射出成形部品の設計パート3:ボス
射出成形部品は、中量から大量の製品に最適なソリューションです。製品、年間の目標売上高、商品原価、および計画された修理戦略に応じて、プラスチックのボスで成形され、部品を低コストで位置合わせし、コンポーネントの取り付けとエンクロージャーの固定用の留め具のオプションを提供します。ただし、プラスチック部品の取り付けボスの設計と配置を適切に検討して、不要な外観上の欠陥を回避し、設計の失敗を回避するための適切な強度を確保する必要があります。
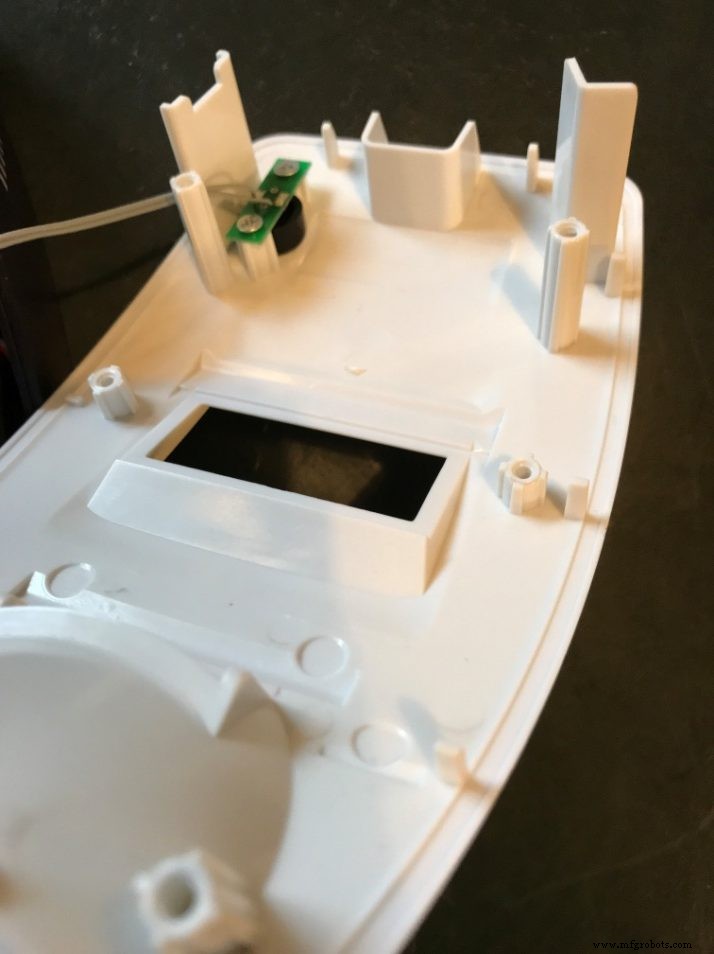
ボスを作成するための射出成形部品の設計に関する提案はたくさんありますが、これらのガイドラインが矛盾していることがよくあります。推奨事項は、ねじ山成形ねじメーカー、射出成形契約メーカー、最終組立チーム、または場合によっては工業デザイナーによって作成されているかどうかによって異なります。真実は、これらの入力のすべてを考慮する必要があり、ボス機能が実行され、部品に見える外観上の欠陥を引き起こさないようにする必要があるということです。しかし、それを達成するには、射出成形部品を設計する機械エンジニアが少し妥協する必要があります。もちろん、すべてのチームメンバーの意見を考慮する必要があります。特に、射出成形機は、成形プロセスを改善し、製造される部品の品質を所有するため、協力する必要があります。
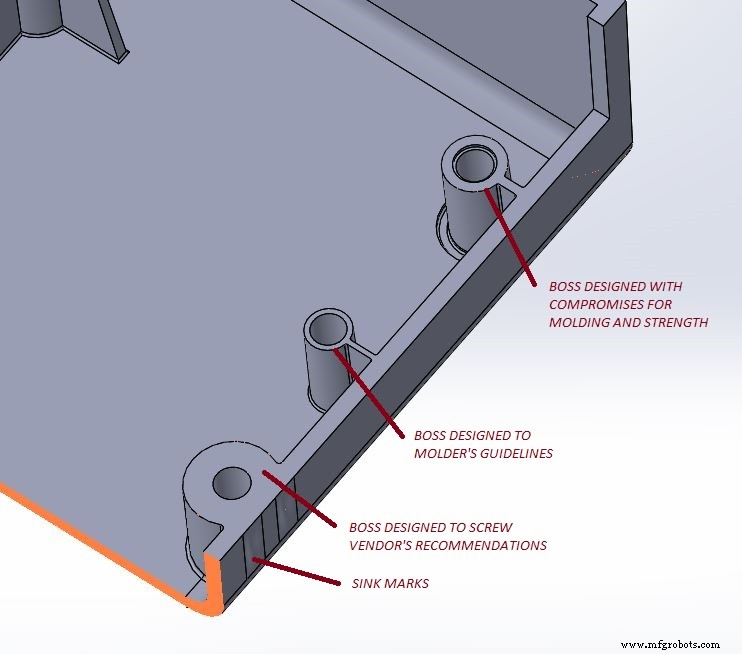
では、問題はどこから始まり、何が問題なのでしょうか。特大のボスまたは不適切に配置されたボスは、射出成形部品の対向する壁にヒケを引き起こす可能性があり、これは主要な化粧品の表面である可能性があります。射出成形部品のシンクは、内部フィーチャーと外壁が交差するためにプラスチックの厚い部分が存在する場所です。厚い部分の体積が射出成形部品の隣接する公称肉厚よりも大きすぎる場合、内部のほとんどのプラスチック材料ははるかにゆっくりと冷却され、周囲のすでに冷却された剛性のあるプラスチックで収縮し、プラスチック表面にディンプルを作成します。外側とパーツの応力。
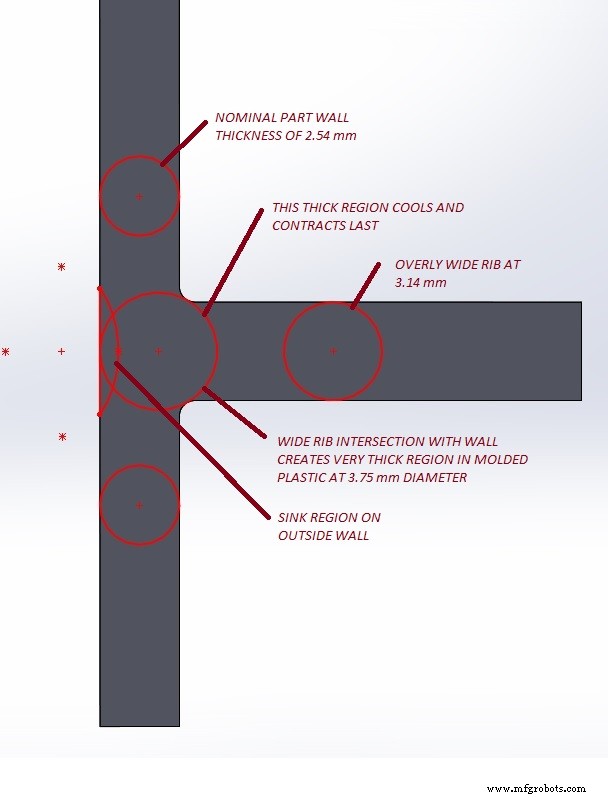
これにより、射出成形部品に反りが発生する可能性があります。さらに悪いことに、成形品のボス機能により、他の欠陥なしに射出成形部品を充填する能力に影響を与える他の金型流動の問題が発生する可能性があります。
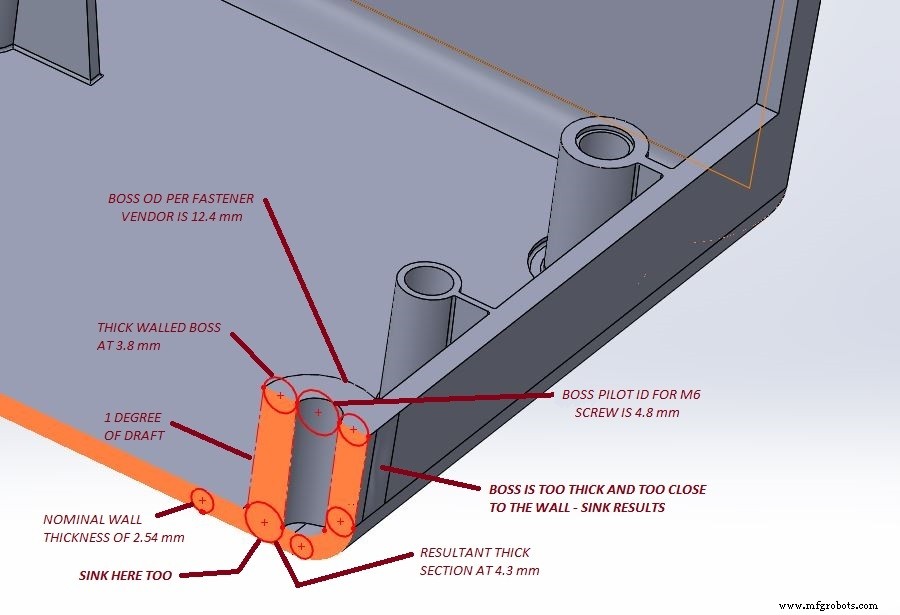
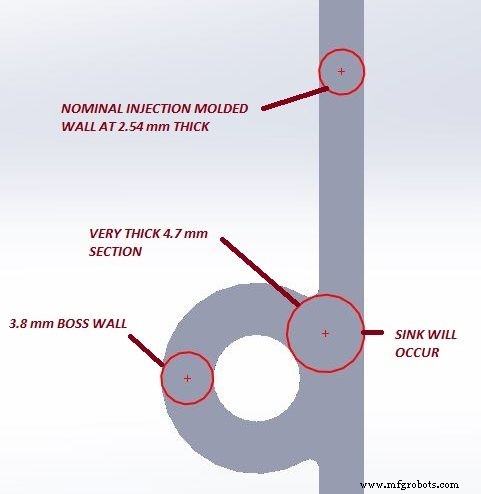
一方、小さめのボスは簡単に成形できますが、取り付けられたファスナーが保持されないため、部品やコンポーネントが緩んで製品が危険にさらされる可能性があります。さらに悪いことに、ボスが破裂して製造時に部品が拒否され、さらには完全になくなる可能性があります。現場での製品の故障。
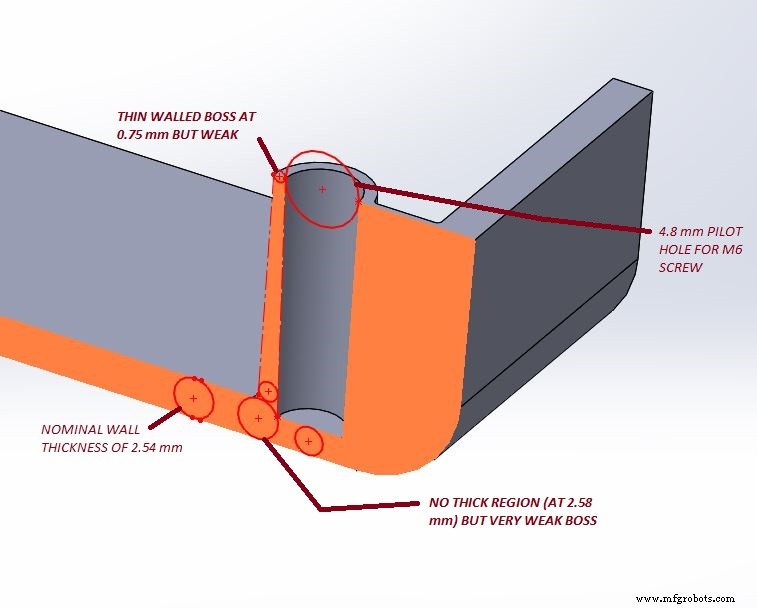
それを正しくするために、ファスナーがボスのパイロット穴に切り込むか、またはその方法を形成するときに、それらの取り付け力を処理するのに十分なプラスチック材料があり、ファスナーのねじ山は、強度を保持するためにボスに依存することができます。材料とプラスチックが少なすぎると、取り付け中に破損しない場合、残りの材料がジョイントの応力を分散するのに十分でないため、冷間流動してファスナー、ひいてはアセンブリが緩む可能性があります。これらの負荷は、製品に期待されるもの、製品に見られる圧力、さらには製品が使用される温度範囲によっても異なります。
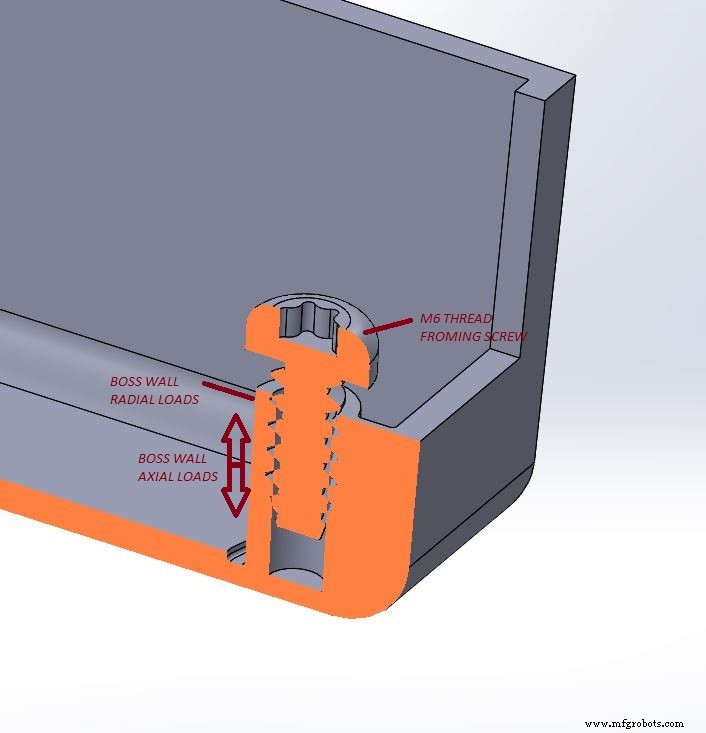
射出成形部品の成形の課題をさらに大きくするには、ボスは、少なくとも外径の壁で部品を鋼製金型ツールから排出できるようにドラフトを設定する必要があります。これは、ボスウォールの断面がベースで大きくなることを意味します。通常、このジャンクションにもわずかなフィレットを配置することをお勧めします。ただし、リブと同じように、先ほど説明したように、ボスは円形のリブと考えることができ、シンクを防ぐために、その壁のセクションは底にある公称壁の50〜60パーセント近くにする必要があります。この制約を維持することは困難になり、ボスの上部に十分な厚さの壁セクションがあり、そこにかみ合う留め具が、少なくとも非常に短いボス以外では、ボスの壁の側面を吹き飛ばすだけではありません。非常に短いプラスチックのボスでは、ファスナーによるねじ山の噛み合いがそれほど多くないことに注意してください。プラスチック製のネジの場合、通常、ネジのかみ合いには公称ネジサイズの2〜2.5倍が推奨されます。プラスチックボスにかみ合うねじ山の数は、スチールナットの金属ファスナーに従来よりも強度を高めるのに役立ちます。
可能な限り最強のボスにダイヤルインするために、射出成形の問題やシンクのような外観上の欠陥がないように、優れたデザインは推奨事項の意図を念頭に置いていますが、両方のサイズを少しごまかし、いくつかのトリックを適用します。
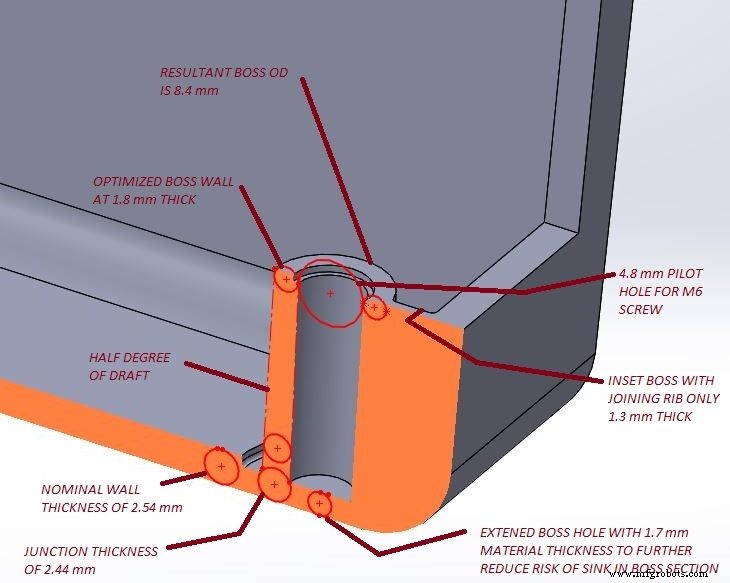
ボスの外径を、ねじメーカーの過度に厚い壁の推奨から、周囲のプラスチック壁と同様の強度を提供する適度に成形可能な厚さに縮小し、滑らかな内部ボス表面に最小限のドラフトを使用し、ボスを外壁から離して立てることにより、強度と射出成形の問題の低リスクの組み合わせ。外壁はほぼ一定の厚さに保たれ、接合リブは公称壁厚の50〜67パーセントに保たれます。ねじのパイロット穴は、推奨される最小直径に近いサイズですが、推奨される最小直径ではありません。ねじの噛み合いの深さが増すと、プラスチック射出成形ボスの強力な接合が保証され、荷重が分散されて応力が低下します。
ボスのボアがボスが位置する公称ベースの30%深くなり、ボスの壁のベースにある外側の周囲のトラフにより、交差する材料セクションが最小限に抑えられ、これらのトリックがない場合よりも厚いボス壁が可能になります。
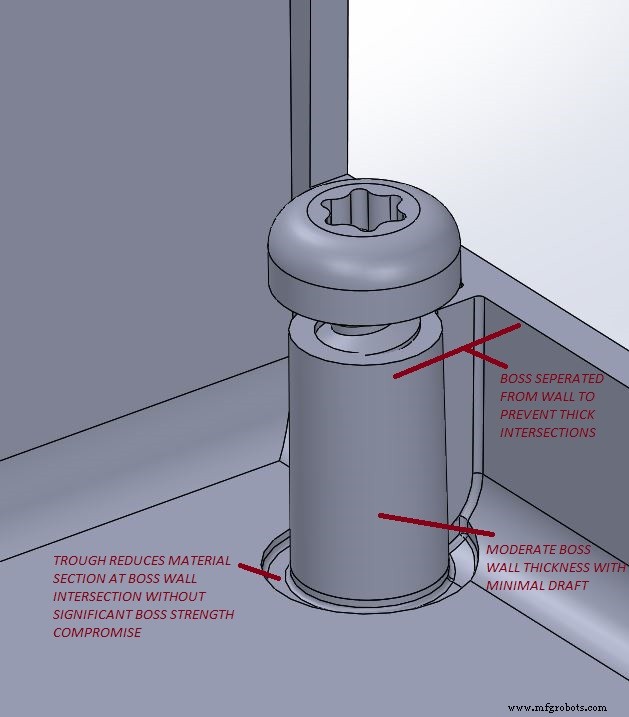
金属射出成形ツールから製造された最初の射出部品では、ボスと指定されたファスナーの性能をさらに評価および確認できることに注意してください。さまざまなねじ設計のプラスチックの用途に使用できる多くのねじタイプがあります。
さらに、製品の組み立てと部品の成形要件を考慮して設計された射出成形部品の適度に設計されたスクリューボスは、さらにダイヤルインするためにどちらの方向にも少し余裕があります。ボスをさらに厚くする射出成形部品の設計では、もう少し工具金属を取り除くだけで済みます。これは、金属または鋼の安全性と呼ばれ、材料を追加するよりも、材料を除去することによって金属射出成形ツールを変更する方がはるかに簡単で安価です。
ボスボアのサイズをいずれかの方法で変更することも、射出成形ツールのスチールピンの交換のみが必要になる可能性があるため、かなり簡単な場合があります。そして、これにより、ファスナーのかみ合い、アセンブリトルク値、およびプラスチック部品の応力を調整できます。これは通常問題ではありませんが、必要に応じてオプションです。たとえば、最初のパーツショットでプラスチック合金を変更する場合などです。
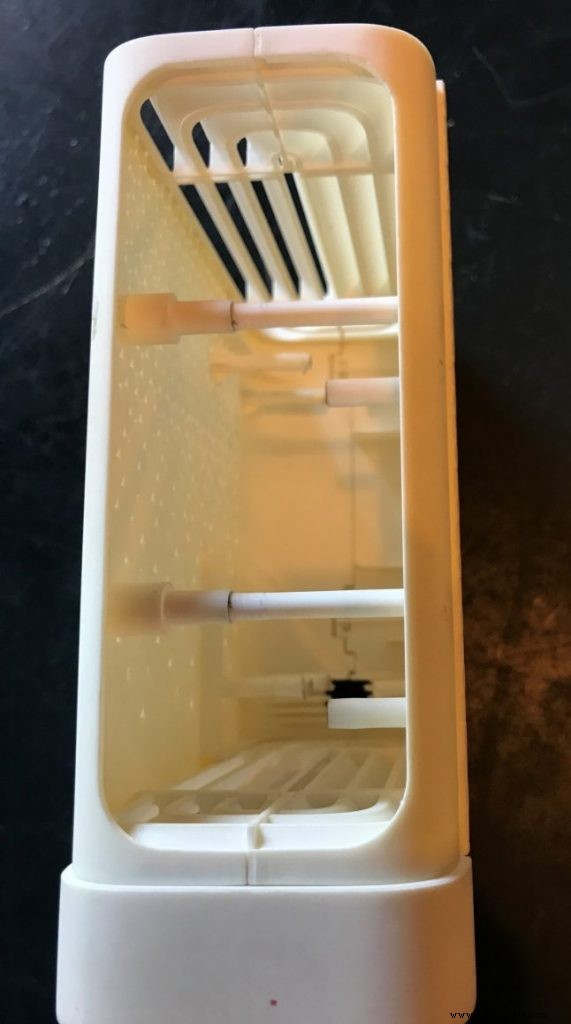
もちろん、個々の設計には独自の要件と優先順位があります。機能のみを目的としており、製品の外側には見られない一部の部品は、全体的な強度を損なう応力を与えない場合、成形上の欠陥を受け入れる可能性があります。これは、設計チームと成形業者が協力して可能な限り最高の部品を作成する必要がある場所です。
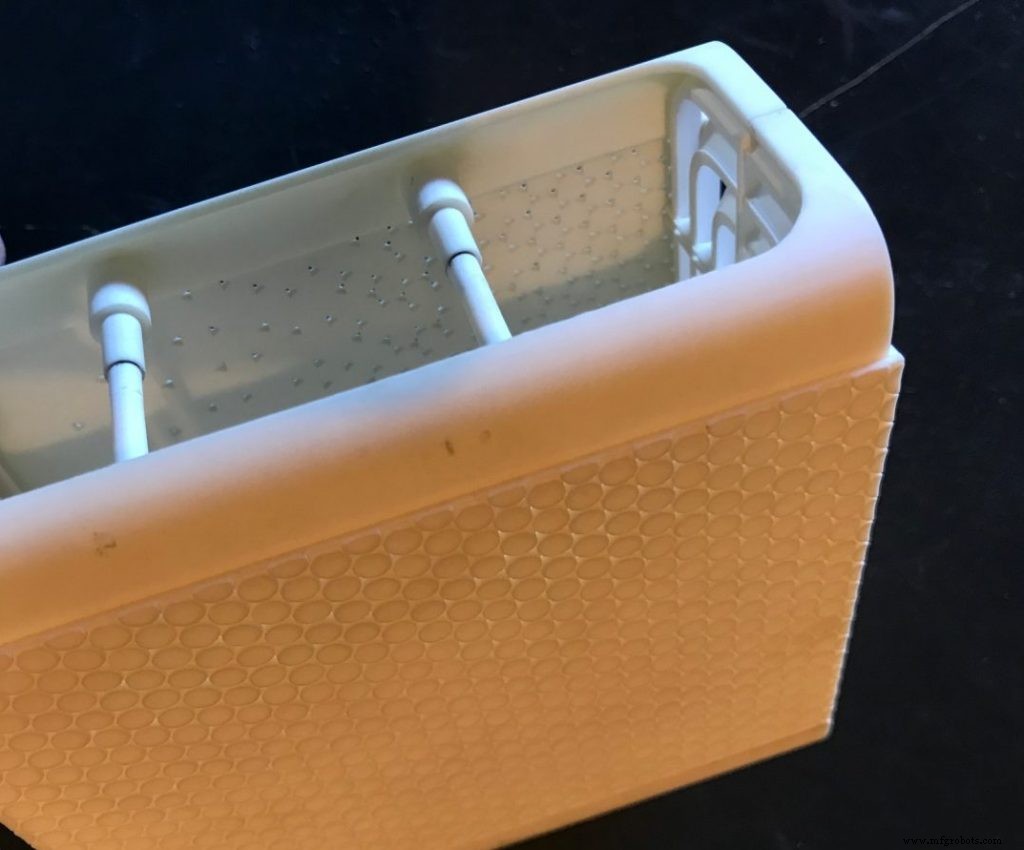
また、射出成形部品とそのボスの設計が両極端の境界線をたどった場合、成形パートナーがプロセス、サイクルタイム、冷却によって調整してマイナーシンクを減らし、「設計された」射出成形部品。
したがって、バランスの取れた設計に向けて作業し、穴の開発チームと協力して、射出成形されたボスの設計が成形しやすく、保持するのに十分な強度があることを確認します。
こちらをチェックしてください:パート1、パート2、パート4
製造プロセス