射出成形における均一な肉厚の重要性[ガイド]
プラスチック部品を分解したことがある場合は、これらの部品の壁の厚さが均一なサイズであることに気付くでしょう。まあ、それは偶然ではありません。肉厚は、成形品の成否を決定する上で大いに役立ちます。これは、射出成形設計の最も重要なルールの1つです。適切に行わないと、部品の加工時に多くの問題が発生する可能性があります。この記事では、均一な射出成形の厚さが重要である理由、適切に行われなかった場合に発生する可能性のある欠陥、および材料の選択と射出成形壁の機械加工との関係について説明します。
射出部品の壁を設計する際に考慮すべき原則
機械加工が終了した後、金型から簡単に取り外せるように、成形品を収縮させる必要があります。射出成形プロセスでプラスチック部品が収縮する速度は、壁の厚さと使用する材料のプラスチックの厚さという2つの主要な要因によって異なります。すべてのプラスチック部品は、冷却すると収縮します。したがって、これらのプラスチック部品の設計は、この収縮が均一になるように行われます。収縮率の変化は、美容上の欠陥と致命的な欠陥の両方につながります。壁の厚さのプラスチック設計中に、設計者が注意するいくつかのルールがあります:
シャープなコーナー
パーツの角は、パーツが故障するかどうかを判断する上で非常に重要です。これは、部品の角が鋭くなり、応力集中が高くなるためです。これにより、塑性流動が妨げられ、成形品に欠陥が生じる可能性があります。これを防ぐために、ほとんどの設計者は、コーナーの内側の半径をプラスチックの厚さの0.5倍にし、外側の半径をプラスチックの厚さの1.5倍にします。
隣接する壁の厚さ
隣接する壁の場合、一方の壁の厚さは、もう一方の壁の40〜60パーセント以上でなければなりません。また、両方の壁の厚さが特定の材料のしきい値内にある必要があります。
ドラフト角度
ドラフトは、金型からの部品の簡単な取り外しを容易にするのに役立ちます。一般に、プラスチックの厚さが許す限り多くのドラフトを許容する必要があります。ほとんどの場合、プラスチックの厚さ0.25mmごとに1.5度追加するとともに、1〜2度のドラフトで十分です。これは、肉厚と成形品の厚さの成形設計によって異なる場合があります。
ボス
壁の厚さに関する成形設計のガイドラインは、ボス(ねじ用の開口部を囲む円筒形の構造)に適用する必要があります。それらは、周囲の領域の40〜60パーセントの厚さである必要があります。
リムとベンド
リムとベンドの厚さも可能な限り均一にする必要があります。これを確実にする1つの方法は、曲線に適切な半径を追加することです。これにより、プラスチック材料が金型キャビティ内をスムーズに流れるようになります。
リブ
リブは、強度が必要な部品に実装できます。部品を厚くするよりもリブを使用する利点は、反りのリスクを減らすことです。リブは、冷却が速く、製造に必要な材料が少ないため、費用対効果も高くなります。
均一な壁の厚さを維持することが重要なのはなぜですか?
外観
不均一な肉厚は、射出成形部品の美観に影響を与えます。壁の厚みが不均一なため、反りやヒケなどの不具合が発生する場合があります。フローラインなどの表面的な問題にも気付く場合があります。
ゲーティングの課題
ゲートは厚い部分から薄い部分へと行われます。壁の厚さが不均一であると、溶融プラスチックが薄い部分から厚い部分に流れる可能性があります。これにより、プラスチック材料が薄い部分で冷却を開始し、厚い部分への流れを効果的に遮断する可能性があるため、問題が発生します。この結果、沈み込みや反りなどの欠陥が発生します。
せん断応力
流動中のプラスチックのせん断応力は、壁の厚さを変えることによって影響を受ける可能性があります。一定の充填速度で移動する流動プラスチックのせん断応力は、肉厚が減少するにつれて増加します。したがって、壁の厚さが不均一になると、せん断応力の程度が異なります。これは、プラスチックの反りの主な原因です。
冷却速度
厚い部分は冷却に時間がかかります。肉厚が不均一な成形品は、成形品全体が冷えるまで金型内に留まらなければなりません。これにより、サイクルタイムと全体的な製造プロセスが向上します。
コスト
より厚い壁は、充填するためにより多くのプラスチック材料を必要とします。また、冷却するのにより多くの時間が必要です。より多くの材料と射出成形機でのより長い時間は、生産コストを増加させるだけです。
壁の厚さが不均一であるために発生する欠陥
射出成形は部品の製造に最適な方法の1つですが、最終製品に欠陥をもたらす可能性のある要因がまだあります。成形プロセスおよび使用される材料の塑性厚さの結果として、いくつかの欠陥が発生する可能性があります。以下に、壁の厚さによって影響を受けるいくつかの欠陥を示します。
ワーページ
反りは、製品のさまざまな部分の不均一な収縮の結果として発生します。これにより、完成時に製品の形状にねじれや曲がりが生じます。強調されているように、壁の厚さが不均一であると、製品の一部がさまざまな速度で冷却され、反りが発生します。
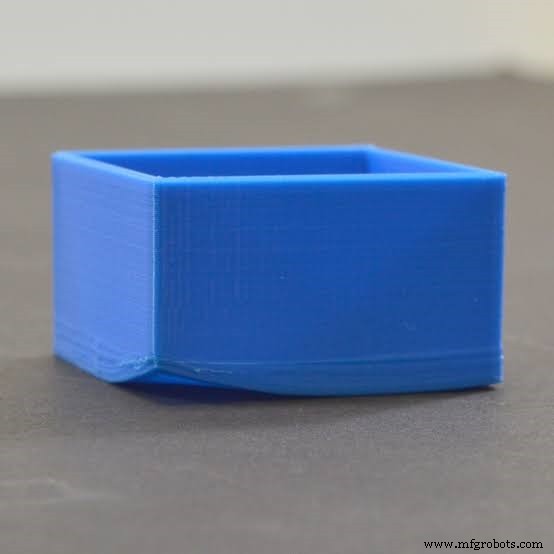
フローライン
フローラインは、プラスチック製品で発生する美的欠陥です。それらは波または線として表示され、通常は周囲の領域とは異なる色調になります。これらは、金型キャビティ内の溶融プラスチックの流量が異なる結果として発生します。
シンクマーク
シンクマークは、射出成形製品に形成された小さなクレーターのようなものです。これらのクレーターは、金型内でプラスチック材料を完全に冷却できない場合に形成されます。収縮マークは、冷却に時間がかかるため、製品の厚い部分に形成されることが多くなります。
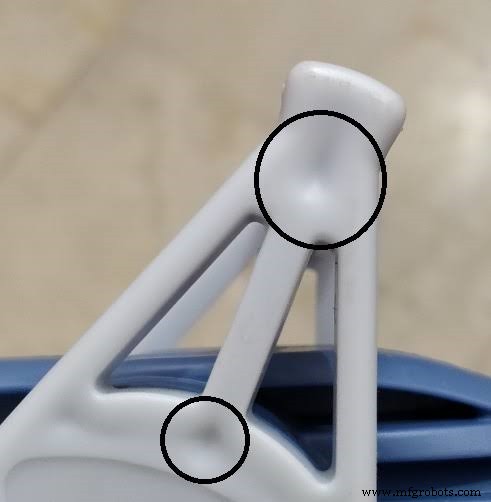
ショートショット
ショートショットは、製品の一部が欠落している場合に発生します。これは、溶融プラスチックが金型のすべてのセクションに到達できないために発生します。不均一な壁の厚さは、この欠陥につながる可能性があります。肉厚が不均一な場合、薄い部分から大きな部分に流れるプラスチックは、時期尚早に冷却される可能性があります。これにより、溶融プラスチックが厚い部分に到達するのを防ぎます。
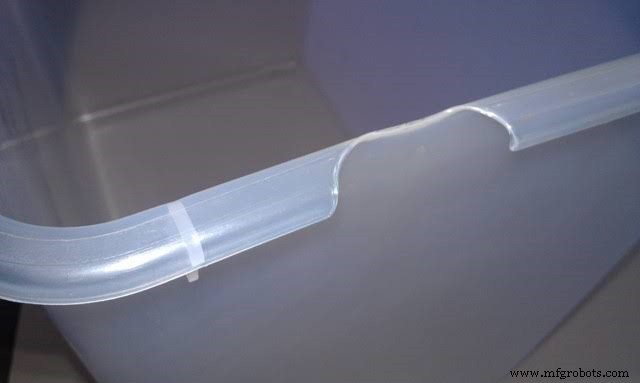
プラスチック射出成形用の材料の選択
壁の厚さを決定するための最も重要な要素の1つは、使用される材料です。これは、壁の厚さのプラスチック設計をどれだけ薄くできるかについて、材料が制限要因になるためです。さまざまな材料により、さまざまな壁の厚さが可能になります。主要な生産を開始する前に、壁の厚さの構成についてさまざまな材料やプラスチックの設計を試すことができるテスト段階を通過することが重要です。
材料の選択によって、プラスチックの厚さも決まります。選択できるいくつかの材料があります。一部の材料では非常に薄い壁を設計できますが、他の材料ではより厚い壁が必要になります。材料を選択するときは、機能、パフォーマンス、およびコストのバランスをとるようにしてください。
RapidDirectでは、部品のさまざまな肉厚に対応できるさまざまな材料を提供しています。資料の詳細については、資料のセクションをご覧ください。さまざまなプラスチック部品の推奨肉厚も以下にあります。
一般的な材料の厚さのガイドライン。
マテリアル | 推奨壁厚 |
ABS | 0.045 – 0.140 |
アセタール | 0.030 – 0.120 |
アクリル | 0.025 – 0.500 |
液晶ポリマー | 0.030 – 0.120 |
長繊維強化プラスチック | 0.075 – 1.000 |
ナイロン | 0.030 – 0.115 |
ポリカーボネート | 0.040 – 0.150 |
ポリエステル | 0.025 – 0.125 |
ポリエチレン | 0.030 – 0.200 |
ポリフェニレンサルファイド | 0.020 – 0.180 |
ポリプロピレン | 0.025 – 0.150 |
ポリスチレン | 0.035 – 0.150 |
ポリウレタン | 0.080 – 0.750 |
硬質PVC | 0.090 – 0.250 |
ソフトPVC | 0.025 – 0.150 |
壁が厚いほど、部品が強くなります。また、反りのリスクが高まり、製品に余分な重量が加わり、製品に余分な時間がかかり、さらに多くの材料が必要になります。一方、薄い壁は安価ですが、製品のひび割れや破損につながる可能性があります。壁の厚さと性能の適切なバランスを見つけることが重要です。
製造可能性のための設計
パーツの肉厚のプラスチック設計を修正した後でも、新しい修正でパーツがどのように機能するかを確認することをお勧めします。そこで、Design for Manufacturabilityプロセスが登場します。DfMを使用すると、新しい欠陥やその他の設計変更を簡単に特定して、壁の厚さを減らすことができます。
この段階の重要性のために、この分野の専門家であり、最良の結果をもたらす専門家にそれを引き渡すことも不可欠です。または、自分で行うこともできます。ただし、これにより製品のリードタイムが長くなるだけです。したがって、この時点で専門家にアウトソーシングしてみませんか。
RapidDirect射出成形サービスを使用すると、製品設計が最高であることを確認するために働く専門のDfMアナリストのチームにアクセスできます。また、設計者はDfMアナリストと協力して、成形品の肉厚のプラスチック設計が最適な形になっていることを確認します。
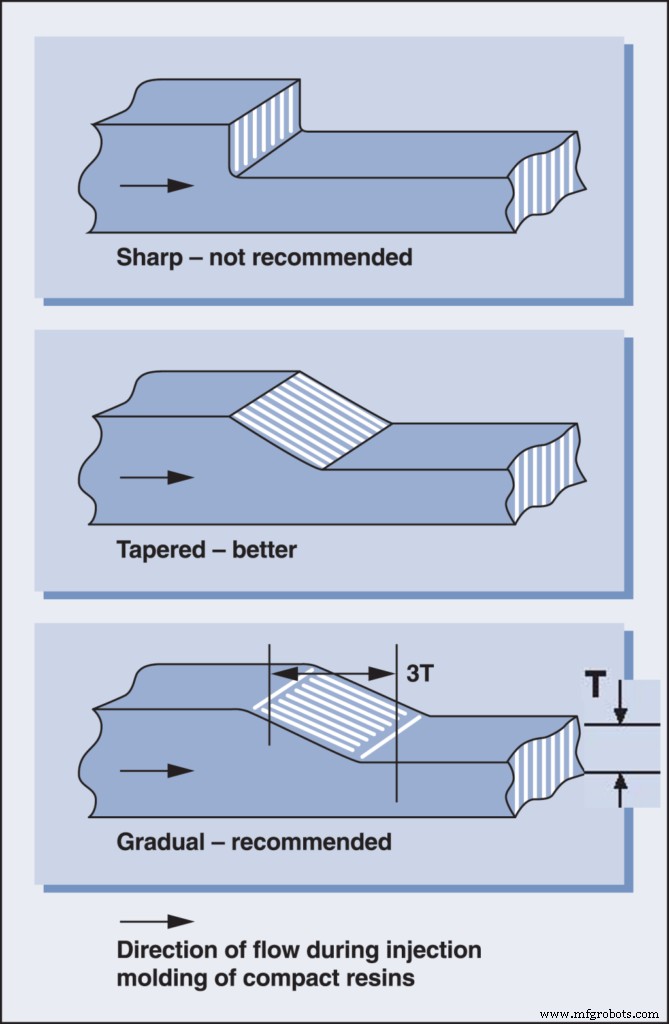
結論
プラスチック射出成形プロセスで肉厚を均一に保つことは、製品の美観と構造的完全性に優れています。考慮しなければならないことがたくさんあるので、これは非常に難しい場合があります。このプロセスを簡素化するには、プロジェクトを複雑にすることなく実現するために必要な経験とスキルを備えた射出成形会社と協力する必要があります。 RapidDirectは、射出成形作業に肉厚の欠陥がないことを確認するのに最適な選択肢です。
RapidDirectプラスチック射出成形サービス
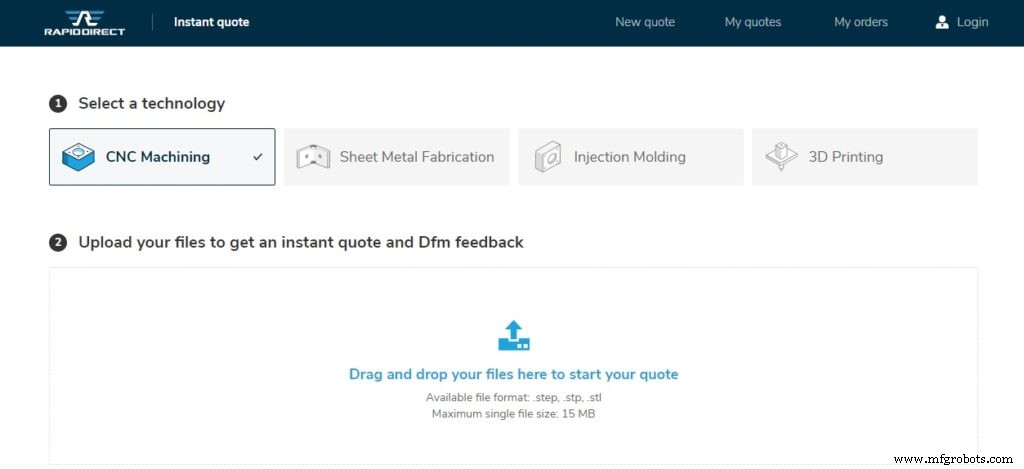
RapidDirectには、さまざまな素材から選択できます。これにより、プロジェクトに最適な機能、パフォーマンス、価格の素材を選択できます。このように、さまざまなプラスチックの厚さも自由に使用できます。また、さまざまなニーズに対応するために、さまざまな射出成形プロセスを提供しています。
高度な設備により、スピーディーにお迎えいたします。 1営業日以内に見積もりを提供します。また、無料のDFMフィードバックにアクセスして、生産を開始する前に設計上の問題を解決するのに役立ちます。
開始するには、今日当社のWebサイトにアクセスしてください。
複合材料