プラスチック射出成形の 7 つの主な利点
長い間、製造業者は常に高速金型を大量生産、スチール加工された耐久性のあるプレス フォーム、および多額の設備投資と関連付けてきました。また、彼らは、プラスチック射出成形が幅広い複雑なプラスチック コンポーネントの製造に理想的な方法であり、さまざまな業界の OEM に利益をもたらすという事実を無視しています。しかし、プロトタイピング技術の発展に伴い、ラピッド 射出成形は、最も優れたプロトタイピング技術の中でその地位を正当に主張するようになりました.
急速射出成形とは
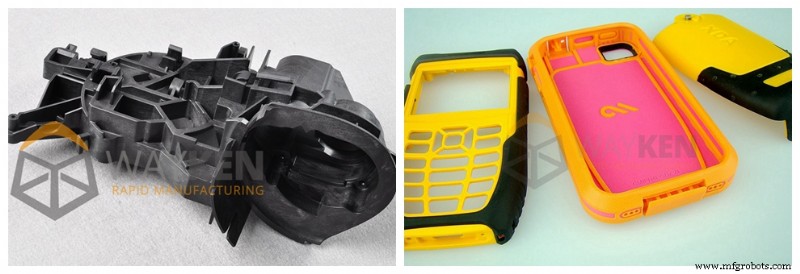
高速射出成形プロセスは、技術的には従来の射出成形と同じです。主な違いは、ツールの製造方法にあります。
まず、RIM は金型にさまざまな材料を使用しています。従来のプロセスでは、金型を可能な限り耐久性のあるものにすることが目的であったため、金型は機械にとって非常に面倒な硬化鋼から製造されていました。高速射出成形は、少量の実行に使用されるため、より柔らかい材料を使用できます。広く普及しているオプションは、航空機グレードのアルミニウム合金です。それらは鋼に似た強度を持っていますが、機械加工や研磨がはるかに簡単です。これにより、機械加工ではツーリング時間が最大 30%、研磨では最大 2 ~ 5 倍短縮されます。
第二に、急速射出成形の金型は簡単に再設計できます。大量生産の射出成形用金型は、接合部が少ないほど精度が高く、寿命が長いため頑丈です。プロトタイピング プロセスでは、柔軟性を高めるために精度が少し犠牲になることがあります。そのため、キャビティはダイのベースとは別の部品として製造されます。こうすれば、調整が必要な場合は、空洞だけを取り除き、残りはそのままにしておくことができます。
第三に、急速射出成形は従来の急速射出成形よりも自動化が少ないため、金型の設計、製造、微調整に必要な時間が短縮されます。
従来の高速射出成形プロセスでは、多くの自動車用エジェクタ、負荷、およびその他の補助機構を使用して、その性能をさらに高めています。ただし、試作は部品ごとの切削時間ではなく、切削準備時間です。したがって、自動車のメカニズムを手動で取り付けられるものに置き換えると、射出システムの製造にかかる時間を大幅に節約できます。
上記のすべてのポイントにより、プロトタイプの作成時間が大幅に短縮されます。クライアントにとっては、従来の射出成形では 2 ~ 5 か月かかるのに対し、迅速な射出成形では 2 ~ 5 週間で部品を入手できるということです。
プロトタイプ製造のための高速射出成形の利点
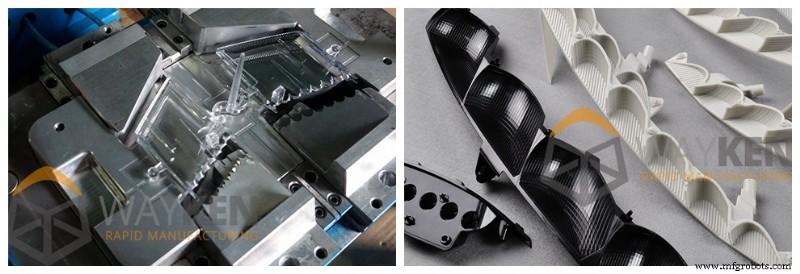
確かに、RIM をプロトタイピングに使用できるようになったにもかかわらず、金型の作成は依然として長く複雑なプロセスです。たとえば、パーツの 3D プリントには、数週間ではなく 2 ~ 5 日かかります。では、なぜラピッド インジェクション モールディングにこだわるのでしょうか?
迅速な射出成形プロセスには、他のプロトタイピング技術には見られない多くの利点があります
1.強さ
最適な射出角度と均一な肉厚を確保する製造可能性を考慮した設計により、液化樹脂は高圧下でキャビティ内に射出されます。パーツに気孔がなく、最終的な材料の品質が可能な限り最高であることを保証します。粉末や細い糸を使い、それを焼き固める3Dプリンターでは、そんなことは言えません。その結果、最終的な材料には細孔や未焼結領域が含まれる場合があります。
2.表面仕上げ
成形品の表面仕上げは、金型の品質に依存します。キャビティは通常、CNC フライス加工とその後の仕上げ操作によって製造されます。その中で最も普及しているのは研磨です。さらに、EDM 切削を使用して、キャビティの内側の角を鋭くします。得られる表面仕上げは、Ra 0.8 mcm まで小さくすることができます。
3.卓越した精度
射出成形は、他のプロトタイピング技術と比較して優れた精度を提供します。たとえば、3D プリンティングはせいぜい IT9 を生成しますが、高速射出成形は金型精度によってのみ制限され、IT7 まで高くなる可能性があります。
4.材料の無駄がほぼゼロ
多くのプロトタイピング手法では、材料がまったく考慮されていません。 1 桁のバッチを製造している場合は問題ありません。ただし、一部の製品では、ライブ環境での広範なテストが必要です。たとえば、医療用プロトタイプの最終テスト段階では、製品を消費者に提供して日常生活のテストを行います。つまり、数百または数千のサンプルが必要になり、ブランク材料の 50% 以上を失うと、かなりの費用がかかります。現在、RIM は必要な量のプラスチックのみをキャビティに注入し、廃棄物を最小限に抑えています。
5.金型はかなり大きなバッチに使用できます
ほとんどのプロトタイピング プロセスは、少数の部品を作成することに優れています。たとえば、シリコン キャスティングは、最大 15 個程度の部品まで実行可能です。その後、鋳造フォームが劣化しすぎて、別のフォームを製造する必要があります。ラピッド インジェクション金型は、従来の金型ほど耐久性はありませんが、ほとんどの試作プロセスよりも多くの実行に耐えることができます。それらの最高のものは、摩耗しすぎる前に最大 100,000 個のパーツを作成できます。
6.普遍性
異なるプラスチックを使用した 3D プリントでは、システム全体を大幅に再ハッシュする必要があります。別のプラスチックから同じ部品を印刷できるようにするには、ブランク材料でカートリッジを交換し、多くの設定を変更する必要があります。最悪の場合、まったく別の機器が必要になります。射出成形について話すとき、それは必要ありません。金型は、あらゆるプラスチックよりもはるかに高い特性を持つ高級アルミニウムで作られています。そのため、基本的には、製造した金型であらゆる材料を使用できます。
7.効率
大量生産に比べれば、試作技術はあまり効果的ではありません。ブランクが最終部品に近く、機械への負荷が少ないという事実だけで、単一の部品は、大量生産された同じ部品よりもはるかに長い時間にわたって機械加工されます。さらに、量産向けの加工プロセスを最適化して、ブランクのセットアップと軌跡を最小限に抑えます。部品数が少ない場合は処理時間が長くても問題ありませんが、バッチが大きくなるほど、1 つの部品を製造するのに必要な時間を最小限に抑えることが重要になります。 RIM テクノロジは、他のすべてのプロトタイピング手法の中で処理時間が最も短いため、バッチが大きいほど、このテクノロジは実行可能になります。
ISO 9001:2005 品質システム認定サプライヤーとして、当社はお客様の要件を満たすことができると確信しています。お気軽に CAD ファイルをこちらから送信するか、電話でお問い合わせください:+86 755 2373 1920
産業技術