13 プラスチック射出成形の問題と解決策
部品製造方法におけるプラスチック射出成形の利点には、生産速度の速さ、高効率、操作の自動化、形状、およびサイズの柔軟性が含まれます。さらに、射出成形品はサイズが正確で、交換が容易で、金型部品を複雑な形状に成形できます。大量生産品や複雑形状品などの成形加工分野に適した環境にやさしい工法です。
しかし、オペレーターはプラスチック部品の成形プロセスにおける特定の機械と操作スキルに精通していますが、金型の設計と材料に関するさまざまな急速な射出成形の欠陥は避けられません。この記事は、主に次のようなプラスチック射出成形の問題と解決策を目的としています:
原材料、プラスチック部品または金型設計、成形プロセスなどから発生するこれらの問題の原因を分析し、関連する解決策を提案します。
1.ショートショット
ショート ショットは、金型キャビティを完全に充填できない現象です。
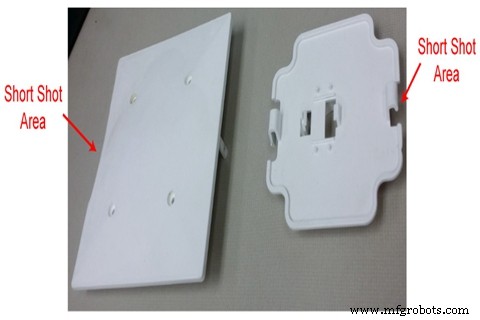
原因: (1) 金型温度、材料温度または射出圧力と速度が低すぎる (2) 原料の可塑化が不均一である (3) 排気が不十分である (4) 原料の流動性が不十分である (5) 成形品が薄すぎる、またはゲート サイズが小さい小さすぎる (6) 不適切な構造設計により、ポリマー溶融物が早期に硬化する
対策: 材料:より流動的な材料を使用してください金型設計:(1)滞留現象を避けるために、薄い壁を埋める前に厚い壁を埋めてください。 (2) ゲートの数とランナーのサイズを適切に増やして、プロセス比率と流動抵抗を減らします。 (3) 排気ポートの位置とサイズを適切に設定して、排気不良の現象を回避する必要があります。
機械:(1) 逆止弁と材料シリンダーの内壁が著しく摩耗していないかどうかを確認します (2) 供給口に材料があるか、ブリッジされていないかどうかを確認します。
プロセス:(1) 射出圧力と射出速度を上げてせん断熱を高めます (2) 射出量を増やします (3) 材料シリンダー温度と金型温度を上げます
2.エアトラップ
エアー トラップとは、キャビティ内に空気が閉じ込められて、パーツ内に気泡が発生することです。
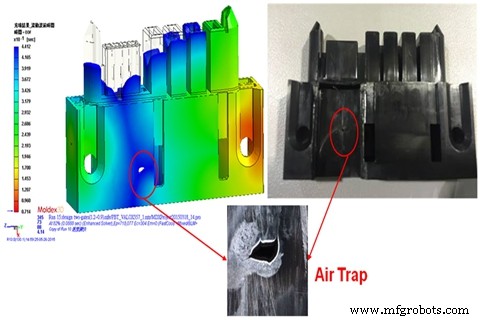
原因: これは、2 つのメルト フロントが合流するときに、パーティング サーフェス、ラム、またはベントから空気が逃げられないことが原因です。
対策: 構造設計:厚みのばらつきを減らし、均一な肉厚を確保するよう努めます
金型設計:(1) 最後の充填場所にベントを追加 (2) ゲートとランナー システムを再設計
プロセス:(1) 最終段階の射出速度を下げる (2) 金型温度を上げる
3.もろさ
脆性とは、プラスチック部分がどこかで簡単に割れたり壊れたりすることです
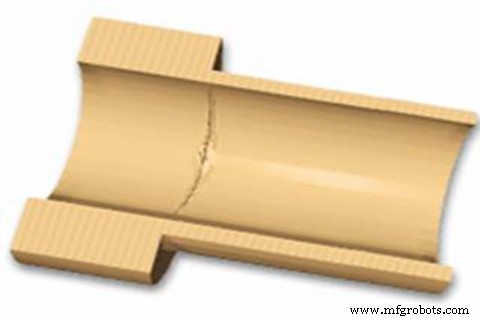
原因: (1) 乾燥した状態は適していません。 (2)射出温度設定が間違っている (3)ゲート・ランナーシステムの設定が適切でない (4)メルトマーク強度が高くない
対策: 材料: (1) 射出成形前の適切な乾燥条件を設定 (2) リサイクル材料の使用を減らし、原材料の割合を増やします。 (3) 高強度プラスチックを使用。金型設計:メインランナー、枝ランナー、ゲートの大型化
機械:適切に設計されたスクリューを選択して、可塑化中の温度分布をより均一にします
プロセス:(1) 材料シリンダーとノズルの温度を下げます (2) 背圧、スクリュー速度、および射出速度を下げます (3) 材料温度と射出圧力を上げ、溶融強度を向上させます
4.焼け跡
焦げ跡は、キャビティ内のガスを時間内に除去できず、フローの終わりに黒ずんでいることです。
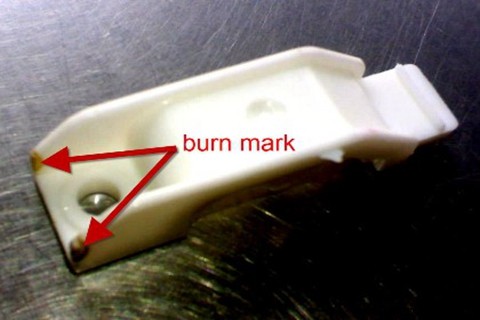
原因: (1)キャビティ内の空気の抜けが間に合わない。 (2) 材料の劣化:溶融温度が高すぎる。曇ったスクリュー速度;ランナー システムの不適切な設計
対策: 金型設計:(1) 排気ガスが発生しやすい場所に排気システムを追加します (2) ランナー システムのサイズを大きくします
プロセス:(1) 射出圧力と速度を下げる (2) バレル温度を下げる (3) ヒーターと熱電対が正常に機能しているかどうかを確認します。
5.フラッシュ
金型パーティングやエジェクタ部に余剰樹脂が存在することを意味します。
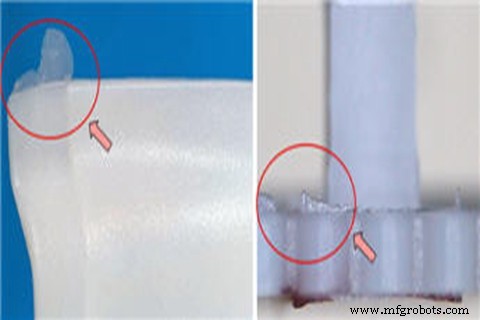
原因: (1) 型締力不足 (2) 金型の不具合 (3) 成形条件の不合理 (4) 排気系の設計不良
対策: 金型設計:(1)金型を閉じたときに金型を閉じることができるように金型を合理的に設計する (2)排気口のサイズを確認する (3)金型表面を清掃する
マシン:適切なサイズのプロセスのマシンを設定します:(1) 射出時間を増やし、射出速度を下げます (2) バレル温度とノズル温度を下げます (3) 射出圧力と圧力を下げます
6.剥離
1層ずつ剥がせる部分の表面を指します。
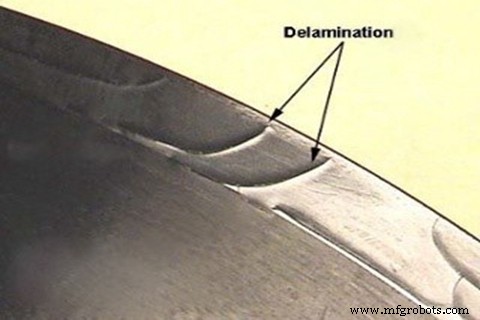
原因: (1) 相容れない他のポリマーの混入 (2) 成形時の離型剤の過剰使用 (3) 樹脂温度の不均一 (4) 湿気の過剰 (5) ゲートと流路の角度が急峻である
対策: 材料:互換性のない不純物や汚染されたリサイクル材料が原材料に混入しないようにする 金型設計:すべてのランナーまたはゲートを鋭角に面取りする
プロセス:(1) バレルと金型の温度を上げる (2) 成形前に材料を適切に乾燥させる (3) 離型剤を使いすぎない
7.ジェッティング
メルトの流れが速すぎるために発生するスプレー跡。通常は曲がりくねっています。
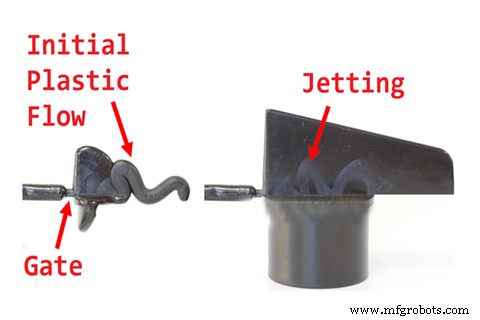
原因: (1)ゲートサイズが小さすぎて、大きな断面積で製品表面に面している (2)充填速度が速すぎる
対策: 金型設計:(1)ゲートサイズを大きくする (2)サイドゲートをラップゲートに変更する (3)ゲート前の止めピンを増やす
8.動線
フロー ラインとは、溶融液の流れが遅いために発生する一種のフロッグ ジャンプとして知られる、製品の表面に波打っている成形不良です。
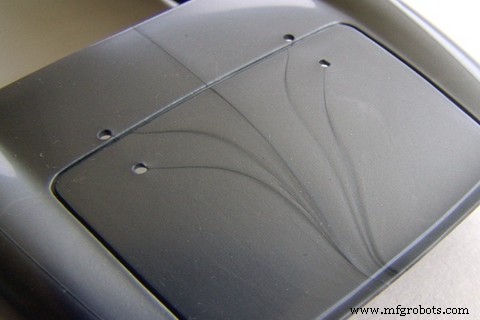
原因: (1)金型温度と材料温度が低すぎる (2)射出速度と圧力が遅すぎる (3)流路とゲートのサイズが小さすぎる (4)製品の構造上、加速度が大きすぎる充填フローが発生すると大きくなります。
対策: 金型設計:(1) 流路内のコールド ウェルのサイズを大きくする (2) ランナーとゲートのサイズを大きくする (3) メイン チャネルのサイズを短くするか、ホット ランナーに切り替える
プロセス:(1)射出速度を上げる(2)射出圧力と圧力を上げる(3)保圧時間を長くする(4)金型温度と材料温度を上げる
9.霧
ゲート付近に雲状の変色が発生。その理由はメルト フラクチャです。
原因: ゲートが小さすぎるか、接着剤のキャビティが薄すぎると、溶融物の流量が大きくなり、破断の面積が小さくなり、せん断速度が大きくなり、せん断応力が大きくなり、多くの場合、溶融物がゴムが壊れて霧シフトが発生します。
対策: モールドフロー シミュレーション。上記の狭いゾーンを通過する溶融物の温度、せん断速度、およびせん断応力を予測することができます。通常、Moldflow では、さまざまなプラスチック材料の温度、せん断速度、およびせん断応力の上限が設定されています。 Moldflow エンジニアは、解析結果に基づいて調整を行い、接着剤入口で適切なゲート サイズとキャビティ壁の厚さを見つけて、曇りをなくすことができます。
10.ストリーク
筋とは、パーツの表面に沿って流れの方向に水、空気、または炭化物が分布しているものです。
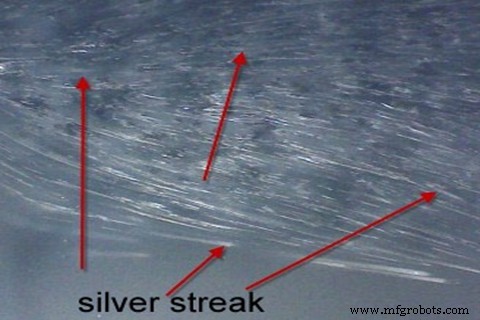
原因: (1) 原材料の水分含有量が高すぎる (2) 原材料に空気が閉じ込められている (3) ポリマーの劣化:材料が汚染されている、バレル温度が高すぎる。不十分な注入量
対策: 金型設計:排気位置が十分かどうかを確認するプロセス:(1) 適切な射出成形機と金型を選択します (2) 材料を切り替えるときは、バレルから古い材料を完全に取り除きます (3) 排気システムを改善します (4) 溶融物を減らします温度、射出圧力または射出速度
11.ヒケ
これは、部品の表面が肉厚で凹んでいる現象です。
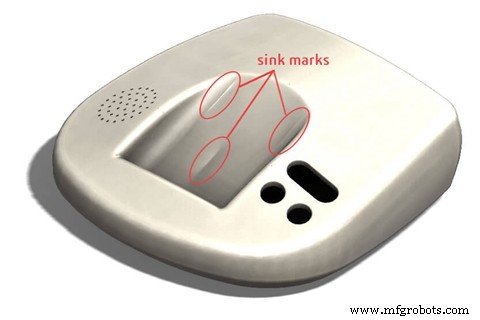
原因:(1) 射出圧力または保持圧力が低すぎる (2)保持時間または冷却時間が短すぎる (3)溶融温度または金型温度が高すぎる (4)部品の構造の不適切な設計
対策: 設計:(1) へこみが発生しやすい表面の凹凸 (2) ワークの厚肉サイズを小さくし、アスペクト比を最小限に抑え、隣接肉厚比を 1.5 ~ 2 に制御し、スムーズな移行を行います。リブ、ざぐり、リブの肉厚を再設計。それらの厚さは、通常、基本的な壁の厚さの 40 ~ 80% として推奨されます。
プロセス:(1) 射出圧力と圧力を上げる (2) ゲート サイズを大きくするか、ゲート位置を変更する
12.溶接線
ウェルド ラインは、2 つの流れが一緒に溶接されることによって生じる表面欠陥を指します。
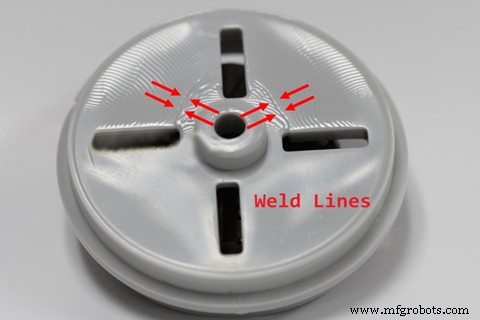
原因: 製造されたパーツに穴、インサート、またはマルチゲート射出成形方法がある場合、またはパーツの肉厚が不均一である場合、ウェルド ラインが生成される場合があります。
対策: 材料:プラスチック メルトの流動性を高める 金型設計:(1) ゲートの位置を変更する (2) 通気スロットを追加する プロセス:(1) メルト温度を上げる (2) 離型剤の量を減らす
13.反り
プラスチック部品の設計と製造において解決が最も困難な問題は、反りです。
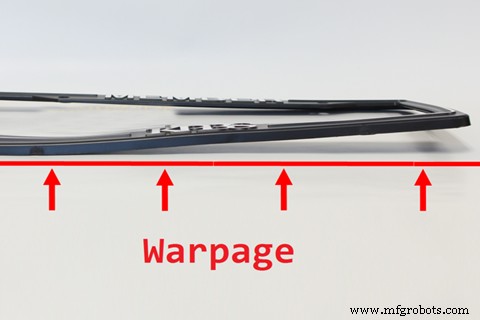
原因: (1)金型構造:注入、冷却システム、および排出システム (2) 製品構造:プラスチック部品の肉厚の変化、湾曲または非対称の形状、リブおよび BOSS カラムの設計が合理的でない (3) 製造プロセス:プラスチック部品が適切でない完全に冷却され、射出曲線と保圧曲線が不合理です (4)プラスチック材料:プラスチック材料には、フィラーが追加されておらず、収縮のサイズがあります。
対策:(1) 金型温度が安定しない。冷却・加熱バランスのとれた金型の提供 (2)断面肉厚の不均一化 樹脂特性に合わせた製品形状・サイズの再設計
WayKen では、プロトタイプの射出成形のいくつかのケースで、多くの同様のプラスチック射出成形の問題と解決策に遭遇しました。お客様のために射出成形製品を作成するために、射出成形機の部品の詳細と射出成形の段階を、部品の製造前および射出成形プロセス中に慎重に検討しています。
産業技術