押し出しプロセス:定義、動作原理、タイプ、アプリケーション、長所、および短所[PDF付きのメモ]
機械工学の分野では、押し出しプロセス 固定断面積を持つオブジェクトを形成するためにエンジニアによって広く使用されています。オブジェクトを作成するために、原材料をダイに押し込み、目的の形状を提供します。
このプロセスの主な機能は、押し出しの場合、せん断応力と圧縮応力のみがプロセスで発生するため、脆性材料を簡単に目的の製品に変えることができることです。
押し出しは半連続的または連続的なプロセスであり、高温または低温の材料を形成するために使用できると主張することができます。
押し出しとは何ですか?
押し出しは、金属成形操作の一種であり、ダイを使用して、本質的に圧縮性のある外力を利用して金属片の形状を変更します。このプロセスにより、あらゆるタイプの複雑な形状を非常に簡単に作成できます。
押し出しの動作原理:
押し出しプロセスの場合に必要な力は、圧縮力を生成するためにプランジャーまたはピストンによって与えられます。押し出しプロセスの動作原理は次のとおりです。
- 最初に、標準サイズのインゴットまたはビレットがメーカーによって開発されます。
- 次に、熱間押出プロセスの場合、ビレットはより高い温度で加熱され、室温で長期間保管されてプレスに押し込まれます。
- ビレットは、プレスに取り付けられたプランジャーによってダイに向かって押され、圧縮力を提供します。
- ダイは、材料を目的の形状に現像するために必要な形状で事前に製造されています。高い圧縮力は、材料が目的の形状を実現するのに役立ちます。
- 最後に、材料はプレスから取り出され、その後、機械的特性を向上させるために仕上げプロセスを通過する必要があります。
押し出しの種類:
押し出しは大きく2つのタイプに分類できます。1つはホット押し出しです。 もう1つはコールドエクストルージョンです 。これらの前述のカテゴリもカテゴリに分類され、次のようになります。
熱間押出し
- 前方押し出し
- 後方押し出し
コールド押し出し
- 前方押し出し
- 静水圧押出成形
- フッカー押し出し
- 後方押し出し
- 衝撃押し出し
- 冷間押出鍛造
それでは、これらのカテゴリについて詳しく見ていきましょう。
熱間押出し:
このタイプの「熱間押出し」の名前ですでに想定されていることを願っています。このプロセスでは、ワークピースまたはビレットが再結晶温度を超えて加熱され、次にコンテナにロードされてから、ラムがそれに力を加えます。
ワークピースはすでに再結晶温度を超えて加熱されているため、ダイを非常に簡単に通過し、非常に正確かつ効果的に再成形されます。
このタイプの押し出しで使用される一般的な材料は、マグネシウム、銅、鋼、アルミニウム、ニッケルなどです。
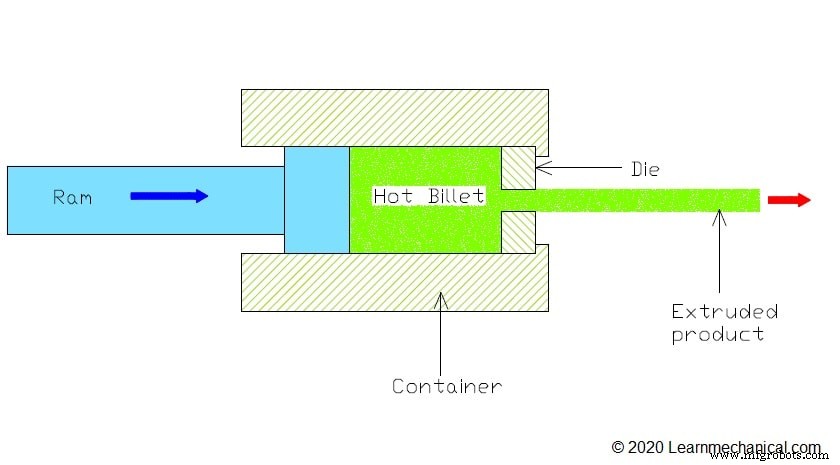
コールド押し出し:
このプロセスでは、ワークピースは通常の室温に保たれます。つまり、再結晶温度以下と言えます。このプロセスで製品を押し出すには、膨大な力が必要です。
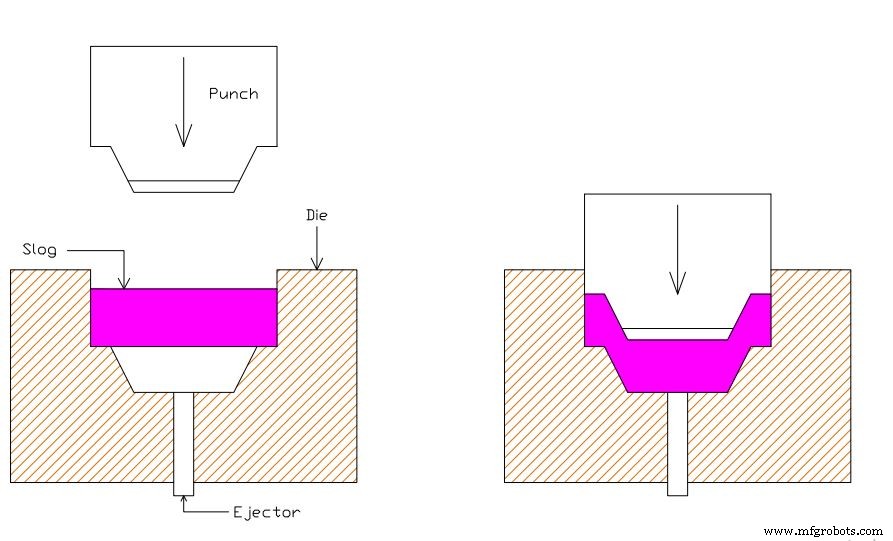
間接押し出し:
このプロセスでは、ラムによって加えられる力の方向と押し出された金属の方向は反対側にあります。このタイプの押し出しは、後方押し出しとも呼ばれます。
この押し出しモードの主な利点は、摩擦を比較的減らすことです。また、このプロセスにより、比較的直径の小さい金属を押し出すことができます。
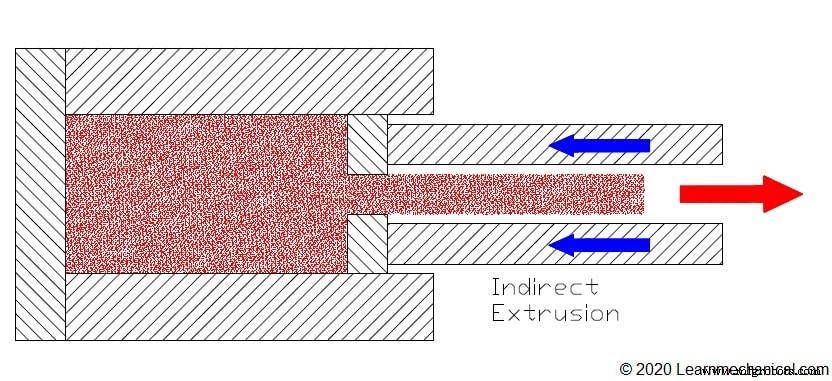
直接押し出し:
この押し出しプロセスでは、ラムの方向と押し出された金属の方向は同じ方向です。この押し出しモードは、前方押し出しとも呼ばれます。
このプロセスの主な利点は、このタイプによって、より長いワークピースを押し出すことができることです。
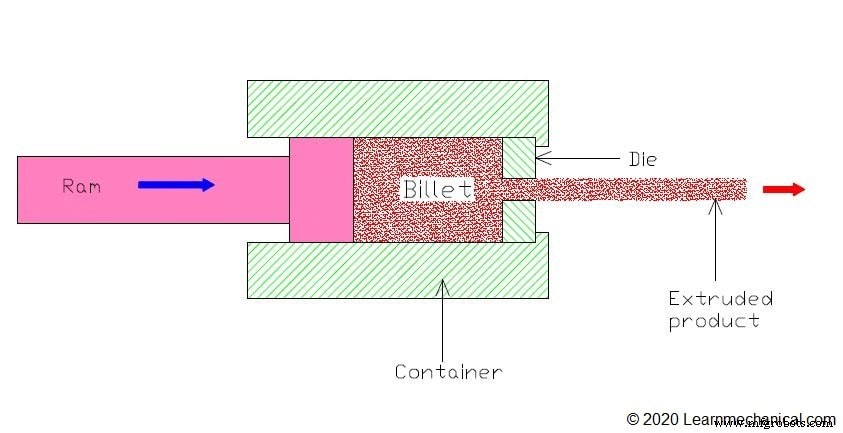
静水圧押出:
このタイプの押し出しでは、流体を使用してビレットを加圧します。最初にビレットがコンテナにロードされ、次にコンテナに液体、通常はヒマシ油が充填されます。次に、ラムとピストンを含むコンテナの片側を除いて、コンテナが閉じられます。
操作をスムーズに保つために、ビレットは円錐形に保たれているため、ダイを簡単に通過できます。
したがって、マシンを起動すると、ラムは流体に大きな圧力をかけ、それからビレットに転送されます。高圧流体により、塑性変形がビレットに発生し、それがダイの反対側に出て、ダイの形状になります。
このプロセスの主な利点は、コンテナの壁とビレットの間に接触がないため、作用する摩擦力が非常に少ないことです。
静水圧押出は通常、室温で行われます。
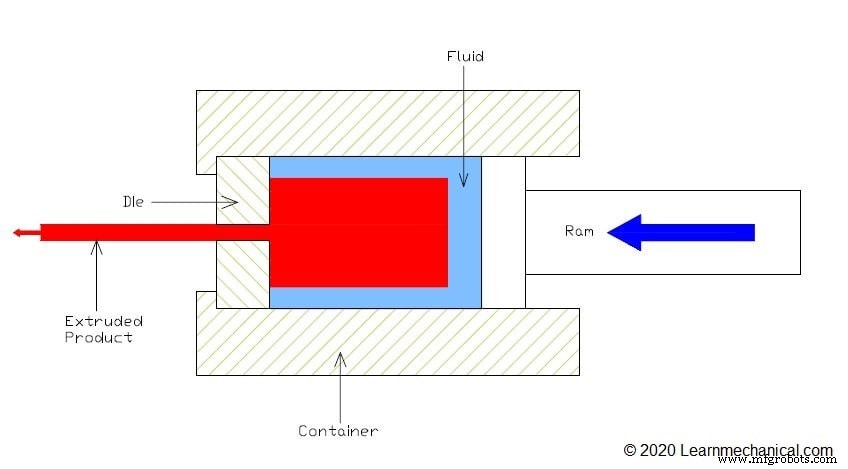
フッカー押し出し:
これは非常に人気のある押し出しプロセスであり、薄壁のシームレスな銅またはアルミニウムのチューブが製造されます。
まず、ビレットまたはブランクを容器に入れ、ワークにパンチを加えてカップ状にします。
次のステップでは、より長いパンチが再びカップに力を加え、それを長い円筒形の製品にし、通常どおり、厚さも減らします。
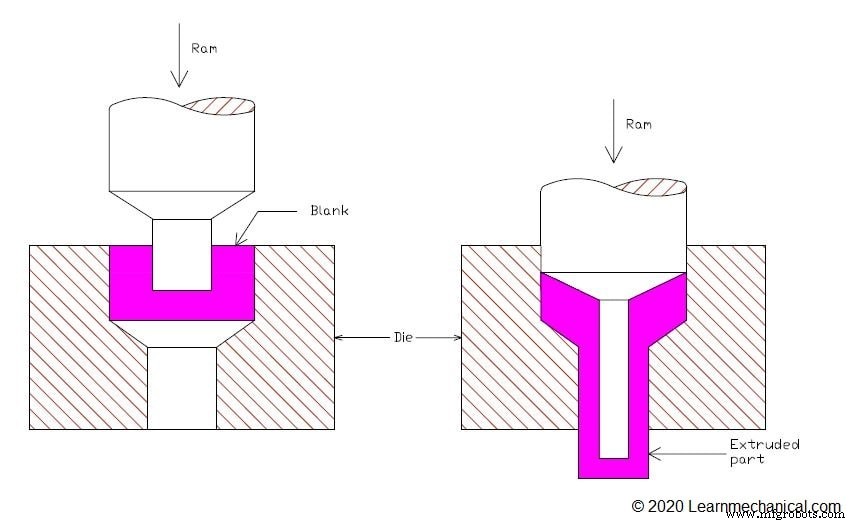
衝撃押し出し:
このプロセスでは、パンチが非常に高速でワークピースに打ち付けられ、衝撃荷重が発生します。フォワード、バックワード、さらにはその両方のような任意のタイプにすることができます。
これは通常、室温で行われます。つまり、冷間押出しです。
カップ、歯磨き粉のカバー、または中空部分などの製品が必要な場合は、通常、非常に一般的な衝撃押出プロセスである後方衝撃押出を行います。
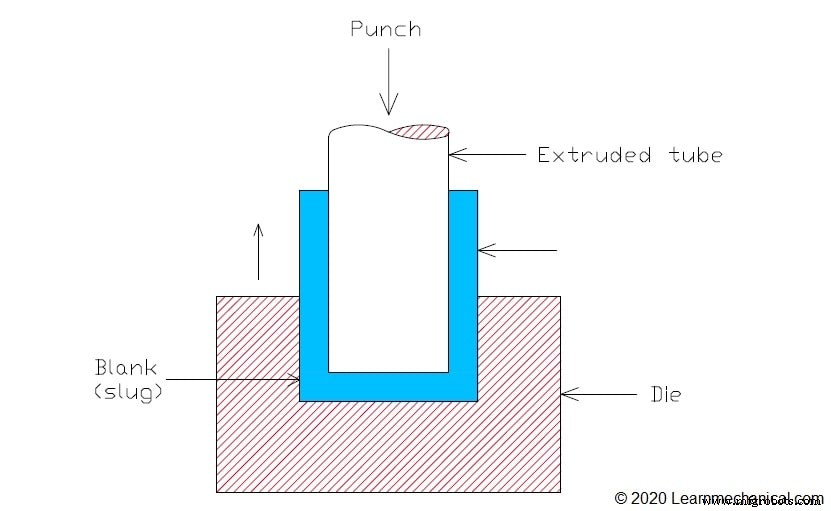
冷間押出鍛造:
冷間押出鍛造は逆押出プロセスです。冷間押出し鍛造のプロセスは、衝撃押出しのプロセスと同じです。このプロセスでは、パンチまたはラムの動きは衝撃押し出しよりも少し遅くなります。ブランクにかかる力が徐々に大きくなるため、押し出された製品の長さはかなり短くなりますが、厚みは大きくなります。
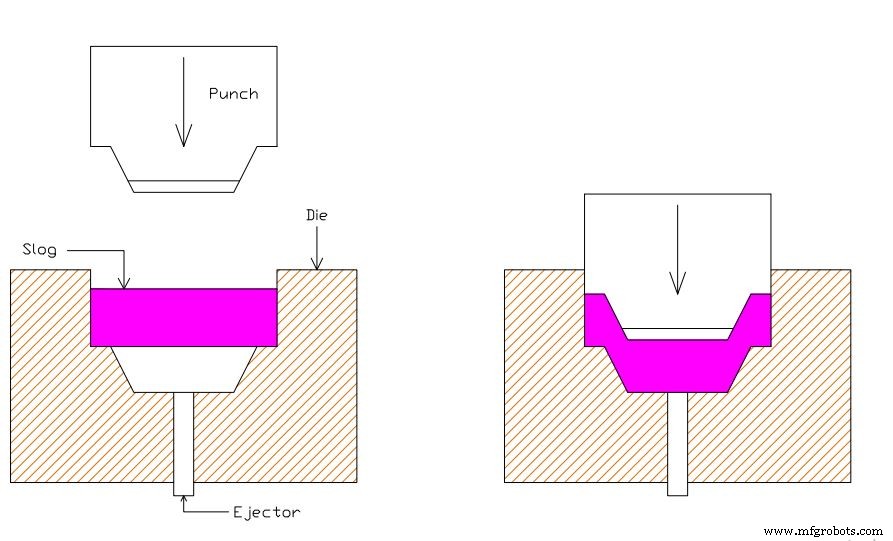
押し出しプロセスのアプリケーション:
- 押し出しプロセスは、主に中空パイプの形成に使用されます そしてそれは生産産業で使用することができます。それとは別に、インスタント食品やスナックタイプの製品を製造するために、製造業者は押し出しプロセスを検討しています。食品加工の場合、押出成形プロセスを使用して製品を加熱し、製品の液相を発生させます。また、調理では、混合、剪断、分離、冷却、加熱などを含む押し出しプロセスが今日使用されています。製品から水分を除去するため、また材料をカプセル化するために、生産者は押し出しプロセスも考慮に入れています。
- ただし、すぐに食べられる材料を開発するには、冷間押出しプロセスが使用されます 。一例として、パスタタイプの製品は、冷間押出しプロセスの助けを借りて製造されます。これらのタイプの製品は低水分で組み込まれているため、製品のライフサイクルが長くなり、顧客へのサービスもより便利になります。
- さらに、医薬品も押し出しプロセスの助けを借りて開発されています 。ポリマーフィルター、ナノポーラス製品は、押し出しプロセスによって形成されます。医薬品の製造プロセスには、高温および低温の押出成形プロセスがあります。製品の溶解性と生物学的利用能を高めるために、熱間押出プロセスが使用されます。このプロセスでは、大量の圧力、熱、および攪拌がメーカーによって考慮されます。
- それとは別に、構造作業では、アルミニウム押し出しプロセスが使用されます 。このプロセスには、ドア、窓などが含まれます。自動車産業では、押し出しプロセスは、脆い材料を使用して目的のタイプの材料を形成するためにも使用されます。
- 最後に、押し出しプロセスはプラスチック材料の製造に広く使用されていると言えます。 。
押し出しプロセスの利点:
押し出しには、次のようないくつかの利点があります。
- 押し出しプロセスは、他の金属成形プロセスと比較して、最短時間で材料の複雑なプロファイルを作成するために広く使用されています。
- 押し出しプロセスは、脆くて延性のある材料を扱う場合に非常に便利です。
- 押し出しプロセスによって開発できる機械的特性は非常に正確であり、製品のライフサイクルを向上させます。
押し出しプロセスのデメリット:
押し出しのいくつかの欠点を以下に示します:
- このプロセスにかかる時間は非常に長くなります。
- 初期のセットアップコストも非常に高くなります。
- 押し出しプロセスに必要な圧縮力の量も非常に大きいため、オペレーターはプランジャーがプレスに適切に固定されていることを確認する必要があります。
結論:
つまり、これはすべて押し出しプロセスの詳細です。
この記事がおもしろいと思います。
もしそうなら、あなたの友人やあなたのお気に入りのソーシャルメディアグループの間でこのリソースを自由に共有してください。あなたの1つのシェアは本当に評価できます。
産業技術
- ホーニングプロセス:定義、部品または構造、動作原理、利点、アプリケーション[PDF付きのメモ]
- ラッピングプロセス:定義、動作原理、タイプ、材料、利点、アプリケーション[PDF付きのメモ]
- すくい角:定義、重要性、およびタイプ(正、負、ゼロ)[PDF付きのメモ]
- クイックリターンメカニズム:定義、タイプ、動作原理、アプリケーション、長所、短所[PDF付きのメモ]
- 電子ビーム溶接:定義、構造、作業、アプリケーション、長所、および短所[PDF付きの注記]
- プラズマアーク溶接:原理、動作、機器、タイプ、アプリケーション、長所と短所
- ソリッドステート溶接プロセス:原理、タイプ、アプリケーション、長所と短所
- 爆発圧接:原理、動作、タイプ、アプリケーション、長所と短所
- 摩擦圧接:原理、動作、種類、用途、長所と短所
- MIG溶接:原理、動作、機器、アプリケーション、長所と短所
- TIG溶接とは:原理、動作、機器、用途、長所と短所