トップガスリサイクル高炉プロセス
トップガスリサイクル高炉プロセス
高炉(BF)による溶銑(HM)の製造分野において、CO2(一酸化炭素)排出量を大幅に削減する最も有望な技術は、CO(一酸化炭素)とH2(水素)のリサイクルです。 BFトップを出るガス。トップBFガスのCOおよびH2含有量は、還元ガス元素として作用する可能性があるため、BFへの再循環は、BF性能を改善し、C(炭素)およびH2の利用を高めるための効果的な代替手段と見なされます。 CO2の排出を削減します。この「トップガスリサイクル」(TGR)技術は、主に、トップBFからCO2を除去した後、還元剤(COおよびH2)を再利用して、化石C(コークスおよび石炭)の使用量を削減することに基づいています。ガス。これにより、必要なエネルギーが削減されます。生産性が高く、PCI(微粉炭注入)率が高く、燃料率が低く、CO2排出量が少ないなどの利点があります。 、TGR-BFプロセスは、将来有望な製鉄プロセスの1つと見なされています。
TGR-BFでは、上部のBFガス中の窒素(N2)を除去するために、熱風の代わりに酸素(O2)がBFに吹き込まれます。 COとH2を含むトップBFガスの一部は、BFの還元剤として再び利用されます。 BFトップガスからのCO2が回収され、貯蔵されます。さまざまな目的のために、いくつかのリサイクルプロセスが提案、評価、または実際に適用されています。これらのプロセスは、(i)CO2除去の有無、(ii)予熱の有無、および(iii)注入位置によって区別されます。
TGR-BFの概念(図1)には、(i)シャフトおよび炉床羽口の上部高炉ガス成分COおよびH2を削減する注入、(ii)コークスの減少による化石C投入量の削減を含む多くの技術が含まれます。 (iii)炉床羽口での高炉ガスの代わりに純粋なO2ガスを使用すること(プロセスからのN2の除去)、および(iv)地下貯蔵用のトップBFガスからの純粋なCO2の回収。
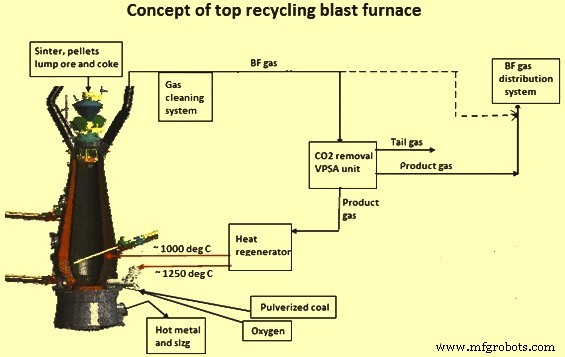
図1TG-BFの概念
トップガスリサイクルの概念は、スウェーデンのルレオにあるLKABの実験的BF(EBF)で実験的にテストされています。 EBFが変更され、VPSA(真空圧力スイング吸着)技術に基づくガス分離プラントがEBFの近くに建設されました。
BFトップガスリサイクルの歴史
還元剤の割合を下げ、BFの生産性を高めるために、従来のBFプロセスに基づくいくつかの新しい概念が20世紀に導入されました。
すでに1920年代に、BFに高温還元ガスを注入するためのコンセプトが開発されました。炉内の羽口からのより低いガス量は、27%CO、33%H2、および26%N2を含む1000℃で予熱された還元ガスを下部シャフトゾーンに注入することによって補償する必要がありました。その結果、BFプロセスに必要なのはコークスの30%(当時は345 kg / tHM)のみでした。 1960年代半ばに、このアイデアはベルギーで再び取り上げられ、1970年代初頭に、最初の試験がベルギーのコッカリル-スランで炉床直径4.6mのBFで実施されました。 1000℃まで予熱された特定量の400Ncum/tHMの改質ガスがBFの下部シャフトに注入されました。還元ガスNcumあたり0.22kgから0.26kgのコークスの置換率が観察されました。
天然ガスのコストが高いため、経済的な理由から、これ以上の調査は行われなかった。 1970年代後半に、ドイツで新しいプロセスの開発作業が開始されました。このプロセスでは、冷たい純粋なO2、燃料、およびリサイクルガスの注入が2つの羽口レベルで実行されました。この考えに基づいて、2番目の羽口列のない従来のBFのために、1984年にカナダでプロセスが開発されました。このコンセプトの主な特徴は、コークスの代わりに石炭を注入することでした。どちらの概念も実現されることはなく、研究としてのみ終了しました。
ほぼ同時に、このアイデアは、シャフトの中央に2列目の羽口が設置された日本のNKKによってさらに使用されました。これらの羽口には、CO2を除去せずにリサイクルされたトップガスからなる予熱された還元ガスが注入されました。ガスは酸素との部分燃焼によって加熱された。コールドO2、石炭、コールドリサイクルトップガスが炉床の羽口に注入されました。 NKKは、3つの羽口、3.9 cumの内容積、および0.95mの炉床直径を備えた実験的なBFでプロセスをテストしました。石炭の注入量は320kg/ tHMに増やすことができ、コークスの注入量は350 kg/tHMに減らすことができます。日本では電気エネルギーと天然ガスの価格が高かったため、トップBFガスのリサイクルによる統合鉄鋼プラントの燃料ガスの不足により、このプロセスの開発が中止されました。
トップガスリサイクルを備えたBFの最初の商業運転は、1980年代後半にロシアのRPA Toulachermetによる12のキャンペーンで、有効量1033cumのBF番号2で実施されました。このオールコークスBFプロセスのコンセプトでは、CO2をほとんど含まないホットトップガスが、純粋なO2とともに炉床羽口に吹き込まれました。脱炭酸されたトップガスは、1200℃まで高温ストーブで加熱されました。この新しいプロセスにより、約250,000トンの溶銑(HM)が生成されました。達成された最低のコークス率は367kg/ tHMでしたが、基準値の606 kg / tHMと比較すると、コークス率が239 kg(39%)減少しました。これらのキャンペーン中に、深刻な羽口の焼損が見られ、羽口の設計に変更が生じました。 CO2洗浄システムの問題により、最終的にプロセスが停止しました。これらの背景調査を考慮して、ULCOS(超低二酸化炭素製鋼)TGR-BFの概念が2004年に開発されました。
ULCOSTGR-BFの開発
開発作業は2段階で実施されています。 2004年から2009年にかけて行われた最初の開発段階では、このプロセスは「ULCOS新高炉プロセス」と名付けられました。このフェーズでは、3つの新しいプロセスコンセプトが開発され、テストされました。 2009年に開始され、「ULCOSトップガスリサイクル高炉プロセス」と名付けられた第2フェーズでは、さらに2つのULCOSTGR-BFキャンペーンが実施されました。
開発中、熱と物質収支モデル、およびBFの3D軸対称モデルを使用して、主要なデータとプロセスの内部状態を計算し、最適な動作パラメーターを選択しました。到達可能なCの節約の可能性と、これらの新しい概念の下でBFを実行する可能性について、4つの代替案が定義され、検討されました。結論として、代替案1、3、および4は、高い微粉炭注入レベルで21%以上の化石Cの節約を達成できるはずです。代替案2は、予想されるCの節約が少なく、リサイクルガスを最初に復熱装置で2段階に加熱し、次に部分酸化によってさらに加熱するという難しい技術が必要なため、却下されました。すべての代替案には、CO2の除去と、炉床羽口へのCOに富む製品ガスの注入、純粋なO2の使用、および還元ガスと一緒の石炭の注入が含まれていました。すべての代替案において、バイオマス、部分的に還元された鉱石、および水素に富むガスの使用が将来の可能性として検討されていました。
代替案1(図2)では、脱炭酸生成ガスは、炉床羽口に純粋なO2と石炭を冷間注入し、シャフト羽口に高温注入します。この代替案の重要なポイントの1つは、炉床羽口レベルでの低温ガス流量が小さいため、通常のBFプロセスと比較してレースウェイのサイズが小さくなり、火炎温度が高くなることでした。また、ガス流量が少ないため、新しい羽口の設計が必要でした。
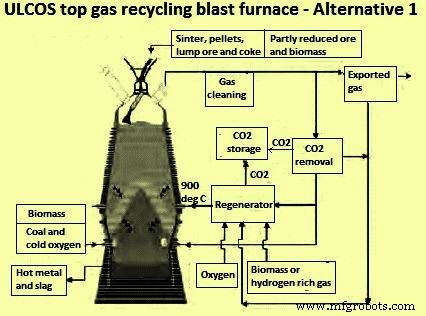
図2ULCOSトップガスリサイクル高炉–代替案1
代替案3(図3)では、脱炭酸生成ガスがO2と石炭とともに通常の炉床羽口に高温で注入されました。高い炭素節約を達成するには、低いRAFT(レースウェイ断熱火炎温度)で操作すると同時に、高い石炭注入率で操作する必要がありました。
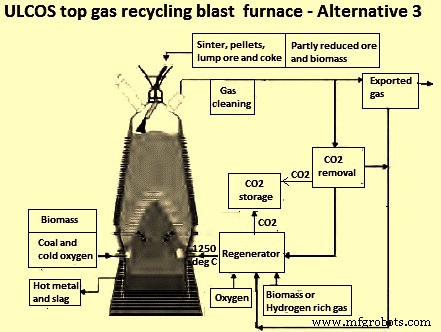
図3ULCOSトップガスリサイクル高炉–代替案3
代替案4(図4)では、脱炭酸生成ガスが炉床羽口に高温で注入され、下部シャフトに高温で注入されました。リサイクルガスの温度は、室温から1250℃まで変化しました。
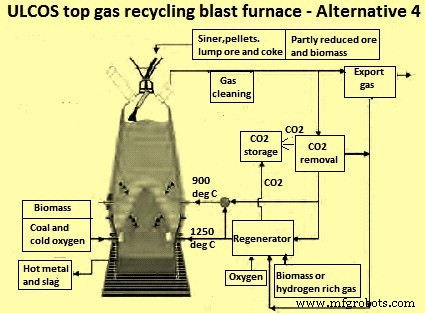
図4ULCOSトップガスリサイクル高炉–代替案4
代替案1および4では、生成ガスもシャフト羽口から注入されます。違いは、ガス注入温度と注入ポイントの位置です。すべての場合において、ガスの少なくとも一部は再生システムで加熱されました。代替案1の予想される化石Cの節約は、石炭量170 kg / tHMで21%、代替案3は石炭量180 kg / tHMで24%、代替案4は石炭量150 kg / tHMで25%でした。 。
次に、レースウェイ条件の数学的モデリングとガス化試験が実施され、リサイクルガス、純O2、微粉炭の同時注入の制約下で羽口の設計とエンジニアリングのために実験室とパイロットの両方の規模の調査が行われました。計算結果に基づいて羽口の形状が改善され、運転中のホットスポットや故障を回避し、ガス流の十分なインパルスを維持して十分な深さのレースウェイを形成します。
実験的BFにおけるTGR-BFプロセスのキャンペーン
試験の目的は、炉床羽口に純粋なO2とPCIを備えた完全なTGRモードでのEBFの動作を実証することでした。これは、3つの定義された代替案の下で実行されました。鉄の負担は、ペレットの30%と焼結物の70%で構成されていました。 HMの生産速度は1時間あたり1.5トンの一定レベルに保たれ、PCI速度は130 kg/tHMから170kg/tHMの間で変化しました。さまざまな試行期間中に、化石Cを最大限に節約するために、リサイクルされたトップガスの量が最大化されました。次に、EBFでの試行中に得られた結果を、モデル計算と比較しました。
代替案3と代替案4は、従来のスタートアップ後の最初のキャンペーン中に2007年にテストされました。代替案3は、2009年秋に2番目のキャンペーンで最適化がテストされ、続いて代替案1がテストされました。2010年の3番目で最後のキャンペーンでは、900℃の代替案4に焦点が当てられました。産業規模でのフォローアップULCOSBFデモンストレーションプロジェクトの好ましい代替案。再注入されたガスの温度の900℃の制限は、耐火材料のH2によるシリカ還元の問題を回避するために設定されました。
各キャンペーン中に、温度とガス組成の現場測定、および負荷材料からのサンプルが、2つの負荷内プローブを使用してEBFから取得されました。新しい運転条件での負担材料の挙動を調査するために、キャンペーンの停止直前に、異なる焼結材料とペレット材料のバスケットがEBFに投入されました。これらのバスケットは、窒素で急冷した後、炉の解剖中にEBFから回収されました。これは2007年と2010年のキャンペーン中に行われました。2009年の2番目のキャンペーンでは、EBF課金システムに問題があり、バスケットが課金されなかったため、キャンペーンの準備ができていなかったため、クエンチのみを実行できました。
>キャンペーン中に、凝集ゾーンからサンプルが回収され、レースウェイのサイズと形状がさらに調査するために測定されました。キャンペーンは、最初に加熱と熱安定化のために、次に従来のBF操作の基準を確立するために、焼結物を使用した従来のBF通常操作(熱風)の1週間で開始されました。参照後、ブロワーを外し、生成ガスをペブルヒーター(再生器)に接続するために停止しました。 TGR-BFモードでの起動は、ランスからの冷たいO2とペブルヒーターからの熱いN2からなる人工爆風によって行われました。プログレッシブステップでは、ペブルヒーターからのN2が脱炭酸トップガス(生成ガス)に置き換えられました。
ULCOSTGR-BFのキャンペーンの結果
キャンペーンから浮かび上がった最初の結論は、ULCOSTGR-BFプロセスを運用することが可能であるということです。新しいプロセスでのキャンペーン中に、安全関連の問題は発生しませんでした。 2番目に重要な施設であるVPSAユニットの運用はスムーズで、大きな故障はありませんでした。 VPSAユニットと組み合わせたEBFは、キャンペーン中に非常にうまく機能しました。
ただし、VPSAユニットの動作は、トップガス組成とEBFからのガスの量の変化によって影響を受けることに注意する必要があります。したがって、両方のユニットは非常に緊密な関係で運用されることになりました。キャンペーン中に達成されたリサイクルトップガスの最大比率は約90%でした。
TGR-BFプロセスのキャンペーン中、BFの安定した動作は、負担のスムーズな下降を経験し、熱安定性を維持するのは簡単でした。 BFシャフト内のガスの効率は、さまざまな代替案の間安定しており、負荷内シャフトプローブの測定によって示されるように、良好なガス分布がありました。ただし、キャンペーン中にいくつかの機器の障害が発生したため、新しいプロセス条件下での操作中にEBFを停止する必要がありました。コールドO2とホットN2の人工熱風による「従来の操作」の操作ステップに戻るには、いくつかの長い停止が必要でした。小さな停止では、ガス注入を停止し、コークスや石炭を追加するだけで済みました。
N2で始動した後、利用可能な最高のBFガスがない場合、生成ガスは約1時間以内に再びリサイクルできます。すべての問題は予測どおりに解決され、BFの熱安定性が深刻な危険にさらされることはありませんでした。キャンペーンに沿って、得られた経験と自信の向上により、EBFの回復を(本番レベルで)より速くすることが徐々に可能になりました。代替案の変更(3から4、3から1)のたびに、シャフト羽口への必要なガス接続と炉床羽口の交換のために、BFを約8時間停止しました。
実験室レベルで実施された実験は、従来の負担材料が新しいプロセスにとって問題ではないことを示していました。これはキャンペーン中に確認されました。負担材料の特性に関連する特定のプロセスの問題はありませんでした。プローブと掘削サンプルの両方の結果は、焼結体とペレットの両方のサンプルについて、壁での還元レベルが低く、炉の中心での還元レベルが高い中央作業炉の還元プロファイルを示していました。掘削サンプルのタンブリング試験では、実験室試験に対応する従来のBFプロセスと同様の崩壊挙動が示されました。負荷試験作業から、現在の従来のBFで使用されている負荷特性はULCOSTGR-BFプロセスに問題がないように思われると結論付けることができます。
ULCOS TGR-BFキャンペーン中に達成された結果は、C(石炭およびコークス)の節約に関して非常に有望でした。 3つのキャンペーンすべての試験では、脱炭酸された高炉ガスの注入によって達成された還元剤の割合の大幅な減少が示されました。 3つのキャンペーン中に、石炭とコークスの投入量は約530 kg/tHMから400kg/ tHMに減少しました。これは、Cの大幅な節約に相当します。炭素投入量は470 kg/tHMから約350kg/ tHMに減少し、結果として約25%のC節約。
2番目のキャンペーンが早期に停止したため、代替案1を完全に検討することはできませんでしたが、コークスを介したC入力の最大削減量は従来のBF操作での参照期間と比較して21%でした。この代替案のために、新しい羽口技術が開発されました。羽口の設計は、微粉炭の注入に使用される内側のパイプとO2の注入に使用される外側のパイプを備えた同軸パイプで構成されていました。設置された3つの羽口は非常にうまく機能し、分解後も損傷や摩耗は見られませんでした。 VPSAはBFトップガスの最大88%をリサイクルすることができました。
代替案3に関しては、最初のキャンペーンでC消費量を最大15%削減でき、トップガスリサイクル率は約72%でした。この代替案の結果は、熱と物質収支の計算(24%)から予想されるよりも低かった(約15%)。これは、トップガスリサイクルモードの最初の経験であり、プロセスが最適化されなかったためです。 2番目のキャンペーンでは、この代替案の結果ははるかに優れていました。最高のガスリサイクル率が最大90%で、C入力の最大削減率が約25%に達したときです。
代替案4の場合、最高ガスリサイクル率90%で24%のC節約が達成されました。コークスと石炭の消費量に関しては、基準運転期間と比較して、新しいプロセス(代替案4)で最大123 kg/tHMの節約がありました。これらの結果から、注入されたガスの量(CO + H2)と還元剤率の低下との間の良好な相関関係を決定することができました。コークスと石炭を介したCの投入量は、注入されたガス(CO + H2)100Nあたり平均17kg削減できます。
EBFのキャンペーンは、現在のBFの消費レベルと比較した場合、はるかに低い化石C消費レベルでBFプロセスを実行できることを証明しました。還元性脱炭酸トップガスの注入により、最大25%のC節約が証明されました。これは、現在の最良のBFプロセスと比較して大幅な低下です。実際のところ、現代のBFにBF-TGR技術を適用すると、C消費量が現在の約405 kg C/tHMから約295kgC/tHMに削減されると期待されています。
>VPSAユニットは安定して動作しています。 VPSAユニットがBFからのトップガスの97%を処理できることに気づきました。注入ガス中のCO2の平均体積分率は約2.67%、CO回収率は88%であり、量と質の要件を満たしています。 VPSAおよびCCSユニットと組み合わせると、TGR-BFプロセスによって削減されるCO2排出量は1270 kg / tHMに達する可能性があり、これは製鉄プロセスの総CO2排出量の76%を占めます。削減されたCO2の24%はガスのリサイクルによるもので、残りの52%はCCSによって地下に輸送および保管されました。
プロセスの観点から、HMの温度と品質に関する限り、ULCOS操作は従来のBF操作よりも安定していると言えます。これは本質的に、はるかに低いレベルの直接還元率(DRR)に関連する溶液損失反応の影響が少ないためと思われます。このDRRの最低観測値は5%です。動作結果には、これが実際にULCOSTGR-BFで到達可能な最小値であるという兆候はありませんでした。 HMの品質は、ULCOSTGR-BFの操作によって大きく影響を受けました。特に、シリコン含有量の大幅な減少(絶対値が1%を超える)とC含有量の相関的な増加が観察されました。ただし、従来のBF動作でのシリコン含有量ははるかに低いため(従来のBFでは約0.5%、EBFでは約2.0%)、ULCOSの適用中にそのような大きな変化は予想されないことに注意する必要があります。工業規模でのBF-TGRプロセス。
ULCOS TGR-BFのテストキャンペーンは、新しいTGR-BFプロセスが実行可能で操作が簡単であることを示しています。優れた安全性、高効率、強力な安定性で操作できます。テストキャンペーンは、EBF操作を4つの操作モード(従来型、代替案1、3、および4)間でシフトできることを証明しました。また、BFプロセスとガス分離プラントVPSAを閉ループで運転できることも証明されました。得られたCの節約は、フローシートの計算からの予測と一致していました。テストでは、従来の負担材であるシンター、ペレット、コークスがULCOSTGR-BFプロセスに適していることも示されました。
EBFキャンペーンの経験に基づくと、ULCOS TGR-BFプロセスの安全で持続可能な産業用途に注意が必要な項目は次のとおりです。(i)羽口レベルでのガス漏れのリスクにより、羽口レベルを鋳造所から物理的に分離する必要があります。防火、(ii)高温でのフランジの曲がりによる漏れのリスク、(iii)周囲の有毒ガスを回避するための高温ストーブ/ヒーターからの煙突の伸長、(iv)始動段階での故障を回避するため、運用担当者は、機能テスト中に人工ガスのトレーニングを受ける必要があります。(v)羽口のノズルでの蓄積/目詰まりを回避するために最適な注入パラメータが重要です。(vi)蓄積を回避するために羽口への個々の爆風流量制御の重要性目詰まりの場合の羽口内の過剰なO2と微粉炭の使用、(vii)耐火物の選択と耐火物の製造を変更し、可能であればC鋼アンカーの使用を回避する必要があります。 C鋼以外の材料、またはアルミナでコーティングされた鋼を使用する必要があります。(viii)金属部品を慎重に選択することにより、金属の粉塵を避けることが重要です。
テスト結果は、代替案4が排出削減の効果が最も高く、次の段階での工業規模のBFに関する試験の最初の選択肢として選択されたことを示しています。
製造プロセス