射出成形部品の設計パート2:シンクマーク
射出成形部品を使用した製品開発では、私たち全員が見栄えの良い製品を求めています。そして、ビジネスでは、グリッチや遅延のために時間、ひいてはお金が実際にはないため、プロジェクトをスムーズに進めることを望んでいます。そのため、正面に大きなヒケがあります。最初の製品の射出成形部品の表面で、製造時にも光沢のある仕上がりになるはずです。これは、これを修正する方法と修正する方法の沈下感につながる可能性があります。それは速い。
何をすべきか?製品のロゴバッジをその上に接着することもできますが、それはすでに他の場所に配置される予定であり、部品の射出成形ゲートを非表示にします。多分別のバッジ?射出成形金型処理と部品設計の両方でこれを修正するためのより良い方法があります。
- <図>
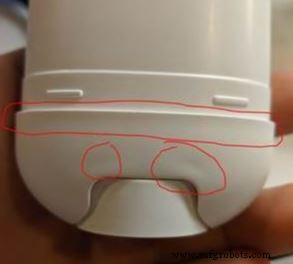
では、なぜシンクが発生するのでしょうか。成形品の射出成形されたプラスチック材料の差動冷却は、通常、内部のリブまたはボスが壁に結合する場所のように、プラスチック部品の壁の厚い部分で、厚いセクションの中央が最後に冷却されるときに材料を引き込み、ディンプルを残します反対側。これは、特に暗いプラスチック色の滑らかで光沢のある表面でより顕著に見えます。
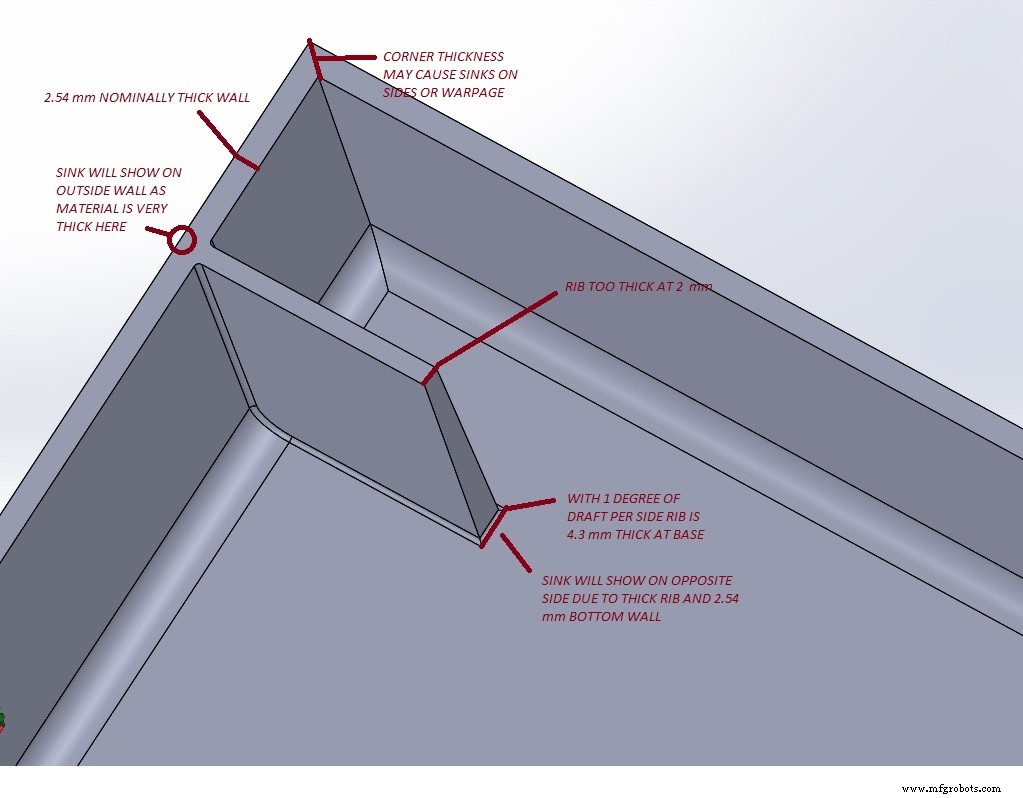
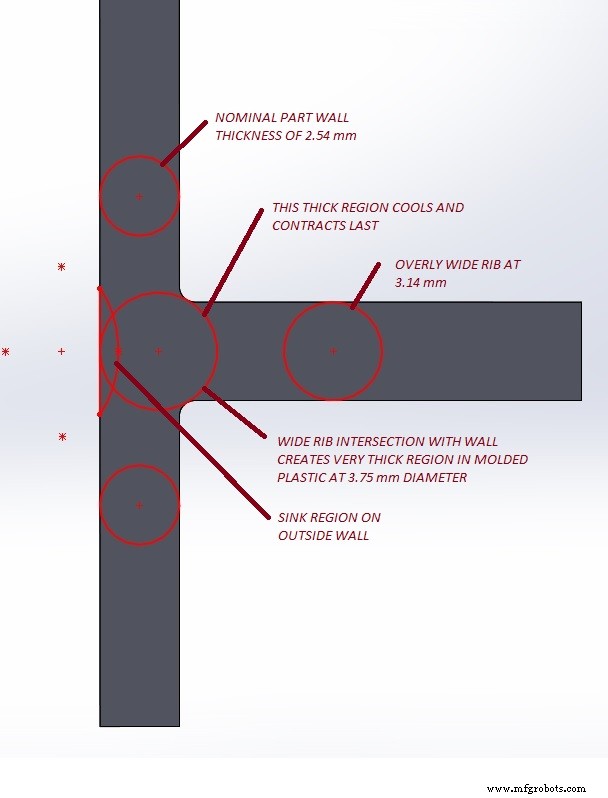
2つの外壁が出会う場所、または「バロニーカット」で適切なサイズのリブに角度の付いた表面が接触する場所でも、シンクが発生する可能性があります。内壁とリブの厚さに関するいくつかの一般的な推奨事項に従って、公称外壁の50〜60%にとどまると、射出成形部品の厚いスポットを回避し、ひいては欠陥を沈めるのに役立ちます。
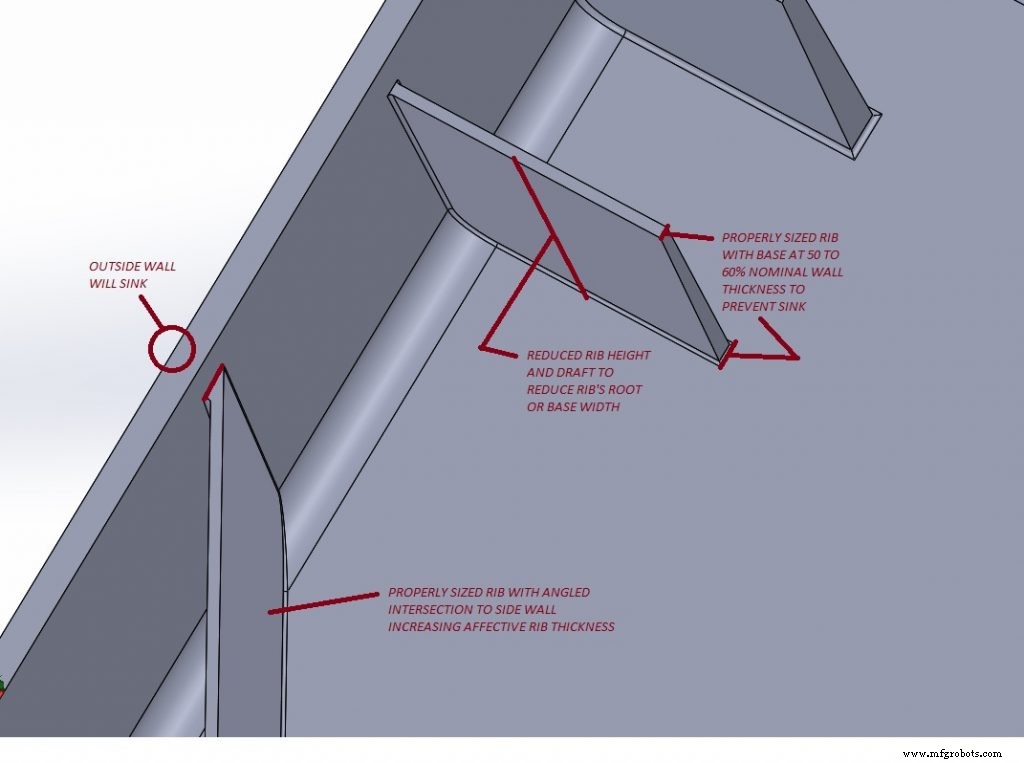
ただし、射出成形部品の設計におけるより複雑な形状やトランジションでは、開発中に厚いセクションが見落とされる可能性があります。よりあいまいなフィーチャ交差点の射出成形部品には、追加のコアリングが必要になる場合があります。上に示した光沢のある白いディスペンシングキャニスターベースは、一般的に一般的な壁の厚さで、内部に重いリブはありませんでした。
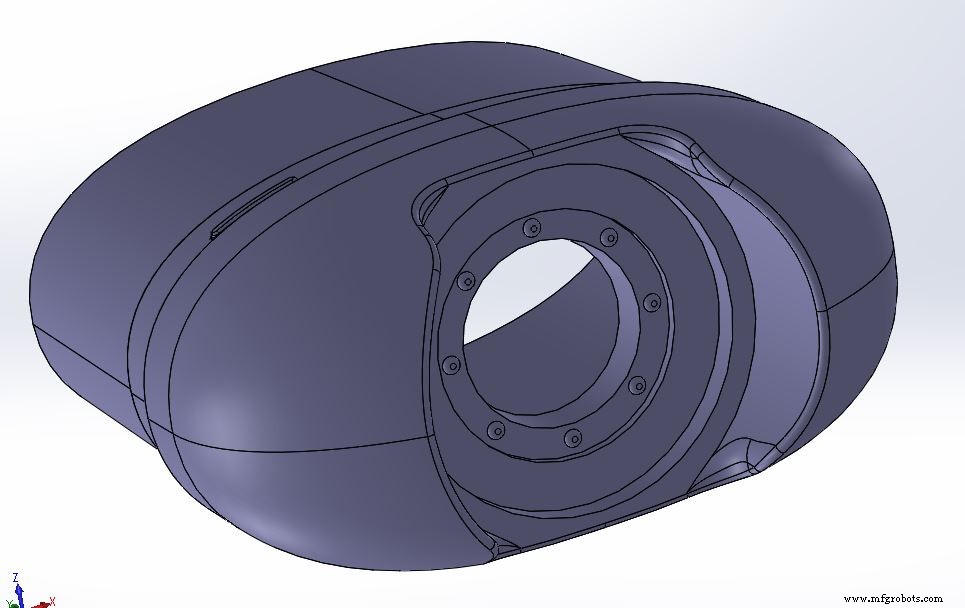
ただし、つまみねじの下部カウンターボアは、壁の交差点に角度を付けて、目に見えるシンクを引き起こしました。断面の正確な位置を詳しく調べると、特徴と材料の収束が明らかになりました。
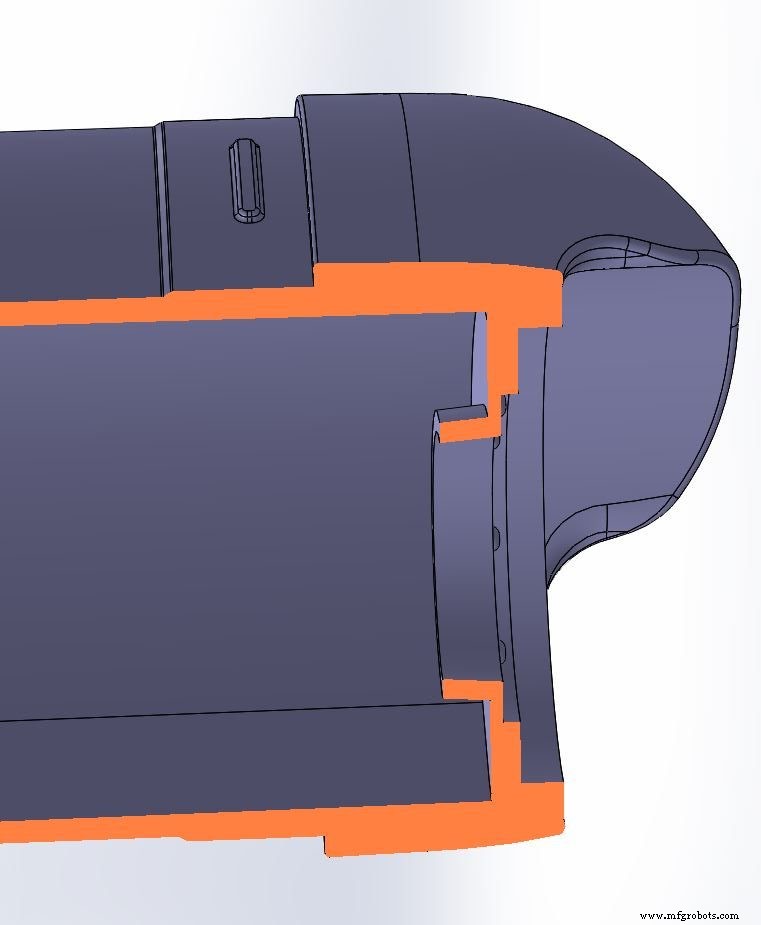
この厚い部分を作成した機能は、製品の小さなサイズと機能を維持するために、薄くしたり、移動したり、削除したりするのに簡単な候補ではありませんでした。そして、外側の流しは受け入れられませんでした。
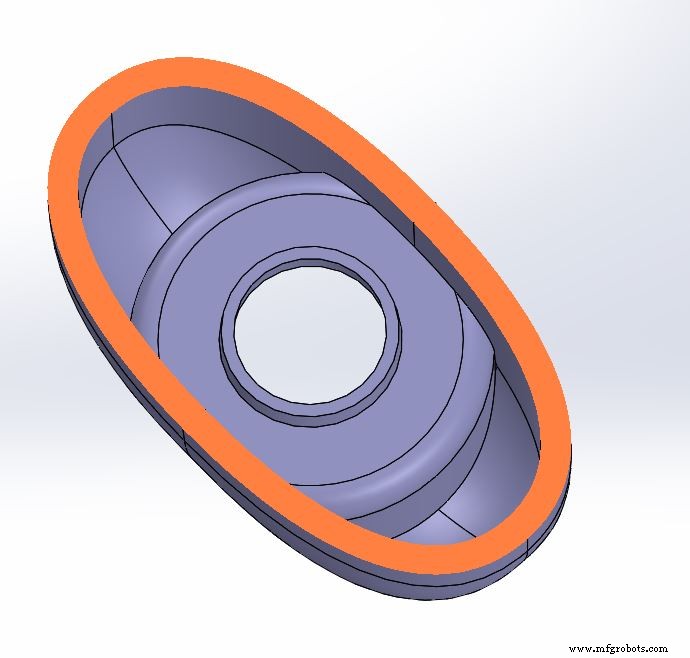
金型工具鋼のコアに追加されたわずかな内部コアリング機能により、次の記事の実行のために射出成形部品の材料の一部が解放されました。
- <図>
コアリング機能が追加される前
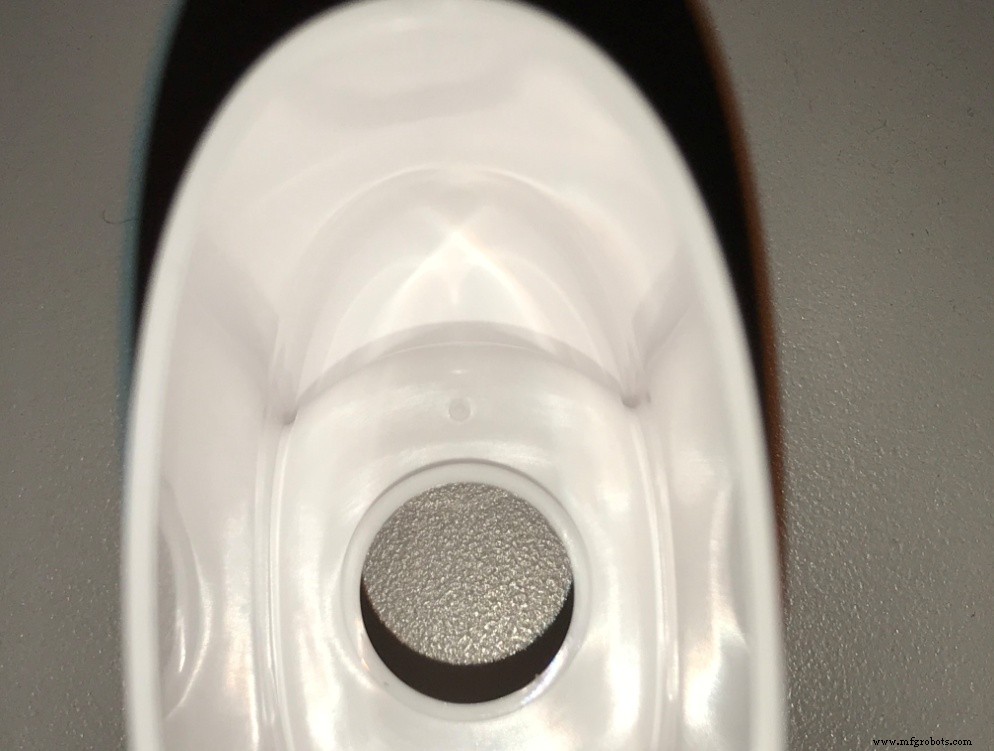
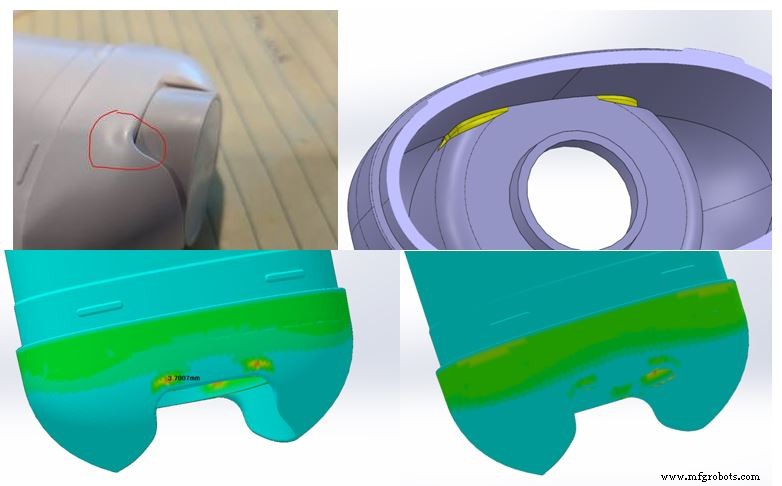
これに加えて、成形業者と協力してサイクルタイム(金型内の冷却)を延長し、プロセスを改良することで、完璧で機能的な部品が得られました。緊密な調整により、物事を迅速に解決することができました。
ボスは、組み立てに不可欠であるため、射出成形部品にも課題があります。それらは円錐形のリブと考えることができます。それらは、ねじ付きファスナーでうまく機能し、強度があるサイズにする必要がありますが、特定の技術に従わない場合、厚い領域に多くの機会をもたらします。ボスは多くの考慮事項を備えた重要な設計機能であるため、今後の議論でさらに詳しく説明します。
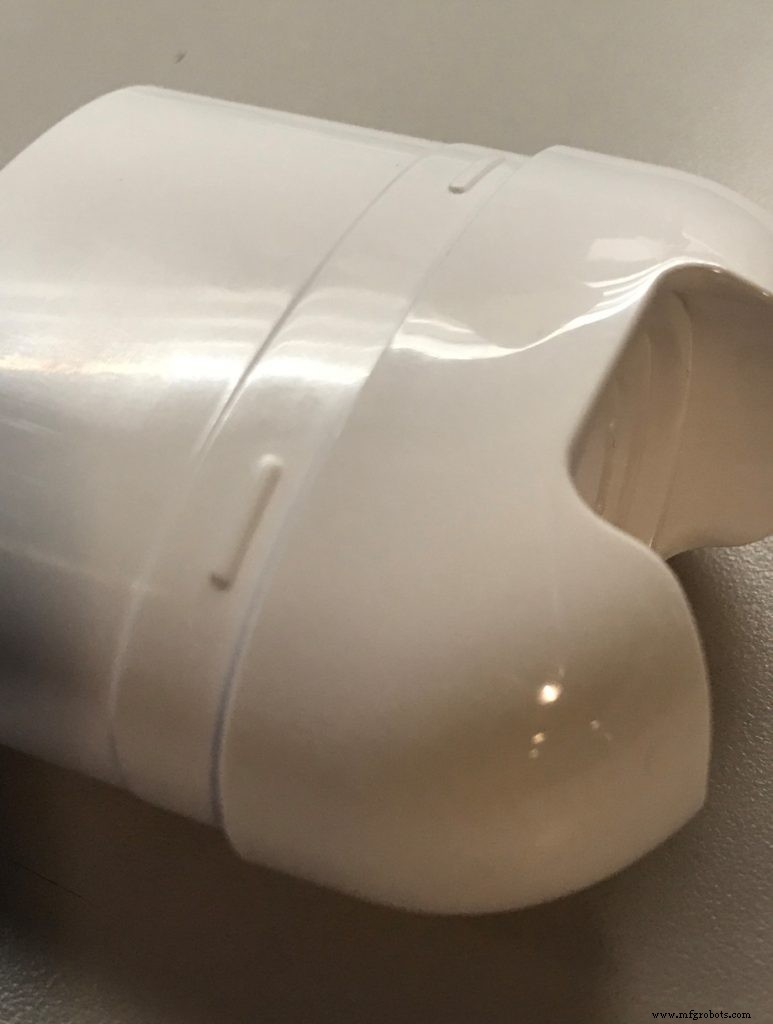
優れた射出成形金型エンジニアリング手法と利用可能な3DCADツールを使用することにより、射出成形部品を設計して、シンクやその他の化粧品の欠陥のリスクを最小限に抑えることができます。また、チームメンバーとして成形業者や工具メーカーと緊密に連携することにより、射出成形部品に改良を加えることができるため、計画どおりに機能する高品質の化粧品射出成形部品が得られます。このアプローチを使用すると、市場投入までの時間が最小限に抑えられます。
したがって、厚さと交差点に関して、内壁とリブの推奨事項を覚えておいてください。これらの機能を可能な限り最小化し、厚さが最小限に変化するようにドラフトをいくらか減らすことを検討してください。厚さ分析などのCADツールを使用し、断面ツールを使用して複雑な交差点を手動で確認し、シンクの可能性のある領域を探します。そして、金型の分析と推奨事項について成形業者と協力します。これには、第1および第2の製品部品の製造中にさらに調整が必要になる場合がありますが、緊密なコラボレーションと細部への注意により、市場投入までの時間が短縮されます。また、パーツの前面にある射出成形の欠陥を隠すために、別のバッジを追加する必要はありません。
リンク先:パート1、パート3、パート4
製造プロセス