医療製造がよりスマートに
デジタル化および自動化された製造は、COVID-19 パンデミックの際に製造ラインに導入された最近のシステムによって証明されているように、医療製造の世界で進歩を遂げています。
医療機器の製造を規制する厳格な基準を考えると、データ中心のインダストリー 4.0 環境は、熟練したオペレーターの劇的な不足に対処しながら、仕様を維持しようとする受託製造業者向けに調整されています。
これまでと同様に、材料はより洗練され、部品はより小さくなり、形状がより複雑になり、公差要件がより厳しくなっています。
広い意味で、ヘルスケアのトレンド (人口の高齢化、高価な病院環境の外での遠隔診断と治療への動き、より個別化された治療) は、医療機器の開発を推進しています。そして、パンデミックの不確実性が続いており、その結果サプライ チェーンがボロボロになっているため、サプライヤーとベンダーの仕組みをさらに可視化することが最優先事項です。
ヘルスケアのデジタル化に伴い、収集されるすべてのデータを保護する必要があります。この目標を達成するために、9 月 9 日に発表されたミネソタ大学の新しい医療機器サイバーセキュリティ センターのようなイニシアチブがあります。ボストン サイエンティフィック、スミス メディカル、オプタム、メドトロニック、アボットの 5 つの医療業界の大物がチームを組んで新しいセンターで協力しています。研究所。彼らの目標は、患者に危害を加えたり、医療施設を混乱させたりする可能性のある医療機器のソフトウェアの脆弱性を排除することです。
ヘルスケアのハイテクの未来は、より多くのロボットによる診断と手順も意味するため、これらのシステムで使用するための専用の医療ツールと部品がさらに必要になります。たとえば、XACT ACE ロボティック システムの開発者であるマサチューセッツ州ヒンガムの XACT Robotics は、8 月 30 日に、経皮的肺処置で使用する XACT ACE を評価する最初の米国研究で、患者登録を無事に完了したと発表しました。これには、がんの存在を確認するための生検が含まれます。ハンズフリーのロボット システムは、癌をより早期かつ低侵襲で検出できます。
一方、iData Research は、2025 年までに年間 300 万件のロボットによる外科手術が行われると予測しています。da Vinci Surgical System のような機器のロボット アームには、これらの低侵襲手術を行うために医師が制御する多数の小型化された器具が必要になります。ロボット手術は切開が小さいため、失血や瘢痕が少なくなり、入院期間が短くなり、回復が早くなります。
データを活用した AI は、患者の転帰を改善する上でも重要な役割を果たします。その道筋の明確な指標は、Stryker によるカリフォルニア州メンロパークの Gauss Surgical の買収です。Gauss は、手術中の失血を監視するための人工知能対応プラットフォームである Triton を開発しました。
また、アディティブ マニュファクチャリングは、患者固有のインプラント、ツール、および手術トレーニング モデルの製造において、その重要な役割を拡大し続けます。たとえば、イタリアの Tsunami Medical は、GE Additive レーザーおよび電子ビーム 3D プリンティング システムを使用して、さまざまな非常に複雑な脊椎インプラントを製造し、業界を驚かせています。
小さな部品、仕分けの課題
医療機器の材料が進化し、部品が小さくなるにつれて、ニュージャージー州アレンデールにある丸紅シチズン シンコム (MCC) の L シリーズ スイス式機械がその要求に応えています。
「Medical には、これまで聞いたことのない資料があります」と、社長兼 COO の Brian That は冗談を言いました。頑丈な素材は、単純なパーツや、さまざまな機能を作成するために多くのツールを使用する必要があるより複雑なコンポーネントに使用できます。
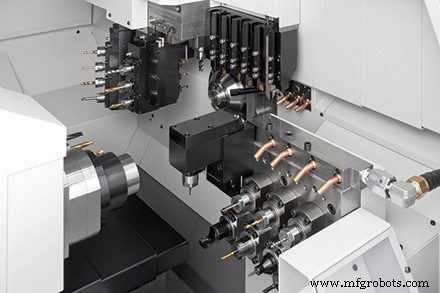
「当社の L シリーズ マシンは、サブスピンドルを備えたくし型マシンです」と説明し、医療用生産におけるそれらの大きな利点は、それらがモジュール化されていることです。 「いつでも多数のツールを利用できるので、1 つをスライドさせて 3 つを同じ場所に配置できます。」
現在の医療用ドリルやミルに典型的なより小さな直径を処理するために、MCC は最大 4 倍の加速のスピーダーを提供しています。 「私たちの回転工具は、モデルによって最大 6,000 または 9,000 rpm の速度に達しますが、別のツールホルダーをスライドさせることができ、現在は 36,000 rpm です。それでも不十分な場合は、最大 80,000 rpm に達する電動スピンドルを後付けできます。」
一例として、Such は次のように述べています。 .当社の 80,000 rpm 電動スピンドルを使用すると、これらのポケットに滑り込むことができます。また、この同じツールを正面ツール、クロス ツール、または後向きツールとして使用できるため、非常にモジュール化されています。」 MCC は、これらの独自のスピンドルを作成するために、高速スピンドルの販売者である NSK と提携しています。
約 2 年前、MCC は L20 マシンの ATC (自動ツール チェンジャー) バージョンを導入することで、マシンの B 軸の機能を拡張しました。 「今では、B 軸に 13 個のツールを使用できるようになりました」と、Such 氏は言いました。通常、B 軸には 4 個のツールしかありませんが、今日の部品の角度が狭いことを考えると、「医療市場にとってはかなりホットなものです」.
2016 年頃に導入された MCC のもう 1 つのイノベーションは、低周波振動 (LFV) 切断です。このプロセスでは、工作機械は「Z 軸または X 軸の切削経路を振動させ、非常に高速で内外に移動して、加工中にエア カットをほとんど行わず、切りくずを破壊します」と、Such 氏は言います。 「医療分野では LFV テクノロジーが高く評価されており、初めて LFV を使用するほとんどの顧客は、『このテクノロジーがなければ、二度とマシンを購入することはないでしょう』と言っています。」その中間はありません。プロセスを実行すると、それが保証されます。切削工具を知る必要があり、切削工具が故障する可能性はありますが、チップ ラップの問題は解消されます。」
MCC の顧客は、300 台または 400 台のマシンを所有する OEM から、10 台のマシンを所有する小規模なメーカーまでさまざまです。そして、これらの顧客は、一般的な骨ねじや脊椎手術用ケージから、股関節や膝の手術に必要な骨リーマーなどのさまざまな手術器具まで、「さまざまな部品を製造しています」。縫合用の穴がある直径約 4 mm の小さな骨ネジがあります。 「さまざまな形状をカットするために、9 つの異なるツールが使用されます」と、Such 氏は言います。 「この小さな骨のねじには多くの特徴があります。ただの頭の付いたねじではありません。」
細かなパーツが出来上がった後は、仕分けがメインになる、と続けた。 MCC は、タスクに合わせた自動化機器を製造しています。
「これらの部品は非常に小さいため、バケツに入れると 300 個になる可能性があります。測定するために最後の 1 つを選ぶとしたら、それはどれでしたか?カウント用の異なるトレイを備えたデバイスを用意できます」と、Such は言いました.
顧客は 100 個の部品を 1 つのトレイに入れることができ、トレイが移動すると、次のトレイに 1 個、次のトレイに 100 個、次のトレイに 1 個、というように配置できます。トレイが 10 個ある場合、無人で 8 時間または一晩稼働できます。部品を間隔をあけて測定することで、お客様は収集トレイのおかげで以前の部品の良し悪しを特定できます。
6 軸の利点
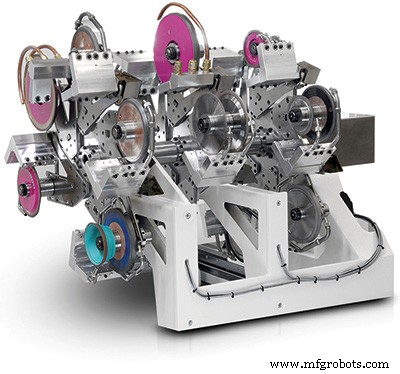
Rollomatic USA Inc. (イリノイ州マンデライン) の切削工具研削盤に対する安定した需要は、医療機器製造の回復力を明確に示していると、エリック シュワルツェンバッハ社長は断言しています。
ロロマティック マシンは、OEM や委託製造業者によって製作が求められる多くの器具の中には、やすり、骨ドリル、頭蓋穿孔器、関節鏡視用バーなどのさまざまな整形外科用切削工具があります。パンデミックの間、整形外科手術や待機手術が延期されたにもかかわらず、「お客様は以前と同じように投資を続けました。それ以上でもそれ以下でもありません」。 「これらの企業を維持し、再投資の必要性を維持するのに十分なビジネスが周りにありました。」
過去数年にわたって、ロボット手術用のさまざまな器具の需要が高まっていると彼は指摘しました。しかし、これらのデバイスには特定の課題があります。
「外科医がハンドピースを使用して骨に穴をあけるドリルは、ロボットが出すものとは異なります」と彼は説明しました。 「ロボットは外科医よりも長いドリルを使用します。長いドリルを作る性質は、短いドリルよりも難しいです。まず、手術器具のブランクは、スイス式旋盤で柔らかい状態で機械加工され、その後硬化されます。これらのプロセスは、本質的にこれらのブランクに反りを引き起こし、それらが長くなるほど、より曲がります。そして、それらが曲がっていると、確実にロード、研削、およびアンロードするのに問題があります。マシンとセットアップをお客様に教えるときは、十分に注意を払い、ある程度深く説明し、曲がったブランクを回避するための機能を確実に理解してもらう必要があります。多くの場合、曲がったブランクはメーカーによってまっすぐにされますが、それでも完璧である必要はありませんが、完璧ではありません。このマシンは小さな歪みを処理できます。」
業界がロボット化すればするほど、「ドリルポイントにより多くの焦点を当てなければなりません。外科医はいつでも骨に穴を開けることができます。なぜなら、彼は見て、見て、手と圧力を調整して、ポイントが離れないようにすることができますが、ロボットはそうではありません。したがって、これらのポイントは、より自己中心的になるように設計する必要があります。私たちは、医療機器メーカーがセルフセンタリング ポイントがどのようなものかを教えられるよう支援しています。」
シュワルツェンバッハは、整形外科用カッター用に 17-4 ステンレスのバリエーションが他にもあることにも注目しました。 「材料は柔らかくなり、硬度が低くなりました。これは、それらを研削するための適切な砥石を見つけるという点で、私たちにとって課題です.ご存知のように、素材が柔らかいほど、研ぎにくくなります。」そのニーズに応えるため、Rollomatic はスイスと米国のホイール メーカーと提携して、より柔らかい素材に適したホイールを調達しています。
「材料が柔らかいほど、バリが多く発生します」と Schwarzenbach 氏は説明しました。当社のお客様は通常、特に柔らかい材料の場合、研磨後のバリを除去するためにナイロン ブラシを使用します。しかし、完璧な車輪やプロセスはありません。何らかの方法で取り除く必要がある少しのゆるいバリが常にあります。これらのバリを取り除くために、ナイロンまたはセラミックまたは研磨剤を含浸させたブラシを使用します。」
医療ツール用のクイック ディスコネクト グリップは、もう 1 つの成長分野です、と彼は続けました。これらのツールは、外科医がクリックしてハンドピースに挿入したり、ロボット アームに固定したりできます。そのようなグリップは、「これまでに見たことがないほど複雑になっています。私たちはそれらのほとんどにピール グラインダーを使用しています。」
Rollomatic の 6 軸機能は、より柔軟なプログラミングと簡単なホイール セットアップを必要とする医療メーカーにとって、ゲーム チェンジャーであると Schwarzenbach 氏は述べています。
「複雑なホイールを使用する必要はありません。特にドリルポイントでは、より単純な形状のホイールを使用できます」と彼は言いました. 「5 軸マシンよりも簡単にドリル ポイントを作成できます。忘れないでください:ドリル ポイントは現在、50 度から 60 度まで下がっています。金属への 120 度または 130 度の超硬ドリルとは対照的に、それらは非常に急勾配です。当社の 6 軸加工機は、5 軸加工機のセットアップに苦労するよりもはるかに簡単にドリル ポイントを研削するのに役立ちます。」
そして、Rollomatic のクイック ホイール チェンジャーには、さらに多くの利点があると彼は付け加えました。 「私たちは、より多くのホイール チェンジャー マシンを販売しています。基本的なホイール チェンジャーには 6 つのステーションがあるため、6 つのホイール パックを配置して柔軟性を高め、短いバッチに対応できます。より短いバッチには、頻繁な切り替えがあるため、より柔軟性が必要です。ホイール チェンジャー マシンは、そのために非常に優れています。」 Rollomatic が医療業界に販売する機械の約 80% は、前後に 1 組のホイールを収容する標準のスピンドルを保持していますが、一部のメーカーは「当社の新しい技術を採用し始めています」。
フォース テストの役割
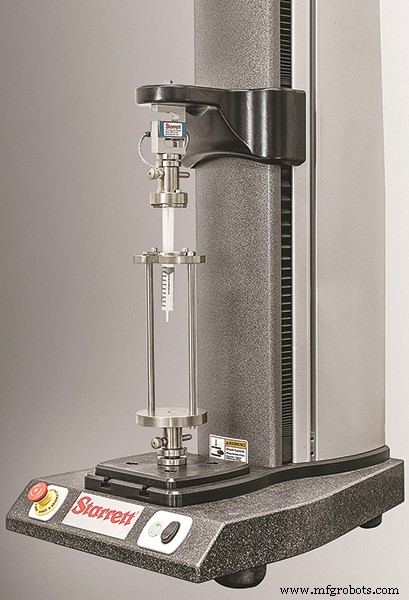
製造の準備から部品の製造後まで、力試験装置とそれに統合されたソフトウェアは、多くの場合、患者の快適さを目標として、医療製品にとって重要な機能を果たします。
たとえば、針の輪郭とコーティングは皮膚への侵入のしやすさをテストすることができ、接着剤は皮膚への付着の程度や除去のしやすさを評価することができます。
The L.S. のテクニカル サポート エンジニアである Jacob Morales 氏は、製造の前に、「製造に使用する前に、機器が正常に機能することを確認するためのテストを構築できます」と説明しています。マサチューセッツ州アソールの Starrett Co. . そして包帯については、「製造ラインで使用する前に接着剤をテストできます」。 「後処理、これらのテストを再度実行して一貫性を確保できます。」
このような試験は、ASTM および ISO 規格に沿って製造する場合や、トレーサビリティに不可欠な文書を作成する場合に特に重要であると、Starrett の力および材料試験の技術マネージャーである Eric Perkins 氏は付け加えました。 Starrett ソフトウェアは、力と材料特性の両方のテストを可能にし、右のアイコンをクリックするだけで、ソフトウェアは適切なテストを実行できます。力の測定は、ピーク荷重、平均荷重、圧縮試験などのテストを含む、ゴー/ノーゴー シナリオをカバーします。一軸力の適用を必要とする主な例である注射器は、制御された注入速度の注入力を決定するためにサンプル物質でテストできます。
これらのテストはサンプル情報を提供しますが、サンプルを構成する材料に固有のデータを常に返すとは限りません。材料試験はさらに進み、材料特性を使用して伸びや応力ひずみなどを試験します。
Starrett ソフトウェアは製造プロセスに統合できると Morales 氏は説明します。
「サンプルをテストする力システムがある場合は、テストが常に実行されるように入出力システムでプログラムすることができます。製造装置はサンプルをマシンに移動し、信号を送信します。マシンはテストを実行することで応答し、テスト結果に基づいて信号出力を提供します。残りの製造装置は適切に対応できます。許容範囲外の結果が得られた場合、信号はオペレータに警告できます。」
その柔軟性は、「フォース システムを PLC に接続して、生産環境に合わせて配置できるため、潜在的な人間によるデータ入力エラーを排除できることを意味します」と Perkins 氏は述べています。 「製品がキューに入れられるたびに、ユーザーは製品を自動的にテストできます。」
Starrett の基本的な L1 フォース ソフトウェアから、より高度な L2、L2Plus、および L3 オプションまで、「あらゆる製造標準状態とまったく同じようにテストできる機能をお客様に提供します」と Perkins 氏は述べています。また、Starrett ソフトウェアはプラットフォーム間で互換性があるため、光学システムとビジョン システムを追加すると、非常に広範な計測ソリューションが作成されます。
ただし、そのレベルのカスタマイズはソフトウェアにとどまりません。 Starrett はメーカーと協力して、完全に自動化されたシステムを作成しています。
「私たちはロボットを使用して部品を力試験システムに挿入しています」と Perkins 氏は言います。 「部品をつかむために空気圧グリッパーを使用しています。」このレベルの自動化と結びついたテスト プラットフォームを常時実行することで、「当社のシステムはパーツの良し悪しを判断し、ロボットが必要なプログラムを実行して、それらのパーツを指定されたビンに入れます。」
GE の全体像
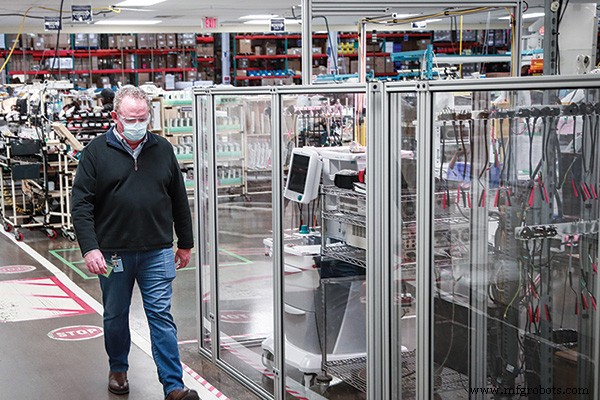
病院のワークフローを改善し、サプライ チェーンの回復力を維持することは、パンデミックの間、GE ヘルスケアにとって最優先事項でした。
ミルウォーキーにある GE Healthcare の高度な製造担当エグゼクティブ チーフ エンジニアである Jimmie Beacham 氏は、次のように述べています。 「これは、新しい従業員や回転する従業員をトレーニングするよりも簡単です。自動化が理にかなっているのは、必ずしも労働力ではなく、サプライ チェーンのセキュリティです。ある地域から別の地域に生産を切り替える必要がある場合、プロセスが既に自動化されていれば、はるかに簡単です。」
その哲学の主要な部分は間違いを防ぐことだと彼は付け加えた。 「私たちはオペレーターを訓練し、手順を文書化しました」とビーチャムは説明しました。 「現在、オペレーターが行う必要があることをデジタル化し、オペレーターとやり取りする他のテクノロジーの採用を検討しています。ボルトにトルクを加えるトルク ステーションがあり、その後に複雑なアセンブリがあり、コボットが続くとします。私たちは、それらすべてをデジタルで接続するテクノロジーを検討しています。これは、オペレーターと足並みをそろえて機能するため、その人と対話し、オペレーターがすべてを記憶する必要はありません。これにより、同じ製品を世界の 3 つの地域で製造する場合に、大きな柔軟性が得られます。これで、制御プロセスが 1 つになりました。オペレーションのいくつかの複雑な部分を繰り返さなければならないときに、オペレーターが紙の手順を覚えていることに頼っていません。」
これは、一連のスマート診断機器を製造している GE ヘルスケアにとって不可欠です。アディティブ マニュファクチャリングは方程式の大きな部分を占めており、GE ヘルスケアはその点でもプロセスを改良しました。
「私たちが最初に始めたとき、私たちの時間のおそらく 80% から 90% は R&D に投資され、添加剤がどのように機能するか、私たちの工学的要件を満たすために材料とパラメータをどのように開発するかを理解しようとしていました」と彼は言いました。 「現在、私たちは約 80% の実行を行っており、生産に移行しています。残りの 20% の時間は、入ってくる新しいファネル用の新しい材料の開発に費やされています。私たちはモンテレーに生産施設を持っています。メキシコ、そして私たちはそこに行く物事のかなり活発なじょうごを持っています.それから、ユースポイントで実行する他のいくつかの付加的なアプリケーションがあります。」
最終的に、パンデミックは困難を極めましたが、GE ヘルスケアは嵐を乗り切りました。
「私たちの大きな課題は、プラントに人々を安全に送り込むことでした」とビーチャムは言いました。 「場合によっては、人工呼吸器のように、前例のない需要を満たすために自動化に大きく依存していました。この作業を行うために多くの人員を投入しましたが、顧客が切実に必要としている大量の製品を製造するための創造的な方法を見つける必要がありました。そして、私たちは物事を異なる方法で製造できることを学びました。それはさらに多くのアイデアを刺激しました。」
自動制御システム