電解加工:定義、部品または構造、動作原理、長所、短所、用途
この記事では、定義、部品または構造、動作原理、長所、短所、電解加工の応用について詳しく説明します。
最初に定義から始めましょう
電解加工の定義:
非従来型の機械加工として特徴づけられる電解加工(ECM)は、高度な機械加工、非接触、逆電気めっきプロセスです(ECMは材料を堆積させる代わりに除去します)。 ECMでは、導電性流体を介してツールとワークピースの間に大電流が流れます。大電流と導電性流体を使用して、ワークピースの金属原子をイオン化して除去し、バリのない表面を生成します。
従来のまたは従来の機械加工プロセスでは、工具材料はワークピース材料よりも硬くなければなりません。しかし、電解加工の際立った特徴は、ワークピース材料の強度、硬度、靭性に依存しないため、あらゆる導電性材料の機械加工や、高強度材料の複雑なキャビティの機械加工にも適しています。
電気分解プロセスは、「電気分解の法則(電気めっき)」に基づくECMの最も基本的な活動です。 」は1833年にファラデーによって策定されました。
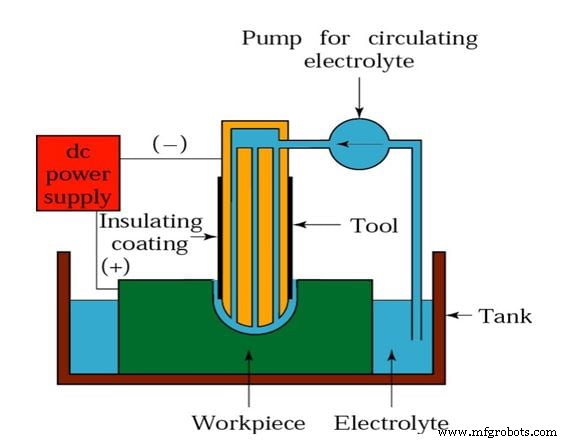
電気分解は、適切な溶液に浸された2つの導体の間に電流が流れるときに発生する化学現象です。
固体導体では、電流は電子によって運ばれます。
電解質では、電流は原子または原子のグループによって運ばれます。原子は、電子を失ったり、獲得したりするときに、それぞれ正または負の電荷を獲得するときにイオンと呼ばれます。正イオン(陽イオン)は、電解質を流れる正電流の方向に陰極に引き付けられ、負イオン(陰イオン)は陽極に引き付けられます。
この電極と電解質のセットアップは、電解セルと呼ばれます。
電解加工部品または構造:
電解加工は次の主要部分で構成されています:
- 電源
- 電解質
- ワークピース
- ツール
- フィードユニット
- タンク
- ワーク保持テーブル
- 圧力計
- 流量計
- 流量制御バルブ
- 圧力逃し弁
- ポンプ
- 貯水池タンク
- フィルター
- スラッジコンテナ
- 遠心分離
- ヒュームエクストラクター
- エンクロージャー
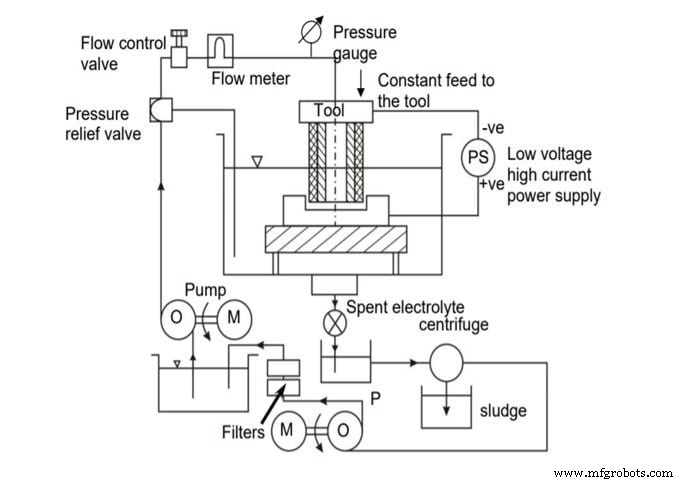
電源:
高いピッチの正確さのために工具とワークピースの間のギャップが小さいため、短絡を避けるために電圧を低く保つ必要があります
材料除去率∝電流密度。したがって、ECMプロセスには高電流値が使用されます。
ECMプロセスの電源パラメータは次のとおりです。
- ECMでは電源は電気です
- タイプ:直流
- 現在の容量:50〜40,000 A
- 電圧を小さく保ちました(短絡を防ぐために ):2〜35 V
電解質:
電解質は導電性流体であり、電極と同等に選択されます。いくつかの電解質と電極の組み合わせを以下に示します:
- 鉄合金には20%の濃度の塩化ナトリウム(NaCl)が使用されます。
- 硝酸ナトリウム(NaNO3)は鉄合金に使用されます。
- ニッケル合金には塩酸(HCl)が使用されています。
塩化ナトリウム(NaCl)と硫酸(H2SO4)の混合物は、ニッケル合金に使用されます。
チタンには、10%フッ化水素酸(HF)、10%塩酸(HCl)、10%硝酸(HNO3)の混合物を塗布しました。
水酸化ナトリウム(NaOH)は炭化タングステン(WC)用です。
電解質には次の特性が必要です:
- 高導電率
- 低粘度
- 低毒性と腐食性
- より良い材料除去率のための化学的および電気化学的安定性。
電解質の3つの機能は次のとおりです:
- ツールとワークピースの間で電流を流します
- 内部電極ギャップから製品を取り除きます
- 電流の通過によって発生する熱を取り除きます。
ECMの電解質パラメータは次のとおりです。
- 温度:20°C–50°C
- 流量:100A電流あたり20リットル/分
- 圧力:0.5〜20バール
- 希釈:100 g / l〜500 g / l
ワークピース:
ワークピースは、材料が溶液に入る機械加工が必要なオブジェクトです。ワークピースはECMでアノードになります。材料の除去率または機械加工は、被削材の原子量と原子価にのみ依存します。
ワークピースは任意の導電性材料にすることができ、電流の漏れや短絡がないようにシステムから絶縁されています。
ツール:
ツールは、ワークピースから材料を取り除くために使用されます。陰極にして電源のマイナス端子に接続します。ツールは、次のプロパティを念頭に置いて選択および製造されています。
- 電気の良い導体。
- 負荷と流体圧力を吸収するのに十分な剛性。
- 電解質に対して化学的に不活性です。
- 簡単に成形でき、希望の形状に加工できます。
- 非常に正確に製造する必要があります
ワークピースに得られたキャビティは、工具形状のレプリカです。したがって、加工後のワークの精度は、工具形状の精度に直接影響されます。
ツール作成に利用できる資料 :銅、真ちゅう、チタン、銅-タングステン、ステンレス鋼、アルミニウム、グラファイト、青銅、プラチナ、炭化タングステン。
材料は、ECMプロセスでツールに堆積されます。ただし、機械加工の産業目的では、材料の堆積は推奨されておらず、溶液中の材料は電解液によって除去されます。
ツールはシステムから絶縁されているため、電流の漏れや短絡はありません。
フィードユニット:
サーボモーターは、ワークピースから材料を除去するための制御されたフィードをツールに提供するために使用されます。送り速度は0.5mm/分から15mm/分です。
- タンク :工具とワークピースを浸す電解液を保持します。
- ワーク保持テーブル :ワーク保持テーブルがワークをしっかりと保持します。
- 圧力計 :これは、電解液がツールに供給される圧力を示しています。
- 流量計 :これは、加工エリアへの電解液の流量を示しています。
- 流量制御バルブ :電解質の流量を制御するのに役立ちます。
- 圧力逃し弁: 供給ラインの圧力が上昇した場合、圧力逃し弁が開き、電解液をタンクにバイパスします。
ポンプ:
ポンプは電解液の循環を助けます。電解液を圧送する速度と圧力は、プロセスの用途や要件に応じて事前に決定する必要があります。
したがって、電解質をポンピングするためのポンプはそれに応じて決定する必要があります。
貯水池 :電解質を保存します。
フィルター:
このフィルターは、供給ラインを詰まらせる可能性のある電解液に存在する不純物をろ過するのに役立ちます。
フィルターは、電解質の品質を一定に保ち、健康と環境保全の目的で電解質から残留有毒イオンを除去することにより、高コストで正確なECMを実現するために使用されます。
スラッジコンテナ :加工時に発生するスラッジを保管します。
遠心分離 :遠心分離機は、遠心力を使用してスラッジを電解液から分離する装置です。
ヒュームエクストラクター :排煙器は、負のドラフトを備えたファンを使用して、エンクロージャーから煙やほこりを引き出す装置です。
エンクロージャー :ECMのシステム全体がエンクロージャーに入れられているため、機械加工プロセスで発生する有毒ガスが環境やオペレーターに影響を与えることはありません。
電解加工の動作原理:
鉄のワークの機械加工の例を見てみましょう。鉄製のワークピースは、ワークピース保持テーブルに組み立てられます。
ツールをワークピースに近づけます。 2つの電極をNaClの電解液(一般的な塩溶液)に浸します。
カソード(ツール)とアノード(鉄のワークピース)は、それぞれ電源のマイナス端子とプラス端子(通常は約10 V)に接続されています。
リザーバータンクからの電解液は、循環ポンプの助けを借りて、ツールの穴を通ってツールとワークピースの間のギャップに流れ込み、継続的にポンプで送られます。
工具送りシステムは、工具をワークピースに向かって前進させます。
アノードでの反応は、アノード反応と呼ばれます。陰極での反応はカトリック反応と呼ばれます。
塩化ナトリウム電解質の基本的な反応:
- 塩化ナトリウムの分離:NaCl ————→Na + + Cl –
- 水の分離:H 2 O ————→H + + OH –
陰極反応:水素イオンが陰極(ツール)から電子を奪い、H 2を形成します ガス。
- 2H + + 2e – ————→H 2 ↑
H 2のみ ガスは陰極で発生します。電極の形状は、ECMプロセスの最も重要な機能である電気分解プロセス中に変更されません。
陽極反応:
- 鉄はワークピース(アノード)から鉄イオンとして出てきます
- Fe ————→Fe ++ + 2e –
- 塩化ナトリウム電解質内での反応
- Na + + OH – ————→NaOH
- Fe ++ + 2OH – ————→Fe(OH) 2 ↓
- Fe ++ + 2Cl – ————→Fe(Cl) 2 ↓
Fe(OH) 2 、Fe(Cl) 2 スラッジとして沈殿します。原子レベルでのこの制御された陽極溶解プロセスにより、ワークピースは徐々に機械加工され、優れた表面仕上げと応力のない表面が得られます。
ツール形状の形状に制約はありません。最初は、工具とワークピースの間のギャップは不均一です。加工後、ギャップはワークピースの長さ全体で均一(0.1mmから2mm)になり、適切な工具またはワークピースの前進速度によってそのように維持されます。
ギャップの幅は徐々に定常状態の値に近づく傾向があり、そのような条件下で得られるキャビティは工具形状のレプリカです。
タンクからのスラッジは、遠心分離機を使用して電解液から取り出され、分離されます。
電解液は、フィルターでのろ過プロセスを経た後、機械加工プロセスのためにポンプで送られるために再びリザーバータンクに運ばれます。
これが電解加工の仕組みです。次に、利点について学習します。
電解加工の利点:
次の電解加工の利点 は:
- 複雑な曲率パーツと凹型の曲率パーツは、凹型と凸型のツールを使用して簡単に作成できます。
- 接続された単一のCNCマシンを使用して、より複雑な形状を作成できます。
- 工具の摩耗はごくわずかであるため、同じ工具を使用して無数の部品を製造できます。
- 工具と被削材が直接接触しないため、力や残留応力が発生しません。
- 原子レベルの溶解による熱損傷がなく、優れた表面仕上げが得られます
- 発熱が少ない。
電解加工のデメリット:
次の電解加工のデメリット は:
- 生理食塩水(酸性)電解質は、ツール、ワークピース、および機器の腐食を引き起こす可能性があります。
- 高い比エネルギー消費量。
- ECMは導電性の被削材のみを加工できます。
- 柔らかい素材には使用できません。
- 大きな生産フロアが必要です。
- ECMは健康と環境への懸念をもたらします。
電解加工アプリケーション:
次の電解加工のアプリケーション は:
- 電解加工は、ダイの沈下と穴の輪郭加工に使用されます。
- (負に帯電した砥石を使用して)研削プロセスと組み合わせて材料を除去することによる研削。このプロセスは、電気化学粉砕とも呼ばれます。
- 空洞を切断し、ジェットエンジンのタービンブレードなどの複雑な構造にさらに深く不規則な形状の穴を開けます。
- ECMは応力のない優れた表面仕上げを提供し、ナノファブリケーションとナノテクノロジーに幅広く適用されるため、トレパニング(キャビティ付きのツール電極を使用)とマイクロマシニングによるマイクロコンポーネントの製造。
- 閉鎖限界内での蒸気タービンブレードのような複雑なプロファイルのプロファイリングと機械加工。
電解加工ビデオ:
産業技術
- ホーニングプロセス:定義、部品または構造、動作原理、利点、アプリケーション[PDF付きのメモ]
- ウォータージェットおよび研磨ウォータージェット加工:原理、動作、機器、アプリケーション、長所と短所
- 電子ビーム加工:原理、動作、機器、アプリケーション、長所と短所
- レーザー加工::原理、動作、機器、アプリケーション、長所と短所
- 研磨ジェット加工:原理、動作、機器、アプリケーション、長所と短所
- 超音波加工:原理、動作、機器、アプリケーション、長所と短所
- 超音波溶接:原理、動作、機器、用途、長所と短所
- 電解加工:原理、破壊、機器、用途、長所と短所
- エレクトロスラグ溶接:原理、動作、アプリケーション、長所と短所
- 鍛接:原理、作業、用途、長所と短所
- 拡散ボンディング:原理、動作、アプリケーション、長所と短所