるパイルアップは、静的スクラッチプロセスと同様に、スクラッチ方向にも依存します。そのため、 V では安定してパイルアップを形成することができません。 3 引っかき方向。図4a、bに挿入された図は、それぞれ0.5および50μm/ sの引っかき速度で機械加工された典型的なナノグルーブの断面図です。 0.5μm/ sの引っかき速度で機械加工されたナノグルーブの断面から、 V で引っかいたときにナノグルーブの底が変動します。 3 方向。これにより、加工された深さのエラーバーが比較的大きくなる可能性があります。 5μm/ sを超える速度で引っ掻く場合、隣接するプレス操作とのオーバーラップ領域が小さくなります。したがって、引っかき方向が重要な役割を果たし、 V で得られる機械加工の深さが比較的小さくなる可能性があります。 3 引っかき方向。
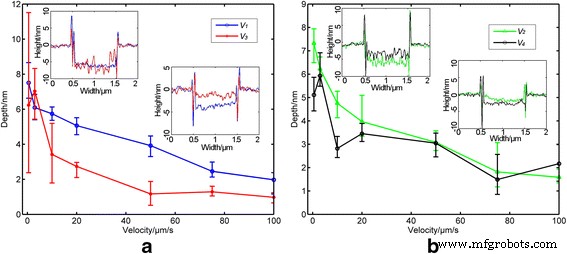
典型的な引っかき方向の引っかき速度に対する溝の深さの依存性: a V 1 および V 3 、カンチレバーの長軸に平行。 b V 2 および V 4 、カンチレバーの長軸に垂直。挿入図は、0.5および50μm/ sの引っかき速度のナノグルーブの断面を示しています
PMMA薄膜は、一種の時間依存性で粘弾性のある材料です。したがって、AFMチップによって加えられる周期的な負荷は、サンプルのヤング率に影響を与える可能性があります。応力緩和係数 G の一般的な表現 G によって定義されます 1 および G 2 [30]:
$$ G \ left(\ omega \ right)={G} _1 \ left(\ omega \ right)+ {iG} _2 \ left(\ omega \ right)$$(1)$$ {G} _1 \ left (\ omega \ right)=\ left [{G} _r \ right] + {\ int} _ {-\ infty} ^ {+ \ infty} \ frac {H \ left(\ tau \ right){\ omega} ^ 2 {\ tau} ^ 2} {1 + {\ omega} ^ 2 {\ tau} ^ 2} d \ left(\ ln \ tau \ right)$$(2)$$ {G} _2 \ left( \ omega \ right)={\ int} _ {-\ infty} ^ {+ \ infty} \ frac {H \ left(\ tau \ right)\ omega \ tau} {1+ {\ omega} ^ 2 {\ tau} ^ 2} d \ left(\ ln \ tau \ right)$$(3)ここで G r は定数であり、ω 周波数に関連しています。 H (τ )は、応力緩和に寄与する緩和時間スペクトルであり、ln τ間の緩和時間と関係があります。 およびln τ + d (ln τ )。励起周波数をカンチレバーの共振周波数に近い値(387 kHz)に設定すると、モジュラスが高い値に達する可能性があります。上記の式を使用した計算から、PMMA薄膜は、高周波負荷が加えられたガラス状態として現れます[30]。タッピングモードは機械加工プロセス全体で使用されるため、スクラッチプロセス中のAFMチップとサンプル表面間の相互作用力とエネルギー散逸は比較的小さく、駆動振幅 V w / V r これらの加工条件では、PMMA薄膜のガラスのような特性と、AFMチップによる比較的小さな負荷荷重のため、ポリマー分子間の鎖は次のようになりません。プレス操作の1サイクルでサンプル表面を修正するために、破損した塑性変形を発生させることは困難です。ただし、チップには、プレス操作の最初の20〜30回の間にこれを達成するのに十分なエネルギー(> 1〜2 eV)があります[27]。したがって、ポリマー分子間の鎖結合を切断して、薄膜表面に塑性変形を発生させることができます。
隣接するプレス操作間の間隔距離は、引っかき速度とチップの振動周波数に関係する重要なパラメータです。 1つのピットラインの距離( L )は、1つのピットラインに使用される時間( t )で取得できます。 )引っかき速度( v )を掛けたもの )。 1つのピットラインでのAFMチップ振動の総数( N )は、カンチレバーの振動周波数( f )を使用して計算できます。 )時間( t )を掛けたもの )。したがって、隣接するプレス操作間の間隔距離( D )式で得ることができます。 4.
$$ D =\ frac {L} {N} =\ frac {v} {f} $$(4)この研究で選択したカンチレバーの固有振動数は約387kHzです。 AFMシステムの駆動周波数は、この値に近くなるように選択されます。上記のように、スクラッチ速度は、ピットの形成を保証するために200〜900μm / sの範囲で選択する必要があります。したがって、隣接するプレス操作間の間隔距離( D e )スクラッチプロセス中は、0.52〜2.33 nmの範囲で計算できます。これは、図5aの赤い曲線で示されています。図5aの青い曲線は、隣接するピット間の間隔距離( D )の関係を表しています。 )実験と引っかき速度から得られた。挿入されたAFM画像は、400、600、および800μm/ sの3つの典型的な引っかき速度で加工されたピットに対して取得されます。したがって、1つのピット形成のプレス操作の数は、 D の比率として計算できます。 D へ e 図5bに示されています。引っかき速度が一定の値であると仮定すると、引っかき長さ( L )から計算すると、PMMA薄膜上に1秒で4800〜5800のピットを生成できます。 )と間隔距離( D )。図5bから、1つのピット形成のプレス操作の数は、引っかき速度の増加とともに増加し、ほとんどが65〜80の範囲にあることがわかります。2つのピット間の平坦な地形を考慮すると、ピットでは、ポリマー鎖を切断してサンプル表面の塑性変形を生成するために必要なプレス操作は約32〜40であり、これはCappellaの結論と一致しています[27]。さらに、比較的小さな速度で引っ掻くと、ポリマー鎖を切断する方が簡単であると結論付けることができます。この研究では、カンチレバーのばね定数は同じです。より硬いカンチレバーをピットの製造に使用することができ、その結果、より大きな力とより高い共振周波数がもたらされます。より大きな力がサンプル表面に加えられると、エネルギー入力は各サイクルで増加します。したがって、より多くのエネルギー散逸がPMMAフィルムの変形に寄与します。したがって、1つのピットをサイクルを減らして生成できます。ただし、発振システムの共振周波数を上げると、サンプル表面とチップ間のプレス動作のサイクルが長くなります。さらに、実験で設定点が減少したため、エネルギー散逸は1サイクルで増加します。臨界速度は、設定点の値によって決定される場合があります。上記の議論に基づいて、速度のしきい値は、加えられた力、カンチレバーシステムの共振周波数、および将来の調査の焦点となる設定点によって影響を受ける可能性があります。
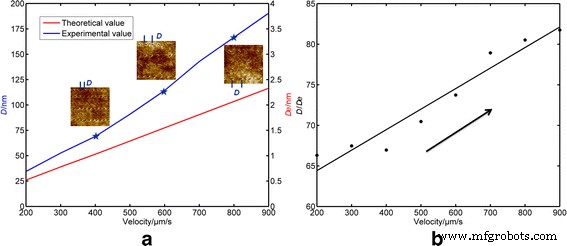
a D のバリエーション および D e 引っかき速度(200〜900μm / s);挿入図は、さまざまな引っかき速度の製造結果を示しています。 b D の比率 D へ e
ピット形成プロセスは、弾性変形、塑性変形、およびパイルアップを乗り越えるという3つのフェーズを含む図6に示されています。上記の説明によると、図6a、bからの距離を横切る先端の引っかき傷の間、プレス操作の数は、PMMA薄膜のポリマー鎖を破壊し、サンプル表面の塑性変形を生成するのに十分な数ではありません。振動チップは、最初の40〜50回の操作中にポリマーサンプルに徐々に浸透することが実証されています[27]。参考文献のインデントプロセスと比較。 [27]、横方向の速度で押すと、2つの隣接する貫通部の間に距離が生じる可能性があります。ただし、隣接する2つの貫通部間の距離(0.52〜2.33 nmの範囲)は、AFMチップの半径(約15 nm)よりもはるかに小さくなっています。したがって、この研究の状況は、インデントプロセスの場合と似ています。最初の30〜40回の貫通ではエネルギーが蓄積されないため、機械加工領域で明らかな塑性変形は見られません。この結果は、エネルギー散逸の主なメカニズムが引っかき傷の最初の段階での弾性変形であることを示しています。したがって、AFMチップは、図6a、bの間の期間、サンプル表面と継続的に接触してスライドします。図6cに示すように、AFMチップによって行われる貫通の数が臨界値(この研究では40回)に達すると、ポリマー鎖が壊れ始め、塑性変形が発生します。同時に、AFMチップの前面とサンプル材料の間の相互作用面で通常のせん断応力が発生します。したがって、AFMチップの前面の前にパイルアップを生成することができます。パイルアップに対する横方向の先端の動きに起因するひずみ(Δ)が発生します。これにより、ポリマーフィルム内に応力が発生し、亀裂の伝播によって解放される可能性があります[31]。ひずみエネルギー解放率 V s 次のように説明できます:[32]。
$$ {V} _s =E \ frac {h} {2} {\ left(\ frac {\ varDelta} {L} \ right)} ^ 2 $$(5)ここで E はポリマー材料のヤング率であり、 L は内部欠陥の長さです。 h サンプルの自由表面への総浸透深さを表します。表面エネルギー項 W 内部欠陥プロセスを制御します。これは、熱力学的平衡によるひずみエネルギー解放率に等しくなります。表面エネルギー項は、内部欠陥の伝播速度( v )に依存します。 L )、これは[33]によって与えられます。
$$ W ={W} _0 \ left(1+ \ alpha {v} _L ^ n \ right)$$(6)ここで v L d L に等しい / d t およびα はサンプル材料に関連する定数値です。 n 材料関連のパラメータでもあります。先端の頂点に加えられる接線方向の力は、ポリマー基板に蓄積された弾性エネルギーによって生成される可能性があります。これは、[32]:
として表すことができます。 $$ {F} _t =\ frac {Eah} {2} \ frac {\ varDelta} $$(7)ここで a チップとサンプル間の接触領域の半径を表します。プローブの剛性はサンプルの剛性よりもはるかに大きいため、形成された穴から材料を取り除くことができます[31]。ただし、マインドリンは、基板表面でチップが滑る可能性のある力の臨界値を定義しました[34]。臨界接線力( F tc )スライド運動の場合、[35,36,37,38]として表される接着力と通常の負荷の関数であると判断できます。
$$ {F} _ {tc} =\ mu \ left(P + 3 \ pi RW + \ sqrt {6 \ pi RW P + {\ left(3 \ pi RW \ right)} ^ 2} \ right)$$( 8)ここでμ は摩擦係数です。 P は正常で、 R AFMチップの半径を表します。 F の場合 t 臨界値 F に到達 tc 、AFMチップは、チップによって生成された穴から材料を押し出す代わりに、材料のパイルアップ上をスライドします。接触は各サイクルで切断されるため、タッピングモードでは各サイクルでスリップが発生しやすくなります。設定点はチップ振動低減の100%に近いわけではありませんが、1サイクルの間に接触時間が発生する可能性があり、この期間中にスティックが発生する可能性があります。
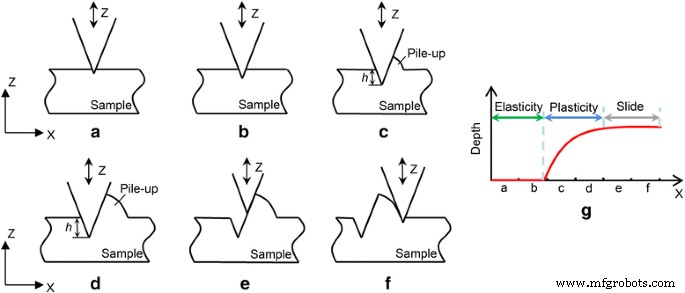
a によるピット形成の概略図 、 b 弾性段階、 c 、 d 可塑性段階、 e 、 f スライドステージ、および g ピット形成の優先順位図
図6dに示すように、この研究では、AFMチップが横方向の速度を受けると、チップとサンプルの接触面積が減少するため、AFMチップがサンプル表面に浸透する深さが深くなります。パイルアップの高さも高くなります。これは、AFMチップによって加えられる通常の負荷のバランスをとるのに役立つ可能性があります。同時に、式(1)で説明されている先端の頂点に加えられる接線方向の力。 7も増やすことができます。侵入深さが増すと、接線力が臨界値 F に達する可能性があります。 tc 式で与えられる。 8. AFMチップは、材料を変更せずに、形成されたパイルアップ上をスライドし始めます。図6eに示すように、AFMシステムのトラッキングサンプル表面の特性により、AFMチップが上昇してパイルアップを乗り越えます。 AFMチップがパイルアップ上を移動した後、1つのピットを実現し、上記の手順を繰り返すことで別のピットを作成します。ピット形成の各段階に対応する変形メカニズムは、図6gにあります。
以前の実験結果によると、引っかき速度は100μm/ sより大きく設定する必要があります。図2bに示すように、スクラッチ方向 V 1 および V 3 を選択し、引っかき方向に垂直なフィードを実行して、5μmの大きな寸法のピットアレイを実現します。図7aは、400μm/ sの引っかき速度で得られたピットアレイを示しています。図7b、cは、それぞれ機械加工されたピットのローカル画像と3DAFM画像を示しています。 2つの異なる引っかき方向の遷移点の近くで引っかき速度が0に減速するため、1つの水平引っかき経路の最初と最後のピットの深さは中央のピットよりもはるかに大きくなります。考えられる理由の1つは上で説明されています。図7b、cに示すように、スクラッチパスの中央にあるピットは均等に分布しています。これは、一定の速度が原因である可能性があります。さらに、図7dに示すピットの断面から、ピットの深さは約2.5nmであることがわかります。さらに、隣接するパスの引っかき方向が反対であるため、隣接するラインのピットの形状が異なります。図8aに示すように、引っかき速度が200 µm / sの場合、隣接するピット間の間隔は比較的小さく、ピットの形状は円形に近くなります。ピットの高速フーリエ変換(FFT)画像から、200μm/ sの引っかき速度で高密度のピットを取得できます。図8bに示すように、900 µm / sの速度で引っ掻くと、間隔距離はほぼ100 nmになり、引っ掻き方向が異なると得られるピット間の違いがはっきりと観察できます。また、引っかき速度が900μm/ sのピットのFFT画像からは、低密度のピットしか達成できません。
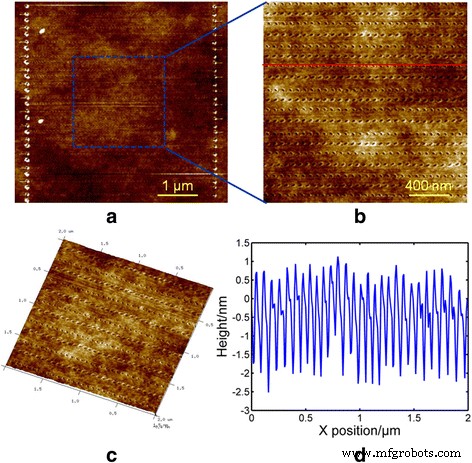
引っかき速度が400μm/ sのピットの配列のAFM画像、 a 5μmの寸法、 b a の一部 2μmの寸法で、 c b の3DAFM画像 、および d b の赤い線のピットの断面
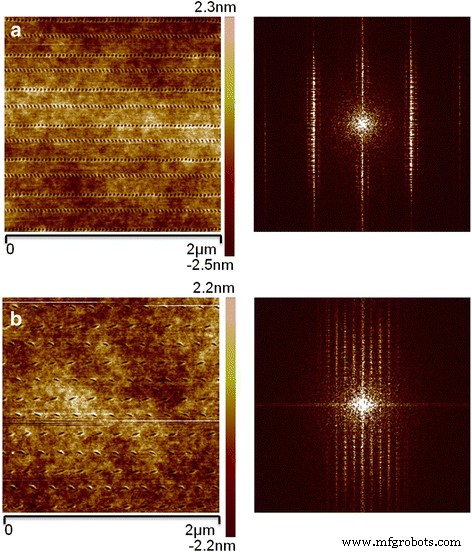
寸法が2μmのピットアラリーのAFM画像と形態のFFT画像。引っかき速度は a 200μm/ sおよび b 900μm/秒
結論
チップベースのDPL法で製造効率を向上させるために、0.1〜1000μm / sの範囲の引っかき速度が調査され、市販のAFMタッピングモードに基づいて実証されています。本研究の結果は、100μm/ sがピット形成の引っかき速度の臨界値であることを示しています。パイルアップのあるナノグルーブは、臨界値よりも遅い引っかき速度で得ることができます。引っかき速度が5μm/ sを超える場合、加工された深さは V を除くすべての一般的な方向で一貫しています。 3 加工深さがはるかに小さくなる方向。対照的に、深さは引っかき方向に依存しません。臨界値の100μm/ sよりも大きい引っかき速度で個別のピットを生成できます。引っかき速度が200〜900μm / sの一定値の場合、製造されたピットの総数は1秒で約4800〜5800に達する可能性があります。応力緩和弾性率理論によれば、高周波負荷をかけると、ポリマー表面はガラス状態になります。サンプル表面に適用されるエネルギーは、AFMチップの1回の貫通中にPMMA分子鎖を切断するのに十分な大きさではありません。 1つのピットを形成するには、65〜80回の貫通が必要です。浸透の初期段階では、弾性変形が主要な材料除去メカニズムです。貫通回数が40倍になると、ポリマー鎖が切れ始め、塑性変形が起こります。侵入深さが増すと、機械加工されたピットの横に蓄積される材料の高さが高くなり、先端の頂点にかかる接線力が増加します。これが、AFMチップがパイルアップ上を滑る理由として考えられます。その後、1つのピットが作成されます。最後に、5 µmの寸法、70 nmの間隔距離、2.5nmの機械加工深さのピットアレイが正常に実現されました。 FFT画像は、ピットの密度と引っかき速度の関係を明らかにするために使用されます。
ナノマテリアル
- カヴリ賞を受賞したAFMパイオニア
- ナノスフェア自己組織化と従来のフォトリソグラフィーを組み合わせたブロードバンド金属平面マイクロレンズとそのアレイのバッチ製造
- トルエン中の塩を含むABCトリブロック共重合体を使用した秩序あるナノパターンの製造
- 修飾された自由表面エレクトロスピニングを使用した高品質ナノファイバーのハイスループット製造
- 構造用カラーマイクロファイバーを使用した光スイッチングパターンの製造
- 3D懸垂構造の製造のためのワンステップマスクベースの回折リソグラフィー
- 高PSRRのナノスケール低電力抵抗なし電圧リファレンス
- アモルファスSiパッシベーションを備えた高移動度GepMOSFET:表面配向の影響
- AFMチップベースのナノミリングプロセス下でのポリジメチルシロキサンナノ流体チップの製造
- ホール移動度の高い非常に薄いアモルファスSnドープIn2O3膜のキャリア輸送を制限する要因に関する新しい洞察
- 導電性の高い安定した高分子インク