線材の圧延の重要な特徴
線材の圧延の重要な機能
線材は通常、鋼の温度が1,000℃を超え、最大圧延速度が毎秒120メートル(m / s)を超え、製造される線材のコイルの長さが最大10 km(km)の高速圧延機で圧延されます。 。線材の圧延中、連続圧延機では通常25パスから30パスが行われます。
線材は非常に幅広い用途の素材です。自動車産業向けのコンポーネント、タイヤコード、電極、ナットやボルトなどの接続要素、ばね、ワイヤーおよびワイヤー製品、鉄筋など、すべてがワイヤーロッドに基づいています。そのため、線材ミルは通常、汎用性を念頭に置いて設計されています。ミルはエネルギー集約型のミルであるため、柔軟性を損なうことなく、最適なソリューションをミルの設計に組み込む必要があります。すべてのサイズ範囲、材料、合金は、線材工場で効率的かつ高い生産性で生産される必要があります。
線材は、線材ユーザーの表面および内部品質、ならびに物理的、化学的、機械的、および冶金学的特性の要件を満たす必要があります。線材は、引き抜き、鍛造、希望の形状への機械加工などの後処理と熱処理を行い、製品が希望の強度を実現できるようにします。したがって、線材は、使用される場所を問わず、製造された部品の良好な性能を保証すると同時に、後処理のさまざまな段階で良好な作業性を確保できる必要があります。
線材のユーザーには、3つの基本的な要件があります。つまり、(i)1つ以上の2次または3次処理を排除または簡素化して生産性を向上させ、処理コストを削減すること、(ii)機能を向上させること、つまり耐用年数を延長することです。軽量化、または線材が使用される最終製品に他の利点をもたらすため、および(iii)後処理プロセス中の環境に有害な物質の使用を排除するため。
消費者のますます厳しくなる要件を満たすために、線材工場は、さまざまな観点から、すなわち(i)寸法精度の向上、(ii)サイズフリー圧延(すなわち、圧延)の実装から、圧延線材の全体的な能力を備えている必要があります。ロールを変更せずにさまざまなサイズの製品)、(iii)ロール交換作業を高速化することで生産性を向上させる(ロール交換時間を短縮する)、(iv)輸送中の表面欠陥の発生を防止することで製品の表面品質を向上させるローリングプロセス。
線材工場は、材料だけでなく、最終製品が製造されるまでの二次および三次処理での長い後続処理の要件を満たすために線材を供給することになっています。さらに、最終製品はさまざまな産業分野で重要な部品として使用されることが多いため、顧客との統合されたコラボレーションにおけるプロセスの合理化が求められます。したがって、ミルは、ユーザーの品質要件を満たすだけでなく、後続の処理中にユーザーの生産性、歩留まり、柔軟性、および製造コストの要件を満たすことができる必要があります。高いミル歩留まりと適切な製品品質は、生産コストの管理にとって最も重要です。
線材工場の生産能力は、いくつかの標準製品の大量生産か、多数の鋼種と特殊な製品品質を備えた線材で構成される多様な製品構成のいずれかに依存します。
線材工場は基本的に(i)初期材料(ビレット)を圧延温度に加熱するための加熱設備、(ii)ロール、チョック、ガイドおよびガードを備えた圧延スタンドからなる圧延設備、(iii)敷設、熱処理、およびコイリング装置、および(iv)運搬および取り扱い装置。すべての機器は、圧延温度、ギャップ時間損失、速度損失、丸石、不適合製品、および転用または拒否につながる品質偏差の制御と緊密に連携して動作する必要があります。
最新の線材工場からの要件
線材工場で線材を圧延するためのいくつかの重要なパラメータ(図1)があります。最新の線材工場は、一般的に「設備総合効率」(OEE)の哲学で機能するように設計されています。ミルのOEE値は、ミルの使用率、ミルの効率、およびミルの歩留まり時間を乗算して得られる値です。ミル使用率は、利用可能な稼働時間を計画生産時間で割ったものであり、パーセンテージで表されます。ミル効率は、稼働時間をミルの利用可能な稼働時間で割ったものであり、パーセンテージで表されます。ミル降伏時間は、稼働時間に関連する主要製品を生産するための時間です。製品の歩留まりは、受け入れられたコイルの重量をビレットの重量で割ったものとして表され、パーセンテージで表されます。
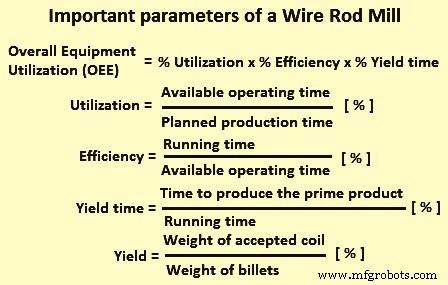
図1ワイヤーロッドミルの重要なパラメーター
線材ミルは通常、他の種類のミルよりもOEEが低くなります。これは、製品のシフト中のロール交換とスタンド交換、および溝とガイドの調整のダウンタイムが長いためです。このダウンタイムを減らすことができれば、工場のOEEを改善できます。
ミルの理論上の生産能力は、損失なしに、つまり100%の使用率、100%の効率、100%の歩留まりで得られる能力です。ただし、実際の容量は工場のOEEレベルによって異なります。ミルのOEEレベルが60%の場合、ミルのミル生産能力は理論能力の60%です。明確に定義された最適化されたミルを備えた最先端の線材ミルのOEEレベルは、通常80%のレベルです。
線材工場の低品質のコストは、一般に、検査コストと、内部および外部の欠陥による線材の拒否/迂回の合計として決定されます。高性能ミルの場合、約10%になる可能性があります。多数のグレードと特殊な製品品質を備えた線材で構成される多様な製品構成を備えた線材ミルでは、最大30%増加する可能性があります。
現代の線材工場では、主な焦点は生産性と品質にあります。高い使用率、効率、および歩留まりにより、高い生産性が得られます。しかし、高い生産性自体が線材工場の成功の唯一のものではありません。それは顧客に価値を与える製品を生産しなければならず、彼らは彼らが線材に対して行っている支払いに値する高品質の線材を手に入れます。
ミルの生産性と使用率は、ミルのレイアウトや製品の組み合わせなど、いくつかの理由によって引き起こされるミルのダウンタイムに依存します。ミルでは、ビレットから最終製品までの歩留まりがすべてのステップで記録され、ミル内の材料の追跡により、ミル内で発生した損失が追跡されます。工場で発生する損失の主なカテゴリは、(i)ギャップ時間損失、(ii)速度損失、(iii)玉石による損失、(iv)品質偏差による損失、(v)工場による損失です。ダウンタイム、(vi)ミルの仕上げ側での検査中の線材の迂回/拒否による損失、および特殊な線材製品の生産の場合の価値向上操作による時間損失。
ミルの柔軟性
線材ミルでは、鋼(ビレット)が再結晶温度以上に加熱され、圧延機のロールのいくつかの溝を通過します。線材工場で使用される一般的なロールパスの設計は、ダイアモンドスクエア、ダイアモンドダイアモンド、ボックスパス、スクエアオーバル、フォールスラウンドオーバル、およびラウンドオーバルです。線材工場では通常、サイズフリーローリングが行われています。つまり、ミルに保持されているロールのパスサイズの制限なしに、任意のサイズの線材を圧延できます。これは、シリーズの柔軟性としても知られています。さらに、上流の圧延機のパススケジュールの簡素化により、ロール交換の頻度を大幅に下げることができます。同じロールで巻くことができる製品サイズの範囲(サイズの放し飼い)が広いほど、ロール交換の頻度を減らす効果が大きくなります。サイズフリーローリングは仕上げミルに限定されません。プレフィニッシングミルにも適用できます。
生産性を向上させるために、線材工場のダウンタイムを最小限に抑えることに重点が置かれています。このような焦点の有効性は、通常、新しい最終寸法と新しい鋼種および形状を製造するときにロールを変更する時間と必要性を減らすことによって強化されます。これは、シリーズの柔軟性とも呼ばれる作業範囲を改善することによって達成されます。圧延スケジュールの変更を最小限に抑えて、さまざまな形状と寸法のさまざまな鋼種を大量に圧延すると、柔軟性が向上します。すべての鋼種は、ロールギャップを通過するときのさまざまな広がりなど、特定のロジスティクスの方法によって特徴付けられます。また、実際の鋼種によっては、起動時間と正しい圧延温度を待つ時間を減らす必要があります。ただし、さまざまなグレードを圧延する場合は、加熱サイクルが異なると、ダウンタイムが長すぎます。小ロットや多種多様な鋼材を含む今日の市場の需要を満たすために、現代の線材工場は高度な柔軟性を示すことが必要になっています。
線材工場の特別な側面は、柔軟なロールパス設計、または高い作業範囲を備えた柔軟なグローブの使用です。柔軟なロールパスシーケンスを使用することで、ロール距離を変更するだけで、幅広い完成品の同じ溝でローリングを実行できます。したがって、溝の変更は、ロールギャップの単純なシフトで置き換えることができ、これにより、ある製品から別の製品に変更するためのダウンタイムが短縮されます。ロールパス設計の柔軟性、ミルの使用率、および歩留まりの間には強い相互依存関係があります。
柔軟なロールパス設計を採用することにより、ミルでの損失の重要な部分を減らすことができます。柔軟なロールパス設計により、鋼種の変更中に溝が過剰に充填されたり、丸石が作成されたりするリスクが最小限に抑えられます。柔軟なロールパス設計は、新しいサイズや鋼種を導入する必要がある場合の製品開発にも利点があります。また、柔軟なロールパス設計により、実行時間を向上させる価値の重要な改善を実現できます。
ミルの生産性
線材ミルは、仕上げブロックの前に冷却床出口を設けることにより、バーミルと組み合わせることができます。これは通常、上流の圧延機の能力を利用するために行われます。線材ブロックでロールが変更されると、ミルの総ダウンタイムを短縮するために、上流のミルがバーを生成します。
最新の線材ミルは、一般的に一本鎖圧延機です。マルチストランドミルの場合、ストランドの同時圧延数の変化の影響を減らすために、第2の中間圧延機が各ストランドに導入されます。第2の中間圧延機は、前仕上げブロックの形をとることができる。また、3ロール圧延機ブロックの形にすることもできます。三圧延圧延機の主な特徴は、従来の二段圧延機と比較して、圧延材の全周を圧延する三溝圧延機間の寸法のばらつきを抑制し、広がりを低減できることです。この中間ミルはサイジングミルとして知られており、低還元によって成形が行われます。これは、工場の上流で家族のローリング哲学を持つのに役立ち、リセット時間を短縮します。
ミル速度を上げてミルの生産性を上げるために、従来の仕上げブロックの後に減速/サイジングミル(RSM)を設置します。従来の仕上げブロックの後にRSMを統合すると、小さなサイズでのミルの生産性が大幅に向上します(最大60%)。その極端な精度は、多くの設置で証明されています。さらに、非常に低温の圧延と組み合わせることで、これにより、追加の二次プロセスを排除できる、より洗練された微細構造が得られます。 RSMは、生産性と完成品の品質向上の両方を提供し、同時に運用コストを削減し、線材製品の品質を向上させます。荒削りグループのスタンド1から仕上げブロックの最後のスタンドまでのシングルロールパス設計に対応します。同じシングルファミリーパスの設計が容易になるため、最終製品のサイズに関係なく、高いミル効率を維持できます。
ワイヤーロッドのローリングでは、通常、スタンド間の張力は可能な限り回避されます。そうしないと、自由端が張力下で回転できないため、ヘッドとテールの端が許容範囲から外れます。この事実により、溝がいっぱいになり、フィンなどの端部に欠陥が生じる可能性があります。ただし、トランスミッションが固定された高速ツイストブロックなしでは、安定したローリング条件を実現するためにスタンド間の張力が使用されます。ロールドバーにスタンド間の張力がかかると、必要な許容誤差が得られるようにグローブが設定されます。
ワイヤーロッドの品質
線材はいくつかの用途で使用されています。多くのアプリケーションでは、線材の品質要件は非常に厳しいものです。線材の品質が悪いと、最終製品の欠陥や流用が増えるだけでなく、顧客側の歩留まりに悪影響を及ぼし、顧客に不満をもたらします。
線材圧延はエネルギーを大量に消費する圧延であるため、欠陥のある線材コイルの圧延を最小限に抑えることが常に必要です。ビレットの欠陥が非常に大きい場合、ミルに玉石が発生することもあります。ビレットからの線材の長さが非常に長いため、圧延後の線材の全長にわたる品質保証には時間と労力が必要です。このため、ビレット(圧延前の出発原料)の品質管理は非常に重要です。欠陥のあるビレットは、ビレット検査によって識別、分離、および除去する必要があります。ビレットは、表面の欠陥と内部の欠陥の両方について検査されます。ビレットを研削(コンディショニング)することで、表面の小さな欠陥を取り除くことができます。
線材(特に細い線材)に求められる重要な特徴は、二次加工での高い生産性と最終延伸後の高強度です。生産性が高いということは、線引きやバンチング時の断線を最小限に抑えるか、理想的には断線がなく、直接延伸性が高く、延伸速度が速いなどの過酷な延伸条件でも良好な延伸性を発揮することを意味します。非金属介在物、分離、脱炭、機械的特性、微細構造などの品質管理項目に厳格な基準を適用することにより、顧客のこれらのますます洗練された要件。
通常、多くの用途の線材には3つの主要な要件があります。これらは、(i)より高い強度、(ii)後処理の排除または簡素化、および(iii)環境に有害な物質の使用の減少です。ユーザー側のコスト削減など多くの理由から、より高い鋼強度が求められています。なぜなら、ユーザー側では、線材は鍛造、線引き、機械加工などのさまざまな種類の二次加工と、焼きなまし、焼き入れ、焼き戻しのための熱処理が行われるためです。
したがって、コスト削減、省エネ、環境保全の観点からの要件は、熱処理と機械加工(ニアネットやチップレス成形など)の排除または簡素化を強く求めています。
非金属介在物、析出物、変態、および冶金学的構造の制御は、線材の特性を向上させるための重要な冶金学的手段です。非金属介在物の制御は、ばね鋼の強度向上、軸受鋼の耐用年数の延長、快削鋼からの鉛の除去などの主要なシード技術の1つです。硫化物は、これらの鋼の望ましい特性を実現するのに効果的です。
線材工場では、指定されたコイル材料の特性を正確に満たすという点で妥協はありません。ここで、制御された冷却コンベヤー(CCC)システムが重要な役割を果たします。線材コイル全体の一貫した高品質を管理する必要があります。
この点で、CCCシステムは、高品質の線材製品を処理するために重要な役割を果たし、望ましい均一性、および冶金学的および機械的特性を実現します。急速に冷却された製品のリング周辺の引張強度の変動を、平均引張強度の1%以内の標準偏差に厳密に制御します。
冷却方式を適切に選択することにより、CCCシステムは、従来のすべての鋼種と、代替の冷却モードを備えた特殊製品の生産に対応します。また、RSMと組み合わせて使用すると、炭素鋼および合金鋼の処理が最適化され、低温圧延および制御された冷却が可能になり、特性と寸法制御の非常に優れた組み合わせが実現します。
CCCシステムは、単一システム内の高速冷却モードと低速冷却モードの両方を含む、幅広い条件での処理を容易にします。この機能により、線材工場は、ステンレス鋼やその他の特殊鋼だけでなく、幅広い種類の普通炭素鋼や合金鋼を製造することができます。 CCCシステムにより、線材の圧延時の棒状特性が向上し、直接使用可能な状態でより多くのグレードを製造できるようになり、球状化焼鈍などの下流プロセスが削減または排除されます。
線材ミルの熱機械圧延(TMR)は、動的再結晶の結果として最終結晶粒径を微細化します。最終的なインライン水冷およびCCCシステムの優れた制御された冷却と組み合わせることで、TMRは最終製品の特性を決定する上で重要な役割を果たします。これは、下流の処理中にその後球状化焼鈍される低合金および中合金鋼製品に特に有益です。結晶粒径を強力に制御する能力は、変態開始時間と温度をシフトすることにより、ベイナイトやマルテンサイトなどの硬質製品へのその後の変態にも影響を与えます。したがって、TMRは、直接下流の冷間加工を最小限に抑え、焼きなまし時間を短縮できます。
CCCシステムでの処理と低い圧延温度の組み合わせにより、いくつかの重要なグレードの線材の焼入れ性を低下させることができます。最終的に、これはフェライト形成を促進し、ベイナイトとマルテンサイトへの進化を遅らせます。 TMRによって達成された微細な粒子サイズは、熱処理中の拡散を改善し、熱処理時間と温度を下げることができます。熱処理されていないロッドの場合、洗練された複雑な構造により、冷間変形時の引張ピックアップが増加し、(i)圧延時の引張強度の低下、(ii)下流応答の改善、(iii)作業の増加などのいくつかの利点が得られます。焼入れ性。改善は、結晶粒の微細化と微細構造の制御に起因します。 CCCシステムでの冷却プロセスの適切な制御と線材の焼入れ性の低下により、プロセスが非常に安定し、不要な硬質相が形成される可能性が低くなります。
製造プロセス