航空機の設計 (パート 2):視野を広げる
投稿日:2020 年 12 月 25 日 | By WayKenラピッドマニュファクチャリング
現代のエンジニアリングの意思決定者は、この段階で過剰な計算能力を使用することは役に立たず、時間の浪費になると考えています。近似を含む手法の採用は、はるかに効率的であり、パラメトリック モデリングの実行に必要な時間を短縮するのに役立ちます。このような手法には、システムの数学的複雑さを軽減しながら、支配的な偏微分方程式の物理的特性をそのまま維持することを保証する低次数モデリングが含まれます。
最初の分析が行われた後、最適化のための設計の変更が結果によって指示される反復手順が開始されます。この手順は、概念設計フェーズと予備設計フェーズの間のリンクです。詳しくは工業デザインプロトタイピングをご覧ください。
プロジェクト統合プロセスの有名なハウ モデルの要約形式を見てみましょう。
- これは実現可能性調査の延長と見なされますが、より詳細で複雑なものが含まれます。
- このプロセスの最初の段階は、1 つまたは複数の構成の選択です。
- 第 2 段階は、飛行体制と動力装置の選択として知られています。この段階で、マッハ数などの特定の一連の動作条件に対して、選択するパワープラントのタイプが絞り込まれます。つまり、ターボプロップ、ピストンプロップ、ターボファン、低バイパス ターボファン、ターボジェット、ラムジェットなどです。
- 次の段階は、機体レイアウトの選択に関するものです。ペイロードの詳細は、多くの場合、この段階の背後にある推進要因です。これは、航空機の質量を最初に予測するための良い出発点となります。
- 次は翼の構成です。これは、多数のパラメーターが関係する空気力学ラボにとって複雑な手順です。これは、予備設計プロセスの基本的な段階です。これは、航空機の揚力、抗力、質量の初期推定につながり、後続の解析が行われた後に翼荷重の推定計算を達成するのにも役立ちます。翼面荷重の推定は、さまざまな飛行条件の経験的データに従って調整された理論式に基づいて行われます。また、推力と重量の比率を概算するのにも役立ちます。
- 最後に、パラメトリック分析の段階に入ります。第 1 段階では、翼と胴体の寸法を組み合わせて、各飛行フェーズの一連の結果を生成します。これにより、デザインスペースが形成されます。パラメトリック解析の第 2 段階では、適切な翼荷重と推力/重量比のセットが選択されます。
- パラメトリック解析の第 2 段階では、選択したデータ セットを組み込み、航空機の全体的な質量を計算します。最適な質量値を提供するセットを使用してレフリー デザインを作成し、それを詳細な分析と評価に使用します。
- 審判のデザインが評価され、次の情報が提供されます。
- コントロール サーフェスの推定サイズ
- 着陸装置のレイアウトを完成させるのに役立ちます
- 揚力、抗力、質量の値のより良い推定
- 調整された入力データと複雑な推定方法に基づくパフォーマンス特性の計算の修正
- 質量収束基準が満たされるまで手順が繰り返されます
- この設計フェーズの最後に、グラフィックスまたは数学的手法を使用して重要な設計領域を特定する感度設計スタディが実施されます。さらに、油圧、電気、消火、防氷、空気圧システムの設計など、他の活動も同時に進行しています。
次の段階、つまり詳細設計段階では魔法が起こります。つまり、設計が完全に定義され、テスト用の縮尺モデルが試作品製造業者に注文され、その後、組立設計と製造設計に基づいた最終図面が実際のトポロジーとともにレイアウトされます。 、形状、寸法、公差、および材料仕様。これについては、次のセクションで詳しく説明します。
詳細設計
この段階の焦点は、主に、前の段階で概説した設計手順の検証を得ることです。これは、設計プロセス全体の中で最も広範なフェーズです。各パーツの最終設計、試作、テストに焦点を当てています。予備設計段階で取得したデータに基づいて、この段階ではコンピューター支援設計およびコンピューター支援製造パッケージを使用して設計活動をサポートします。
検討中の要素は、パフォーマンス、製造コスト、所要時間、運用効率の 3 つです。包括的な結果を得るには、地上試験と飛行中試験の 2 種類の試験手順が必要です。両方のタイプの詳細を見てみましょう.
- 地上試験: これには、CFD パッケージの結果を検証するための風洞試験、構造試験、アビオニクス評価、およびシステム チェックが含まれます。これは、プロトタイピングが時間を節約する段階です。コストと貴重な時間を節約するためには、初期テスト用にスケーリングされたパーツのプロトタイプを作成することが重要です。優れたプロトタイピング サービス プロバイダーは、適切な専門知識を使用して、必要な材料仕様から構造を作成します。プロトタイプを使用して、強度、剛性、フラッター、弾性安定性、およびその他のシステム パラメータを解析できます。静的荷重、動的荷重、振動モーダル解析、およびフラッター解析は、実行する重要なテストの一部です。スケーリングされた航空機部品の場合、ステレオリソグラフィー 3D プリントは、概略設計と実験結果との間の包括的な評価に必要な精度を提供します。
- 飛行中のテスト: 実際の航空機の性能と飛行特性を検証するための認証機関の関与。これらの機関は、耐空性当局として知られています。彼らは、連邦航空規則の耐空性基準で概説されている事前設定された設計と安全要件に基づいて、航空機の設計を評価します。次の表は、すべての耐空基準とそれぞれの使用法を包括的にまとめたものです。
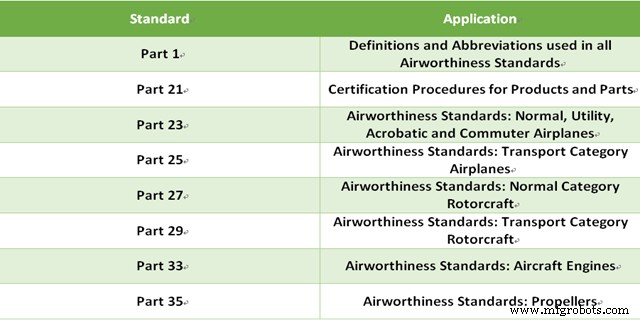
これらの基準の中で最も注目に値するのは、最大離陸重量 (MTOW) が 12,500 ポンド未満で、乗客定員が 9 人以下の通常の、実用的な、およびアクロバット航空機に適用される FAR Part 23 です。また、MTOW が 19,000 ポンド以下で、乗客定員が 19 人以下の通勤用飛行機の基準も定めています。
エアバス A320 やボーイング 737 などの商用輸送カテゴリの航空機については、FAR Part 25 が必要な基準を定めています。パート 25 には、A、B、C、D、E、F などのさまざまなサブパートが含まれており、すべてが民間輸送機のさまざまなシステムとサブシステムの基準を定めています。
同様に、回転翼航空機 (最も一般的にはヘリコプターとして知られている) については、FAR Part 27 および 29 がそれぞれ通常および輸送カテゴリの基準を定めています。耐空性認証を取得した後、設計サイクルは実質的に、この段階で発生するライフサイクル コストの 95% で終了します。その後、大規模な製造段階が続きます。
航空機の設計プロセスを完了する
航空機の設計サイクルに関するこの詳細なレビューは、非常に複雑に思えるかもしれません。ただし、段階的なアプローチ、批判的思考に基づく成熟した意思決定、および賢明な意思決定により、航空機の設計サイクルは達成可能な偉業です。コストと時間の両方の面でリスクが高い現代では、航空機設計の成功は設計アイデアの包括的な検証に完全に依存しているため、必要なときに必要な場所でプロトタイピングを使用することが不可欠です。しかし、プロトタイプの精度は非常に重要であるため、航空分野では適切なプロトタイプ メーカーのサービスを提供することが非常に重要です。最近のボーイング 737 Max の場合のように、設計サイクルのどの段階でも近道をすると、後で破壊的であることが判明します。
製造プロセス