17 第 7 章:リーン生産方式
目的
この単元を完了すると、次のことができるようになります:
- 機械工場で 5S を適用する
- カイゼンのコンセプトを説明する
- リーン生産方式の導入について説明する
リーン 5S:
「5S」とは、「整理」「整頓」「磨き」「標準化」「持続」の5つの言葉からなる職場整理の手法です。これらの単語はすべて文字 S で始まります。これらの 5 つのコンポーネントは、アイテムを保管し、新しい順序を維持する方法を説明しています。意思決定の際に従業員が標準化について話し合うことで、従業員の間で作業プロセスが明確になります。これにより、各従業員はプロセスの所有権を感じることができます。
フェーズ 0:安全性
5Sプログラムを適切に実施すれば職場の安全性が向上すると思われがちですが、これは誤りです。安全はオプションではありません。最優先事項です。
フェーズ 1:並べ替え
必要なものだけを残して、職場のすべてのアイテムを確認してください。
フェーズ 2:まっすぐにする
すべてに場所があり、適切に配置されている必要があります。アイテムは分割してラベルを付ける必要があります。すべてを慎重に配置する必要があります。従業員は繰り返しかがむ必要はありません。使用する場所の近くに機器を配置します。このステップは、リーン 5 が「標準化されたクリーンアップ」と見なされない理由の一部です。
フェーズ 3:輝き
職場が清潔で整頓されていることを確認してください。こうすることで、物がどこにあるのか、どこにあるべきなのかを意識しやすくなります。作業が終わったら、作業スペースをきれいにして、すべてを元の位置に戻します。職場を清潔に保つことは、日課に組み込む必要があります。
フェーズ 4:標準化
作業手順を標準化し、一貫性を持たせます。すべての労働者は、最初の 3 つのステップに従うときに、自分の責任が何であるかを認識する必要があります。
フェーズ 5:持続
基準を評価し、維持します。前述の手順は、操作の新しい標準になるはずです。徐々に古いやり方に戻らないでください。新しい手順に参加するときは、改善方法を考えてください。新しいツールまたは出力要件が提示されたら、最初の 4 つのステップを確認してください。
カイゼン
無駄のない 5S プロセスが無駄の除去に焦点を当てているのに対し、カイゼンは継続的な改善の実践に焦点を当てています。無駄のない 5S と同様に、カイゼンは職場の 3 つの主要な側面を特定します。M ウダ (廃棄物)、M ura (矛盾) と M ウリ(人や機械への負担)。ただし、カイゼンの段階的なプロセスは、無駄のない 5S プロセスよりも広範です。
改善プロセスの概要:
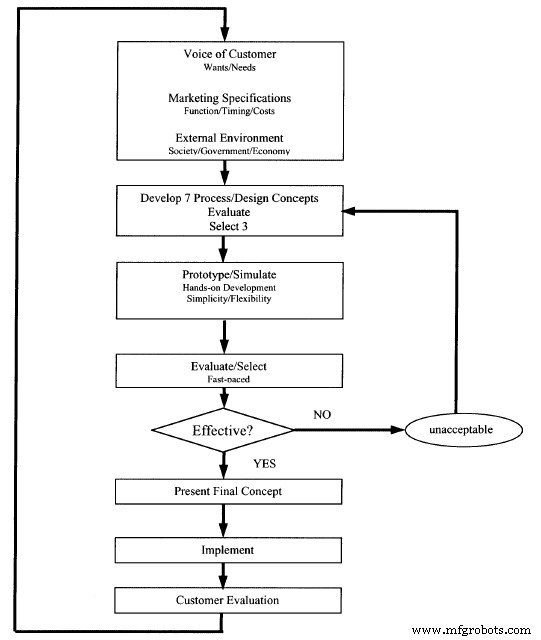
1. 問題を特定します。
2. チームを編成します。
3. 社内外の顧客から情報を収集し、プロジェクトの目標を決定する
4. 現在の状況またはプロセスを確認します。
5. ブレーンストーミングを行い、7 つの可能な代替案を検討してください。
6. 7 つの選択肢の中から 3 つの最良の選択肢を決定します。
7. 実装前にこれらの代替案をシミュレートして評価します。
8. マネージャーにアイデアと提案を提示します。
9. カイゼンの結果を物理的に実装し、その効果を考慮します。
リーン生産方式は時間の経過とともに改善されるため、標準を維持するための教育を継続することが重要です。新しい設備や規則が提示された場合、基準を変更し、労働者を訓練することが重要です。
無駄のない
メンテナンス部門は、社内のさまざまな部門や従業員など、社内の顧客にサービスを提供するものと考えてください。
リーンは、利益を生み出すために規模の経済に依存する従来の西洋の大量生産モデルとは異なります。製品が安くなればなるほど、潜在的な利益率は大きくなります。それは、顧客のニーズの予測、または顧客のニーズの作成に基づいています。需要の異常な変化に対処するのは困難です。
無駄のない生産は、実績のある顧客の要求に応えます。プル処理 – 顧客が生産をプルします。大量システムでは、生産者は製品を市場に投入し、処理を推進します。
改善に重点を置いた長期的な文化を構築します。
よりよく訓練され、教育を受け、より柔軟な労働者を尊重する
リーンは、以下に焦点を当てた哲学です:
<オール>無駄:リソースを使いすぎている (材料、時間、エネルギー、スペース、お金、人的資源、不十分な指示)
廃棄物:
<オール>無駄のない生産には、サプライヤー、下請け業者、販売業者と協力してプロセス全体を合理化することが含まれます。
目標は、コストのかかる開始と停止を回避して、生産がスムーズに流れるようにすることです。
「必要なものを、必要なときに、必要な量だけ生産する」というジャスト・イン・タイムの考え方です。制作プロセスは柔軟かつ迅速でなければなりません。
在庫 =必要なものだけ
大量生産中=念のため。予備の備品や製品は、必要になった場合に備えて保管されます。
用語:
プロセスの簡素化 – 生産の流れの外にあるプロセス
欠陥 – 大量生産システムは、生産の最後に検査を行い、出荷前に欠陥を見つけます。問題は、廃棄物を作るために資源がすでに「費やされている」ことです。生産中、生産の各段階での検査
安全 – 傷ついた時間は無駄な時間です
情報 – 適切なタイミングで適切な情報が必要 (多すぎる、少なすぎる、遅すぎる)
原則:
ポカヨケ – 問題の原因を特定し、原因を取り除いてさらなるエラーを防止するミスプルーフ
判断ミス – プロセス後に問題を見つける
有益な検査 – プロセス中の検査データの分析
ソース検査 – エラーを防ぐためのプロセス開始前の検査。
MEAN LEAN
リーンの単純なコスト削減、ジョブ削減の解釈に適用される用語の 1 つは、ミーン リーンです。多くの場合、現代のマネージャーは、従業員と長期的な関係の重要性を理解せずに無駄を省いていると考えています。
信頼性重視のメンテナンス
信頼性中心の保守は、費用対効果の高い保守プログラムを設計するためのシステムです。それは、統計的に駆動される詳細で複雑なコンピューターである可能性がありますが、その基本はかなり単純です。そのアイデアは、PM システムの設計と操作に適用できます。また、メンテナンス、トラブルシューティング、修理、およびエネルギー作業を行う際の学習にも役立ちます。
これらは RCM のコア原則です。これらの 9 つの基本概念は次のとおりです。
- 失敗はつきもの
- すべての失敗の確率が同じというわけではありません
- すべての失敗が同じ結果になるわけではありません
- 単純なコンポーネントは摩耗し、複雑なシステムは故障します
- 適切なメンテナンスにより、必要な機能を実行可能な最小限のコストで提供
- メンテナンスは、機器固有の設計上の信頼性のみを達成できます
- 不必要なメンテナンスは、必要なメンテナンスからリソースを奪います
- 優れたメンテナンス プログラムは継続的に改善されます
メンテナンスは、コンポーネント、機器、およびシステムが必要なときに意図した機能を確実に提供するために実行されるすべてのアクションで構成されます。
RCM システムは、次の質問への回答に基づいています:
1. 機器の機能と望ましい性能基準は何ですか?
2. どのような場合に、その機能を果たせなくなる可能性がありますか? (最も可能性の高い失敗はどれですか?各タイプの失敗の可能性はどれくらいですか?失敗は明らかですか?それは部分的な失敗でしょうか?)
3. それぞれの失敗の原因は?
4. それぞれの障害が発生するとどうなりますか? (リスク、危険性などは何ですか?)
5. それぞれの失敗はどのように重要ですか?完全または部分的な失敗の結果はどうなりますか?
6. 各障害を予測または防止するために何ができますか?それぞれの失敗を予測または防止するには、どのくらいの費用がかかりますか?
7. 適切なプロアクティブ タスクが見つからない場合 (既定のアクション)、どうすればよいですか (タスクが利用できないか、リスクに対してコストがかかりすぎる可能性があります)?
機器は、いつ、どこで、どのように使用されるかという文脈で調査されます
すべてのメンテナンス アクションは、次のいずれかのカテゴリに分類できます。
- 修正メンテナンス – 失われた、または低下した機能を回復する
- 予防保守 – 機能障害の可能性を最小限に抑えます
- オルタティブ メンテナンス – システムの設計や使用方法を変更して、不満足な状態を解消します
予防保守のカテゴリ内で達成されるすべてのタスクは、次の 5 つの主要なタスク タイプのいずれかに属していると説明できます。
- Condition Directed – 標準と比較した測定状態に基づいて寿命を延ばします
- 時間指定 – 状態に関係なく生命を再生
- 障害の発見 – 障害が発生したかどうかを判断する
- サービス – 消耗品の追加/補充
- 潤滑 - オイル、グリース、その他の潤滑剤
ハードウェアの信頼性は経年劣化しますが、元の信頼性を回復または維持するために何かを行うことができると信じているため、保守を行います。
RCM は信頼性を重視しています。その目的は、システムまたは機器設計の固有の信頼性を維持することであり、固有の信頼性の変更は設計の変更によってのみ達成できることを認識しています。機器またはシステムは、それが機能している状況で調査する必要があることを理解しなければなりません。
リーン生産方式の導入
変更を加える前に、元のプロセスの各ステップを分析する
リーン生産の主な焦点は、コストの削減と売上高の増加、および製造プロセスに付加価値をもたらさない活動の排除です。基本的にリーン生産方式とは、適用と保守が容易なツールと手法を導入することで、企業が目標とする生産やその他のことを達成するのを支援することです。これらのツールと技術が行っていることは、製造プロセスで必要とされない無駄を削減および排除することです.
製造エンジニアは、管の製造に関連する顧客の要件を満たすために、6 シグマ DMAIC (設計、測定、分析、改善、制御) 手法をリーン製造と組み合わせて使用することに着手しました。
製造エンジニアは、チューブ生産ラインの新しいプロセス レイアウトの設計を担当しました。プロジェクトの目的には以下が含まれていました:
- 品質の向上
- スクラップの減少
- 使用場所への配達
- 小ロットサイズ
- プル システムの実装
- より良いフィードバック
- 生産量の増加
- 個人の責任
- WIPの減少
- 食事の柔軟性
変更を加える前に、チームはチューブ生産ライン プロセスの元のレイアウトの各ステップを分析します。
1. 元の状態のプロセスを理解しようとし、問題領域、不要なステップ、付加価値のない部分を特定します。
2. プロセスをマッピングした後、無駄のないチームは材料審査委員会 (MRB) ベンチからデータを収集して、主要なタイプの欠陥を測定および分析しました。プロセスをよりよく理解するために、チームは 20 日間の生産期間の時間調査も行いました。
元の状態では、チューブ ラインは 1 人のオペレーターと 4 つのオペレーションで構成され、プッシュ システムを使用した大きなテーブルで 2 つのステーションに分けられていました。テーブルは、2 番目と 3 番目の操作の間の区切りとして機能しました。
最初に発見された問題は、ラインのアンバランスでした。最初の駅は約 70% の時間使用されました。 2 番目のステーションのオペレーターは、サイクル タイム間の待ち時間に多くの時間を費やしていました。ステーション 1 と 2 を組み合わせることで、個人の責任、オペレーターによる在庫管理、および問題発生時の即時フィードバックに関して、改善の余地が明らかになりました。タイム スタディと部門のレイアウトは、これらの調査結果を反映しています。
2 番目の問題が認識されました。プロセス フローが原因で、生産速度が 2 つのステーションで生産スケジュールを満たすことができませんでした。オペレータはマシン サイクルを見失ったため、マシンはオペレータの注意を待っていました。また、オペレータは最初のステーション (プロセスのボトルネックとなる操作) に部品を押し込み、最後の 2 つの操作で部品の製造を続けました。通常、WIP は長期にわたって積み上げられ、多くの不良品が生産されるまで品質問題は発見されませんでした。
元の状態データは、変更前の過去 20 日間から取得されました。チームは、オリジナルと変更の各ステップを分析します。元のプロセスに関するタイム スタディの調査結果は、サイクル タイムの短縮、ラインのバランス調整、ジャスト イン タイムかんばんの使用とスケジューリングの設計、品質の向上、ロット サイズと WIP の削減、およびフローの改善の基礎を提供しました。新しいプロセス データは、実装の 1 か月後に取得されました。この遅れにより、機械オペレーターはトレーニングを行い、新しいプロセス レイアウト システムに慣れる機会を得ました。
U字型のセルデザイン。部品はすべての顧客の要求を満たします。元工程の表がなくなり、仕掛品がほぼなくなりました。仕掛品の削減と生産量の増加により。
プロセスを改善するために使用された概念には、全従業員の関与 (TEI)、ロットサイズの縮小、スケジューリング、使用場所の在庫、およびレイアウトの改善が含まれていました。部門のすべての従業員と監督者が、プロジェクトのすべての段階に関与しました。彼らのアイデアや提案は、プロセスの変更がより広く受け入れられるように、計画と実装のプロセスに組み込まれました。欠陥が検出される前に生産される部品の数を最小限に抑えるために、より小さなロットサイズが導入されました。 WIP を管理し、プル システムを実装するために、かんばんが (マテリアル ハンドリング ラックの形で) 導入されました。また、セル レイアウトにより、操作間の移動が減少しました。
問題が発生した場合、オペレーターはラインを停止する権限がありました。元の状態では、オペレーションがダウンしても、オペレーターは部品の実行を続けていました。かんばんあり
制御するために、レイアウトにより WIP を保管する機能が排除され、オペレーターはライン全体をシャットダウンする必要がありました。セル レイアウトは、問題や調整に関するオペレーター間のコミュニケーションを改善し、品質を向上させる絶好の機会を提供します。
オペレーターは、マテハン担当者を待ったり、マテハンとして実行したりするために、日々の元の状態のプロセスの検査に多くの時間を費やしていました。 U 字型のセルを使用すると、使用場所への配送がオペレーターにとってより有利になります。オペレータは、簡単に取り出せる 6 台の移動可能なローラー カートに原材料の箱を置きます。 6 箱で 24 時間使用できます。
セットアップ時間を短縮するために、機械の修理や調整に必要なツールはセル内に配置されています。ネジは標準化されていません。ツールはサイズの大きい順に設定され、適切なツールをすばやく識別できます。
3 か月間、プロセスが管理されていることを確認するために監視されました。元の状態と実装されたレイアウトの時間調査を比較すると、シフトあたりの完成品の生産量が 300 から 514 に増加したことが示されました。新しいレイアウトにより、2 回目と 3 回目の操作の間、および梱包ステップでの二重処理がなくなりました。また、プル システムの順序で 4 つの操作すべてを簡単に循環できるようにすることで、全体の時間を短縮しました。顧客の需要は 2 シフトで満たされ、人件費が削減されました。
再設計の結果は次のとおりです:
- 仕掛品が 97% 減少
- Production increased 72%
- Scrap was reduced by 43%
- Machine utilization increased by 50%
- Labor utilization increased by 25%
- Labor costs were reduced by 33%
- Sigma level increased from 2.6 to 2.8
This project yielded reduced labor and scrap costs, and allowed the organization to do a better job of making deliveries on time, while allowing a smaller finished-goods inventory. Daily production numbers and single-part cycle time served as a benchmark for monitoring progress towards the goal. Although the sigma level increase , the 43% reduction in defects, 97% reduction in WIP, and production increase of 72% contributed to the project objective.
Implementing lean is a never ending process; this is what continuous improvement is all
約。 When you get one aspect of lean implemented, it can always be improved. Don’t get hung up on it, but don’t let things slip back to the starting point. There will always be time to go back and refine some of the processes.
Before Lean Manufacturing was implemented at Nypro Oregon Inc., we would operate using traditional manufacturing. Traditional manufacturing consists of producing all of a given product for the marketplace so as to never let the equipment idle. These goods them need to be warehoused or shipped out to a customer who may not be ready for them. If more is produced than can be sold, the products will be sold at a deep discount (often a loss) or simply scrapped. This can add up to an enormous amount waste. After implementing Lean Manufacturing concepts, our company uses just in time. Just in time refers to producing and delivering good in the amount required when the customer requires it and not before. In lean Manufacturing, the manufacture only produces what the customer wants, when they want it. This often a much more cost effective way of manufacturing when compared to high priced, high volume equipment.
Unit Test:
1. What is 5S?
2. Please Explain each “S” of the 5S.
3. Please Explain Kaizen concept.
4. What is the Pull processing?
5. What is the Poka-yoke?
6. What is the six-sigma DMAIC?
7. What is the objectives for a new process layout of the tube production line?
8. Before making changes, The Manufacturing engineers team do what first?
9. Please lists the results of the redesign.
10. The key to implementing lean new idea or concept is to do what?
CHAPTER ATTRIBUTION INFORMATION
This chapter was derived from the following sources.
- Lean 5S derived from Lean Manufacturing by various authors, CC:BY-SA 3.0.
- Kaizen derived from A Kaizen Based Approach for Cellular Manufacturing System Design:A Case Study by VirginiaTech, CC:BY-SA 4.0.
- Kaizen (image) derived from A Kaizen Based Approach for Cellular Manufacturing System Design:A Case Study by VirginiaTech, CC:BY-SA 4.0.
産業技術