恐ろしく悪いデザインを避ける:すべきでない 12 のこと
通常、パーツが完璧であることを確認するのに役立つベスト デザイン プラクティスについて書きたいと思います。すべての不気味でハロウィーンの精神で、実に恐ろしい悪い部分を避けるために、「すべきでないこと」に関するサービスライン固有のヒントをいくつか取り上げましょう.毎年何十万もの部品を製造してきましたが、背筋がゾクゾクするような部品をいくつか見てきました。避けるべきことは次のとおりです。
射出成形事故
厚く敷く
肉厚は、成形部品の重要な考慮事項です。壁が厚すぎると、沈み込み、反り、内部空隙 (空気のポケット) が形成されやすくなります。恐れることはありません。肉厚のガイドラインに従うことで、これらの問題を回避できます。注:これは一般的なルールに過ぎないことに注意してください。すべての部品が表に示されている上限と下限の肉厚を持つわけではないためです。
樹脂 | インチ |
---|---|
ABS | 0.045 - 0.140 |
アセタール | 0.030 - 0.120 |
アクリル | 0.025 - 0.500 |
液晶ポリマー | 0.030 - 0.120 |
長繊維強化プラスチック | 0.075 - 1.000 |
ナイロン | 0.030 - 0.115 |
ポリカーボネート | 0.040 - 0.150 |
ポリエステル | 0.025 - 0.125 |
ポリエチレン | 0.030 - 0.200 |
硫化ポリプロピレン | 0.020 - 0.180 |
ポリプロピレン | 0.025 - 0.150 |
ポリスチレン | 0.035 - 0.150 |
ポリウレタン | 0.080 - 0.750 |
ドラフトと半径を実装しない
勾配と半径は、適切に設計された射出成形部品にとって重要です。ドラフトは、材料が金型コアに収縮するため、部品の表面の抗力を抑えて金型から部品を離すのに役立ちます。制限されたドラフトでは、排出システムに過度の圧力が必要になります。部品や金型を損傷する可能性があります。目安としては、キャビティの深さ 1 インチ (25.4 mm) ごとに 1 度の抜き勾配を適用することですが、選択した材料や金型の能力によっては、それでも十分でない場合があります。設計チームに常に確認して、部品に予定しているドラフトが十分であることを確認してください。
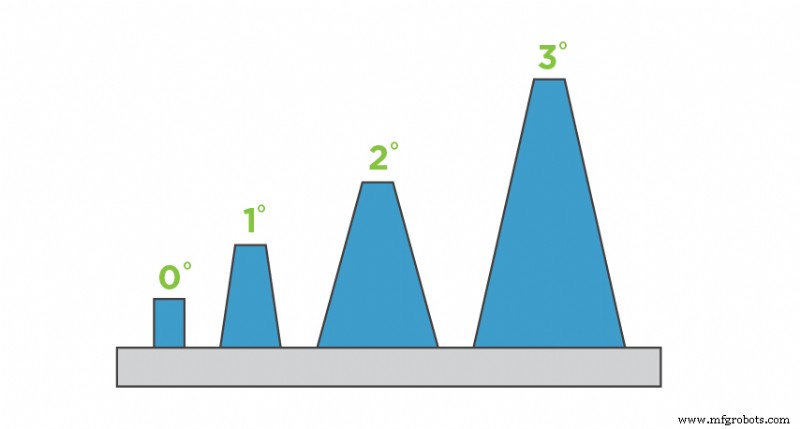
抜き勾配は、金型からのパーツのリリースに役立ちます。さまざまな程度のドラフトがここに示されています。
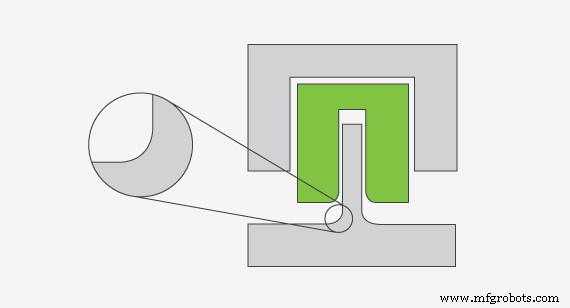
シャープ コーナーは応力集中が高く、塑性流動が阻害されます。対照的に、丸みを帯びた角は応力集中を軽減し、塑性流動を向上させます。
一方、半径は射出成形に必要なものではありませんが、成形品に適用する必要があります。成形品の鋭い角をなくすと、成形品だけでなくマテリアル フローも改善されます。威厳。金型キャビティに充填された樹脂は、丸みを帯びた角の周りでよりよく流れます。プラスチック樹脂は、材料と金型へのストレスを最小限に抑えるために、最も抵抗の少ない経路をたどります。半径を設定することで、パーツの突き出しが容易になり、金型からパーツを取り出すときにパーツが反ったり壊れたりする可能性が低くなります。
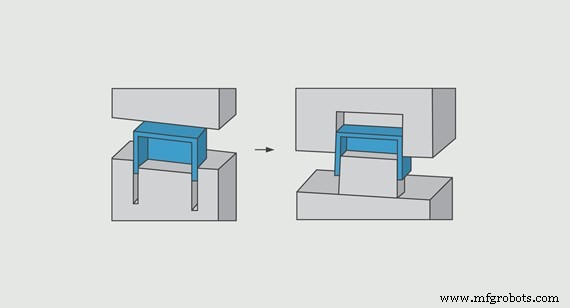
芯抜きやうねりをしない
コアとキャビティは、金型の A 面と B 面 (上半分と下半分) として参照されることがよくあります。部品設計へのコア キャビティ アプローチは、製造時間とコストを節約し、部品全体の外観を向上させることができます。この設計手法では、外壁と内壁が互いに平行になるように下書きを作成する必要があります。この方法により、一貫した肉厚が維持され、部品の完全性が維持され、強度と成形性が向上し、全体的な製造コストが削減されます。
3D プリントの危険
3D プリントのミスの多くは、製造プロセス固有のものです。当社のアディティブ プロセスは互いに異なり、独自の考慮事項があります。ここでは、避けるべき 3 つの印刷上の問題を示します。
高解像度 STL ファイルをアップロードしない
場合によっては、低解像度の STL ファイルを受け取ることがあります。低解像度のファイルがパーツの製造を妨げることはありませんが、美観に影響を与える可能性があります。ほとんどの CAD モデリング ソフトウェアでは、エクスポート設定で解像度を調整できます。 STL が高解像度であることを確認することをお勧めしますが、サイズが大きすぎてアップロードや操作ができないほどではなく、約 100 MB 以下にすることをお勧めします。もう 1 つのオプションは、弊社側で STL に変換できる STP/STEP ファイルを送信することです。
STL ファイル以外にも、ネイティブの SolidWorks (.sldprt) または ProE (.prt) ファイル、および他の CAD システムから出力された IGES (.igs)、STEP (.stp)、ACIS (.sat) またはParasolid (.x_t または .x_b) 形式。
SLS と MJF で縮小を回避しない
収縮差は、成形品の材料分布が不均等な場合に発生する可能性があります。成形品の片面が残りの面に比べて非常に厚い場合、冷却速度が異なります。厚い部分は薄い部分よりも冷却速度が遅いため、収縮する可能性があります。パーツに厚いフィーチャが必要な場合は、フィーチャを約 0.100 インチ (2.54 mm) から 0.125 インチ (3.175 mm) のシェルまで中空にすることをお勧めします。可能であれば、パーツ全体の厚さを大きなフィーチャのシェルの厚さと一致させてください。
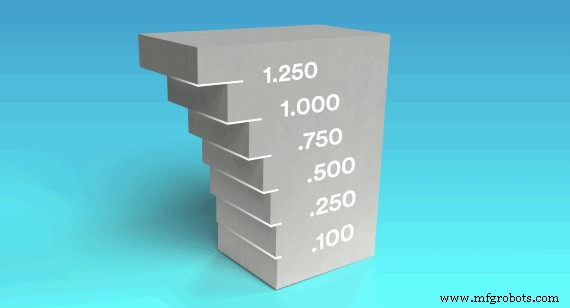
金属 3D プリント パーツの大きなオーバーハングを避けない
部品設計に滑らかな傾斜を提供する自己支持角度とは異なり、オーバーハングは部品の形状の急激な変化です。 DMLS/金属 3D 印刷は、ステレオリソグラフィーや選択的レーザー焼結などの他の 3D 印刷技術と比較すると、オーバーハングのサポートがかなり制限されています。オーバーハングを設計するときは、限界を超えないようにすることが賢明です。オーバーハングが大きいと、パーツのディテールが失われ、さらに悪いことに、ビルド全体がクラッシュする可能性があるためです。金属 3D プリント パーツに関するこの設計のヒントを確認してください。DMLS を使用して複雑で耐久性があり軽量な金属パーツを作成する方法について、より詳しいガイダンスが提供されています。
CNC 加工の間違い
不要な機械加工が必要なフィーチャーを避けない
よくある間違いの 1 つは、機械切削を必要としない領域を持つパーツを設計することです。このような不必要な機械加工は、部品の実行時間に追加されます。実行時間は、最終的な生産コストの主要な要因です。この例を考えてみましょう。この例では、部品の用途に必要な重要な円形ジオメトリが設計で指定されています (右の画像の左側の図を参照)。中央の四角い穴/機能を機械加工し、周囲の材料を切り取って完成部品を表示する必要があります。ただし、このアプローチでは、残りの材料を機械加工するための実行時間が大幅に長くなります。
よりシンプルな設計 (右側の右側の図を参照) では、機械は単純にブロックから部品を切り出すため、余分な材料を追加で無駄に加工する必要がなくなります。この例の設計変更により、マシン時間がほぼ半分に短縮されます。余分な実行時間、無意味な機械加工、および追加コストを避けるために、設計をシンプルに保ちます。
高くて薄い壁を設計に組み込む
CNC マシンで使用される切削工具は、切削される材料と同様に、機械加工の力でわずかに撓んだり曲がったりします。これにより、望ましくない波状の表面や部品の公差を満たすことが困難になるなどの問題が発生する可能性があります。また、壁が欠けたり、曲がったり、壊れたりする可能性があります。壁の高さが高くなればなるほど (当社の最大値は 2 インチ (51 mm))、材料の剛性を高めるために、より厚くする必要がある場合があります。壁の目安は、幅と高さの比率が 3:1 です。垂直ではなく先細になるように壁にドラフトを追加すると、機械加工が容易になり、残りの材料が少なくなります。
小さいテキストまたは浮き上がったテキストの追加
コンポーネントには、加工された部品番号、説明、または会社のロゴが必要になる場合があります。テキストを追加すると、コストも増加します。また、テキストが小さいほど、コストが高くなります。これは、テキストを切断する非常に小さなエンドミルが比較的低速で動作するため、実行時間が長くなり、最終的なコストがかかるためです.一方、パーツが対応できる場合は、より大きなテキストのカットが大幅に高速化され、コストが削減されます。プロのヒント:可能であれば、隆起したテキストではなく、凹んだテキストを選択してください。
板金問題
曲げ線に近すぎるフィーチャの配置
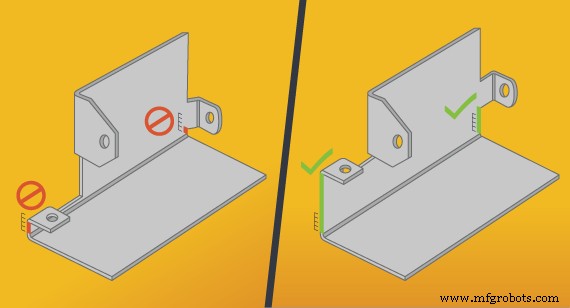
製造中に問題を引き起こす簡単な方法は、穴、タブ、またはその他のフィーチャを曲げに近づけすぎることです。さて、どこまで近づけるでしょうか? 4Tルールに従ってください。すべてのフィーチャを曲げ線から材料の厚さの 4 倍以上離してください。したがって、設計で 0.050 インチ (1.27 mm) の銅を使用するように指示されている場合は、フィーチャに少なくとも 0.200 インチ (5.08 mm) のクリアランスを与えてください。そうしないと、プレス ブレーキでパーツがぎこちなく変形し、誰もそれを望んでいません。
板金の垂直コーナーの設計
プレス ブレーキで板金を曲げる場合、完全な 90 度の角度にはなりません。代わりに、ツールの先端が丸くなっているため、曲げに半径が追加されます。その曲がった部分の長さを測定して 2 で割ると、曲げ半径が得られます。この数値は、それを作成したツールによって定義されます。
最も一般的な内部曲げ半径 (およびデフォルト) は 0.030 インチ (0.762 mm) です。覚えておくべき重要な考慮事項は、外側の曲げ半径 (プレス ブレーキ ツールセットのダイ側で形成されるもの) が、材料の厚さに内側の曲げ半径を加えたものに等しいということです。一部の設計者は、パーツの曲げごとに異なる半径を作成したいと考えていますが、切削コストが最優先の場合は、すべての曲げに同じ半径を使用することを選択します。
ハードウェア仕様を含まない
トップレベルのアセンブリ情報に詳細を含めて、使用するハードウェアの種類を製造元に知らせることを常に忘れないでください。たとえば、セルフ クリンチ ナットを含めたいとします。設計ファイルでこれを指定して、期待するパーツの場所に配置したいものを確実に取得してください。これらの 12 の「してはいけないこと」のヒントに注意することは、出発点として最適ですが、製造プロセスを開始する際には、当社の有能なアプリケーション エンジニアと協力して部品設計に関するアドバイスを提供してください。どの製造プロセスを使用する場合でも、パーツが完璧に仕上げられるように、あらゆる段階でサポートが提供されます。
産業技術