最も包括的な鋳造プロセスの概要
鋳造プロセスの分類
- 砂型鋳造
- シェルモールド鋳造
- インベストメント鋳造
- ダイカスト
- 低圧鋳造
- 遠心鋳造
- 重力鋳造
- 真空鋳造
- スクイーズキャスティング
- 消失消失鋳造
- 継続的なキャスト
砂型鋳造
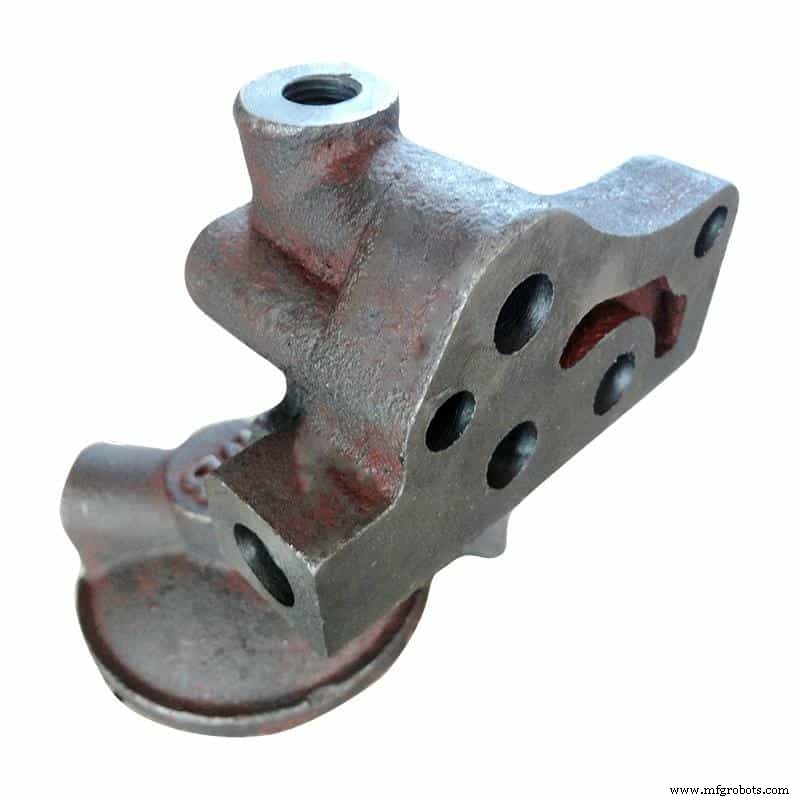
砂型で鋳物を製造するための鋳造方法。鋼、鉄、およびほとんどの非鉄合金鋳物は、砂型鋳造によって得ることができます。
プロセスフロー:
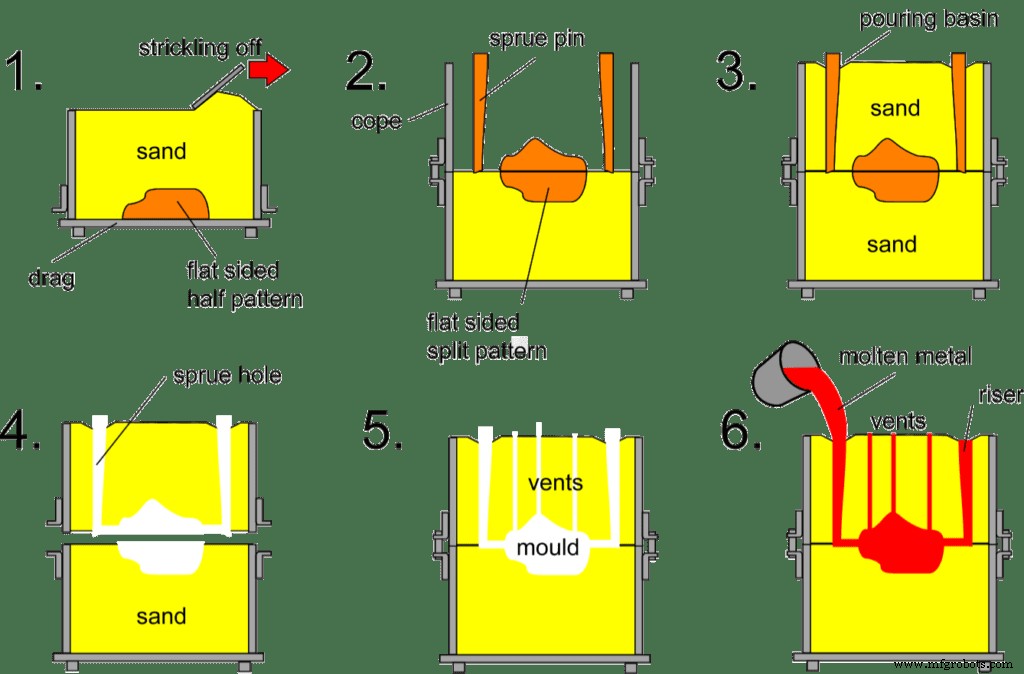
技術的機能:
- 複雑な形状のブランク、特に複雑な内部空洞のあるブランクの作成に適しています。
- 幅広い適応性と低コスト;
- 鋳鉄などの可塑性の低い一部の材料では、砂型鋳造が部品またはブランクを製造する唯一の成形プロセスです。
アプリケーション:
自動車用エンジンのシリンダーブロック、シリンダーヘッド、クランクシャフト、その他の鋳造品。
シェルモールド鋳造
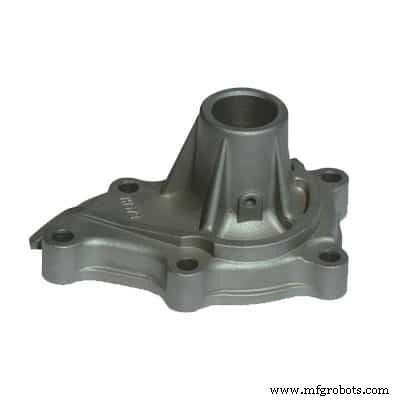
シェルモールド鋳造は、消耗品のモールド鋳造プロセスです。つまり、溶融金属を使い捨てのモールドに流し込みます。樹脂で覆われた砂は、加熱された再利用可能な金型で覆われ、薄い金型シェルに硬化されます。次に、薄い金型シェルを加熱および固化して、十分な強度と剛性を実現します。したがって、上下のモールドシェルをクランプでクランプするか、樹脂で接着した後、使い捨てのモールドを形成することができます。
プロセスフロー:
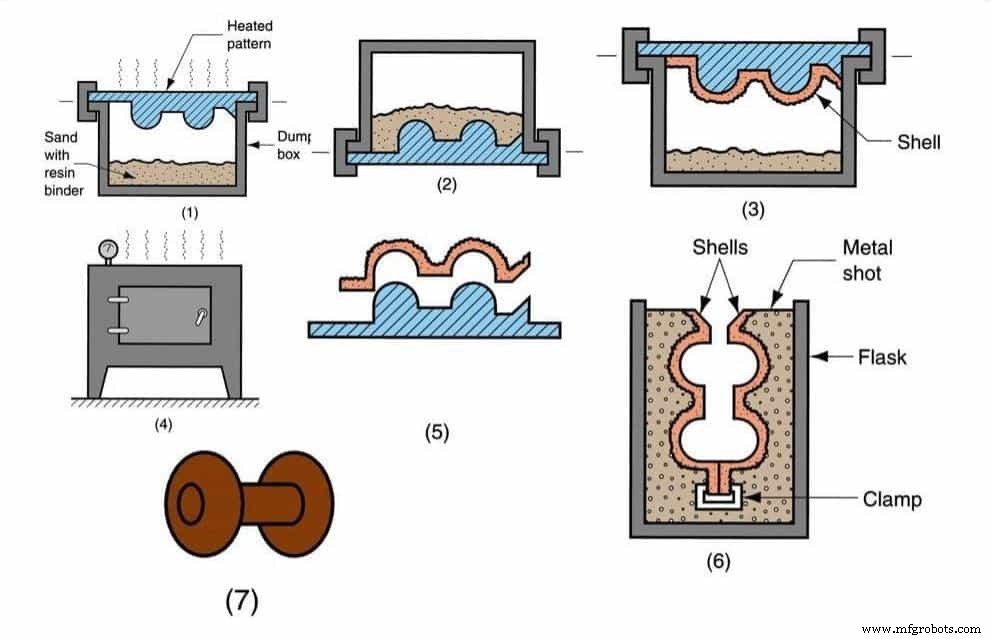
技術的機能:
利点:
- 自動大量生産を実現できます;
- 優れた表面仕上げと加工精度により、その後の加工コストを削減できます。
- 大きな部品や複雑な形状を作成できます。
- 金型コストが低く、廃棄物の発生が少ない。
短所:
- シェルモールド鋳造に使用される樹脂は高価です。
- 再利用可能な金型は、高コストで精密に機械加工する必要があります。
- 注入中に刺激性ガスが発生します;
- 気孔率の高い低強度の鋳物。
アプリケーション:
シリンダーヘッド、コネクティングロッド、マニホールドなど、大量のバッチ、高寸法精度、薄肉、複雑な形状のさまざまな中小規模の合金鋳物の製造に適しています。
インベストメント鋳造
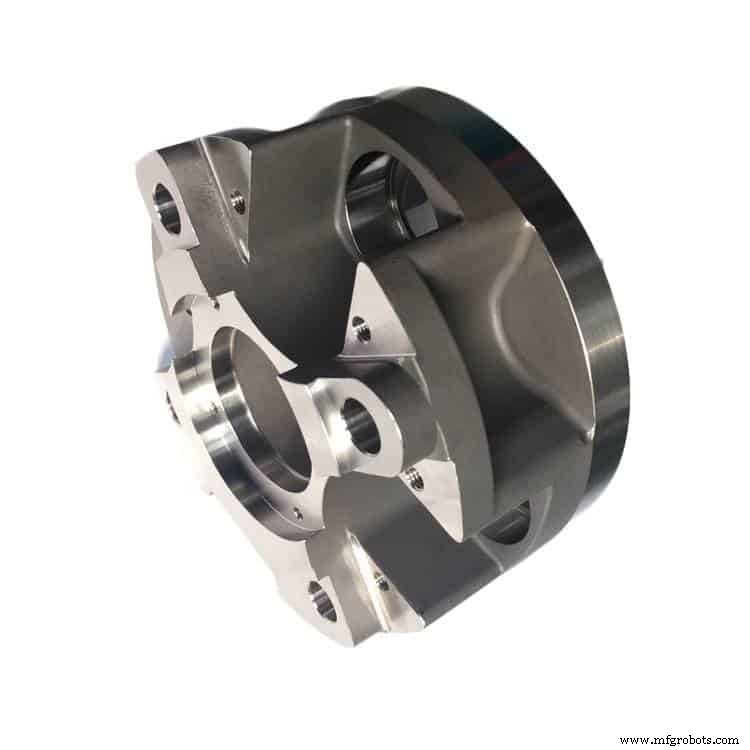
これは通常、可融性材料をパターン化し、パターンの表面に耐火材料を何層かコーティングしてモールドシェルを作成し、次にパターンをモールドシェルから溶かす鋳造方式を指します。高温焙焼後に砂を充填できる、パーティング面のない型を得る。 「ロストワックス鋳造」と呼ばれることもあります。
プロセスフロー:
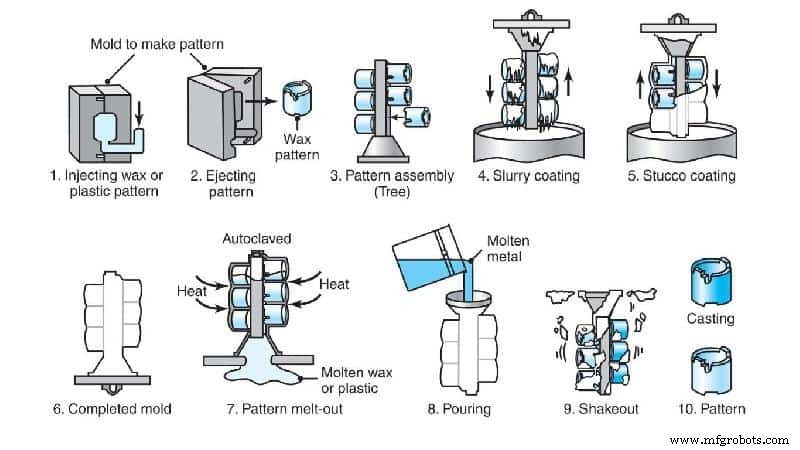
技術的機能:
利点:
- 高寸法および幾何学的精度;
- 高い表面粗さ;
- 複雑な鋳物を鋳造でき、鋳造合金に制限はありません。
短所:
複雑なプロセスと高コスト。
アプリケーション:
複雑な形状、高精度の要件、またはタービンエンジンブレードなどの他の処理が困難な小さな部品の製造に適しています。
ダイカスト
高圧を使用して溶融金属を精密な金型キャビティに高速で押し込み、溶融金属を圧力下で冷却および凝固させて鋳物を形成します。
プロセスフロー:
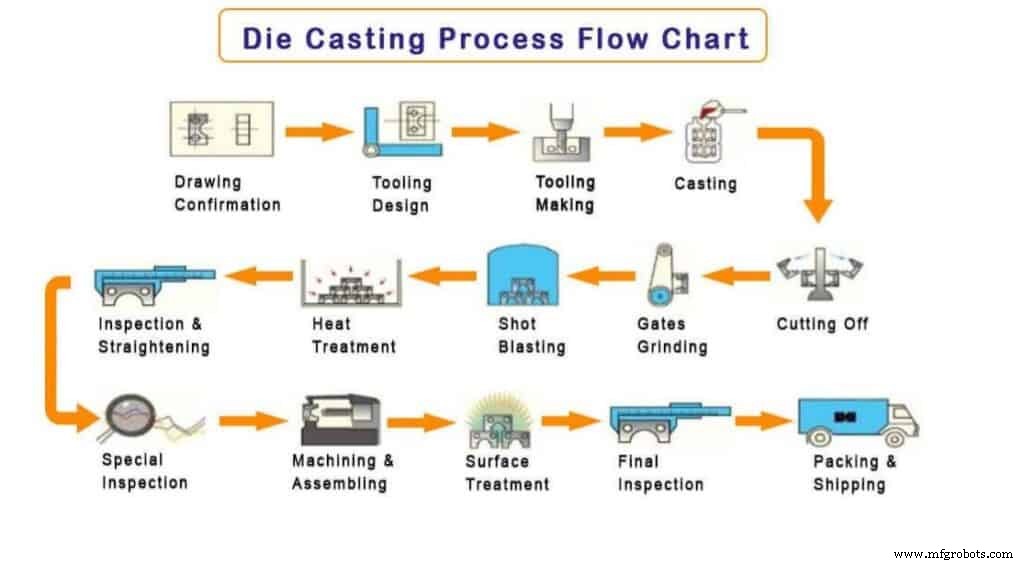
技術的機能:
利点:
- 溶融金属は高圧と高流量に耐えます。
- 高い製品品質、安定したサイズ、優れた互換性;
- ダイカスト金型の高い生産効率と長い耐用年数;
- 経済的利益があり、大量生産に適しています。
短所:
- 鋳物は小さな細孔と収縮多孔性を起こしやすいです;
- ダイカストの可塑性が低いため、衝撃荷重や振動下での作業には適していません。
- 高融点合金ダイカストは、ダイカスト金型の寿命を縮め、ダイカスト生産の拡大に影響を与える可能性があります。
アプリケーション:
ダイキャスティングは、自動車産業や計器産業で最初に使用され、その後、農業機械、工作機械産業、電子産業、国防産業、コンピューター、医療機器、時計、カメラ、日常のハードウェアなどのさまざまな産業に徐々に拡大しました。他の業界。
L圧力キャスティング
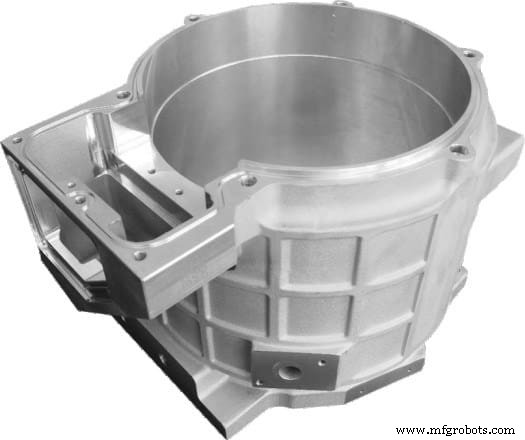
これは、型に低圧(0.02〜0.06MPa)で溶融金属を充填し、圧力下で結晶化して鋳物を形成する方法を指します。
プロセスフロー:
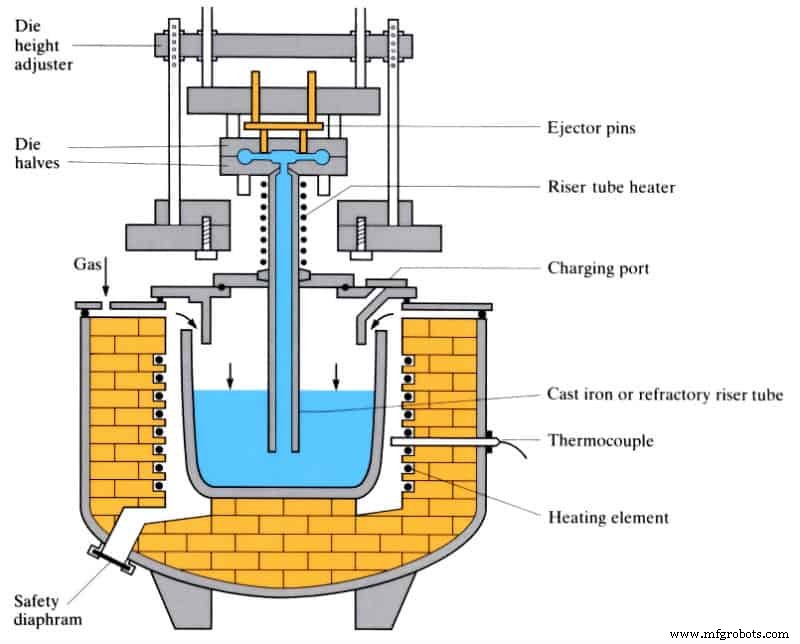
技術的機能:
- 注入中の圧力と速度を調整できるため、さまざまな合金の鋳造やさまざまなサイズの鋳造に適した、さまざまな鋳造型(金型、砂型など)に適用できます。 >
- ボトムインジェクションタイプの充填を採用し、溶融金属の充填は安定しており、飛沫がないため、ガスの閉じ込めや金型の壁やコアへの精練を回避でき、鋳造の適格率が向上します。
- 鋳物は圧力下で結晶化し、コンパクトな構造、明確な輪郭、滑らかな表面、および高い機械的特性を備えています。これは、大きくて薄い壁の鋳物に特に有益です。
- フィーディングライザーを省略し、金属利用率を90〜98%に引き上げました。
- 労働集約度が低く、労働条件が良好で、設備がシンプルで、機械化と自動化が容易に実現できます。
アプリケーション:
主に従来の製品(シリンダーヘッド、ホイールハブ、シリンダーフレームなど)。
遠心鋳造
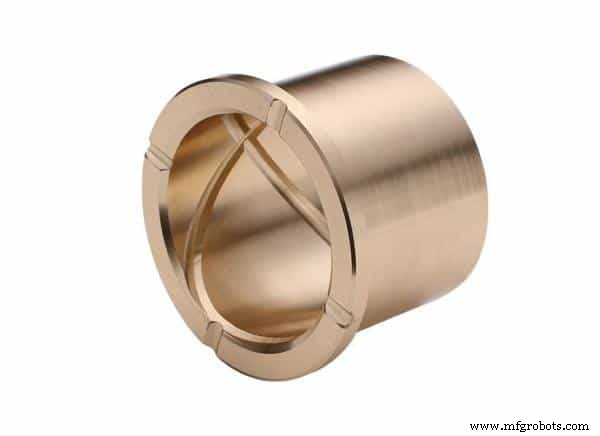
回転する金型に溶湯を流し込み、遠心力で型を埋めて固化させる鋳造法。
プロセスフロー:
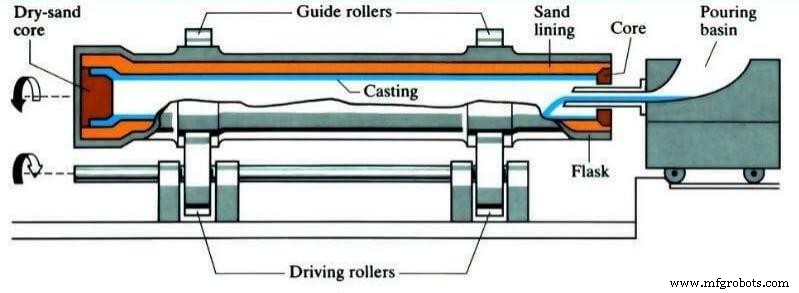
技術的機能:
利点:
- プロセスの歩留まりを向上させるためのゲートシステムとライザーシステムの金属消費はほとんどありません。
- 中空鋳物の製造ではモールドコアが不要であるため、長い管状鋳物の製造では金属充填能力を大幅に向上させることができます。
- 鋳物の細孔、スラグ介在物、その他の欠陥が少なく、密度が高く、機械的特性が高い。
- バレルとスリーブの複合金属鋳物の製造に便利です。
短所:
- 特殊な形状の鋳物の製造には一定の制限があります。
- 鋳造品質が悪く、内穴の直径が不正確で、内穴の表面が粗く、加工代が大きい。
- 鋳造は比重分離を起こしやすいです。
アプリケーション:
遠心鋳造は、最初に鋳造パイプを製造するために使用されました。遠心鋳造プロセスは、冶金、鉱業、輸送、排水および灌漑機械、航空、国防、自動車、およびその他の産業で使用され、鉄鋼、鉄、および非鉄炭素合金の鋳造品を製造します。その中でも、内燃機関の遠心鋳鉄管、シリンダーライナー、シャフトスリーブが最も一般的です。
重力鋳造
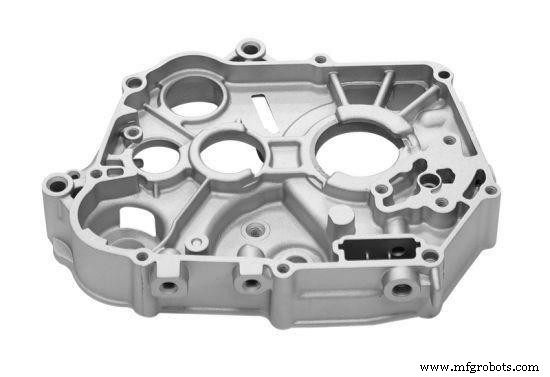
これは、溶融金属に重力の作用下で金型を充填し、金型内で冷却および固化して鋳物を得る成形方法を指します。
プロセスフロー:
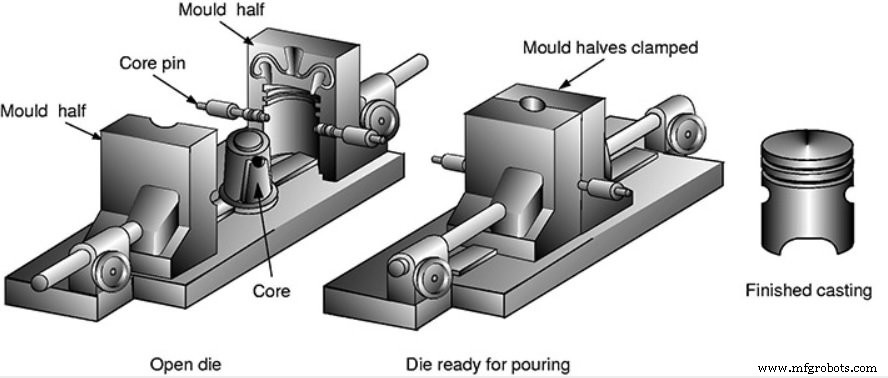
技術的機能:
利点:
- 金型の大きな熱伝導率と熱容量、速い冷却速度、緻密な鋳造構造、および機械的特性は、砂型鋳造部品よりも約15%高くなっています。
- 寸法精度が高く、表面粗さが低く、品質安定性に優れた鋳造品。
- サンドコアは使用されていないか、ほとんど使用されていないため、環境を改善し、ほこりや有害ガスを減らし、労働強度を減らすことができます。
短所:
- 金型自体には通気性がないため、キャビティ内の空気と砂のコアによって生成されたガスを排出するために特定の対策を講じる必要があります。
- 金型は変形しにくく、固化すると鋳物にひびが入りやすくなります。
- 金型の長い製造サイクルと高い製造コストは、大量生産でのみ経済効果を発揮します。
アプリケーション:
重力鋳物は、複雑な形状のアルミニウム合金やマグネシウム合金鋳物などの非鉄合金の大量生産に適しているだけでなく、鉄鋼の金属鋳物やインゴットの製造にも適しています。
真空鋳造
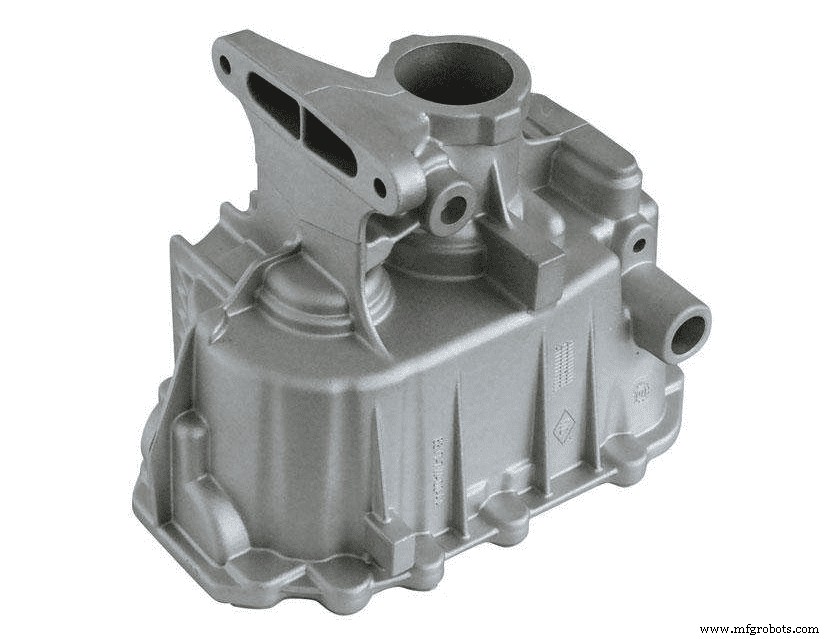
鋳造プロセス中に鋳造金型キャビティからガスを抽出することにより、鋳造部品の細孔と溶存ガスを除去または大幅に削減し、それによって鋳造部品の機械的特性と表面品質を向上させる高度な鋳造プロセス。
プロセスフロー:
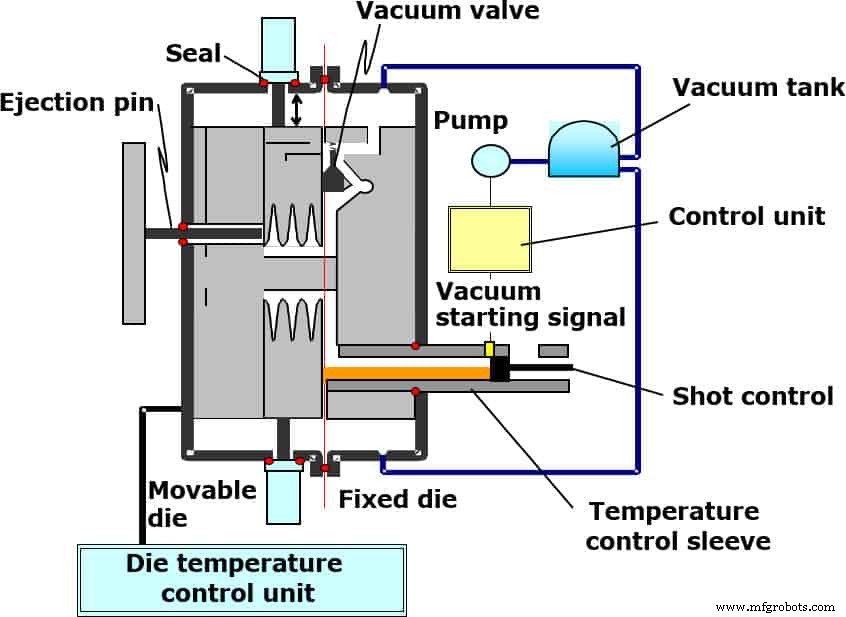
技術的機能:
利点:
- 鋳物内部の細孔をなくすか減らし、鋳物の機械的特性と表面品質を改善し、めっき性能を改善します。
- キャビティの背圧を下げると、比圧が低く鋳造性能の悪い合金を使用でき、小型の機械で大きな鋳造物を鋳造することができます。
- 充填条件が改善され、肉厚の薄い鋳物を製造できるようになりました。
短所:
- 金型のシール構造が複雑なため、コストが高くなり、製造と設置が困難になります。
- 真空鋳造法が不適切に制御されている場合、その影響はそれほど重要ではありません。
カスティンを絞る g
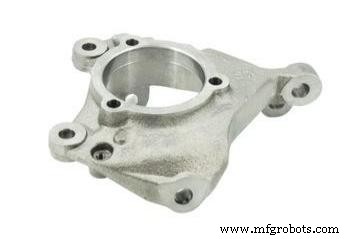
これは、高圧下で液体または半固体の金属を凝固および流動成形して、部品またはブランクを直接得る方法です。液体金属の利用率が高く、工程が簡素化され、品質が安定しているというメリットがあります。これは、潜在的なアプリケーションの見通しを持つ省エネ金属成形技術です。
プロセスフロー:
ダイレクトスクイーズキャスティング:
コーティングスプレー、合金注入、金型閉鎖、加圧、圧力維持、圧力解放、金型分割、ブランク離型、およびリセット。
間接スクイーズキャスティング:
コーティングスプレー、金型閉鎖、供給、金型充填、加圧、圧力保持、圧力解放、金型分割、ブランク離型、およびリセット。
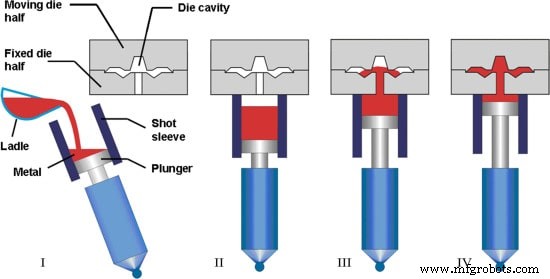
技術的機能:
- 細孔、収縮穴、収縮多孔性などの内部欠陥を排除できます。
- 低い表面粗さと高い寸法精度;
- キャストクラックを防ぐことができます;
- 機械化と自動化を簡単に実現できます。
アプリケーション:
アルミニウム合金、亜鉛合金、銅合金、ダクタイル鋳鉄など、さまざまな種類の合金の製造に使用できます。
消失消失鋳造
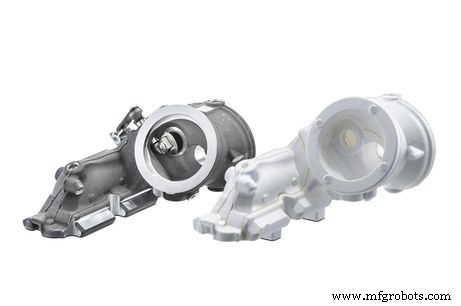
ロストフォームキャスティング(フルモールドキャスティングとも呼ばれます):
これは、鋳造物とサイズと形状が類似しているパラフィンワックスまたはフォームモデルをモデルクラスターに結合して組み合わせる新しいタイプの鋳造方法です。耐火コーティングをブラッシングして乾燥させた後、振動モデリングのために乾燥した石英砂に埋め、負圧下で注いでモデルをガス化し、液体金属がモデルの位置を占め、凝固と冷却の後に鋳造物を形成します。
プロセスフロー:
予備発泡→発泡成形→浸漬コーティング→乾燥→
モデリング→注ぐ→サンドドロップ→クリーニング
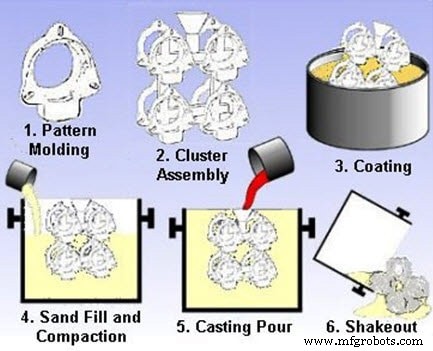
技術的機能:
- 高精度の鋳造、サンドコアが不要なため、処理時間が節約されます。
- パーティング面がなく、柔軟な設計で、設計の自由度が高い。
- 汚染のないクリーンな生産;
- 投資と生産コストを削減します。
アプリケーション:
複雑な構造、無制限の合金タイプ、製造バッチを備えたさまざまなサイズの精密鋳造品の製造に適しています。ねずみ鋳鉄製のエンジンボックス、高マンガン鋼製のエルボなど。
継続的なキャスト
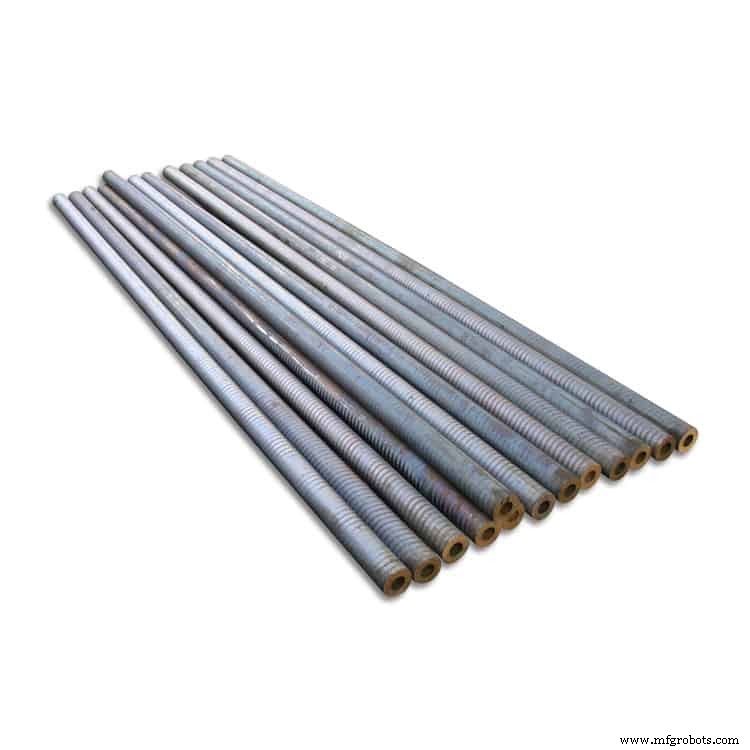
継続的なキャスト は高度な鋳造方法であり、原理は、晶析装置と呼ばれる特殊な金型に溶融金属を連続的に注入することです。固化した(固まった)鋳物は、晶析装置のもう一方の端から連続的に引き出されます。この鋳造方法により、任意の長さまたは特定の長さの鋳造物を得ることができます。
プロセスフロー:
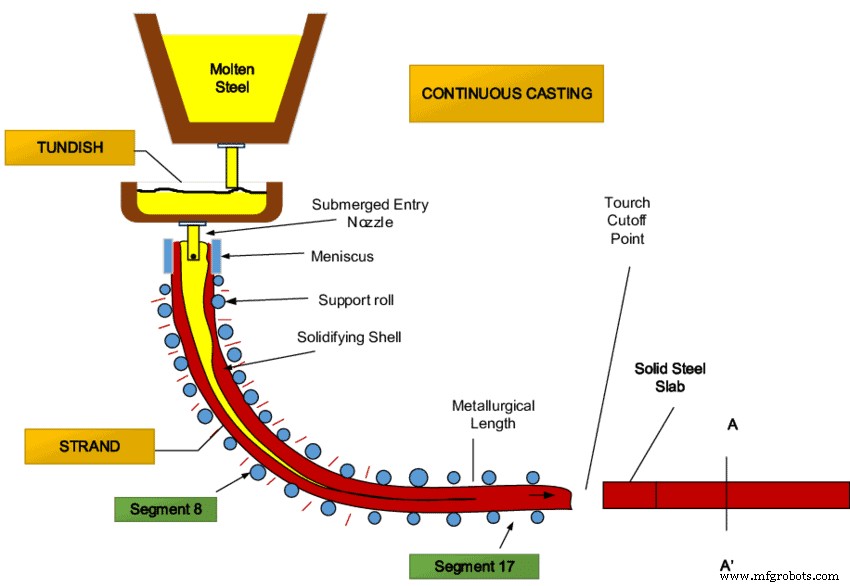
技術的機能:
- 金属が急速に冷却されるため、緻密な結晶、均一な構造、および優れた機械的特性。
- 金属を節約し、歩留まりを向上させます。
- プロセスを簡素化し、モデリングやその他のプロセスを排除し、労働集約度を減らし、必要な生産エリアを大幅に削減します。
- 機械化と自動化を簡単に実現し、生産効率を向上させます。
アプリケーション:
連続鋳造法は、鋼、鉄、銅合金、アルミニウム合金、マグネシウム合金、およびインゴット、スラブ、バーブランク、パイプなどの断面形状が変更されていないその他の長い鋳造に使用できます。
産業技術