スタンピングプロセスに関する16のキーポイント[実務経験]
スタンピングプロセスは、板金に所望の形状を与える金属成形プロセスです。スタンピングプロセスには、パンチング、曲げ、ブランキング、せん断、ピアシングなど、他のさまざまな板金操作が含まれる場合があります。
この記事では、シェーンの実際の経験から、板金プレス加工のさまざまな側面について学びます。
1。廃棄物からの情報
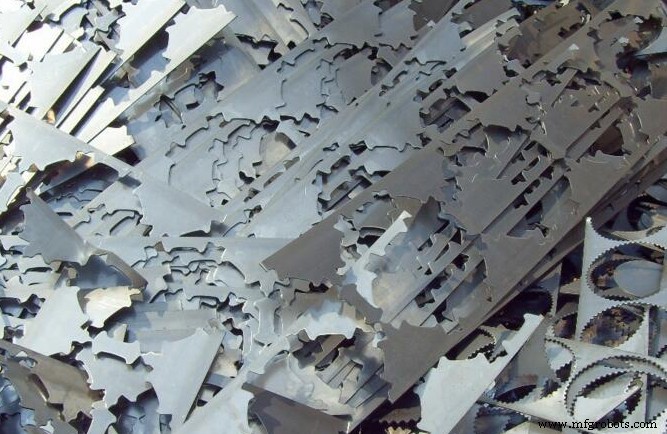
スクラップは本質的に、形成された穴の反射です。それは反対の位置にある同じ部分です。スクラップをチェックすることで、上型と下型の隙間が正しいかどうかを判断できます。
ギャップが大きすぎると、廃棄物は粗く起伏のある破面と狭い明るいゾーンになります。ギャップが大きいほど、破面とブライトゾーン領域の間の角度が大きくなります。
ギャップが小さすぎると、廃棄物は小さな角度の破面と広い明るいバンド領域を示します。ギャップが大きすぎると、大きなカールとエッジの裂け目がある穴が形成され、セクションからわずかに薄いエッジが突き出ます。
ギャップが小さすぎると、わずかな圧着と大きな角度の裂け目があるバンドが形成され、材料表面にほぼ垂直なセクションになります。
理想的な廃棄物は、適度な崩壊角度と均一な明るいバンドを持っている必要があります。これにより、打ち抜き圧力が最小限に抑えられ、バリの少ないきれいな丸い穴が形成されます。
この観点から、ダイの耐用年数を延ばすためにギャップを増やすことは、完成した穴の品質を犠牲にすることと引き換えになります。
2。ダイクリアランスの選択
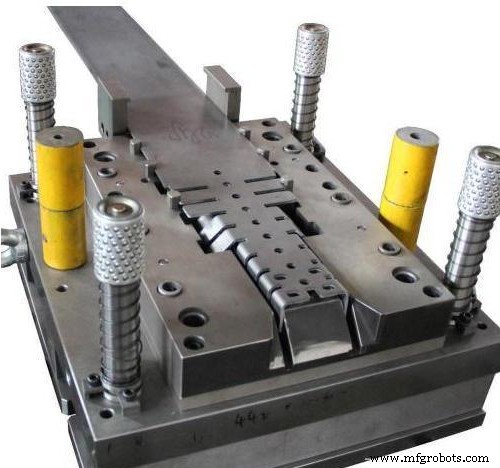
ダイのクリアランスは、打ち抜かれる材料の種類と厚さに関係します。不当なクリアランスは、次の問題を引き起こす可能性があります。
(1)ギャップが大きすぎると、打ち抜き加工物のバリが比較的大きくなり、打ち抜き品質が悪くなります。
クリアランスが小さすぎると、パンチング品質は良好ですが、ダイの摩耗が深刻であるため、ダイの耐用年数が大幅に短くなり、パンチが破損しやすくなります。
(2)ギャップが大きすぎたり小さすぎたりすると、パンチ材に付着しやすくなり、スタンピング時に素材が曲がってしまいます。
ギャップが小さすぎると、パンチの底面と板金の間に真空が形成されやすくなり、廃棄物が跳ね返ります。
(3)適度なクリアランスは、ダイの耐用年数を延ばし、良好な除荷効果をもたらし、バリとフランジングを低減し、プレートを清潔に保ち、穴の直径が一定であり、プレートを傷つけず、研削時間を短縮し、プレートをまっすぐにして正確なパンチングポジショニング。
次の表を参照して、金型クリアランスを選択してください(表のデータはパーセンテージです)
クリアランスの選択(合計クリアランス) | |||
材料科学 | 最小 | ベスト | 最大 |
赤銅 | 8% | 12% | 16% |
真ちゅう | 6% | 11% | 16% |
軟鋼 | 10% | 15% | 20% |
アルミニウム(ソフト) | 5% | 10% | 15% |
ステンレス鋼 | 15% | 20% | 25% |
%×材料の厚さ=ダイクリアランス |
3。ダイの耐用年数を改善する方法
ユーザーにとって、ダイの耐用年数を改善することで、スタンピングコストを大幅に削減できます。
ダイの耐用年数に影響を与える要因は次のとおりです。
- 材料の種類と厚さ;
- 妥当な低いダイクリアランスが選択されているかどうか
- カビの構造形態
- 材料のスタンピング中に良好な潤滑があるかどうか
- 金型に特別な表面処理が施されているかどうか
- チタンメッキ、カーボン窒化チタンなど
- 上部タレットと下部タレットの位置合わせ
- 調整ガスケットの合理的な使用
- 傾斜エッジダイが適切に使用されているかどうか
- 工作機械のダイベースが摩耗しているかどうか
4。特別なサイズの穴をスタンプする際に注意が必要な問題
- 最小穴径がφ0.8〜φ1.6の範囲の場合は、専用パンチを使用してください。
- 厚板を打ち抜く場合は、加工穴径よりも大きいダイを使用してください。
例1.次の表の処理条件によると、処理アパーチャはステーションAのダイに対応していますが、ステーションBのダイを使用してください。
素材のテクスチャ | プレートの厚さ(mm) | 絞り(mm) |
軟鋼(40kg / mm 2 ) | 6.0 | 8.2-12.7 |
ステンレス鋼(60kg / mm 2 ) | 4.0 | 8.2-12.7 |
例2.次の表の処理条件によると、処理アパーチャはBステーションダイに対応していますが、Cステーションダイを使用してください。
素材のテクスチャ | プレートの厚さ(mm) | 絞り(mm) |
軟鋼(40kg / mm 2 ) | 6.0 | 22.9-31.7 |
ステンレス鋼(60kg / mm 2 ) | 4.0 | 22.9-31.7 |
(3)一般に、パンチエッジの長さに対する最小幅の比率は1:10以上でなければなりません。
例3.長方形パンチの場合、刃先長さが80mmの場合、刃先幅≥8mmが最適です。
(4)パンチエッジの最小寸法と板厚の関係。
パンチエッジの最小寸法は、プレートの厚さの2倍にすることをお勧めします。
5。金型研削
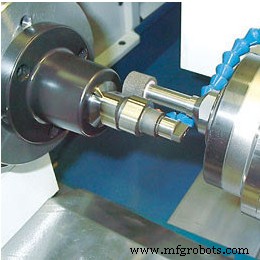
1。金型研削の重要性
ダイの定期的な研削は、パンチング品質の一貫性を保証します。
ダイを定期的に研削すると、ダイの耐用年数が向上するだけでなく、機械の耐用年数も向上します。正しい研削時間を把握する必要があります。
2。ダイの特定の特性を研ぐ必要があります
金型研削の場合、研削が必要かどうかを判断するための厳密な数の打撃はありません。
主にエッジの鋭さに依存します。
主に次の3つの要因によって決定されます:
(1)刃先のフィレットを確認します。フィレット半径がR0.1mmに達する場合(最大R値は0.25mmを超えてはなりません)、研削が必要です。
(2)パンチングの品質と大きなバリがないか確認してください。
(3)機械のスタンピングのノイズによって研削が必要かどうかを判断します。
スタンピング中に同じダイのノイズが異常である場合は、パンチが鈍く、研削が必要であることを示しています。
注:刃先が丸くなったり、刃先の後部が粗くなったりした場合も、研削を検討する必要があります。
3。粉砕方法
ダイを研削する方法はたくさんありますが、これは特殊な研削盤または平面研削盤で実現できます。
パンチと下型の研削頻度は一般的に4:1です。研削後、ダイの高さを調整してください。
(1)不適切な粉砕方法の危険性:
不適切な研削は、ダイエッジの急速な損傷を悪化させ、その結果、研削あたりの打撃回数が大幅に減少します。
(2)正しい粉砕方法の利点:
ダイを定期的に研削することで、パンチングの品質と精度を安定させることができます。
ダイの刃先はゆっくりと損傷し、耐用年数が長くなります。
4。粉砕ルール
金型研削では、次の要素を考慮する必要があります。
(1)エッジフィレットがR0.1〜0.25mmの場合、エッジの鋭さによって異なります。
(2)砥石の表面を清掃する。
(3)緩く、粗く、柔らかい砥石をお勧めします。 WA46KVなど。
(4)毎回の研削量(切削量)は0.013mmを超えてはならない。
過度の研削量は、焼きなまし処理と同等のダイ表面の過熱を引き起こし、ダイを柔らかくし、ダイの耐用年数を大幅に短縮します。
(5)研削中に十分なクーラントを追加する必要があります。
(6)研削中は、パンチと下型を安定して固定し、専用の工具固定具を使用する。
(7)金型の研削量は一定です。この値に達すると、パンチは廃棄されます。
使い続けると金型や機械にダメージを与えやすく、損をするだけの価値はありません。
(8)研削後、エッジをオイルストーンで処理して、過度に鋭いエッジとラインを除去する必要があります。
(9)粉砕後、ブレードを洗浄し、消磁し、油をさします。
注:ダイの粉砕量は、主に刻印されたプレートの厚さに依存します。
6。使用前にパンチに注意してください
1。ストア
(1)上型スリーブの内側と外側をきれいな布で拭きます。
(2)保管の際は、表面に傷やへこみをつけないように注意してください。
(3)さびを防ぐためのオイル。
2。使用前の準備
(1)使用前に上ダイスリーブを完全に清掃してください。
(2)表面に傷やへこみがないか確認してください。ある場合は、オイルストーンで取り除きます。
(3)内外のオイル。
3。上ダイスリーブにパンチを取り付ける際の注意事項
(1)パンチを清掃し、長いハンドルにオイルを塗ります。
(2)パンチを大型ステーションダイの上部ダイスリーブの下部に無理に挿入します。
ナイロンハンマーは使用できません。
取付時、上ダイスリーブのボルトを締めてパンチを固定することはできません。ボルトは、パンチが正しく配置された後でのみ締めることができます。
4。上部モールドアセンブリをタレットに取り付けます
ダイの耐用年数を延ばしたい場合は、上ダイスリーブの外径とタレット穴の隙間をできるだけ小さくする必要があります。
したがって、以下の手順を慎重に実行してください。
(1)タレット穴のキー溝と内径を清掃してオイルを塗ります。
(2)上型ガイドスリーブのキー溝をタレット穴のキーと一致するように調整します。
(3)上部モールドスリーブをタワーの穴にまっすぐ挿入し、傾かないように注意してください。
上型ガイドスリーブは、自重でタレット穴にスライドする必要があります。
(4)上型スリーブが片側に傾いている場合は、ナイロンハンマーなどの柔らかい素材の工具で軽くたたくことができます。
上型ガイドスリーブが自重で正しい位置にスライドするまで、ノックを繰り返します。
注:上型のガイドスリーブの外径に力を加えないでください。パンチの上部にのみ力を加えてください。
砲塔の穴を損傷したり、個々のステーションの耐用年数を短くしたりしないように、上部ダイスリーブの上部をノックしないでください。
6。カビのメンテナンス
パンチが素材に噛まれて取り出せない場合は、以下の項目で確認してください。
1。パンチと下型の再研磨。
鋭いエッジのダイは、美しい切断部分を処理できます。エッジが鈍い場合は、追加のパンチ圧が必要です。また、ワーク部が粗いため抵抗が大きく、パンチが素材に噛まれてしまいます。
2。ダイクリアランス。
プレートの厚さに対してダイのクリアランスが適切に選択されていない場合、パンチを材料から分離するときに大きな離型力が必要になります。
このため、パンチが素材に引っ掛かる場合は、下型を適度なクリアランスで交換してください。
3。処理された材料のステータス。
素材が汚れていたり、汚れているとダイに汚れが付着し、パンチが素材に噛まれて加工できなくなります。
4。変形した素材。
穴を開けた後、反った材料がパンチをクランプし、パンチを噛みます。
反りのある材料は、処理する前に平らにする必要があります。
5。スプリングの過度の使用。
春の疲労を引き起こします。必ず春の性能をチェックしてください。
7。給油
オイルの量と注入回数は、加工材料の状態によって異なります。
冷間圧延鋼板や耐食鋼板など、錆やスケールのない材料の場合は、ダイにオイルを注入する必要があります。
オイル注入ポイントは、ガイドスリーブ、オイル注入ポート、ナイフ本体とガイドスリーブの接触面、下型などです。オイルには軽質エンジンオイルを使用してください。
錆びやスケールのある素材の場合、加工時にパンチとガイドスリーブの間にサビ粉が吸い込まれ、汚れが発生し、ガイドスリーブ内でパンチが自由にスライドできなくなります。
この場合、オイルを塗るとサビが付着しやすくなります。
したがって、逆に、この材料を洗い流すときは、オイルを拭き、月に1回分解し、パンチと下型の汚れを蒸気(薪)オイルで取り除き、再組み立てする前にきれいに拭きます。
これにより、金型の潤滑性能を確保できます。
8。カビの使用過程における一般的な問題と解決策
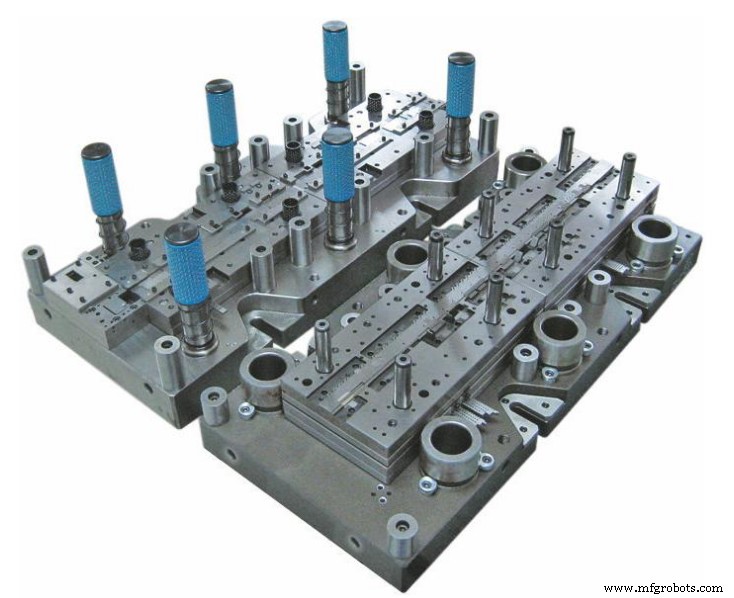
問題1:プレートが顎から出てくる
理由 | 解決策 |
不完全な金型のアンロード | 1。傾斜のあるパンチを使用する |
2。プレートに潤滑剤を塗布します | |
3。ヘビーデューティーダイを採用 |
問題2:深刻なダイの摩耗
理由 | 解決策 |
不当なダイクリアランス(小さすぎる) | ダイクリアランスを増やす |
上下のダイシートのずれ | 1。上ダイと下ダイのステーション調整と位置合わせ2。タレットレベル調整 |
摩耗したダイガイドコンポーネントとタレットインサートが時間内に交換されませんでした | 交換 |
パンチの過熱 | 1。シートに潤滑剤を追加します2。パンチと下型ダイの間の潤滑を確認します3。同じ仕様とサイズの複数の金型セットが同じプログラムで使用されます |
不適切な研削方法は、ダイの焼きなましにつながり、摩耗を悪化させます | 1。軟質砥石2。砥石を頻繁に清掃する3。小さな一口4。十分なクーラント |
ステップパンチング | 1。ステップ距離を大きくします2。ブリッジステッピングを採用 |
問題3:パンチベルトとパンチの接着
理由 | 解決策 |
不当なダイクリアランス(小さすぎる) | ダイクリアランスを増やす |
パンチエッジパッシベーション | タイムリーな粉砕 |
潤滑不良 | 潤滑状態を改善する |
問題4:廃棄物のリバウンド
理由 | 解決策 |
下部モジュールの問題 | 防弾素材を使用してカビを下げます |
小径の穴の場合、クリアランスは10%減少します | |
直径が50.00mmを超え、ギャップが拡大 | |
ダイのエッジ側にスクラッチが追加されます | |
パンチ | ダイの深さを増やす |
排出ポリウレタンエジェクターバーを取り付けます | |
斜めの刃先を採用 |
問題5:荷降ろしが難しい
理由 | 解決策 |
不当なダイクリアランス(小さすぎる) | ダイクリアランスを増やす |
パンチウェア | タイムリーな粉砕 |
春の倦怠感 | スプリングを交換してください |
パンチ接着 | 接着を取り除く |
質問6:スタンピングノイズ
理由 | 解決策 |
荷降ろしの難しさ | より低いダイクリアランスと良好な潤滑を増やします |
排出力を増やす | |
表面が柔らかい排出プレート | |
作業台とタレットでのシートのサポートに問題があります | 球形サポートダイ |
作業サイズを縮小する | |
作業厚さを増やす | |
シートの厚さ | 斜めエッジパンチを使用 |
9。特殊成形工具使用上の注意
1.異なるモデルの機械のスライドブロックのストロークは異なるため、成形ダイの閉鎖高さの調整に注意してください。
2.成形が十分であることを確認する必要があるため、慎重に調整する必要があります。毎回0.15mmを超えないようにしてください。
調整が大きすぎると、機械や金型に損傷を与えやすくなります。
3.ストレッチフォーミングの場合は、板金の破れや不均一な変形による荷降ろしの困難を防ぐために、軽いスプリングアセンブリを選択してください。
4.シートが傾かないように、成形金型の周りにボールサポート金型を取り付けます。
5.成形位置は、クランプからできるだけ離してください。
6.成形は、処理プログラムの最後に行うのが最適です。
7.プレートの潤滑が良好であることを確認してください。
8.注文するときは、特殊成形工具の歩留まりに注意してください。 2つの成形距離が近い場合は、必ず当社の営業担当者にご連絡ください。
9.成形工具はアンロード時間が長いため、成形処理時には低速を採用する必要があり、遅延が最適です。
10。長方形カッター使用上の注意
1.ステップ距離は可能な限り大きくする必要があります。これは、工具全体の長さの80%を超える必要があります。
2.プログラミングによるジャンプステップを実現するのが最善です。
3.斜めのエッジダイを使用することをお勧めします。
12.機械の公称力を超えずにパンチする方法は?
製造工程では、直径114.3mmを超える丸い穴を開ける必要があります。
このような大きな穴は、特に高せん断強度の材料の場合、機械の公称力の上限を超えます。
この問題は、複数のパンチング方法で大きな穴を開けることで解決できます。
小さなダイで大きな円の円周に沿って切断すると、パンチ力を半分以上減らすことができます。あなたがすでに持っているダイのほとんどはそうすることができるかもしれません。
11。大きな丸い穴を開ける簡単な方法
この凸レンズの型は、必要な半径サイズに作ることができます。
穴の直径がパンチの公称力を超える場合は、スキーム(A)をお勧めします。
このダイを使用して、円の周囲を打ち抜きます。
パンチの公称力範囲内で穴径を打ち抜くことができれば、ラジアルダイと凸レンズダイでダイを回転させずに必要な穴を4回打ち抜くことができます(B)。
12。最後に、それは下向きに形成されます
成形ダイを選択するときは、下向きの成形操作を避ける必要があります。これは、垂直方向のスペースを占有しすぎて、追加のシートレベリングまたは曲げプロセスにつながるためです。
下向きの成形も下型に落ちて、タレットから引き出される場合があります。
ただし、下向き成形が唯一のプロセスオプションである場合は、板金処理の最後のステップと見なす必要があります。
13。材料の歪みを防ぐ
プレートに多数の穴を開ける必要があり、プレートを平らに保つことができない場合は、スタンピング応力の蓄積が原因である可能性があります。
穴を開けるとき、穴の周りの材料が下向きに引き伸ばされ、プレートの上面の引張応力が増加します。
下向きの動きは、プレートの下面の圧縮応力の増加にもつながります。
少数の穴を開ける場合、結果は明らかではありませんが、穴の数が増えると、プレートが変形するまで引張応力と圧縮応力も指数関数的に増加します。
この変形をなくす1つの方法は、次のとおりです。
1つおきに穴を開けてから、戻って残りの穴を開けます。
これにより、プレートに同じ応力が発生しますが、同じ方向に次々にパンチすることによって発生する引張/圧縮応力の蓄積が崩壊します。
このようにして、最初のバッチの穴は、2番目のバッチの穴の変形効果を共有します。
14。ステンレス鋼のフランジが変形した場合
フランジを付ける前に、高品質の成形潤滑剤を材料に塗布します。これにより、材料をダイからより適切に分離し、成形中にダイの下面をスムーズに移動できます。
これにより、材料を曲げたり伸ばしたりしたときに発生する応力を分散させて、成形フランジ穴のエッジの変形やフランジ穴の底部の摩耗を防ぐことができます。
15。荷降ろしの問題を克服するための提案
1.細かいゴム粒子のパンチを使用します。
2.下型のクリアランスを増やします。
3.スプリングの疲労をチェックします。
4.頑丈なダイを使用します。
5.斜めエッジダイの適切な使用。
6.プレートに注油します。
7.大型ステーションダイにはポリウレタン排出ヘッドを設置する必要があります。
16。廃棄物のリバウンドの主な原因
1.刃先の切れ味。刃先のフィレットが大きいほど、廃棄物の跳ね返りが発生しやすくなります。
2.ダイの侵入係数。各ステーションでダイをプレス加工する場合、侵入係数の要件は確実です。侵入弾性率が小さいため、廃棄物のリバウンドが発生しやすい。
3.ダイのクリアランスが妥当かどうか。不当なダイクリアランスは、廃棄物のリバウンドを引き起こしやすいです。
4.加工板の表面に油汚れがないか。
ただし、クーラントと供給システムが期待どおりに機能するように、定期的かつ定期的なメンテナンスを実行する必要があります。
これはShaneによるゲスト投稿です MachineMfgチームから
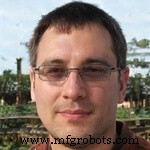
シェーンは機械工学業界で5年以上働いています。彼は執筆が大好きで、技術情報、ガイダンス、詳細な解決策、および金属と金属加工に関連する考えを共有することに焦点を当てています。彼の記事を通じて、ユーザーはいつでも簡単に関連する問題を解決し、必要なものを見つけることができます。
産業技術