射出成形部品の設計パート4:ワープ
私たちは、射出成形部品で発生する可能性のあるさまざまな課題と欠陥について話してきました。これは、外観上の欠陥、これらの部品の内部応力を引き起こし、市場投入の遅れを引き起こす可能性があり、これらの問題を防ぐための射出成形部品の設計方法です。射出サイクル後の射出成形部品の反りについては、言及しましたが対処しなかった1つの領域です。これは、新たに成形された成形品のプラスチックの冷却差が原因で発生します。これは、材料の厚さ、内部の特徴または壁の接合部、成形品のアスペクト比、および射出成形プロセスの変化が原因である可能性があります。
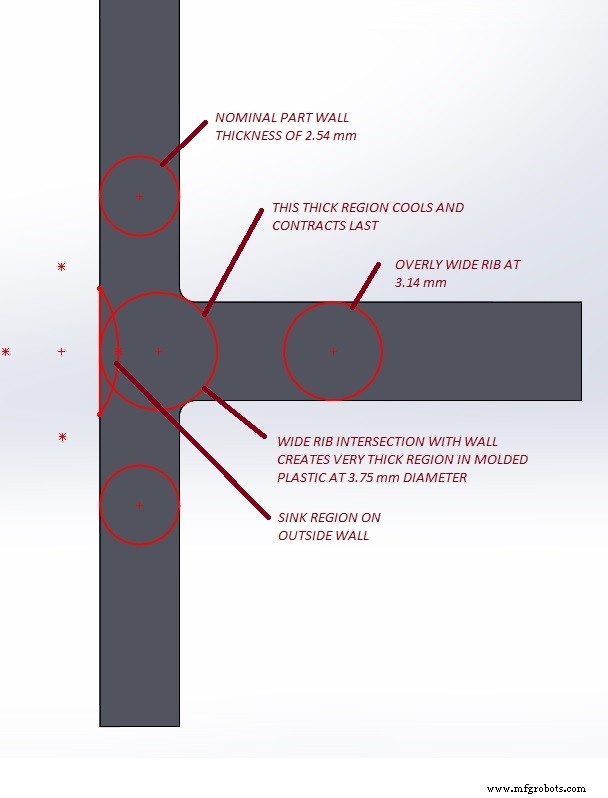
射出成形されたプラスチック部品の反りは、実際にはそれ自体の課題であり、少し驚く可能性があります。 3D設計CADファイルを使用したモールドフロー解析はこれを予測するのに役立ちますが、パーツジオメトリだけでなく、ワープに影響を与えるいくつかのパラメータがあるため、予測は正確ではありません。多くの場合、予測される少量の反りは、プラスチック部品の内部応力としてより深刻になる可能性があり、部品作成後のプラスチック材料のコールドフローは、製品の組み立て時に見過ごされない曲げを引き起こす可能性があります。新しいプラスチック部品の設計の多くの適合、形状、および機能の側面は、プロトタイプの段階で確認できますが、機械加工または印刷された部品を使用して、反りが必ずしもここに現れるとは限りません。

これらの理由から、いくつかの一般的なガイドラインに従って、徐々に変化する比較的一貫したプラスチック部品の壁の厚さを維持し、最近説明したリブとボスのサイズに関する推奨事項に従うことが重要です。ただし、これだけでは必ずしも十分ではありません。必要な機能やスタイルに起因する一部の製品設計は、射出成形部品の反りを防ぐことに関して、依然として重大な課題を抱えている可能性があります。鋭い角、非常に大きな平らな側面、非対称または開いたパーツの形状はすべて、意図した形状とフィット感を維持する上で問題が発生する可能性があります。
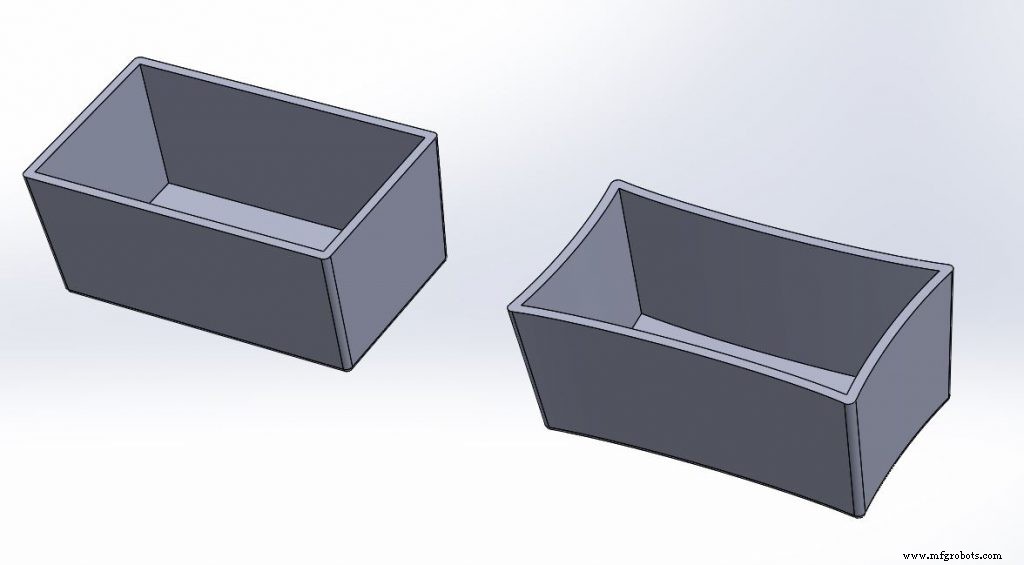
古典的なワープの欠陥は、側壁が内側に変形した5面のエンクロージャーピースです。パーツの壁の厚さはエンクロージャーの5つの側面すべてで比較的一定ですが、コーナーはより厚いセクションを表すことができ、冷却と収縮が遅くなり、パーツの壁の内側を外側よりも強く引っ張ることができます。
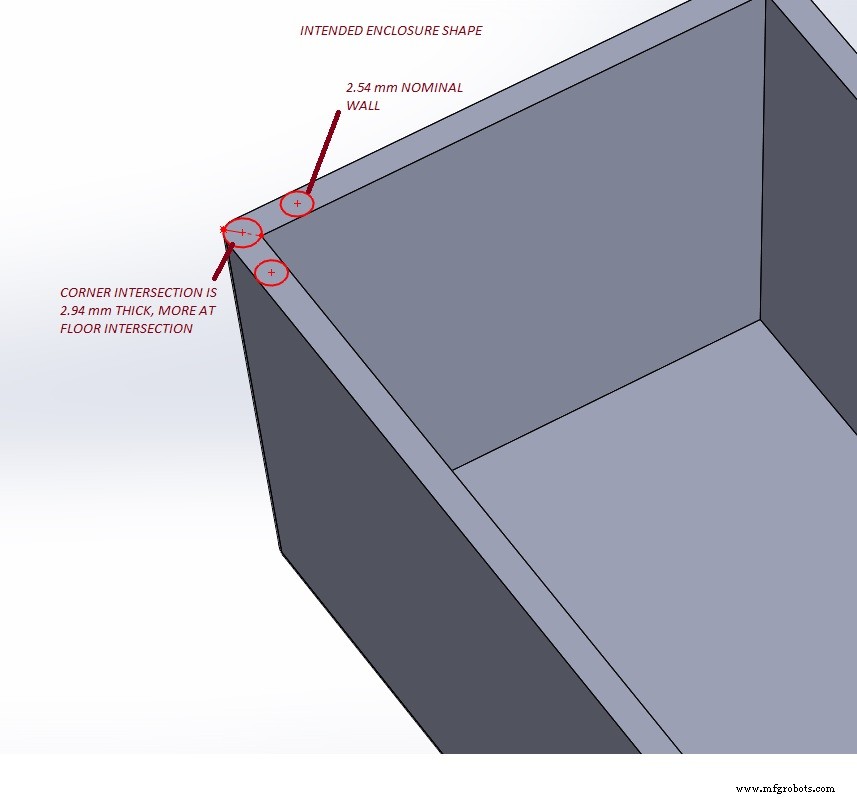
これらのコーナーでは、厚さやコアリングレリーフの追加に注意する必要があります。 1つのオプションは、パーツの外側のコーナー半径を大きくし、内側のフィレットの半径と共通の肉厚を維持することです。
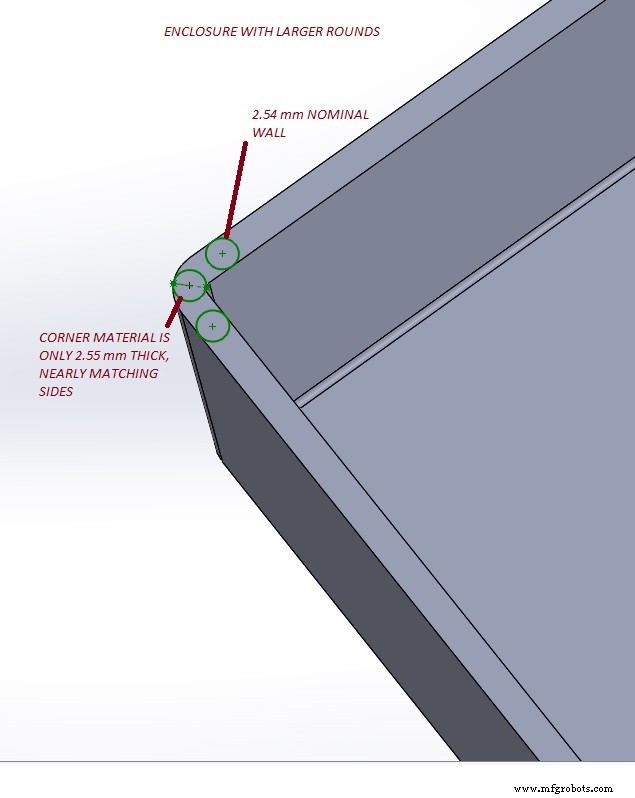
あるいは、製品の外側でより鋭いエッジのある外観が必要な場合は、コアのある内側の角が鋭い内側の角によって局所的に厚さを薄くすることができます。
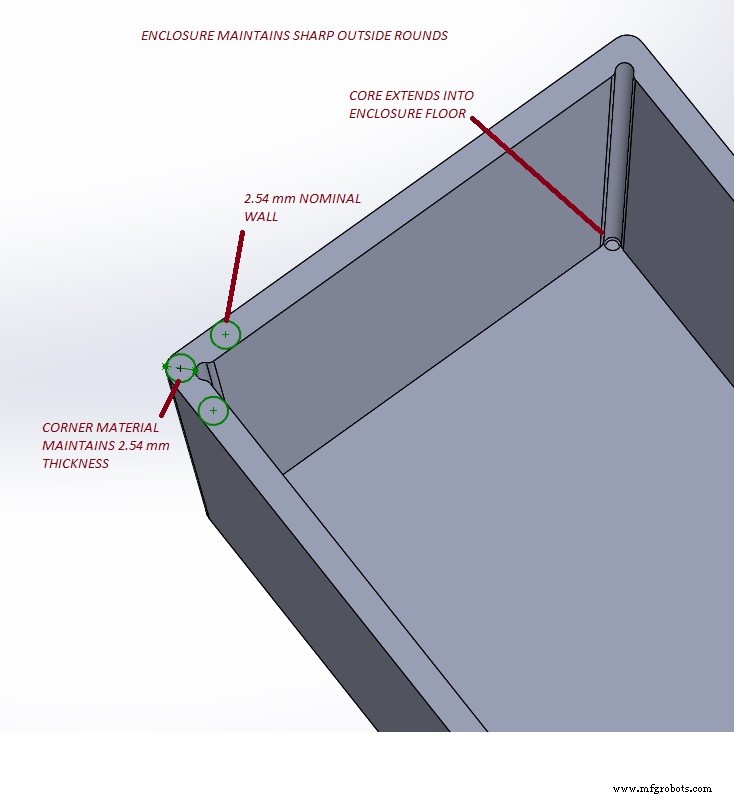
前述のように、このコアリングアプローチは、側壁と床壁の交差点にも適用されます。
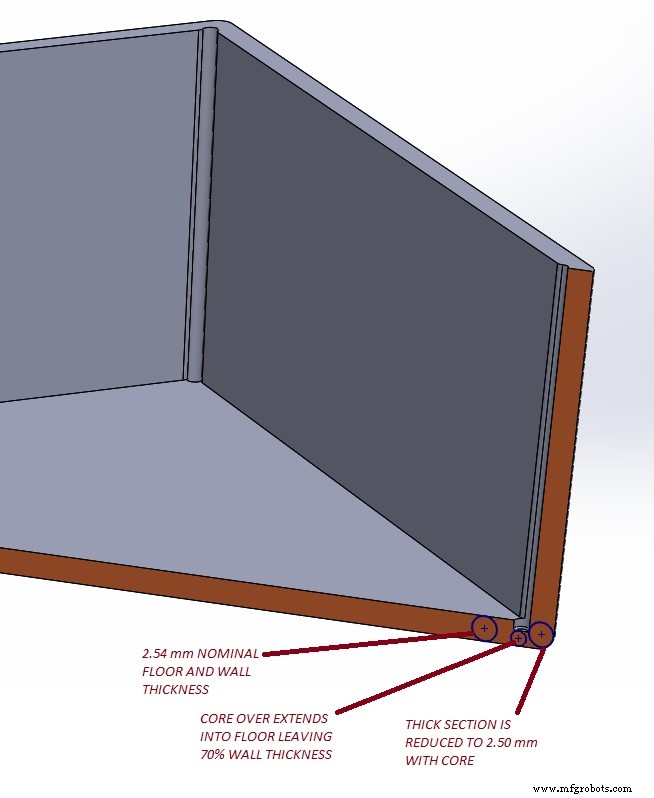
大きな平面で設計された製品は、イメージを再ブランド化し、競合他社との差別化を図りたい企業にとって、明確でクリーンでモダンな外観を備えています。しかし、このようなプラスチック部品には、より大きな表面全体の平坦性を維持するという独自の課題があります。
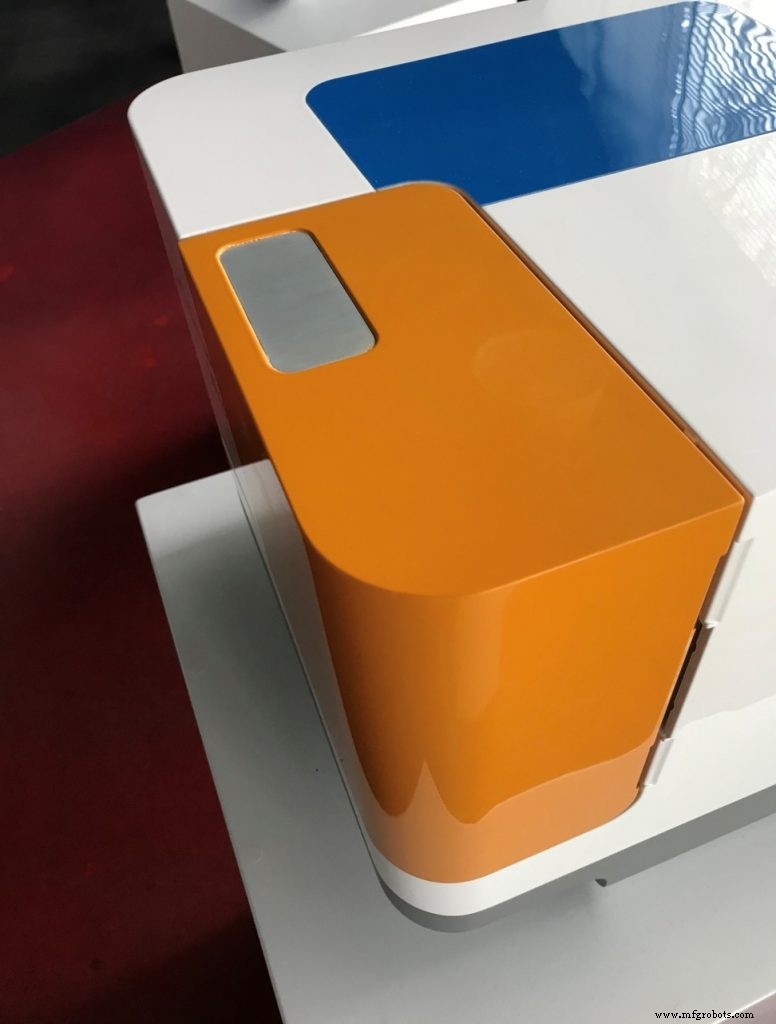
光沢のある仕上がりで、たるみ、くぼみ、ずれが強調され、非常に目立ちます。反射光を魚に向けると、表面が奇妙に見えることがあります。ラボ機器のProteinSimpleラインの部品(WESモデルを示しています)には、必要な直交外観を最適化するためのドラフトすらありませんでした。これらの部品は構造用発泡プラスチックを使用して成形されていますが、このプロセスは、シンクと反りの懸念の一部を軽減するだけです。完璧な部品を得る秘訣は、壁の厚さの急激な変化を最小限に抑えて部品を設計し、成形チームと緊密に協力して必要な平坦度を伝え、冷却時の反りを防ぐための射出後固定具の考案を支援することでした。
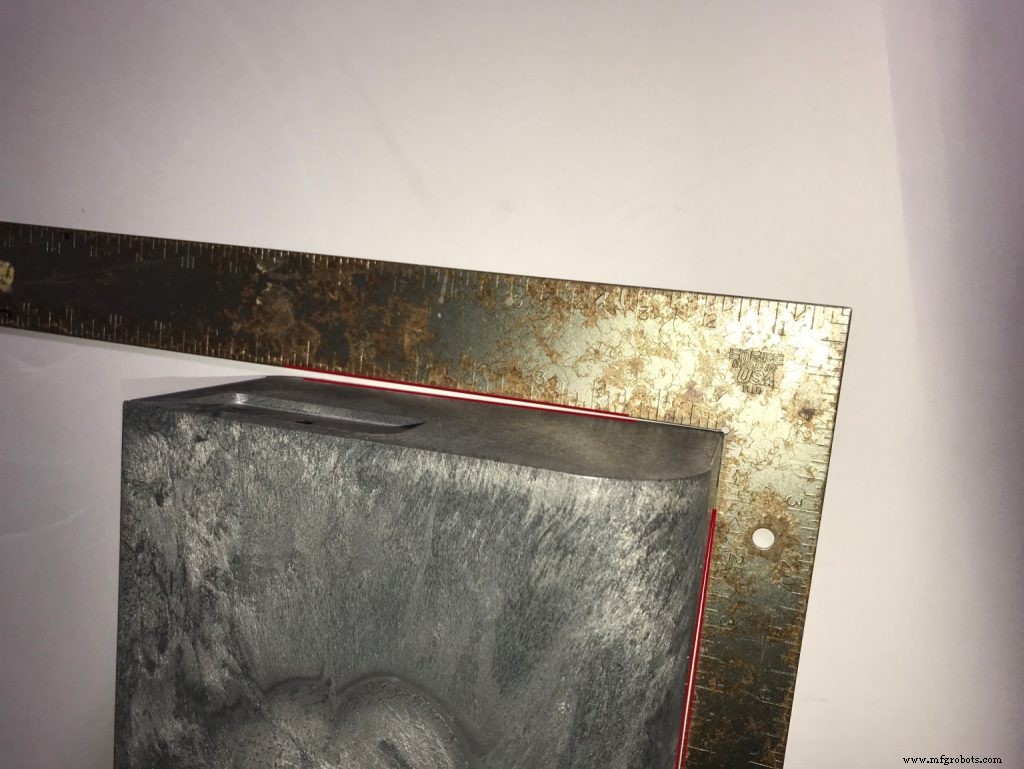
部品の生産量が少ないため、フィクスチャは実行可能なオプションでしたが、目的の結果を達成するように設計する必要がありました。多くの場合、成形業者は、公差を満たし、設計図のコールアウトを形成するように独自の固定具を設計します。これらの器具は、StudioRedの製品設計チームとモールドハウスによって共同開発されました。
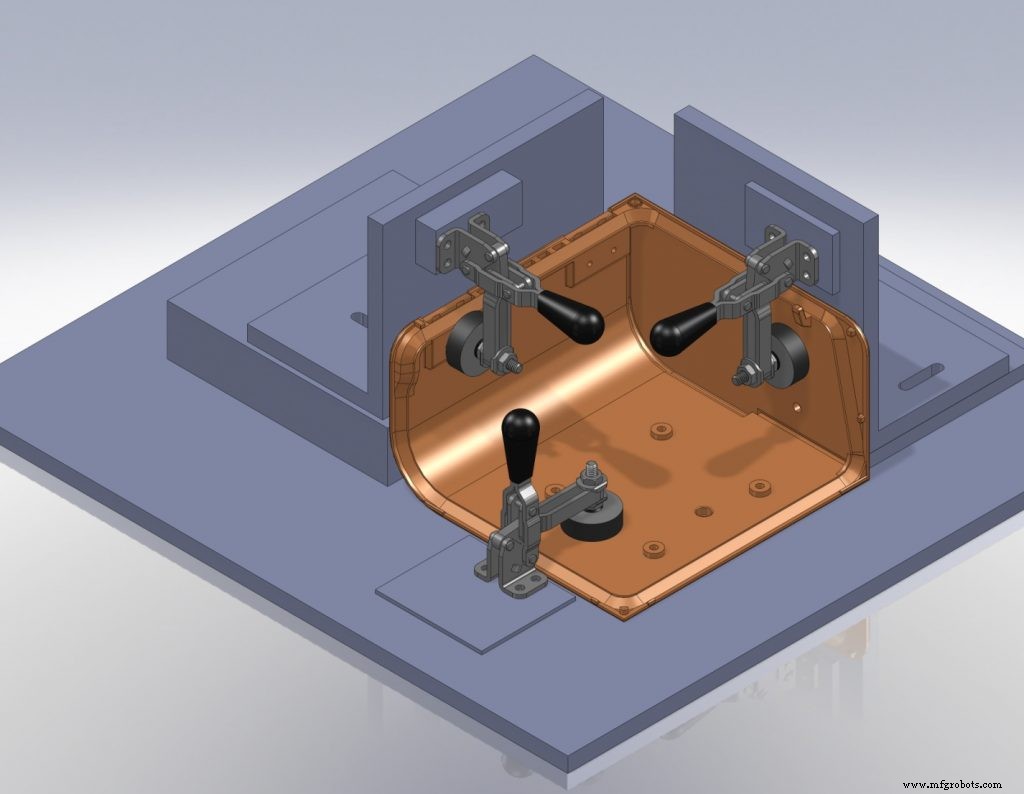
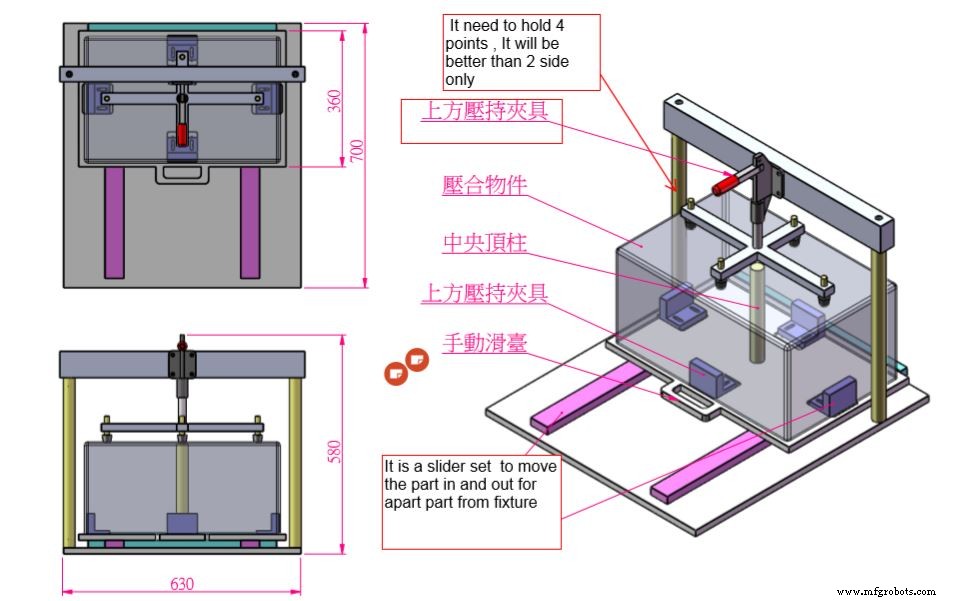
エンジニアリングとフィクスチャの使用における余分な努力により、Protein Simpleの新製品の外観に望ましい結果が得られ、追加の手仕上げの反り部品よりも低コストでした。新しい外観は、デザイン賞を受賞しただけでなく、意図したブランドメッセージを市場に送り出し、最初の1か月で売上が6倍に増加しました。
平坦性と位置合わせが重要なプラスチック成形の課題と、厚い部分が意図した形状をどのように歪める可能性があるかについて見てきました。射出成形されたプラスチック部品は、組み立て、部品の破損、またはベントなどの他の機能要件によって駆動される大きな開口部または欠落領域を持つように設計される場合もあります。これらの非対称形状とプラスチックの薄いスパンは、反りにつながる可能性があります。これは、ラックマウント型サーバー、スイッチ、およびストレージ製品のベゼル設計ではしばしば課題になります。
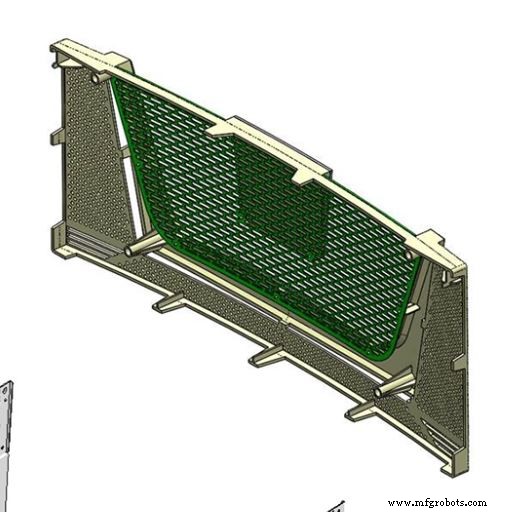
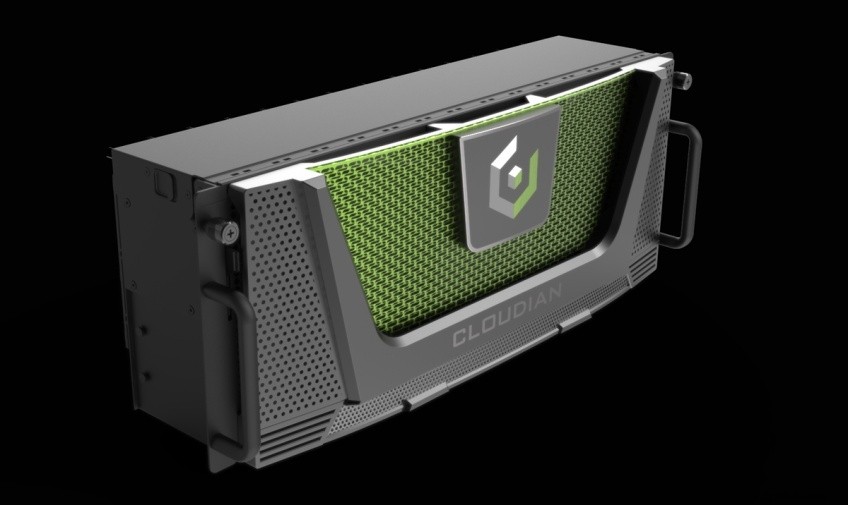
ベゼルは、ラックに取り付けられた製品にブランドを提供し、一般的な金属製のシャーシの上に持ち上げるための鍵となる可能性があります。また、セキュリティを提供し、OEMベンダーのハードウェアプラットフォームを偽装します。
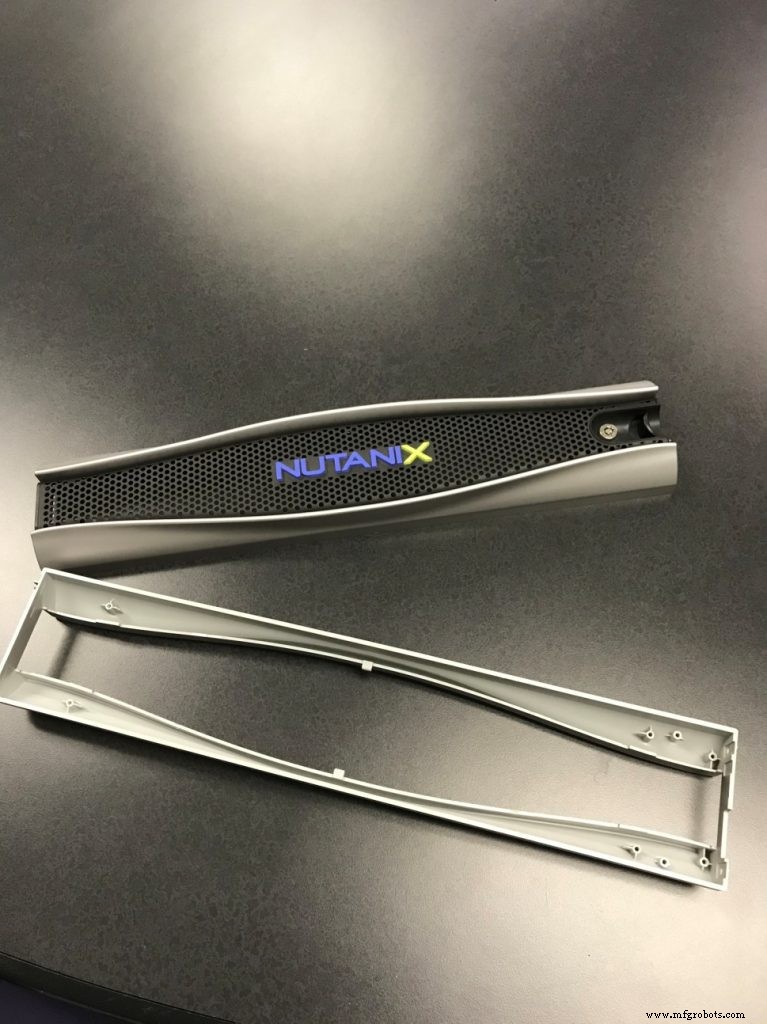
ベゼルの射出成形部分があまりにも素晴らしくなりすぎたり、通気開口部、アクセス、その他の部品の適合ニーズを満たすために非常に大きな開口部を橋渡しする必要がある場合、部品はブリッジングセクション全体で簡単に反ります。
成形プロセスがさらにダイヤルインされるときに、2番目の物品のプラスチック部品が撃たれるまで、部品の反りは明らかにならない場合があります。
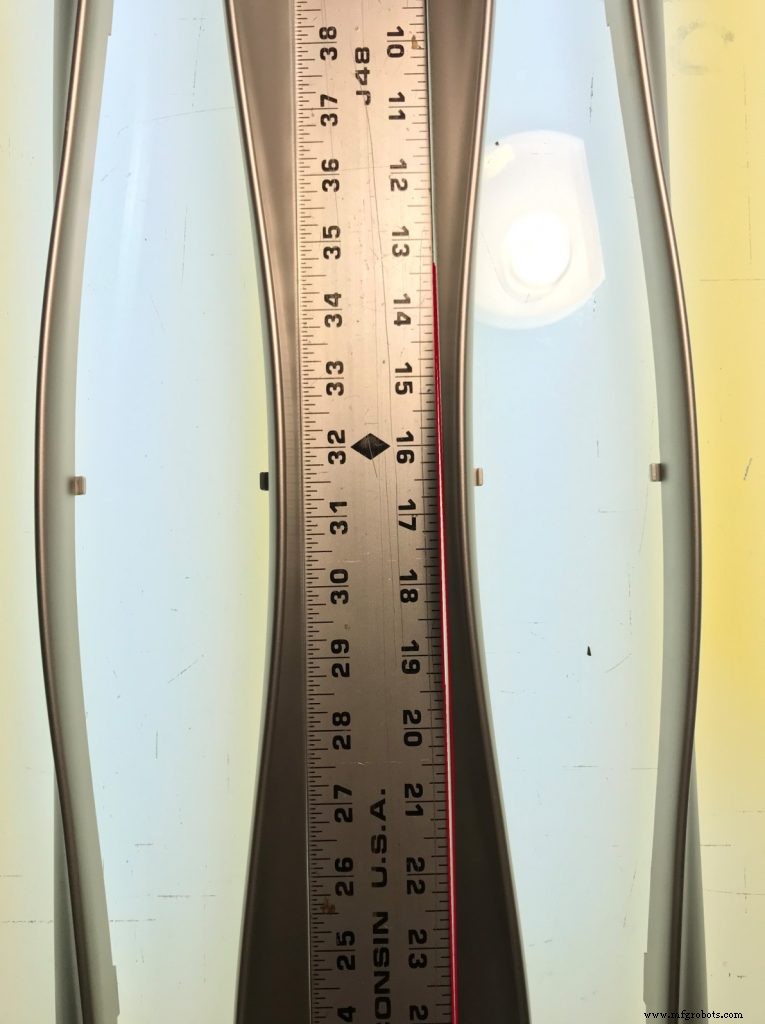
多くの場合、金属製のパフォーマンススクリーンなど、他の部品からの追加の構造的サポートは、取り外し可能であるか、材料とコストの目標のために非常に正確に形成されない可能性があるため、期待できません。
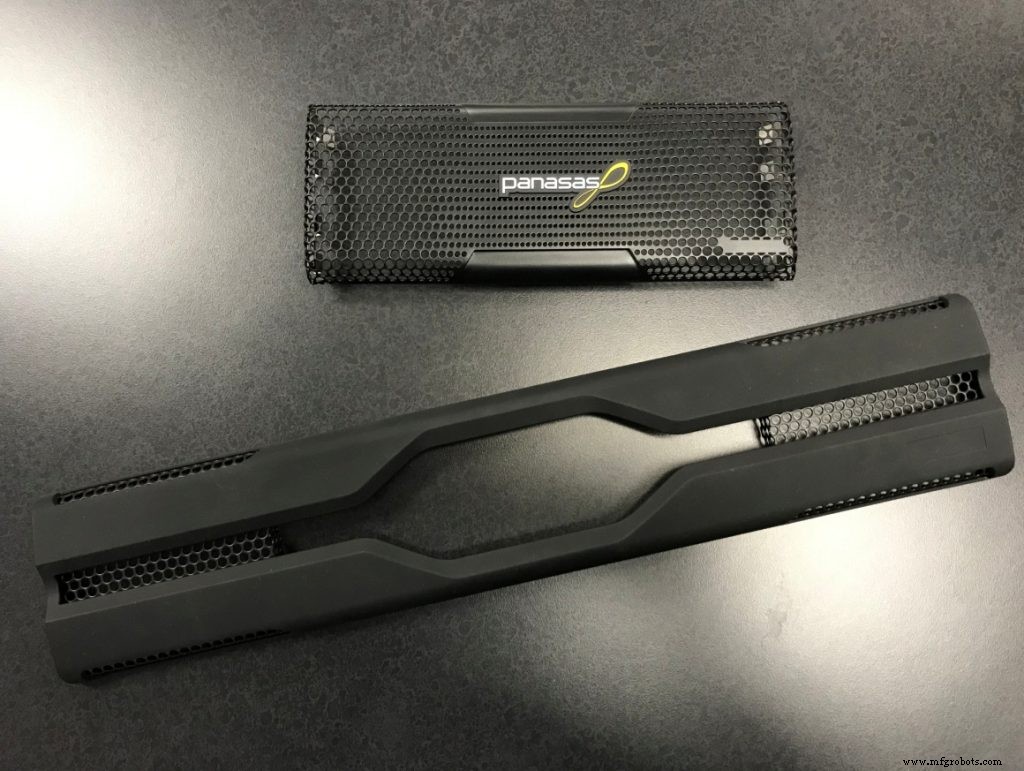
成形品または偏心断面に大きな開口領域がある射出成形ベゼル部品に関するこれらの課題は、成形品全体の材料の厚さと遷移を綿密に検討し、成形チームと緊密に連携し、プロセスと冷却時間を調整し、射出後を追加することで解決しました。より極端な場合には、成形後にプラスチック部品の形状を保持するための固定具。
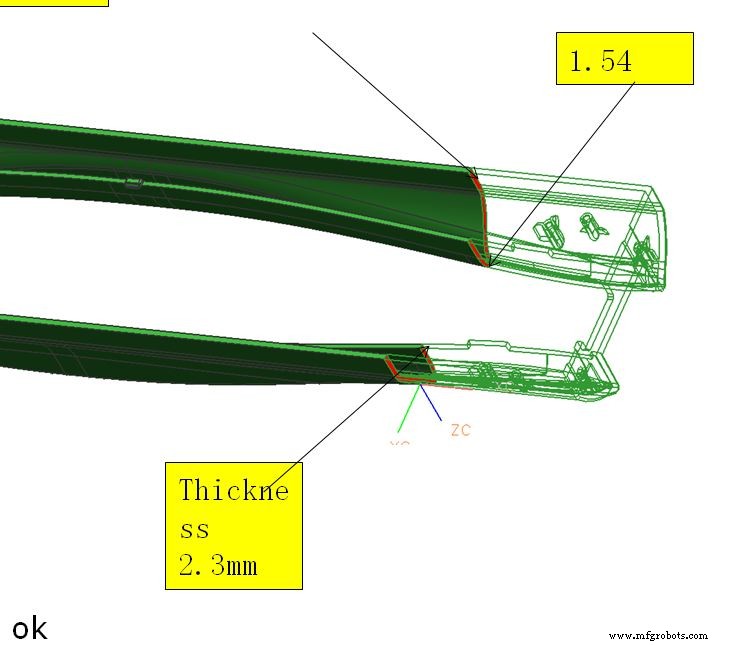
その結果、さまざまなシャーシにうまく適合し、差別化を図りたい企業にブランド定義を提供する高品質のコンポーネントが実現しました。
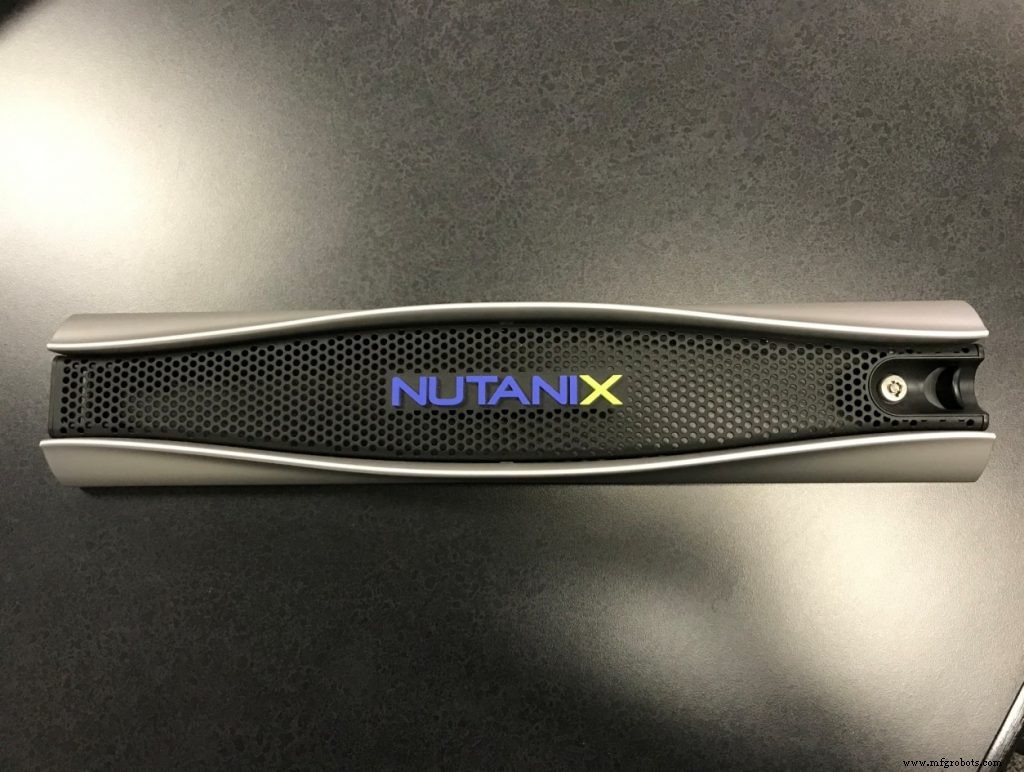
したがって、反りは一部の部品設計にとって課題となる可能性がありますが、最初の金型ショットでの驚きでさえ、部品の厚さに関する基本的な設計ガイドラインに従い、成形チームと協力することで問題を迅速に解決し、意図したとおりに機能するハイエンド製品設計を生み出すことができます。必要です。
このようにもっと見る:アンダーカット、シンクマーク、ボス
製造プロセス