超音波加工プロセス–部品の動作原理、利点
この記事で取り上げるトピックは、超音波加工プロセス、動作原理、長所、短所、およびその詳細な動作です。
超音波加工プロセスとは何ですか?
超音波加工プロセス (USM)は、超音波周波数で軸方向に振動するツールを使用して硬くて脆い材料を除去するプロセスです。 [18〜20キロヘルツ(kHz)]。
その振動の間、B4CまたはSiCの研磨剤スラリーは、軟工具(ろう鋼)とワークピースの間の加工ゾーンに連続的に供給されます。したがって、研磨粒子はワークピースの表面に打ち込まれ、そこから微粒子が欠けます。
振動ツールは、振幅が10〜40 µmの範囲で、砥粒に静圧をかけ、材料が除去されて必要なツール形状を形成するときにフィードダウンします。 Balamuthは、1945年に研磨剤粉末の超音波粉砕中にUSMを最初に発見しました。
産業用アプリケーションは、新しい工作機械が登場した1950年代に始まりました。 USMは、ワークピース材料の金属構造に悪影響がないことを特徴としています。
超音波加工プロセスの動作原理
超音波溶接と同じ原理で動作します。

この機械加工方法では、超音波を使用して、研磨駆動力として機能する高周波、低振幅の力を生成します。超音波装置は、周波数が約 20000〜30000 Hzの高周波振動波を生成します。 振幅は約25-50ミクロンです 。
この高周波振動は、研磨剤スラリーに含まれる研磨剤粒子に伝達されます。これにより、研磨粒子が脆いワークピースをへこませ、接触面から金属を取り除きます。
超音波加工の部品
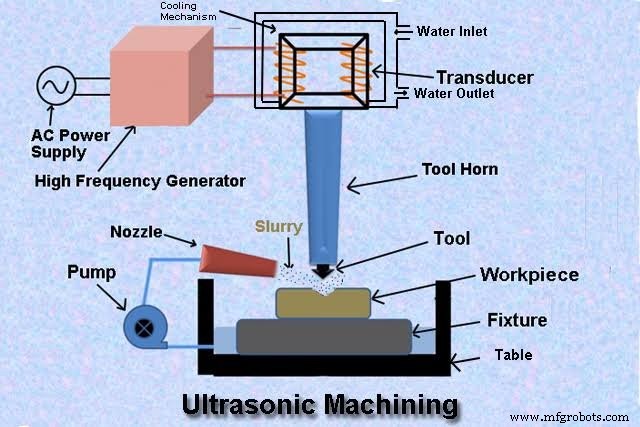
- 電源
- トランスデューサー
- 高周波発生器
- 超音波振幅トランスまたはツールホーン
- 冷却メカニズム
- ツール
- ツールホルダー
- ノズル
- ソリューション
- ポンプ
1.電源
この機械加工プロセスでは、通常、 50〜60 Hzの範囲の電流電源が必要です。 。その結果、プロセスを開始するために交流電源を利用できます。
2.トランスデューサー(磁歪)
このトランスデューサは磁歪です 本来は。このトランスデューサーは、磁石に変換されると、磁歪作用に基づいて作用することにより、機械的振動の周波数を変更します。このトランスデューサーは上下両方向に振動します。
3。高周波発生器
高周波発生器は、超音波電源または電子発振器としても知られています。これは通常、50または60ヘルツで動作する従来の電源装置を変換するために使用されます。 高周波電気エネルギーに。最も一般的に使用される周波数は20〜40 kHz 。これらの周波数は、電気変換器に送られます。
4。超音波振幅トランスフォーマーまたはツールホーン
このユニットは、その名前が示すように、ツールをトランスデューサーに接続します。 増幅された振動を伝達します ブースターからツールまで。耐久限度が高いはずです。
ツールコンセントレーターとも呼ばれます 。トランスデューサーによって生成される振動振幅は、約0.025ミリメートルの範囲であり、機械加工には不十分です。振動の振幅をブーストするために使用されます。
振動もツールチップに向けられ、集中されます。ツールはツールホーンの下端に取り付けられており、材料の除去に役立ちます。溶接、ねじ込み、ろう付け、またははんだ付けを使用して、ツールをツールのホーンに接続します。
5.冷却メカニズム
トランスデューサーの上部に冷却システムが取り付けられています。冷水は入口ゲートから入り、トランスデューサーから熱を受け取り、出口を避けます。 冷却目的のために、ケーシングがトランスデューサーを囲んでいます。 、そして水はこのケーシング内を流れます。
6 。ツール
超音波機械加工装置は、通常、炭化タングステン、ステンレス鋼、チタン、銅などの、脆性破壊下で破損せず、延性のある強力な硬化および脆性材料でできています。
ツールを使用して、ワークピースから材料を取り除きます。デバイスは、ワークピースの表面に形成する必要のあるキャビティと同じ形状で作られています。
7。ツールホルダー
ツールを保持するために使用されます。
8 。ノズル
ノズルはタングステンでできています 。柔らかい材料でできている場合、ポンプからのスラリーがノズルを損傷する可能性があるため、タングステンはノズルの作成に使用されます。タングステンなどの硬い素材でできています。
9 。ソリューション
機械加工分野では、通常、炭化ケイ素、炭化ホウ素、および水または油に硬質研磨粒子を含む混合アルミナ溶液が継続的に提供されます。
10 。ポンプ
ポンプは、ノズルに研磨液を供給するために使用されます。
超音波加工の働き
図1および2に示す機械加工システムは、主に磁歪器、コンセントレータ、ツール、およびスラリー供給装置で構成されています。
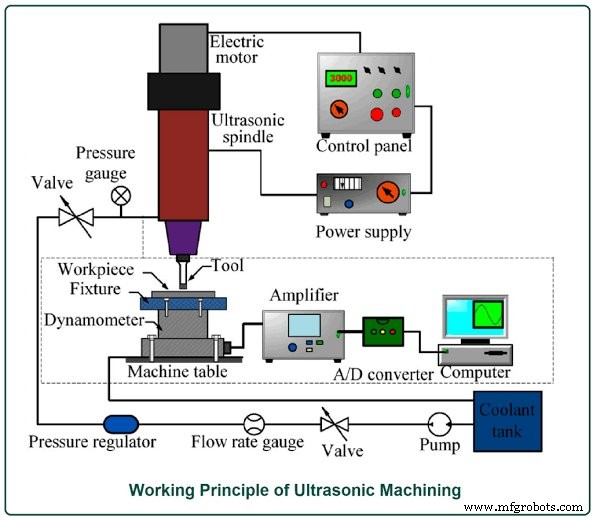
この高周波入力は、電気機械変換に供給されます。 つまり、超音波周波数で通電される(磁歪)と
小振幅の振動を生成します。
ホーンはトランスデューサーとツールホルダーの間にあります。ホーンは、トランスデューサーの振動の振幅を増加させるために使用されます。その後、トランスデューサーの振動は、機器に焦点を合わせて方向付けられます。交流電源を高周波発生器に接続すると、入力電源の周波数が20kHzから40kHzに上昇します。デバイスが振動すると、ツールホルダーがデバイスをつかみます。
研磨剤スラリーは、装置が振動するときにツール表面とワークピースの間のポンプの助けを借りて一定の速度で供給されます。次に、工具をワークピースに軽く押し付け、スラリーがツールとワークピースの間に流れるのに十分なスペースを残します。材料除去の結果としてワークピースに生成されるサイズは、ツールのサイズと同じになります。
振動装置がワークピースに押し付けられると、振動の高い運動エネルギーがこれらの研磨粒子に伝達され、これらの研磨粒子がワークピースの表面に適用され、微視的な摩擦によって材料が除去されます。
超音波機械加工(USM)を使用した材料除去プロセス
図は、USMの完全な材料除去メカニズムを示しています。
これには、3つの異なるアクションが含まれます。
1。 振動工具と隣接する作業面の間に詰まった砥粒を局所的に直接ハンマーで叩くことによる機械的摩耗。
2。 加工ギャップを横切って飛んで、ランダムな位置でワークピースに衝突する粒子の自由な衝撃によるマイクロチッピング。
3。 スラリー流のキャビテーションによる作業面の侵食。
キャビテーション効果の相対的な寄与は、除去された全材料の5パーセント未満であると報告されています。すべての材料のUSMに関係する主要なメカニズムは、直接ハンマーです。柔らかくて
軟鋼のような弾性材料は、多くの場合、最初に塑性変形し、
後で低いレートで削除されます。
ガラスなどの硬くて脆い材料の場合、加工率が高く、自由衝撃の役割もわかります。
超音波加工プロセスの切削速度はに依存します
切断率: USMを使用した切断率は、特定の要因によって異なります。これらは :
1。 研磨剤の粒径。
2。 研磨材。
3。 スラリーの濃度。
4。 振動の振幅。
5。 頻度
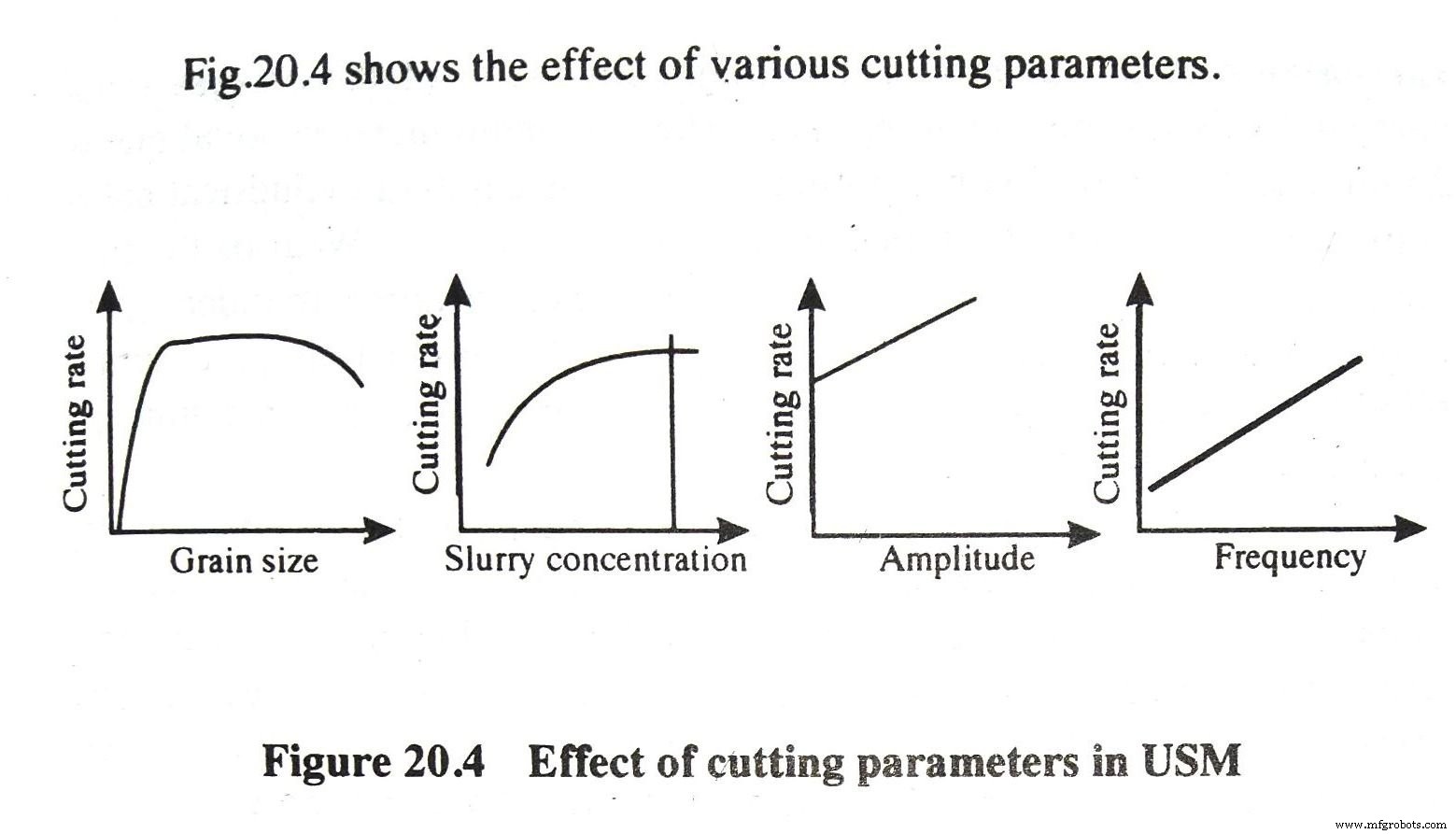
精度: ソフトセラミックなどの柔らかくて脆い材料の最大浸透速度は20mm/ minのオーダーですが、硬くて丈夫な材料の場合、浸透速度は遅くなります。 + 0.005 mmまでの寸法精度が可能であり、Rまでの表面仕上げが可能で、0.1〜0.125uの値を得ることができます。仕上げ加工では、最小コマー半径0.10mmが可能です。 USMマシンのサイズの範囲は、約20Wの入力を持つ軽量のポータブルタイプから、最大2kWの入力を持つ重いマシンまでさまざまです。
超音波加工のアプリケーション
アプリケーション:プロセスが単純なため、次のような幅広いアプリケーションで経済的です。
1。 丸穴や工具を作ることができるあらゆる形状の穴をご紹介します。切削時にワークを動かすことで、得られる形状の範囲を広げることができます。
2。 導電性と非導電性の両方のすべての材料の穴あけ、研削、プロファイリング、フライス盤加工などの実行/機械加工操作。
3。 ガラス、セラミック、タングステン、その他の超硬、宝石、合成ルビーなどの石の機械加工。
4。 ワークピースまたはツールのいずれかをほぼ回転および平行移動させることにより、硬質金属および合金で作られたコンポーネントのねじ山を切断する場合。
5。 タングステンカーバイドとダイヤモンドワイヤーの伸線ダイと鍛造および押出成形プロセス用のダイの製造。
6。 歯科医が痛みを伴わずに歯に任意の形状の穴を開けることができるようにします。
超音波加工の長所と短所
1。 脆く、非導電性で、硬く、壊れやすい材料はすべて、超音波加工を使用して加工できます。
2。 この機械加工プロセスでは熱が発生しないため、ワークピースの物理的な変化はほとんどまたはまったくありません。
3。 導電率が低いためEDMまたはECMで加工できない非金属ですが、超音波加工では非常にうまく加工できます。
4。 バリや歪みのないプロセスです。
5。 EDM、ECG、ECMなどの他の新しいテクノロジーと組み合わせて使用できます。
6。 運転中の騒音はありません。
7。 熟練したオペレーターと熟練していないオペレーターの両方が、この機械加工で使用される装置を使用できます。
8。 高水準の表面仕上げを維持しながら、高水準の精度を達成することが可能です。
9。 導電率に関係なく、どのような材料でも加工できます。
欠点
1。 マイクロチッピングまたはエロージョンメカニズムのため、金属の除去は遅くなります。
2。 ソノトロードの先端はより早く摩耗します。
3。 この方法では、穴の底に研磨剤スラリーが流れないため、深穴加工は困難です(回転式超音波加工を除く)。
4。 超音波振動加工(HRC:材料の硬度を測定するロックウェルスケール)を使用して加工できるのは、硬度値が45HRC以上の材料のみです。
超音波加工の制限
プロセスの制限: このプロセスの主な制限は、金属の切削速度が比較的遅いことです。最大金属除去率は3mm/sで、消費電力が大きいです。現在、円筒穴の深さは工具の直径の2.5倍に制限されています。工具が摩耗すると穴の角度が大きくなり、鋭い角が丸くなります。これは、正確な止まり穴を作成するには工具の交換が不可欠であることを意味します。また、プロセスは、現在の形では、比較的小さなサイズの表面で機械加工することに限定されています。
USMで使用される工具材料は、丈夫で延性がある必要があります。アルミニウムのような非常に延性のある金属の問題は、工具寿命が短いために追跡できます。この問題は、工具材料として低炭素鋼とステンレス鋼を使用することで解消できます。
実験による検証では、金属除去率はワークピースの硬度とツールの硬度の比率とともに減少することが示されています。したがって、ワークの硬度が高くなると、工具の硬度も高くなることが予想されます。
工具金属の選択は、金属除去と工具コストを最適化するための最も重要な意思決定の1つです。ツールの材料が超音波エネルギーの多くを吸収し、効率を低下させるため、ツールの質量の長さも困難になります。ツールが長いと、過度のストレスが発生します。粒子サイズと砥粒も正しい寸法です。結晶粒径が振動の振幅よりも大きいか小さい場合、加工速度が低下することが観察されています。
仕上げ加工用の粒子の選択は、深い穴を開けるときに指定された粗加工の粒子と重ならないようにする必要があります。ツールホルダーを介してスラリーを供給するために特別な技術が必要です。
強制循環、より大きなサイズとより小さなサイズの粒子の交互の混合、吸引は、この深穴加工の問題を取り除くために続く多くの効果的な方法の一部です。
超音波加工の最近の開発
最近の開発:最近、超音波加工の新しい開発が行われ、ダイヤモンドダストを含浸させた工具を使用し、スラリーを使用していません。ツールは超音波周波数で振動するだけでなく、回転します。ツールを回転させることができない場合は、ワークピースを回転させることができます。
この革新により、深い穴を開ける従来のプロセスの欠点が取り除かれました。たとえば、穴の寸法は+0.125mm以内に保つことができます。従来の工程のように加工速度を落とすことなく、75mmまでの深さの穴をセラミックに開けました。
頻繁に質問
超音波加工では、材料はによって除去されます
A.ツールとワークの間に研磨剤スラリーを使用する
B.ツールとワークの直接接触
C.ワークとツールの間の電解液を2つの間の非常に小さなギャップに維持する
D.ツールとワークの間で急速に繰り返される火花放電によって引き起こされる侵食
回答: オプションA
超音波機械加工(USM)は、可聴範囲を超える周波数でワークピースとワークピースに垂直に振動するツールとの間を循環するグリットを充填した液体スラリーの研磨作用による材料の除去です。
超音波加工では、トランスデューサーの機能は次のようになります
A.機械的エネルギーを熱に変換する
B.電気エネルギーを熱に変換する
C.電気エネルギーを機械的振動に変換する
D.機械的エネルギーを電気エネルギーに変換する
(回答: c)
トランスデューサは、振動電流を機械的振動に変換します。超音波加工では2種類のトランスデューサーが使用されています。圧電または磁歪のいずれか:…磁歪は、材料を通過する磁場が変化したときに、材料の形状をわずかに変化させる効果です。
超音波加工では、工具が動きます
A.横方向に移動します
B.縦方向に移動する
C.横方向に振動する
D.縦方向に振動する
(回答: d)
これらはすべて、超音波機械加工プロセス、それがどのように機能するか、それがどの原理で機能するか、超音波機械加工プロセスの長所と短所は何かに関する情報でした。
この記事が気に入ったら、友達と共有して、下のコメントでフィードバックを送ってください。
産業技術